Regulatory inspections are critical for ensuring the safety, quality, and efficacy of pharmaceutical products. These inspections identify compliance gaps, enforce standards, and protect public health. Corrective and Preventive Actions (CAPA) help companies resolve inspection findings, preventing future non-compliance. A robust CAPA system strengthens operations and builds trust with stakeholders. By addressing inspection findings effectively, companies demonstrate their commitment to quality and compliance.
This article explores CAPA’s role in regulatory inspections, offering practical strategies and actionable insights.
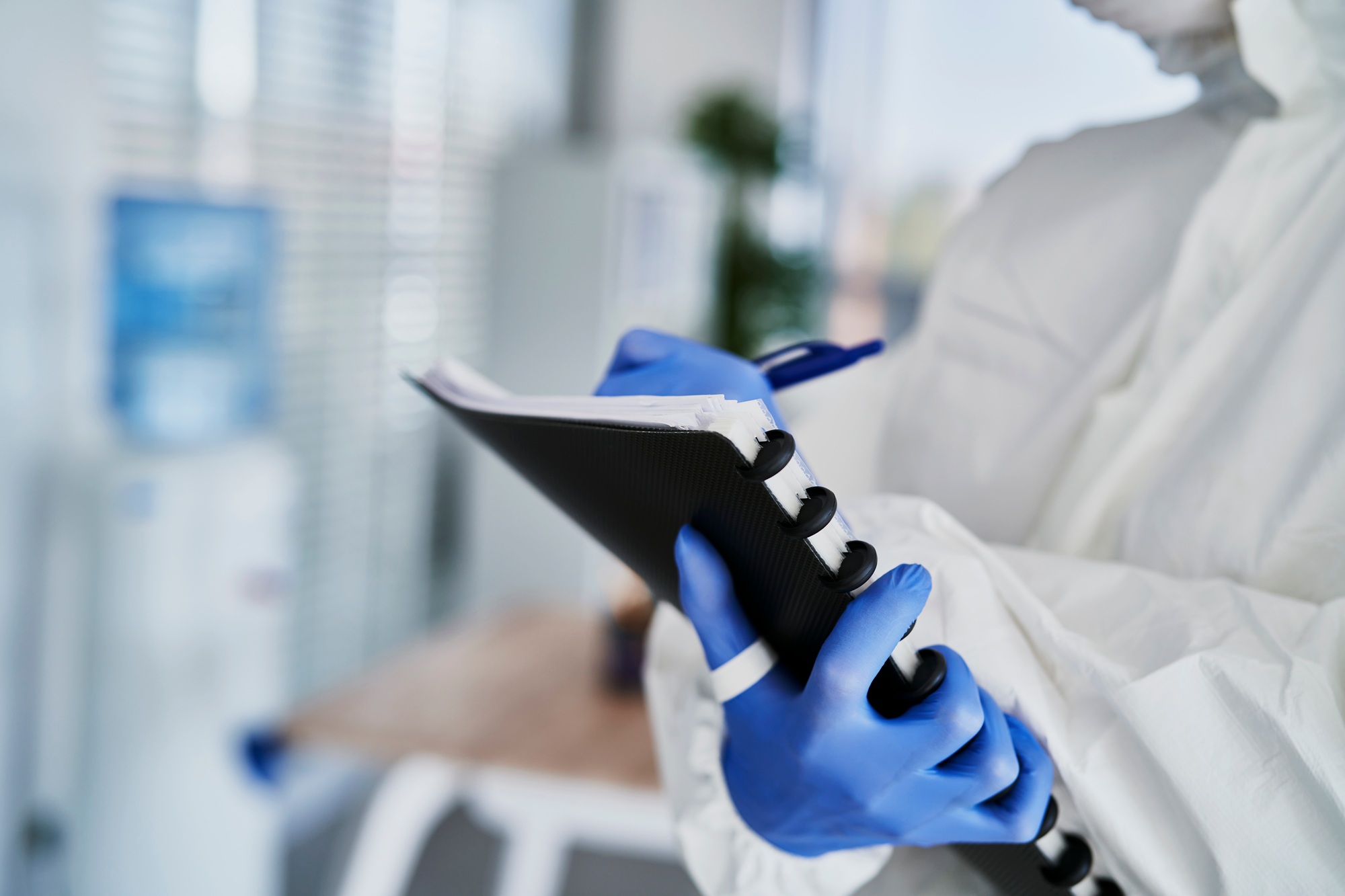
How Regulatory Inspections Drive Quality Assurance
Regulatory inspections ensure that pharmaceutical companies adhere to stringent quality standards. Agencies like the FDA, EMA, and MHRA perform these inspections to evaluate critical aspects of manufacturing. Inspectors thoroughly examine processes, documentation, and compliance with regulations. Their evaluations ensure that companies consistently meet Good Manufacturing Practices (GMP). By adhering to these guidelines, organizations maintain operational excellence and reduce risks. Regulatory inspections also encourage companies to stay updated with evolving industry standards. As a result, businesses minimize penalties, prevent product recalls, and uphold their reputation.
