In the pharmaceutical industry, maintaining quality and compliance is essential. Deviation management plays a crucial role in ensuring product safety and meeting regulatory requirements. It helps identify and address issues quickly, minimizing the impact on production and quality systems. Effective deviation management boosts efficiency and ensures consistent adherence to Good Manufacturing Practices (GMP).
This article offers practical tips to master deviation management in your pharmaceutical processes.
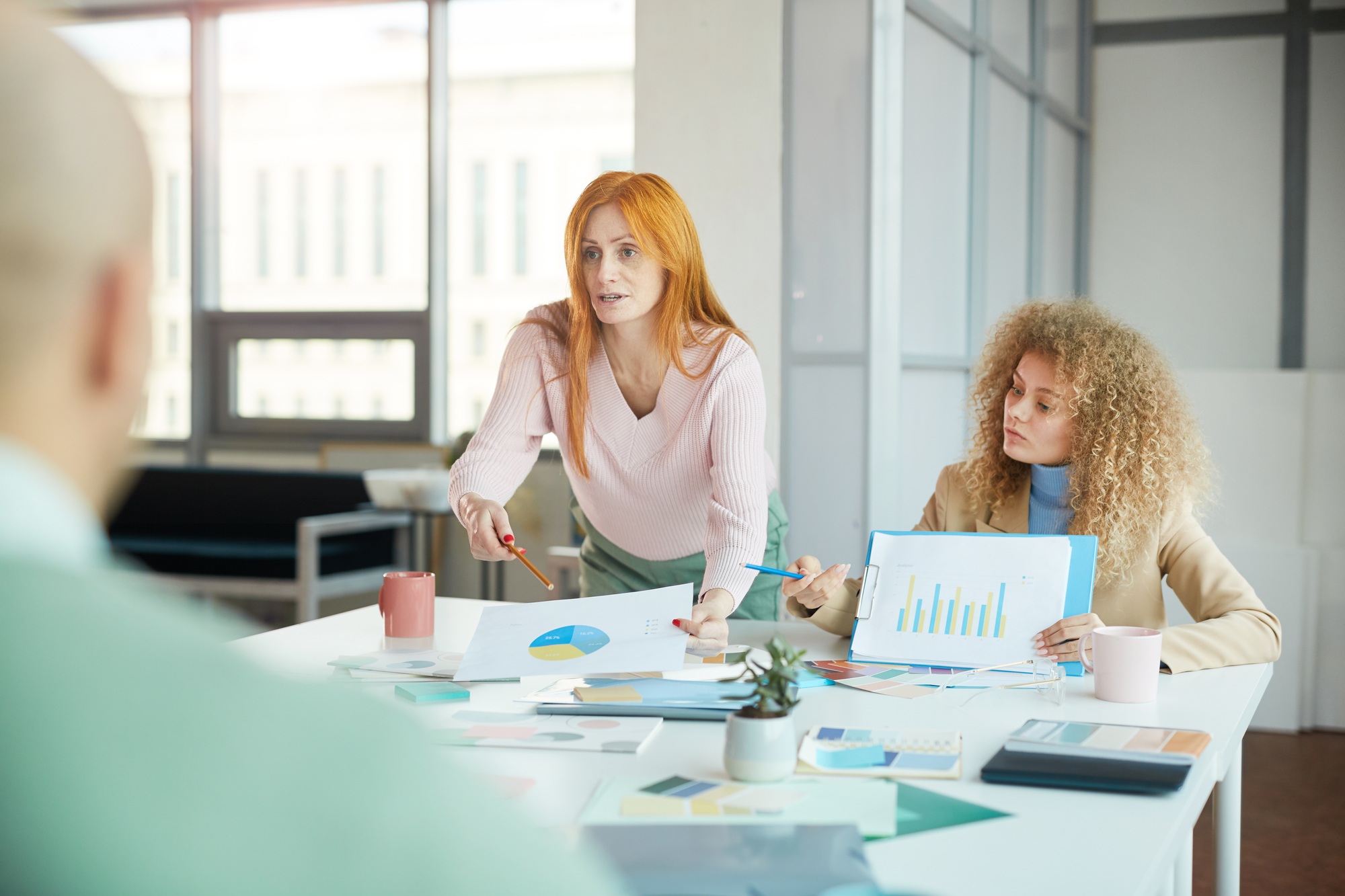
What is Deviation Management in Pharma?
