The Risk-Based Approach underpins GMP by aligning activities with potential risks to product quality. It is a systematic process that involves identifying hazards, assessing their impact, and implementing control measures to minimize risks. Regulatory guidance such as ICH Q9 outlines a structured framework for integrating this approach into quality management systems.
Manufacturers benefit from RBA by focusing resources where they are most needed. For instance, critical production steps, like sterile filtration or temperature-sensitive storage, demand close monitoring. Conversely, low-risk activities require less oversight, enabling efficient resource allocation.
Pharmaceutical companies adopting an RBA reduce deviations, improve regulatory compliance, and ensure consistent product quality. This proactive strategy aligns quality processes with business goals, avoiding unnecessary costs and disruptions caused by quality failures.
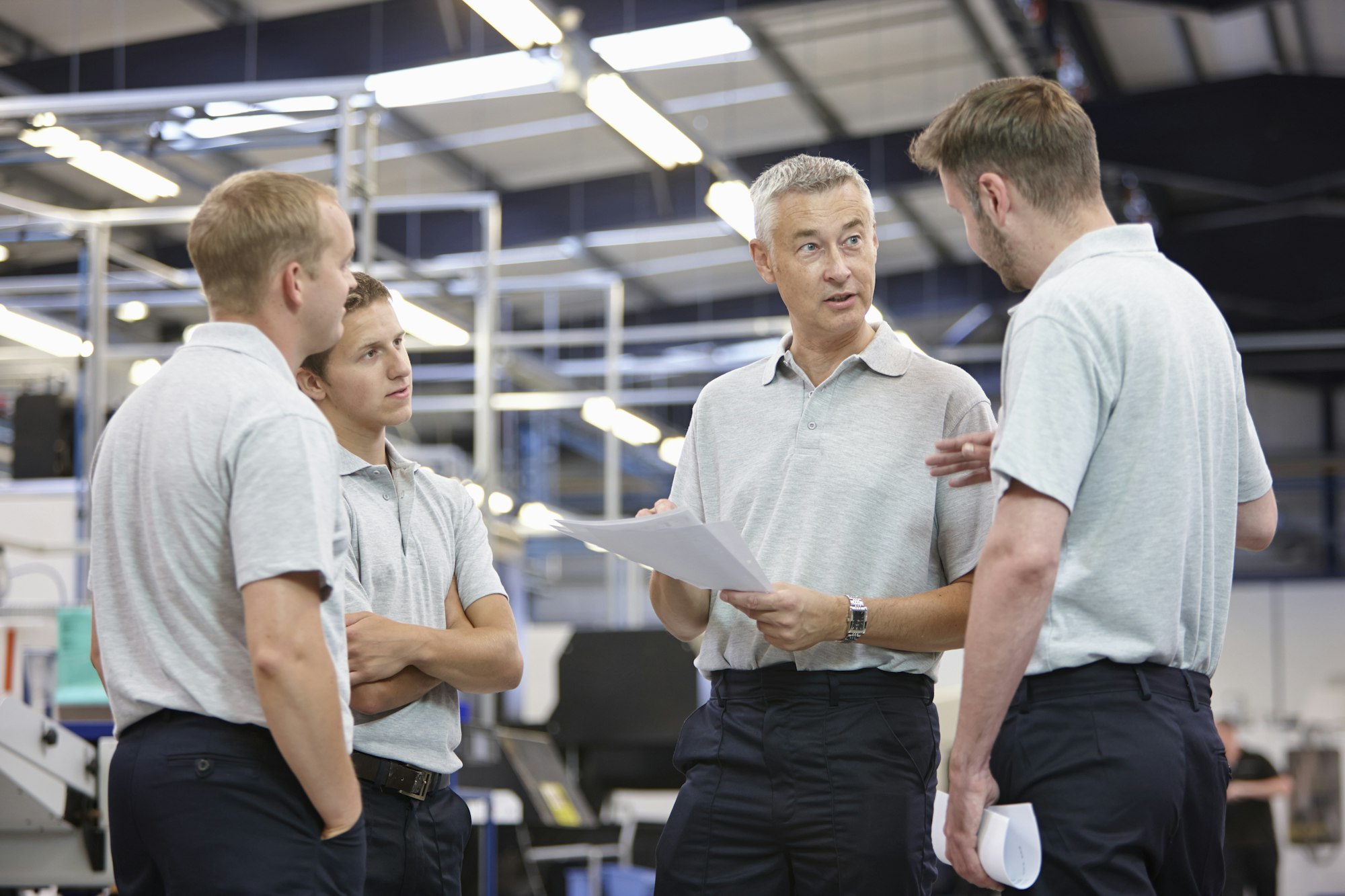
The Fundamentals of Risk-Based Approaches in GMP
The Risk-Based Approach strengthens GMP by focusing on risks that impact product quality. It helps manufacturers prioritize efforts on areas with the highest potential for harm. By identifying hazards early, teams can evaluate their likelihood and potential impact systematically.
