Meeting ISO 9001 requirements requires pharmaceutical companies to maintain the highest quality standards. These standards guarantee product consistency, ensure regulatory compliance, and enhance patient safety. Quality assurance (QA) methods play a crucial role in achieving these objectives. By implementing structured QA processes, companies minimize risks and improve overall efficiency. Following ISO 9001 guidelines also strengthens product reliability and increases the chances of regulatory approval. Without a strong QA framework, firms may face compliance challenges, operational setbacks, and reputational damage.
To obtain ISO 9001 certification, pharmaceutical companies must adopt robust quality assurance methods. They need to establish precise procedures, enforce strict documentation practices, and commit to continuous improvement. Staying compliant requires a proactive approach, ensuring that QA processes evolve alongside regulatory changes. Investing in well-structured quality assurance systems helps companies meet industry standards while maintaining competitiveness.
This article explores key QA methods essential for ISO 9001 compliance. It provides insights into critical procedures, main objectives, and practical implementation strategies for pharmaceutical firms.
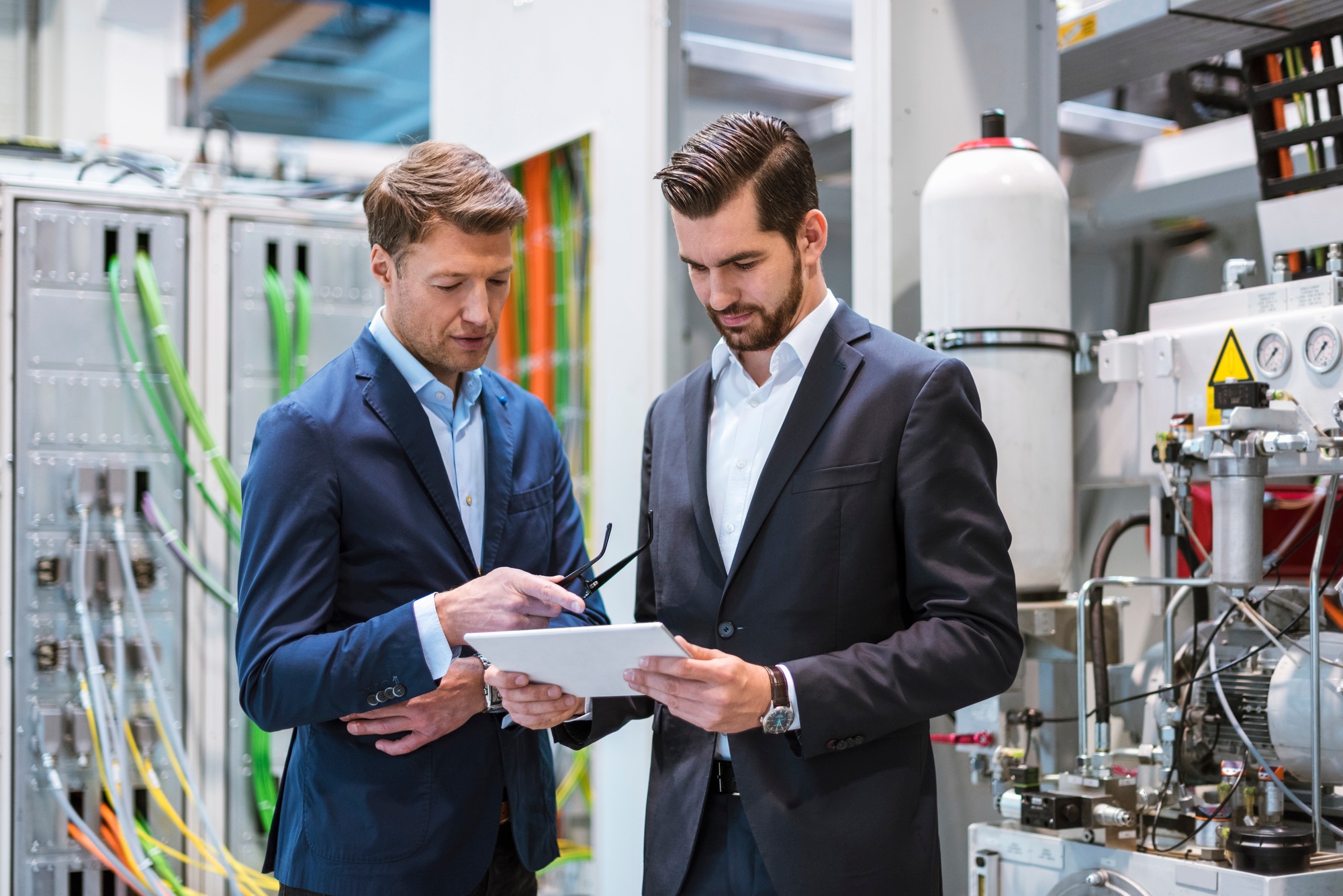
Understanding Quality Assurance Methods in Pharma
Ensuring compliance with strict regulatory and safety standards requires pharmaceutical companies to implement strong quality assurance methods. These methods emphasize quality control, risk management, and continuous improvement. Companies that adopt structured QA processes minimize errors and maintain consistent product quality. By following standardized procedures, firms can detect deviations early and prevent defects before reaching the market. Effective QA practices also enhance manufacturing efficiency and reduce compliance risks. Regulatory agencies like the FDA and EMA enforce rigorous quality guidelines to protect patient safety. Companies that fail to meet these regulations risk product recalls, financial losses, and reputational harm. Maintaining a strong QA system helps pharmaceutical firms avoid these challenges while ensuring product reliability.