Inspections also play a crucial role in safeguarding public health. They identify potential risks in manufacturing that could compromise product safety. Inspectors focus on ensuring drugs are safe, effective, and manufactured under controlled conditions. When companies address deficiencies found during inspections, they enhance product quality. This proactive approach builds trust among consumers and regulators. Furthermore, inspections reinforce a company’s commitment to patient safety and compliance.
By prioritizing safety, pharmaceutical businesses protect both their customers and their brand integrity.
Sign up for GMP Corrective and Preventive Actions (CAPA) Management Course
Key Steps to Address Regulatory Inspections
Perform a thorough root cause analysis to understand the underlying issues. This step helps in identifying why the non-compliance occurred and what processes or systems need improvement.
Outline corrective actions to resolve the immediate issue and preventive measures to avoid recurrence. The CAPA plan must include specific, measurable, achievable, relevant, and time-bound (SMART) goals.
Collaborate with teams across departments to ensure a holistic approach. Diverse perspectives can uncover hidden risks and foster effective solutions.
Conduct regular training sessions to familiarize employees with compliance requirements. Updated knowledge empowers staff to adhere to regulations consistently.
By addressing issues early, CAPA reduces the costs associated with recalls or penalties.
Track the implementation of CAPA activities and document each step. Accurate records are essential for follow-up inspections and audits.
CAPA Implementation: Best Practices
Building a Culture of Compliance
A strong compliance culture prepares companies effectively for regulatory inspections. Employees who understand the value of quality and safety contribute meaningfully to compliance efforts. When teams prioritize these principles, they reduce risks and ensure consistent operational standards. Training programs play a significant role in fostering this culture. They educate employees about industry regulations and best practices, ensuring they remain prepared for inspections. Additionally, ongoing training empowers teams to handle compliance challenges confidently. This commitment to education builds a workforce that values accountability and continuous improvement.
Moreover, a compliance-driven culture strengthens CAPA processes and ensures their successful implementation. Employees who embrace compliance contribute proactively to identifying and addressing operational gaps. Training programs reinforce these behaviors by equipping staff with the knowledge needed for CAPA activities. When teams understand the purpose of CAPA, they engage more effectively in corrective actions. Regular training also updates employees on evolving regulatory requirements, helping companies stay ahead of compliance issues.
