When it comes to GMP procedures for equipment, the preparation phase is the foundation upon which everything else builds. Without proper planning, all the sophisticated systems and methods in the world can’t guarantee success. Whether you’re dealing with equipment installation, qualification, or maintenance, following the correct protocols is critical.
In this article, we’ll dive into the world of GMP procedures for equipment and how to prep like a pro. From regulatory expectations to test protocols, we’ll explore the key steps and best practices that ensure compliance and efficiency. So, buckle up and get ready to master the art of GMP prep!
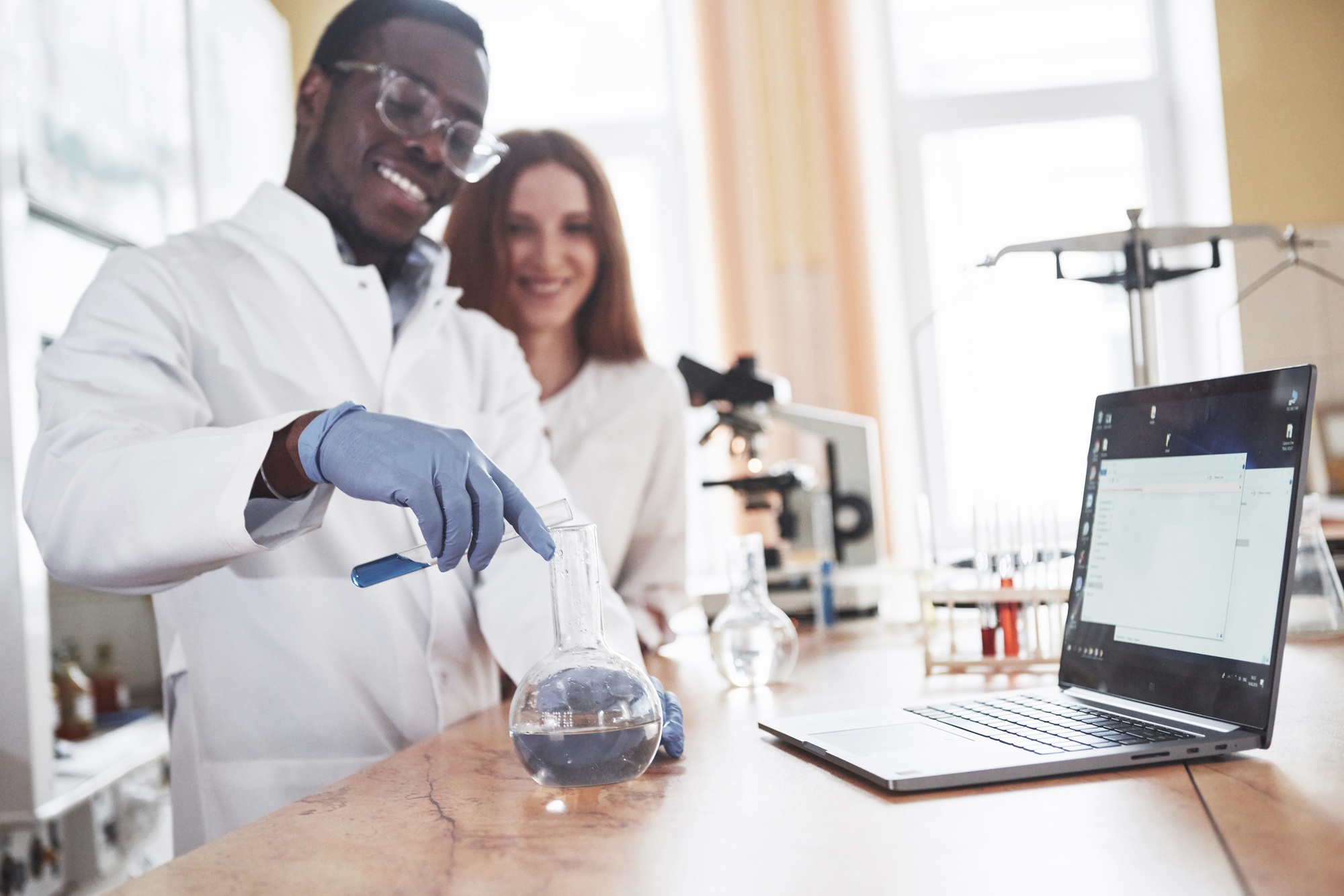
Defining GMP Procedures for Equipment
GMP (Good Manufacturing Practices) procedures set clear standards that ensure equipment in pharmaceutical production meets safety and quality requirements. These standards apply to every phase of equipment use, starting from the initial design all the way through to its ongoing maintenance. GMP procedures are designed to prevent contamination, mix-ups, and errors, making sure the final products are safe and effective for consumers. They also ensure that every piece of equipment functions consistently and reliably over time.
