Good Manufacturing Practice (GMP) regulations are critical for ensuring quality and safety in manufacturing. These regulations provide clear guidelines that companies follow to produce reliable products. GMP covers every stage of production, from sourcing raw materials to packaging finished goods. By adhering to these standards, manufacturers create products that consistently meet high-quality requirements. This commitment reduces risks such as contamination or defects, protecting both businesses and consumers. Additionally, GMP regulations help streamline processes, improving efficiency and minimizing waste. Companies that prioritize GMP compliance demonstrate their dedication to producing safe, dependable products.
This article explains how GMP regulations improve product quality and support manufacturing success. It highlights the benefits of adhering to GMP, such as reducing risks, building consumer trust, and ensuring consistent quality.
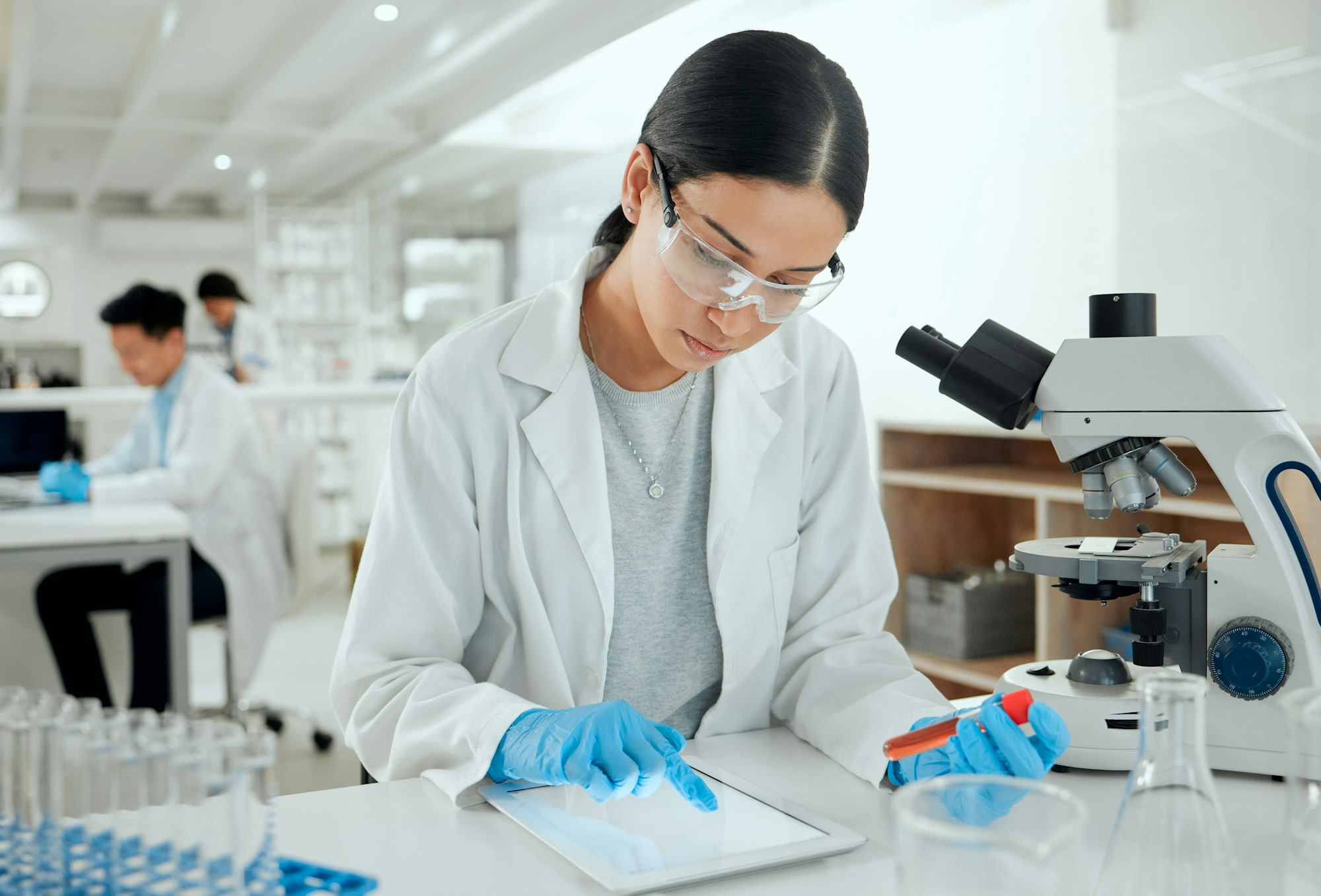
Why Are GMP Regulations Important for Product Quality?