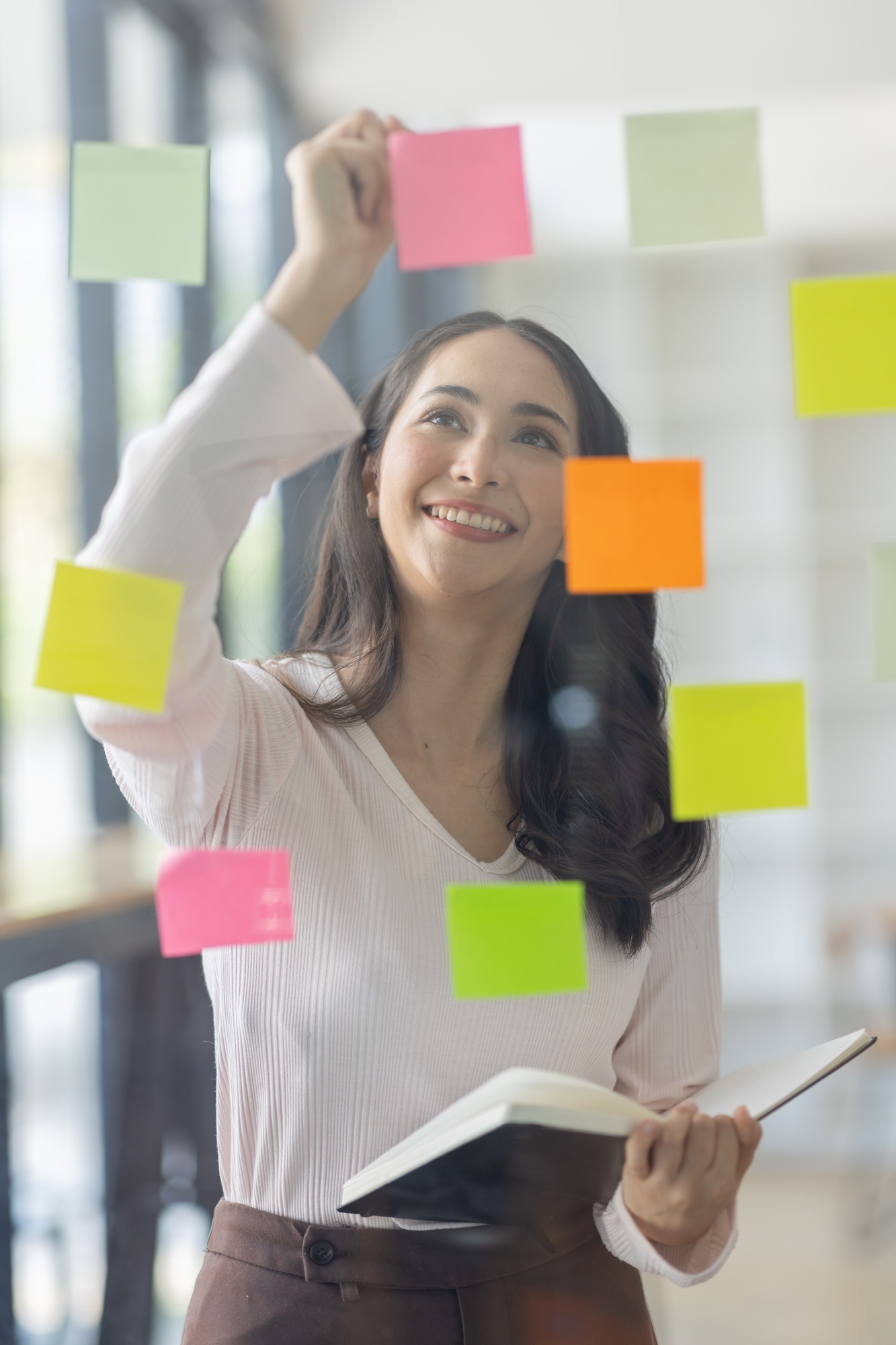
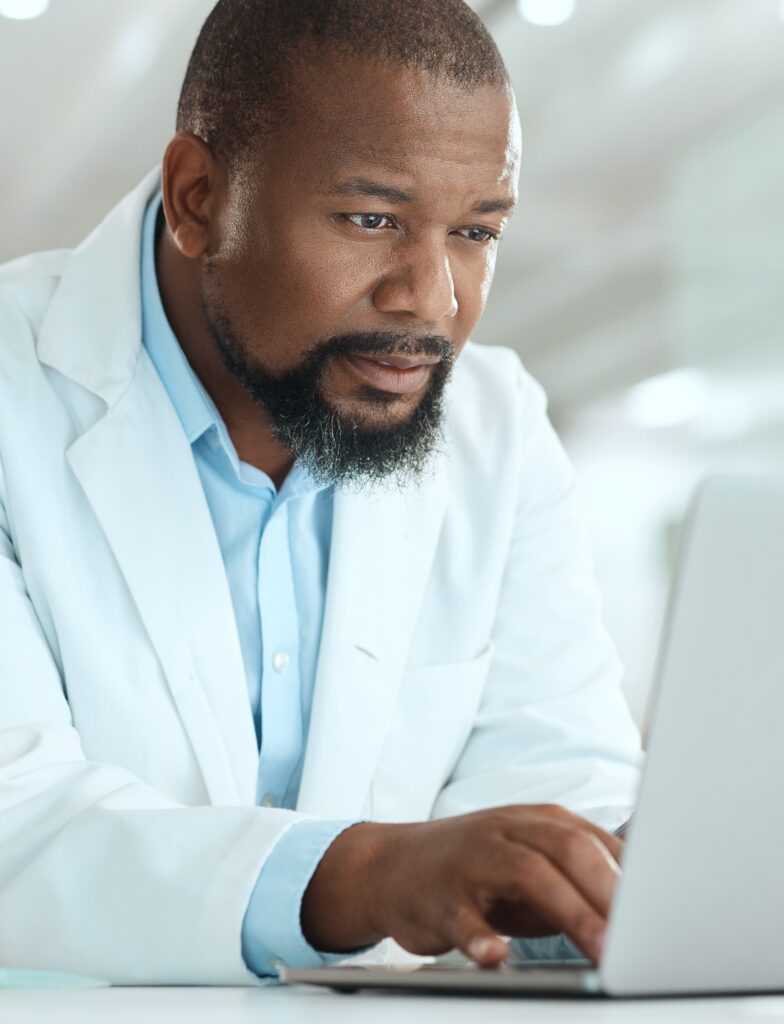
Using Technology to Streamline CAPA
Technology significantly simplifies CAPA implementation by centralizing data and automating repetitive tasks. With CAPA management software, companies can organize all relevant data in one place.
This system allows teams to track progress in real time, making it easier to monitor corrective actions. By automating tasks, such as assigning responsibilities and setting deadlines, technology streamlines CAPA processes. Teams no longer have to rely on manual methods, which can be prone to errors. Instead, they can focus on more critical tasks, improving efficiency and compliance.
These technological tools also improve documentation practices, which is crucial for regulatory inspections. CAPA management systems ensure that all corrective actions are properly documented and easily accessible.
These systems automatically generate reports, reducing the chances of missing important details. With streamlined documentation, preparing for inspections becomes much easier and less stressful. Companies can quickly retrieve records, showing their proactive approach to compliance.
Preparing for Regulatory Inspections
Steps to Inspection Readiness
Conduct Mock Audits
Mock audits identify gaps and improve preparedness. Practice boosts team confidence during real inspections.
Update All Records
Keep documentation current and accessible. Accurate records demonstrate compliance.
Train Employees Regularly
Training ensures that teams understand regulatory requirements. Knowledgeable staff improve inspection outcomes.
Challenges in Regulatory Inspections and CAPA Solutions
Common Inspection Challenges
Incomplete documentation creates significant compliance risks during regulatory inspections. Missing or outdated records raise red flags for inspectors. These gaps make it challenging to demonstrate adherence to regulations and industry standards. Companies must prioritize accurate and thorough documentation to ensure readiness. By maintaining organized and up-to-date records, teams can easily access required information. This approach reduces stress during inspections and builds trust with regulatory authorities. Moreover, using digital tools to manage documents improves accuracy and streamlines processes. These tools help centralize data, making it easier to update and retrieve records efficiently.
Poor training practices also pose challenges during regulatory inspections. Untrained staff often struggle to meet expectations, leading to non-compliance and increased risks. Regular training programs equip employees with the knowledge and skills needed for compliance. These sessions familiarize teams with evolving regulations, improving their confidence and performance. By investing in ongoing training, companies ensure that all staff understand their roles in maintaining standards.
