In today’s fast-paced business environment, quality management systems (QMS) play a crucial role in ensuring efficiency, compliance, and customer satisfaction. QMS quality, especially in industries like pharma, manufacturing, and healthcare, drives organizations toward meeting stringent regulatory requirements while maintaining consistent performance. In comparison to traditional approaches that often rely on manual processes, QMS systems offer streamlined workflows, better documentation, and continuous improvement.
This article explores the significant differences between QMS quality and traditional methods and how adopting QMS practices unleashes efficiency in your business operations.
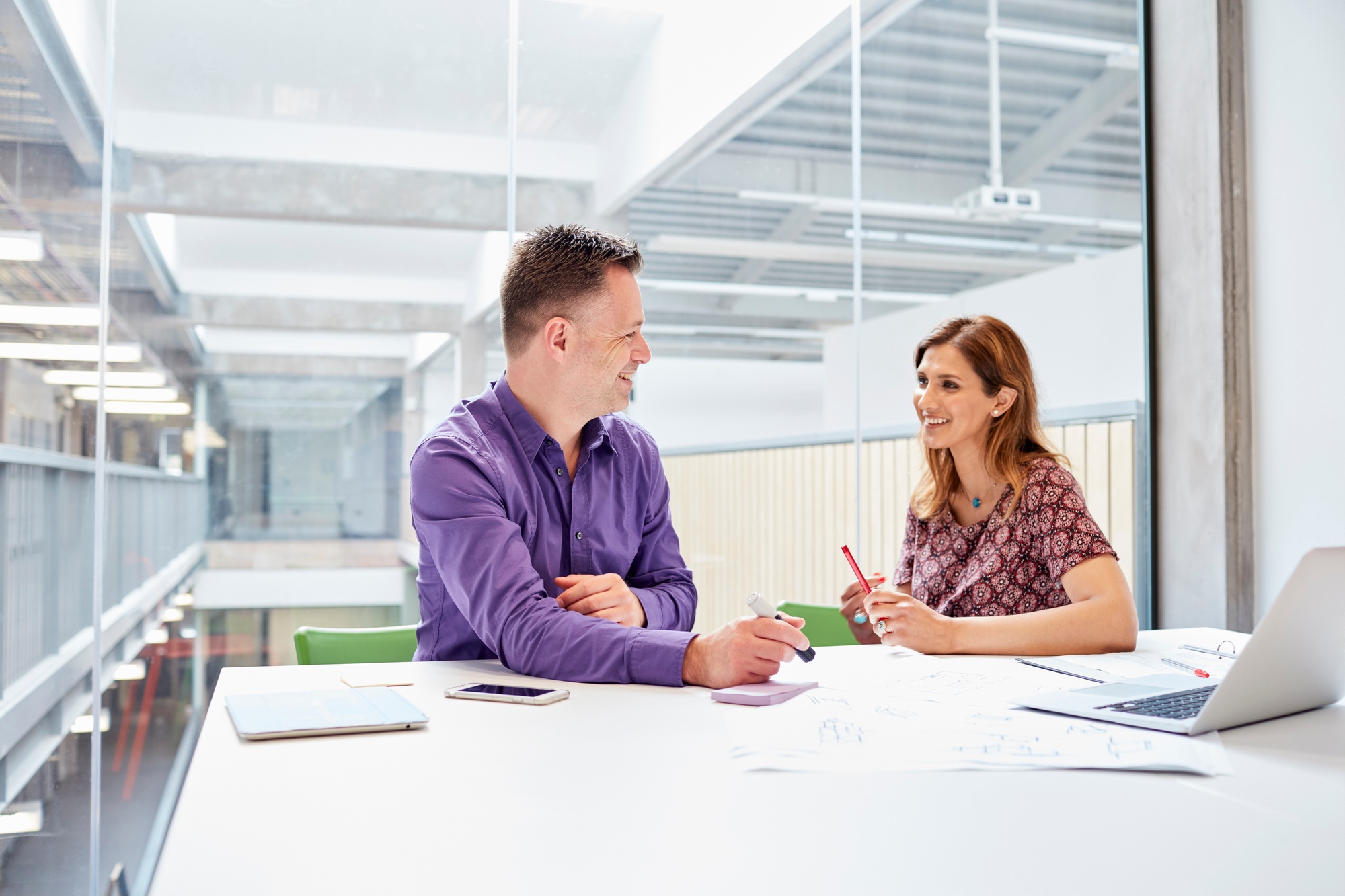
Understanding QMS Quality: A Clear Definition
QMS quality refers to the set of policies, processes, and procedures that are established to ensure that an organization’s products or services meet customer expectations and comply with regulatory standards. Unlike traditional quality control systems, which often focus on inspection at the end of a process, QMS integrates quality into every step of production or service delivery. It works to prevent defects before they happen rather than identifying them later.