Deviation management focuses on identifying and handling events that deviate from standard procedures. These deviations may result from equipment failure, mistakes by staff, or unexpected environmental factors. Teams must act quickly to document these events and understand their impact. Clear records ensure transparency and help identify patterns over time. This systematic approach allows organizations to take prompt action and maintain operational consistency. Transitioning from detection to resolution requires collaboration among departments, ensuring all aspects of the deviation are addressed.
The primary objective of deviation management is to uncover the root cause and prevent recurrence. Teams use tools like the 5 Whys or Fishbone Diagram to analyze issues thoroughly. Corrective actions resolve immediate problems, while preventive steps minimize future risks. Organizations benefit by improving efficiency and avoiding regulatory penalties. Effective deviation management ensures compliance with GMP standards and builds trust with regulators. Additionally, it fosters a culture of continuous improvement within teams. With consistent efforts, companies can enhance product quality and strengthen their processes.
Sign up for GMP Corrective and Preventive Actions (CAPA) Management Course
How to investigate a deviation?
Investigating deviations thoroughly is vital to identify causes and prevent recurrence. Here are key steps:
Document the Deviation
Record the deviation promptly and include relevant details such as date, time, and personnel involved.
Categorize the Event
Classify the deviation based on its severity (critical, major, or minor) to prioritize actions.
Form an Investigation Team
Assign a team of experts to analyze the deviation and gather evidence.
Identify Root Causes
Use tools like Fishbone Diagrams or the 5 Whys method to pinpoint the root cause.
Implement CAPA
Develop corrective measures to address immediate issues and preventive steps to avoid future deviations.
Verify Effectiveness
Monitor implemented actions to ensure they resolve the deviation effectively.
Deviation Management vs. Nonconformance
Deviations
