CAPA documentation is more than paperwork—it’s your shield against FDA warnings, product recalls, and compliance failures. If you’re in the pharmaceutical, biopharmaceutical, or medical device field, one poor CAPA form can ruin your audit record. But don’t worry—we’re here to help.
In this guide, you’ll uncover common CAPA documentation mistakes, how to fix them, and best practices to make your next audit “inspection-ready.”
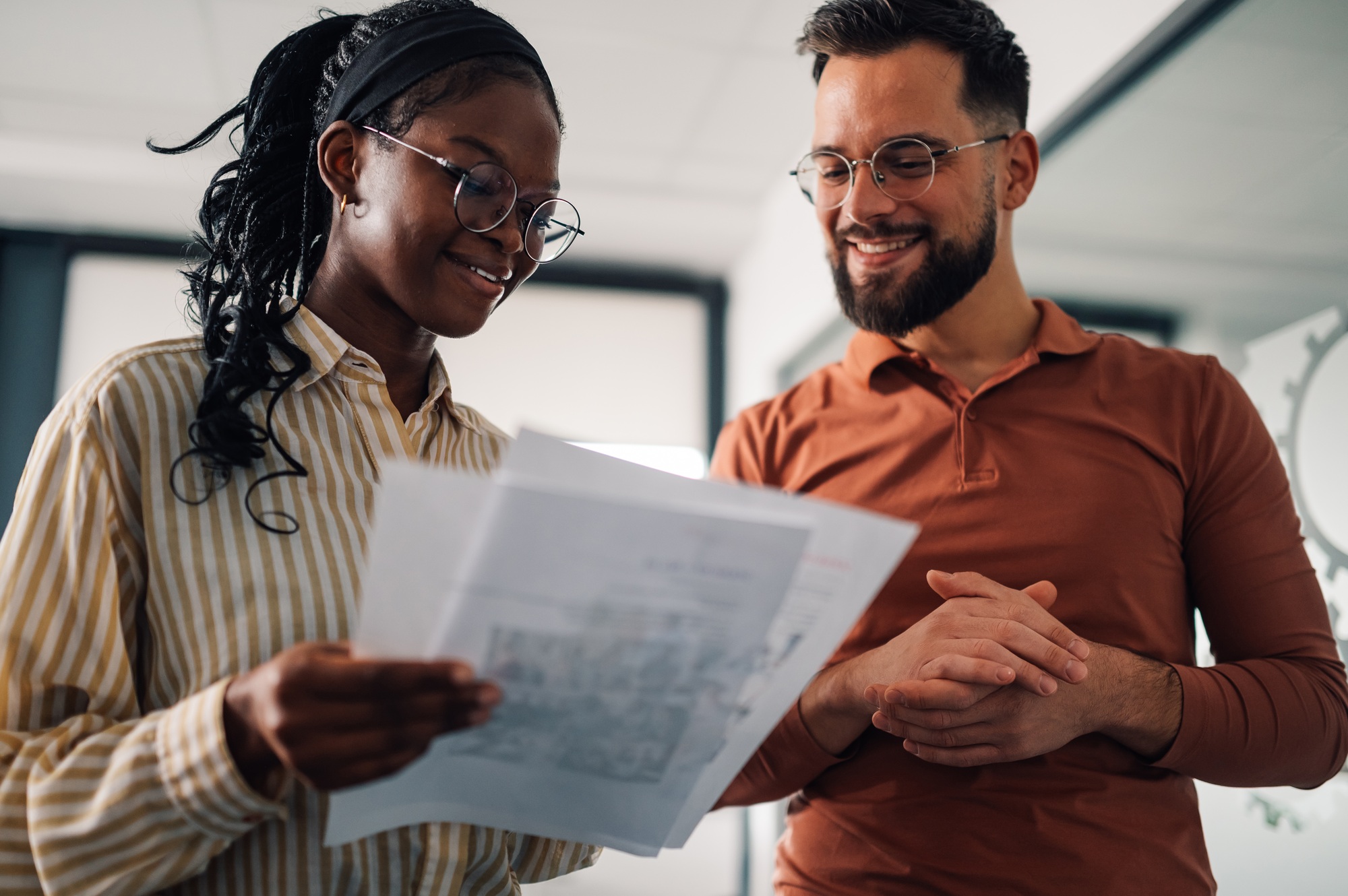
What Is the Purpose of CAPA Documentation?