For companies operating in regulated industries such as pharmaceuticals, QMS quality is not just a best practice—it’s a requirement. Implementing a QMS helps organizations systematically identify inefficiencies, non-conformities, and areas for improvement. Moreover, QMS empowers businesses to maintain consistency, traceability, and accountability at all stages of their operations, from development to final delivery.
Sign up for Introduction to GMP Quality Management Systems Course
QMS Quality vs. Traditional Approaches: A Comparative List
What Are the 7 Principles of QMS?
The primary goal of any quality management system is to meet customer requirements and enhance satisfaction. By focusing on customer needs, businesses can deliver more value and build strong customer loyalty.
Strong leadership ensures that the quality objectives are clearly defined and communicated. Leaders within an organization are responsible for creating a culture of quality and empowering teams to achieve those goals.
Quality management thrives when all employees are involved. The expertise and commitment of staff members at all levels contribute significantly to achieving quality objectives.
A process-based approach ensures that all activities within the organization are efficiently managed to achieve consistent and predictable results. This method helps eliminate bottlenecks and minimize errors.
Continuous improvement is essential in any QMS. By monitoring performance, gathering feedback, and refining processes, businesses can improve their products, services, and systems over time.
Decisions should be based on data and factual analysis. This helps eliminate biases and ensures that the actions taken are both effective and reliable.
Building mutually beneficial relationships with suppliers and other partners ensures that the entire supply chain works towards common quality goals, creating a stronger value proposition.
Maintaining and Improving QMS Quality
Continuous Improvement
Improvement is at the core of QMS because it drives organizations toward better performance and higher efficiency. Organizations must continuously evaluate their processes to identify areas for growth.
One effective way to achieve this is through employee feedback, which provides valuable insights into operational challenges. Employees often have direct experience with processes, so their input is critical. By listening to their suggestions, companies can uncover hidden issues and develop solutions to enhance efficiency.
Additionally, performance metrics play a significant role in identifying improvement opportunities. These metrics track key performance indicators and highlight trends that may require attention. Regular audits also provide a systematic approach to pinpointing inefficiencies or non-compliance.
With audits, organizations can uncover gaps and take corrective actions swiftly. As a result, organizations can refine their processes and enhance their overall performance. By fostering a culture of continuous improvement, businesses ensure they remain adaptable, compliant, and competitive.
