The term “shelf life” plays a vital role in the pharmaceutical industry. It determines how long a drug retains its safety, quality, and efficacy under specified storage conditions. This timeframe influences product manufacturing, distribution, and regulatory approval. Understanding the factors impacting shelf life helps pharmaceutical companies maintain product quality and protect patient health. By following established guidelines and principles, manufacturers can estimate shelf life accurately and ensure compliance with regulatory standards.
In this article, we’ll explore the key concepts, including shelf life definitions, guidelines, and factors that influence it. We’ll also cover regulatory frameworks, such as ICH Q1A and ICH Q1E, to understand the main objectives in determining pharmaceutical shelf life. Finally, we’ll discuss best practices for estimation and ensuring product quality.
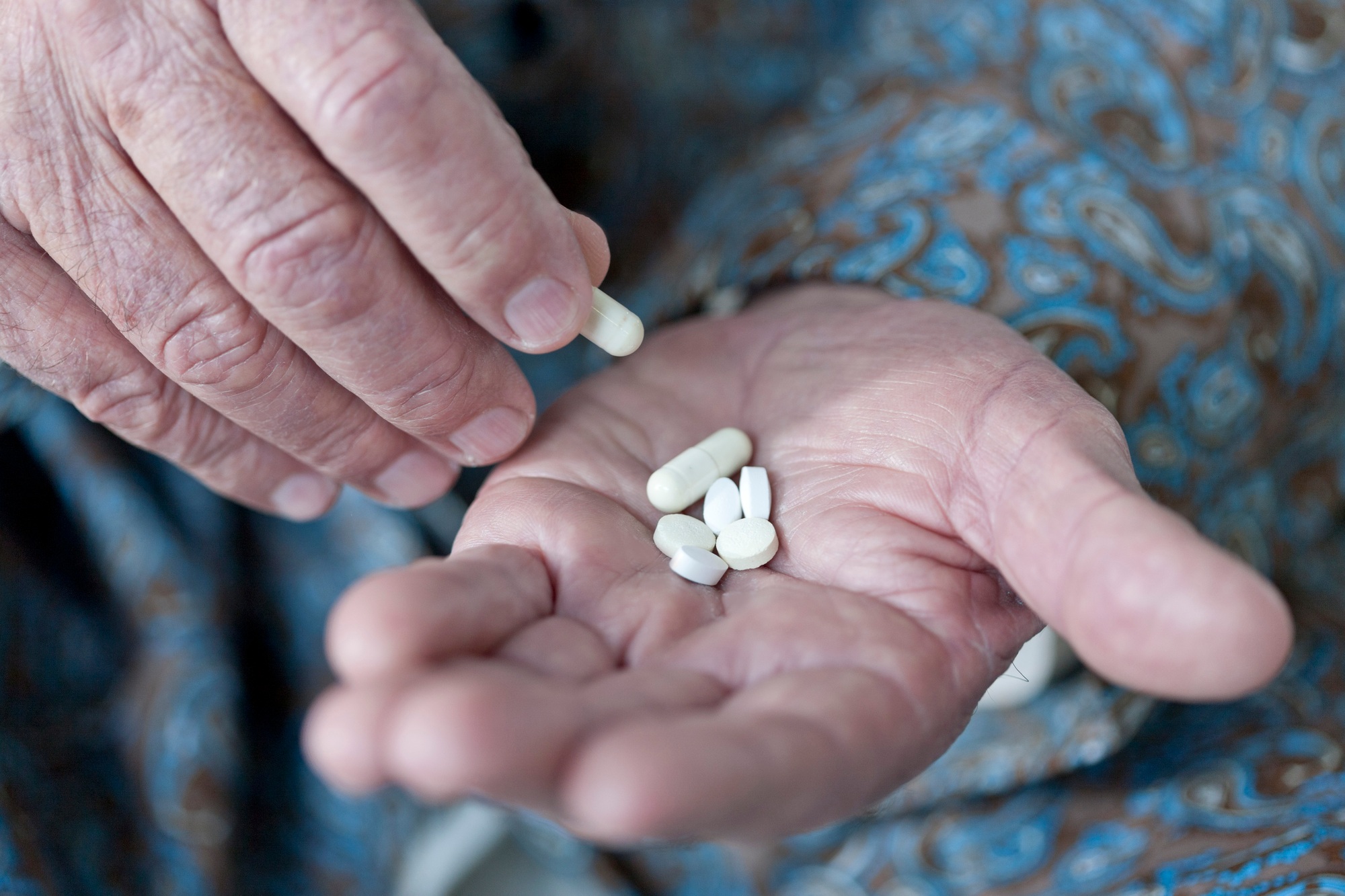
Shelf Life Definition & Meaning
Shelf life represents the time during which a pharmaceutical product remains safe and effective. It ensures that patients use medications that deliver the intended therapeutic benefits. Manufacturers regularly assess shelf life to guarantee product quality throughout its lifecycle.
