Organizations constantly strive to improve processes, reduce errors, and maximize efficiency. Achieving operational excellence requires a strategic approach, and quality tools are invaluable in this journey. These tools help teams identify problems, streamline workflows, and ensure high-quality outputs.
In this article, we explore key quality tools that can optimize operations and lead to better business outcomes.
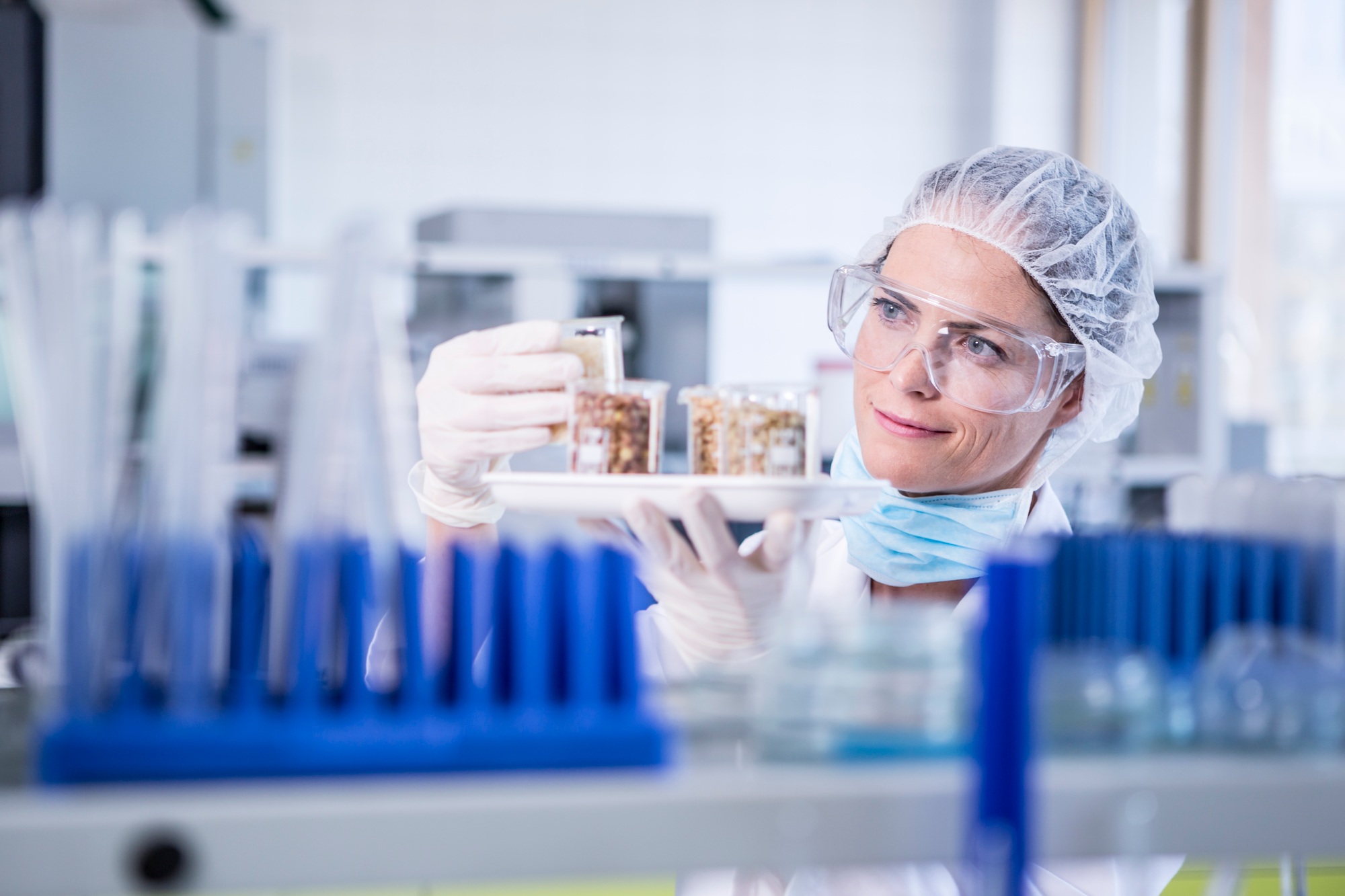
Understanding Quality Tools
Quality tools are systematic techniques that simplify complex processes and improve efficiency. They help organizations maintain consistency by providing clear methods to analyze and monitor operations. These tools empower teams to identify root causes of problems and implement effective solutions. Moreover, they enable data-driven decisions, ensuring actions align with measurable insights. Across industries like manufacturing, healthcare, and education, quality tools support teams in achieving their goals. By mastering these techniques, businesses enhance productivity, reduce errors, and maintain customer satisfaction. Consistently using quality tools helps organizations stay competitive in a rapidly changing market.