Deviations happen when processes do not follow standard operating procedures (SOPs). These events indicate something unexpected occurred, but they do not always harm product quality. For example, a slight temperature change during storage might exceed limits but leave the product intact. Teams need to act quickly to assess the situation and evaluate its impact. Clear communication and detailed documentation help organizations determine whether a deviation affects product safety. By addressing deviations early, companies prevent small issues from growing into significant problems.
Not all deviations cause product defects, but they still require careful attention. Ignoring these events can lead to missed opportunities for process improvement. For instance, investigating a storage temperature excursion can reveal equipment calibration issues. Understanding these root causes allows teams to take corrective action before defects appear. Organizations that manage deviations effectively maintain compliance with GMP requirements and improve operational efficiency. Regularly monitoring deviations helps companies spot trends and strengthen their quality systems.
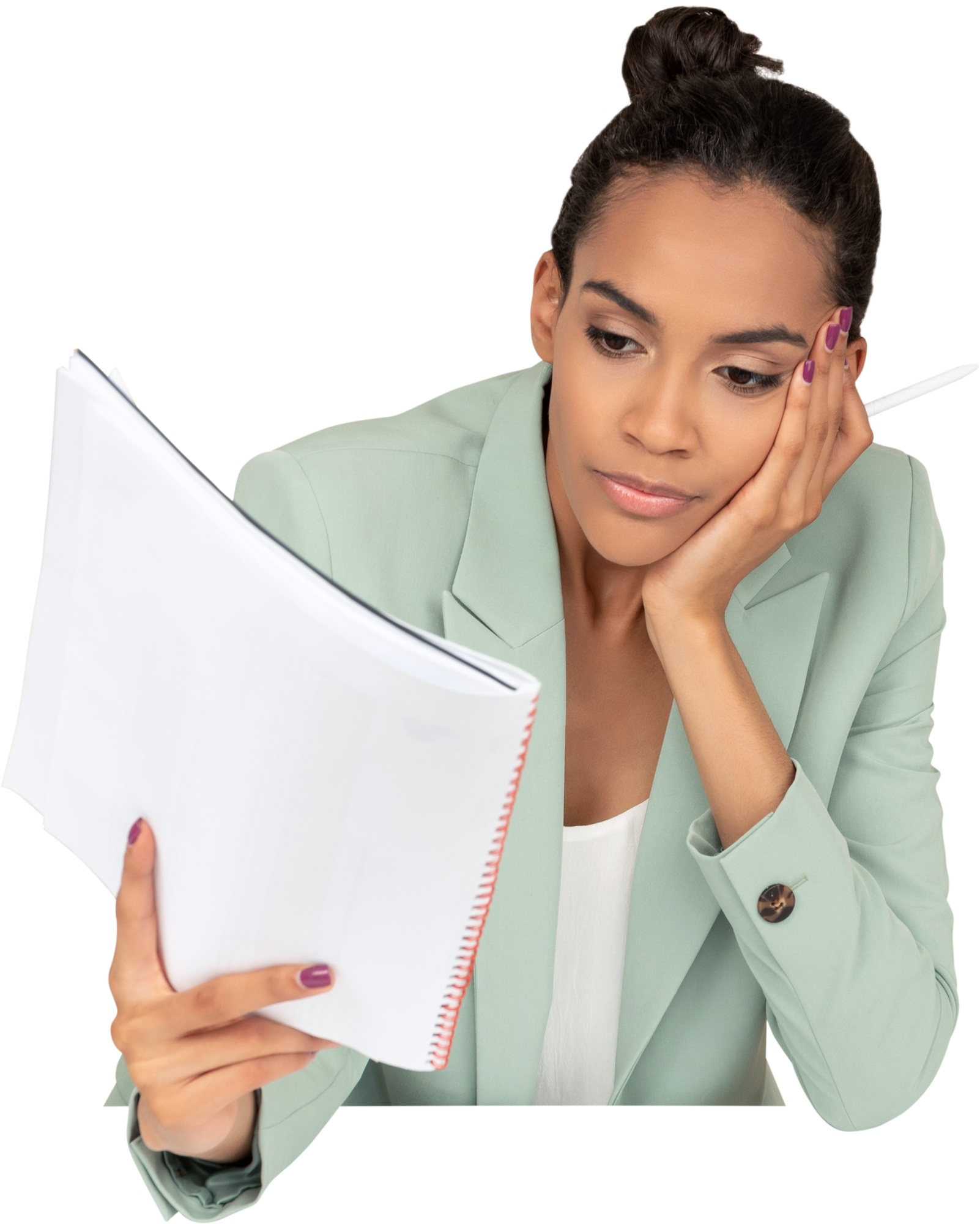
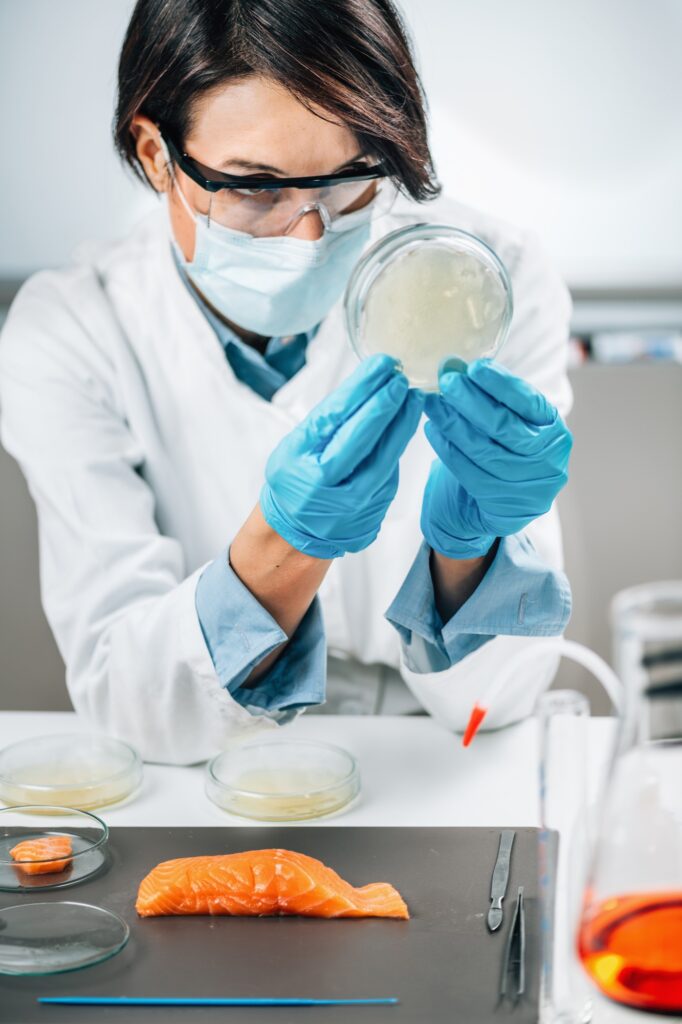
Nonconformance
Nonconformance involves product-specific issues that compromise safety or effectiveness. These issues often arise when a product fails a quality test or does not meet specifications. For example, a batch of tablets with inconsistent active ingredient levels poses a safety risk. Teams must act quickly to identify the problem and quarantine affected products. By addressing nonconformance immediately, organizations protect consumers and maintain compliance with regulations. Clear procedures help teams document nonconformance, evaluate the root cause, and take corrective action promptly.
Managing nonconformance requires a structured approach to minimize risks and ensure compliance. First, teams investigate the issue using proven methods like root cause analysis. Then, they implement corrective actions to resolve the problem and prevent recurrence. Regular audits and inspections help detect nonconformance early and reduce potential impact. Effective communication across departments ensures everyone understands their roles in resolving the issue.