GMP regulations provide a framework that helps manufacturers produce goods under strict standards, minimizing variations and ensuring consistency. This framework applies to every production stage, ensuring products meet quality requirements. When companies implement GMP regulations, they minimize the risks of contamination, defects, and recalls, which could otherwise harm consumers and damage the company’s reputation.
Implementing GMP regulations not only enhances product quality but also improves operational efficiency by reducing waste. For manufacturers, this means fewer disruptions, while consumers benefit from products they can trust.
Ultimately, GMP regulations help create a level of reliability that builds consumer confidence and aligns with regulatory requirements.
Sign up for Introduction to Good Manufacturing Practices (GMP) Free Course
Key Aspects of GMP Regulations
GMP regulations cover various elements essential for maintaining product quality and safety. Here’s an overview of some critical components of these regulations:
Companies must ensure that all staff members involved in production are fully trained and qualified for their roles, as their expertise directly impacts product quality and safety.
Maintaining a clean and sanitized facility is crucial for preventing contamination, and GMP regulations require that companies uphold high hygiene standards across production areas.
Regular calibration and maintenance of equipment help ensure it operates accurately and consistently, minimizing the risk of variability that could affect product quality.
Verifying the quality of raw materials before they enter production is vital; GMP standards require thorough testing to confirm materials meet specified criteria for safety and quality.
To minimize product variability, companies must implement standardized, controlled processes that consistently produce goods meeting predetermined quality standards.
Before distribution, products must undergo rigorous testing to detect any defects, ensuring they are safe and meet quality specifications.
Proper packaging is essential to protect products during handling, storage, and transport, and GMP regulations ensure packaging standards are met to maintain product integrity.
Effective tracking and control during distribution prevent mishandling and ensure that products reach consumers in their intended, safe form.
How Do GMP Regulations Reduce Manufacturing Variability?
Consistency Impact Product Quality
Consistency plays a vital role in achieving high product quality and ensuring customer satisfaction. Customers expect reliable products that meet the same standards every time they buy. By maintaining consistency, companies build trust and increase customer loyalty. Additionally, consistent quality reduces defects, saving companies time and money on replacements or repairs. Consistent products create a sense of reliability that strengthens a brand’s reputation, encouraging repeat purchases and positive reviews. Ultimately, consistency in quality is a cornerstone of a successful business, attracting and retaining satisfied customers.
GMP regulations provide essential support for maintaining this level of consistency. These guidelines cover every stage of production, from sourcing raw materials to packaging finished products. When companies follow GMP standards, they create a structured process that ensures each batch meets the same high standards.
This structure prevents variations that could lead to defects or safety issues. Moreover, consistent quality reduces the chance of consumer complaints and costly returns. GMP guidelines help manufacturers achieve dependable quality, building a solid reputation and boosting customer confidence in their products.