A structured approach makes quality tools essential for addressing operational challenges. These tools provide visual data representations, which improve analysis and simplify communication among teams. For example, a flowchart can map processes, revealing inefficiencies that need attention. Teams use this clarity to align strategies and take decisive action. Regularly implementing quality tools helps businesses meet standards while driving continuous improvement.
Furthermore, organizations that adopt these tools create a culture of accountability and innovation. By embracing this structured approach, businesses not only excel in their operations but also achieve long-term success.
Sign up for Preparation Phase of GMP Equipment Management Course
Key Quality Tools and Their Applications
Quality tools come in many forms, each serving specific purposes. Below is a list of essential quality tools, with a brief explanation of their benefits:
Check Sheet
Collects and organizes data systematically for problem identification.
Histogram
Displays data distribution to highlight trends and variations.
Fishbone Diagram
Identifies root causes of issues through cause-and-effect analysis.
Pareto Chart
Highlights the most significant problems based on frequency or impact.
Flowchart
Visualizes processes to pinpoint inefficiencies or bottlenecks.
Control Chart
Tracks process stability over time using statistical methods.
Brainstorming
Encourages idea generation and creative problem-solving.
The Five Whys
Explores root causes by repeatedly asking “Why?” for deeper analysis.
Procedures for Using Quality Tools Effectively
Building an Effective Check Sheet
The check sheet simplifies data collection by organizing information based on occurrences. It helps teams detect patterns quickly, making it easier to prioritize improvement areas. For instance, manufacturing teams track machine defects over time to identify recurring issues. Using this data, they plan preventive maintenance to avoid costly breakdowns. Teams in other industries can also benefit from check sheets to monitor trends and enhance processes. Additionally, this tool allows teams to focus on measurable results and actionable insights. By using a check sheet, organizations save time and improve decision-making accuracy.
To use a check sheet effectively, teams must follow a clear process. First, they should define categories that align with specific goals or metrics. This step ensures the collected data remains relevant and useful. Next, teams should involve all stakeholders to ensure everyone contributes accurate information. Regularly reviewing the data helps teams identify emerging trends and refine their strategies. Moreover, teams can adapt the check sheet format as needs evolve, maintaining its relevance. Consistent use of the check sheet supports continuous improvement and ensures sustained success.
