Welcome to our comprehensive guide on CAPA in Pharmaceutical Manufacturing. In this article, we explore the fundamentals and advanced strategies behind Corrective and Preventive Actions (CAPA) to help pharmaceutical companies maintain quality and compliance. We explain each step in simple language, use active verbs throughout, and guide you with clear lists and structured sections.
You will learn actionable tips, practical techniques, and gain insight into how a robust CAPA process can drive continuous improvement. Let’s dive in and empower your operations with effective CAPA in Pharma.
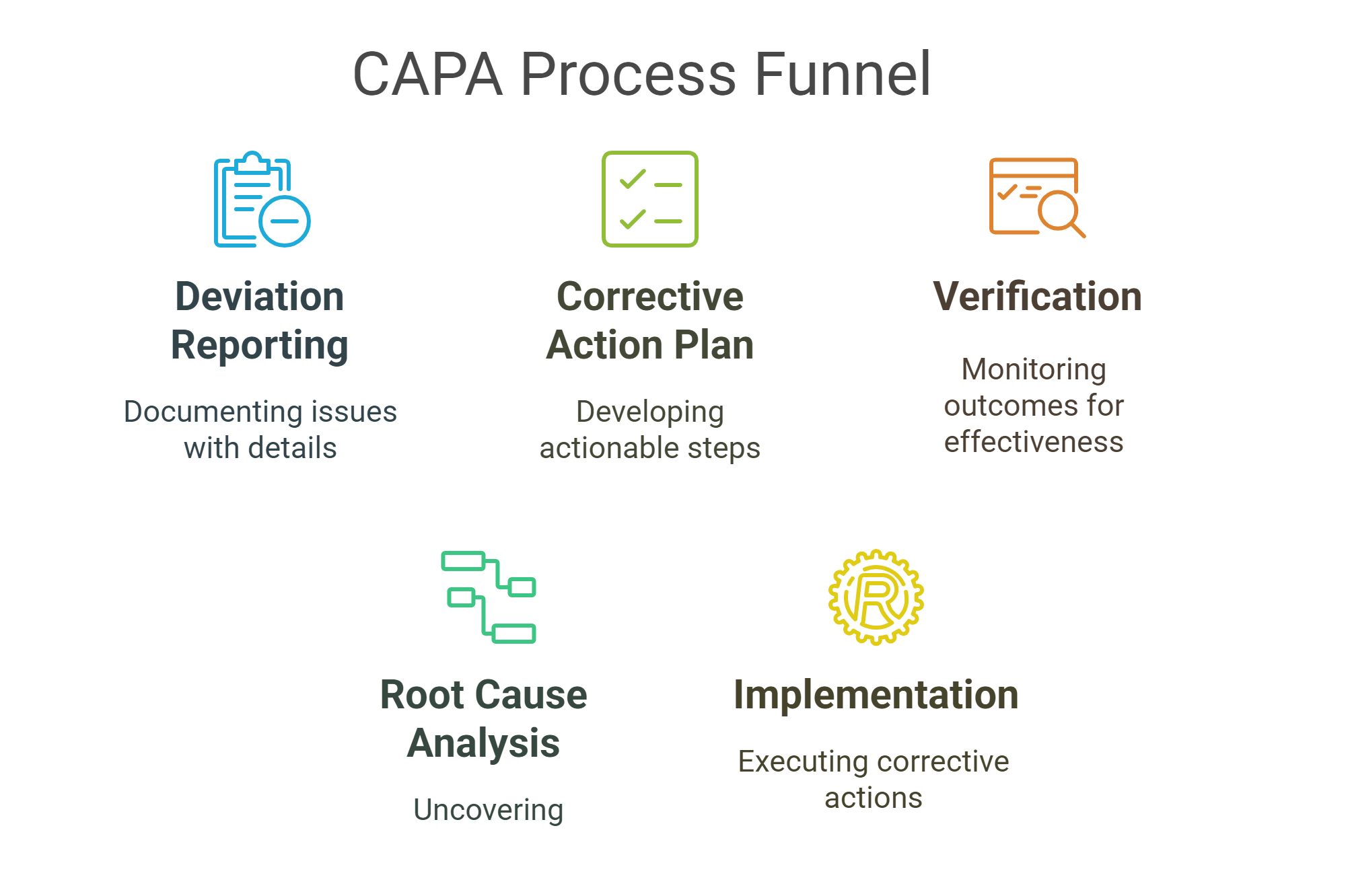
Key Insights on CAPA in Pharma: Driving Quality Improvement
Pharmaceutical companies use CAPA in Pharma to identify and correct process deviations actively. In this section, we outline the core insights that make CAPA a powerful tool for quality improvement.
