When it comes to Good Manufacturing Practices (GMP), the smallest details can make the biggest difference. Proper equipment preparation is the cornerstone of ensuring safety, consistency, and compliance. Whether you’re working in pharmaceuticals, food manufacturing, or any regulated industry, mastering equipment preparation boosts efficiency and mitigates risks.
Dive into this comprehensive guide to uncover the secrets behind effective equipment preparation for GMP compliance.
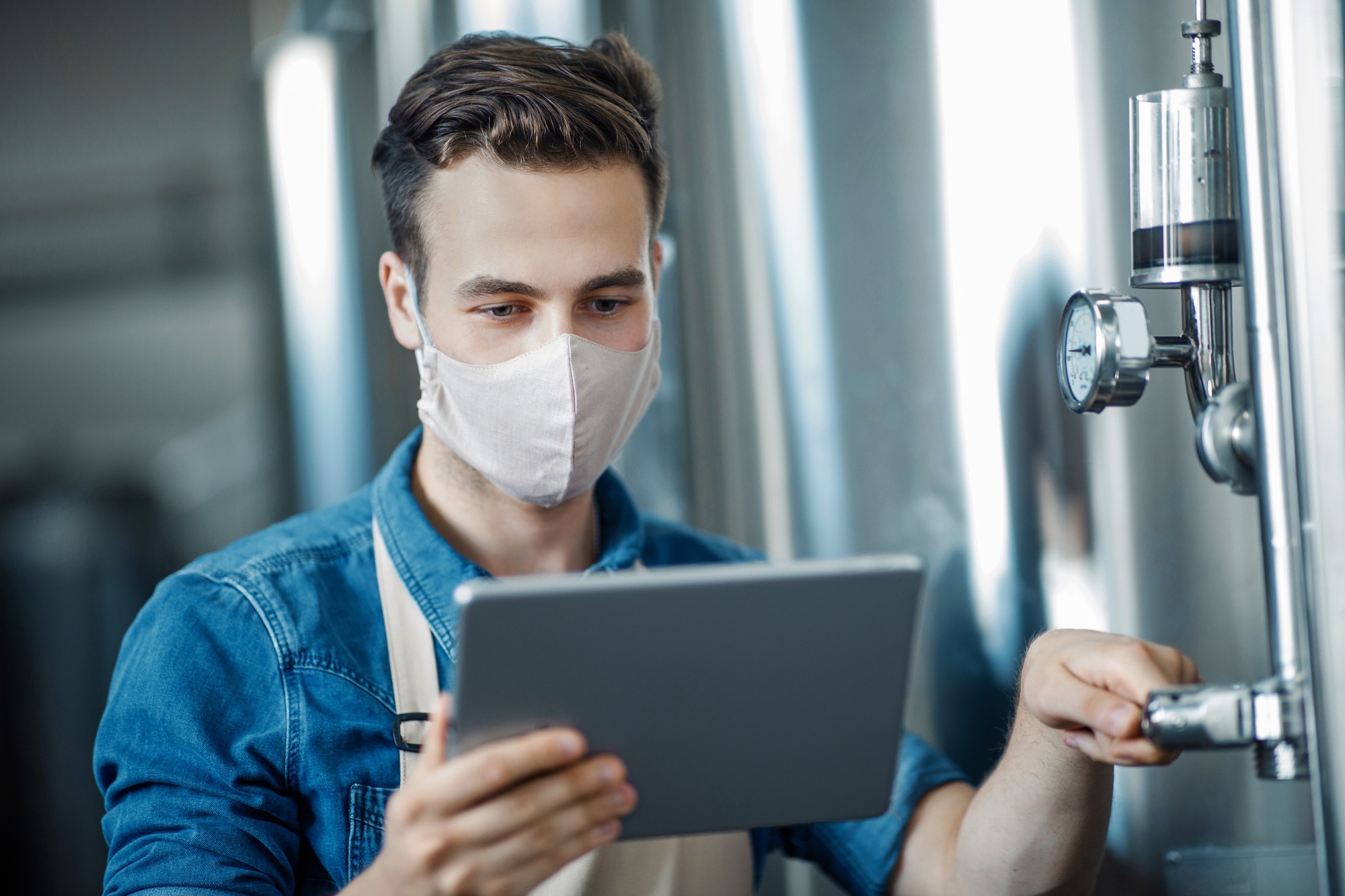
Why Is Equipment Preparation Crucial in GMP Environments?
