Continuous improvement helps organizations maintain high-quality standards and adapt to changes. This approach involves making incremental improvements to processes, products, and services over time. In the pharmaceutical industry, continuous improvement ensures compliance with regulations and enhances product quality. Companies use proven frameworks to implement continuous improvement and achieve operational excellence. These strategies help improve efficiency, reduce risks, and enhance customer satisfaction.
In this article, we will define continuous improvement, describe key procedures, and list actionable guidelines. We will also discuss the main objectives and key performance indicators for tracking success. Additionally, we will explore the PDCA model.
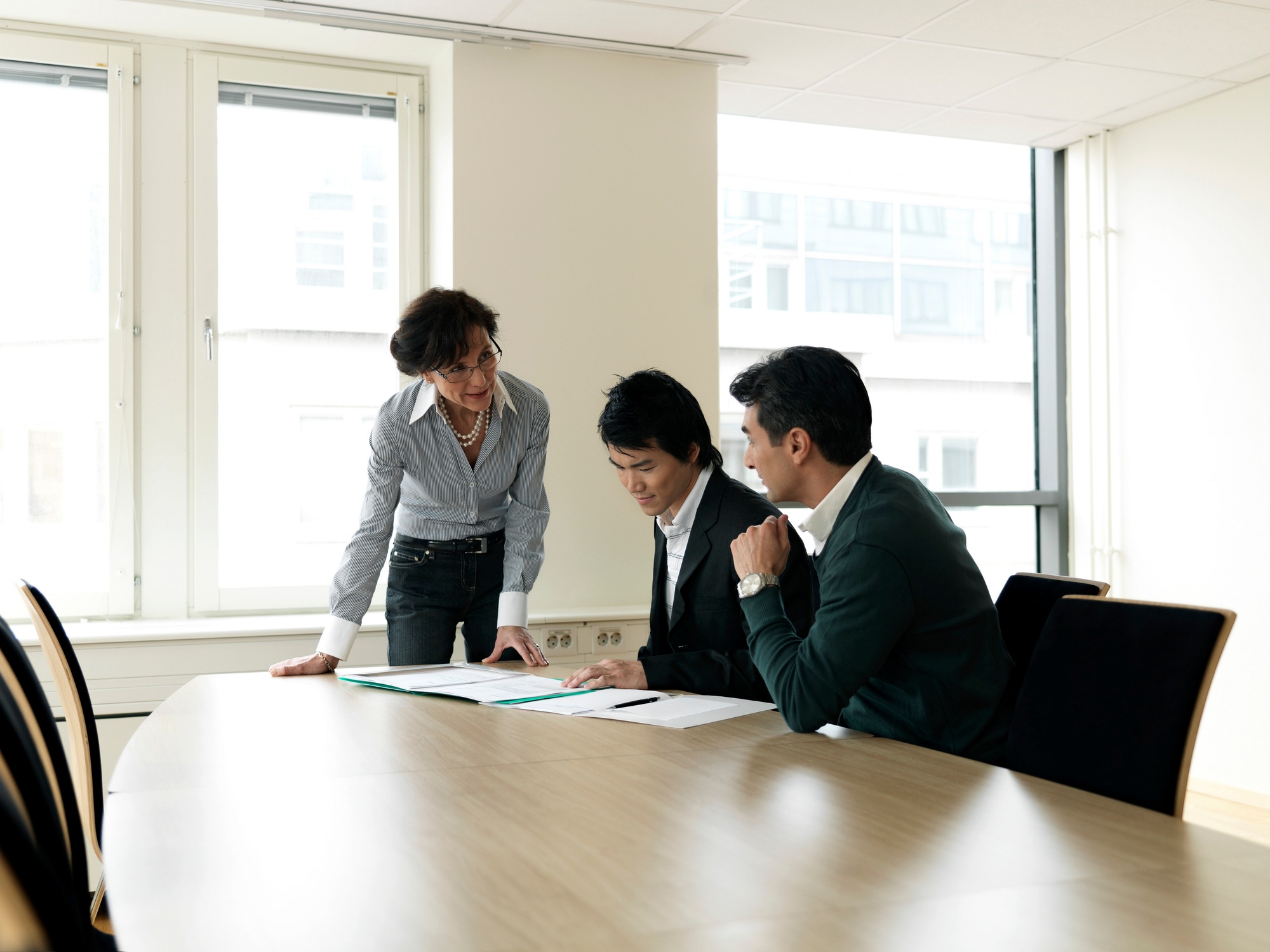
Definition and Importance of Continuous Improvement
Continuous improvement means systematically enhancing processes to achieve better outcomes. Companies use this approach to reduce errors, improve efficiency, and maintain product quality. They consistently evaluate current methods and identify areas for refinement. This ongoing effort allows organizations to keep up with changing industry standards. Additionally, continuous improvement encourages teams to develop innovative solutions. As a result, businesses can adapt quickly and enhance their overall performance. By focusing on small, manageable changes, companies create sustainable progress over time.