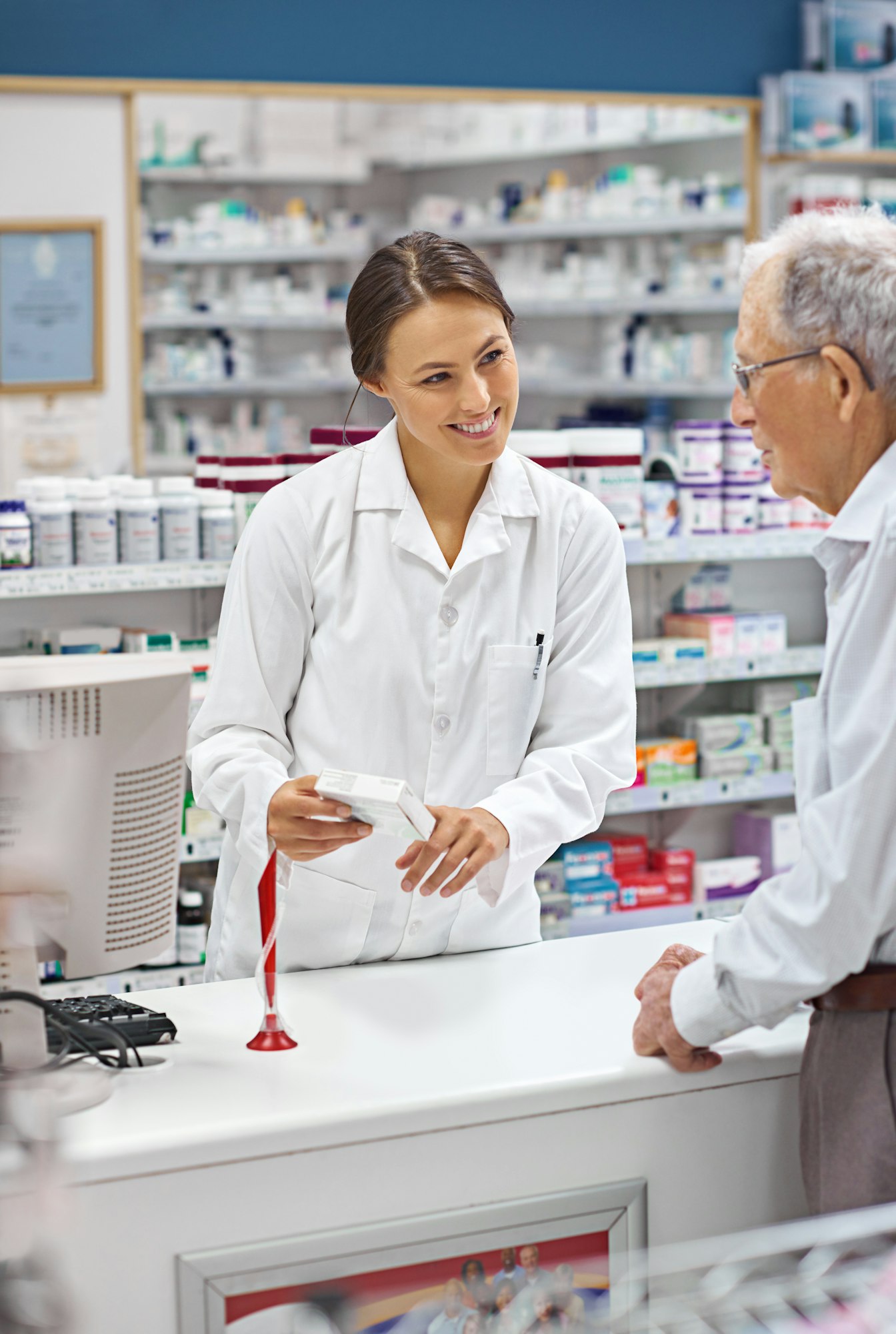
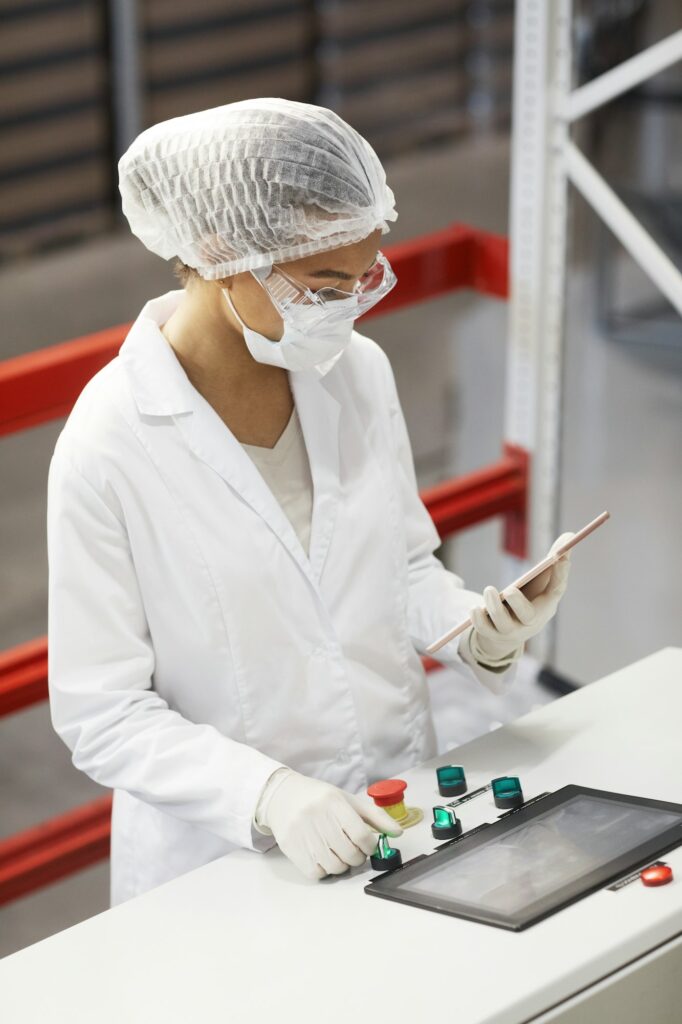
GMP Improve Traceability
Traceability is essential in GMP regulations because it allows full visibility in production. With detailed documentation, manufacturers track each step of the production process.
