Quality Management System (QMS) implementation is essential for any organization aiming to improve efficiency, maintain compliance, and ensure customer satisfaction. QMS provides a structured framework to streamline operations, enhance quality, and drive continuous improvement. When implemented effectively, it helps businesses achieve their goals and maintain a competitive edge in the market.
In this article, we will explore the steps, objectives, and benefits of QMS implementation to guide you through the process.
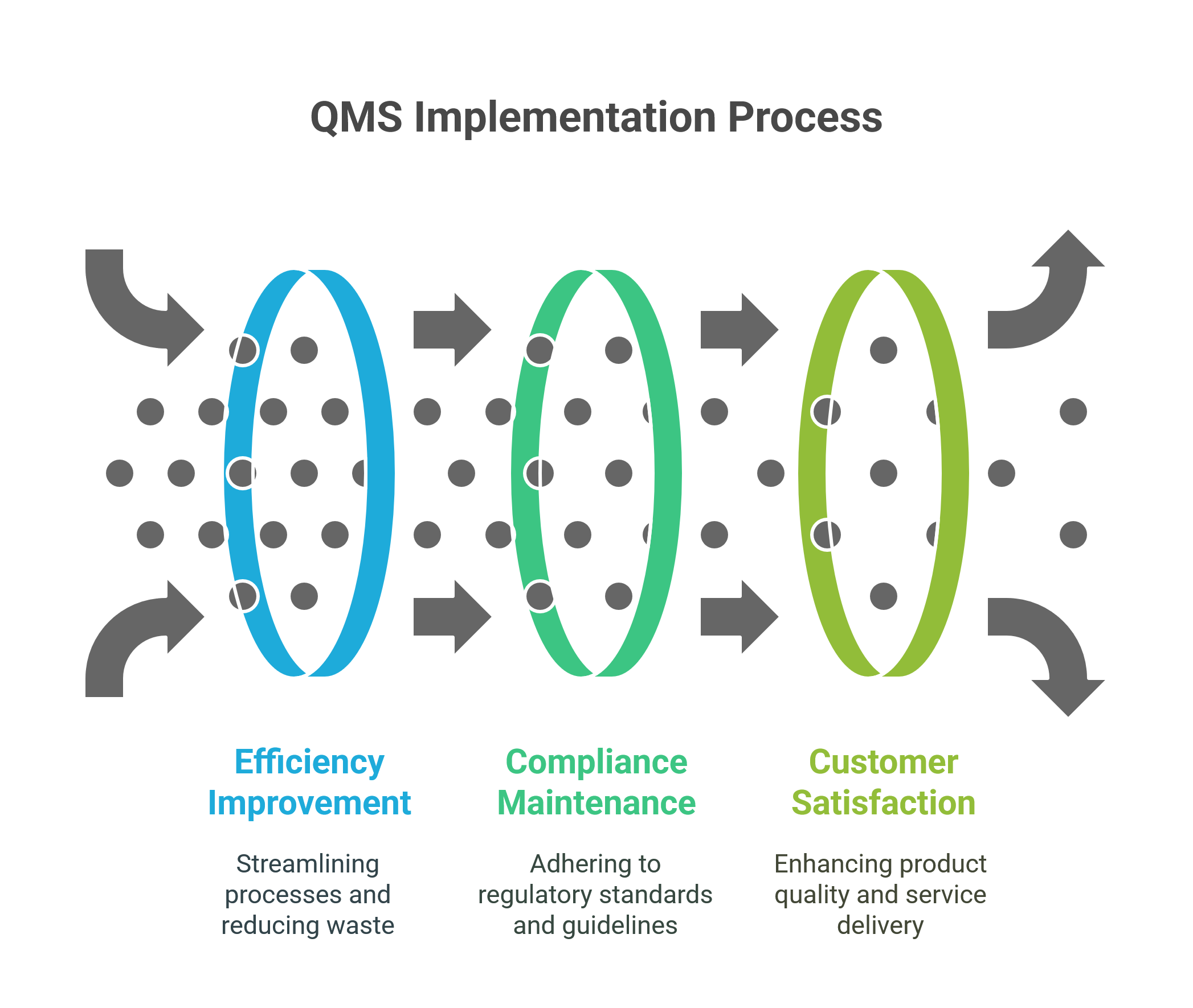
What Is QMS Implementation?
QMS implementation refers to creating, documenting, and executing processes to ensure consistent quality. It helps organizations maintain high standards while meeting customer expectations effectively.
