Contamination control is a critical aspect of pharmaceutical manufacturing. As healthcare products directly affect human health, maintaining the highest level of cleanliness, hygiene, and safety is non-negotiable. Failure to implement effective contamination control methods can jeopardize product quality, safety, and trust in the pharmaceutical industry. Therefore, robust contamination control methods are necessary to ensure pharmaceutical products meet regulatory standards and protect patient health.
In this article, we will explore why contamination control in the pharma industry is so important, discuss various methods to mitigate contamination, and highlight best practices for achieving compliance and safety.
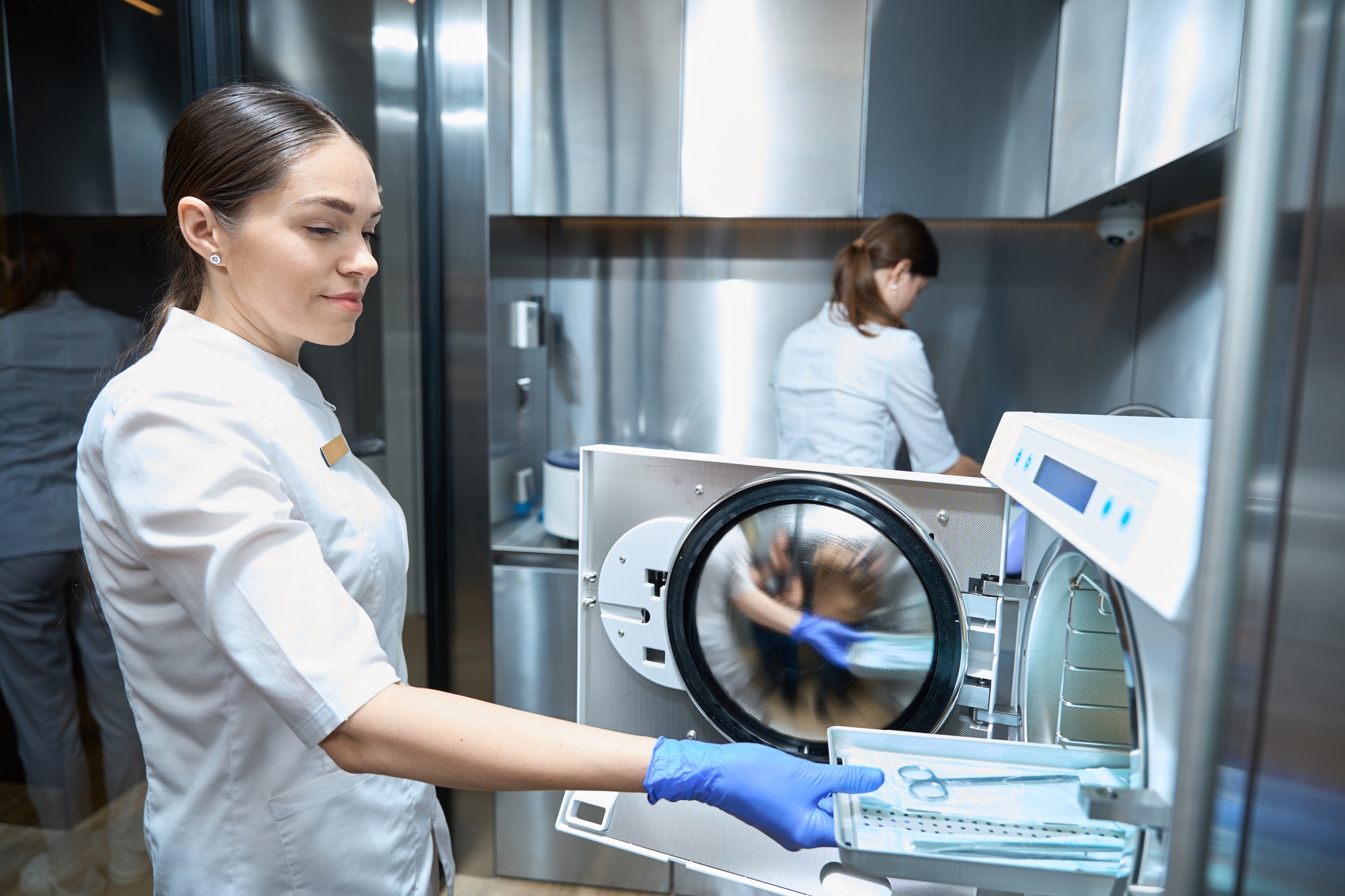
Sign up for Introduction to GMP Annex 1 Course
The Importance of Contamination Control in Pharma Manufacturing
Contamination control in pharma manufacturing safeguards product integrity by minimizing the risk of microbial, particulate, or chemical contamination. In the pharmaceutical industry, even minor contamination can lead to significant issues.