To enhance their QA frameworks, pharmaceutical companies rely on ISO 9001 standards. This internationally recognized framework establishes best practices for quality management, documentation, and process control. Firms that implement ISO 9001 create structured procedures that ensure consistency across all operations. These procedures help teams identify risks early and apply corrective actions efficiently. Continuous improvement remains a key element of ISO 9001 compliance, promoting long-term process optimization. By refining QA methods, companies improve efficiency, enhance product safety, and strengthen regulatory compliance. A well-executed quality assurance strategy builds trust with regulators and customers alike. When companies prioritize QA, they reduce operational risks, maintain market credibility, and achieve higher levels of performance.
Sign up for Introduction to Good Documentation Practices Course
Key Procedures for Quality Assurance in Pharma
SOPs guide employees on standardized quality processes. Companies use them to ensure repeatable and controlled workflows.
GMP ensures products meet safety and efficacy requirements. Pharma firms follow GMP to avoid contamination and manufacturing errors.
Testing ensures products meet specifications before reaching the market. It involves stability testing, chemical analysis, and batch verification.
Companies monitor deviations and track changes in quality processes. They implement corrective actions to prevent recurring issues.
Pharma firms assess supplier performance and compliance. They conduct audits to ensure raw materials meet required standards.
Risk-based approaches identify potential hazards in production. Companies implement mitigation plans to ensure patient safety.
CAPA systems resolve quality issues and prevent future defects. Firms track root causes and implement corrective measures.
Fast-track your career with VIP consultation
Quality Assurance vs. Quality Control in Pharma
Quality Assurance: Preventing Defects
Companies follow strict QA procedures to identify potential issues early in the manufacturing process. By implementing process validation, firms ensure that production methods consistently deliver reliable results. Regular inspections and audits help detect deviations before they become serious problems. Companies also use risk management strategies to minimize the chances of defects occurring. When businesses prioritize QA, they improve efficiency, reduce waste, and enhance overall product reliability.
Strong documentation plays a key role in preventing defects and ensuring compliance. Companies maintain detailed records of each production step to track quality standards. By training employees on proper QA procedures, firms strengthen their ability to catch issues before they escalate. Automated monitoring systems provide real-time data to improve decision-making.