By accurately determining this period, companies can prevent the distribution of ineffective or unsafe drugs. Understanding shelf life also reduces waste by minimizing the disposal of expired products. Moreover, it helps optimize production schedules and improves overall supply chain efficiency.
To determine lifetime, manufacturers conduct stability tests under controlled conditions. These tests evaluate how a product’s physical, chemical, and microbiological properties change over time. For instance, extreme temperatures or moisture exposure can degrade active ingredients. Poor packaging may also affect product stability by allowing contaminants to enter. Companies analyze stability data to set an appropriate expiration date for each product. Accurate expiration dates help maintain consistent product performance and patient safety. Additionally, stability testing supports compliance with regulatory guidelines and ensures global market approval.
Sign up for Introduction to Production Batch Management Course
Key Factors That Affect Shelf Life
Several factors can influence the expiration date of a pharmaceutical product. Below is a list of these factors, along with a brief explanation of each:
Temperature
High temperatures can accelerate chemical degradation, leading to reduced efficacy.
Humidity
Excessive moisture can compromise packaging and degrade the product’s stability.
Light Exposure
UV light may break down active ingredients, altering the drug’s effectiveness.
pH Levels
Improper pH conditions can cause chemical reactions, reducing product stability.
Packaging Material
Poor-quality packaging may fail to protect the product from environmental factors.
Microbial Contamination
Contaminants can spoil the product, posing safety risks to patients.
Storage Conditions
Incorrect storage environments may accelerate degradation.
Regulatory Guidelines for Shelf Life
ICH Q1A Guideline: Stability Testing for New Drugs
The ICH Q1A guideline provides clear requirements for stability testing of new pharmaceutical drugs. It helps manufacturers determine the shelf life by outlining specific testing protocols. Companies must conduct stability tests under different storage conditions, including long-term, intermediate, and accelerated environments. Long-term tests simulate typical storage conditions, ensuring products remain stable during normal usage. On the other hand, accelerated studies expose products to extreme conditions, such as higher temperatures and humidity. These studies help predict how environmental factors might affect product quality over time.
Manufacturers use data from both long-term and accelerated tests to evaluate product stability. They assess changes in physical properties, such as appearance or texture, and monitor chemical degradation. In addition, they examine microbiological stability to prevent contamination risks during storage. After completing these tests, companies document their findings in detailed stability reports. These reports include test results, statistical evaluations, and lifetime predictions. Regulatory authorities require stability reports to approve drugs for commercial use. By following ICH Q1A guidelines, manufacturers ensure reliable data and smooth regulatory approval processes.