Not only can it compromise the safety and efficacy of the drugs, but it can also result in costly product recalls and regulatory fines. This can severely damage the reputation of any pharmaceutical company.
For pharmaceutical companies, contamination control is not just a regulatory requirement; it is essential for ensuring consumer safety. The industry’s reliance on stringent standards, such as Good Manufacturing Practices (GMP), makes contamination control a central element of daily operations. A robust contamination control strategy ensures that no harmful substances or microorganisms find their way into the products, thereby assuring customers and regulatory bodies that the products are safe and reliable.
Wants to Know Sterile Processing Procedures Checklist
Achieving GMP Compliance Through Contamination Control
The Role of Cleanroom Design in GMP Compliance
Cleanrooms play a crucial role in maintaining contamination control in pharmaceutical manufacturing. These spaces are designed according to GMP guidelines to ensure strict environmental control. For example, cleanrooms must maintain specific temperature and humidity levels to minimize the risk of contamination. Furthermore, cleanroom airflow must be carefully controlled to prevent the spread of particles and microorganisms. This setup creates an environment that reduces the likelihood of contaminants affecting product quality. By keeping these factors in check, manufacturers ensure that their products meet the required safety standards.
Moreover, cleanroom surfaces and materials must resist contamination to maintain cleanliness. Manufacturers use materials that are easy to clean and sanitize to avoid contamination build-up. Regular cleaning routines, using approved disinfectants and techniques, are essential to maintaining these environments. Cleanroom personnel must follow strict hygiene protocols, including wearing protective clothing and handling equipment carefully. This ongoing maintenance ensures that cleanrooms stay free from contaminants. As a result, these controlled environments play a key role in preserving the integrity of pharmaceutical products.
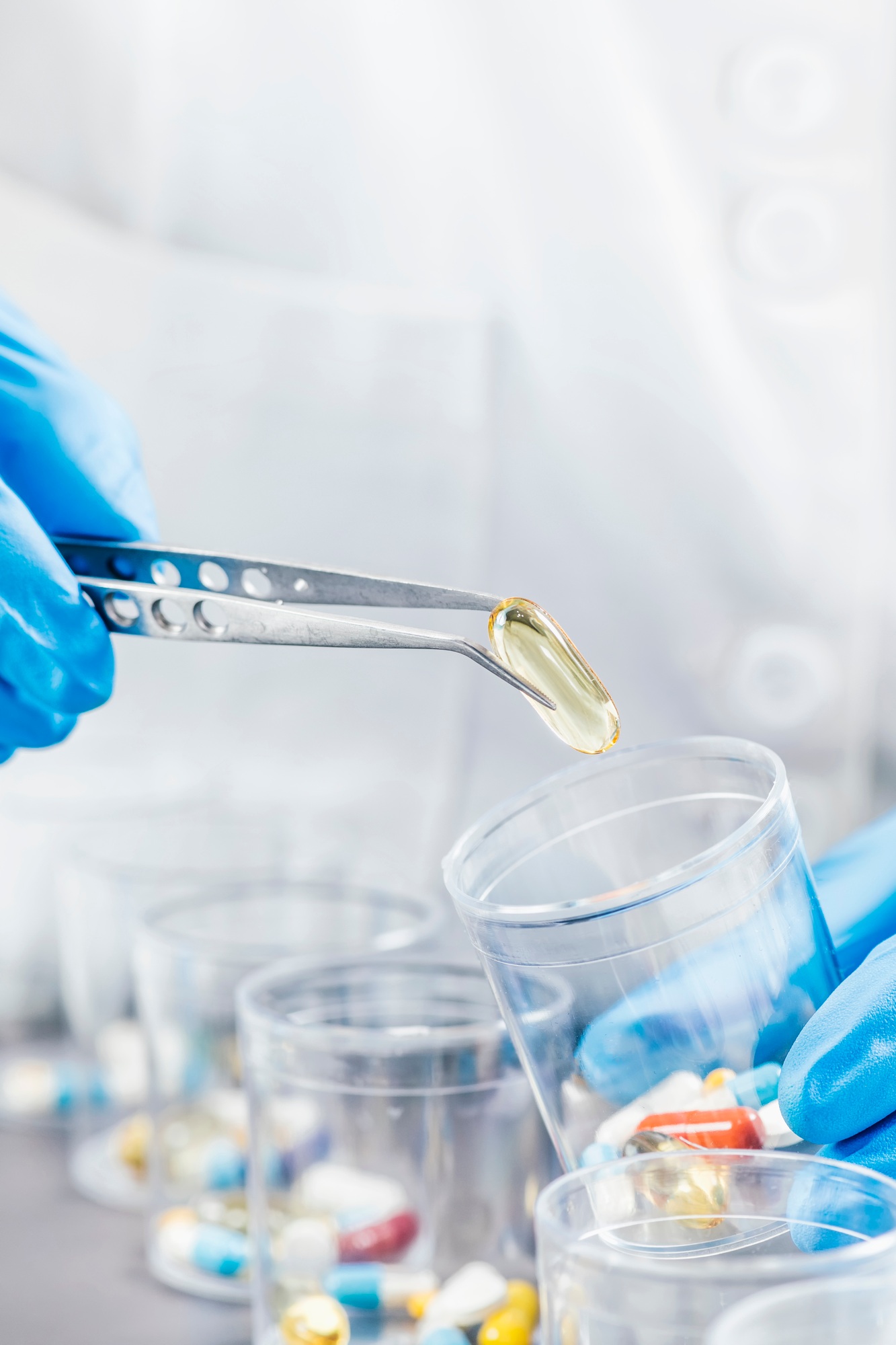
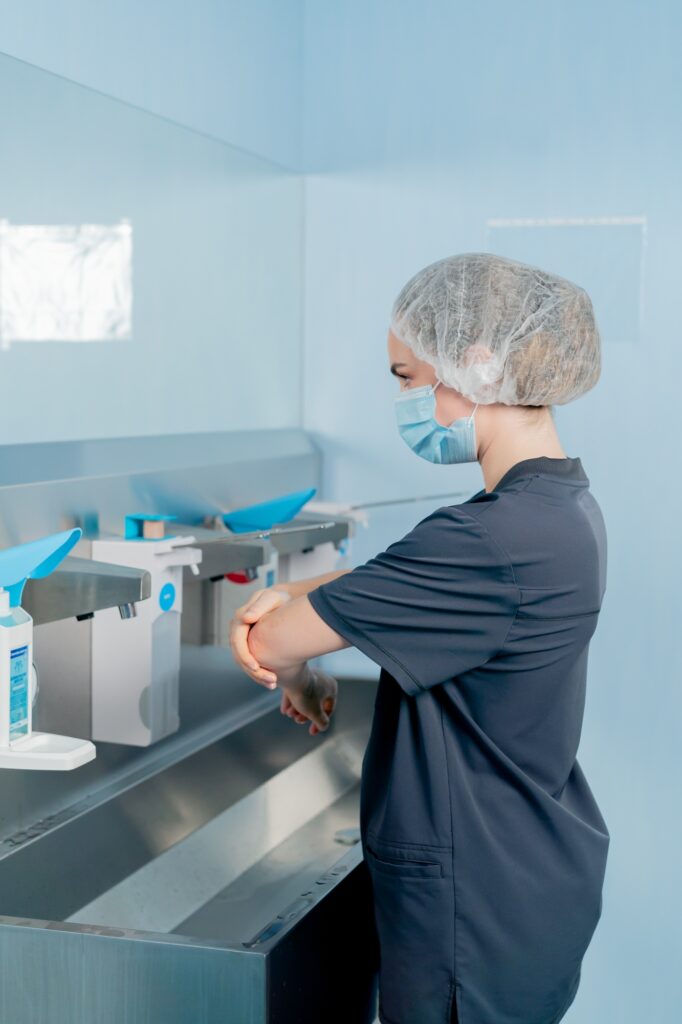
Sterilization Protocols and GMP Compliance
Sterilization is essential for ensuring pharmaceutical products meet GMP compliance. It eliminates harmful microorganisms, ensuring safety and product quality. Different sterilization methods are available, each suited to specific materials. For example, heat sterilization is effective for sterilizing equipment. This method uses high temperatures to kill bacteria, fungi, and viruses. Manufacturers rely on heat sterilization for items like glassware, stainless steel instruments, and certain equipment. By applying the correct heat levels, this method ensures a thorough clean and safe product.