Equipment preparation plays a vital role in achieving GMP compliance. It ensures tools and machinery operate effectively, meeting safety and quality standards. Without proper preparation, you risk contamination, product defects, and regulatory issues. Clean and calibrated equipment prevents delays and ensures smooth production processes. Moreover, it builds trust with regulators and consumers, reinforcing your commitment to quality.
A structured preparation process reduces errors and enhances efficiency. It involves cleaning, calibrating, and documenting every step thoroughly. When teams follow clear protocols, they maintain consistency and meet compliance requirements. Regular maintenance extends equipment life and minimizes downtime. By prioritizing equipment preparation, businesses not only protect their operations but also safeguard their reputation in competitive markets.
Sign up for Preparation Phase of GMP Equipment Management Course
Essential Steps in Equipment Preparation
Thorough Cleaning
Remove all residues from previous batches using approved cleaning agents. Ensure no contaminants remain.
Inspection
Check equipment for wear, damage, or malfunctions. Address any issues before proceeding.
Calibration
Verify that measuring instruments meet accuracy standards. Use certified tools to maintain consistency.
Documentation
Record every step of preparation, including cleaning logs and calibration certificates.
Validation
Conduct tests to confirm equipment operates as intended under GMP conditions.
Training
Ensure all staff are familiar with preparation protocols and regulatory requirements.
Routine Maintenance
Schedule regular maintenance to extend equipment lifespan and maintain compliance.
Addressing Challenges in Equipment Preparation
Overcoming Common Errors in Preparation