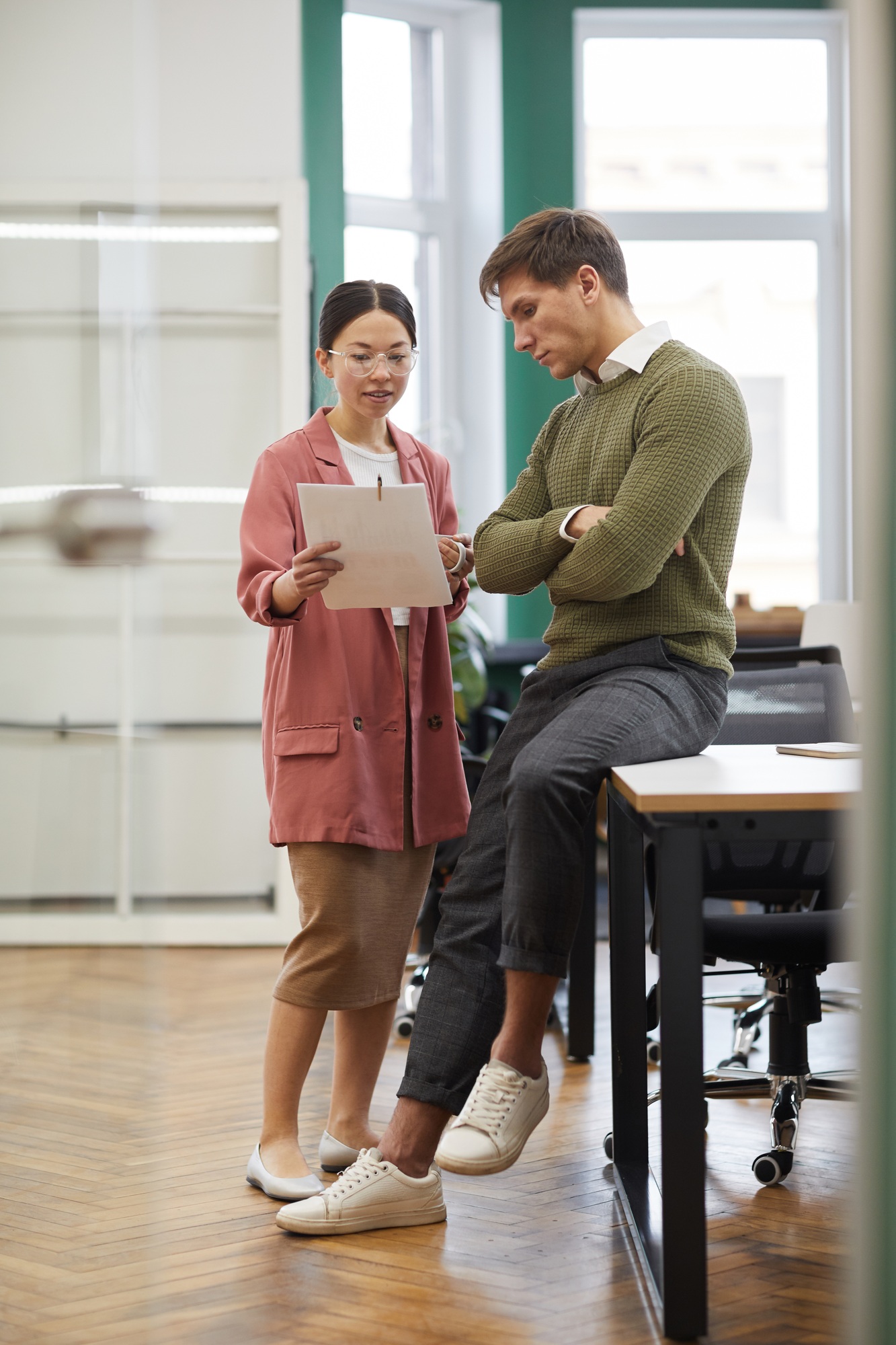
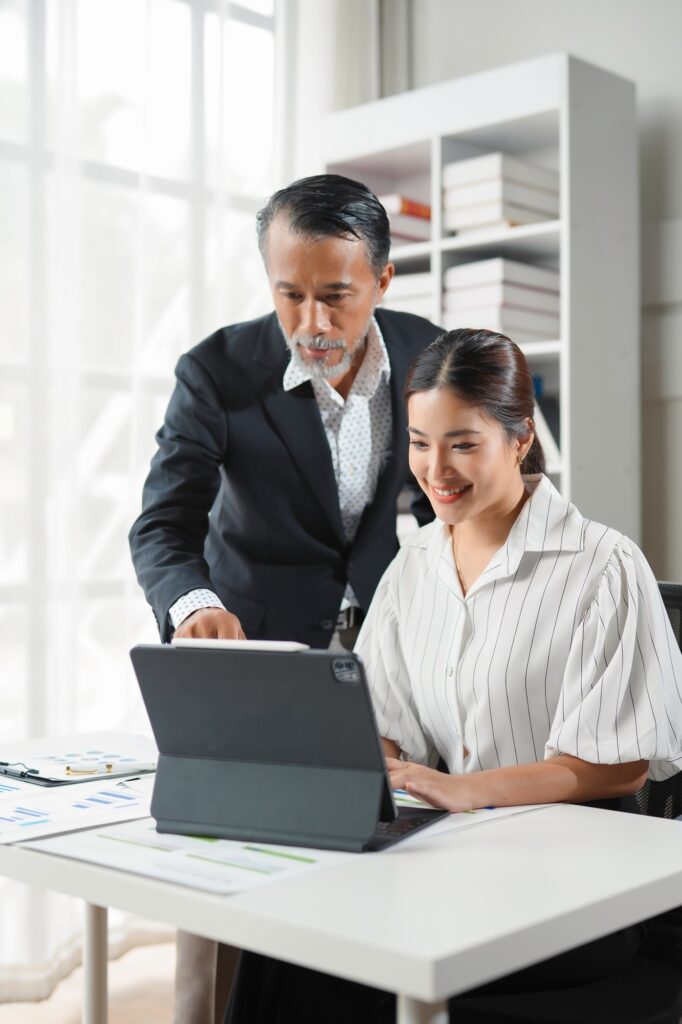
Ongoing Training and Development
Employees must continuously develop their skills to keep up with new quality standards and innovations. As industries evolve, so do the expectations for quality management.
For instance, new technologies and regulations often change the way organizations approach quality. To stay ahead, employees need regular training to learn about these updates and apply them effectively. Without ongoing skill development, organizations risk falling behind in their quality efforts.
Regular training ensures that the workforce remains equipped with the knowledge and tools needed to maintain high-quality standards. Training programs can cover new industry standards, software, or quality tools that help employees perform at their best.
Furthermore, when employees receive regular training, they stay confident in their roles and are more likely to spot areas for improvement. This, in turn, helps maintain consistency and compliance. By investing in training, organizations also foster a culture of growth and accountability, ensuring long-term success in achieving quality goals.
Key Elements of QMS Quality
When implementing a QMS quality system, several critical elements come into play. These elements ensure that the system functions effectively and that quality is consistently maintained.
Quality Policy
A clearly defined quality policy sets the foundation for the entire QMS. It aligns everyone in the organization with the goals and expectations related to quality.
Quality Objectives
These are measurable targets set to meet the broader quality policy. They guide day-to-day operations and keep all teams aligned with the organization’s quality goals.
Internal Audits
Regular audits help identify non-conformities and areas for improvement. Audits ensure that the QMS is functioning as intended and reveal potential areas of improvement.
Management Review
Top management must review the QMS periodically to assess its effectiveness. These reviews help ensure that the system continues to meet its objectives and align with the business strategy.
The Process of Achieving QMS Certification
Initial Assessment and Planning
The first step in achieving certification is to conduct a comprehensive assessment of your current quality management practices. This assessment allows you to evaluate how your processes align with the required standards. It helps identify any gaps or areas that need improvement. By thoroughly reviewing your practices, you can pinpoint inefficiencies, compliance issues, or missing components. This step is crucial because it serves as the foundation for improvement and certification.
After completing the assessment, planning begins to establish a roadmap for aligning your processes with ISO 9001 standards. The planning phase involves setting clear objectives and determining the necessary steps to meet these standards. Companies must define timelines, assign responsibilities, and allocate resources for each phase of the implementation. During this process, it’s essential to involve key stakeholders who can contribute valuable insights. By creating a detailed plan, organizations ensure they stay on track to meet ISO 9001 certification requirements and improve their overall quality management system.