First, companies must detect nonconformances early and investigate them thoroughly. They collect data, perform root cause analysis, and implement immediate corrective actions that resolve issues. Then, teams create preventive measures to avoid recurring problems and boost overall process reliability. Furthermore, CAPA in Pharma strengthens compliance and fosters a culture of continuous improvement by urging every team member to contribute ideas for process enhancements.
Moreover, managers lead by example and coordinate cross-functional teams, which helps integrate CAPA into daily operations. Additionally, teams use digital tools that streamline documentation and facilitate real-time tracking of CAPA tasks. They use active communication and regular reviews to keep the process transparent. In turn, this proactive approach minimizes risks, reduces waste, and drives operational efficiency.
Finally, the emphasis on solving root causes rather than merely treating symptoms creates lasting quality improvements. In summary, CAPA in Pharma drives meaningful change that enhances both product quality and patient safety.
Sign up for GMP Corrective and Preventive Actions (CAPA) Management Course
Core Components of a CAPA Process
Detection of Deviations
Identify nonconformities swiftly.
Documentation
Record issues clearly and accurately.
Root Cause Analysis
Uncover underlying causes using effective methods.
Corrective Action
Implement solutions that address immediate problems.
Preventive Action
Establish measures to avoid future deviations.
Verification
Monitor outcomes to ensure lasting resolution.
Advanced Strategies for CAPA in Pharma
Enhancing Corrective Actions
Pharmaceutical manufacturers must enhance corrective actions to resolve issues effectively. First, leaders actively assign responsibilities and use data to drive decisions. They perform detailed root cause analysis using tools such as the 5 Whys and fishbone diagrams.
In doing so, teams quickly discover the true source of each deviation and develop targeted solutions. They use clear, concise language and active verbs in every report. Moreover, managers hold regular review meetings to assess progress and validate corrective measures. This collaborative approach minimizes risks and reduces downtime. Furthermore, teams adjust processes dynamically by implementing rapid fixes that deliver immediate improvements. Additionally, they invest in training programs so that staff remain skilled and confident in executing corrective actions. In summary, enhancing corrective actions not only fixes current issues but also builds a resilient quality system that stands up to future challenges.
Moreover, companies use technology to automate corrective workflows, which speeds up the resolution process. They set measurable targets for time-to-resolution and track performance using digital dashboards. In addition, they document every step meticulously to prepare for regulatory audits. This method ensures that each corrective action contributes to a systematic improvement plan.
