You run a GMP compliant facility and want to strengthen quality control. The CAPA process helps you fix issues fast, prevent recurrence, and ace audits. In this post, we dive into why CAPA matters, how to implement it, and how to elevate your team with proven strategies.
Learn how to avoid FDA 483 CAPA observations, build a robust CAPA workflow, and prepare for FDA QSIT CAPA inspection steps—plus, discover how Pharmuni’s GMP CAPA Management course can empower your quality professionals.
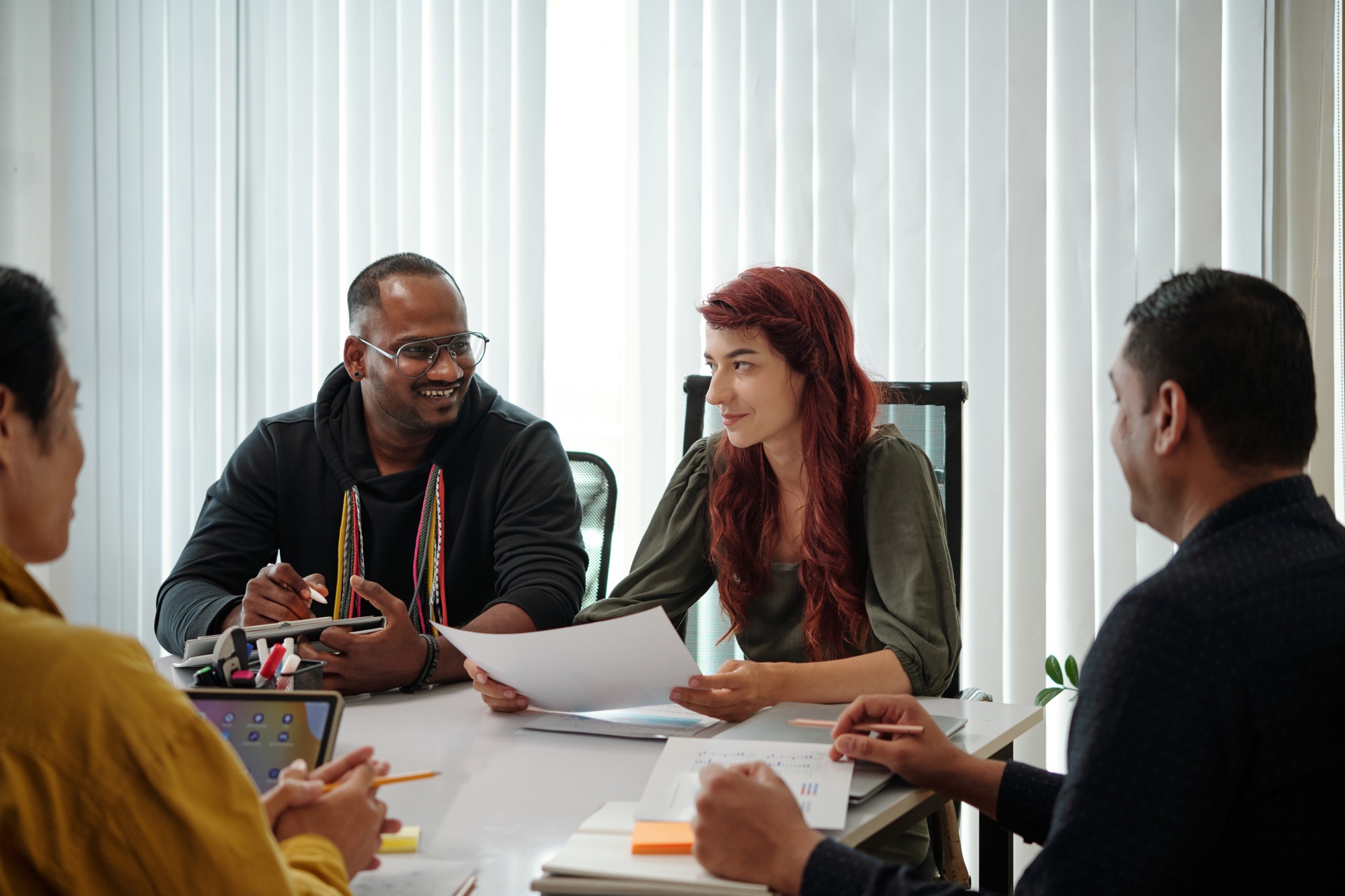
What Is the CAPA Process?