Corrective and Preventive Actions (CAPA) documentation plays a vital role in ensuring GMP compliance. It serves as the formal record for identifying, investigating, correcting, and preventing quality issues. More importantly, it proves to auditors that your organization reacts to deviations with structured logic and measurable outcomes.
When documentation fails, it’s not just your quality system at risk—your product, patients, and reputation are on the line.
Each CAPA report example must clearly document:
• What went wrong (problem statement)
• Why it happened (root cause analysis)
• What you did to fix it (corrective action)
• What you will do to prevent recurrence (preventive action)
⚠️ CAPA documentation must comply with FDA 21 CFR 820 and EU GMP Annex 15.
Clear Problem Description
Define the issue in plain terms with reference numbers and dates.
Immediate Containment Actions
Record what was done to stop further impact.
CAPA Root Cause Analysis
Use 5 Whys or Fishbone methods to dig deep.
Corrective Action Plan
State specific tasks, owners, and deadlines.
Preventive Action Strategy
Show how you will stop future recurrence.
Effectiveness Checks
Define how and when results will be verified.
Approval and Closure
Ensure signatures, date stamps, and clear status.
Where Most CAPA Documentation Fails
Incomplete Root Cause Investigations
Many teams rush through CAPA documentation and jump to conclusions without proper analysis. They often reuse past reports or copy answers from similar issues.
However, each deviation tells a different story and needs its own investigation. Therefore, you must ask the right questions and collect all the facts.
Always use structured tools like the 5 Whys or a Fishbone diagram. These methods help you explore all possible causes before deciding the root one.
When you skip proper root cause analysis, you only fix the surface problem. As a result, the issue often comes back during production or inspections. Worse, auditors will notice and question your CAPA effectiveness.
To avoid this, connect your findings to data, logs, and expert interviews. Then, write your CAPA root cause investigation report in clear, simple steps.
This not only prevents future failures but also builds trust with regulators and managers. Make every investigation count, even when the issue seems minor.
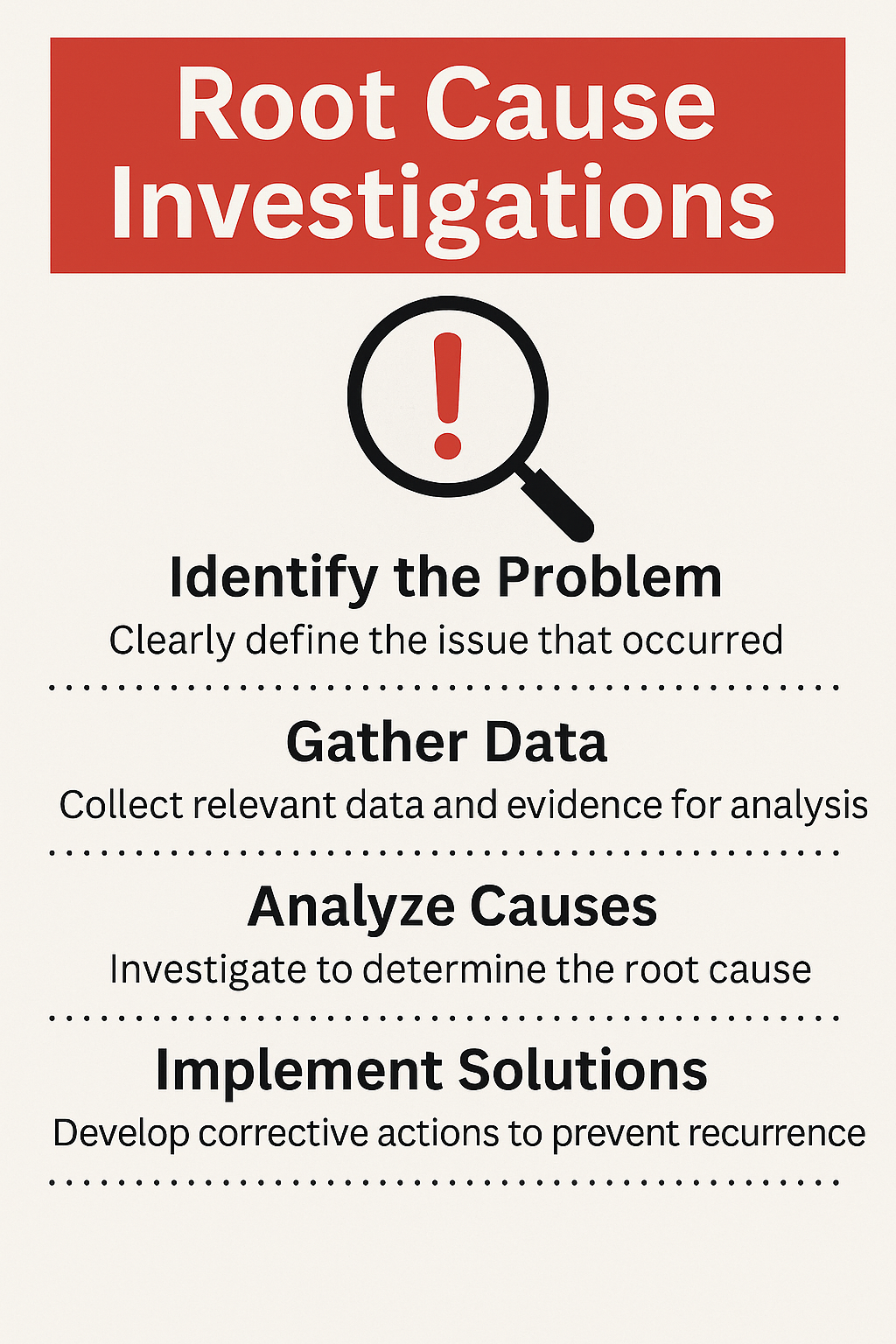
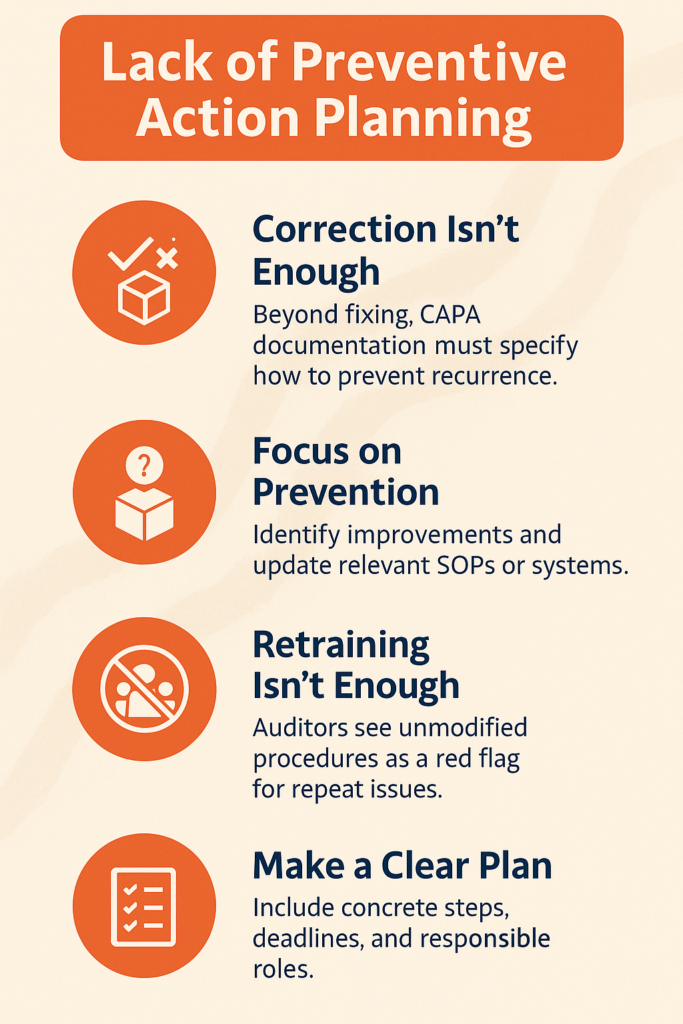
Lack of Preventive Action Planning
Many teams stop after fixing the problem, but that approach creates bigger risks later. You must go beyond correction and build a plan to prevent the issue from returning.