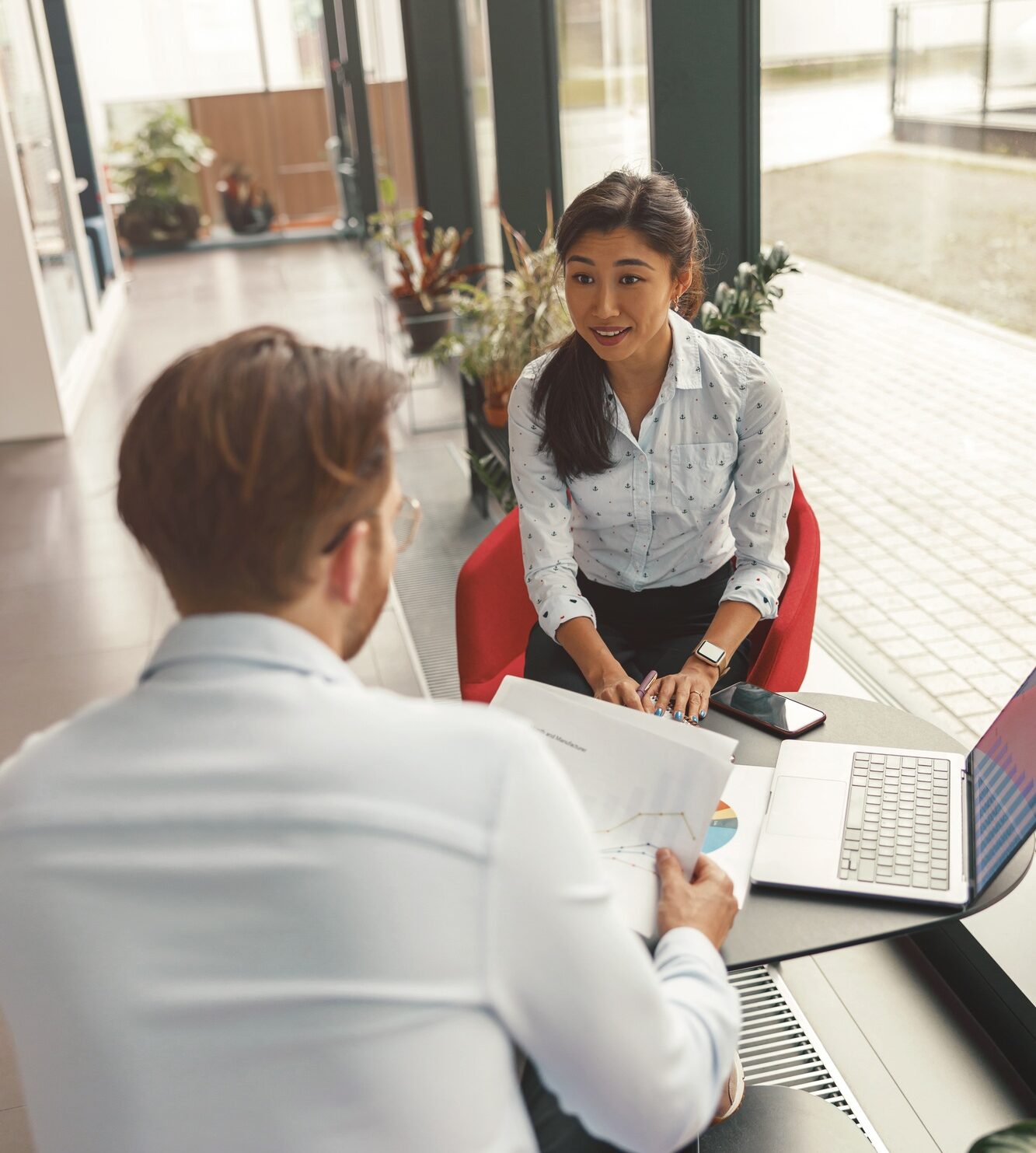
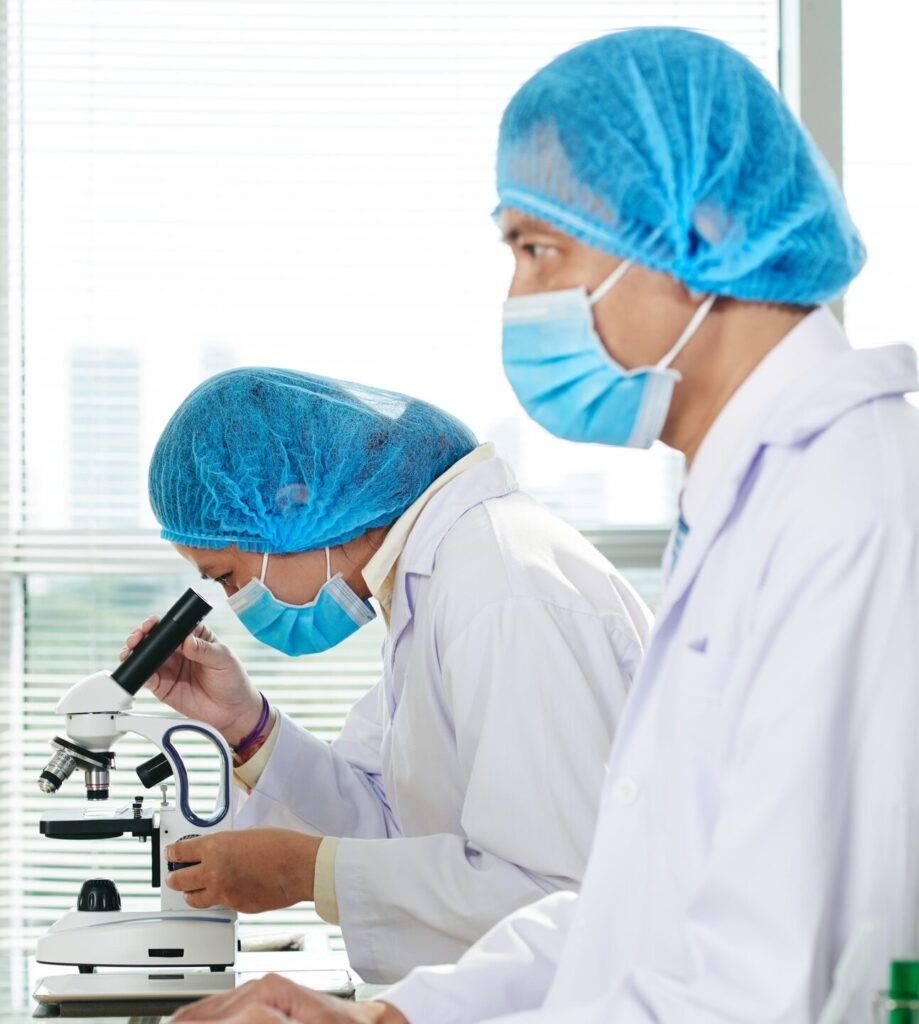
Quality Control: Detecting Defects
Quality control helps pharmaceutical companies detect defects before releasing products to the market. It involves batch testing, stability testing, and raw material inspections. Batch testing checks if each production lot meets quality standards. Stability testing ensures products maintain effectiveness throughout their shelf life. Raw material inspections verify that ingredients meet required specifications before use. Companies follow strict QC procedures to identify and eliminate defective products. By conducting thorough testing, they prevent substandard drugs from reaching patients. Regulatory agencies require pharmaceutical firms to perform QC testing at multiple production stages. Without proper QC, companies risk recalls, financial losses, and regulatory penalties.
Quality assurance and quality control work together to maintain product safety and compliance. QA focuses on preventing defects by ensuring smooth and standardized processes. QC verifies that finished products meet quality specifications before distribution. While QA emphasizes process control, QC relies on testing and inspection.