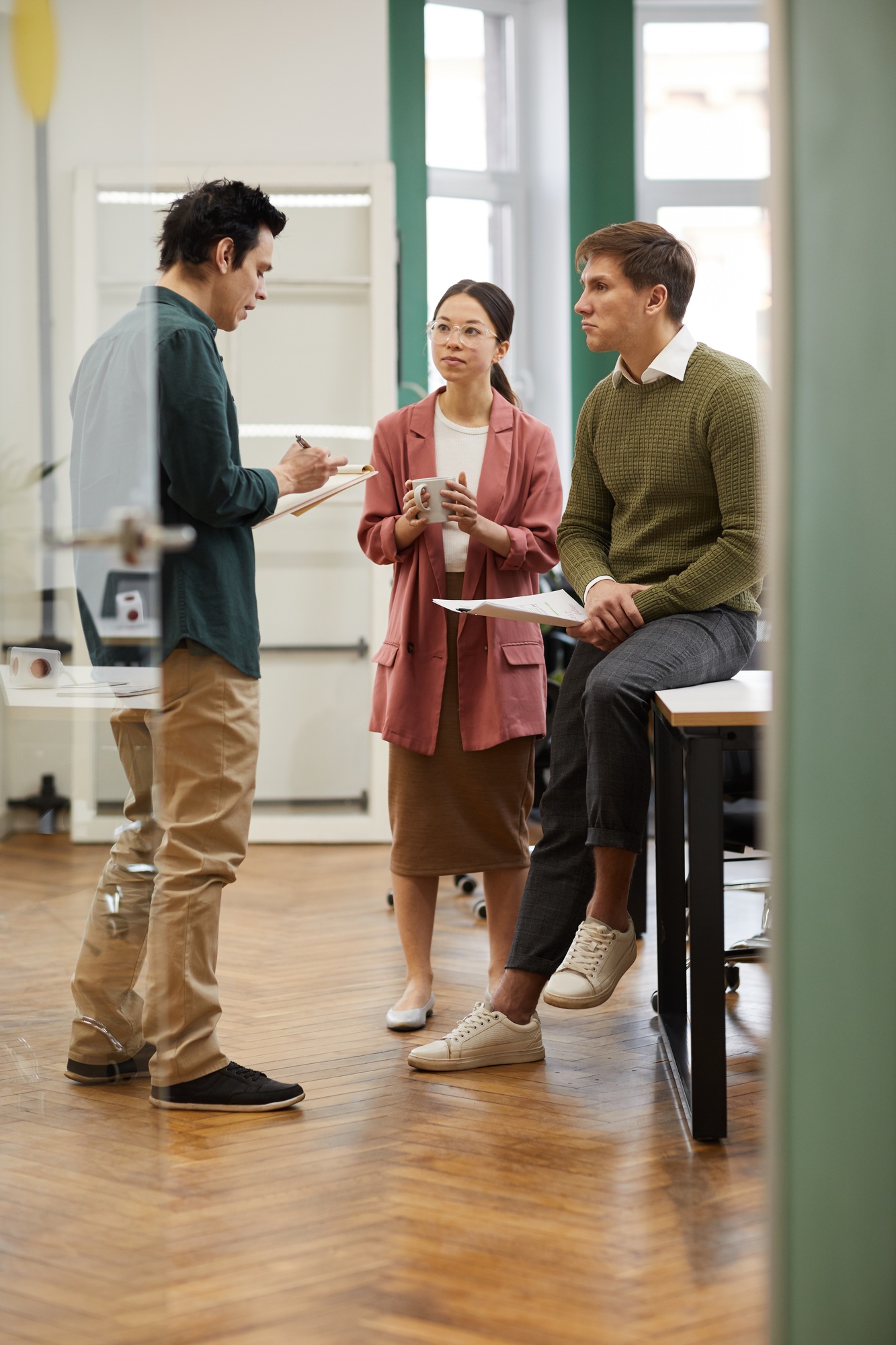
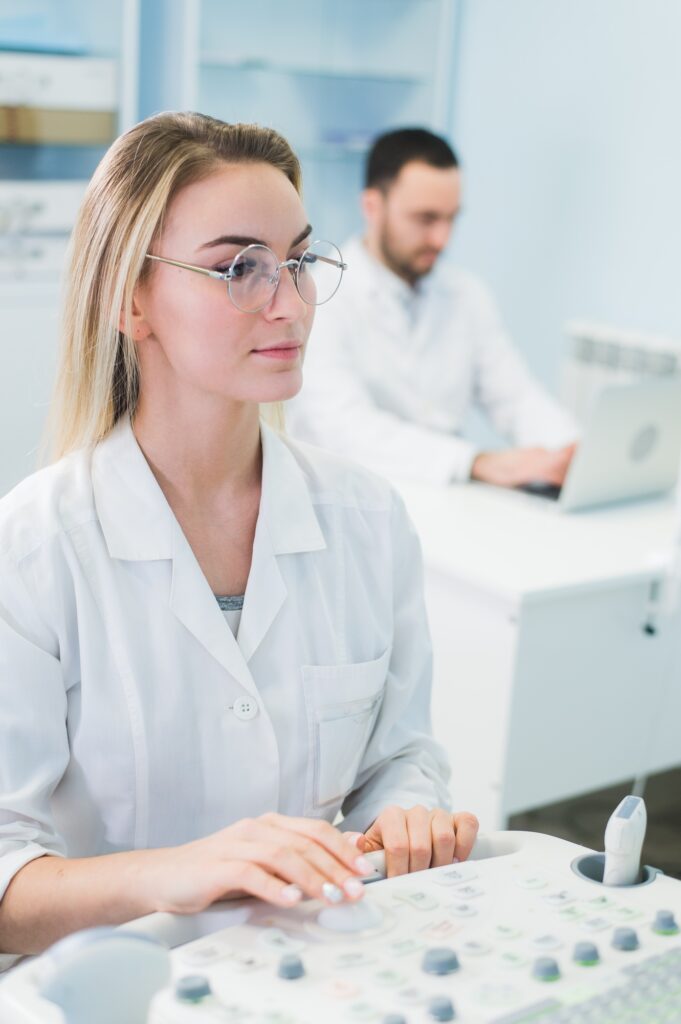
Optimizing Preventive Measures
Pharmaceutical firms must also optimize preventive measures to avert potential issues. Initially, teams analyze historical data to identify recurring problems and potential risks. They then design process improvements that mitigate these risks and incorporate preventive controls into standard operating procedures. Furthermore, cross-functional teams collaborate to brainstorm proactive solutions that enhance quality.
They actively share ideas and adopt a forward-thinking approach. In addition, organizations integrate preventive measures with regular training programs to keep employees updated on best practices and regulatory changes. Moreover, the use of automation tools and CAPA management software facilitates real-time monitoring and early detection of issues. This proactive stance minimizes disruption and enhances overall process stability.
Additionally, companies align preventive actions with strategic business goals. They measure the effectiveness of these actions through key performance indicators and adjust processes based on performance data. In doing so, they reinforce a culture of continuous improvement and risk management. Furthermore, preventive measures support regulatory compliance and help companies stay audit-ready. Finally, optimizing preventive actions ensures that quality remains embedded in every stage of pharmaceutical manufacturing, thus safeguarding both patients and product integrity.
Essential Tools for CAPA in Pharma Process
CAPA Management Software
Automates documentation and tracking tasks.
It streamlines workflows and reduces manual errors.
Root Cause Analysis Tools
Include Fishbone Diagrams and 5 Whys techniques.