By managing nonconformance diligently, companies protect their reputation and enhance their quality systems. This proactive approach strengthens processes and ensures consistent product safety and efficacy.
Key Principles from ICH Q10 for Deviation Management
Lifecycle Approach
Address deviations at every stage of the product lifecycle to ensure continuous improvement.
Knowledge Management
Use deviation data to enhance organizational knowledge and optimize processes.
CAPA Effectiveness
Monitor and assess CAPA to prevent recurring deviations and improve processes.
Management Oversight
Ensure leadership involvement in reviewing deviation trends and implementing systemic improvements.
Regulatory Expectations for Deviation Management
FDA Perspective
The FDA prioritizes effective deviation management to ensure quality and safety in pharmaceutical manufacturing. According to 21 CFR Part 211, manufacturers must investigate every deviation and document findings in detail. These requirements emphasize the importance of transparency and accountability in quality processes. Companies must identify the root cause of deviations, implement corrective actions, and monitor results. By following these guidelines, organizations can address potential risks and maintain product integrity. Clear documentation of deviation investigations also helps during audits and inspections, reducing compliance risks.
Adopting robust deviation management practices ensures manufacturers meet FDA expectations and avoid penalties. Thorough records of investigations and CAPA actions demonstrate a strong commitment to quality and compliance. These practices also improve operational efficiency by preventing recurring issues and optimizing processes. Companies that prioritize deviation management gain a competitive edge by building trust with regulators and customers. Additionally, effective management of deviations helps organizations identify improvement opportunities within their Quality Management System (QMS). With consistent adherence to FDA guidelines, businesses can strengthen their reputation and ensure long-term success.