By following GMP procedures, manufacturers can maintain a high level of control over their production environment. This includes verifying that equipment is correctly installed, calibrated, and regularly maintained. Each step involves detailed documentation, which ensures traceability and accountability. For instance, during the installation phase, equipment is tested against design specifications to confirm proper functionality. Moreover, operators are trained to handle equipment correctly and maintain it according to GMP guidelines.
Sign up for Preparation Phase of GMP Equipment Management Course
The Key Stages of GMP Equipment Qualification
Understanding the three key phases of GMP equipment qualification is crucial to ensuring compliance with GMP procedures for equipment.
Installation Qualification (IQ)
The first step involves confirming that the equipment has been installed correctly, following the design specifications. This ensures all physical installations are completed according to the manufacturer’s guidelines.
Operational Qualification (OQ)
The OQ phase ensures that the equipment functions as expected under the defined operational conditions. This step typically involves running the equipment under various conditions to test its operational limits.
Performance Qualification (PQ)
In the final phase, PQ, the equipment is tested under real production conditions to verify its long-term performance. This phase ensures the equipment can consistently produce quality results in a controlled environment.
Regulatory Expectations in GMP Procedures for Equipment
EU and FDA GMP Procedures for Equipment Guidelines
Both the EU and FDA enforce strict guidelines for GMP procedures regarding equipment. The EU’s Annex 15 outlines detailed expectations for equipment qualification, installation, and validation. Similarly, FDA 21 CFR 211 provides guidelines for the operational and performance qualifications of manufacturing equipment. These regulations ensure that equipment meets all necessary standards before it can be used in production. Both sets of guidelines stress the importance of validating equipment for its intended purpose and ensuring long-term reliability.
Manufacturers must fully understand and adhere to these regulations to stay compliant. Equipment must not only meet the initial installation and operational standards but also remain maintainable over time. Regular checks and documentation are critical for ensuring that equipment continues to meet predetermined quality standards. Manufacturers need to track and verify performance continuously, ensuring all equipment operates efficiently and safely. Failing to comply with these regulatory standards can lead to costly mistakes, including product recalls or penalties. Therefore, staying up to date with EU and FDA guidelines is essential for maintaining quality and avoiding regulatory issues.