This record-keeping helps companies catch issues early and resolve them quickly. When companies address problems immediately, they protect the quality and safety of their products. Additionally, tracking every step builds a reliable foundation, enabling companies to understand the origins of any quality issue. As a result, companies maintain greater control over product quality, ensuring they meet customer expectations consistently.
Moreover, strong traceability supports effective recall procedures if necessary. When companies need to recall a product, traceability helps them identify affected batches accurately. This precision allows companies to recall only specific products rather than the entire line. By managing recalls efficiently, companies can limit customer inconvenience and uphold brand reputation.
Efficient recall procedures also demonstrate a commitment to consumer safety, which builds trust in the brand. Overall, GMP regulations’ emphasis on traceability helps companies protect consumers and maintain a positive image.
What Checklist Ensures Quality Control in GMP Compliance?
Conduct Regular Audits
Performing frequent internal and external audits of the production facility and processes allows companies to identify potential areas for improvement and ensure compliance with GMP standards at all times.
Implement Training Programs
Consistently providing employees with regular and updated training sessions ensures they stay knowledgeable about the latest GMP requirements, reinforcing proper procedures and reducing the likelihood of human errors in production.
Maintain Clean Facilities
Routine and thorough cleaning of production facilities significantly reduces the risk of contamination, which is crucial for meeting GMP hygiene standards and safeguarding product safety.
Calibrate Equipment Periodically
Regularly calibrating and maintaining production equipment helps ensure it functions accurately and reliably, reducing the chances of variability that could impact product quality.
Document Every Step
Keeping meticulous and accurate records of each stage in the production process is essential for traceability and accountability, enabling quick response and troubleshooting if any quality issues arise.
Verify Raw Materials
Testing and verifying the quality of raw materials upon receipt ensures that only compliant, high-quality ingredients and components enter the production process, supporting consistent end-product quality.
Enforce Process Consistency
Standardizing and strictly following production procedures help minimize variability, ensuring that each batch of products meets the same quality standards set by GMP regulations.
Influence Consumer Confidence
Ensure Product Safety
GMP regulations guide companies to consistently create safe products by enforcing strict standards at every stage of production. From sourcing raw materials to final packaging, these comprehensive guidelines ensure both safety and quality are maintained. Furthermore, when companies diligently follow GMP regulations, they control each step to prevent errors, contamination, or inconsistencies. As a result, this meticulous attention to detail significantly reduces the chances of unsafe products reaching consumers. Additionally, with every batch meeting the same rigorous standards, GMP regulations establish a reliable and repeatable process that fosters safe and consistent production.
Moreover, by prioritizing safety and quality, GMP regulations play a vital role in building consumer trust in a brand. When consumers know a company adheres to strict GMP guidelines, they feel more confident and assured about their purchases. This enhanced confidence naturally leads to stronger brand loyalty, as customers trust that the products consistently meet essential health and safety standards. Additionally, the emphasis on consistent quality and safety demonstrates to consumers that the brand genuinely values their well-being.