They help teams pinpoint underlying issues quickly.
Digital Dashboards
Offer real-time data monitoring.
They enable managers to track corrective actions effectively.
Automated Reporting Systems
Generate compliance reports on schedule.
They simplify audits and regulatory reviews.
Training Platforms
Provide up-to-date CAPA training modules.
They enhance staff competence and ensure continuous improvement.
Implementing CAPA in Pharma: Best Practices for Long-Term Success
Building a Quality Culture
Pharmaceutical companies must embed CAPA in Pharma into their organizational culture. First, executives set clear quality goals and lead by example. They actively promote accountability and encourage every employee to share feedback. Moreover, companies conduct regular training sessions so staff learn to identify nonconformances and execute CAPA processes confidently.
In addition, they invest in modern technology to streamline CAPA workflows and support proactive quality management. This approach empowers teams to address issues promptly, reduce downtime, and increase product safety. Furthermore, clear communication channels ensure that every department remains aligned with the CAPA strategy. Managers hold periodic reviews to assess CAPA effectiveness, which fosters continuous improvement. Finally, companies celebrate successes and learn from failures to reinforce a robust quality culture.
Moreover, the integration of CAPA practices into daily routines drives sustainable success. Employees follow standard operating procedures and report deviations without hesitation. This transparent approach builds trust among team members and regulatory bodies alike. In summary, building a quality culture through CAPA in Pharma empowers organizations to maintain high standards and achieve long-term operational excellence.
