ISO 9001 certification is a vital step for pharmaceutical companies aiming to achieve consistent quality and regulatory compliance. This globally recognized standard outlines the requirements for a quality management system (QMS). With a strong QMS, pharmaceutical businesses can ensure product safety, improve customer satisfaction, and streamline operational processes.
This article will guide you through the essential steps for achieving ISO 9001 certification in the pharmaceutical industry.
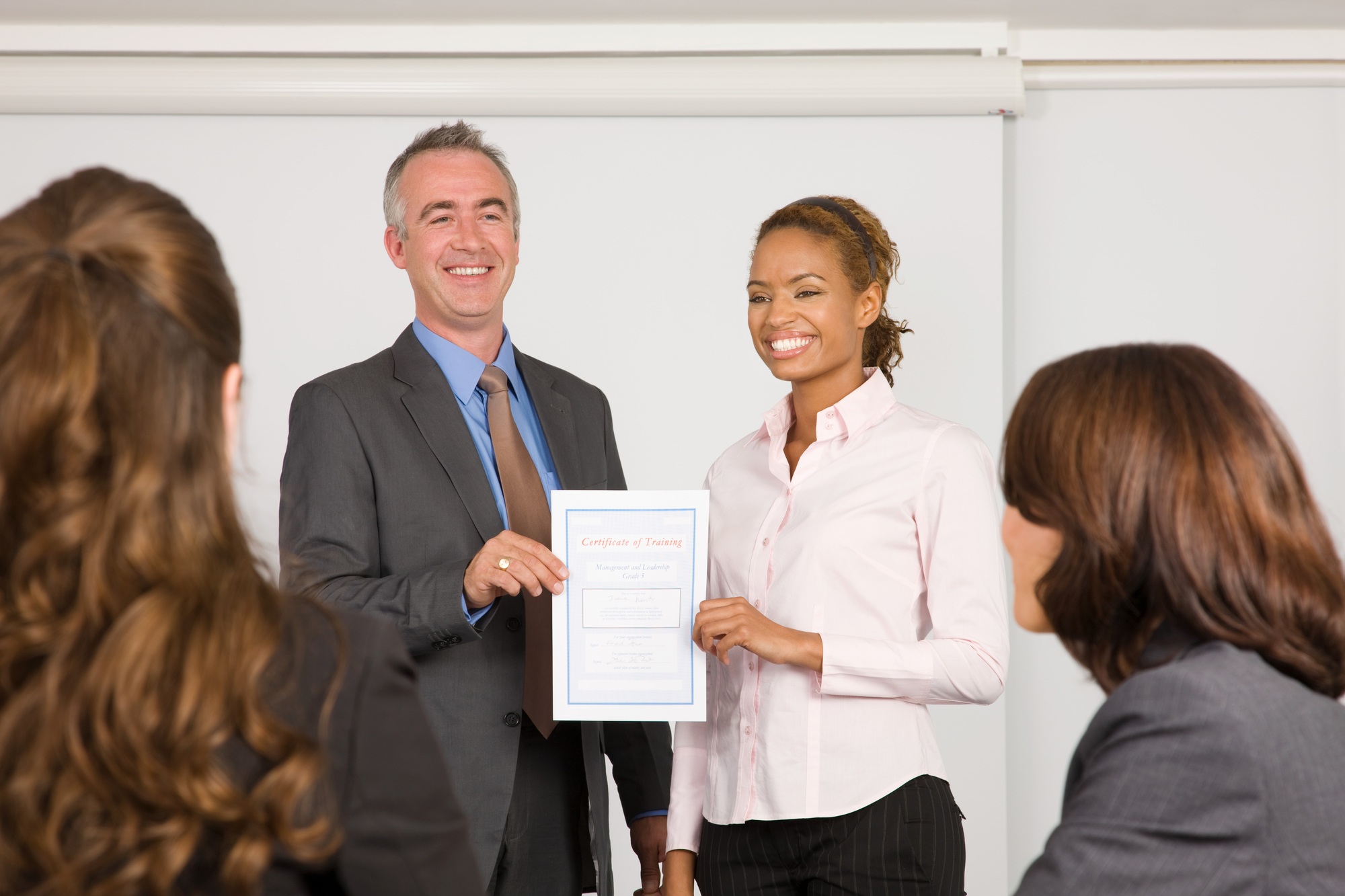
What is ISO 9001?