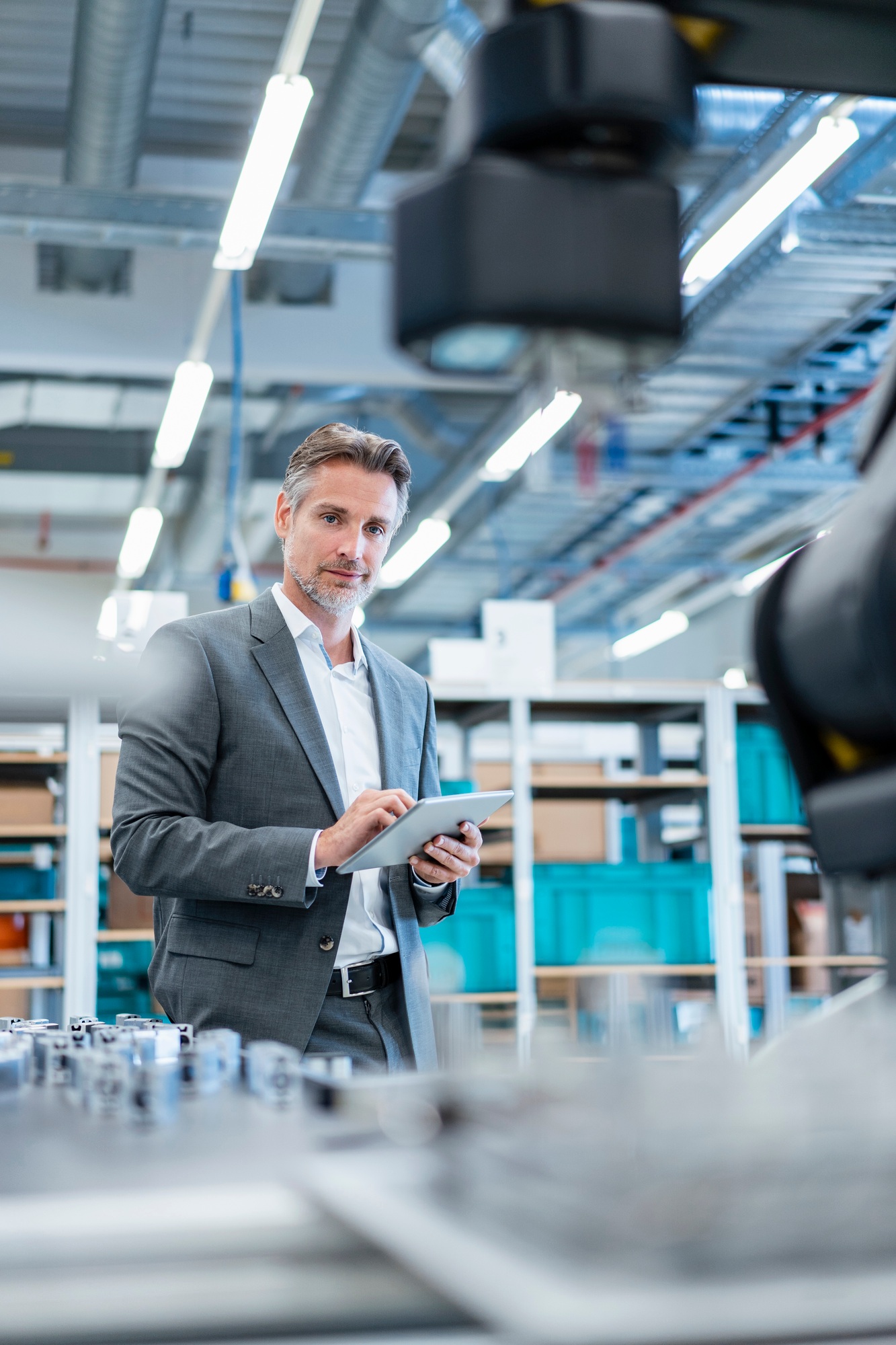
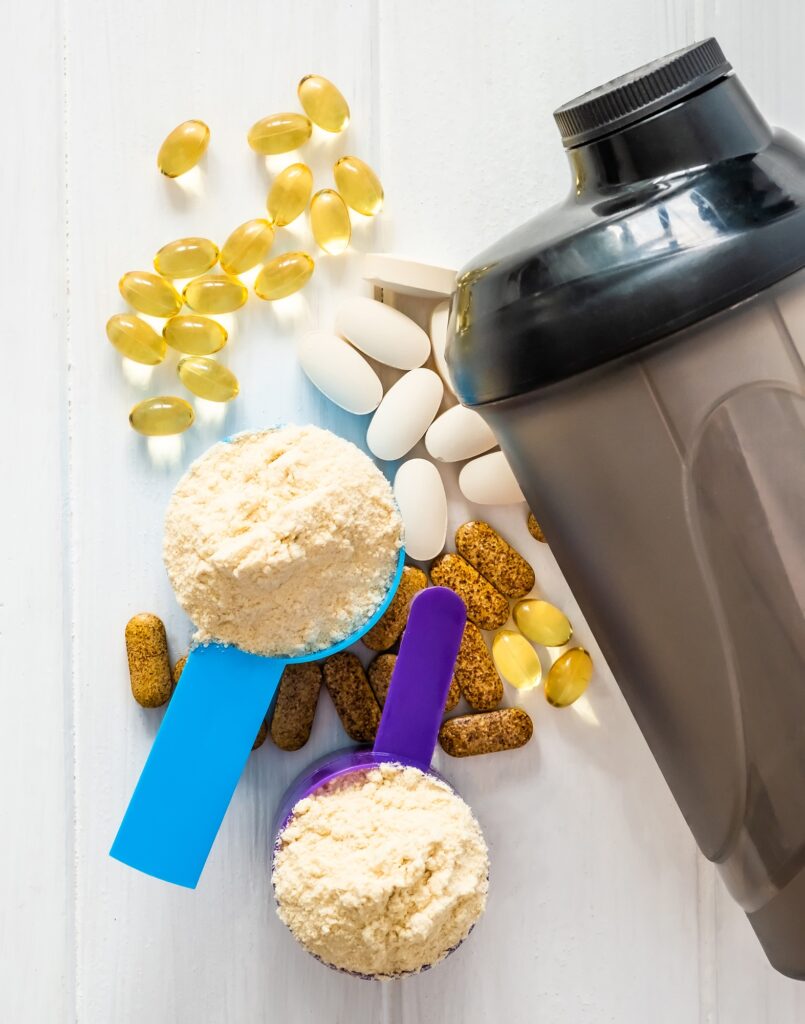
Impact of Regulatory Non-Compliance
Non-compliance with GMP procedures can lead to severe consequences, such as product recalls, fines, and even shutdowns. When companies fail to meet regulatory requirements, they risk not only damaging their reputation but also putting consumer safety in jeopardy. For example, faulty equipment or unqualified machinery can cause production errors, leading to the release of substandard products. This not only affects public trust but also results in expensive product recalls and legal action. Therefore, staying up-to-date with GMP regulations is crucial for maintaining operational efficiency and consumer safety.
Implementing robust GMP procedures for equipment helps prevent such risks. Any gaps in equipment qualification or documentation can lead to serious issues that disrupt the production process. Without proper documentation, manufacturers cannot prove their equipment meets required standards, leaving them vulnerable to non-compliance. Additionally, improper qualification of equipment can directly affect product quality, risking harm to consumers. To avoid these dangers, companies must regularly review and update their GMP practices. Proactive measures, such as continuous training and thorough documentation, ensure that all equipment stays compliant and operational.
Key Components of GMP Procedures for Equipment: A Checklist
Regulatory Compliance
Ensure that equipment adheres to local and international regulatory standards such as EU Annex 15 or FDA 21 CFR 211.
Documentation
Maintain accurate and complete records of all equipment qualifications, including installation, operational, and performance qualifications.
Calibration
Proper calibration of instruments like thermometers, sensors, and meters is critical to guarantee accuracy in production.
Training
Equip staff with proper training on how to handle and operate the equipment within GMP guidelines to avoid errors.
Maintenance
Regular maintenance schedules ensure the equipment remains in optimal working condition.
Manufacturer Collaboration
Collaborate with equipment manufacturers to ensure installations and calibrations align with GMP standards.
Performing IQ Under GMP Procedures
GMP Procedures for Equipment Installation
The installation qualification (IQ) phase ensures that equipment installation aligns with the qualification plan. During this phase, teams verify the equipment’s location, ensuring it matches design specifications.
They also confirm that power requirements and environmental conditions, like temperature and humidity, meet operational needs. By addressing these factors, manufacturers can ensure the equipment functions as intended. Additionally, teams must assess the installation environment to identify and resolve potential risks early.
Utility connections such as water, air, and electricity require careful inspection during the IQ phase. Each connection must meet the manufacturer’s specifications to guarantee equipment reliability.
Teams document all installation details, ensuring a clear record for future reference. This documentation serves as evidence of compliance and helps troubleshoot any issues that arise later. With proper planning and precise execution, the IQ phase sets a strong foundation for the next qualification stages, reducing risks and ensuring compliance.
