The Role of CAPA (Corrective and Preventive Action) is essential for achieving and maintaining compliance with FDA and EMA regulations. These regulatory agencies require robust quality management systems (QMS) to ensure product safety, efficacy, and consistency. CAPA processes help organizations identify non-conformities, investigate root causes, and prevent recurring issues, directly contributing to regulatory adherence. FDA and EMA both emphasize CAPA as a critical component of their quality and safety standards.
This article explores the role of CAPA in meeting FDA and EMA requirements, its benefits, and practical steps to enhance CAPA implementation. Whether you manage pharmaceutical manufacturing, medical devices, or clinical trials, understanding CAPA will strengthen your compliance strategies.
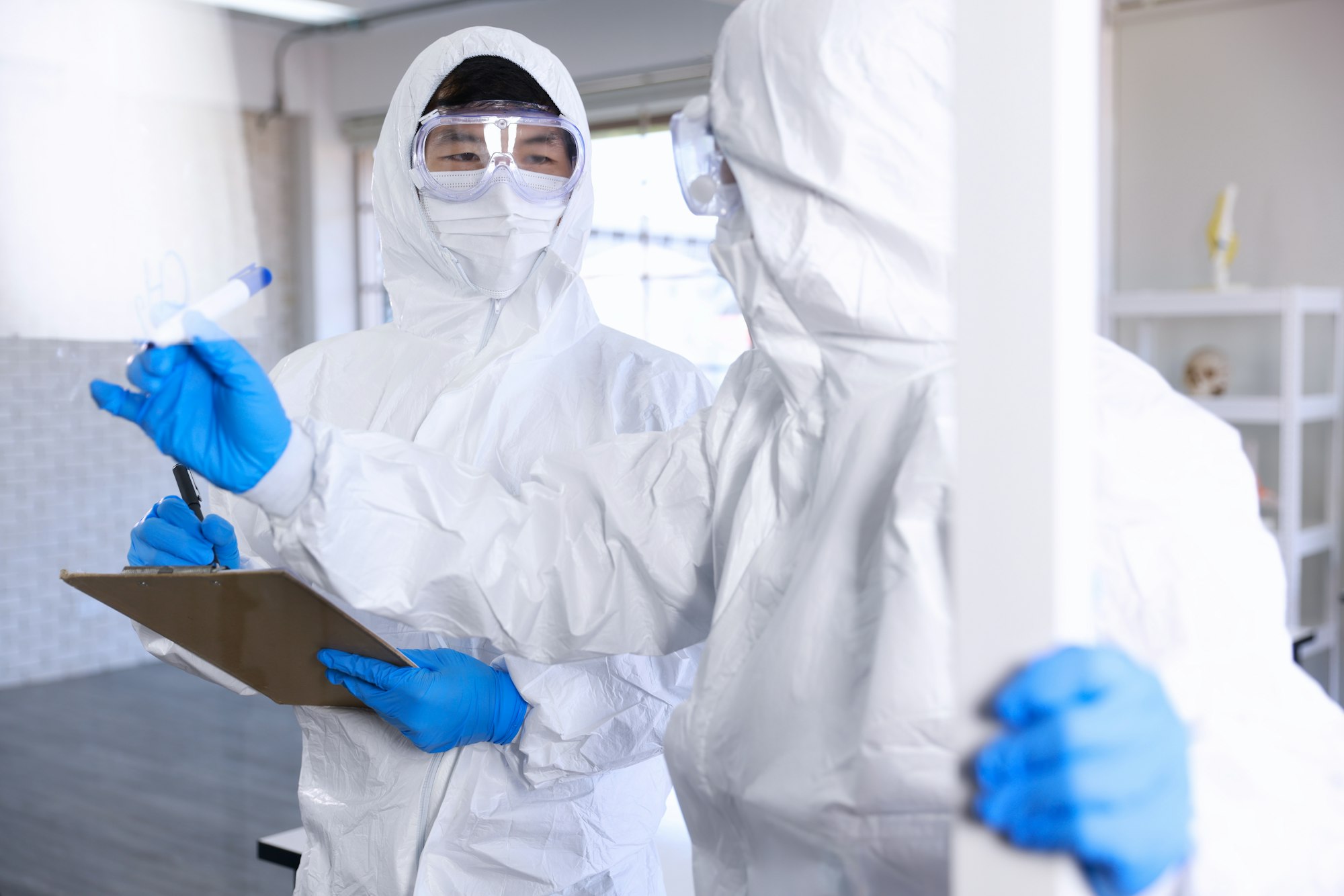
FDA Guidelines for CAPA
The FDA emphasizes CAPA in 21 CFR Part 820, which focuses on medical devices. This regulation requires companies to establish systems that identify, address, and prevent quality issues. Companies must actively investigate any deviations and implement corrective actions to resolve problems. Additionally, they must take preventive measures to stop similar issues from recurring. The FDA expects organizations to monitor their processes continuously and improve their quality systems. These efforts ensure that medical devices meet safety and effectiveness standards. By complying with this regulation, companies reduce risks, avoid penalties, and protect patients.