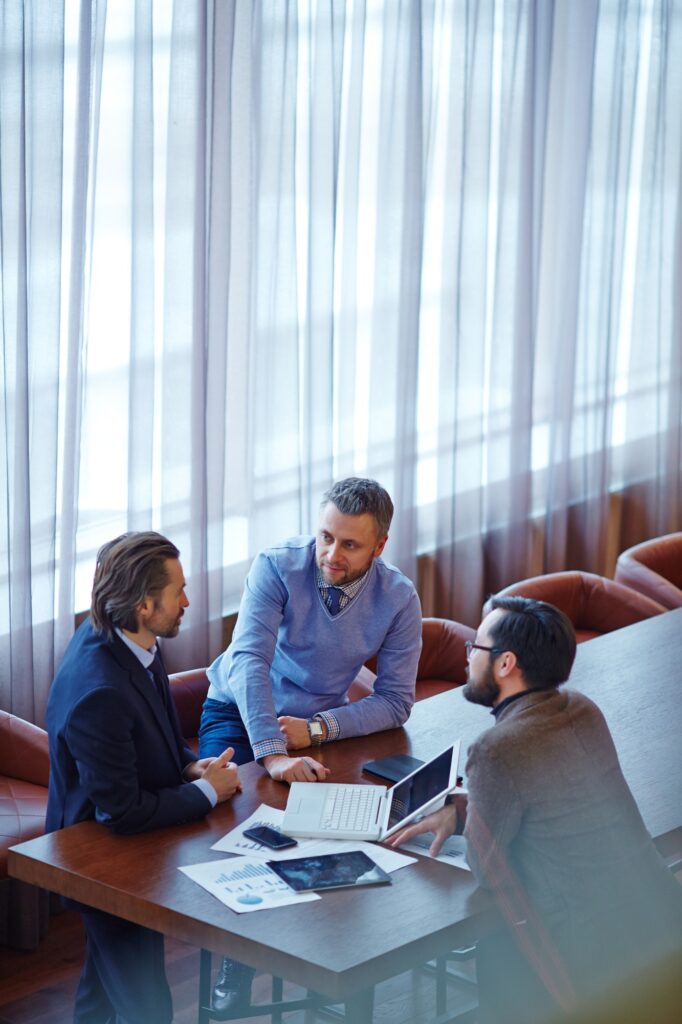
Driving Continuous Improvement
Companies must drive continuous improvement by using CAPA strategically. First, they conduct periodic audits to assess CAPA performance and identify trends.
They then use the insights to refine their processes, enhance training programs, and adjust preventive measures accordingly. Additionally, they track key performance indicators such as CAPA closure rates and deviation reductions.
This data-driven approach enables them to make informed decisions. Moreover, by sharing success stories and lessons learned, organizations foster collaboration and motivate teams to embrace quality initiatives.
In addition, they continuously update CAPA protocols to reflect regulatory changes and industry best practices. Finally, by incorporating employee feedback and using advanced digital tools, companies achieve a dynamic, responsive quality system that adapts to evolving challenges.
Furthermore, a commitment to continuous improvement ensures that CAPA becomes an integral part of the company’s DNA. Organizations that invest in these strategies enjoy improved product quality, enhanced regulatory compliance, and reduced operational risks. In essence, continuous improvement drives competitive advantage and safeguards public health while ensuring operational success.
Sustainable CAPA in Pharma: The Road Ahead
Pharmaceutical manufacturers face an evolving regulatory landscape and increased market pressures. In response, CAPA in Pharma is adapting through innovative digital transformation and smarter quality management practices. Companies are now integrating artificial intelligence and machine learning into CAPA management software to predict potential nonconformances before they occur. These digital tools analyze vast datasets and generate actionable insights, which empower quality teams to make proactive decisions.
Moreover, cloud-based systems streamline documentation and enable real-time monitoring, reducing manual errors and ensuring prompt corrective actions.
Furthermore, organizations emphasize data-driven decision making to enhance CAPA effectiveness. They collect and analyze performance metrics, such as deviation trends and CAPA closure rates, to measure process improvements continuously.
Additionally, regulatory bodies encourage the adoption of digital solutions that improve traceability and transparency in CAPA processes. In parallel, training programs now incorporate virtual simulations and interactive modules that make learning about CAPA engaging and effective. Manufacturers also collaborate more closely with technology providers to tailor CAPA solutions that fit their specific needs.
Moreover, the shift toward a more proactive quality culture drives innovation in CAPA practices. Companies are leveraging real-time analytics to identify subtle patterns that may indicate emerging quality issues.