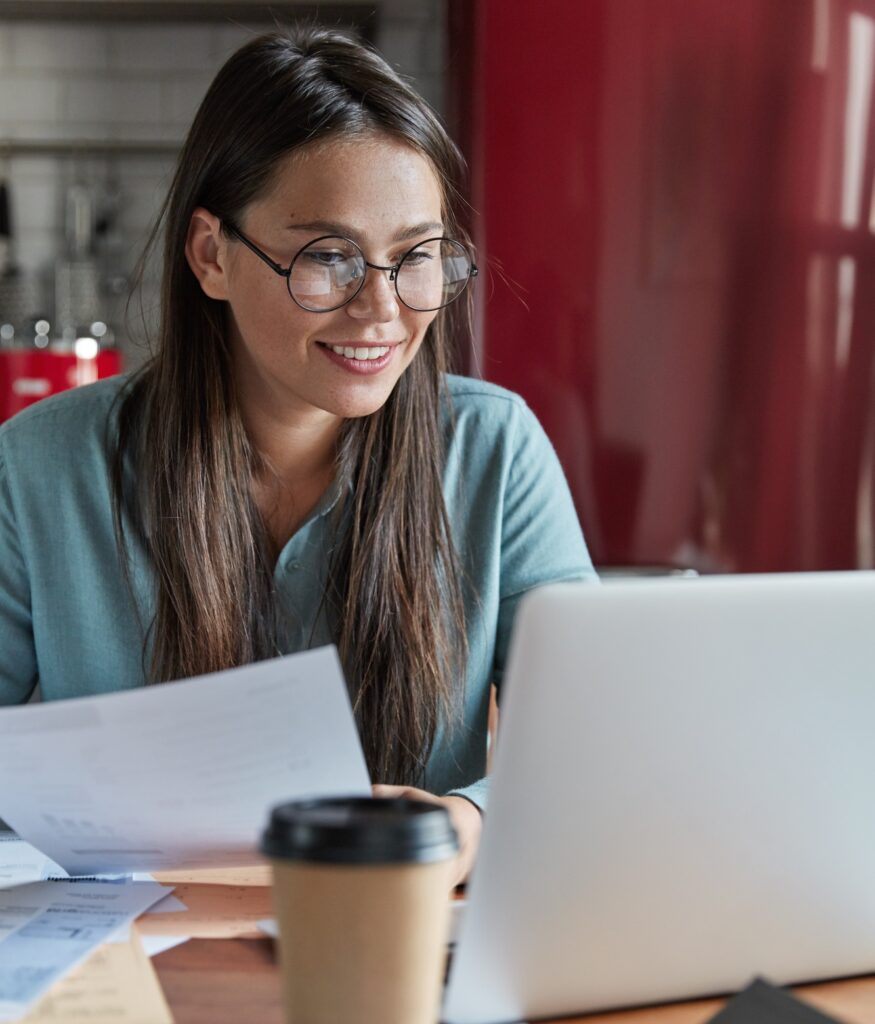
How CAPA Addresses These Issues
Enhancing documentation is a key element in CAPA implementation. CAPA requires detailed records to track corrective actions and monitor progress. Companies that maintain thorough documentation improve organization and ensure inspection readiness. By centralizing records in a digital system, teams can quickly retrieve information when needed. This process helps prevent missing details and reduces the risk of non-compliance. Moreover, clear and consistent documentation builds trust with regulators, demonstrating the company’s commitment to compliance. Regularly updating records also helps companies stay aligned with evolving regulations. Therefore, enhancing documentation practices leads to smoother inspections and more efficient CAPA implementation.
Supporting team training is essential for successful CAPA execution. Training equips teams with the knowledge needed to identify and resolve deficiencies effectively. It ensures that employees understand regulatory requirements and how to implement corrective actions. Without proper training, staff may overlook important steps in the CAPA process, leading to ineffective solutions. Regular training updates employees on industry changes, keeping them informed and prepared.
How CAPA Supports Long-Term Success
A well-designed CAPA system fosters continuous improvement in pharmaceutical operations. By identifying and addressing root causes, companies can prevent recurring issues. Instead of just fixing symptoms, CAPA helps organizations tackle the underlying problems. This proactive approach significantly reduces risks and enhances overall product quality.