This approach ensures efficient resource allocation, directing attention to critical processes like sterile filtration or temperature-sensitive storage. Additionally, tools like risk matrices and Failure Mode and Effects Analysis (FMEA) provide structured methods to assess and rank risks effectively. Using these tools, companies can make informed decisions and implement timely measures to reduce potential threats.
Regulatory guidelines, such as ICH Q9, offer a clear framework to integrate a Risk-Based Approach into GMP systems. These guidelines emphasize the importance of a proactive, data-driven strategy for managing quality risks. Companies that adopt these practices not only meet compliance requirements but also improve operational efficiency. For instance, they reduce unnecessary oversight in low-risk areas while maintaining strict control over critical operations. Moreover, integrating RBA into quality management systems fosters a culture of continuous improvement. Teams regularly review processes, adapt to changes, and ensure ongoing alignment with regulatory standards. This approach ultimately safeguards patient safety and reinforces trust in pharmaceutical products.
Sign up for Introduction to Good Manufacturing Practices (GMP) Free Course
Benefits of a Risk-Based Approach in GMP
A Risk-Based Approach offers multiple advantages for GMP compliance. These include:
Prioritize activities critical to product safety and quality, ensuring robust control.
Assign resources effectively to areas of high risk, reducing unnecessary costs.
Meet regulatory requirements by systematically addressing potential risks.
Use data-driven assessments to make informed decisions about risk controls.
Minimize the chances of costly recalls by proactively addressing risks.
Streamline operations by reducing oversight on low-risk areas.
Deliver consistent product quality, fostering confidence among patients and stakeholders.
Implementing Risk-Based Approach in GMP: Key Steps
Identifying and Assessing Risks
The Risk-Based Approach strengthens GMP by focusing on risks that impact product quality. It helps manufacturers prioritize efforts on areas with the highest potential for harm. By identifying hazards early, teams can evaluate their likelihood and potential impact systematically. This approach ensures efficient resource allocation, directing attention to critical processes like sterile filtration or temperature-sensitive storage. Additionally, tools like risk matrices and Failure Mode and Effects Analysis (FMEA) provide structured methods to assess and rank risks effectively. Using these tools, companies can make informed decisions and implement timely measures to reduce potential threats.
Regulatory guidelines, such as ICH Q9, offer a clear framework to integrate a Risk-Based Approach into GMP systems. These guidelines emphasize the importance of a proactive, data-driven strategy for managing quality risks. Companies that adopt these practices not only meet compliance requirements but also improve operational efficiency. For instance, they reduce unnecessary oversight in low-risk areas while maintaining strict control over critical operations. Moreover, integrating RBA into quality management systems fosters a culture of continuous improvement. Teams regularly review processes, adapt to changes, and ensure ongoing alignment with regulatory standards. This approach ultimately safeguards patient safety and reinforces trust in pharmaceutical products.