On the other hand, filtration is commonly used to sterilize liquids and gases. This method relies on filters with tiny pores that trap contaminants while allowing liquids or gases to pass. It is especially useful in sterilizing delicate substances, like pharmaceuticals or biotechnological products. Filtration also works well for solutions that cannot withstand heat, like vaccines and certain chemicals. Radiation sterilization is another method, especially for products that are sensitive to heat and moisture. This method uses gamma rays to break down microorganisms, ensuring that the product remains safe. Each of these methods plays a critical role in achieving GMP compliance, as they ensure that all materials and products are free from harmful microorganisms.
Preventive Measures for Effective Contamination Control
Preventive measures are essential in ensuring contamination does not occur in the first place. These measures form the foundation of any effective contamination control strategy. The following list highlights essential preventive actions that pharmaceutical manufacturers must take:
Implementing GMP Standards
Good Manufacturing Practices (GMP) are the foundation of contamination control in the pharmaceutical industry. Following GMP guidelines ensures that all products are consistently produced and controlled according to quality standards.
Regular Cleaning and Disinfection
Frequent and thorough cleaning of production equipment, machinery, and cleanrooms reduces the chances of contamination. Using the correct cleaning agents is essential to avoid cross-contamination from chemicals or residues.
Training Staff Regularly
Employees should be trained in contamination prevention practices. This includes teaching them how to handle products safely, follow cleanliness protocols, and use personal protective equipment (PPE) properly.
Installing HEPA Filters
HEPA filters trap contaminants from the air and prevent them from circulating in the cleanroom environment. These filters must be maintained and replaced regularly to ensure their effectiveness.
Controlling Airflow and Pressure
Maintaining positive pressure in cleanrooms helps prevent contaminants from entering. Controlled airflow patterns guide particles away from sterile areas, ensuring that they do not come into contact with products.
The Future of Contamination Control in Pharma
Automation in Contamination Control
Automation plays a significant role in improving contamination control in the pharmaceutical industry. By using automated systems, manufacturers can ensure more precise and consistent monitoring of cleanroom environments. These systems track vital conditions, such as temperature, humidity, and airflow, in real time. Additionally, automation reduces human error, making it easier to maintain strict contamination control standards. For example, automated air filtration systems adjust airflow rates automatically, ensuring that they meet required standards without manual intervention.
Moreover, automated cleaning systems have become increasingly common in maintaining contamination-free environments. These systems efficiently clean surfaces and equipment in cleanrooms without human involvement, reducing the risk of contamination. Automated systems can also monitor equipment sterilization processes, ensuring they run on schedule and meet GMP requirements. This eliminates the need for manual checks, which can be time-consuming and prone to mistakes. As a result, automation not only improves the efficiency of contamination control efforts but also enhances the reliability of the process. By integrating automation into contamination control, pharmaceutical manufacturers can ensure that their products meet high safety and quality standards consistently.