Essential QA Goals for Pharma Success
Ensuring product safety, regulatory compliance, and customer satisfaction requires strong quality assurance methods. Pharmaceutical companies implement these methods to maintain high standards and prevent defects. By following strict QA procedures, firms reduce risks and improve overall product reliability.
Ensuring Product Consistency
Companies use QA methods to maintain uniformity across production batches. Consistent products improve reliability and regulatory approval.
Meeting Regulatory Compliance
Pharma firms align QA processes with ISO 9001, GMP, and FDA standards. Compliance prevents legal issues and market recalls.
Enhancing Patient Safety
QA ensures pharmaceutical products meet safety and efficacy standards. Strict quality checks prevent harmful side effects.
Reducing Production Errors
Quality assurance helps identify and resolve manufacturing defects. This reduces product waste and operational costs.
Improving Supply Chain Integrity
QA ensures raw materials and components meet quality standards. Companies assess suppliers to maintain consistency.
Strengthening Documentation Processes
Pharma firms document quality procedures and testing results. Proper documentation supports audits and regulatory submissions.
Encouraging Continuous Improvement
QA fosters a culture of continuous improvement. Companies refine processes to enhance efficiency and innovation.
Latest FDA and EMA Regulations on Quality Assurance Methods
FDA’s Latest Quality Assurance Regulations
The FDA now requires pharmaceutical companies to strengthen data integrity and risk-based quality assurance. Companies must maintain accurate, complete, and secure documentation for every stage of manufacturing. They need validated electronic record systems to prevent data manipulation and ensure regulatory compliance. The FDA has increased oversight, making regular audits and real-time monitoring essential for companies. Firms that fail to meet these requirements risk penalties and product recalls. To comply, companies must train employees on proper documentation practices and system validation. Investing in secure digital solutions helps organizations improve data integrity and minimize compliance risks.
Risk management has become a top priority under the FDA’s updated quality assurance framework. Companies must proactively identify, assess, and control risks before they affect product quality. The FDA expects firms to implement structured risk assessment models to detect potential hazards early. Businesses that lack strong risk management strategies face increased regulatory scrutiny. To stay compliant, companies should integrate predictive analytics, real-time tracking, and automated reporting. These tools help detect deviations and prevent quality failures before they escalate.
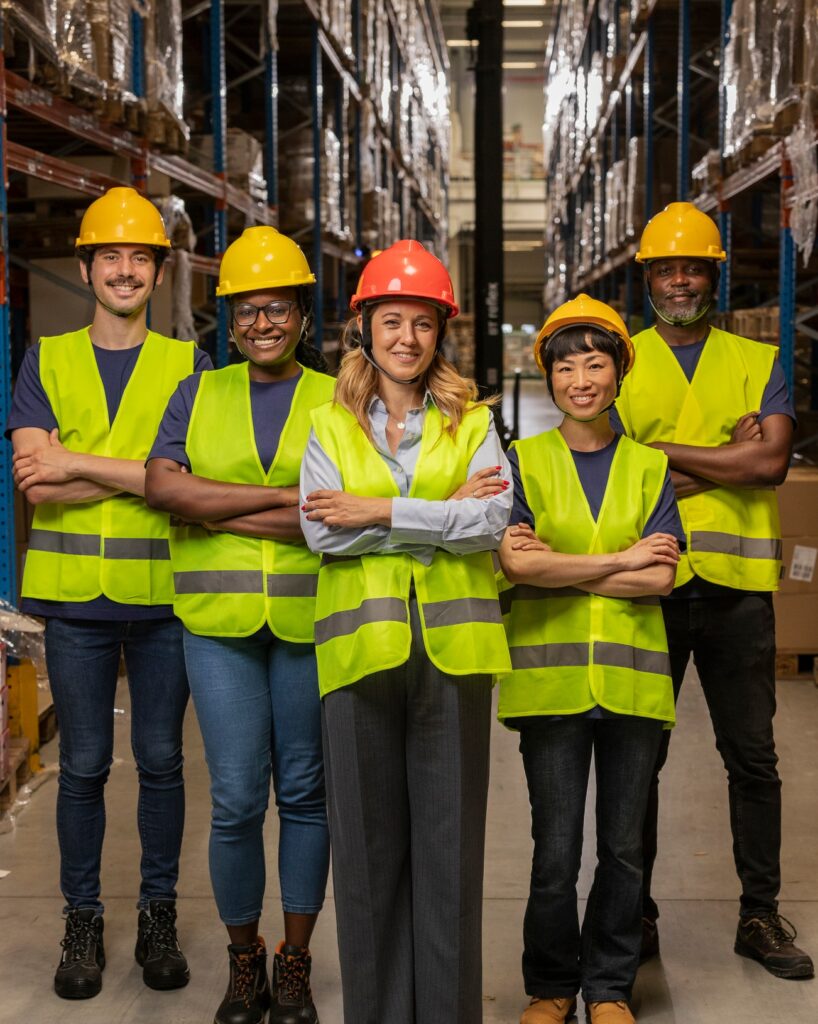
EMA’s New Approach
The EMA now enforces stricter regulations on supply chain transparency and good manufacturing practices (GMP).