This forward-looking approach not only minimizes risks but also optimizes resource allocation and enhances overall productivity. In summary, future trends in CAPA in Pharma signal a transition from reactive troubleshooting to a dynamic, preventive quality management paradigm that ensures long-term compliance and operational excellence.
Pitfalls and Solutions for CAPA in Pharma
Inadequate Root Cause Analysis
Teams often stop at surface issues. They must use comprehensive RCA techniques to uncover true causes.
Delayed Implementation
Slow corrective actions increase risks. Teams should set strict deadlines and monitor progress.
Poor Documentation
Incomplete records hinder compliance. Companies need to maintain detailed and clear documentation.
Resistance to Change
Employees may hesitate to adopt new processes. Organizations must foster open communication and provide regular training.
Inefficient Collaboration
Siloed departments can slow CAPA progress. Cross-functional teamwork and clear role definitions can resolve this challenge.
Conclusion
In conclusion, this ultimate guide has provided a deep dive into CAPA in Pharmaceutical Manufacturing. We explored the core insights, advanced strategies, essential tools, and best practices needed to build a robust CAPA system.
Throughout this guide, we learned how to implement corrective and preventive actions, conduct thorough root cause analysis, and leverage digital tools to drive continuous improvement. Moreover, we examined common challenges and emerging trends that shape the future of CAPA. By adopting these proactive strategies, pharmaceutical companies can improve quality, ensure compliance, and safeguard patient safety.
Embrace CAPA in Pharma to build a culture of excellence, reduce operational risks, and secure long-term success in a highly regulated industry.
References
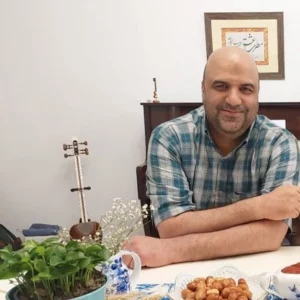
Ershad Moradi
Ershad Moradi, a Content Marketing Specialist at Zamann Pharma Support, brings 6 years of experience in the pharmaceutical industry. Specializing in pharmaceutical and medical technologies, Ershad is currently focused on expanding his knowledge in marketing and improving communication in the field. Outside of work, Ershad enjoys reading and attending industry related networks to stay up-to-date on the latest advancements. With a passion for continuous learning and growth, Ershad is always looking for new opportunities to enhance his skills and contribute to pharmaceutical industry. Connect with Ershad on Facebook for more information.
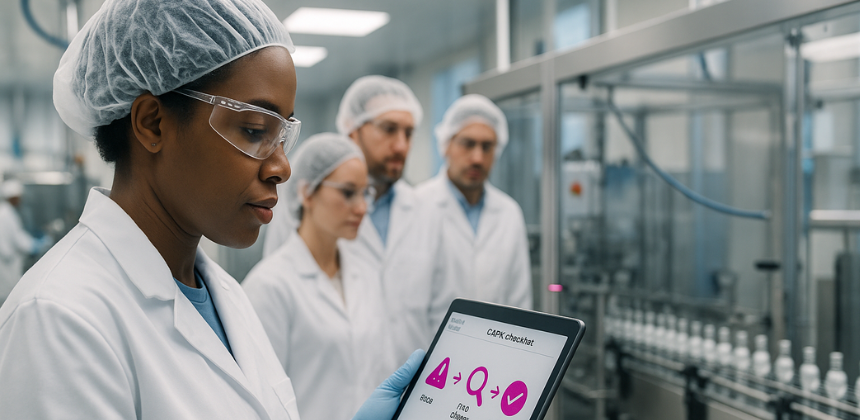
What Is a CAPA Plan? A Beginner’s Guide
This beginner’s guide explains CAPA plans in plain language. You’ll define problems clearly, analyze root causes with proven tools, and turn findings into targeted corrective and preventive actions. Then, you’ll verify effectiveness with metrics and close confidently.

Computerized Maintenance Management: The Complete 2025 Guide
This guide explores computerized maintenance management with practical strategies, CMMS comparisons, and implementation tips. Designed for professionals, entrepreneurs, and job seekers, it helps you choose the right tools, optimize workflows, and boost ROI with preventive and predictive maintenance methods.