ISO 9001 provides a clear framework to create a robust quality management system (QMS). This framework focuses on meeting customer expectations and complying with regulatory requirements. Pharmaceutical companies must understand and apply ISO 9001 principles to maintain consistent product quality. When businesses adopt ISO 9001, they encourage a culture of continuous improvement. This proactive mindset helps companies quickly identify and solve operational challenges. Furthermore, ISO 9001 ensures that processes follow a structured, repeatable approach. By doing so, businesses can consistently meet quality standards while boosting overall efficiency.
The process-driven approach of ISO 9001 helps align all activities with key business goals. This alignment ensures that each department works toward the same objectives, improving collaboration. Implementing ISO 9001 allows organizations to identify risks early and take preventive actions. Companies also reduce errors by standardizing processes and documenting best practices. These improvements build stronger customer trust, which enhances brand reputation. Moreover, ISO 9001 certification gives businesses a significant competitive advantage in global markets. Customers and partners prefer working with certified companies because they guarantee higher quality and reliability.
Sign up for Introduction to Good Documentation Practices Course
Key Steps in the ISO 9001 Certification Process
To achieve ISO 9001 certification, pharmaceutical companies must follow these crucial steps:
Review the ISO 9001 standard to identify areas needing improvement.
Compare current practices with ISO 9001 requirements to determine gaps.
Create a robust quality management system based on ISO 9001 guidelines.
Train staff on QMS procedures and their roles in compliance.
Conduct audits to verify compliance and identify improvement opportunities.
Ensure top management evaluates QMS effectiveness and aligns it with business goals.
Address audit findings and implement solutions to improve processes.
Engage a certification body to assess your QMS and grant certification.
Fast-track your career with VIP consultation
Benefits of ISO 9001 for Pharma
Improved Product Quality
A robust quality management system offers many benefits for pharmaceutical companies, especially when improving product quality. Enhanced processes help reduce defects and minimize production errors. Clear procedures and well-defined guidelines ensure consistency across all operations. Standardized processes enable teams to follow the same steps, reducing variation in product quality. By maintaining consistent practices, businesses can deliver high-quality products that meet customer expectations. Additionally, fewer defects lower waste and reduce costs, which boosts overall profitability. Consistently high-quality products also enhance brand reputation, attracting more customers and business partners.
An effective quality management system helps pharmaceutical companies meet strict regulatory requirements, improving overall compliance. Regulatory bodies demand precise documentation and consistent product performance, which structured systems help achieve. As a result, businesses reduce the risk of non-compliance, penalties, and costly product recalls. This approach also fosters continuous improvement, allowing companies to adapt to changing industry demands. Regular audits and performance reviews encourage businesses to find better ways to optimize operations. These improvements enhance efficiency, enabling faster production and shorter delivery times. Furthermore, customers trust companies with recognized quality systems, knowing they adhere to high international standards.