Start by asking what changes can stop the problem for good. Then, review all related SOPs, tools, and systems. If you only retrain staff without updating documents, the change won’t last.
Also, make sure your preventive actions include clear steps and deadlines. This shows auditors that your team acts with long-term thinking.
Additionally, preventive actions must cover more than one department if needed. For example, if a warehouse error caused the issue, check if production faces the same risk.
After that, update all linked processes and assign responsible people. Always track the progress using a CAPA management system or checklist. Moreover, include metrics to measure the action’s impact.
Finally, document everything clearly so the next auditor sees your improvements. Remember, real prevention proves that your quality system works properly.
Top 6 Tools That Improve CAPA Documentation
CAPA Management System Software
Helps track actions, responsibilities, and timelines efficiently.
CAPA Report Example Templates
Standardizes structure and ensures all fields are filled.
Root Cause Analysis Diagrams
Visual tools like Ishikawa or 5 Whys drive deeper insights.
CAPA Form FDA Format Guide
Helps ensure your documentation meets FDA expectations.
21 CFR 820 Compliance Checklist
Matches your CAPA to regulatory clauses.
CAPA System Implementation Checklist
Verifies readiness before audits or inspections.
What Are the Key Objectives of CAPA Documentation?
Ensure Long-Term Compliance
You must treat CAPA documentation as a long-term responsibility, not a one-time task. Every entry supports your overall Quality Management System (QMS) health.
Therefore, update your CAPA documentation regularly and follow through on all actions. Also, link each CAPA to specific QMS goals like risk reduction or error prevention. When you do this, your records show a full story of improvement. Moreover, consistent updates help you track patterns across departments.
To stay compliant with CAPA documentation compliance 21 CFR 820, follow clear procedures and templates. Always check if your CAPA corrective action plan template meets FDA expectations.
Then, make sure each CAPA report example includes preventive steps and outcome tracking. In addition, use CAPA training programs to educate your team on compliance rules. Include progress checks and audits in your CAPA system implementation checklist. This way, your CAPA quality management documentation stays strong and reliable. Over time, strong records prove that your team prevents problems—not just reacts to them.