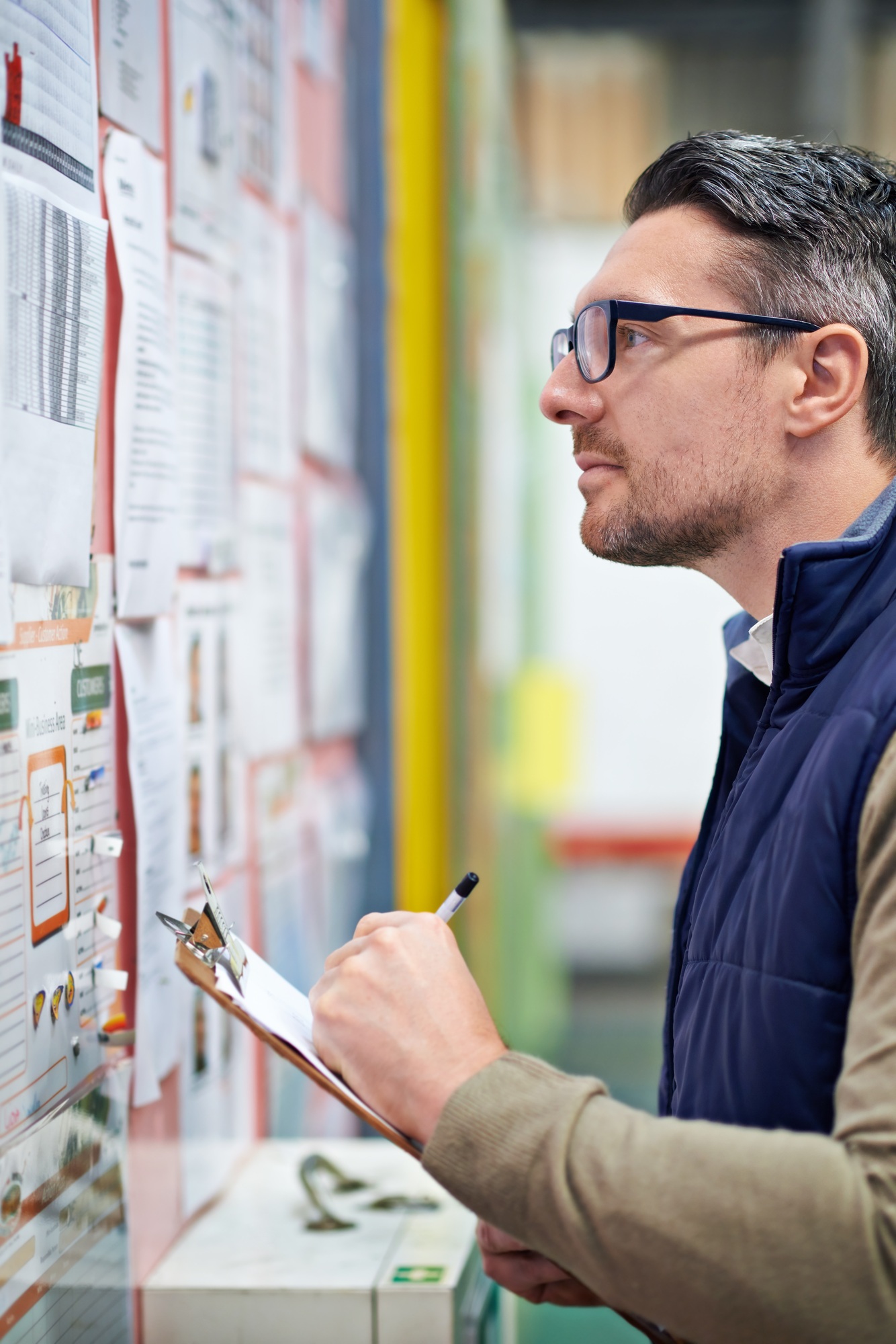
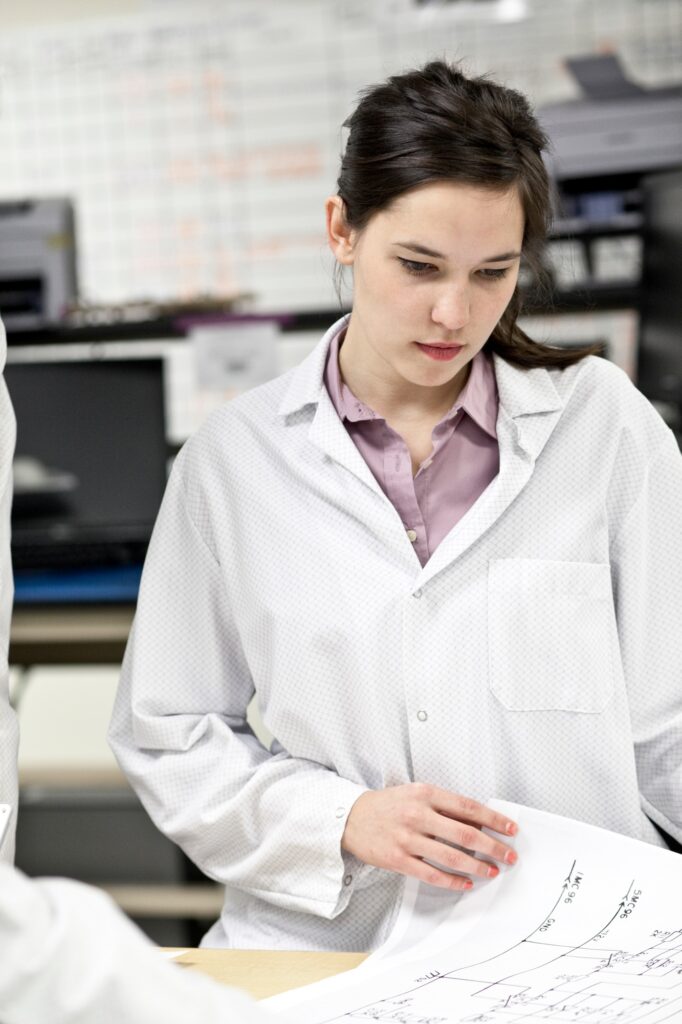
Creating a Histogram for Insights
A histogram groups data into intervals, allowing teams to spot trends and anomalies quickly. It helps simplify complex data by presenting it in a visual format that is easy to interpret. For example, a customer service department might use a histogram to track response time variations. This approach highlights periods of delay, enabling the team to address inefficiencies promptly. Additionally, histograms allow teams to compare data patterns over time, ensuring consistent performance. By identifying process deviations early, teams can take corrective actions and avoid bigger issues. Using a histogram enhances decision-making and drives continuous improvement in operations.
To create an effective histogram, start by ensuring the data is accurate and complete. Next, choose intervals that represent the data meaningfully and align with your goals. Proper interval selection ensures the histogram highlights significant trends without oversimplifying the data. Once you construct the histogram, review the graphical output thoroughly for actionable insights. Look for clusters, gaps, or outliers that indicate potential areas for improvement. Use these findings to refine processes and optimize performance consistently. By revisiting the histogram regularly, teams can track progress and stay ahead of potential challenges.
Practical Examples of Quality Tools in Action
Check Sheet
A manufacturing plant tracks machine errors daily using a check sheet. They identify recurring faults and implement timely solutions, reducing downtime.
Histogram
A service team analyzes customer feedback scores via a histogram, identifying peak satisfaction times and replicating successful practices.
Fishbone Diagram
A software company investigates project delays using this diagram, revealing communication gaps as the root cause.