Businesses align quality principles with their daily operations and long-term goals during this process. A well-structured QMS enables teams to streamline workflows and eliminate inefficiencies. This approach also reduces operational risks and ensures compliance with industry standards. Organizations that implement QMS successfully can improve their performance and deliver reliable products or services. Furthermore, a clear focus on quality enhances customer satisfaction and builds trust with stakeholders.
By embedding quality into every stage of operations, businesses can identify and address potential issues quickly. This proactive approach reduces errors and minimizes costly disruptions. Additionally, QMS implementation fosters a culture of accountability and teamwork among employees. Teams collaborate more effectively because they follow clear guidelines and understand their responsibilities. Over time, this culture drives continuous improvement, enabling organizations to adapt to market demands. Businesses also strengthen relationships with customers and regulatory bodies by demonstrating a commitment to quality. In the long run, QMS implementation supports sustainable growth and long-term success.
Sign up for Introduction to GMP Quality Management Systems Course
7 Steps in the QMS Implementation Process
A systematic approach is essential for QMS implementation. Here are the main steps to follow:
Identify measurable goals that align with customer expectations and regulatory requirements.
Research and understand the standards relevant to your industry, such as ISO 9001.
Ensure that leadership commits to quality initiatives and involves employees across all levels.
Create detailed procedures and policies for key business operations to maintain consistency.
Provide comprehensive training on QMS principles and how to apply them in daily tasks.
Regularly review the system’s performance to identify areas for improvement.
Use audits, feedback, and performance metrics to refine processes over time.
These steps ensure a well-structured QMS implementation, which can lead to improved operational efficiency and compliance.