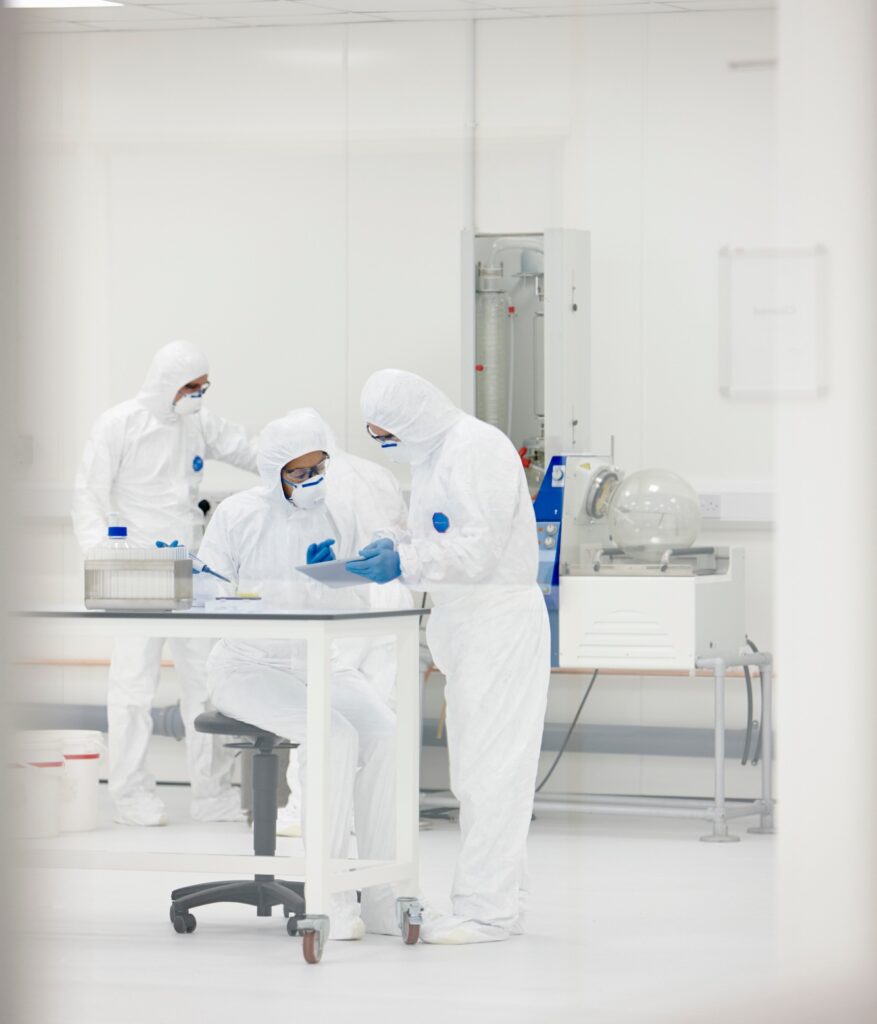
Documentation Requirements for IQ
During the IQ phase, maintaining thorough documentation is essential to ensure compliance with GMP procedures. Teams must verify the installation against the design specifications outlined in the qualification plan.
This includes recording every detail of the equipment’s setup, ensuring everything aligns with the intended design. Any deviation from the original plan must be documented clearly and thoroughly, explaining the reason for the change. By keeping precise records, teams can trace back any issues that arise during later stages.
Moreover, adjustments made during the installation process must be carefully documented and justified. If any modifications are necessary, teams should provide a valid reason for the change and outline the steps taken.
This documentation serves as a safeguard, ensuring that all changes remain compliant with GMP guidelines. Properly maintaining these records helps prevent future complications and supports the integrity of the entire qualification process. Additionally, it ensures that teams can demonstrate adherence to GMP procedures if inspected or audited.
Execute PQ Under GMP Procedures
Performance qualification (PQ) is where you confirm that equipment can deliver consistent, high-quality results under actual production conditions. During PQ, you test the equipment in real-world scenarios to ensure it meets operational expectations. You run the equipment as it will be used in production, considering variables like temperature, humidity, and pressure. These factors affect the equipment’s performance and must be accounted for to ensure it operates correctly. Testing under these conditions confirms the equipment’s ability to handle production loads without compromising product quality.