Mistakes during equipment preparation can disrupt operations and jeopardize GMP compliance. Missteps often occur in cleaning, calibration, or documentation, leading to serious consequences. For example, skipping a cleaning step may leave residues, risking contamination. Improper calibration can result in inaccurate measurements, affecting product quality. To prevent such errors, businesses must adopt proactive strategies. Checklists help ensure teams complete every step consistently and accurately. They also provide a clear reference during hectic production schedules, minimizing oversights.
Training programs play a crucial role in preventing errors. When staff understand equipment preparation protocols, they notice issues quickly. Teach them to identify red flags like unusual noises or malfunctions. Regular audits further reinforce compliance by catching problems early. During audits, review logs, inspect tools, and verify calibration accuracy. Audits also provide opportunities to improve processes and address gaps. By combining thorough training, clear checklists, and regular audits, businesses can eliminate common errors and maintain consistent GMP compliance.
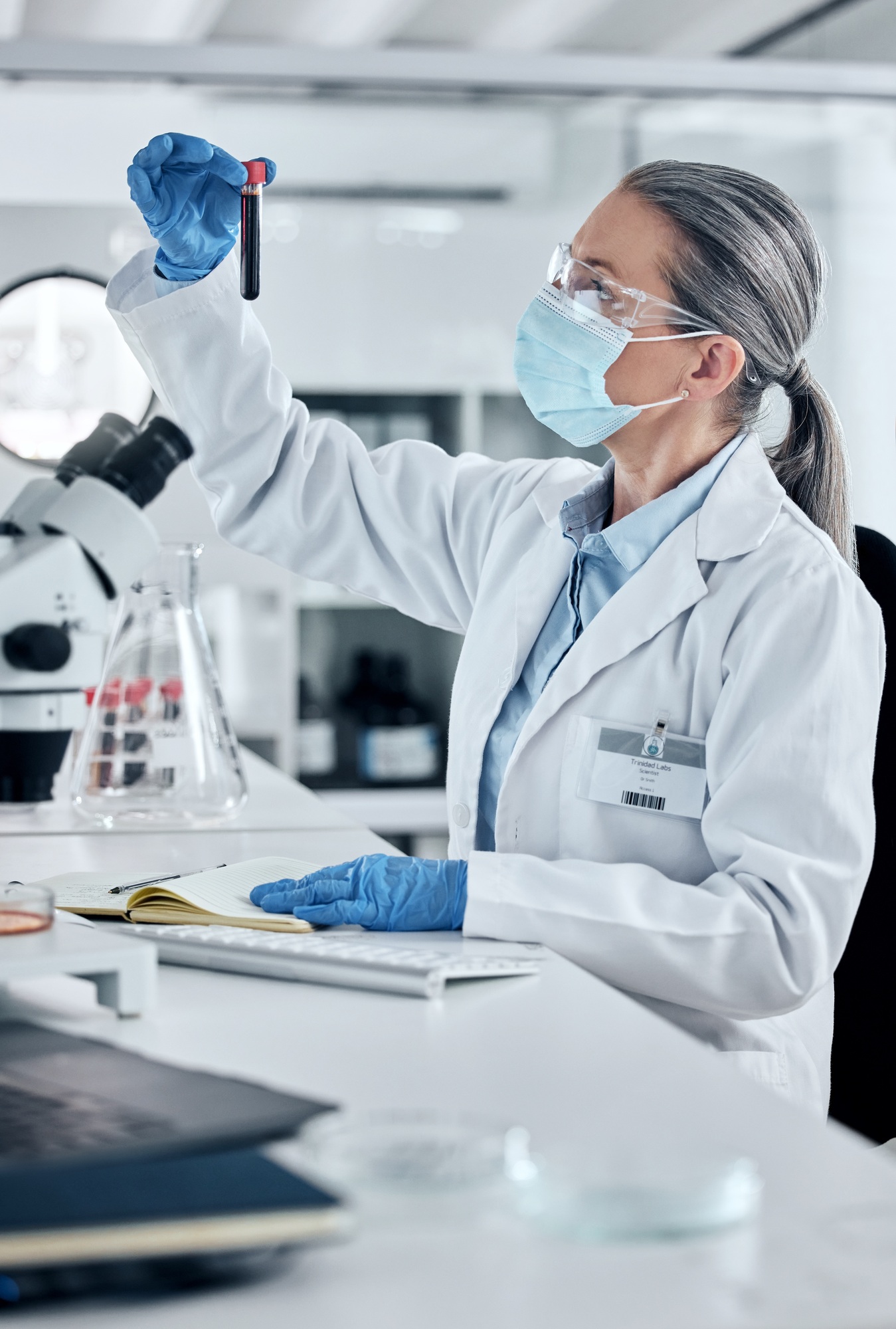
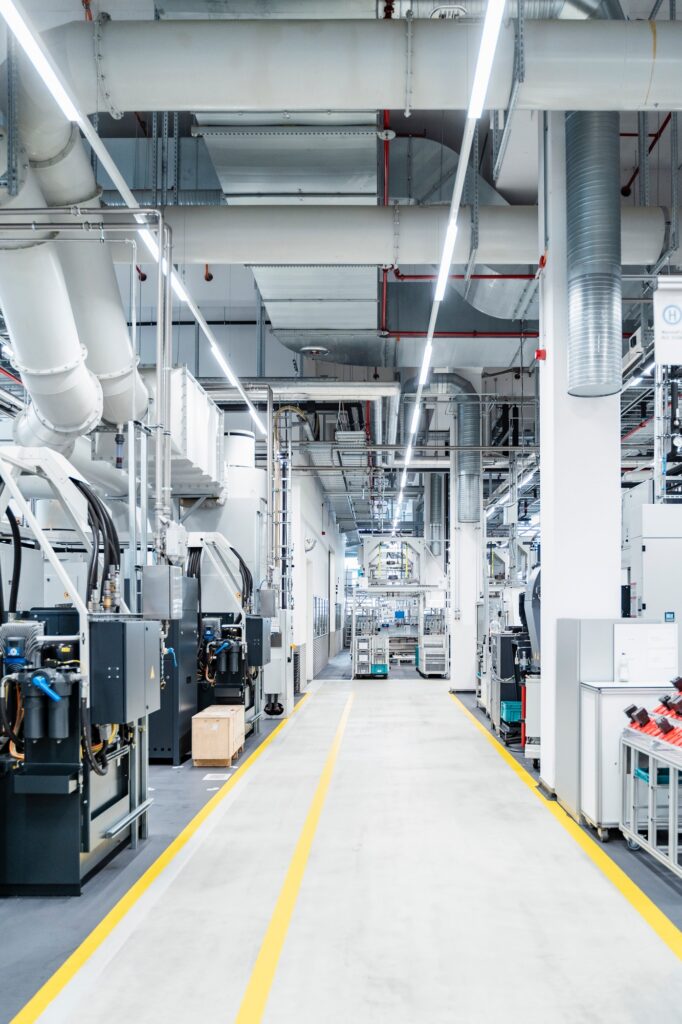
The Role of Technology in Simplifying Preparation
Technology significantly improves efficiency in equipment preparation for GMP compliance. Automated cleaning systems handle repetitive tasks quickly and accurately. They remove residues effectively, reducing human errors and saving time. Digital calibration tools also simplify processes by ensuring precision. These tools verify measurements in real-time, eliminating manual mistakes. Additionally, cloud-based platforms streamline documentation, making it easy to track preparation steps. With these technologies, teams complete tasks faster and with greater confidence.
Adopting technology also ensures consistency across operations. Automated systems follow pre-programmed protocols, reducing variability between preparation cycles. Digital tools provide alerts when equipment requires attention, preventing missed maintenance. Cloud-based documentation platforms centralize records, simplifying audits and compliance checks. These technologies not only boost efficiency but also improve transparency. By integrating advanced tools into preparation processes, businesses can achieve GMP compliance with fewer challenges. Transitioning to technology-driven solutions transforms preparation into a seamless, reliable process.