Identifying Requirements for QMS Implementation
Internal Requirements
Internal requirements for QMS implementation focus on organizational goals, employee engagement, and process documentation. First, assess your company’s mission and vision to align them with quality objectives.
Clearly defined goals help ensure every process supports the organization’s overall direction. Next, evaluate your team’s skills and resources to determine their readiness for QMS implementation. This step highlights strengths you can leverage and areas where additional training is necessary. Moreover, involving employees at all levels fosters engagement and creates a sense of ownership. When teams feel connected to the process, they work more effectively and contribute to its success.
Process documentation plays a vital role in meeting internal requirements for QMS implementation. Start by reviewing your current workflows and identifying gaps that impact efficiency.
This evaluation allows you to understand where improvements are necessary to meet quality standards. Next, create detailed documentation for every process to ensure consistency across departments. Clear documentation helps employees understand their roles and responsibilities, reducing confusion and errors.
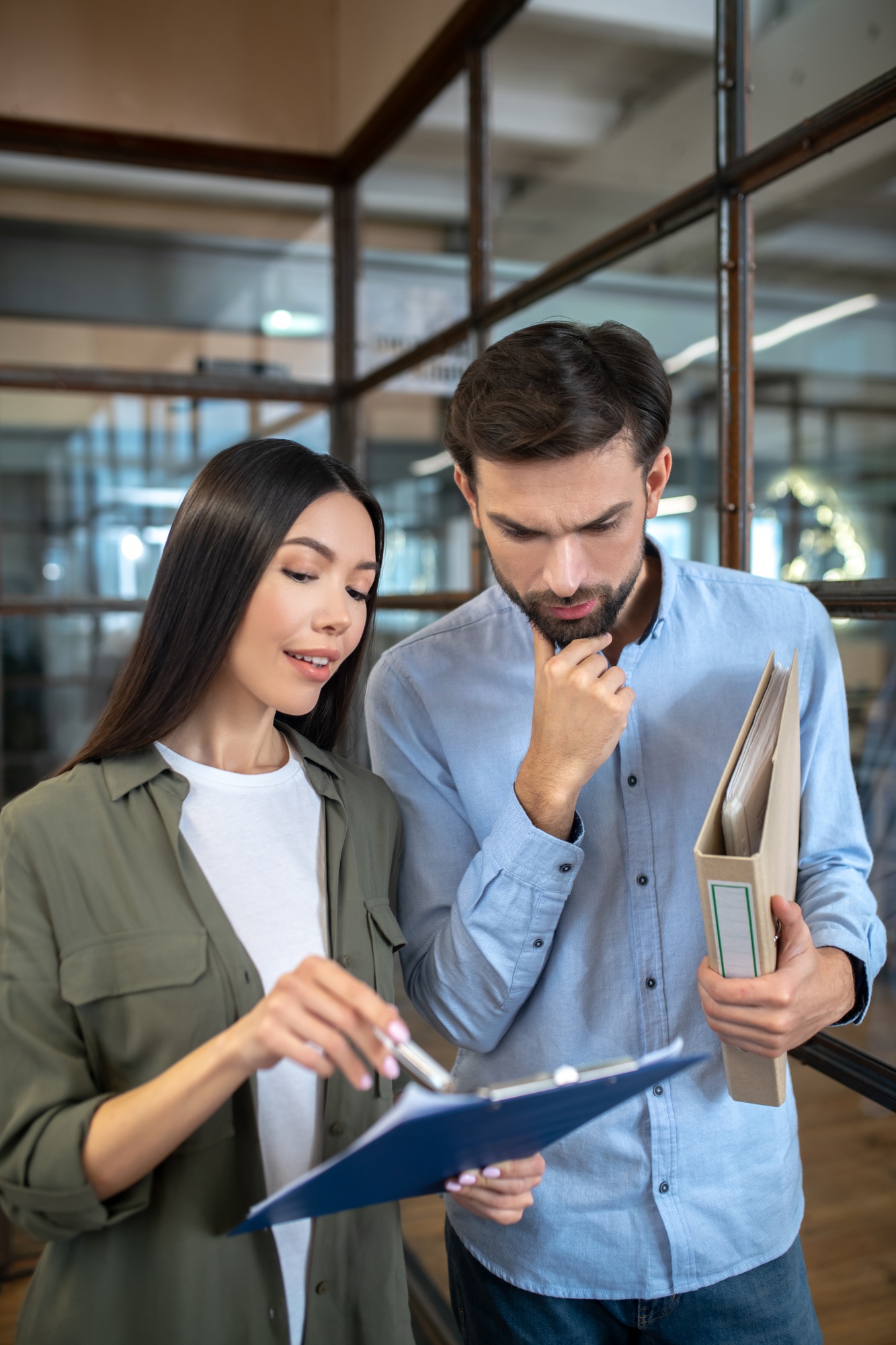
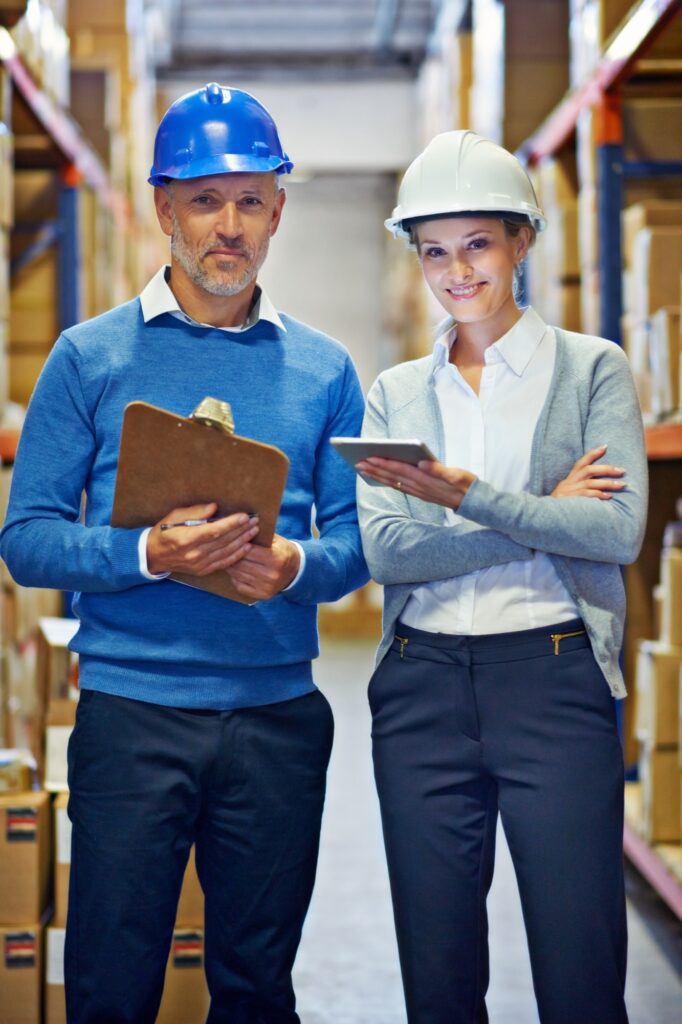
External Requirements
External requirements for QMS implementation focus on meeting industry standards and regulatory compliance. For instance, ISO 9001 offers a globally recognized framework to guide organizations in building effective systems. Businesses must first understand the specific standards applicable to their industry and location. These regulations help ensure product or service quality, safety, and reliability. Additionally, companies should evaluate the expectations of customers and suppliers to align their processes accordingly. By addressing these factors, organizations can design a QMS that meets both legal and stakeholder requirements. Regularly reviewing regulatory updates also helps businesses stay compliant and maintain credibility.