The CAPA process means implementing Corrective and Preventive Actions to address non-conformities and stop them from occurring again. Rooted in standards like CAPA FDA 21 CFR 820, ISO 9001 CAPA, and ISO 13485 CAPA, it’s essential in regulated industries.
CAPA helps maintain quality, ensure compliance, and support continuous improvement. It supports Medical Device CAPA requirements, aligns with IMDRF guidance on CAPA, and helps you avoid CAPA in warning letters.
Info Box: Core Objectives of CAPA
• Fix issues permanently
• Prevent future problems
• Ensure regulatory compliance
• Support audit readiness and culture building
By following a CAPA lifecycle, you build trust, minimize risk, and stay ahead of CAPA audit readiness checks.
Sign up for GMP Corrective and Preventive Actions (CAPA) Management Course
How Does the CAPA Procedure Work? 5 Key Steps
Trigger
In first Step, CAPA begins when specific issues arise. Common triggers include customer complaints, audit findings, FDA 483 CAPA observations, or trends identified through data analysis. Recognizing these signals early ensures timely corrective actions.
Investigation
Next, teams conduct a thorough investigation using tools like 5 Whys and fishbone diagrams. The goal is to uncover the root cause, not just surface symptoms. Document findings clearly using CAPA documentation best practices.
Action
Implement corrective and preventive actions based on the investigation. Cross-functional collaboration is essential. Engage CAPA cross-functional teams to develop effective solutions and ensure accountability for each action item.
Verify
Once actions are implemented, verify their effectiveness. Use CAPA verification & validation methods to confirm that the issue will not recur. Ensuring a closed loop CAPA approach here prevents repeat problems.
Why CAPA Training Process Matters
CAPA Training Programs Build Quality Culture
CAPA training programs help your team build a strong quality culture. First, align everyone with GMP, ISO, and FDA expectations. Then, use scenario-based learning to teach real-world CAPA applications. This approach makes concepts easier to understand and apply. For example, train teams on CAPA escalation strategies and how to handle complex cases. Next, focus on building a clear documentation culture. Encourage everyone to follow consistent practices. Also, emphasize effective cross-functional team collaboration. When teams work together, they solve problems faster and more accurately.
Additionally, focus on preventive skills from the start. Teach trend analysis for CAPA early in the program. This skill helps your team spot patterns before they become major issues.
Moreover, encourage them to shift from reactive to preventive CAPA thinking.