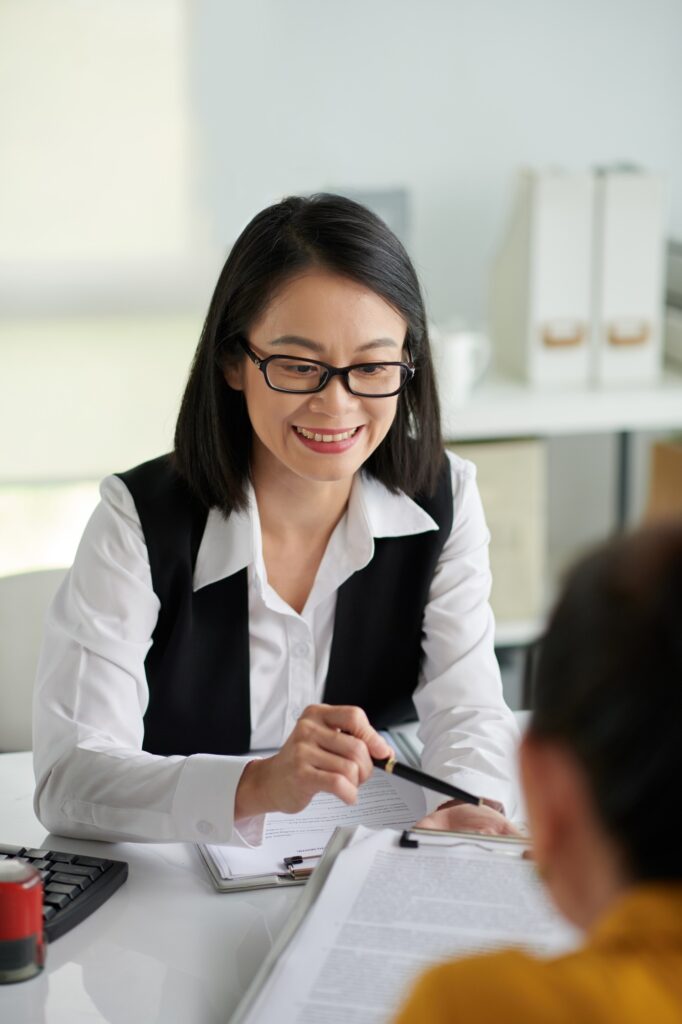
Implementation and Training
After planning, organizations must implement the necessary changes in their operations to align with the QMS. This step involves setting up process controls to ensure consistent quality and efficiency. Employees must receive proper training so they understand the importance of the QMS and their role in maintaining high standards. Additionally, organizations should create clear documentation for each process to maintain transparency and consistency. By documenting procedures, businesses provide employees with reference materials to follow, reducing errors and confusion.
Furthermore, organizations must establish performance measures to track progress and ensure compliance with the QMS. These measures help identify areas that require improvement and ensure that the QMS is functioning effectively. Regular monitoring of key metrics allows for timely corrective actions if needed. It’s also important to maintain open communication with all team members, as their feedback will provide valuable insights for continuous improvement. By implementing these changes and creating a supportive environment, organizations can foster a culture of quality and increase their chances of successful ISO 9001 certification.
How QMS Quality Supports Compliance and Regulatory Standards
QMS quality systems play a crucial role in ensuring compliance with industry standards, particularly in sectors such as pharmaceuticals, manufacturing, and healthcare. By embedding quality into every process, organizations are better equipped to meet regulatory requirements and pass audits.
Regulatory Adherence
A robust QMS quality system ensures that all processes are compliant with regulations like ISO standards, FDA guidelines, and EU directives. Compliance is no longer a one-time task but an ongoing part of the organization’s operations. With a well-established QMS, businesses can continuously monitor their adherence to regulatory requirements, making adjustments as needed to stay compliant.
Consistent Documentation
QMS systems ensure that all processes, inspections, and corrective actions are thoroughly documented. This level of documentation is invaluable when it comes time for audits or regulatory reviews. Clear, accurate records provide evidence that processes are consistently followed and help organizations demonstrate their commitment to quality and regulatory adherence.