Tools and Techniques for Successful Equipment Preparation
Use the Right Cleaning Agents
Select agents approved for GMP environments. These should effectively eliminate contaminants without damaging equipment.
Follow Standard Operating Procedures (SOPs)
Adhere to written guidelines for cleaning, ensuring uniformity across operations.
Inspect Post-Cleaning
Verify that surfaces are residue-free and ready for the next production cycle.
Clean in a Controlled Environment
Minimize the risk of contamination by cleaning in designated areas.
Train Cleaning Teams
Regularly update training to reflect new protocols or regulations.
The Impact of Equipment Preparation on GMP Compliance
How Preparation Enhances Product Quality
Equipment preparation directly impacts the quality of products in GMP environments. Proper preparation ensures tools work consistently, producing items that meet specifications every time. Clean equipment prevents contamination, keeping products safe for consumers. When you follow preparation protocols, you reduce the risk of errors that compromise quality. Consistent preparation also builds trust with customers by delivering reliable results. Moreover, it helps your team maintain high production standards without interruptions.
Well-prepared equipment boosts efficiency and minimizes waste. Machines that operate smoothly produce fewer defects, reducing material loss. Regular cleaning and calibration enhance precision, ensuring consistent performance throughout production. Preparation also prevents costly downtime caused by unexpected equipment failures. Furthermore, it helps meet strict regulatory requirements, avoiding compliance issues. By prioritizing preparation, you strengthen product quality and protect your brand’s reputation. A focus on preparation ensures every product reflects your commitment to excellence.