Pareto Chart
An e-commerce business highlights that 80% of delivery delays stem from two logistics partners. They switch providers and improve efficiency.
Flowchart
A hospital maps patient admission procedures, spotting redundant steps and optimizing the process for faster care delivery.
The Five Whys
A retail store solves recurring inventory issues by asking “Why?” five times, identifying miscommunication as the root cause.
Fishbone Diagram: A Key Quality Tool
Uncovering Root Causes
The fishbone diagram, or cause-and-effect diagram, helps teams visually organize potential problem causes. It simplifies complex issues by categorizing them into clear labels like “People,” “Methods,” and “Materials.” These categories help teams systematically identify and address each contributing factor. For example, if a production delay occurs, the diagram can reveal whether staffing, processes, or equipment cause the issue. This visual approach enables teams to focus their efforts on the most impactful areas. Additionally, the fishbone diagram encourages collaborative problem-solving by involving multiple perspectives. Teams can use this tool to brainstorm solutions and create actionable plans.
To use a fishbone diagram effectively, start by clearly defining the problem you want to solve. Then, categorize potential causes under logical labels that align with your operations. Ensure all team members contribute their insights during this step to create a comprehensive analysis. Next, examine each category to pinpoint root causes and prioritize actionable steps. Regularly revisit the diagram to track progress and refine solutions as needed. By consistently using the fishbone diagram, teams can uncover hidden issues and prevent recurring problems. This proactive approach supports continuous improvement and drives long-term success.