Similarly, 21 CFR Part 211 outlines CAPA requirements specifically for pharmaceutical manufacturing. This regulation highlights the need to detect and address deviations promptly. Companies must investigate root causes and implement corrective actions to restore compliance. Furthermore, preventive actions should focus on avoiding future problems and improving operational consistency. The FDA requires detailed documentation of CAPA activities to demonstrate compliance during inspections. These measures help ensure the safety, purity, and quality of pharmaceutical products. Adhering to these requirements not only satisfies FDA expectations but also builds trust with consumers.
Sign up for GMP Corrective and Preventive Actions (CAPA) Management Course
The Role of CAPA in Ensuring Regulatory Compliance
A robust CAPA system provides several advantages:
CAPA ensures compliance with FDA and EMA regulations, reducing the risk of non-compliance.
CAPA identifies and corrects defects, ensuring high-quality products.
It mitigates risks by preventing recurring issues.
CAPA strengthens audit readiness by demonstrating a proactive approach to quality.
By addressing issues early, CAPA reduces the costs associated with recalls or penalties.
CAPA enhances trust by delivering safe and reliable products.
The Role of CAPA in EMA’s Compliance Approach
The EMA includes CAPA in its Good Manufacturing Practices (GMP) guidelines to strengthen quality control. Inspectors assess CAPA during audits to confirm companies address and prevent quality issues. They check whether CAPA processes identify root causes and take corrective and preventive actions. As a result, companies improve their systems and reduce the risk of repeated problems. Furthermore, the EMA’s focus on CAPA helps ensure pharmaceutical companies maintain high-quality standards. By implementing CAPA effectively, businesses enhance compliance and avoid regulatory penalties.
In addition, CAPA aligns with the EMA’s commitment to patient safety and reliable product quality. It ensures companies prioritize the health and well-being of consumers. Through CAPA, businesses identify potential risks and take steps to mitigate them. This approach also supports consistency in manufacturing processes and reduces production errors. Moreover, CAPA fosters a culture of continuous improvement, benefiting both companies and patients. With CAPA, companies build trust and demonstrate their dedication to delivering safe and effective products.
The Role of CAPA in FDA and EMA Implementation
Addressing Quality Issues
Addressing quality issues promptly helps companies maintain compliance and meet regulatory requirements. CAPA plays a vital role in identifying problems and resolving them effectively. Furthermore, it supports a structured approach to managing risks and improving processes. By using CAPA systems, companies can quickly address quality issues before they escalate. This proactive strategy not only ensures compliance but also protects product integrity and patient safety.
The FDA focuses on thorough investigations and timely corrective actions to address quality problems. An effective CAPA system helps companies identify root causes and implement appropriate solutions. Moreover, it minimizes production delays and reduces the risk of warnings or recalls. Similarly, the EMA emphasizes CAPA integration into GMP frameworks to ensure compliance. Proactive CAPA implementation strengthens manufacturing processes and maintains consistent product quality. By addressing quality issues through CAPA, companies align with regulatory standards and build trust in their operations.