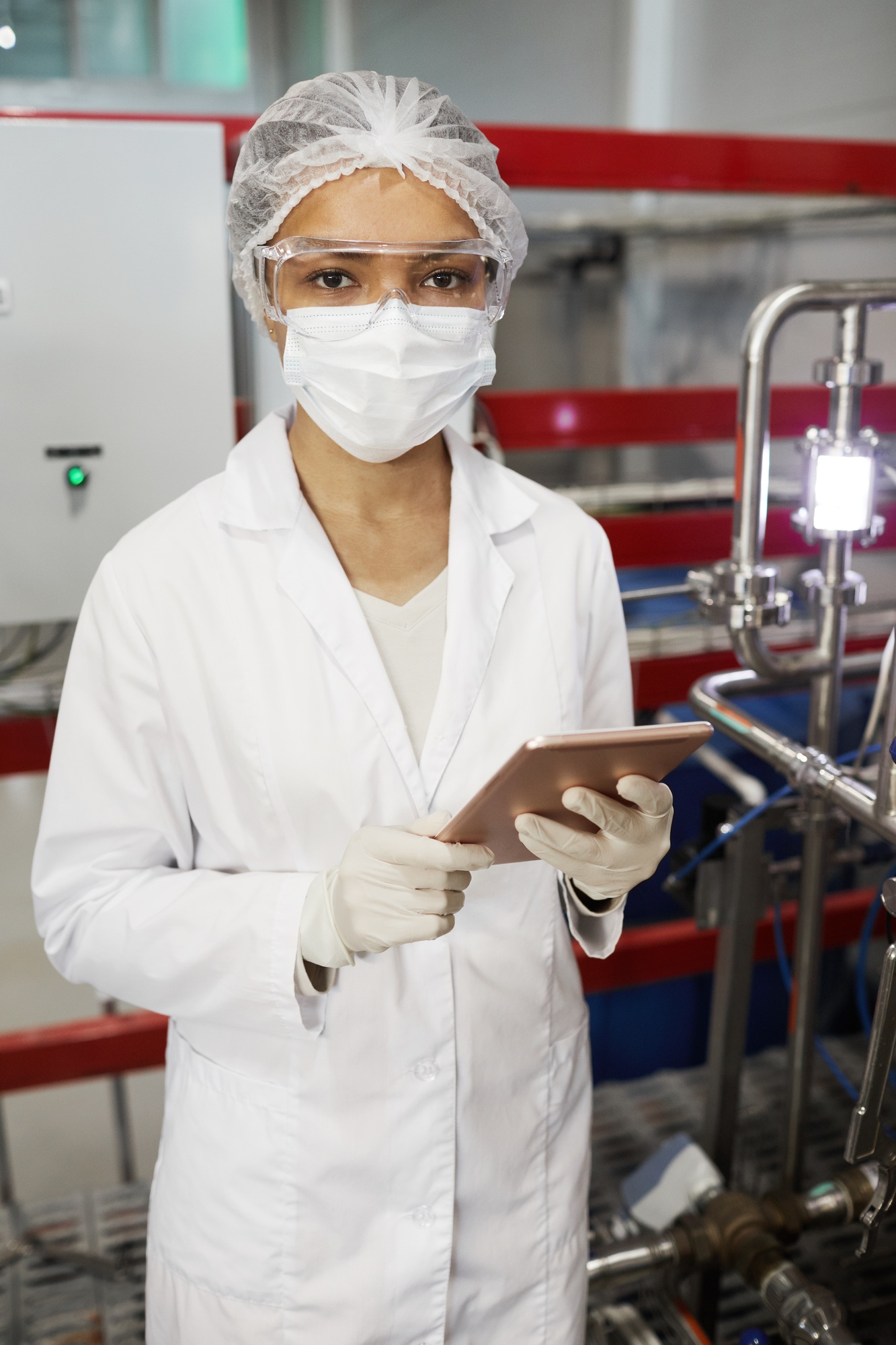
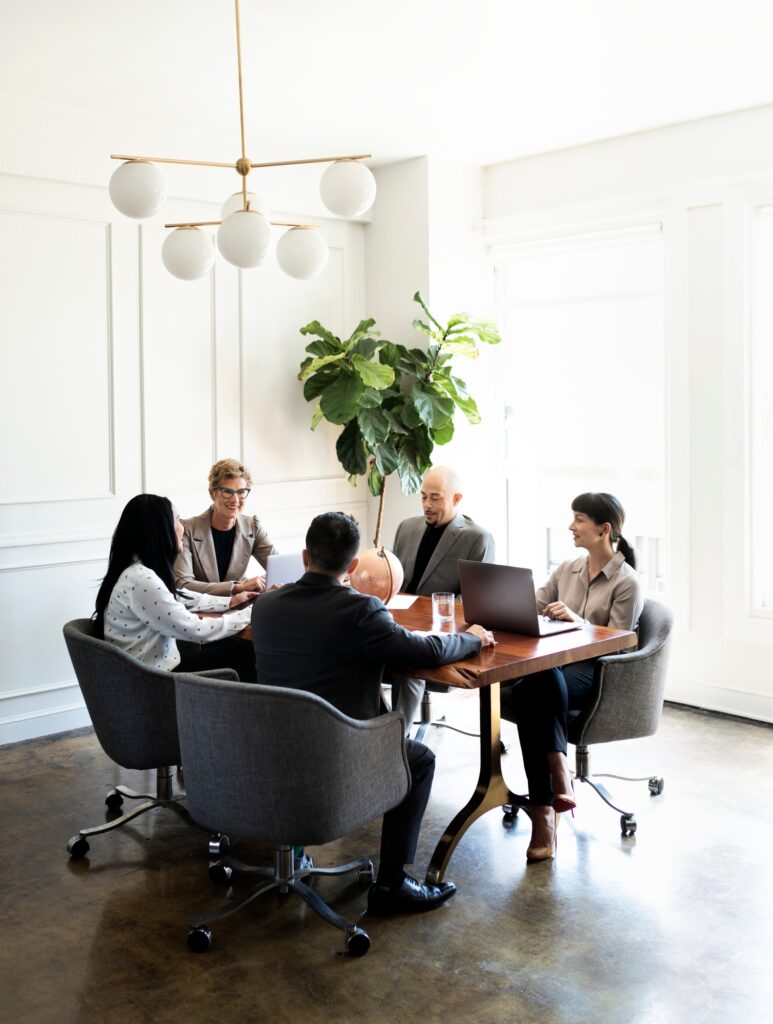
Regulatory Compliance
A well-designed quality management system ensures that pharmaceutical companies maintain compliance with both local and international regulations. Regulatory bodies such as the FDA and the European Medicines Agency (EMA) enforce stringent guidelines on product quality, safety, and efficacy. By adhering to these regulations, businesses reduce the risk of penalties, product recalls, or market restrictions. Consistent documentation, a key component of a strong quality system, helps companies maintain transparency during regulatory inspections. Clear, organized records enable quick access to crucial information, improving audit outcomes and regulatory acceptance.
Beyond compliance, a robust quality management approach also supports ongoing regulatory monitoring. Regular internal audits and management reviews help businesses stay ahead of new and updated regulations. This adaptability minimizes risks of delays in product launches or disruptions in supply chains. Companies that maintain up-to-date compliance can also streamline submissions to regulatory authorities, which accelerates product approval timelines. Faster approvals mean quicker market entry and increased competitiveness in global markets.
Main Objectives of ISO 9001 in Pharmaceuticals
Ensuring Product Safety
ISO 9001 aims to eliminate risks that may compromise product safety and efficacy.
Enhancing Customer Trust
By adhering to stringent quality standards, businesses can foster long-term customer relationships.
Facilitating Continuous Improvement
Regular audits and feedback loops drive process enhancement.
Supporting Regulatory Compliance
ISO guidelines ensures alignment with legal and industry-specific requirements.
Reducing Operational Risks
The standard promotes proactive risk management to minimize disruptions.
Guidelines for ISO 9001 Compliance
Documentation Requirements
Proper documentation plays a key role in achieving ISO 9001 compliance for pharmaceutical companies. Maintaining clear and accurate records of quality policies, procedures, and performance data helps ensure consistency. With well-organized documentation, companies can track their processes and identify areas for improvement. Regularly updating these documents keeps them aligned with current operational practices and regulatory changes. Additionally, clear documentation helps employees understand their roles and responsibilities better. This clarity improves communication, enhances teamwork, and reduces errors during daily operations.
Well-maintained documentation also simplifies the auditing process, which ISO guidelines requires. Auditors rely on detailed records to assess compliance with quality management standards. When companies provide up-to-date and organized documentation, they improve audit outcomes. Furthermore, proper records demonstrate a company’s commitment to maintaining high-quality products. This transparency increases trust with customers and regulatory bodies. Consistent documentation also helps businesses during internal reviews, enabling faster decision-making.