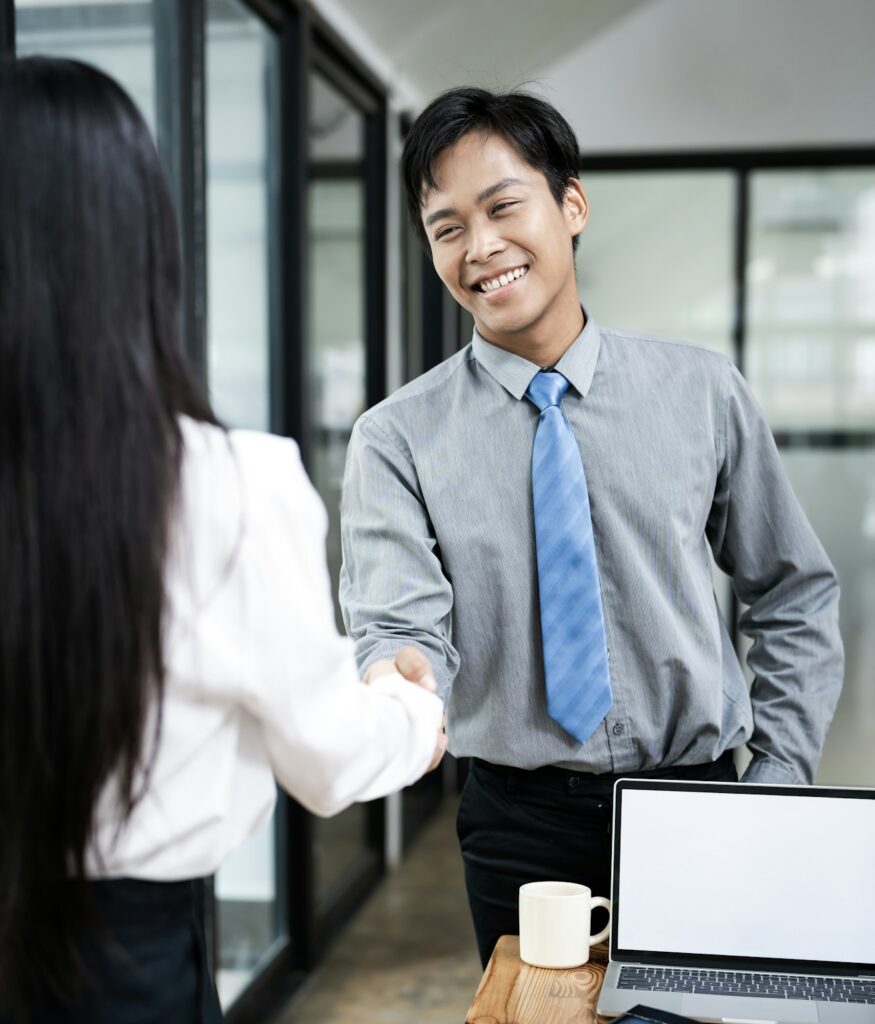
How Does Compliance with GMP Build Trust?
Compliance with GMP regulations shows that a company values industry standards and quality. By meeting these guidelines, companies demonstrate their commitment to producing safe, reliable products. This dedication reassures consumers that each product has passed strict quality checks.
When companies follow GMP regulations, they establish a solid reputation for quality and integrity. As a result, customers feel more confident in choosing their products, knowing they prioritize safety and consistency.
Moreover, GMP compliance positively influences consumers’ trust in a brand. When people see a company committed to GMP standards, they view it as reliable and responsible. This trust encourages customers to choose the brand over others, building loyalty and repeat purchases. Additionally, consistent adherence to GMP standards strengthens a company’s image, making it a preferred choice for quality-conscious buyers. Overall, by complying with GMP regulations, companies not only meet industry requirements but also gain lasting consumer confidence.
How Does Cost Impact GMP Compliance?
Implementing GMP regulations requires companies to invest in several areas, such as training and equipment maintenance. Regular employee training helps ensure everyone understands GMP standards, which reduces errors. Equipment maintenance, another essential cost, keeps machines running accurately and efficiently. Additionally, companies need to test raw materials to guarantee high-quality inputs. While these costs may seem high, they protect the company from greater expenses caused by recalls or quality issues. By prioritizing these investments, companies establish a strong foundation for reliable production.