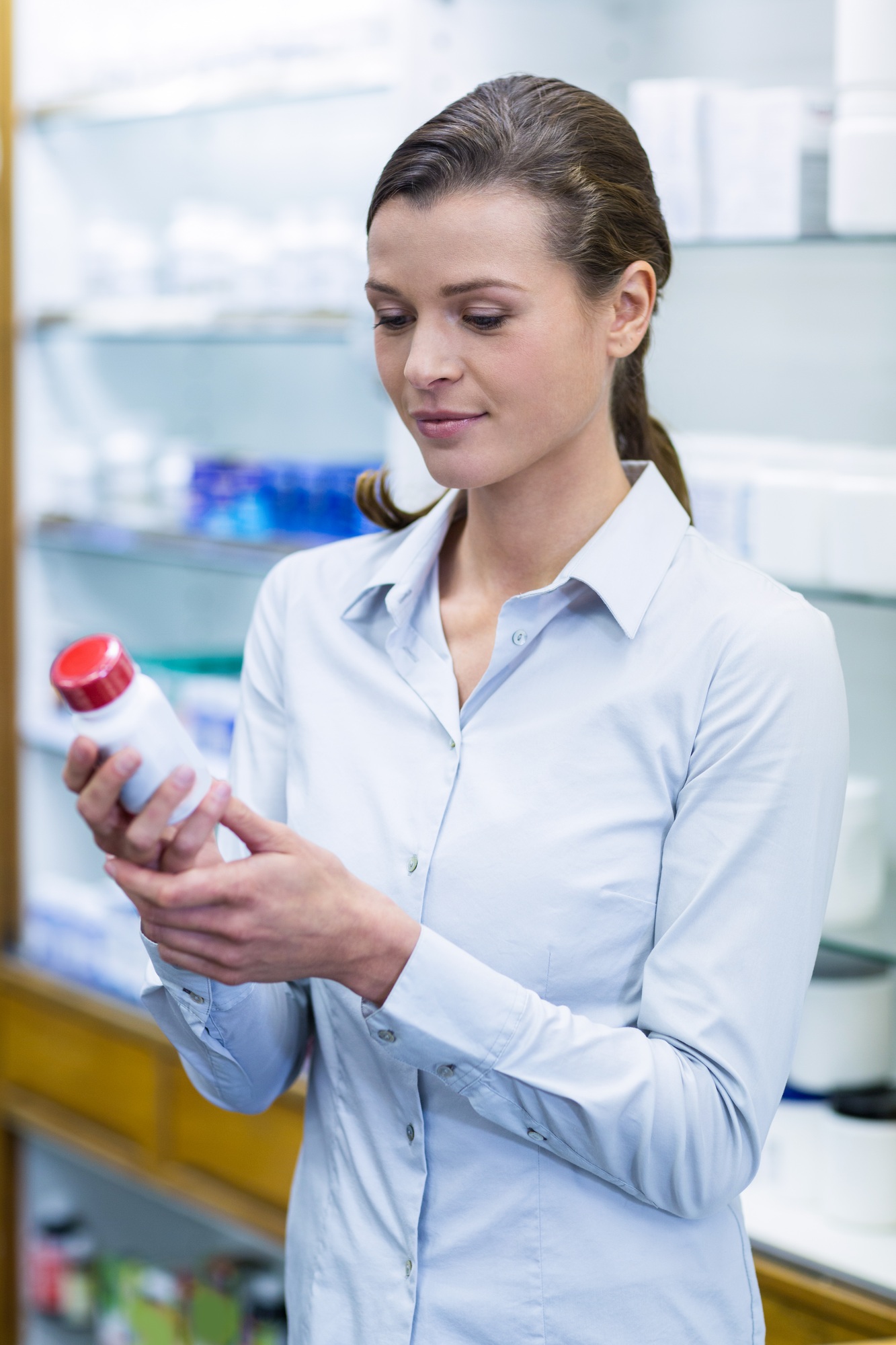

ICH Q1E Guideline: Evaluation of Stability Data
The ICH Q1E guideline helps manufacturers evaluate stability data to determine a product’s shelf life. It outlines statistical methods that improve the accuracy of shelf life predictions. Companies use these methods to analyze data collected from stability tests under different conditions. By applying these approaches, they can detect trends in product quality over time. For example, statistical models help track changes in active ingredient levels or product appearance. With reliable data analysis, manufacturers can confidently set expiration dates for their products.