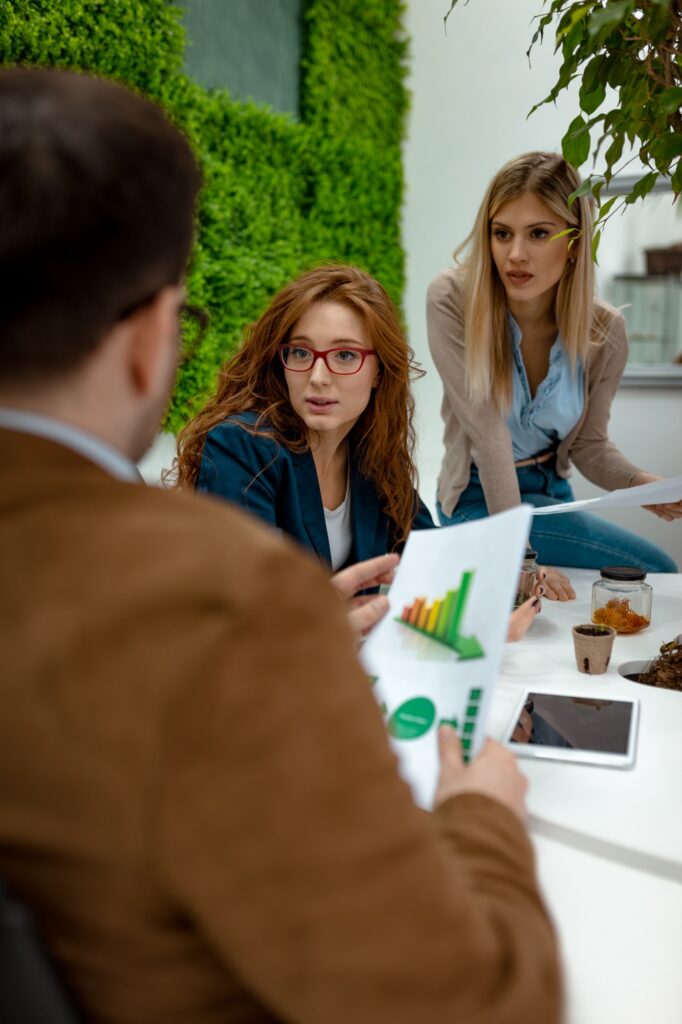
Practical Applications
The fishbone diagram is a powerful tool for solving product defects, service delays, or inefficiencies. Teams use it to break down complex problems into manageable categories, making solutions easier to find. For instance, in a restaurant, the fishbone diagram can identify causes behind long wait times. It might reveal staffing shortages or ingredient supply issues that slow operations. With this information, managers can prioritize hiring or streamline supply chains to improve efficiency. Additionally, the diagram helps focus attention on the most significant contributing factors, ensuring efforts lead to meaningful improvements. By using this tool, teams can tackle problems systematically and effectively.
To maximize its impact, teams should apply the fishbone diagram to recurring or significant issues. Start by defining the specific problem, such as customer complaints about delays. Then, categorize potential causes into areas like staffing, methods, or equipment. For example, insufficient staff training might contribute to delays in service. Analyzing these categories helps identify actionable solutions, like providing additional training or adjusting schedules. Regularly updating the diagram allows teams to monitor progress and address new challenges as they arise. Using this approach not only solves current issues but also prevents similar problems in the future. By leveraging the fishbone diagram, teams can achieve greater consistency and operational excellence.
Enhancing Problem-Solving Capabilities with Quality Tools
Quality tools strengthen problem-solving by helping teams approach challenges systematically and effectively. They break complex issues into smaller, manageable parts, making solutions more attainable. For instance, the fishbone diagram helps teams uncover hidden factors causing recurring problems. By organizing potential causes into categories, it enables teams to focus on root issues. This clarity allows for targeted interventions that address the problem at its source. Furthermore, quality tools encourage collaboration, ensuring that diverse perspectives contribute to better solutions. Using these tools regularly fosters a proactive mindset, enabling teams to tackle challenges before they escalate.