Analyzing external requirements thoroughly ensures a comprehensive and effective QMS design. Start by gathering relevant information about industry standards, customer needs, and supplier quality criteria. This analysis helps identify gaps between existing processes and required compliance levels. Next, prioritize these requirements and create actionable plans to address them. Engaging stakeholders in the process ensures clarity and builds trust throughout the implementation. Moreover, consider how external factors, such as market trends or regulatory changes, may influence operations.
Main Objectives of QMS Implementation
Organizations adopt QMS implementation for several key reasons. Each objective supports business growth and operational excellence:
Streamline Operations
By standardizing processes, businesses can reduce inefficiencies and optimize workflows.
Ensure Regulatory Compliance
Compliance with standards and regulations avoids penalties and builds credibility with customers and authorities.
Reduce Operational Risks
QMS identifies potential risks and establishes controls to mitigate them effectively.
Foster Customer Satisfaction
Meeting customer requirements consistently leads to higher satisfaction and long-term loyalty.
Drive Continuous Improvement
QMS implementation focuses on ongoing evaluation and refinement of business processes.
What to Consider During QMS Implementation?
Procedure Development
Developing procedures is a crucial step in QMS implementation. Clear and concise procedures guide employees and reduce confusion in daily tasks. Start by defining the scope of each procedure to clarify its purpose and boundaries. This ensures employees understand what the procedure covers and how it applies to their roles. Next, outline the responsibilities of all involved team members to avoid misunderstandings. Assign specific tasks to individuals or groups to streamline accountability and improve efficiency. Additionally, detail the steps required to complete the task, making the process easy to follow and repeatable.
Involve key stakeholders during the procedure development process to ensure accuracy and relevance. Collaborating with stakeholders allows you to gather valuable insights and address potential challenges early. Encourage open communication to identify gaps and refine the procedures accordingly. Test the draft procedures with employees to confirm they are practical and easy to implement. Regularly review and update procedures to adapt to changes in processes, standards, or organizational goals. Providing employees with training on the new procedures ensures smooth adoption and consistent application.
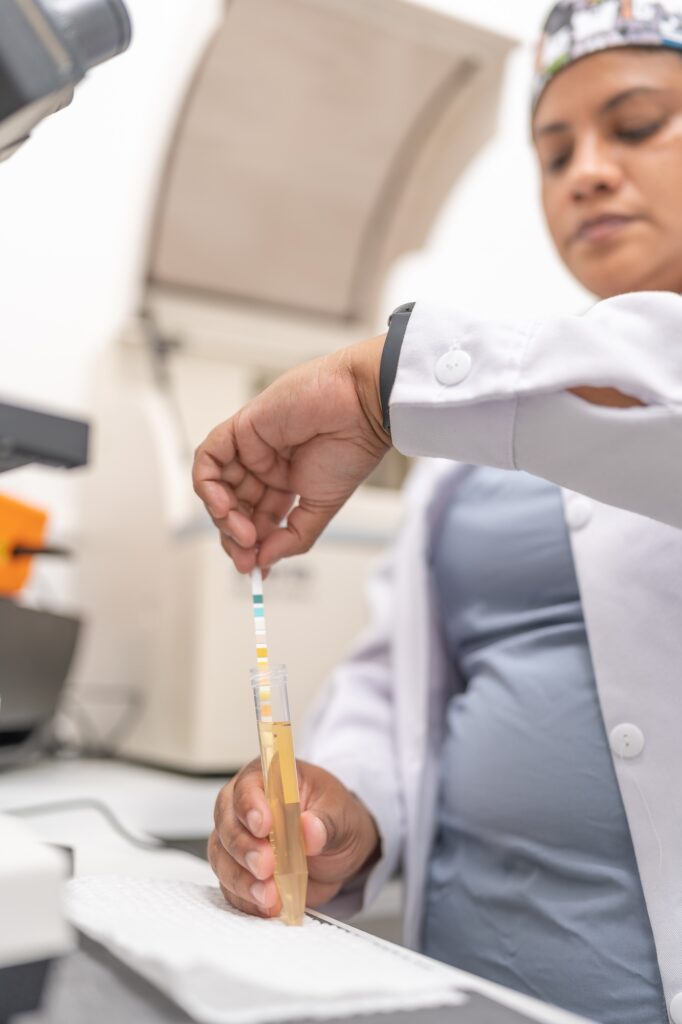
Measuring Success
Employee training programs are essential for maintaining an effective Quality Management System (QMS) in pharma. Continuous training ensures that employees remain up-to-date with the latest procedures and regulatory requirements.