Regression analysis, a common method in ICH Q1E, predicts shelf life based on stability trends. This approach helps companies estimate how long a product remains safe and effective. By using consistent statistical methods, manufacturers ensure their lifetime determinations are scientifically valid. This consistency improves the credibility of data submitted to regulatory authorities. Moreover, following ICH Q1E helpslifetime streamline the approval process for new drugs. Companies that comply with this guideline meet international regulatory standards, simplifying global market entry. Ultimately, accurate shelf life estimation protects patient safety and ensures high-quality pharmaceutical products.
Objectives in Shelf Life Determination
Understanding the objectives behind determining lifetime helps manufacturers align with regulatory expectations and ensure product quality. Below are the main goals:
Ensuring Patient Safety
Accurate shelf life prevents the use of degraded or ineffective drugs, protecting patients from potential harm.
Maintaining Product Quality
It ensures that the product retains its intended properties throughout its lifespan.
Regulatory Compliance
Meeting guidelines, such as ICH Q1A and Q1E, demonstrates compliance with global regulatory standards.
Minimizing Waste
Proper estimation of expiration date reduces expired inventory, optimizing production and storage costs.
Enhancing Supply Chain Efficiency
Knowing the shelf life helps plan distribution, ensuring products reach consumers before expiration.
Quality Standard and Acceptance Criteria
Quality Standards in Shelf Life Estimation
Pharmaceutical companies follow strict quality standards to ensure accurate shelf life determination. These standards cover various aspects, including stability testing, data evaluation, and packaging requirements. Companies conduct stability tests by following protocols that specify test batches and storage conditions. They also perform tests at specific intervals to monitor changes in product quality. By adhering to these standards, manufacturers maintain consistent product quality and meet regulatory expectations. This approach not only ensures safe products but also reduces the risk of errors.
In addition, companies apply Good Manufacturing Practices (GMP) to achieve reliable and repeatable results. GMP guidelines help ensure that manufacturers use validated testing methods and follow strict procedures. Companies select high-quality materials to improve product stability and extend shelf life. They also train staff to handle tests and equipment properly to avoid mistakes. Following GMP strengthens the accuracy of shelf life estimations, which supports regulatory submissions. Ultimately, these practices help protect consumers and maintain the company’s reputation for quality.

Acceptance Criteria for Stability Testing
Acceptance criteria play a crucial role in ensuring the reliability of pharmaceutical products during their shelf life. They define the allowable variations in product properties while maintaining safety and efficacy.
For instance, limits on active ingredient potency prevent under-dosing or overdosing risks. Similarly, physical attributes like color, texture, and appearance must remain stable to assure patients of product quality. Companies also set limits on dissolution rates to ensure proper drug absorption in the body. Regular testing against these criteria ensures that the product maintains its intended performance throughout storage.
By establishing clear acceptance criteria, pharmaceutical companies enhance their ability to detect potential stability issues early. For example, if test results show significant deviation from predefined limits, companies can investigate and resolve problems quickly.
This proactive approach helps prevent costly recalls and product failures in the market. Furthermore, meeting acceptance criteria consistently strengthens regulatory compliance. It also supports global distribution since regulatory agencies in different regions often have aligned expectations. Ultimately, well-defined acceptance criteria protect patient health and enhance the company’s credibility in delivering high-quality pharmaceutical products.
Challenges in Shelf Life Determination
Stability testing poses significant challenges for pharmaceutical companies due to its demanding nature. These tests require substantial time, financial resources, and specialized expertise. Long-term stability studies often take years, delaying product approvals and market entry. Companies perform accelerated tests to speed up the process, but these tests may not always predict real-world performance. Balancing the need for faster results with accuracy becomes a difficult task. Additionally, companies must ensure consistent testing conditions, as environmental fluctuations can impact data accuracy. To reduce this risk, they invest in controlled environments and validated testing equipment.
Regulatory compliance adds another layer of complexity to stability testing. Different countries may impose unique stability testing requirements, complicating the process for global manufacturers. Even when companies follow ICH guidelines, local authorities might demand extra tests or data. Keeping up with regulatory changes in different regions requires constant attention and effort. Failure to meet specific requirements can result in costly delays or product rejections. To overcome these hurdles, companies maintain a dedicated regulatory team to monitor updates and ensure timely compliance. By addressing these challenges, manufacturers can streamline the approval process and bring high-quality products to market faster.