In the pharmaceutical industry, continuous improvement plays a key role in ensuring compliance with GMP. Companies must meet strict regulatory requirements while maintaining consistent product quality. Regular process evaluations help identify deviations and address them early. This proactive approach reduces risks and prevents costly errors. Continuous improvement also helps optimize resource usage and minimize waste. As companies streamline operations, they lower production costs while maintaining high standards. Moreover, fostering a culture of improvement boosts employee engagement.
Sign up for Introduction to GMP Quality Management Systems Course
Procedures in Implementing Continuous Improvement
Organizations must follow structured procedures to implement continuous improvement effectively. Below are the key steps:
Identifying Areas for Improvement
Teams assess current processes to identify gaps and opportunities for enhancement.
Setting Clear Objectives
Companies define specific, measurable goals for improvement initiatives.
Developing Action Plans
Teams create detailed plans outlining tasks, responsibilities, and timelines.
Implementing Changes
Organizations execute the planned changes while ensuring minimal disruption to operations.
Monitoring Results
Teams track progress and gather data to measure the effectiveness of changes.
Refining Processes
Based on the results, companies make further adjustments to optimize processes.
Main Objectives of Continuous Improvement
Enhancing Product Quality and Safety
Continuous improvement ensures companies consistently deliver high-quality and safe products to customers. Organizations achieve this by regularly reviewing processes and identifying areas needing enhancement. They then refine these processes to reduce defects and prevent errors. This proactive approach minimizes risks and helps maintain consistent product quality. As a result, companies can better meet customer expectations and regulatory requirements. Additionally, continuous improvement fosters a systematic way of thinking about problem-solving. By focusing on small, incremental changes, companies build long-term stability and success.
Moreover, continuous improvement helps businesses enhance customer satisfaction by delivering reliable products. When organizations reduce errors, customers gain trust in the product’s safety and performance. This trust strengthens the company’s reputation in the market, driving long-term growth. Companies also use improvement strategies to increase efficiency and lower production costs. By refining workflows and reducing waste, they achieve better results with fewer resources. Furthermore, a culture of continuous improvement encourages collaboration and innovation among employees.