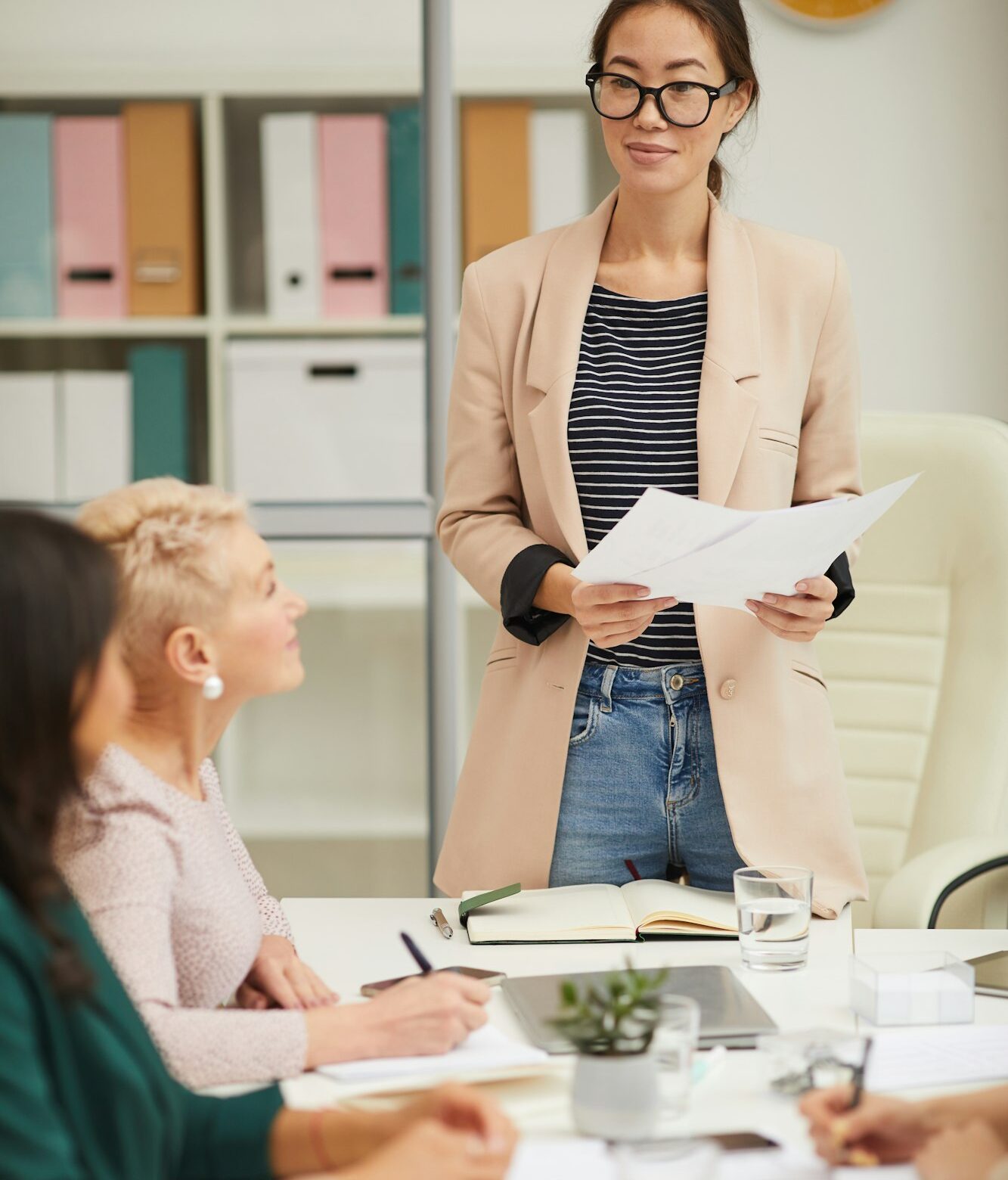
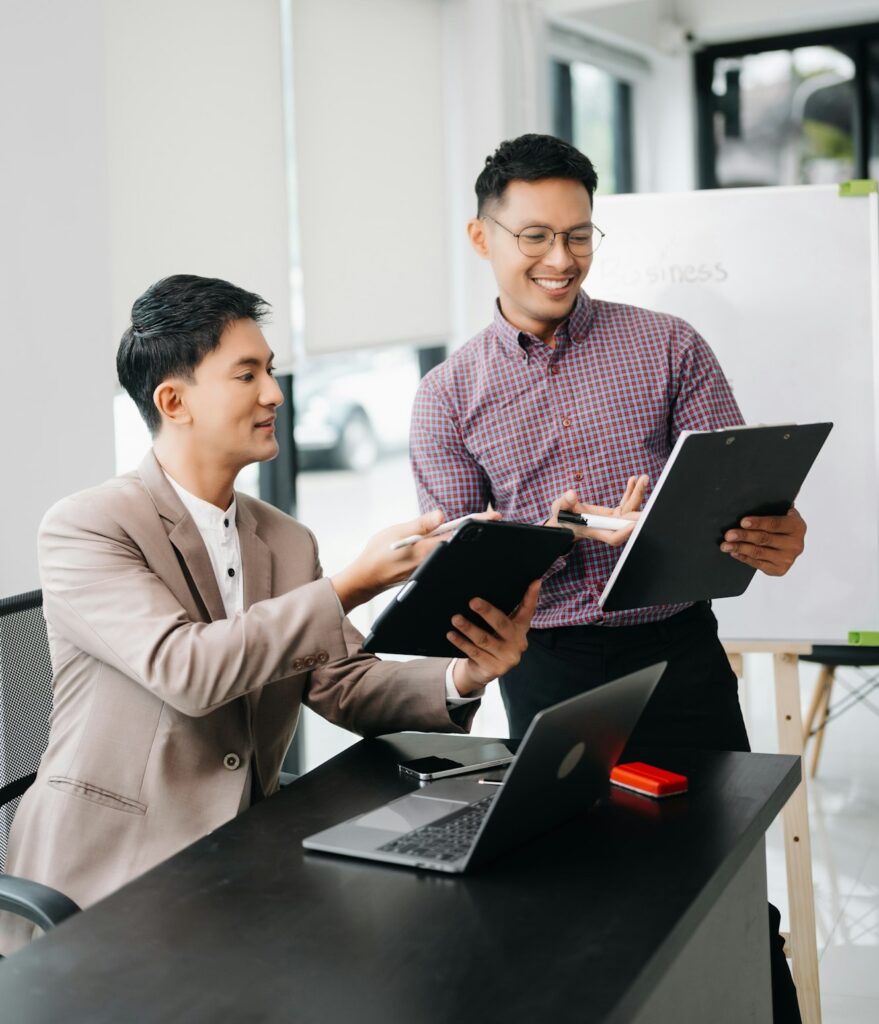
Integrating Preventive Measures
Integrating preventive measures into CAPA helps companies address potential issues before they occur. These actions focus on identifying risks and implementing solutions to eliminate them early. Furthermore, they reduce disruptions and improve overall operational efficiency. By preventing problems, companies save time and avoid unnecessary costs. Regularly analyzing data and monitoring processes further strengthens this proactive approach. As a result, businesses maintain smoother production workflows and consistent product quality.
Both the FDA and EMA highlight the importance of preventive actions in CAPA systems. The FDA encourages companies to use risk management strategies that prioritize prevention over correction. Similarly, the EMA emphasizes proactive measures to maintain compliance and protect patient safety. These preventive actions ensure higher standards and fewer regulatory violations. Moreover, companies that integrate such measures build a culture of continuous improvement. By aligning with these regulatory expectations, businesses enhance their credibility and ensure long-term success.
Steps to Enhance CAPA Effectiveness
Follow these steps to align CAPA processes with FDA and EMA requirements:
Define Responsibilities
Assign roles to ensure CAPA tasks are executed effectively.
Perform Root Cause Analysis
Use methods like the 5 Whys to identify root causes.
Develop Action Plans
Create actionable steps for corrective and preventive measures.
Execute Timely Actions
Resolve issues promptly to avoid delays.
Verify Effectiveness
Assess whether CAPA actions successfully resolve issues.
Document Everything
Keep detailed records for audits and inspections.
The Role of CAPA in Driving Continuous Improvement
FDA’s Emphasis on Quality
The FDA emphasizes quality by promoting CAPA as a key tool for improvement. CAPA helps companies identify issues and implement corrective and preventive actions effectively.
Moreover, it ensures processes align with evolving regulatory standards and industry expectations.