Steps for Shelf Life Estimation
Below is a step-by-step guide for estimating shelf life, with a brief description of each step:
Conduct Stability Testing
Perform long-term, intermediate, and accelerated tests to gather data.
Evaluate Testing Data
Use statistical models to analyze stability trends and predict expiration dates.
Define Acceptance Criteria
Establish allowable changes in product properties during storage.
Document Findings
Compile test results in stability reports for regulatory review.
Submit to Regulatory Authorities
Provide documentation to gain approval for the product’s shelf life.
Monitor Shelf Life Post-Approval
Conduct ongoing stability studies to confirm the product’s performance over time.
Conclusion
Determining shelf life is a critical process in the pharmaceutical industry. It ensures product safety, quality, and efficacy while maintaining compliance with global regulatory standards. By understanding the factors that influence shelf life, such as temperature, humidity, and packaging, manufacturers can make informed decisions. Adhering to guidelines like ICH Q1A and Q1E further enhances the accuracy of shelf life estimations. Ultimately, a well-established shelf life benefits both patients and manufacturers, fostering trust and efficiency in the healthcare system.
References
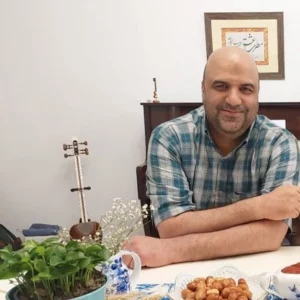
Ershad Moradi
Ershad Moradi, a Content Marketing Specialist at Zamann Pharma Support, brings 6 years of experience in the pharmaceutical industry. Specializing in pharmaceutical and medical technologies, Ershad is currently focused on expanding his knowledge in marketing and improving communication in the field. Outside of work, Ershad enjoys reading and attending industry related networks to stay up-to-date on the latest advancements. With a passion for continuous learning and growth, Ershad is always looking for new opportunities to enhance his skills and contribute to pharmaceutical industry. Connect with Ershad on Facebook for more information.
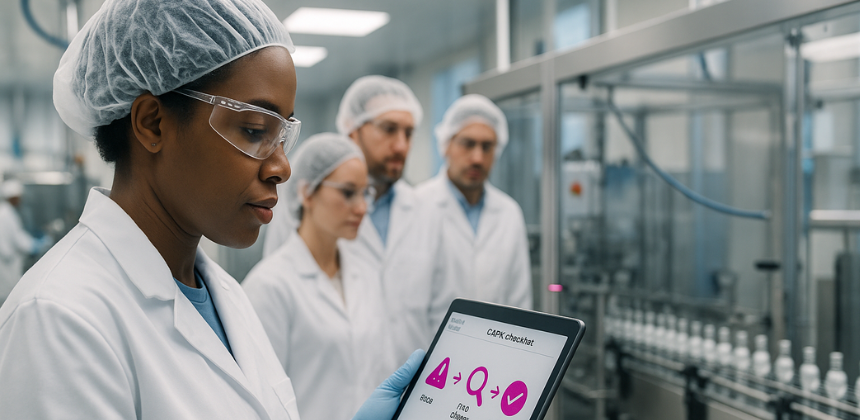
What Is a CAPA Plan? A Beginner’s Guide
This beginner’s guide explains CAPA plans in plain language. You’ll define problems clearly, analyze root causes with proven tools, and turn findings into targeted corrective and preventive actions. Then, you’ll verify effectiveness with metrics and close confidently.

Computerized Maintenance Management: The Complete 2025 Guide
This guide explores computerized maintenance management with practical strategies, CMMS comparisons, and implementation tips. Designed for professionals, entrepreneurs, and job seekers, it helps you choose the right tools, optimize workflows, and boost ROI with preventive and predictive maintenance methods.