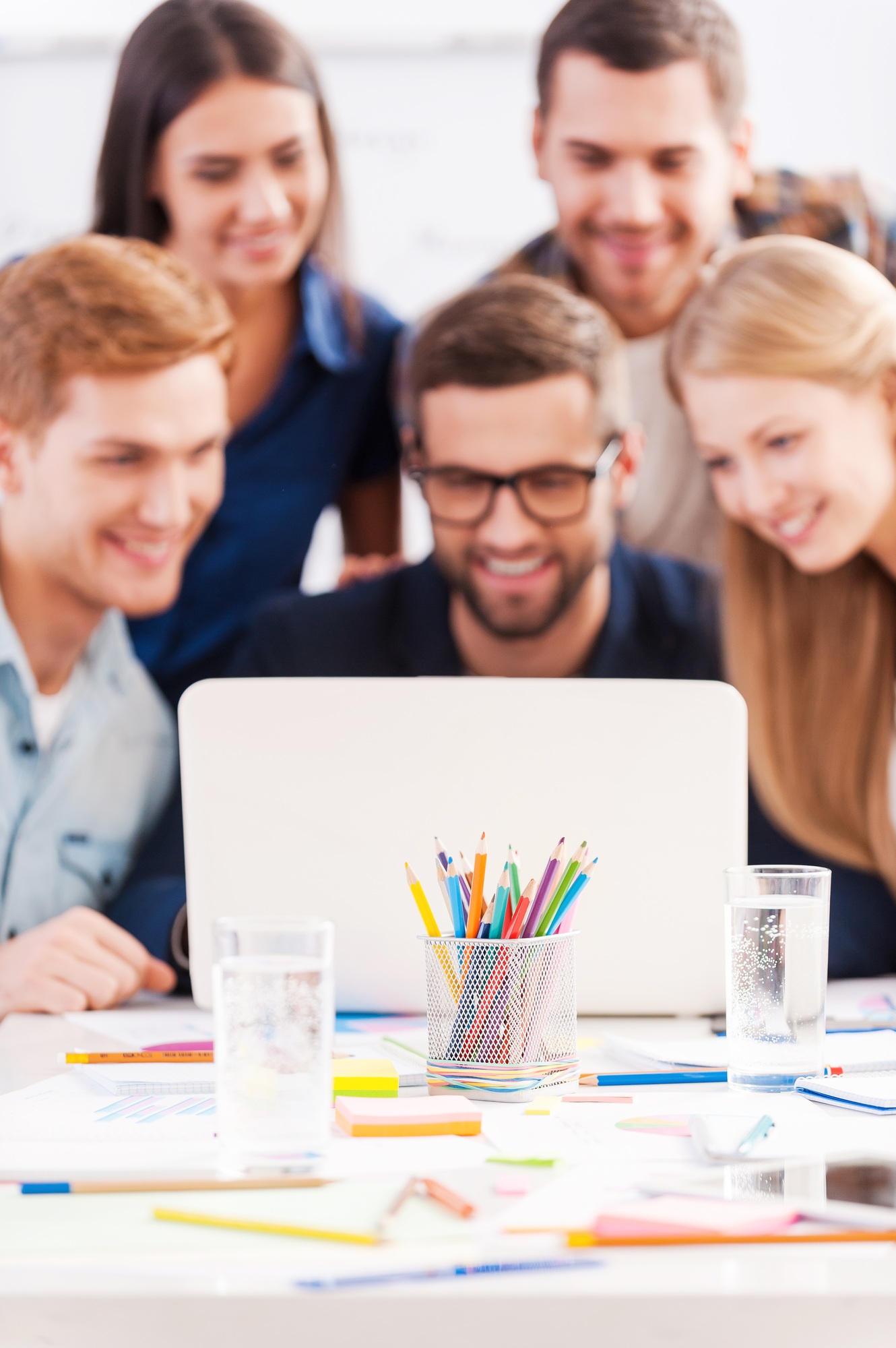
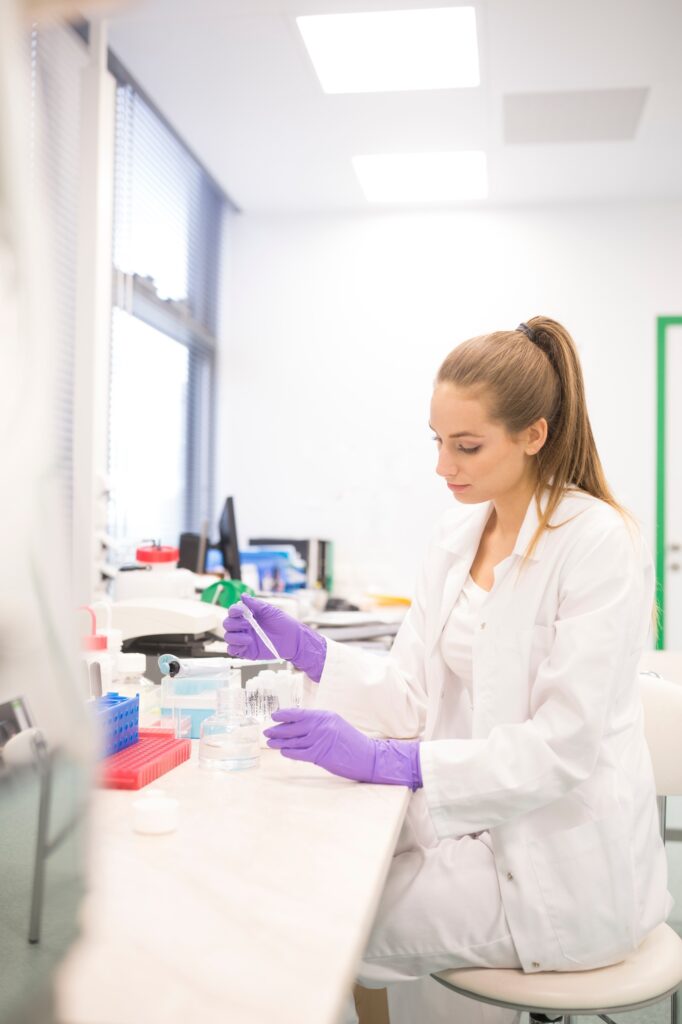
Ensuring Regulatory Compliance
In regulated industries like pharmaceuticals, continuous improvement helps companies maintain compliance with strict standards. Regular process evaluations allow organizations to identify potential issues before they become serious problems. Audits also play a key role by ensuring that processes consistently meet regulatory requirements. When companies focus on continuous improvement, they reduce risks associated with non-compliance. This proactive approach minimizes the likelihood of receiving costly penalties from regulatory bodies. Moreover, regular improvements strengthen internal controls and boost operational efficiency. As a result, organizations can better handle evolving regulations and industry expectations.
Continuous improvement also enhances a company’s ability to implement effective corrective actions. When audits or evaluations reveal issues, companies can quickly address them and prevent recurrence. This quick response reduces downtime and keeps production running smoothly. Additionally, by fostering a culture of improvement, companies encourage employees to follow best practices. This focus on compliance ensures consistent product quality and safety. Furthermore, continuous improvement reduces costs by optimizing resources and eliminating unnecessary steps. Over time, companies experience fewer disruptions and better overall performance.
Key Performance Indicators for Continuous Improvement
Monitoring the success of continuous improvement requires tracking specific metrics. Below are key performance indicators (KPIs) that help measure progress:
Rate of Process Improvements
This KPI tracks the number of successful improvement initiatives over time.