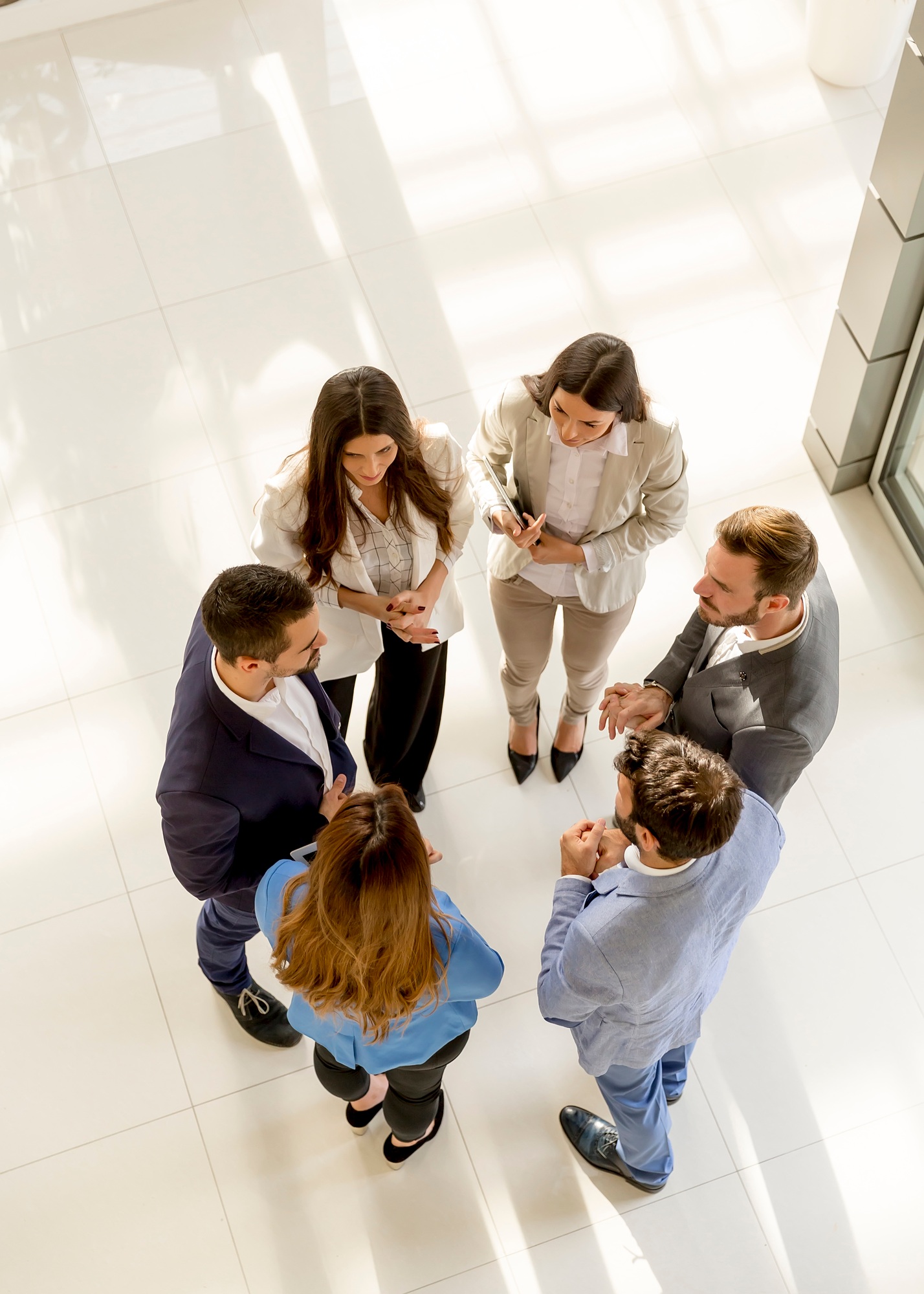
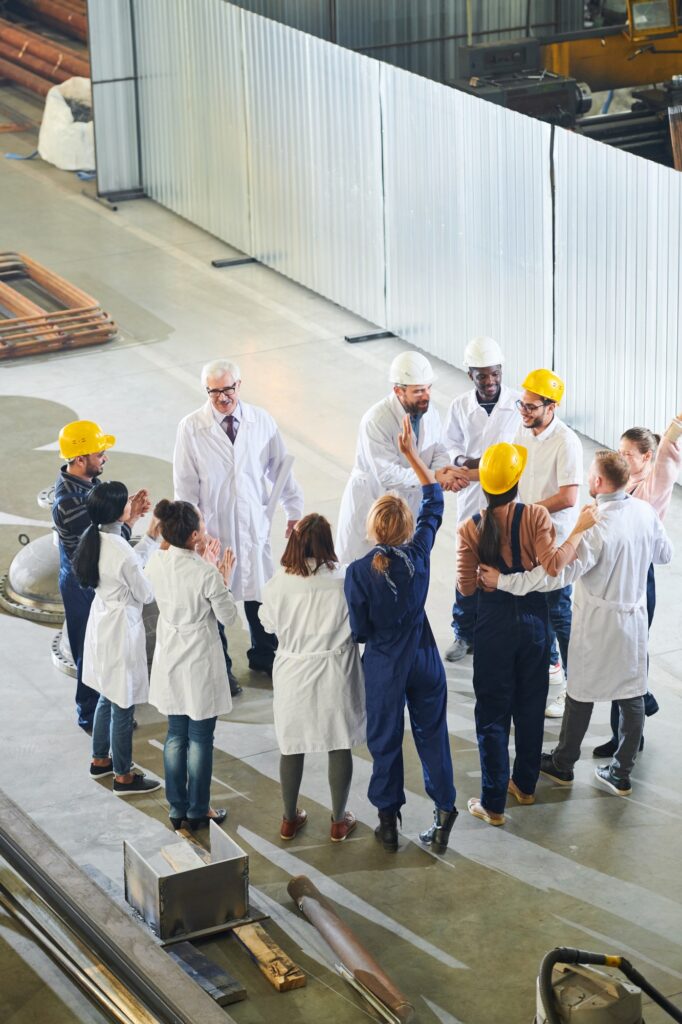
CAPA Ownership Model Drives Accountability
A clear CAPA ownership model builds accountability across your quality system. First, define each role precisely. Assign a CAPA owner who oversees the entire process. Next, appoint investigators who find root causes. Then, designate verifiers who confirm corrective actions work.
This structure ensures no step gets overlooked. Moreover, it creates a culture where every team member knows their role.
As a result, accountability improves and CAPA outcomes become more effective. Additionally, cross-functional teams collaborate better when roles stay clear.
A strong CAPA ownership model also prepares your team for audits.
For instance, auditors often ask who owns each CAPA. When you document clear responsibilities, you demonstrate full control. Furthermore, this clarity helps you manage CAPA timelines effectively.
Teams act faster because they know exactly what to do. Moreover, consistent ownership improves tracking of CAPA effectiveness.
Key Benefits of Closed loop CAPA
Continuous improvement
Captures lessons learned and applies them across operations.
Compliance assurance
Meets FDA QSIT CAPA inspection steps reliably.
Cost reduction
Prevents repeated failures, lowering rework and recalls.
Cross-functional engagement
Promotes better collaboration across teams.
Risk mitigation
Integrates SPC & CAPA, CAPA and supply chain risk strategies for proactive controls.
How to Transition From Reactive to Preventive CAPA
Use Trend Analysis for CAPA
You must track key metrics to improve your CAPA process continuously. First, monitor the frequency of non-conformities. Next, analyze audit findings and customer complaints regularly. This helps you spot recurring patterns early. When you see trends, act fast to prevent future issues. Moreover, use preventive action triggers to stop problems before they escalate.
This proactive approach reduces risks and improves quality. Additionally, tracking metrics helps you prioritize which issues need immediate attention. As a result, your team works more efficiently and focuses on high-impact areas.
These tools give you clear visibility of your closed loop CAPA progress. Furthermore, the course explains how to implement CAPA escalation strategies.
This ensures that critical issues move up the chain quickly. Moreover, you learn to build preventive controls that reduce repeat problems. With these skills, you strengthen your quality system and boost audit readiness significantly.