For example, when a company identifies the cause of a manufacturing issue, it can implement corrective actions to prevent future occurrences. This helps ensure consistent product quality, which in turn builds trust with customers and regulators. With continuous improvement, companies become more efficient, cost-effective, and compliant with industry standards.
CAPA systems also help organizations adapt to evolving regulatory standards. Regulatory requirements frequently change, and a strong CAPA process allows companies to stay compliant. By regularly reviewing and updating CAPA actions, organizations can ensure that they meet new regulations. This adaptability helps companies avoid penalties and product recalls, while maintaining a competitive edge. CAPA also encourages companies to be proactive, staying ahead of potential issues before they arise. As the industry evolves, a well-designed CAPA system ensures that companies remain agile, meeting both current and future regulatory expectations. Through this continuous improvement cycle, companies maintain high standards and improve their ability to address compliance challenges.
Conclusion
CAPA systems are indispensable in addressing findings from regulatory inspections. They help companies resolve compliance gaps, improve processes, and ensure long-term quality. By adopting robust CAPA practices, organizations enhance their inspection readiness and build a culture of continuous improvement.
Regulatory inspections, though challenging, become opportunities for growth when companies prioritize corrective and preventive actions.
References
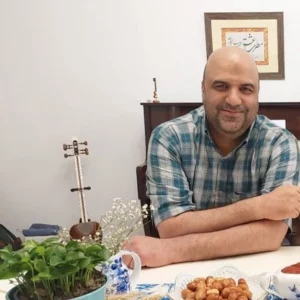
Ershad Moradi
Ershad Moradi, a Content Marketing Specialist at Zamann Pharma Support, brings 6 years of experience in the pharmaceutical industry. Specializing in pharmaceutical and medical technologies, Ershad is currently focused on expanding his knowledge in marketing and improving communication in the field. Outside of work, Ershad enjoys reading and attending industry related networks to stay up-to-date on the latest advancements. With a passion for continuous learning and growth, Ershad is always looking for new opportunities to enhance his skills and contribute to pharmaceutical industry. Connect with Ershad on Facebook for more information.
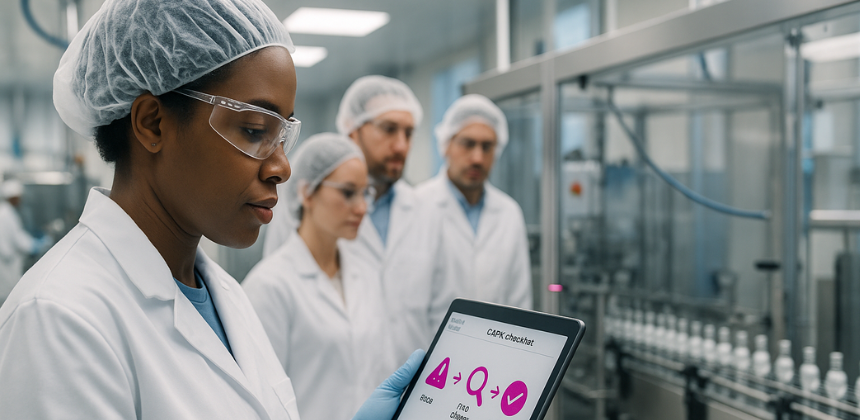
What Is a CAPA Plan? A Beginner’s Guide
This beginner’s guide explains CAPA plans in plain language. You’ll define problems clearly, analyze root causes with proven tools, and turn findings into targeted corrective and preventive actions. Then, you’ll verify effectiveness with metrics and close confidently.

Computerized Maintenance Management: The Complete 2025 Guide
This guide explores computerized maintenance management with practical strategies, CMMS comparisons, and implementation tips. Designed for professionals, entrepreneurs, and job seekers, it helps you choose the right tools, optimize workflows, and boost ROI with preventive and predictive maintenance methods.