Defect Reduction Percentage
Measuring defect reduction helps evaluate the impact of process enhancements on product quality.
Cycle Time Reduction
This metric tracks how much time is saved by optimizing processes.
Compliance Audit Findings
A lower number of audit findings indicates effective continuous improvement practices.
Employee Participation Rate
High participation rates in improvement initiatives reflect an engaged workforce.
Guidelines for Effective Continuous Improvement
Establishing a Clear Improvement Framework
Organizations need to create a structured framework to guide their continuous improvement efforts effectively. This framework provides a clear path for implementing changes and achieving desired outcomes. By defining clear policies, companies ensure that every team understands improvement expectations. Clear roles and responsibilities help employees know their specific duties in the improvement process. When teams understand their tasks, they collaborate better and complete projects faster. Additionally, a structured framework promotes consistency by standardizing procedures across different departments. This consistency reduces errors and improves overall process reliability.
Moreover, a well-defined framework strengthens accountability within the organization. Assigning roles ensures that team members take ownership of their tasks. When employees feel responsible for outcomes, they focus more on delivering quality results. Regular reviews within the framework help track progress and identify improvement opportunities. These reviews also allow managers to recognize and reward successful initiatives. Furthermore, setting measurable goals ensures that teams stay motivated and aligned with company objectives.