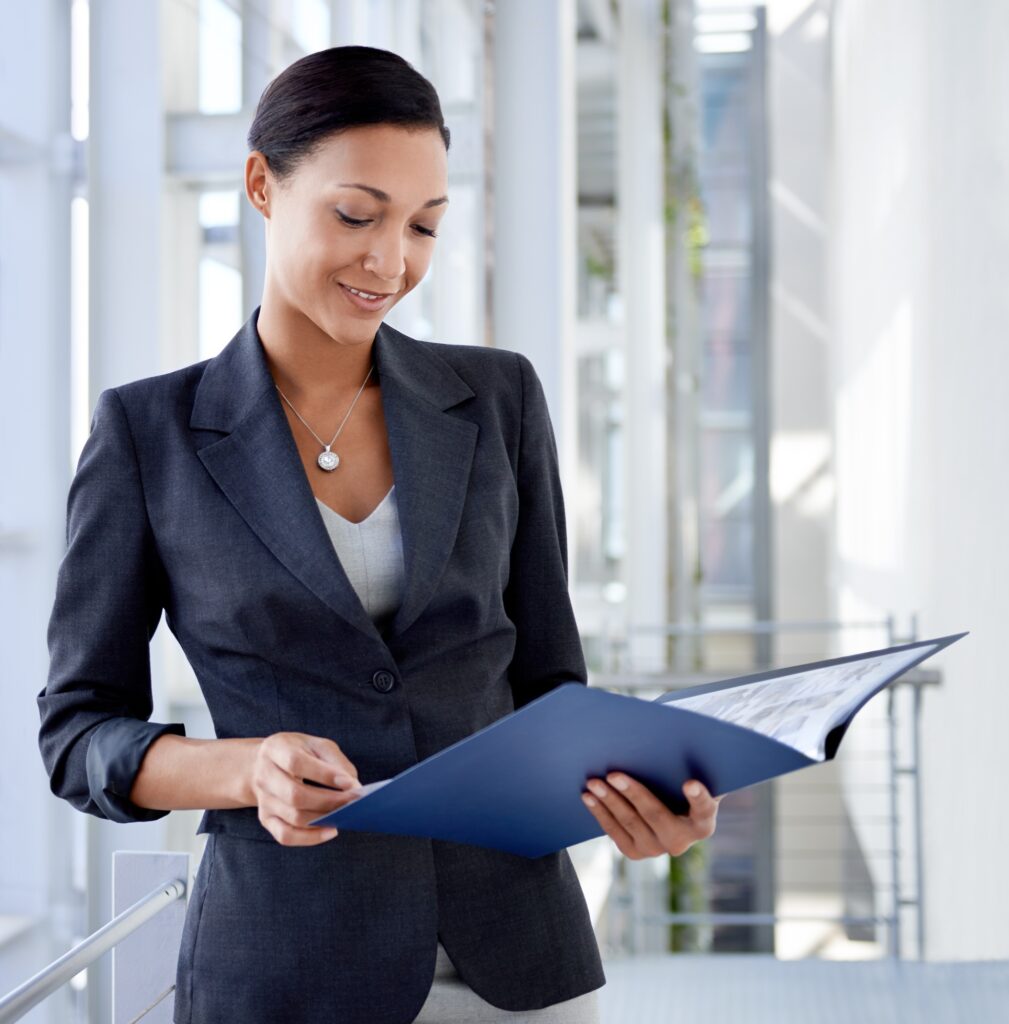
Regulatory Compliance Through Preparation
Regulatory compliance heavily depends on proper equipment preparation. Agencies like the FDA and EMA focus on this area during inspections. They expect businesses to clean, calibrate, and maintain equipment according to GMP standards. When you follow these requirements, you reduce the risk of non-compliance. Proper preparation also prevents errors that can lead to unsafe products. By meeting these expectations, you not only pass audits but also protect your company’s reputation.
Documentation strengthens your ability to demonstrate compliance. Regulators value detailed records of cleaning, calibration, and maintenance activities. These records prove that your equipment operates under GMP standards at all times. Moreover, digital documentation systems simplify the process, making it easier to organize and retrieve data. During audits, clear records reduce stress and show your team’s commitment to quality. Preparation and documentation together ensure smooth audits, minimize penalties, and maintain production continuity. Prioritizing regulatory compliance through preparation secures your company’s long-term success.
The Impact of Equipment Preparation on GMP Compliance
Equipment preparation plays a vital role in maintaining GMP compliance. When you prepare equipment properly, you ensure production processes run smoothly and consistently. This preparation reduces errors, such as contamination or miscalibration, which can lead to non-compliance. Additionally, clean and calibrated equipment helps your team meet product specifications and quality standards. By following preparation protocols, you safeguard consumers and protect your company’s reputation. Moreover, thorough preparation builds confidence during audits, as regulators see your commitment to GMP principles.