Audit Readiness
A well-structured QMS enables organizations to be audit-ready at all times. Regular internal audits and process reviews ensure that the company is continuously meeting regulatory expectations. These audits identify areas for improvement, which helps organizations stay proactive rather than reactive during official inspections.
Corrective and Preventive Actions (CAPA)
QMS systems facilitate the identification of non-conformities and the implementation of corrective and preventive actions. By addressing issues early and preventing recurrence, companies ensure long-term compliance and operational efficiency. CAPA processes help maintain regulatory standards, minimizing the risk of non-compliance.
Employee Training and Awareness
QMS emphasizes continuous employee training, ensuring that all staff members understand the latest regulatory standards. Trained employees can more effectively contribute to maintaining compliance and improving the quality management system. With ongoing education, businesses stay ahead of regulatory changes and maintain their certification status.
Conclusion
QMS quality offers an efficient, proactive approach to managing quality that vastly outperforms traditional methods. It integrates quality management into every phase of a business’s processes, from design to delivery, ensuring better compliance, fewer errors, and more satisfied customers. For organizations looking to stay competitive and maintain operational excellence, embracing QMS quality is the way forward. Whether you are just starting with QMS or looking to refine your processes, it’s clear that the shift from traditional quality methods to QMS will unleash significant efficiency gains and help build a stronger, more reliable organization.
References
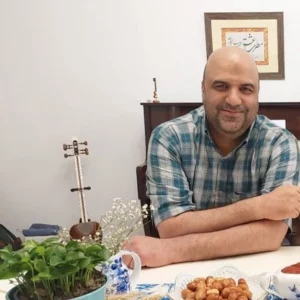
Ershad Moradi
Ershad Moradi, a Content Marketing Specialist at Zamann Pharma Support, brings 6 years of experience in the pharmaceutical industry. Specializing in pharmaceutical and medical technologies, Ershad is currently focused on expanding his knowledge in marketing and improving communication in the field. Outside of work, Ershad enjoys reading and attending industry related networks to stay up-to-date on the latest advancements. With a passion for continuous learning and growth, Ershad is always looking for new opportunities to enhance his skills and contribute to pharmaceutical industry. Connect with Ershad on Facebook for more information.
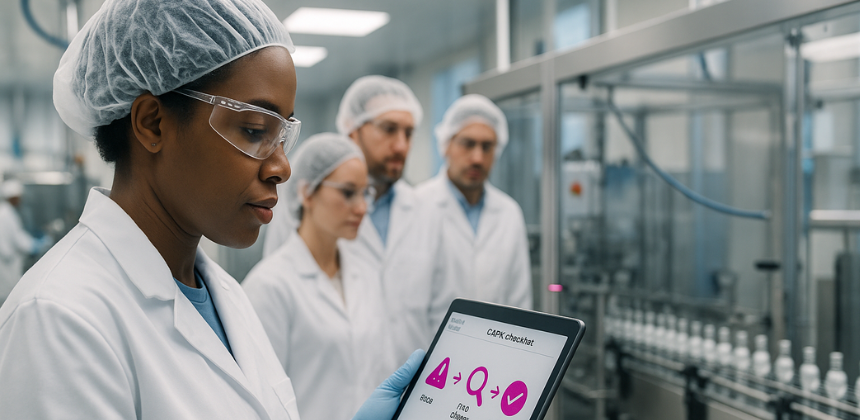
What Is a CAPA Plan? A Beginner’s Guide
This beginner’s guide explains CAPA plans in plain language. You’ll define problems clearly, analyze root causes with proven tools, and turn findings into targeted corrective and preventive actions. Then, you’ll verify effectiveness with metrics and close confidently.

Computerized Maintenance Management: The Complete 2025 Guide
This guide explores computerized maintenance management with practical strategies, CMMS comparisons, and implementation tips. Designed for professionals, entrepreneurs, and job seekers, it helps you choose the right tools, optimize workflows, and boost ROI with preventive and predictive maintenance methods.