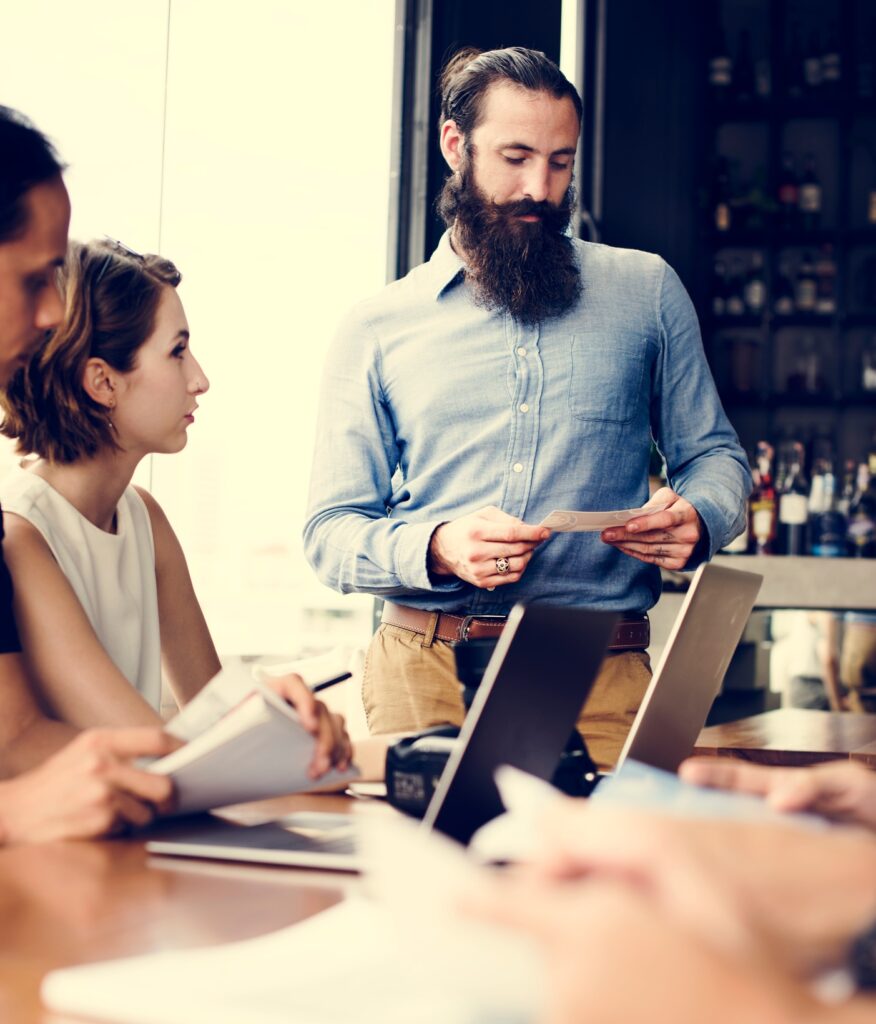
Encouraging a Culture of Improvement
Building a culture that encourages employees to suggest and implement improvements drives long-term success. Companies need to involve employees at all levels to foster a sense of ownership. When employees feel valued, they actively participate in generating new improvement ideas. Providing regular opportunities for feedback helps spark innovation and strengthens collaboration across teams. Additionally, managers should create open communication channels to promote idea-sharing. This inclusive approach boosts employee morale and keeps teams motivated to contribute. Over time, companies can build a steady flow of ideas that enhance overall performance.
Moreover, companies must invest in training programs to develop a mindset of continuous learning. Training equips employees with the skills needed to identify improvement opportunities. By offering regular workshops, businesses ensure that employees stay updated with the latest industry practices. Continuous support also helps employees feel confident in applying their knowledge. Furthermore, recognizing employees for their improvement efforts encourages further participation.
Applying the PDCA Model for Continuous Improvement
Planning and executing changes effectively requires a structured approach like the Plan-Do-Check-Act (PDCA) model. During the planning phase, teams identify specific areas that need improvement. They gather data, analyze issues, and create detailed action plans to address gaps. By setting clear objectives, companies ensure everyone understands the expected outcomes. Once the plans are ready, teams move on to the execution phase. During this phase, they implement changes while closely monitoring progress. Regular monitoring helps teams track results and detect potential problems early. With this method, organizations can make informed adjustments and achieve better results.