Regularly educating staff helps them understand their roles in maintaining quality standards. By doing so, companies reduce the risk of errors that can arise from outdated practices. Training programs also ensure that employees know how to operate within the QMS, improving efficiency and accuracy in their daily tasks.
Moreover, investing in employee development fosters a culture of quality throughout the organization. Well-trained staff are more likely to take responsibility for ensuring that processes run smoothly. This proactive approach leads to fewer mistakes and more consistent compliance with regulatory standards.
Training also encourages teamwork, as employees gain the skills needed to collaborate effectively across departments. Regularly updating training programs as regulations evolve helps companies stay compliant and reduces the chance of non-conformities.
Ultimately, employee training strengthens the QMS and helps companies maintain long-term success in a highly regulated industry.
Documenting Your Quality Management System
A key aspect of QMS implementation involves creating detailed documentation for every process. Proper documentation serves as a blueprint for maintaining quality and consistency.
Policy Manuals
Draft comprehensive manuals outlining your organization’s quality policy and objectives. These documents set the foundation for QMS.
Standard Operating Procedures (SOPs)
Create step-by-step instructions for critical tasks to ensure uniformity across departments.
Overseeing Batch Record Reviews
QA reviews batch records to ensure that each product batch complies with regulatory and internal quality requirements.
Work Instructions
Provide detailed guides for specific tasks to assist employees in executing their roles effectively.
Records and Logs
Maintain records of quality inspections, audits, and corrective actions to ensure traceability and compliance.
Conclusion
QMS implementation is a strategic investment that yields long-term benefits for organizations in any industry. By following a structured approach, identifying key requirements, and engaging your team, you can streamline operations, enhance quality, and ensure compliance. The process not only improves efficiency but also builds a culture of continuous improvement and accountability. With a strong QMS in place, your organization can confidently meet customer expectations and achieve sustainable growth.
References
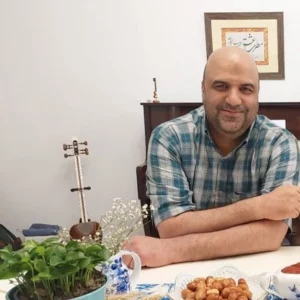
Ershad Moradi
Ershad Moradi, a Content Marketing Specialist at Zamann Pharma Support, brings 6 years of experience in the pharmaceutical industry. Specializing in pharmaceutical and medical technologies, Ershad is currently focused on expanding his knowledge in marketing and improving communication in the field. Outside of work, Ershad enjoys reading and attending industry related networks to stay up-to-date on the latest advancements. With a passion for continuous learning and growth, Ershad is always looking for new opportunities to enhance his skills and contribute to pharmaceutical industry. Connect with Ershad on Facebook for more information.
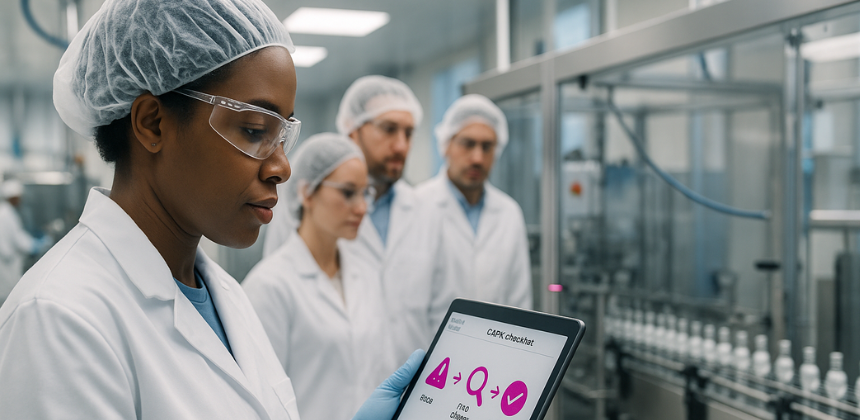
What Is a CAPA Plan? A Beginner’s Guide
This beginner’s guide explains CAPA plans in plain language. You’ll define problems clearly, analyze root causes with proven tools, and turn findings into targeted corrective and preventive actions. Then, you’ll verify effectiveness with metrics and close confidently.