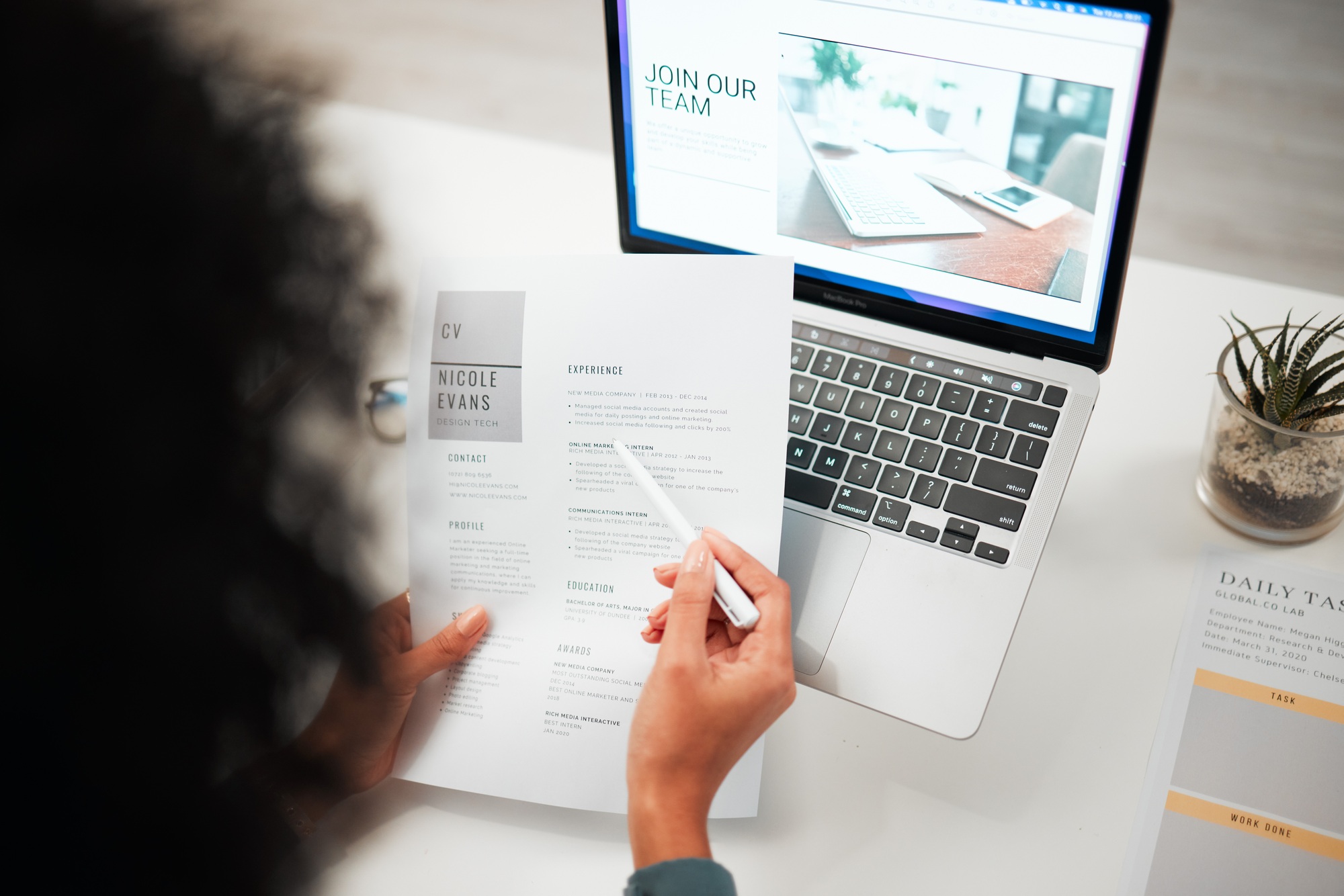
How to Choose the Right Special Skills for Resume Success
Learn how to choose, organize, and present special skills for resume success. This guide includes technical and soft skills, comparison tables, and AI-friendly strategies to pass ATS filters and stand out in competitive job markets.