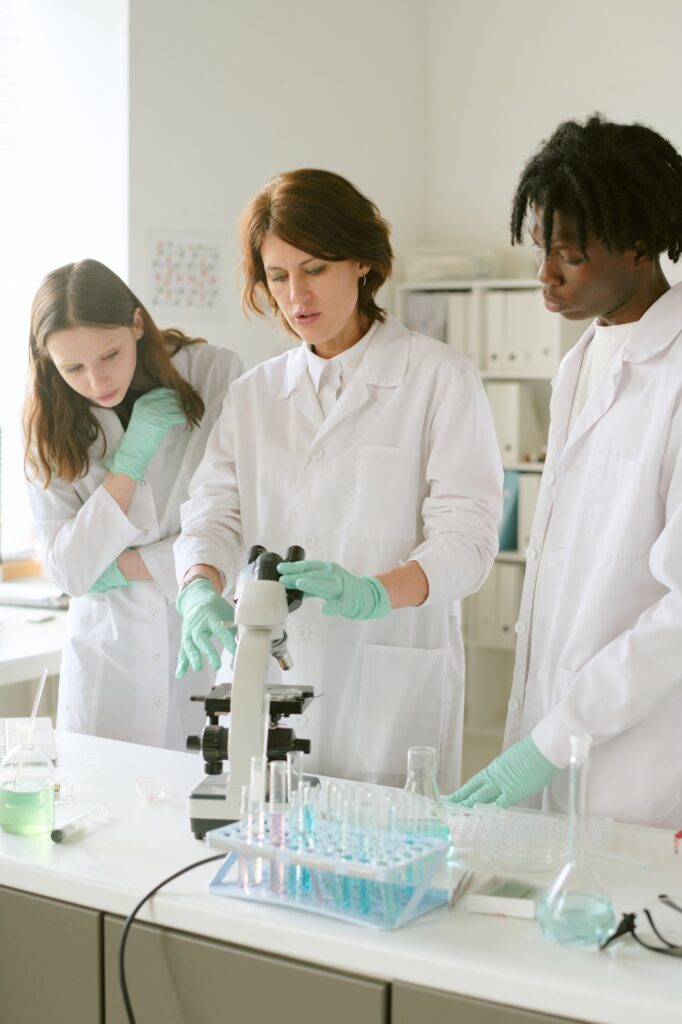
Implement Preventive Action Culture
You should create a culture that rewards early issue detection. First, encourage staff to report problems quickly. Next, promote clear and open communication plans. When teams share information early, you prevent bigger issues later. Moreover, recognize employees who contribute to quality improvements.
This motivates others to follow their example. Additionally, train everyone to use your CAPA system effectively. When staff understand the process, they engage more actively. As a result, your entire organization becomes more proactive about quality.
The course provides templates to guide consistent record-keeping. Moreover, it offers practical examples to align documentation across all departments.
This consistency ensures compliance with GMP and FDA expectations. Additionally, clear documentation improves audit readiness and supports continuous improvement. When everyone follows the same standards, your CAPA process becomes more reliable. As a result, you build a strong foundation for long-term quality success.
When to Use Automation in CAPA Proccess
Use automation when you want to improve CAPA process speed and accuracy. First, implement CAPA tracker tools to assign tasks automatically. These tools also send timely reminders. Next, use dashboard and reporting modules to gain real-time visibility. This helps you track KPIs and identify any backlog. Moreover, automation supports faster decision-making during audits. Additionally, automate CAPA workflow steps to speed up initiation and escalation. This prevents delays and keeps your CAPA system responsive. As a result, your team handles more CAPAs effectively without extra manual work.
You must also integrate automation with your existing Quality Management System (QMS). Doing so connects audits, complaints, and supplier CAPA seamlessly. Moreover, integration reduces errors caused by managing data in silos. With connected systems, you create a true closed loop CAPA process. Additionally, automation improves your team’s compliance with FDA QSIT CAPA inspection steps.
Getting Audit Ready With Your CAPA Process
Mock 21 CFR 820 walkthrough
Ensure all CAPA steps meet regulatory definitions.
Document verification
Validate documentation aligns with CAPA documentation best practices.