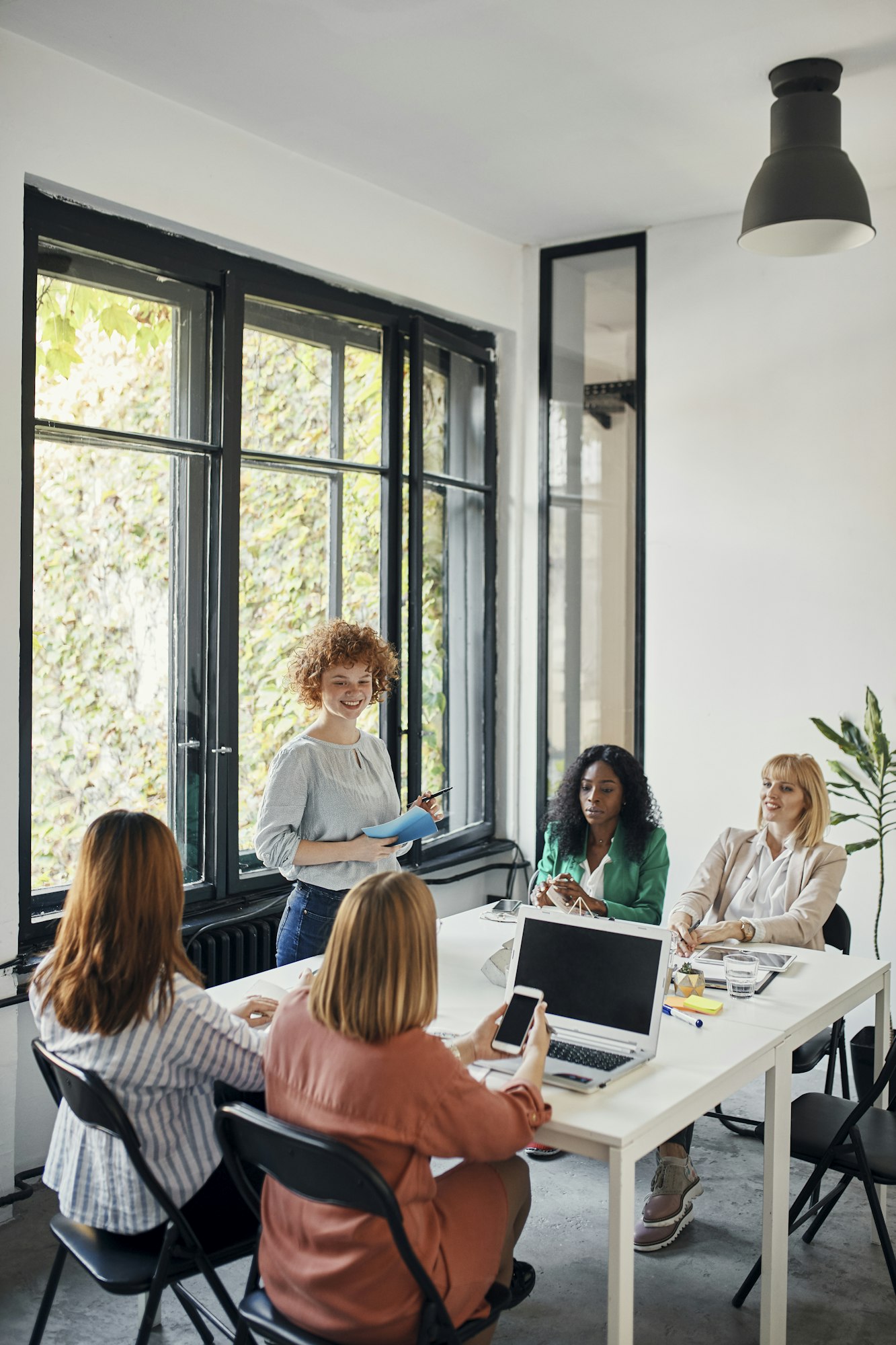
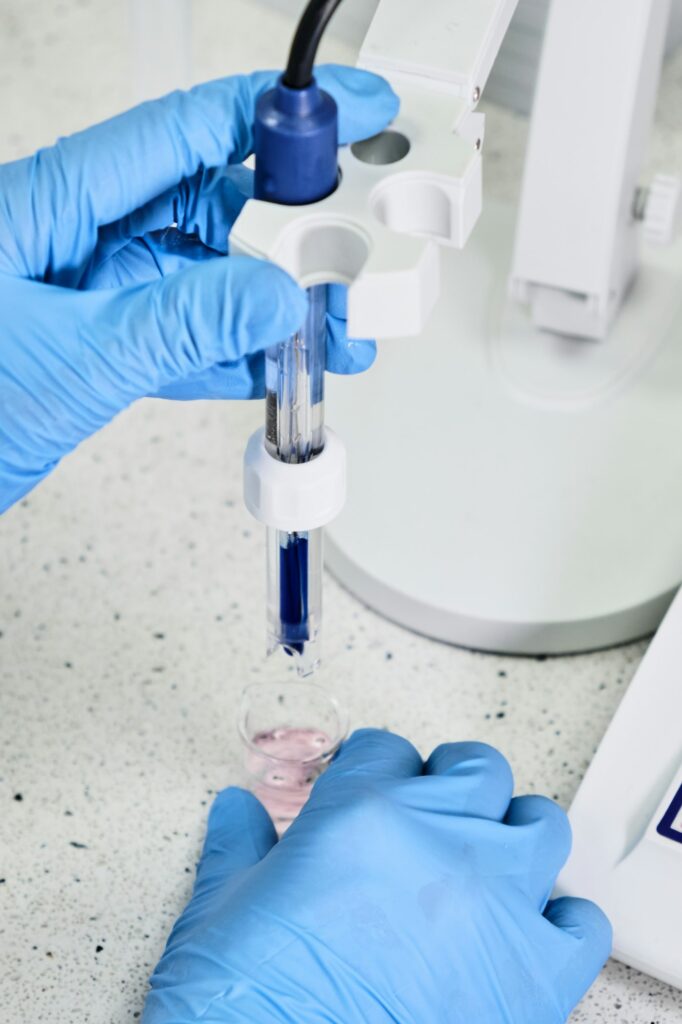
Developing Mitigation Strategies
Once you prioritize risks, implement control measures to address them effectively. Start by scheduling regular equipment calibrations to ensure machines operate accurately and reliably. Next, establish environmental monitoring programs to track critical factors like temperature, humidity, or cleanliness. These programs help detect potential issues early and prevent product contamination. Additionally, qualify your suppliers by assessing their reliability and compliance with industry standards. Reliable suppliers reduce risks associated with raw materials or outsourced services. These measures work together to maintain product quality and meet regulatory requirements.
Along with these strategies, invest in staff training to strengthen risk management practices. Educated employees can identify and address risks faster, minimizing disruptions to operations. Training programs should focus on GMP principles, risk assessment tools, and proper implementation of control measures. Teams that understand risks act with greater confidence and efficiency in their roles. Moreover, regular refresher courses ensure staff stay updated on new regulations or evolving risks. This proactive approach builds a culture of compliance and accountability throughout the organization. By combining well-planned control measures with thorough staff training, you create a robust system for managing risks.
Tools and Techniques for Effective Risk-Based Approach Implementation
Risk Identification Tools
1. Failure Mode and Effects Analysis (FMEA)
Analyze potential failure points and their impact.
Create mitigation plans based on severity rankings.
2. Hazard Analysis and Critical Control Points (HACCP)
Focus on preventing hazards in critical processes.
Ensure consistent monitoring and control.