Though initial costs can feel burdensome, they offer lasting benefits for product quality. Spending on GMP compliance safeguards the company’s reputation by delivering consistent, safe products. This commitment to quality earns consumers’ trust, leading to customer loyalty and repeat purchases. Moreover, companies avoid costly mistakes and inefficiencies when they maintain high GMP standards. In the long run, these investments lower risks and increase overall operational efficiency. Therefore, while GMP compliance requires upfront spending, it builds value that pays off over time.
Benefits of Following GMP Regulations
GMP regulations bring a variety of benefits, from enhancing product quality to improving brand reputation. Here are some of the top advantages for both manufacturers and consumers:
Reduces Product Recalls
Prevents costly recalls and consumer mistrust.
Enhances Process Efficiency
Streamlined processes minimize delays and waste.
Builds Brand Reputation
Consistent quality fosters a positive brand image.
Increases Regulatory Approval
Simplifies the process of obtaining regulatory approvals.
Minimizes Contamination Risks
Strict hygiene reduces contamination chances.
Supports Market Expansion
Compliance allows access to global markets.
Improves Employee Morale
Structured practices make roles clearer for staff.
Conclusion
GMP regulations play a crucial role in ensuring product quality and safety across industries. By following these guidelines, companies minimize risks like contamination, defects, and recalls. GMP practices ensure that products consistently meet high standards, from raw materials to final packaging. This consistency not only enhances quality but also reassures consumers, showing that the brand values their health and satisfaction. Ultimately, GMP compliance supports regulatory standards while protecting both companies and their customers from potential issues.
Moreover, adhering to GMP regulations builds consumer trust, which strengthens brand loyalty over time. When customers know a company is committed to quality, they feel confident choosing its products again and again. Although GMP compliance requires effort and investment, the benefits outweigh the costs in the long run. Companies that embrace GMP practices create a reliable reputation, reducing operational risks and fostering long-term success. In today’s competitive market, committing to GMP standards reflects a dedication to excellence that resonates with customers and builds lasting value.
References
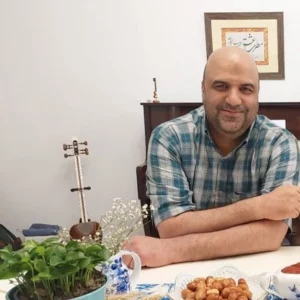
Ershad Moradi
Ershad Moradi, a Content Marketing Specialist at Zamann Pharma Support, brings 6 years of experience in the pharmaceutical industry. Specializing in pharmaceutical and medical technologies, Ershad is currently focused on expanding his knowledge in marketing and improving communication in the field. Outside of work, Ershad enjoys reading and attending industry related networks to stay up-to-date on the latest advancements. With a passion for continuous learning and growth, Ershad is always looking for new opportunities to enhance his skills and contribute to pharmaceutical industry. Connect with Ershad on Facebook for more information.
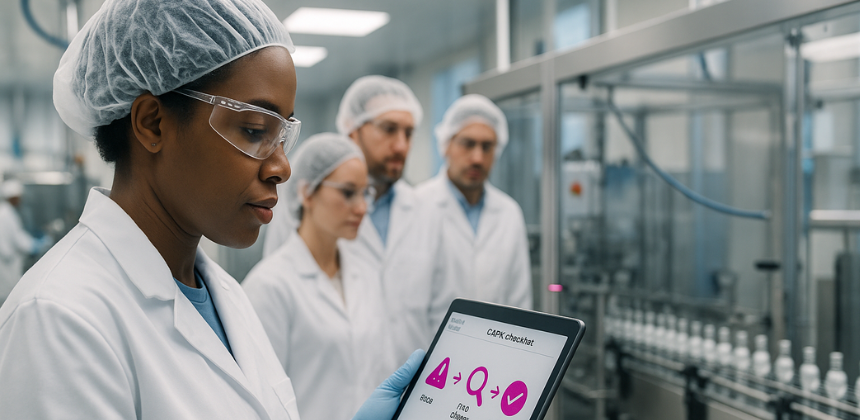
What Is a CAPA Plan? A Beginner’s Guide
This beginner’s guide explains CAPA plans in plain language. You’ll define problems clearly, analyze root causes with proven tools, and turn findings into targeted corrective and preventive actions. Then, you’ll verify effectiveness with metrics and close confidently.