Trace corrective/preventive actions
No orphan CAPAs.
Train your people
Host CAPA training programs on your workflow and procedures.
Prepare CAPA audit readiness packs
Include corrective action logs, verification evidence, and trend analyses.
Review past FDA 483 CAPA observations
Ensure none recur.
Conclusion
By mastering the CAPA process, you protect your organization from repeat issues, support audits, and foster a proactive quality culture. You’ll meet Medical Device CAPA requirements, align to IMDRF guidance on CAPA, and stay compliant with CAPA FDA 21 CFR 820, ISO 9001 CAPA, and ISO 13485 CAPA.
Take action today:
➡️ Enroll in PharmUni’s GMP Corrective and Preventive Actions (CAPA) Management course to supercharge your CAPA skills and build a culture of quality and compliance.
➡️ Visit Pharmuni to explore other GMP courses.
➡️ Check out our guides: The Ultimate Guide to CAPA in Pharma Manufacturing and CAPA Implementation Tools for Risk Mitigation in Pharma for deeper insights.
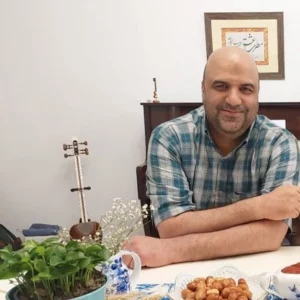
Ershad Moradi
Ershad Moradi, a Content Marketing Specialist at Zamann Pharma Support, brings 6 years of experience in the pharmaceutical industry. Specializing in pharmaceutical and medical technologies, Ershad is currently focused on expanding his knowledge in marketing and improving communication in the field. Outside of work, Ershad enjoys reading and attending industry related networks to stay up-to-date on the latest advancements. With a passion for continuous learning and growth, Ershad is always looking for new opportunities to enhance his skills and contribute to pharmaceutical industry. Connect with Ershad on Facebook for more information.
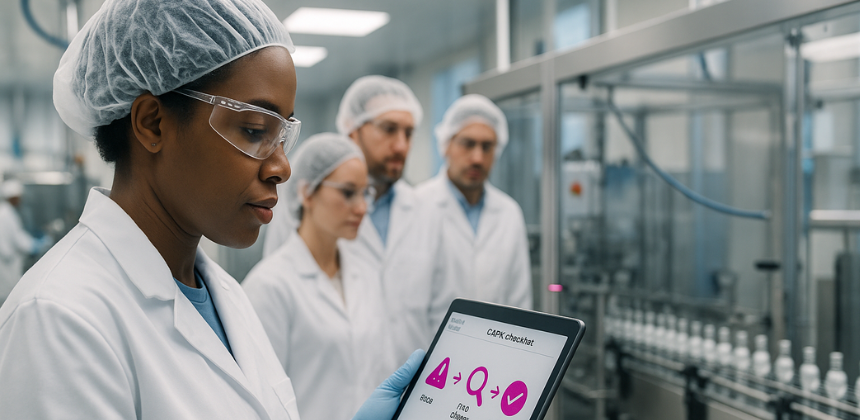
What Is a CAPA Plan? A Beginner’s Guide
This beginner’s guide explains CAPA plans in plain language. You’ll define problems clearly, analyze root causes with proven tools, and turn findings into targeted corrective and preventive actions. Then, you’ll verify effectiveness with metrics and close confidently.

Computerized Maintenance Management: The Complete 2025 Guide
This guide explores computerized maintenance management with practical strategies, CMMS comparisons, and implementation tips. Designed for professionals, entrepreneurs, and job seekers, it helps you choose the right tools, optimize workflows, and boost ROI with preventive and predictive maintenance methods.