3. Root Cause Analysis (RCA)
Investigate deviations to identify their origins.
Implement corrective actions to prevent recurrence.
Risk Assessment Techniques
1. Risk Matrices
Visualize risks by likelihood and severity.
Prioritize high-impact risks for immediate action.
2. Fault Tree Analysis (FTA)
Map failure pathways to understand system vulnerabilities.
Use insights to design more robust processes.
3. Quantitative Risk Assessment (QRA)
Use statistical models to evaluate risks numerically.
Support data-driven decision-making for mitigation.
Practical Applications of Risk-Based Approaches in GMP
Risk Management in Manufacturing
Risk management in manufacturing plays a crucial role in ensuring consistent product quality. A Risk-Based Approach helps manufacturers assess and control risks during production effectively. Start by evaluating process risks, such as deviations in critical parameters or operator mistakes. These risks can lead to defects or non-compliance, so addressing them early is essential. Use real-time monitoring systems to track production conditions and detect issues immediately. Regular audits further support this process by identifying areas needing improvement. By taking these proactive steps, manufacturers reduce the likelihood of failures and maintain operational efficiency.
Moreover, implementing corrective actions promptly strengthens risk management efforts. When monitoring systems flag a deviation, teams must investigate and resolve the issue quickly. This approach prevents small problems from escalating into costly failures. Training staff to follow standard operating procedures (SOPs) also reduces the chance of human error during production. Additionally, fostering communication between departments ensures risks are shared and addressed collaboratively. Manufacturers benefit from fewer disruptions, improved compliance, and better resource allocation.