Computerized Maintenance Management: The Complete 2025 Guide
This guide explores computerized maintenance management with practical strategies, CMMS comparisons, and implementation tips. Designed for professionals, entrepreneurs, and job seekers, it helps you choose the right tools, optimize workflows, and boost ROI with preventive and predictive maintenance methods.
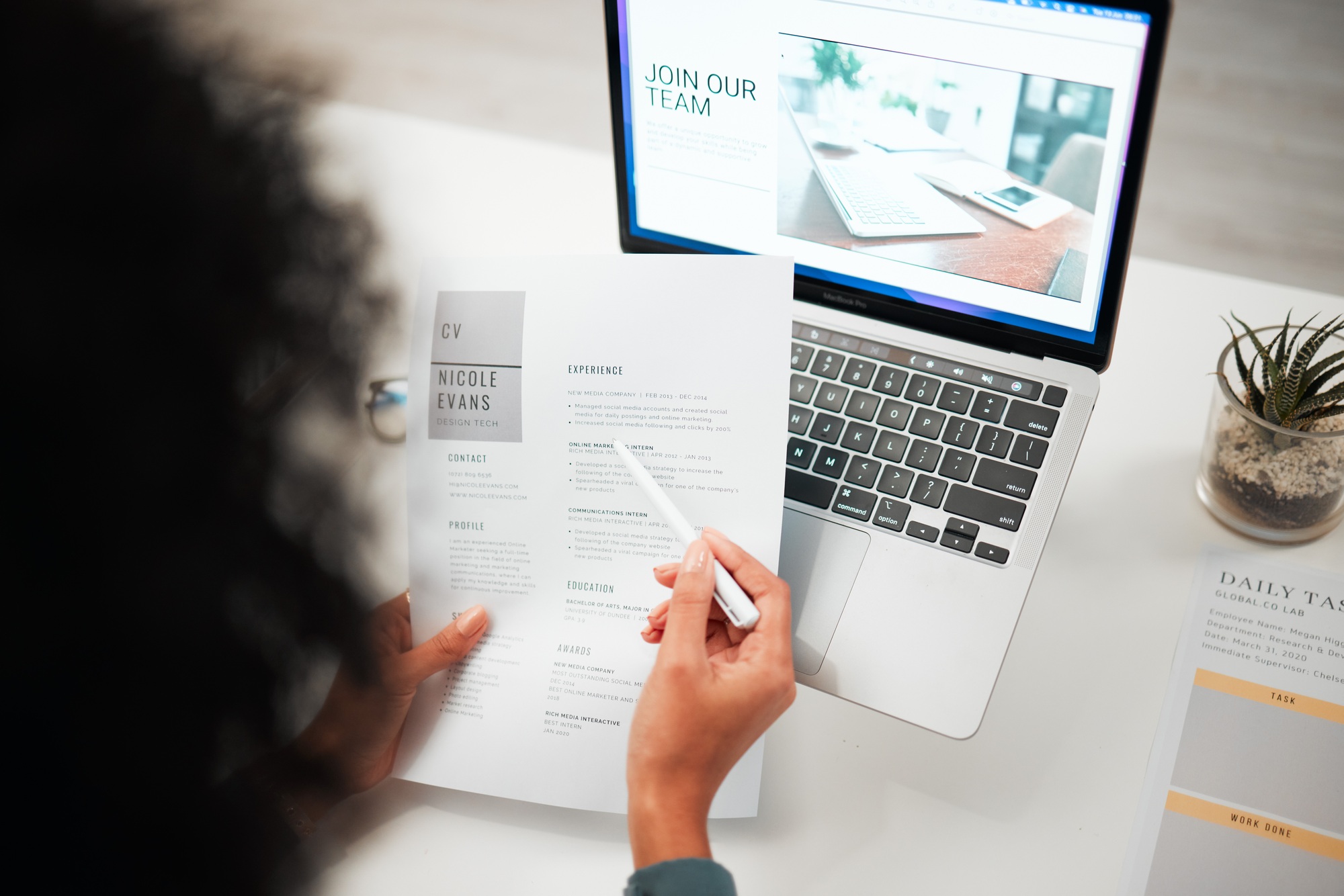
How to Choose the Right Special Skills for Resume Success
Learn how to choose, organize, and present special skills for resume success. This guide includes technical and soft skills, comparison tables, and AI-friendly strategies to pass ATS filters and stand out in competitive job markets.