By prioritizing CAPA, organizations create systems that address problems and prevent them from recurring. This proactive approach not only enhances product quality but also strengthens overall compliance efforts.
Organizations that follow the FDA’s guidance on CAPA build robust systems to manage risks. CAPA encourages thorough investigations to find root causes and develop long-lasting solutions. Furthermore, it supports continuous improvement, ensuring companies adapt to regulatory changes. By focusing on CAPA, businesses reduce the likelihood of production delays and costly recalls.
Additionally, this focus fosters trust with regulators and consumers, reinforcing the company’s commitment to safety and quality.
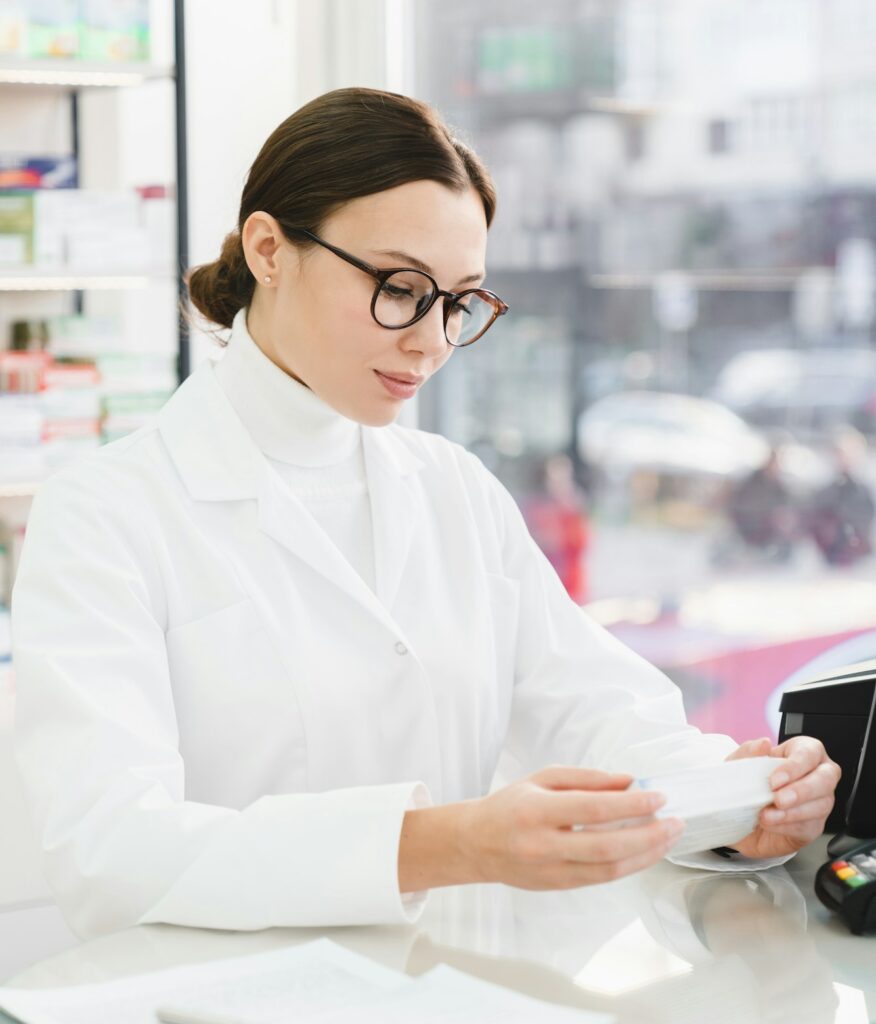
EMA’s Focus on Patient Safety
The EMA places a strong focus on patient safety by prioritizing CAPA in its guidelines. CAPA helps pharmaceutical companies identify risks and address them before they affect patients. Furthermore, it ensures that companies maintain high-quality standards throughout the product lifecycle. By implementing CAPA effectively, organizations reduce the chances of product defects and safety concerns. This proactive approach protects patients while enhancing the reliability of pharmaceutical products.