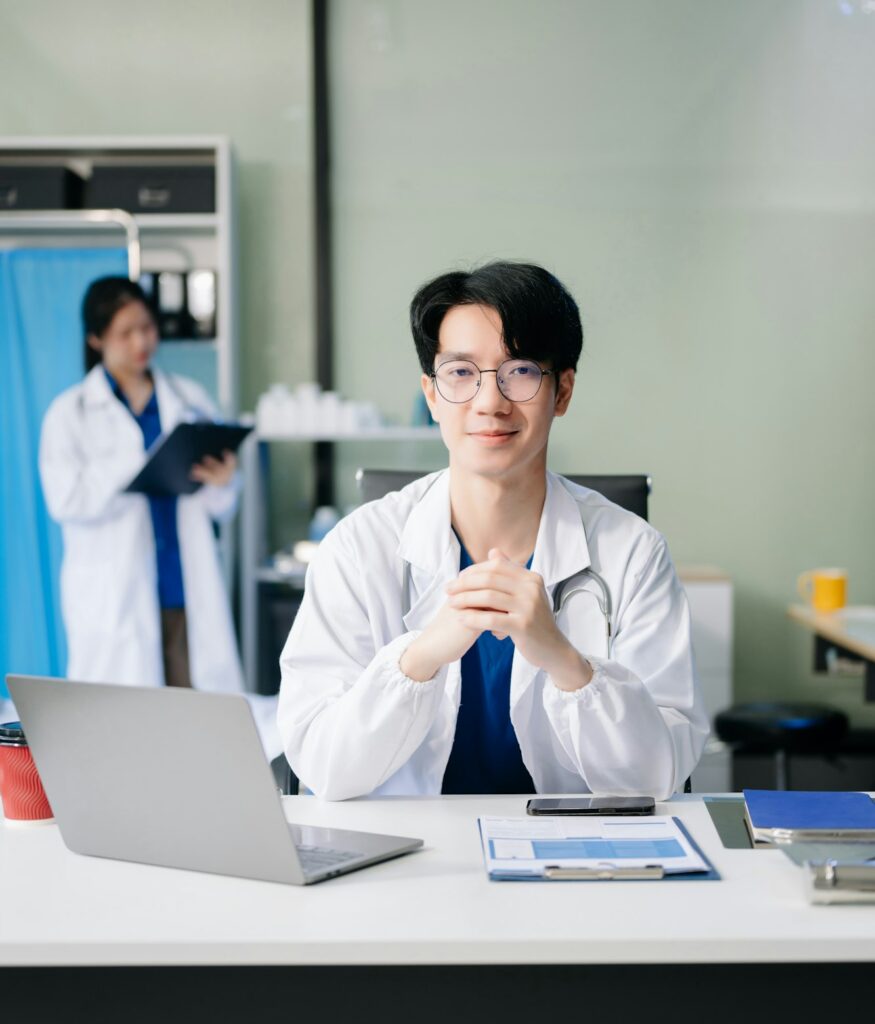
Role of Risk Assessment in Equipment Qualification
A Risk-Based Approach (RBA) is essential in equipment qualification for maintaining GMP compliance. Begin by categorizing equipment into classes (A, B, C) based on their risk level. Class A equipment, which has the highest impact on product quality, requires rigorous qualification and monitoring. Class B and C equipment, with lower risks, demand less stringent measures. This categorization helps companies focus efforts on high-risk tools, ensuring critical equipment meets regulatory standards. By prioritizing resources in this way, manufacturers save time and streamline qualification processes. This targeted strategy also minimizes unnecessary delays and avoids redundant checks on low-risk equipment.
Moreover, RBA supports efficient management of qualification activities, reducing downtime while maintaining compliance. For example, companies can schedule calibration and performance checks more frequently for Class A tools. They can allocate fewer resources to Class B and C equipment, freeing time for critical tasks. Teams also benefit from clearer guidelines when performing qualifications, ensuring consistency across processes. By using data-driven insights, companies address potential risks before equipment issues arise. This approach improves operational efficiency, reduces disruptions, and builds confidence in equipment reliability.
Overcoming Barriers in Risk-Based Approach
To overcome barriers in Risk-Based Approach (RBA) implementation, focus on enhancing collaboration among teams. Start by involving cross-functional groups in risk assessment discussions to share diverse insights. This collaboration ensures all potential risks are considered from multiple perspectives. Create open communication channels to encourage feedback and transparency throughout the process.
When teams work together, they identify issues faster and develop practical solutions more effectively. Regular meetings and workshops can further strengthen these efforts, helping everyone align with the RBA’s objectives. By fostering teamwork, you create a culture where everyone takes responsibility for risk management.