After implementing changes, teams need to review the outcomes and gather feedback. This step involves analyzing data to measure the success of the improvements. Teams then identify lessons learned and document findings for future reference. Using this information, they refine existing processes and improve future action plans. By repeating this cycle, organizations continuously enhance their operations and maintain high-quality standards. Furthermore, this systematic approach helps businesses stay agile and respond quickly to new challenges. Over time, repeating the PDCA cycle ensures ongoing quality assurance and operational excellence.
Key Factors for Success in Continuous Improvement
Strong Leadership Commitment
Success in continuous improvement starts with committed leadership. Leaders set the tone by promoting a culture of innovation and supporting improvement initiatives.
Employee Engagement and Involvement
Engaging employees ensures a consistent flow of improvement ideas. Companies achieve better results when employees feel empowered to suggest and implement changes.
Clear and Measurable Goals
Defining measurable goals helps teams stay focused on improvement efforts. Clear objectives also enable companies to track progress and assess success effectively.
Regular Training and Development
Ongoing training equips employees with the skills to drive improvements. Companies that invest in development create a knowledgeable workforce ready to adapt to changes.
Data-Driven Decision-Making
Using data ensures objective decision-making during improvement initiatives. Companies can identify trends and make evidence-based adjustments for optimal results.
Conclusion
Continuous improvement plays a vital role in ensuring quality assurance and compliance in the pharmaceutical industry. By following structured procedures, setting clear objectives, and tracking key performance indicators, companies can enhance product quality and safety. The PDCA model provides a proven framework for achieving continuous improvement. Additionally, learning from successful companies can inspire organizations to adopt best practices. Embracing continuous improvement not only ensures compliance but also drives long-term success in a competitive market.
References
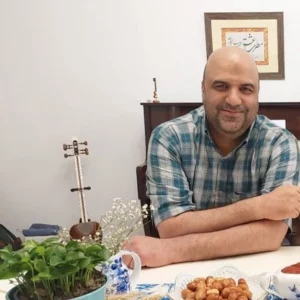
Ershad Moradi
Ershad Moradi, a Content Marketing Specialist at Zamann Pharma Support, brings 6 years of experience in the pharmaceutical industry. Specializing in pharmaceutical and medical technologies, Ershad is currently focused on expanding his knowledge in marketing and improving communication in the field. Outside of work, Ershad enjoys reading and attending industry related networks to stay up-to-date on the latest advancements. With a passion for continuous learning and growth, Ershad is always looking for new opportunities to enhance his skills and contribute to pharmaceutical industry. Connect with Ershad on Facebook for more information.
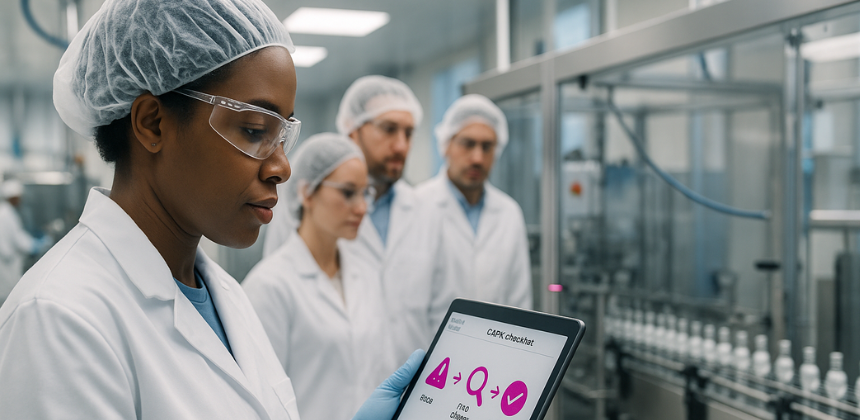
What Is a CAPA Plan? A Beginner’s Guide
This beginner’s guide explains CAPA plans in plain language. You’ll define problems clearly, analyze root causes with proven tools, and turn findings into targeted corrective and preventive actions. Then, you’ll verify effectiveness with metrics and close confidently.

Computerized Maintenance Management: The Complete 2025 Guide
This guide explores computerized maintenance management with practical strategies, CMMS comparisons, and implementation tips. Designed for professionals, entrepreneurs, and job seekers, it helps you choose the right tools, optimize workflows, and boost ROI with preventive and predictive maintenance methods.