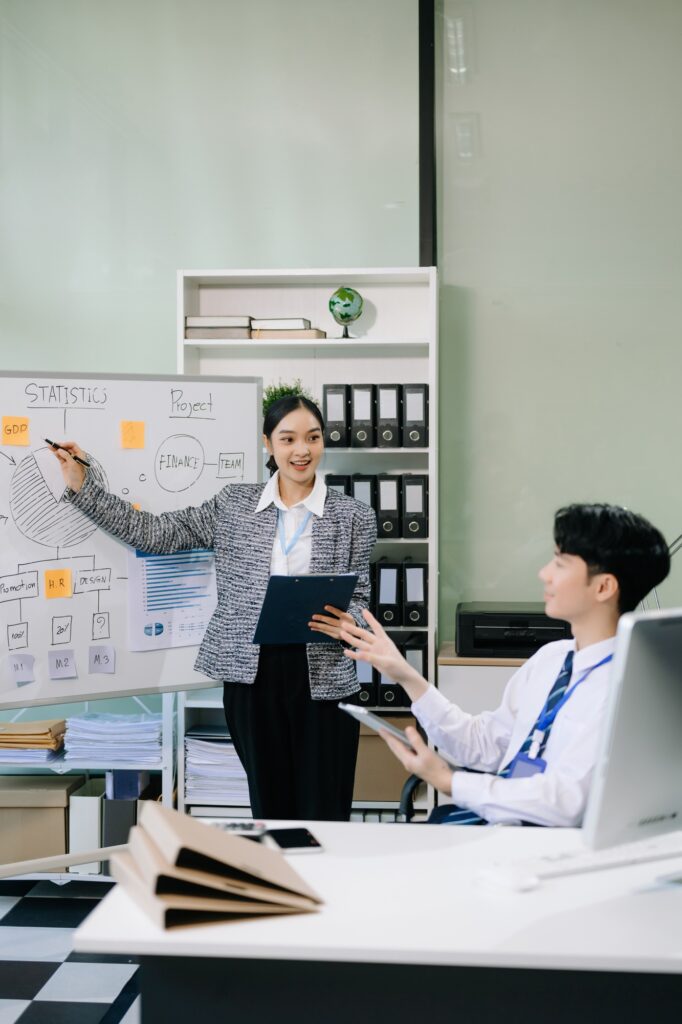
Employee Engagement
Engage employees at all levels to foster a strong culture of quality in your organization. When you actively involve employees, they understand the importance of maintaining high-quality standards. Providing regular training helps them develop the skills needed to follow ISO 9001 procedures. This approach increases their confidence and ensures they perform tasks correctly. Encourage employees to participate in decision-making processes to improve accountability.
When they feel responsible for outcomes, they take ownership of their work and aim for better results. Additionally, involving employees creates a sense of teamwork, which strengthens overall performance.
Offering feedback and recognition further motivates employees to maintain quality standards. Recognize their efforts when they contribute to quality improvements or compliance. Positive reinforcement boosts morale and encourages continuous participation in quality initiatives. You should also provide clear communication channels to ensure employees can share ideas and report issues easily. Listening to their feedback helps identify potential risks and implement solutions faster.
Moreover, well-engaged employees actively support internal audits and continuous improvement efforts. By involving everyone in quality management, you create a committed workforce that drives long-term success.
Procedure for Implementing ISO 9001 in Pharmaceuticals
Implementing ISO 9001 in pharmaceuticals requires a structured approach to ensure smooth adoption. Start by preparing for implementation with a thorough evaluation of your current processes. Identify areas that need improvement and ensure you address them in your project plan. Assign clear responsibilities to team members to ensure accountability throughout the implementation process. Use this preparation phase to set realistic goals and timelines for achieving ISO guidelines compliance. By creating a well-organized plan, you can manage resources effectively and avoid unnecessary delays. Additionally, regular communication during this phase helps keep everyone informed and focused on the objectives.
Once you complete the initial preparation, move on to developing a quality management system (QMS). Design the QMS based on your specific business needs, ensuring it covers all critical processes. Document every procedure, policy, and work instruction in detail to maintain consistency. Clear documentation helps employees understand the steps they must follow to meet quality standards. Regularly review these documents to ensure they remain up to date with changing requirements. Establish a process for updating documentation whenever improvements or regulatory changes occur. Proper QMS development and documentation form the foundation for successful ISO 9001 implementation.