Implementing quality tools also promotes a culture of continuous improvement throughout an organization. Teams focus on resolving root causes instead of merely treating symptoms. This approach leads to long-lasting improvements that enhance operational efficiency. Additionally, regularly applying these tools builds confidence and problem-solving skills within teams. By leveraging these capabilities, organizations achieve greater consistency, improved performance, and sustained success.
Ensuring Data-Driven Decisions with Quality Tools
Monitor Process Stability
Control charts track performance and quickly highlight trends that require immediate attention.
Identify Priorities
Pareto charts focus on the most impactful issues, helping teams allocate resources efficiently.
Simplify Decision-Making
Quality tools present data visually, making complex analysis more accessible and actionable.
Forecast Outcomes
Teams use insights from quality tools to predict potential results and avoid costly errors.
Align Actions
Data-driven strategies reduce uncertainty, ensuring decisions support long-term success and growth.
Conclusion
Quality tools are essential for organizations aiming to optimize operations and enhance outcomes. Tools like the fishbone diagram, Pareto chart, and control chart empower teams to identify, analyze, and address issues systematically.
By integrating these tools into daily practices, businesses can achieve efficiency, reduce errors, and maintain high-quality standards. Start leveraging quality tools today to stay competitive and drive success in your operations!
References
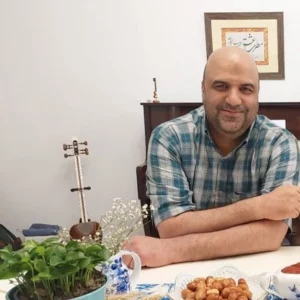
Ershad Moradi
Ershad Moradi, a Content Marketing Specialist at Zamann Pharma Support, brings 6 years of experience in the pharmaceutical industry. Specializing in pharmaceutical and medical technologies, Ershad is currently focused on expanding his knowledge in marketing and improving communication in the field. Outside of work, Ershad enjoys reading and attending industry related networks to stay up-to-date on the latest advancements. With a passion for continuous learning and growth, Ershad is always looking for new opportunities to enhance his skills and contribute to pharmaceutical industry. Connect with Ershad on Facebook for more information.
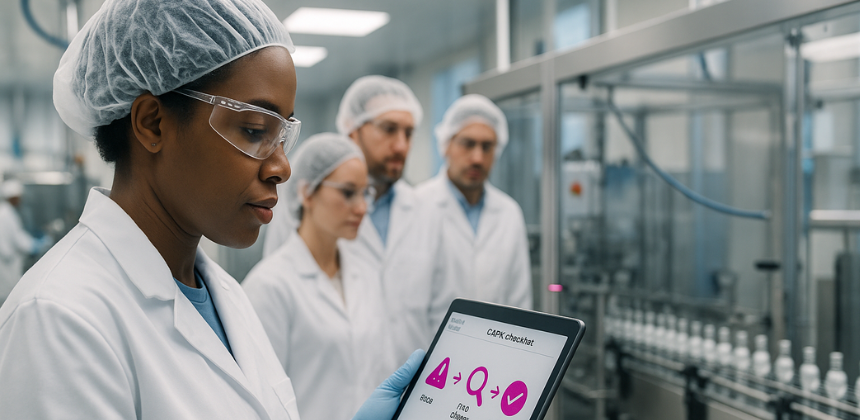
What Is a CAPA Plan? A Beginner’s Guide
This beginner’s guide explains CAPA plans in plain language. You’ll define problems clearly, analyze root causes with proven tools, and turn findings into targeted corrective and preventive actions. Then, you’ll verify effectiveness with metrics and close confidently.

Computerized Maintenance Management: The Complete 2025 Guide
This guide explores computerized maintenance management with practical strategies, CMMS comparisons, and implementation tips. Designed for professionals, entrepreneurs, and job seekers, it helps you choose the right tools, optimize workflows, and boost ROI with preventive and predictive maintenance methods.