Effective CAPA processes also support the EMA’s commitment to continuous improvement in patient safety. These processes help companies analyze root causes and prevent recurring quality issues. Moreover, CAPA ensures consistency in manufacturing, which further enhances product safety. The EMA encourages companies to use CAPA to align their practices with regulatory expectations. By focusing on CAPA, organizations demonstrate their dedication to delivering safe and effective medicines. Additionally, this focus fosters public trust and reinforces the importance of patient care in the pharmaceutical industry.
The Role of CAPA in Building an Effective Quality System
An effective CAPA system includes several key components to meet FDA and EMA standards. First, companies must prioritize issue identification by detecting and logging quality deviations and complaints. Next, they should conduct root cause analysis to understand why problems occur. By identifying the root cause, organizations can take targeted corrective actions to resolve current issues. Furthermore, preventive actions help companies address risks and stop problems before they arise. These steps ensure smoother operations and protect product quality.
Documentation and verification also play crucial roles in a CAPA system. Companies need to maintain detailed records of all CAPA activities to prepare for audits. Additionally, they must verify the effectiveness of corrective and preventive actions to ensure success. Regular monitoring of CAPA processes helps businesses stay compliant and improve over time. By integrating these components, organizations align with regulatory expectations and strengthen quality control. Moreover, a robust CAPA system fosters continuous improvement, ensuring products remain safe and reliable for patients.
Conclusion
The role of CAPA in FDA and EMA compliance is indispensable. CAPA systems ensure organizations address quality issues, meet regulatory expectations, and enhance operational efficiency. By implementing robust CAPA processes, companies can maintain compliance, build trust with regulators, and deliver safe products to consumers.
Investing in CAPA is not just a regulatory requirement. it is a step toward achieving excellence in quality management.
References
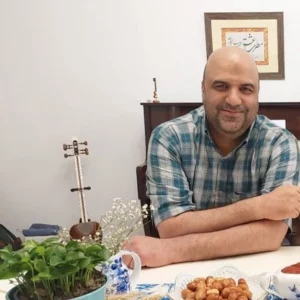
Ershad Moradi
Ershad Moradi, a Content Marketing Specialist at Zamann Pharma Support, brings 6 years of experience in the pharmaceutical industry. Specializing in pharmaceutical and medical technologies, Ershad is currently focused on expanding his knowledge in marketing and improving communication in the field. Outside of work, Ershad enjoys reading and attending industry related networks to stay up-to-date on the latest advancements. With a passion for continuous learning and growth, Ershad is always looking for new opportunities to enhance his skills and contribute to pharmaceutical industry. Connect with Ershad on Facebook for more information.
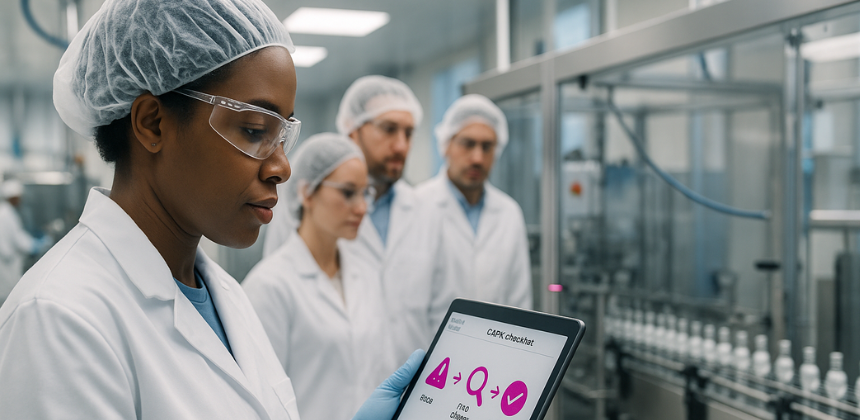
What Is a CAPA Plan? A Beginner’s Guide
This beginner’s guide explains CAPA plans in plain language. You’ll define problems clearly, analyze root causes with proven tools, and turn findings into targeted corrective and preventive actions. Then, you’ll verify effectiveness with metrics and close confidently.

Computerized Maintenance Management: The Complete 2025 Guide
This guide explores computerized maintenance management with practical strategies, CMMS comparisons, and implementation tips. Designed for professionals, entrepreneurs, and job seekers, it helps you choose the right tools, optimize workflows, and boost ROI with preventive and predictive maintenance methods.