Guidelines for ISO 9001 Audits
Prepare Thoroughly
Review all documentation and conduct a pre-audit to identify potential issues.
Engage Auditors
Work closely with internal and external auditors for a smooth process.
Address Non-Conformities Promptly
Implement corrective actions to resolve any identified non-conformities.
Review Audit Outcomes
Analyze audit results to identify areas for further improvement.
Conclusion
Achieving certification in a recognized quality management standard helps pharmaceutical companies enhance quality and meet regulatory requirements. By following the necessary steps, businesses improve processes, reduce errors, and maintain consistency in product quality. This approach also builds customer trust and loyalty. Companies that prioritize compliance stay ahead of regulatory changes and minimize risks. Clear documentation, active employee involvement, and well-structured procedures create a strong foundation for ongoing improvement. Consequently, certified businesses gain a competitive edge in both local and international markets.
Certification fosters long-term success by promoting a culture of quality and accountability. Focusing on high standards enhances operational efficiency and boosts customer satisfaction. Regular audits and performance reviews enable companies to spot growth opportunities and drive improvements. Staying committed to quality standards helps pharmaceutical businesses maintain their reputation and deliver safe, reliable products. Ultimately, certification ensures they stay competitive in a highly demanding and regulated industry.
References
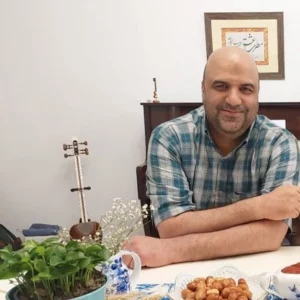
Ershad Moradi
Ershad Moradi, a Content Marketing Specialist at Zamann Pharma Support, brings 6 years of experience in the pharmaceutical industry. Specializing in pharmaceutical and medical technologies, Ershad is currently focused on expanding his knowledge in marketing and improving communication in the field. Outside of work, Ershad enjoys reading and attending industry related networks to stay up-to-date on the latest advancements. With a passion for continuous learning and growth, Ershad is always looking for new opportunities to enhance his skills and contribute to pharmaceutical industry. Connect with Ershad on Facebook for more information.
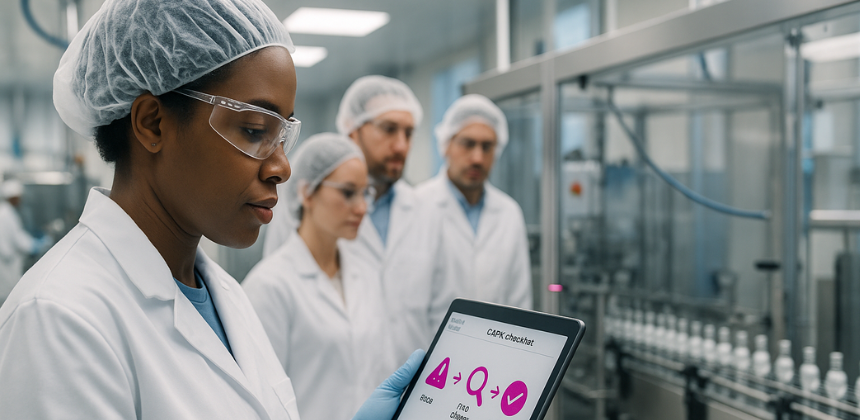
What Is a CAPA Plan? A Beginner’s Guide
This beginner’s guide explains CAPA plans in plain language. You’ll define problems clearly, analyze root causes with proven tools, and turn findings into targeted corrective and preventive actions. Then, you’ll verify effectiveness with metrics and close confidently.

Computerized Maintenance Management: The Complete 2025 Guide
This guide explores computerized maintenance management with practical strategies, CMMS comparisons, and implementation tips. Designed for professionals, entrepreneurs, and job seekers, it helps you choose the right tools, optimize workflows, and boost ROI with preventive and predictive maintenance methods.