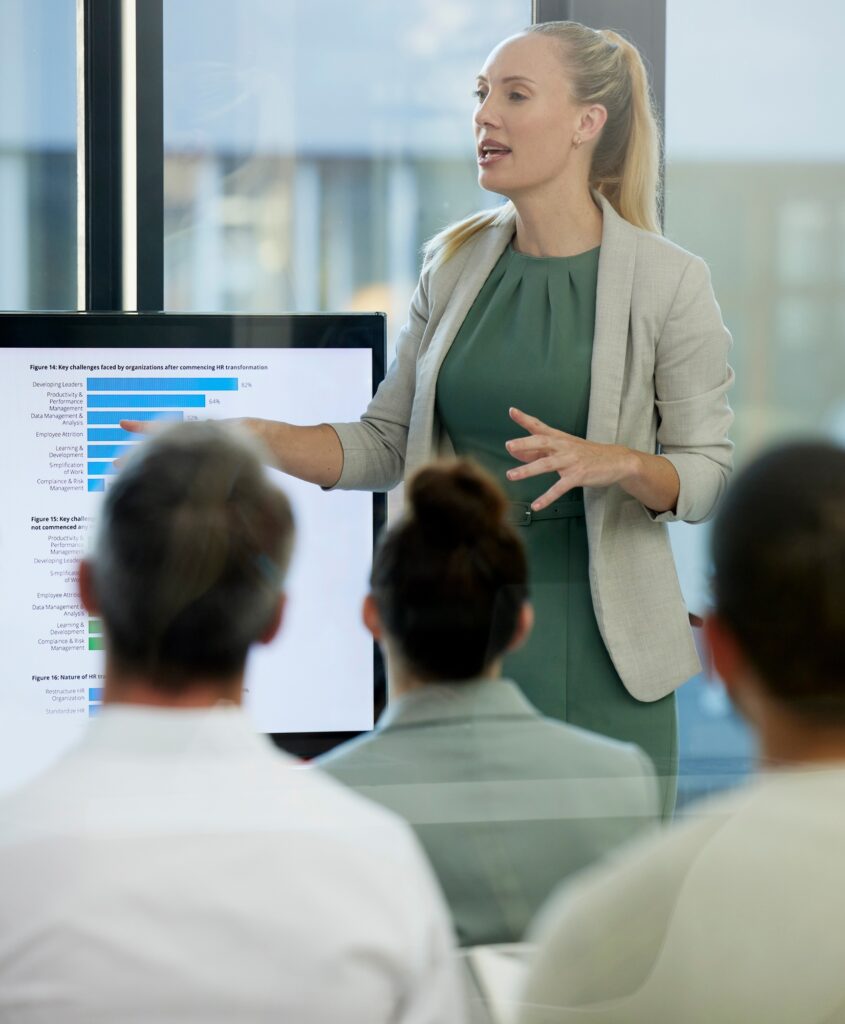
EU GMP Chapter 8 Guidelines
EU GMP Chapter 8 sets clear guidelines for managing deviations in pharmaceutical processes. It requires companies to classify deviations based on their severity and potential impact. Teams must document every deviation thoroughly, including details about the root cause and corrective actions. This systematic approach ensures transparency and helps organizations identify recurring patterns. By following these steps, companies can resolve issues quickly and minimize disruptions. Regularly reviewing deviation records helps teams spot trends and improve overall process quality.
Consistently adhering to EU GMP Chapter 8 reduces the risk of regulatory noncompliance and ensures smoother audits. Addressing deviations effectively also enhances product quality, ensuring safety and reliability for consumers. Implementing CAPA systematically strengthens internal processes and prevents similar deviations in the future. Companies that follow these guidelines build trust with customers and regulatory bodies alike. By prioritizing deviation management, organizations improve operational efficiency and maintain compliance with strict industry standards. This proactive approach fosters long-term success and supports continuous improvement in manufacturing processes.
WHO Guidelines for Deviation Handling
The World Health Organization (WHO) highlights the importance of efficient deviation management to protect public health. WHO guidelines require companies to document deviations clearly and include all relevant details. Teams must investigate deviations thoroughly to understand their root causes and potential impacts. Transparency in documentation helps organizations demonstrate compliance with global regulatory expectations. By addressing deviations systematically, companies strengthen their quality systems and reduce risks. Regularly reviewing deviation records also helps identify trends and implement preventive measures.
A strong CAPA framework plays a vital role in effective deviation handling under WHO guidelines. Teams must analyze root causes carefully to prevent recurring issues and improve processes. Implementing corrective actions promptly ensures immediate issues do not escalate further. Preventive actions help organizations avoid future deviations and maintain consistent quality. Verifying the effectiveness of CAPA actions builds confidence in the system and supports continuous improvement. Adhering to WHO guidelines enhances product safety and fosters trust with regulators worldwide. By prioritizing these practices, companies safeguard public health and ensure long-term success.
Common Problems in Deviation Processes
Inadequate Documentation
Poorly documented deviations hinder investigations. Use digital tools to streamline records and improve accuracy.