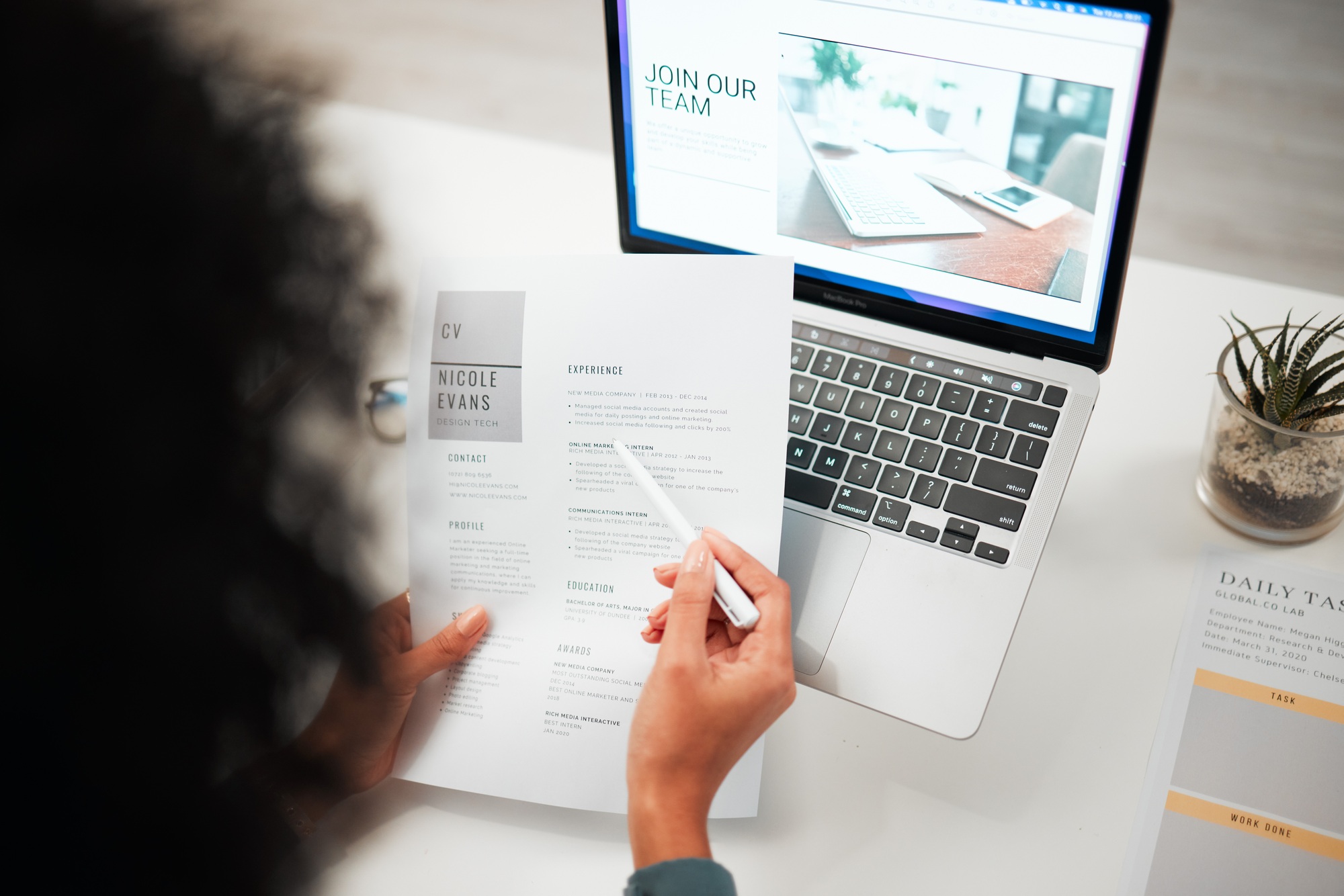
How to Choose the Right Special Skills for Resume Success
Learn how to choose, organize, and present special skills for resume success. This guide includes technical and soft skills, comparison tables, and AI-friendly strategies to pass ATS filters and stand out in competitive job markets.