Companies must track raw materials, active pharmaceutical ingredients (APIs), and finished products with detailed traceability data. They need to document supplier qualifications, transportation conditions, and storage procedures to ensure compliance. These measures help prevent counterfeit products from entering the market and protect patient safety.
Firms that lack proper traceability risk supply chain disruptions and regulatory penalties. To stay compliant, companies must adopt advanced tracking systems and maintain real-time visibility. Strong supply chain transparency builds trust with regulators and strengthens product integrity.
The EMA has also revised GMP requirements to match advancements in pharmaceutical technology. Companies must integrate digital quality control systems to detect deviations immediately. The updated regulations emphasize continuous process verification, ensuring products remain compliant at every stage. Businesses that implement AI-driven quality assurance improve efficiency and reduce human errors.
Common Challenges in Implementing Quality Assurance Methods
Maintaining high-quality standards and regulatory compliance presents significant challenges for pharmaceutical companies. As they implement quality assurance methods, they must navigate various obstacles that can impact efficiency and compliance. One of the biggest challenges involves regulatory complexity. Pharmaceutical regulations change frequently, making it difficult for companies to stay up to date. Firms must constantly monitor ISO 9001 requirements and evolving industry regulations to ensure compliance. Without proper oversight, businesses risk audits, product recalls, and financial penalties. To prevent these risks, companies should invest in regulatory tracking systems and continuous compliance training.
Another significant challenge is resource allocation constraints. QA implementation requires both financial investment and skilled personnel. Companies often struggle to balance operational costs with compliance demands. They need to optimize budgets while maintaining high-quality assurance standards. Smart resource management helps firms achieve efficiency without compromising product safety. Additionally, data management and documentation present ongoing challenges. Accurate record-keeping is essential for audits, inspections, and regulatory reporting. Companies must implement structured documentation systems to store and retrieve quality data easily. Without proper systems, firms risk compliance failures and lost information.
Seven Main Categories of Quality Assurance Methods
Pharmaceutical companies apply various quality assurance categories to comply with ISO 9001.
Process Validation
Validation ensures that manufacturing processes produce consistent results. Companies document each step to verify reproducibility.
Documentation Control
Proper documentation supports audits and regulatory compliance. Firms maintain SOPs, batch records, and test results.
Internal Audits and Compliance Checks
Companies conduct internal audits to assess compliance with quality standards. Audits identify areas for improvement and ensure regulatory adherence.
Supplier and Vendor Audits
Pharmaceutical firms audit suppliers to ensure material quality. Vendor compliance impacts product integrity and safety.
Training and Employee Competency
Well-trained employees understand QA procedures and compliance requirements. Companies invest in ongoing training programs.
Deviation and Non-Conformance Management
QA teams track deviations and implement corrective actions. Effective management reduces recurring issues and improves compliance.