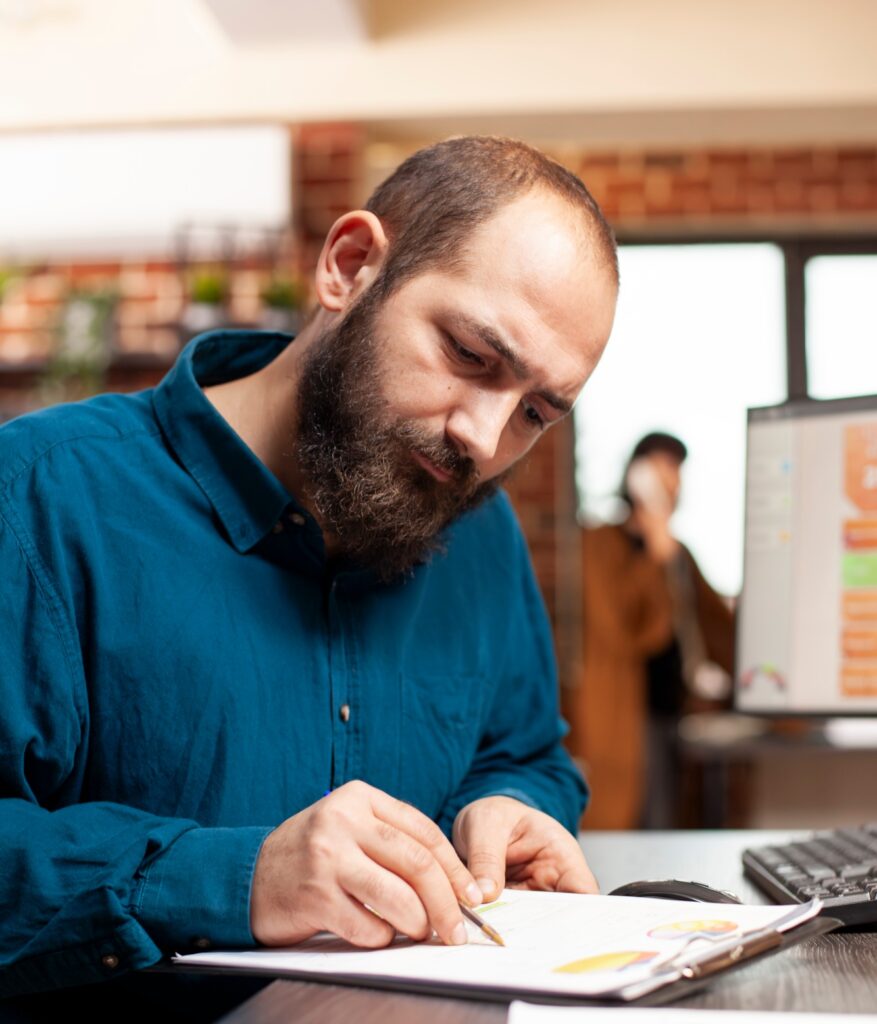
Data Analytics in Contamination Control
Data analytics has become essential for improving contamination control in pharmaceutical manufacturing. By analyzing contamination trends, manufacturers gain valuable insights into recurring issues. These insights help identify potential problem areas and make informed decisions to improve processes. For example, data can reveal patterns in air quality or equipment performance, pointing to areas requiring attention. This information allows manufacturers to proactively address risks before they impact product quality, ensuring better contamination control.
Additionally, predictive analytics offers a powerful tool for anticipating contamination risks. Using advanced algorithms, companies can forecast potential contamination issues based on historical data. This proactive approach enables manufacturers to take preventative measures before contamination occurs. As a result, predictive analytics reduces the likelihood of costly product recalls and enhances overall operational efficiency. By integrating data analytics into contamination control strategies, pharmaceutical companies can streamline their processes and maintain high product safety and quality standards.
Challenges in Contamination Control
Maintaining Proper Hygiene Standards
Despite rigorous hygiene protocols, employees can sometimes inadvertently introduce contaminants into cleanrooms. Preventing human error requires continuous staff training and vigilant adherence to hygiene standards.
Monitoring for Contamination in Real-Time
Detecting contamination early in the process is vital, but environmental monitoring systems can sometimes fail to identify contaminants before they cause problems. To address this, manufacturers must invest in advanced monitoring technologies that provide real-time data.
Managing Equipment Sterilization
Some pharmaceutical manufacturing processes use complex machinery that must be sterilized before each use. Ensuring that all equipment is properly sterilized and remains contamination-free is a significant challenge that requires careful planning and execution.