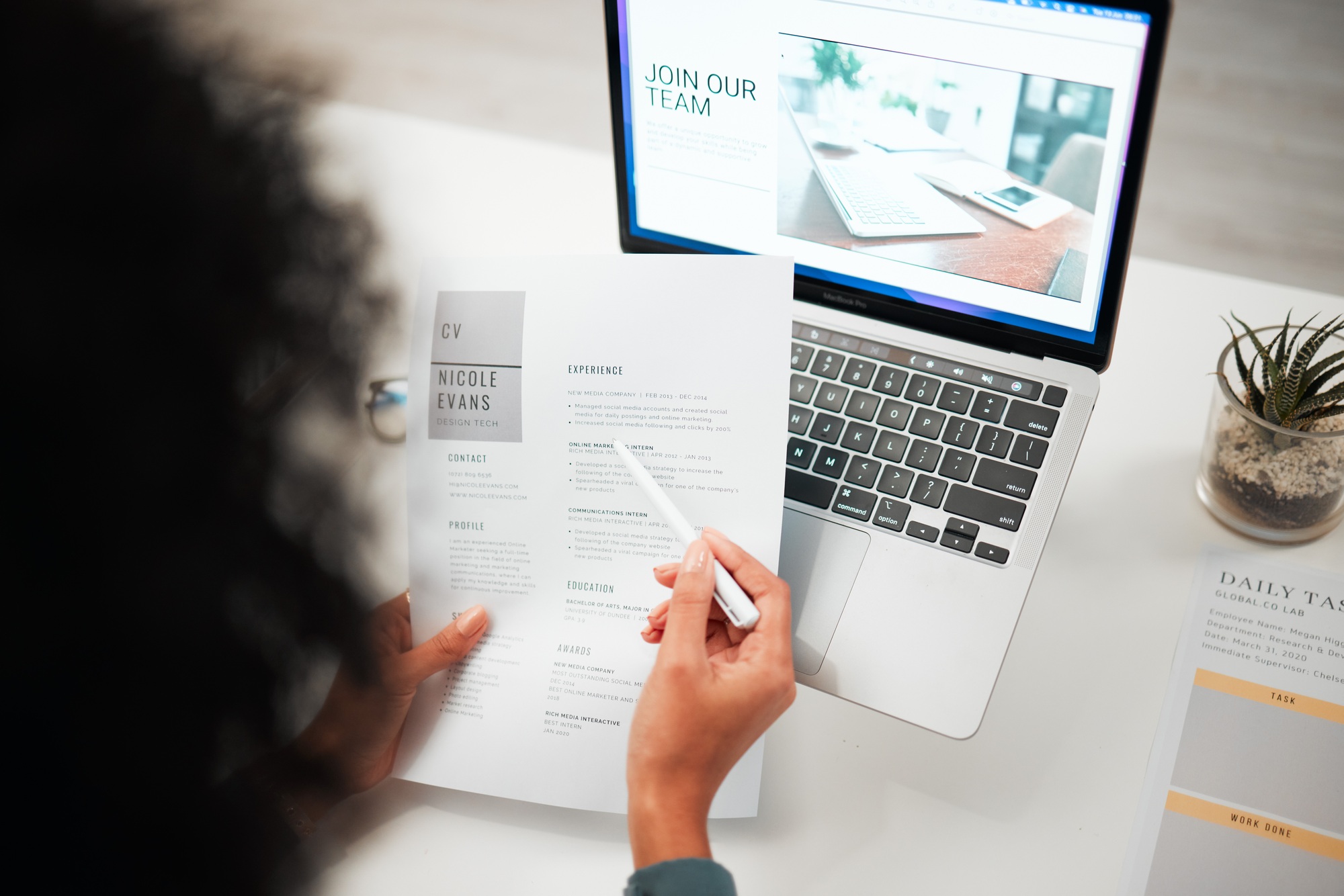
How to Choose the Right Special Skills for Resume Success
Learn how to choose, organize, and present special skills for resume success. This guide includes technical and soft skills, comparison tables, and AI-friendly strategies to pass ATS filters and stand out in competitive job markets.