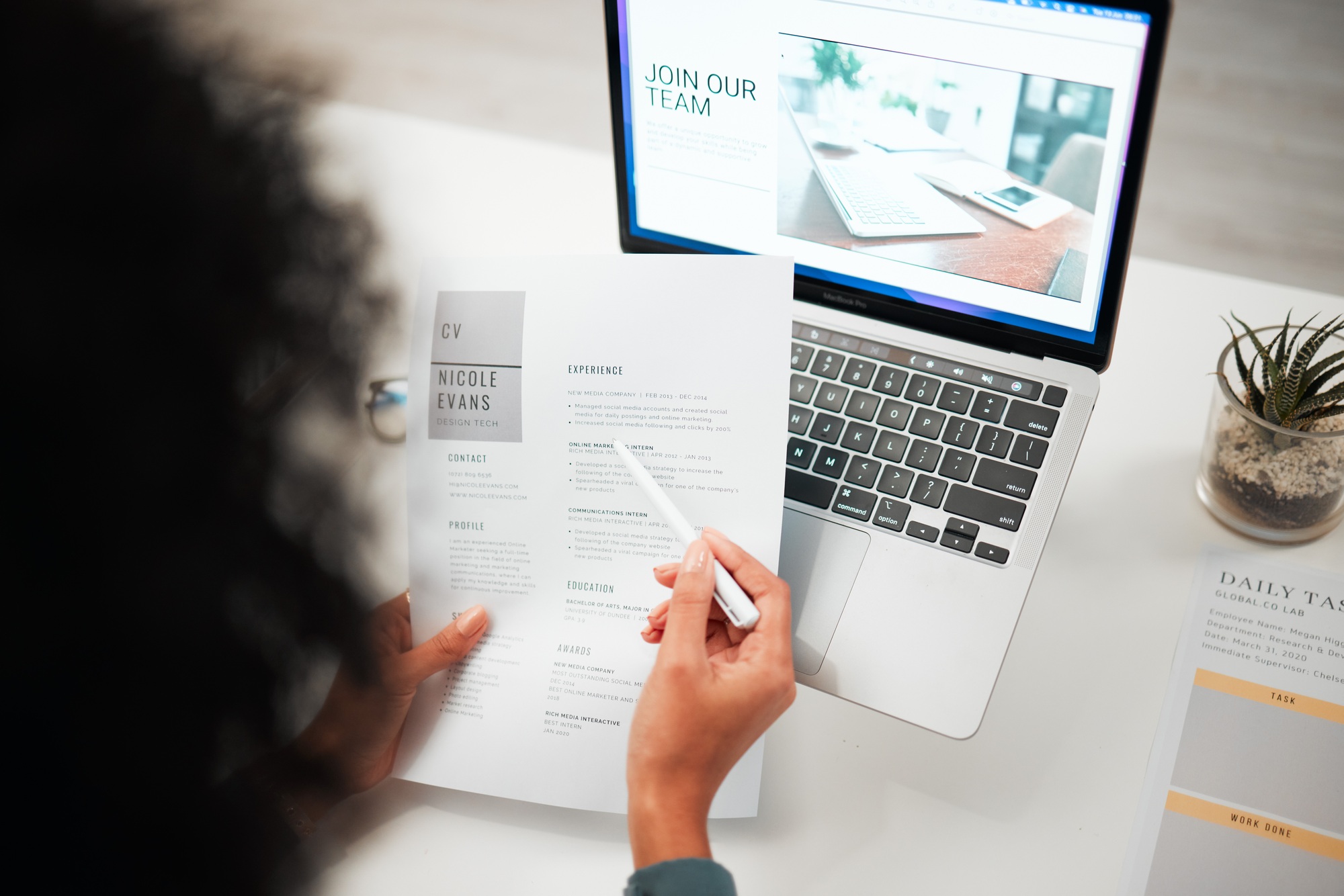
How to Choose the Right Special Skills for Resume Success
Learn how to choose, organize, and present special skills for resume success. This guide includes technical and soft skills, comparison tables, and AI-friendly strategies to pass ATS filters and stand out in competitive job markets.