In addition to testing equipment under real conditions, PQ also involves establishing long-term performance metrics. You assess the equipment’s ability to maintain performance over time, not just in a single trial. Monitoring efficiency, downtime, and any operational issues is critical in this phase. These metrics provide insights into the equipment’s reliability and help predict potential failures. By keeping detailed records of performance, you can ensure that the equipment continues to meet GMP standards. This data is crucial for identifying trends, adjusting procedures, and improving overall equipment performance, ensuring sustained compliance with GMP requirements.
OQ for Equipment Under GMP Procedures
Verify Operational Limits
Confirm that the equipment can operate within the parameters defined in its specification. Test the limits of the equipment and document the results.
Use of Control Software
If the equipment uses control software, it must be tested to ensure it performs as expected.
Conduct Performance Testing
Test the equipment’s ability to perform the required tasks consistently. For example, if the equipment is a mixer, ensure it can handle all required speeds without malfunctioning.
Conclusion
GMP procedures for equipment are the backbone of any compliant pharmaceutical manufacturing process. By following the right steps, from installation to performance qualification, and maintaining rigorous documentation throughout, you can ensure that your equipment not only meets regulatory standards but also contributes to the creation of safe, high-quality products. Following these best practices will help you prep like a pro, ensuring your equipment runs smoothly and in full compliance with GMP requirements.
References
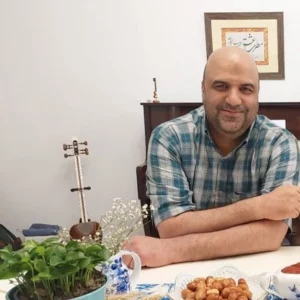
Ershad Moradi
Ershad Moradi, a Content Marketing Specialist at Zamann Pharma Support, brings 6 years of experience in the pharmaceutical industry. Specializing in pharmaceutical and medical technologies, Ershad is currently focused on expanding his knowledge in marketing and improving communication in the field. Outside of work, Ershad enjoys reading and attending industry related networks to stay up-to-date on the latest advancements. With a passion for continuous learning and growth, Ershad is always looking for new opportunities to enhance his skills and contribute to pharmaceutical industry. Connect with Ershad on Facebook for more information.
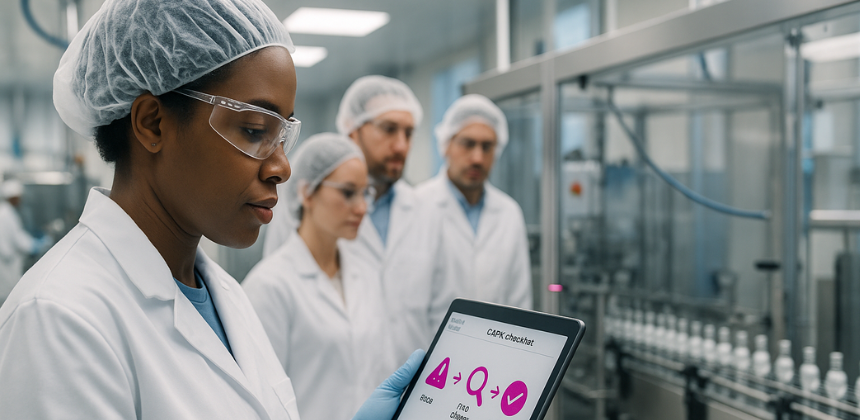
What Is a CAPA Plan? A Beginner’s Guide
This beginner’s guide explains CAPA plans in plain language. You’ll define problems clearly, analyze root causes with proven tools, and turn findings into targeted corrective and preventive actions. Then, you’ll verify effectiveness with metrics and close confidently.

Computerized Maintenance Management: The Complete 2025 Guide
This guide explores computerized maintenance management with practical strategies, CMMS comparisons, and implementation tips. Designed for professionals, entrepreneurs, and job seekers, it helps you choose the right tools, optimize workflows, and boost ROI with preventive and predictive maintenance methods.