Complaint Handling
Companies analyze customer complaints to improve product quality. Feedback provides insights into potential product issues.
Conclusion
To comply with ISO 9001, pharmaceutical companies must establish structured quality assurance methods. These methods help maintain product consistency, ensure regulatory adherence, and protect patient safety. By focusing on process validation, documentation control, and risk management, companies can improve efficiency and reduce errors. Additionally, strong QA systems help firms detect potential quality issues early, preventing costly recalls and regulatory penalties. Without a well-defined approach, businesses risk non-compliance, operational inefficiencies, and loss of consumer trust.
To further enhance quality assurance, pharmaceutical companies should invest in advanced technologies such as AI, blockchain, and digital auditing. These innovations streamline QA processes, improve accuracy, and strengthen regulatory compliance. AI-driven systems enable real-time monitoring, reducing the risk of human error. Blockchain technology enhances traceability, ensuring transparency across the supply chain. Digital auditing simplifies compliance checks, making regulatory reporting more efficient. By prioritizing quality assurance, companies build long-term market trust and achieve sustained success. Implementing ISO 9001 with robust QA methods fosters continuous improvement, giving businesses a strong competitive edge in the pharmaceutical industry.
References
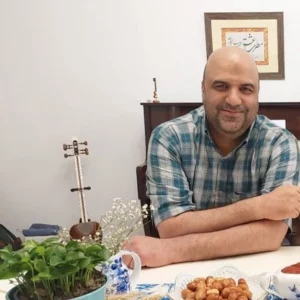
Ershad Moradi
Ershad Moradi, a Content Marketing Specialist at Zamann Pharma Support, brings 6 years of experience in the pharmaceutical industry. Specializing in pharmaceutical and medical technologies, Ershad is currently focused on expanding his knowledge in marketing and improving communication in the field. Outside of work, Ershad enjoys reading and attending industry related networks to stay up-to-date on the latest advancements. With a passion for continuous learning and growth, Ershad is always looking for new opportunities to enhance his skills and contribute to pharmaceutical industry. Connect with Ershad on Facebook for more information.
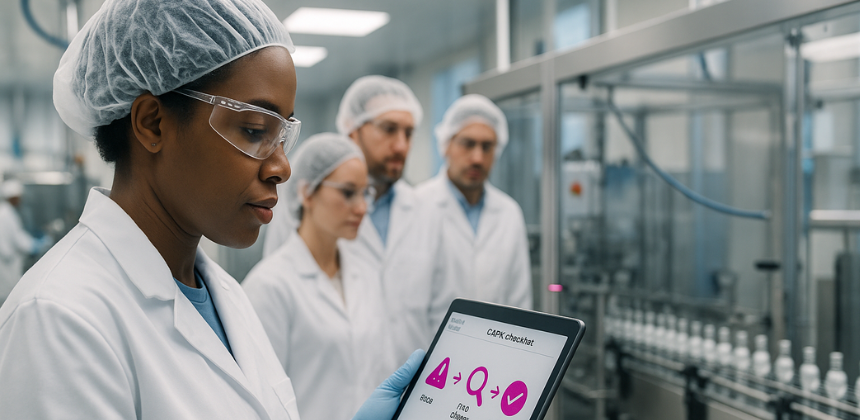
What Is a CAPA Plan? A Beginner’s Guide
This beginner’s guide explains CAPA plans in plain language. You’ll define problems clearly, analyze root causes with proven tools, and turn findings into targeted corrective and preventive actions. Then, you’ll verify effectiveness with metrics and close confidently.

Computerized Maintenance Management: The Complete 2025 Guide
This guide explores computerized maintenance management with practical strategies, CMMS comparisons, and implementation tips. Designed for professionals, entrepreneurs, and job seekers, it helps you choose the right tools, optimize workflows, and boost ROI with preventive and predictive maintenance methods.