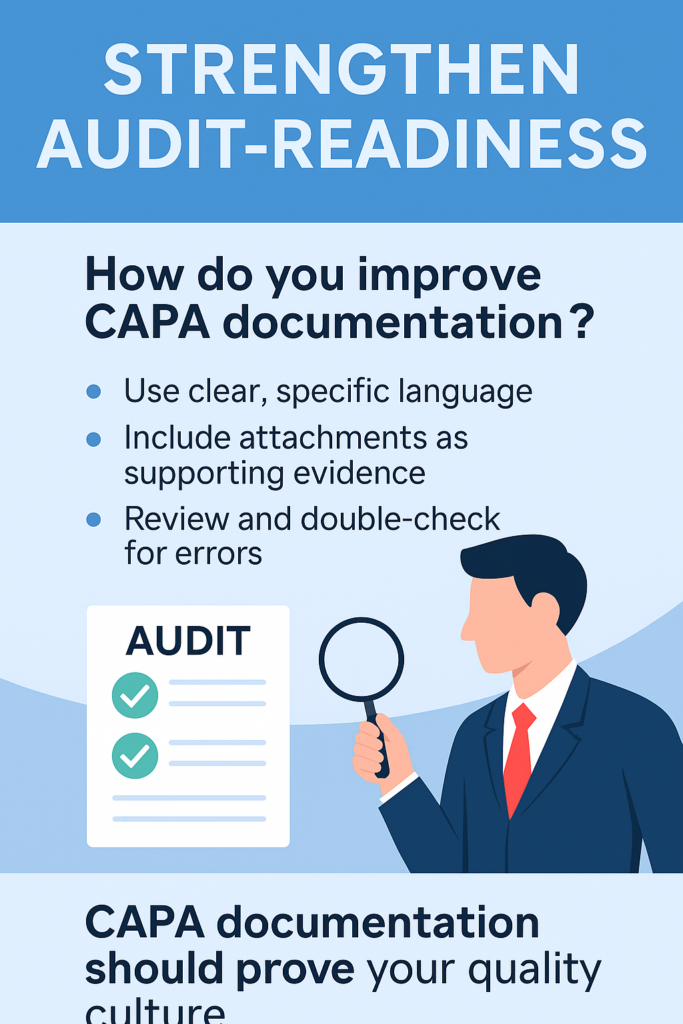
Strengthen Audit-Readiness
You must prepare your CAPA documentation before any audit takes place. Auditors always ask for it first.
Therefore, write clear and complete reports that match your CAPA procedure template. Use strong facts, not vague statements, in every section.
Also, include attachments like logs, emails, and calibration records. These show that your CAPA actions are real and trackable. Moreover, keep your CAPA form FDA-aligned by using approved templates and formats.
Poor CAPA documentation sends the wrong message to inspectors.
It tells them your team lacks discipline. In contrast, strong reports reflect a mature and reliable quality system.
So, always review your CAPA report example before finalizing. After that, ask a peer to check for errors or gaps. Then, file each document in a system that’s easy to access.
You should also include each CAPA in your audit prep checklist. Finally, train your team on how to write CAPA documentation that passes audits.
Strong documentation makes inspections smoother and builds auditor confidence.
What Makes a CAPA Form FDA-Compliant?
1. Clearly Defined Roles and Deadlines
A CAPA form without defined owners is a compliance risk. FDA expects names, not just titles. Each step—containment, investigation, correction—must have owners and due dates.
2. Measurable Effectiveness Criteria
If your CAPA says “issue resolved,” that’s not enough. You must document metrics, timelines, and follow-ups. For example: “Reject rate reduced to <0.5% by end of Q2.”
How to Write CAPA Documentation That Auditors Approve
Write Actively, Not Passively
Say: “QA updated SOP 421” instead of “SOP was updated.”
Use Facts, Not Assumptions
Back your claims with test results, logs, or certificates.
Stay Consistent
Use the same terminology, structure, and fonts.
Include Attachments
Link calibration records, emails, forms.
Highlight Completion
Use checkboxes or dates to show task status.
Peer Review Your Document
Have another expert cross-check for gaps.
Final Thoughts: Fix Your CAPA Documentation Before It Fails You
CAPA documentation isn’t just about writing—it’s about accountability, prevention, and compliance. Whether you’re submitting a CAPA form FDA reviewers will assess or training a junior QA specialist, doing it right builds trust and protects your product’s integrity.
You now understand:
• What makes documentation audit-proof
• Where teams often fail
• How to structure every section
• Tools and templates to simplify your work
Ready to take action?