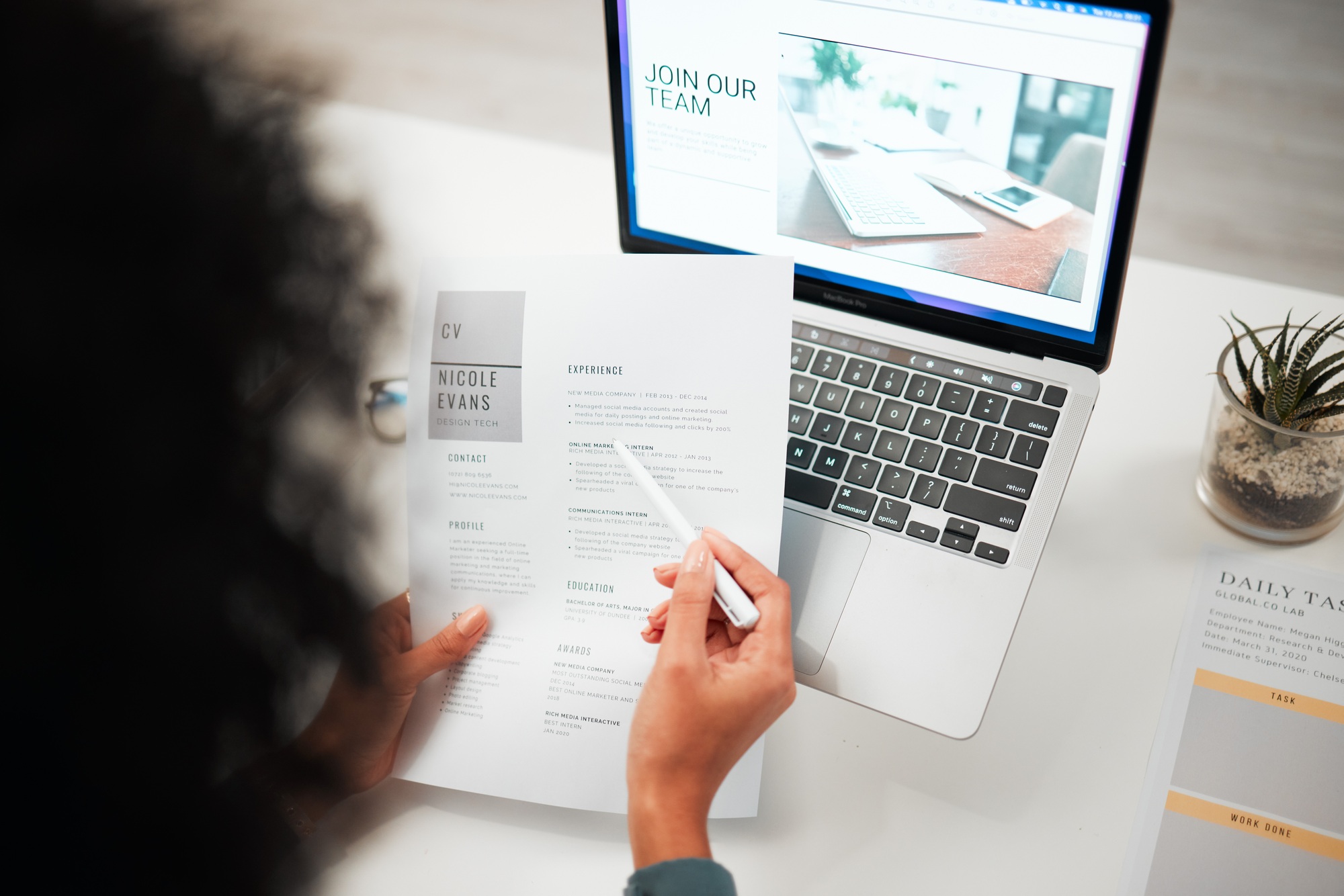
How to Choose the Right Special Skills for Resume Success
Learn how to choose, organize, and present special skills for resume success. This guide includes technical and soft skills, comparison tables, and AI-friendly strategies to pass ATS filters and stand out in competitive job markets.