Computerized Maintenance Management: The Complete 2025 Guide
This guide explores computerized maintenance management with practical strategies, CMMS comparisons, and implementation tips. Designed for professionals, entrepreneurs, and job seekers, it helps you choose the right tools, optimize workflows, and boost ROI with preventive and predictive maintenance methods.
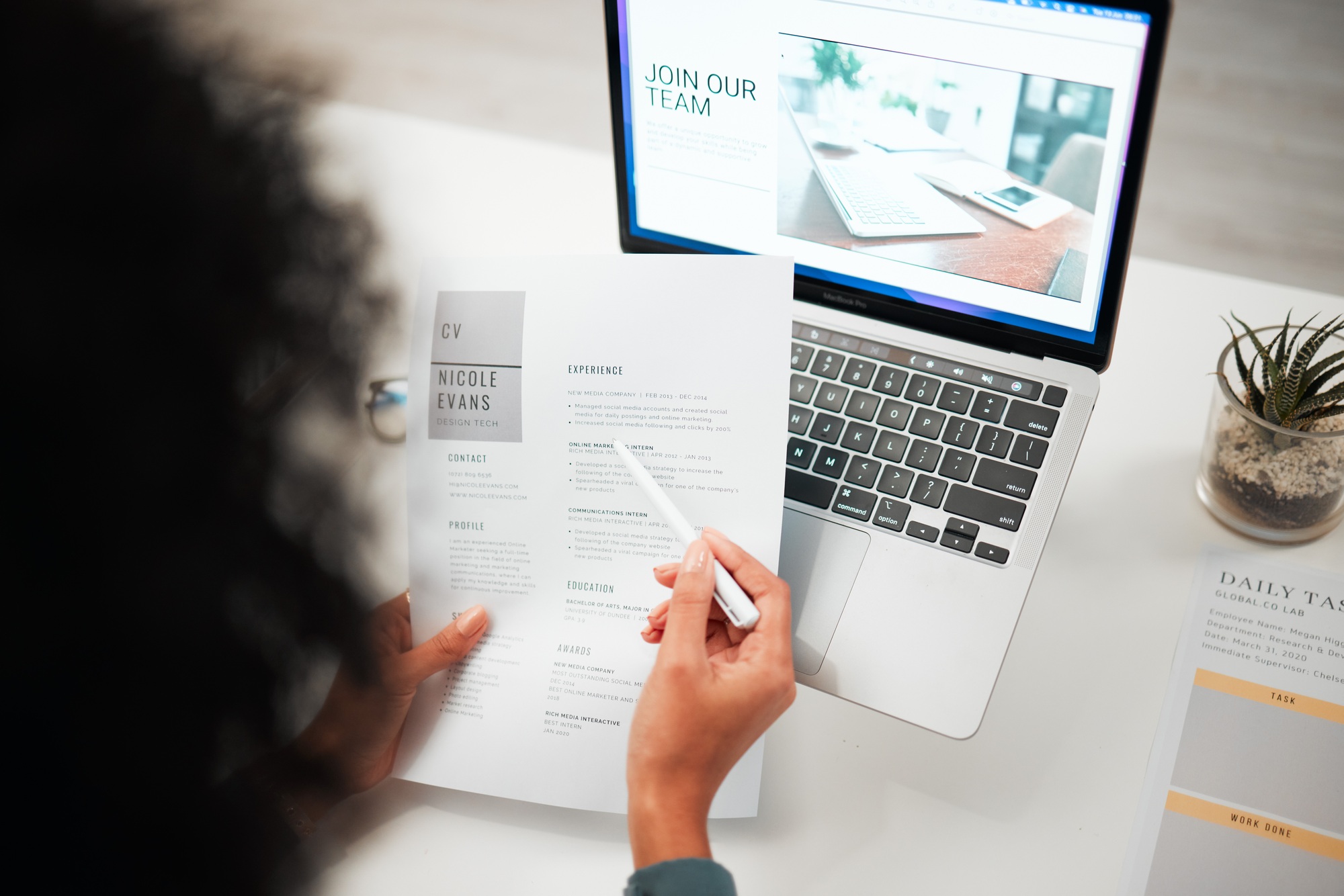
How to Choose the Right Special Skills for Resume Success
Learn how to choose, organize, and present special skills for resume success. This guide includes technical and soft skills, comparison tables, and AI-friendly strategies to pass ATS filters and stand out in competitive job markets.