- Join the CAPA Management Course
- Explore all Pharmuni courses at Pharmuni.com
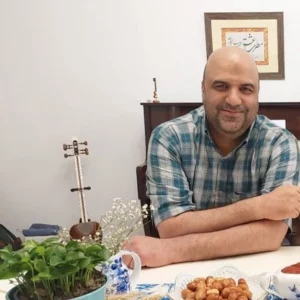
Ershad Moradi
Ershad Moradi, a Content Marketing Specialist at Zamann Pharma Support, brings 6 years of experience in the pharmaceutical industry. Specializing in pharmaceutical and medical technologies, Ershad is currently focused on expanding his knowledge in marketing and improving communication in the field. Outside of work, Ershad enjoys reading and attending industry related networks to stay up-to-date on the latest advancements. With a passion for continuous learning and growth, Ershad is always looking for new opportunities to enhance his skills and contribute to pharmaceutical industry. Connect with Ershad on Facebook for more information.
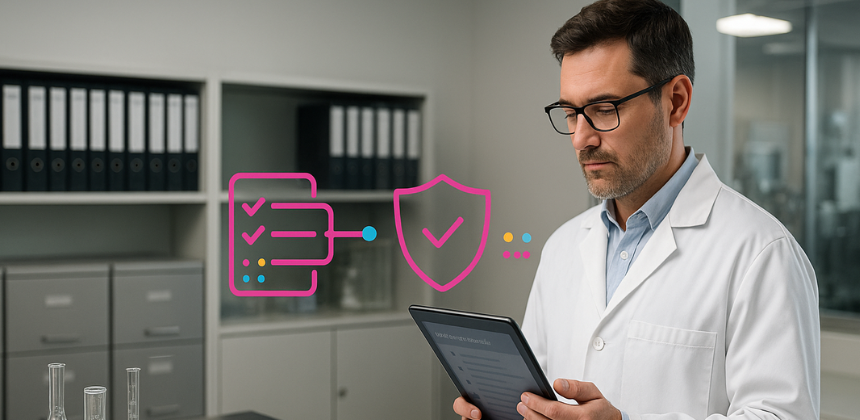
GMP Audit Checklist: Pass Your Next Inspection With ConfidenceÂ