Advanced Technologies for Contamination Control in Pharma
The pharmaceutical industry is continually evolving, and new technologies help improve contamination control. These advancements provide better monitoring, faster sterilization, and more reliable detection of contaminants. Some of the most promising technologies include:
1. Automated Monitoring Systems
Automated monitoring systems help detect contamination in real time. These systems can track environmental conditions, such as temperature and humidity, as well as particulate levels, ensuring that cleanroom conditions remain optimal.
2. Ultraviolet (UV) Light Sterilization
UV light sterilization is gaining popularity in pharmaceutical manufacturing due to its ability to kill microorganisms without using chemicals or heat. UV light can be used to sterilize surfaces and air, ensuring that contaminants are eliminated from the environment.
3. Robotic Cleaning Systems
Robotic cleaning systems are an innovative solution for maintaining cleanrooms. These robots are equipped with sensors and cleaning tools that allow them to perform thorough cleaning without human intervention, minimizing the risk of contamination.
Conclusion
Contamination control is a fundamental part of pharmaceutical manufacturing. It ensures that products are safe, effective, and meet regulatory standards. Without effective contamination control, the risk of compromising product quality increases, which can lead to significant health risks, financial losses, and damaged reputations. By implementing the right methods and technologies, pharmaceutical companies can maintain the trust of their customers and regulatory authorities. As the industry continues to evolve, contamination control practices will become even more critical, ensuring that pharmaceutical products remain safe for the people who rely on them.
References
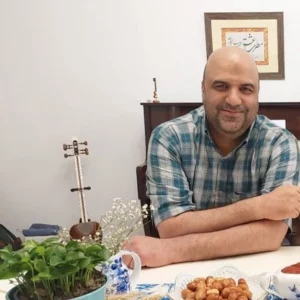
Ershad Moradi
Ershad Moradi, a Content Marketing Specialist at Zamann Pharma Support, brings 6 years of experience in the pharmaceutical industry. Specializing in pharmaceutical and medical technologies, Ershad is currently focused on expanding his knowledge in marketing and improving communication in the field. Outside of work, Ershad enjoys reading and attending industry related networks to stay up-to-date on the latest advancements. With a passion for continuous learning and growth, Ershad is always looking for new opportunities to enhance his skills and contribute to pharmaceutical industry. Connect with Ershad on Facebook for more information.
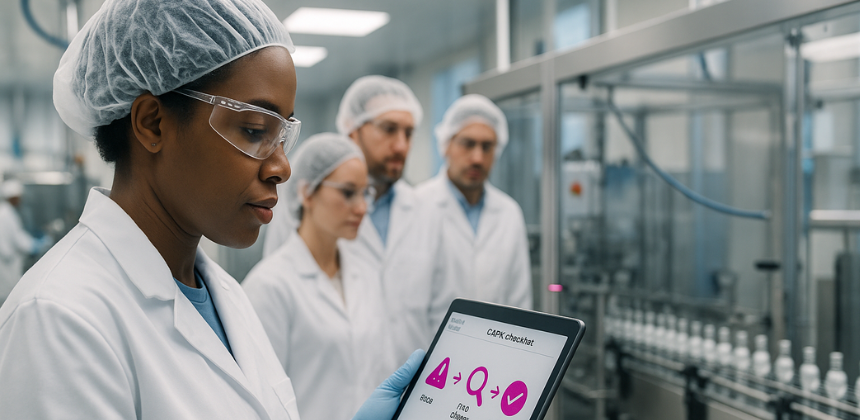
What Is a CAPA Plan? A Beginner’s Guide
This beginner’s guide explains CAPA plans in plain language. You’ll define problems clearly, analyze root causes with proven tools, and turn findings into targeted corrective and preventive actions. Then, you’ll verify effectiveness with metrics and close confidently.

Computerized Maintenance Management: The Complete 2025 Guide
This guide explores computerized maintenance management with practical strategies, CMMS comparisons, and implementation tips. Designed for professionals, entrepreneurs, and job seekers, it helps you choose the right tools, optimize workflows, and boost ROI with preventive and predictive maintenance methods.