In addition, leveraging technology plays a significant role in overcoming RBA implementation challenges. Advanced tools like digital twins simulate manufacturing processes, enabling teams to predict risks before they occur. Predictive analytics also helps analyze historical data to identify trends and anticipate future challenges. These technologies provide accurate, data-driven insights, allowing companies to make informed decisions quickly. Moreover, automated monitoring systems track real-time performance, helping teams address issues immediately. Investing in technology not only improves risk management accuracy but also boosts operational efficiency. By combining collaboration with cutting-edge tools, companies can effectively implement and sustain a strong Risk-Based Approach.
Overcoming Barriers in Risk-Based Approach Implementation
Enhancing Collaboration
Engage cross-functional teams in risk assessment discussions. A collaborative approach leverages diverse perspectives and strengthens outcomes.
Leveraging Technology
Use advanced tools like digital twins and predictive analytics to enhance risk management accuracy.
Providing Comprehensive Training
Train employees on RBA principles, tools, and processes to ensure consistent understanding and implementation.
Clear Communication
Create transparent communication pathways to ensure all stakeholders stay informed about risk management updates.
Developing Standardized Procedures
Write clear, standardized guidelines for risk assessment and mitigation to reduce inconsistencies across teams.
Securing Leadership Support
Gain buy-in from leadership to prioritize RBA implementation and allocate necessary resources effectively.
Utilizing Data Analytics
Analyze historical data to identify trends and anticipate potential risks in manufacturing processes.
Conclusion
A Risk-Based Approach (RBA) in GMP helps manufacturers prioritize what truly matters—product quality and patient safety. By focusing on high-risk areas, companies streamline their processes and improve compliance with regulatory requirements. This approach ensures efficient resource allocation, reducing unnecessary efforts in low-risk areas. Additionally, implementing structured strategies and leveraging advanced tools like risk matrices or predictive analytics simplifies risk management. Manufacturers can proactively address challenges, avoid costly disruptions, and maintain consistent product quality. These efforts not only enhance compliance but also build trust with stakeholders.
References
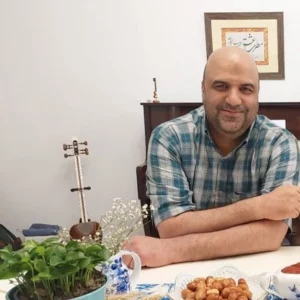
Ershad Moradi
Ershad Moradi, a Content Marketing Specialist at Zamann Pharma Support, brings 6 years of experience in the pharmaceutical industry. Specializing in pharmaceutical and medical technologies, Ershad is currently focused on expanding his knowledge in marketing and improving communication in the field. Outside of work, Ershad enjoys reading and attending industry related networks to stay up-to-date on the latest advancements. With a passion for continuous learning and growth, Ershad is always looking for new opportunities to enhance his skills and contribute to pharmaceutical industry. Connect with Ershad on Facebook for more information.
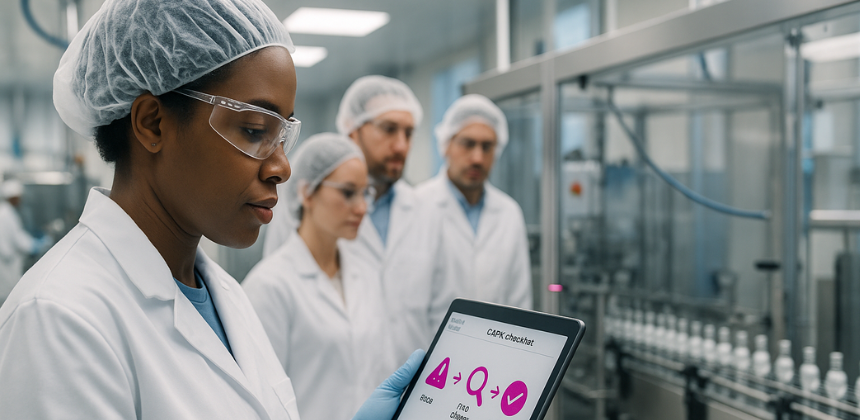
What Is a CAPA Plan? A Beginner’s Guide
This beginner’s guide explains CAPA plans in plain language. You’ll define problems clearly, analyze root causes with proven tools, and turn findings into targeted corrective and preventive actions. Then, you’ll verify effectiveness with metrics and close confidently.