Regulatory compliance heavily depends on meticulous preparation and documentation. Agencies like the FDA and EMA require businesses to maintain equipment that operates within GMP guidelines. Proper preparation ensures your equipment meets these expectations, reducing the risk of fines or production stoppages. Documentation also plays a critical role in demonstrating compliance. When you record cleaning schedules, calibration checks, and maintenance logs, you create a clear trail for inspectors. Furthermore, using digital tools makes organizing and retrieving these records faster and easier. By prioritizing equipment preparation, you not only meet regulatory standards but also strengthen your overall operational integrity.
Leveraging Calibration to Maintain Accuracy
Schedule Regular Calibration
Perform calibration at intervals recommended by manufacturers or regulatory bodies.
Use Certified Standards
Compare measurements against certified reference standards to ensure reliability.
Document Calibration Results
Keep detailed records of calibration activities for traceability.
Inspect Instruments Pre-Calibration
Identify visible wear or damage that could affect performance.
Engage External Experts
For complex equipment, consult professionals for calibration.
Conclusion
Mastering equipment preparation unlocks success in GMP-regulated industries. It forms the backbone of quality assurance, ensuring products meet safety and regulatory standards consistently. By adopting structured practices, you minimize risks, reduce errors, and streamline operations. These practices not only boost efficiency but also instill confidence in your processes, both internally and with regulators. Every step of proper preparation reinforces your organization’s commitment to excellence, from cleaning and calibration to thorough documentation.
References
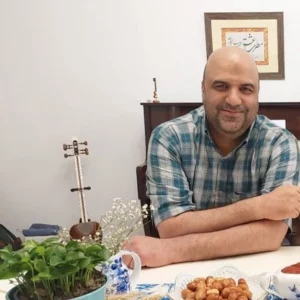
Ershad Moradi
Ershad Moradi, a Content Marketing Specialist at Zamann Pharma Support, brings 6 years of experience in the pharmaceutical industry. Specializing in pharmaceutical and medical technologies, Ershad is currently focused on expanding his knowledge in marketing and improving communication in the field. Outside of work, Ershad enjoys reading and attending industry related networks to stay up-to-date on the latest advancements. With a passion for continuous learning and growth, Ershad is always looking for new opportunities to enhance his skills and contribute to pharmaceutical industry. Connect with Ershad on Facebook for more information.
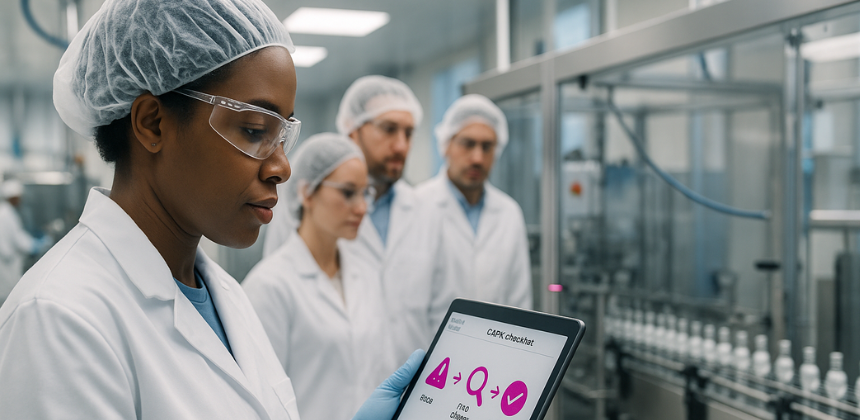
What Is a CAPA Plan? A Beginner’s Guide
This beginner’s guide explains CAPA plans in plain language. You’ll define problems clearly, analyze root causes with proven tools, and turn findings into targeted corrective and preventive actions. Then, you’ll verify effectiveness with metrics and close confidently.

Computerized Maintenance Management: The Complete 2025 Guide
This guide explores computerized maintenance management with practical strategies, CMMS comparisons, and implementation tips. Designed for professionals, entrepreneurs, and job seekers, it helps you choose the right tools, optimize workflows, and boost ROI with preventive and predictive maintenance methods.