Lack of Root Cause Analysis
Superficial investigations fail to address underlying issues. Invest in training for effective root cause analysis techniques.
Delays in CAPA Implementation
Slow CAPA implementation increases risks. Establish clear timelines and responsibilities for CAPA actions.
Regulatory Complexity
Navigating various regulatory requirements can be overwhelming. Stay updated with evolving guidelines to ensure compliance.
Resistance to Change
Teams may resist new processes. Foster a culture of quality by emphasizing the benefits of robust deviation management.
Conclusion
Mastering deviation management is critical for achieving success in the pharmaceutical industry. It ensures product safety, builds regulatory compliance, and enhances operational efficiency. By addressing deviations promptly and thoroughly, companies can minimize risks and prevent recurring issues. Following industry guidelines from the FDA, EU GMP Chapter 8, ICH Q10, and WHO strengthens quality systems and boosts confidence in processes. These practices not only safeguard public health but also improve organizational reliability and reputation.
To excel in deviation management, businesses must embrace modern solutions and prioritize continuous improvement. Automation simplifies processes, reduces human errors, and enhances efficiency in documentation and investigation. Investing in regular training ensures teams stay updated on best practices and regulatory expectations. Focusing on CAPA effectiveness helps organizations resolve issues swiftly and prevent future deviations. By adopting these strategies, companies can create a culture of quality and drive long-term success. Proactive deviation management empowers organizations to meet challenges confidently and maintain compliance in a highly regulated industry.
References
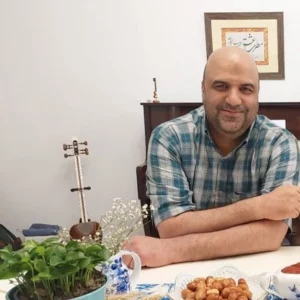
Ershad Moradi
Ershad Moradi, a Content Marketing Specialist at Zamann Pharma Support, brings 6 years of experience in the pharmaceutical industry. Specializing in pharmaceutical and medical technologies, Ershad is currently focused on expanding his knowledge in marketing and improving communication in the field. Outside of work, Ershad enjoys reading and attending industry related networks to stay up-to-date on the latest advancements. With a passion for continuous learning and growth, Ershad is always looking for new opportunities to enhance his skills and contribute to pharmaceutical industry. Connect with Ershad on Facebook for more information.
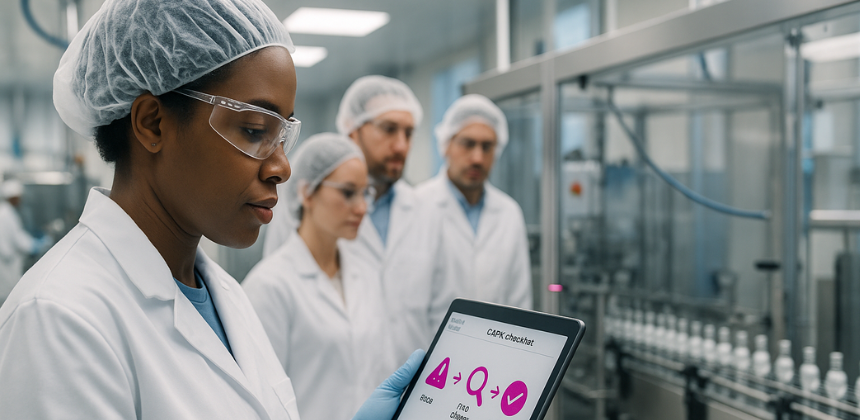
What Is a CAPA Plan? A Beginner’s Guide
This beginner’s guide explains CAPA plans in plain language. You’ll define problems clearly, analyze root causes with proven tools, and turn findings into targeted corrective and preventive actions. Then, you’ll verify effectiveness with metrics and close confidently.

Computerized Maintenance Management: The Complete 2025 Guide
This guide explores computerized maintenance management with practical strategies, CMMS comparisons, and implementation tips. Designed for professionals, entrepreneurs, and job seekers, it helps you choose the right tools, optimize workflows, and boost ROI with preventive and predictive maintenance methods.