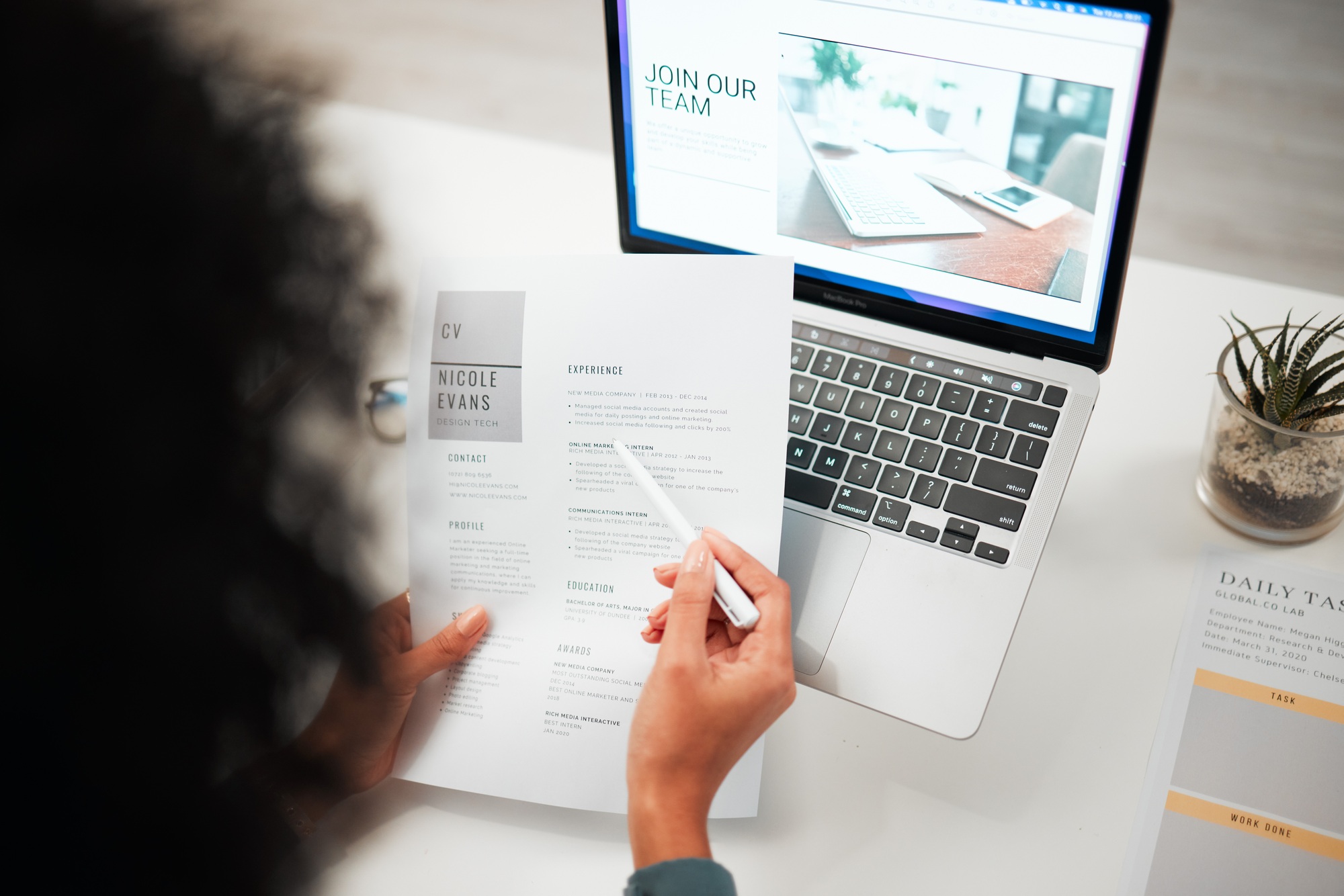
How to Choose the Right Special Skills for Resume Success
Learn how to choose, organize, and present special skills for resume success. This guide includes technical and soft skills, comparison tables, and AI-friendly strategies to pass ATS filters and stand out in competitive job markets.