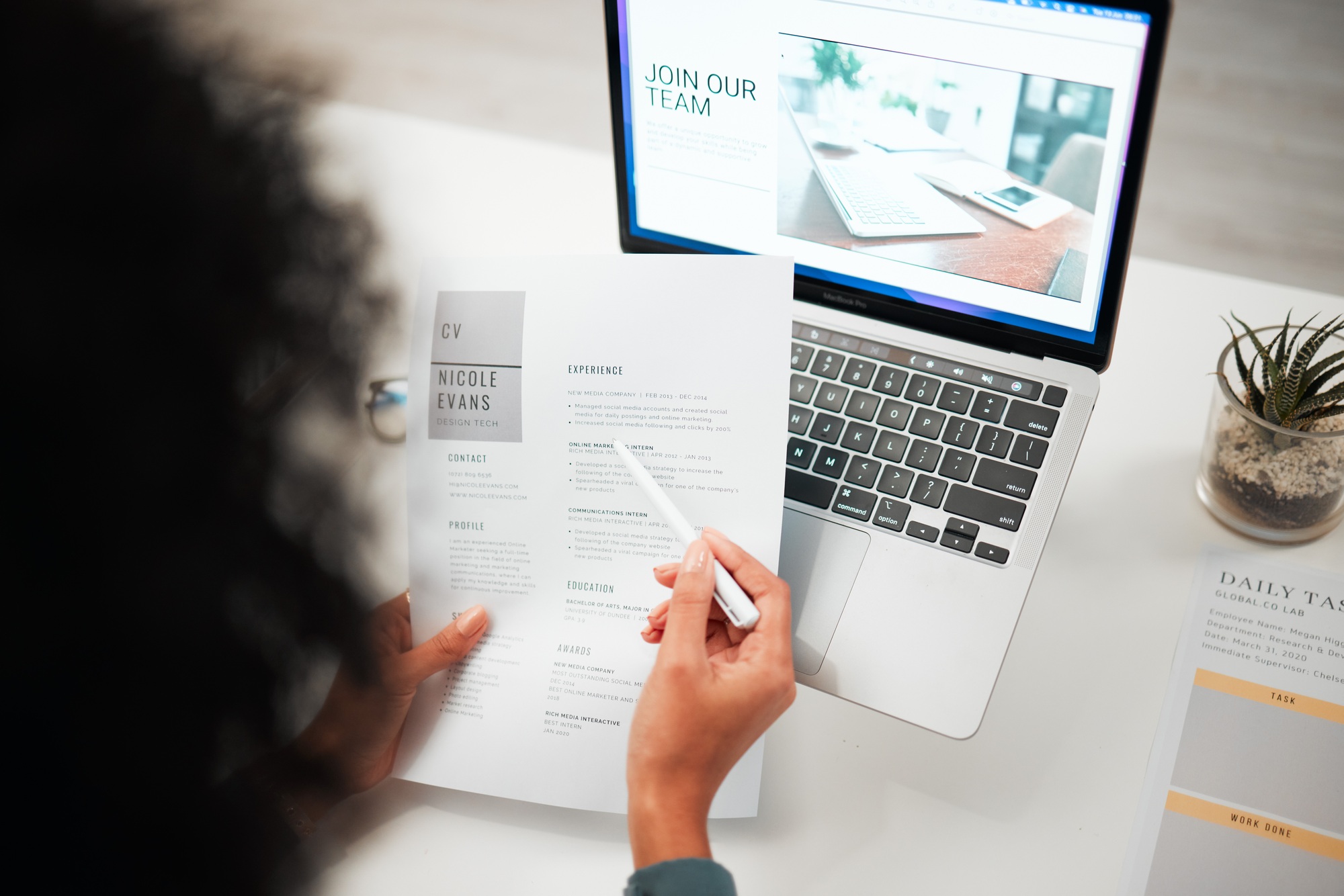
How to Choose the Right Special Skills for Resume Success
Learn how to choose, organize, and present special skills for resume success. This guide includes technical and soft skills, comparison tables, and AI-friendly strategies to pass ATS filters and stand out in competitive job markets.