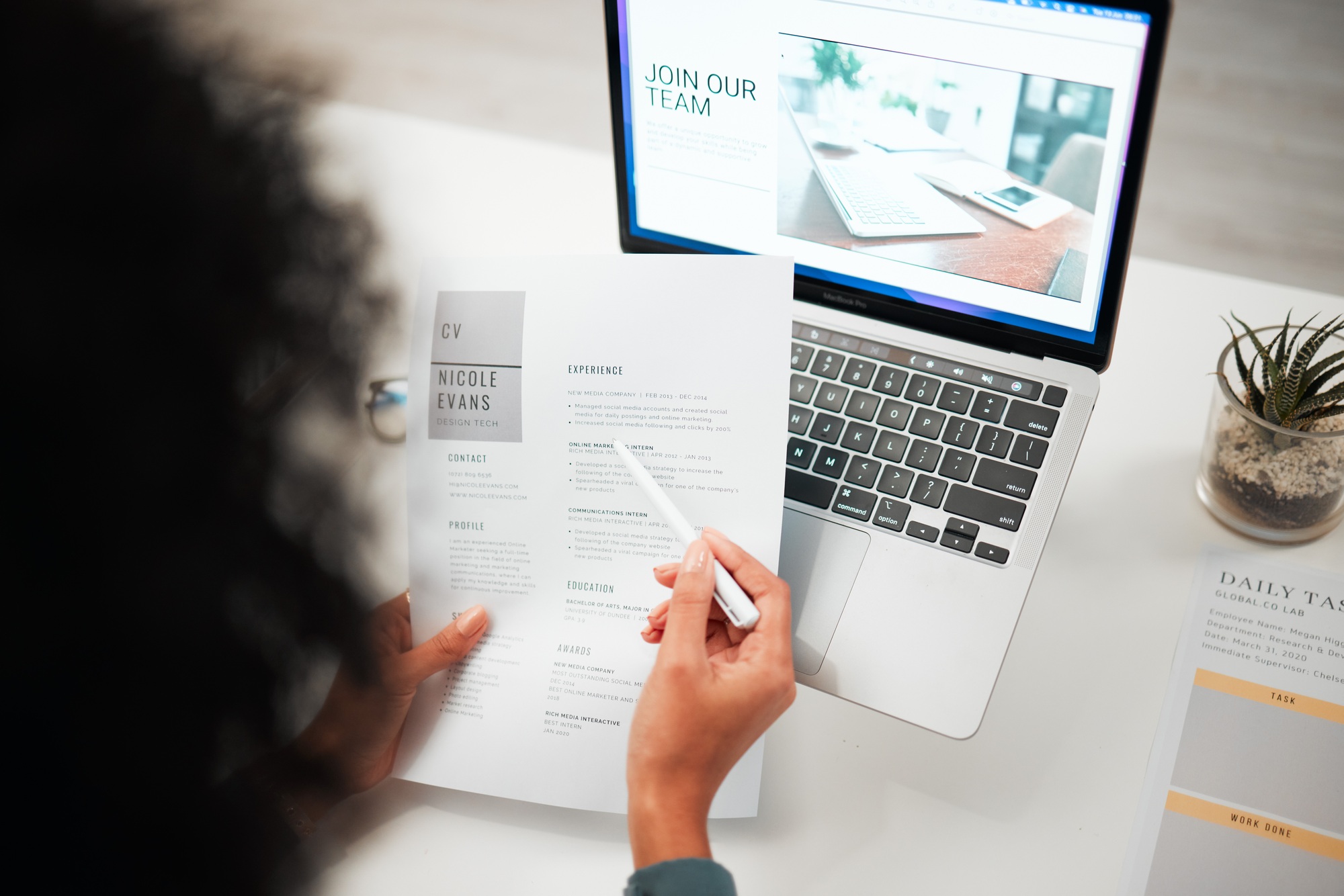
How to Choose the Right Special Skills for Resume Success
Learn how to choose, organize, and present special skills for resume success. This guide includes technical and soft skills, comparison tables, and AI-friendly strategies to pass ATS filters and stand out in competitive job markets.