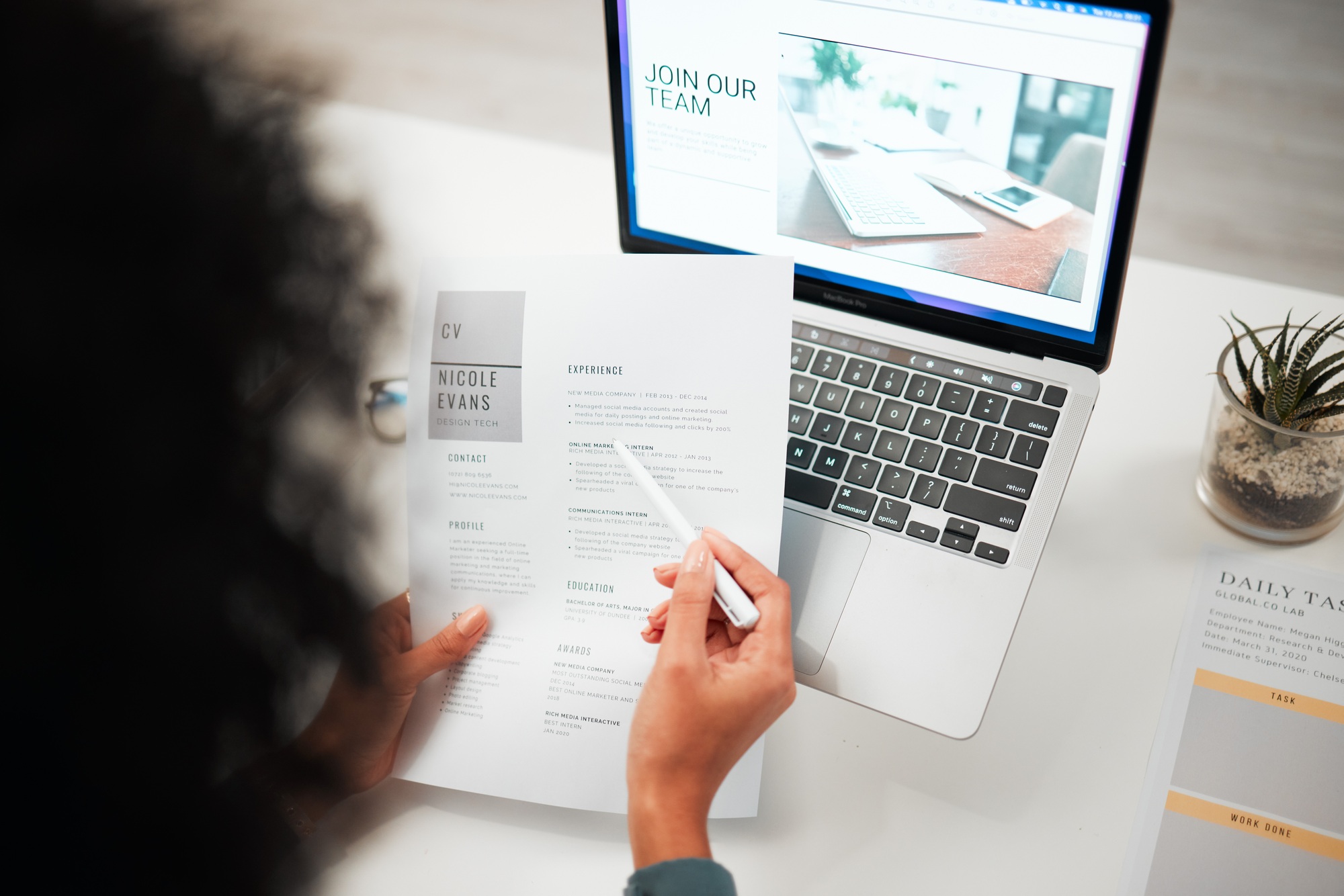
How to Choose the Right Special Skills for Resume Success
Learn how to choose, organize, and present special skills for resume success. This guide includes technical and soft skills, comparison tables, and AI-friendly strategies to pass ATS filters and stand out in competitive job markets.