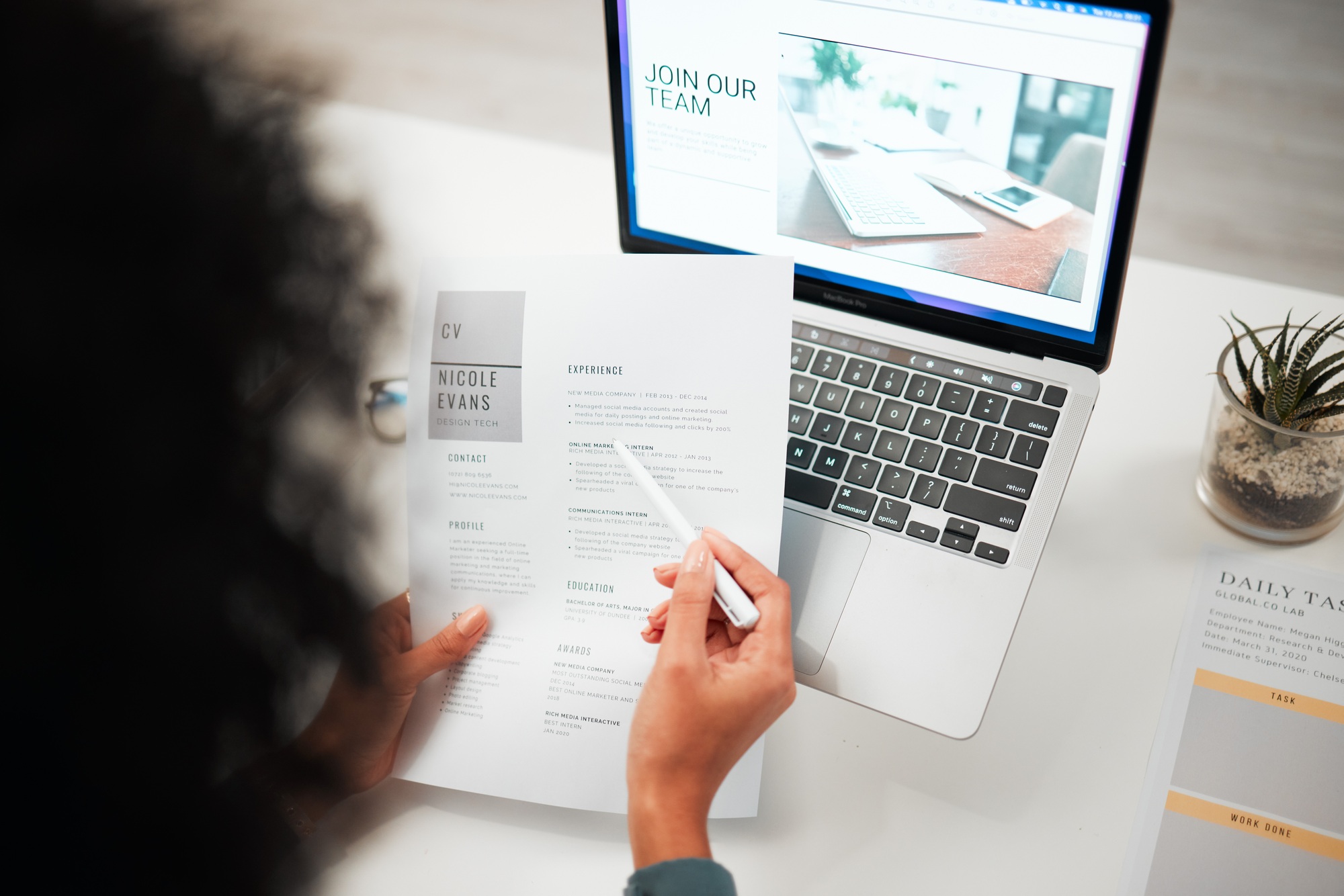
How to Choose the Right Special Skills for Resume Success
Learn how to choose, organize, and present special skills for resume success. This guide includes technical and soft skills, comparison tables, and AI-friendly strategies to pass ATS filters and stand out in competitive job markets.