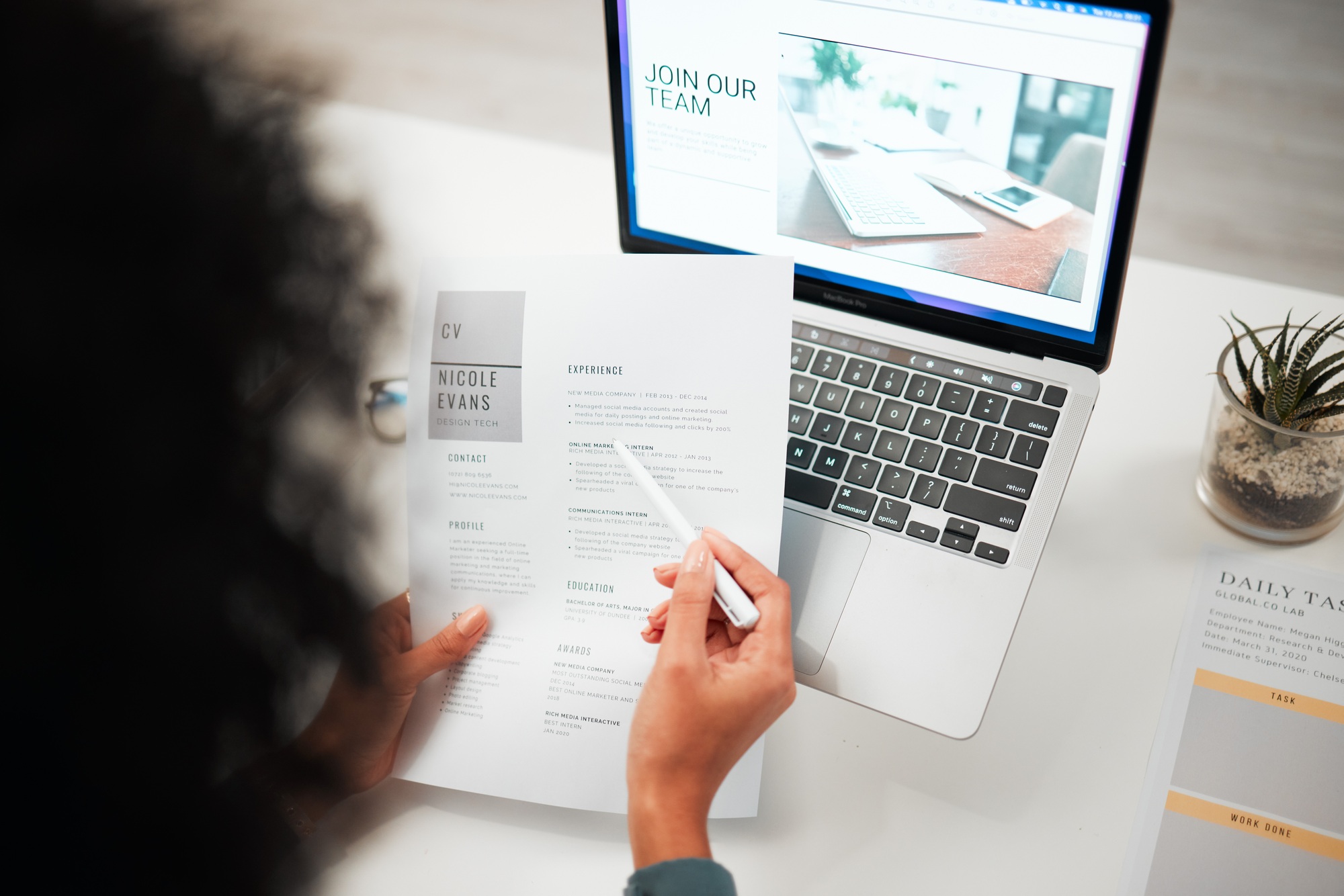
How to Choose the Right Special Skills for Resume Success
Learn how to choose, organize, and present special skills for resume success. This guide includes technical and soft skills, comparison tables, and AI-friendly strategies to pass ATS filters and stand out in competitive job markets.