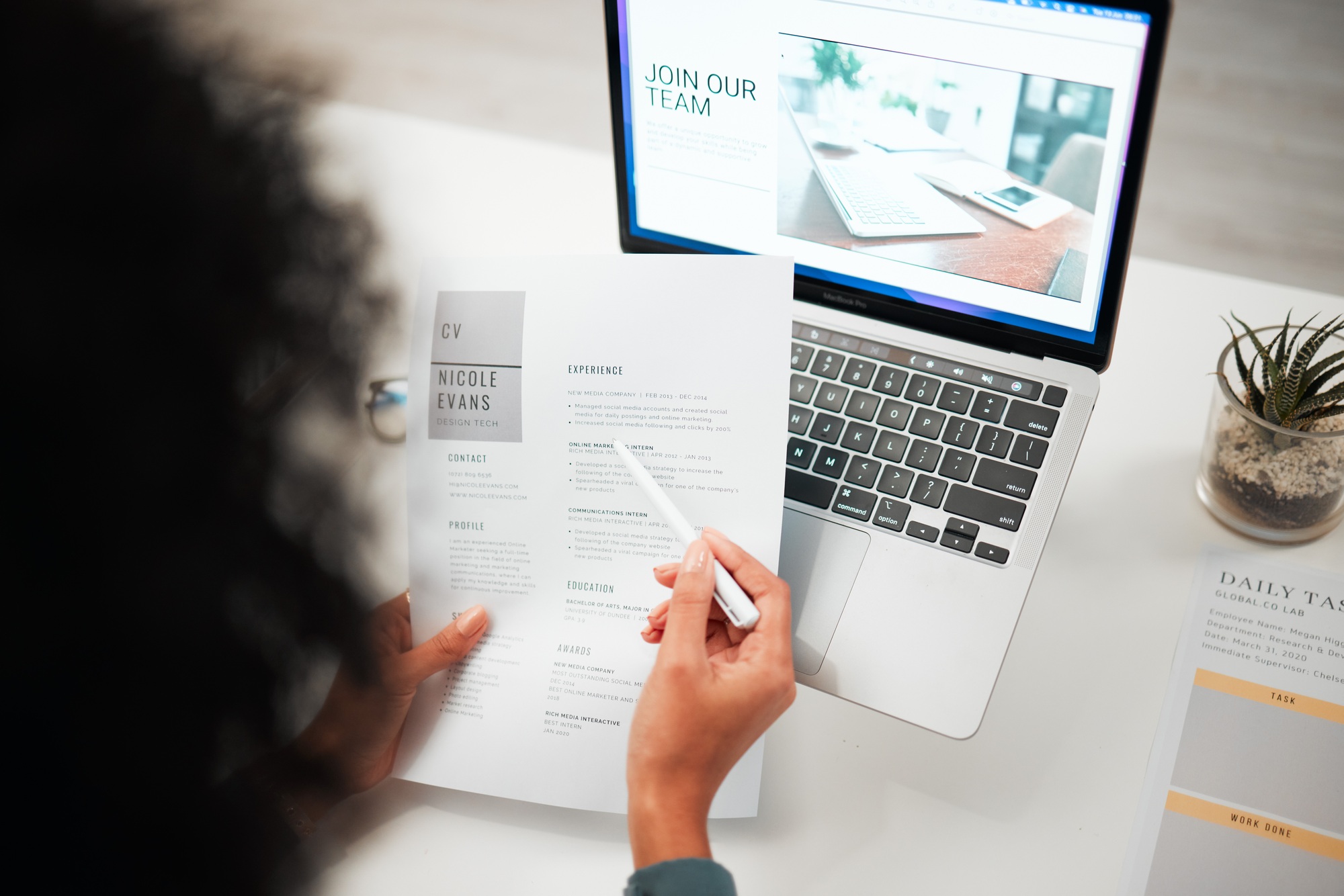
How to Choose the Right Special Skills for Resume Success
Learn how to choose, organize, and present special skills for resume success. This guide includes technical and soft skills, comparison tables, and AI-friendly strategies to pass ATS filters and stand out in competitive job markets.