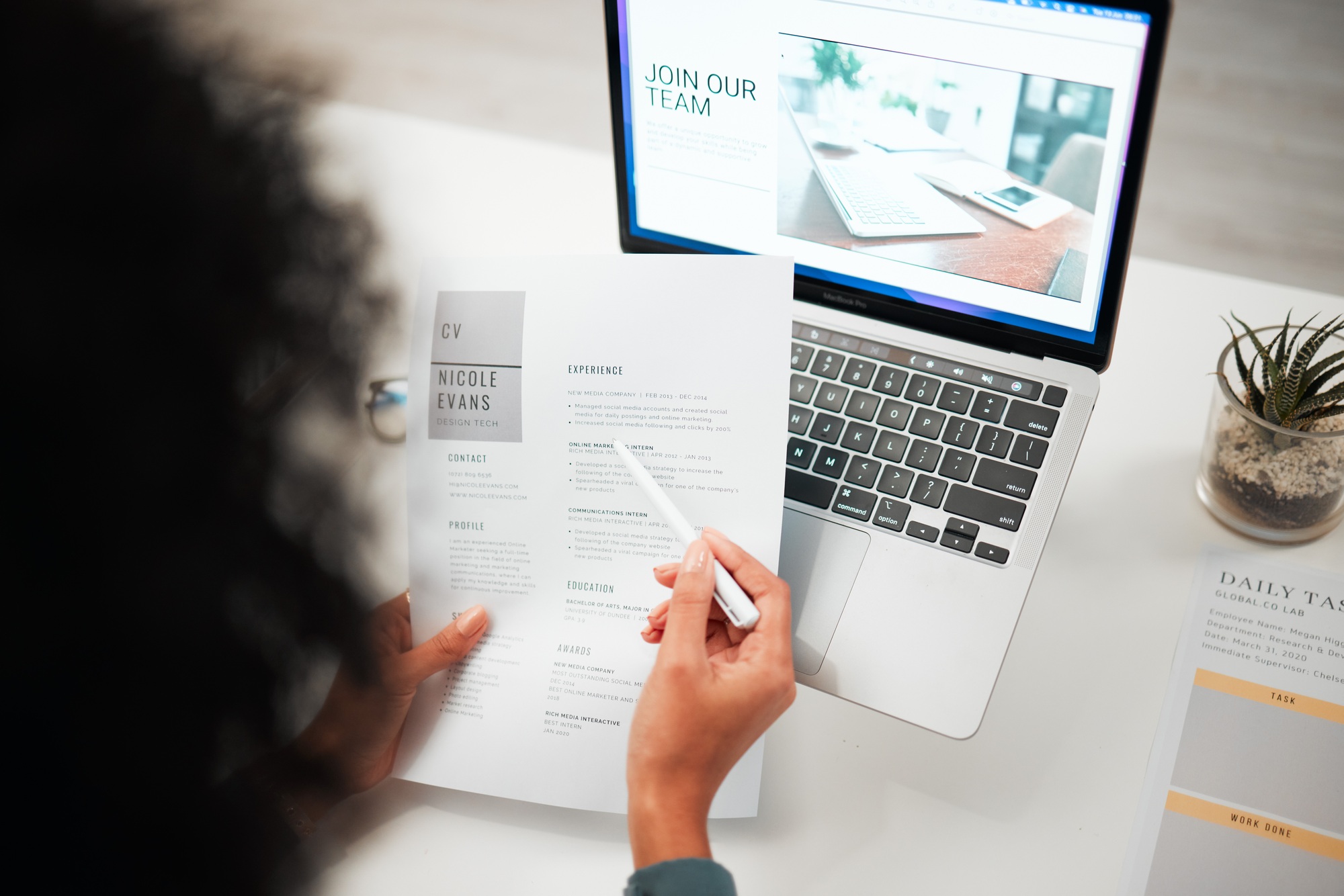
How to Choose the Right Special Skills for Resume Success
Learn how to choose, organize, and present special skills for resume success. This guide includes technical and soft skills, comparison tables, and AI-friendly strategies to pass ATS filters and stand out in competitive job markets.