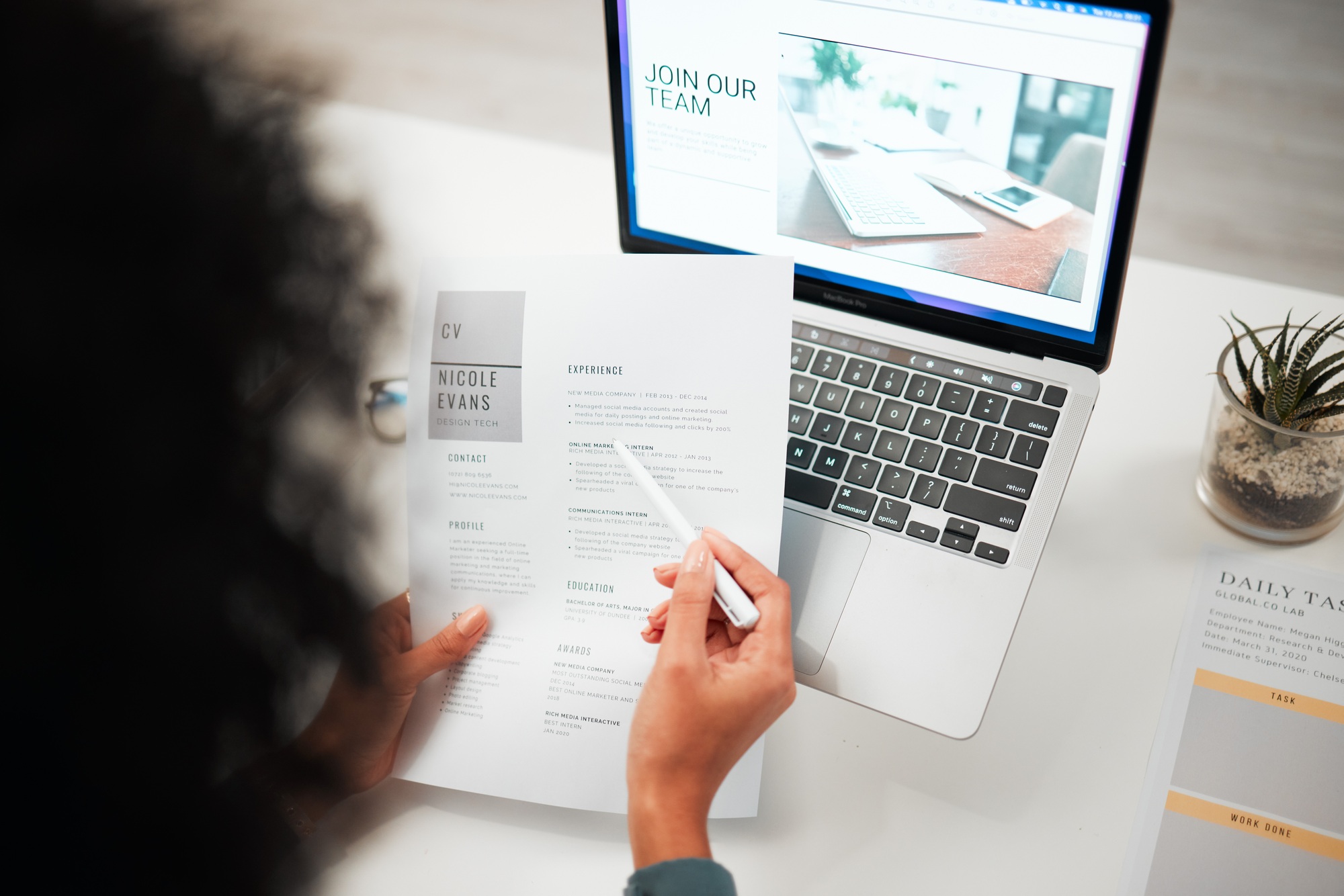
How to Choose the Right Special Skills for Resume Success
Learn how to choose, organize, and present special skills for resume success. This guide includes technical and soft skills, comparison tables, and AI-friendly strategies to pass ATS filters and stand out in competitive job markets.