Use this gmp audit checklist to see if you would pass today. Run a 10-minute self-test, verify evidence, and prioritize fixes. Then follow 30- and 90-day plans to strengthen data integrity, CAPA, Annex 1, training, and documentation. Build proof that convinces auditors, reduces risk, and keeps your site inspection-ready year-round.
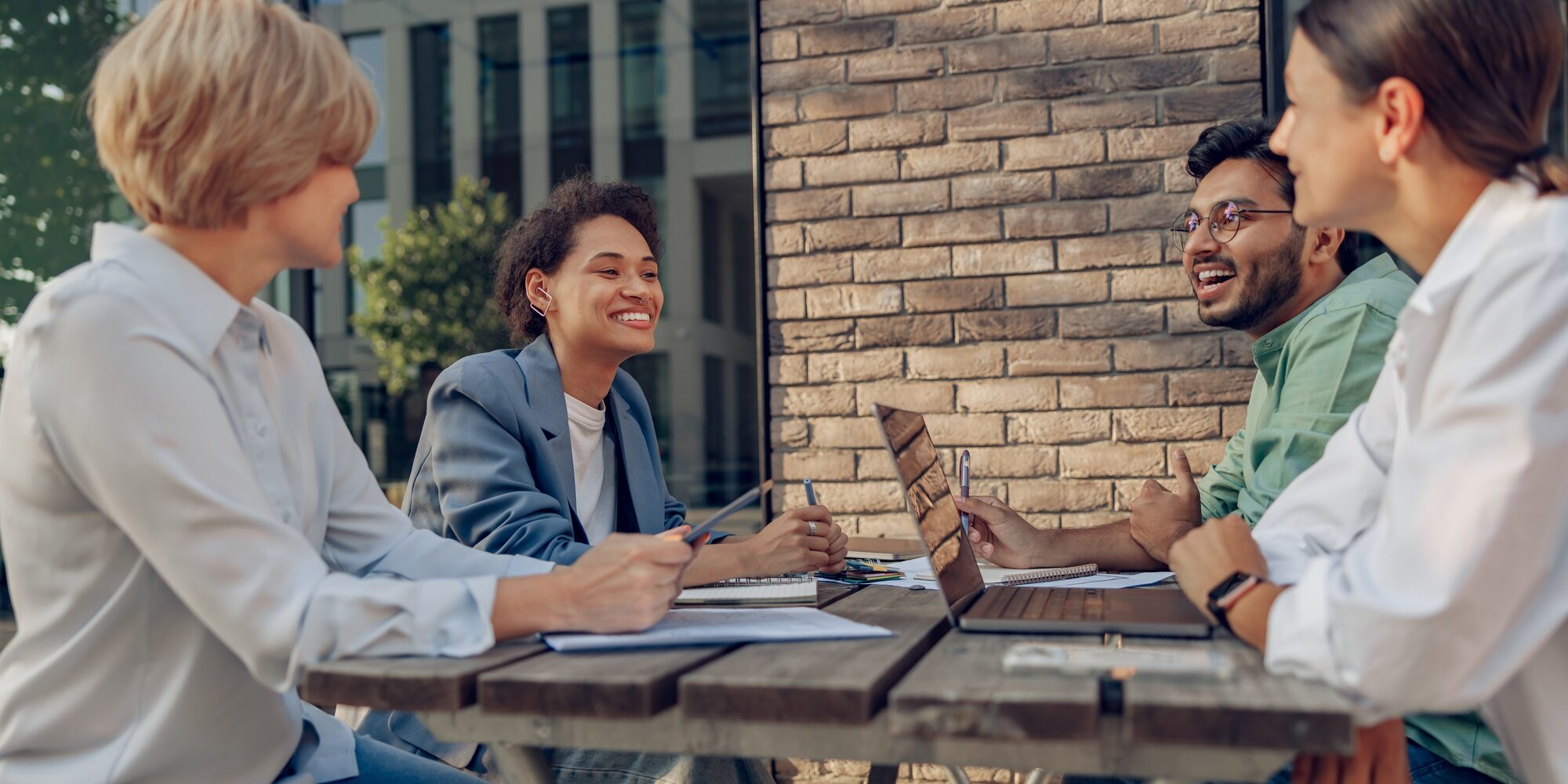
Pharma Sales Secrets to Skyrocket Success
Pharma sales is more than just selling medications. It combines science, strategy, and relationship building. Whether you’re starting out or refining your approach, this guide gives you practical tools, career insights, and tips to succeed in today’s competitive pharmaceutical sales industry.
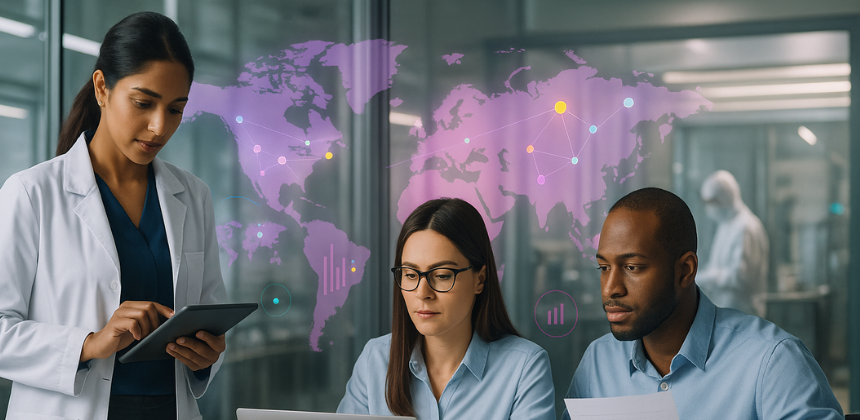
Pharma Job Market Trends: What’s Hot Now
Pharma job market trends show sustained growth across quality, regulatory affairs, pharmacovigilance, and data. New modalities, including cell and gene therapy, expand validation and aseptic roles quickly. Meanwhile, digital tools reshape trials, manufacturing, and safety reporting. Therefore, candidates who blend science, GxP, and analytics win more interviews.