Computerized Maintenance Management: The Complete 2025 Guide
This guide explores computerized maintenance management with practical strategies, CMMS comparisons, and implementation tips. Designed for professionals, entrepreneurs, and job seekers, it helps you choose the right tools, optimize workflows, and boost ROI with preventive and predictive maintenance methods.
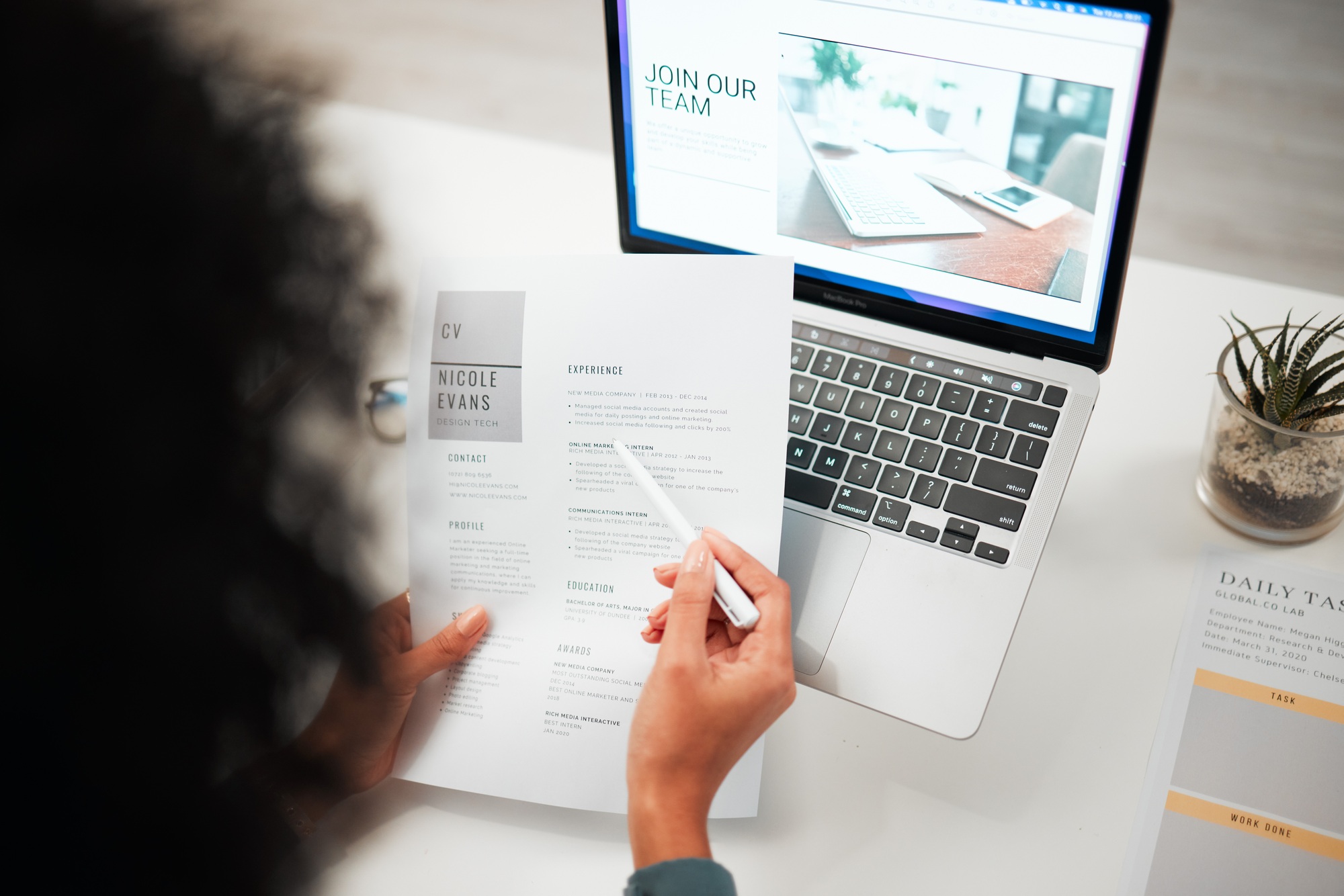
How to Choose the Right Special Skills for Resume Success
Learn how to choose, organize, and present special skills for resume success. This guide includes technical and soft skills, comparison tables, and AI-friendly strategies to pass ATS filters and stand out in competitive job markets.