The role of Corrective and Preventive Actions (CAPA) within Good Manufacturing Practices (GMP) is instrumental in maintaining high-quality standards. CAPA addresses the root causes of deviations and quality issues, ensuring product safety and regulatory compliance. By measuring the impact of CAPA, organizations can assess the effectiveness of their quality processes, making data-driven improvements. CAPA fosters a proactive approach to quality management, enhancing consistency and reducing risks.
This article explores how to measure CAPA’s impact on GMP, focusing on essential metrics, analysis methods, and strategies to maximize CAPA’s effectiveness in various areas of GMP compliance.
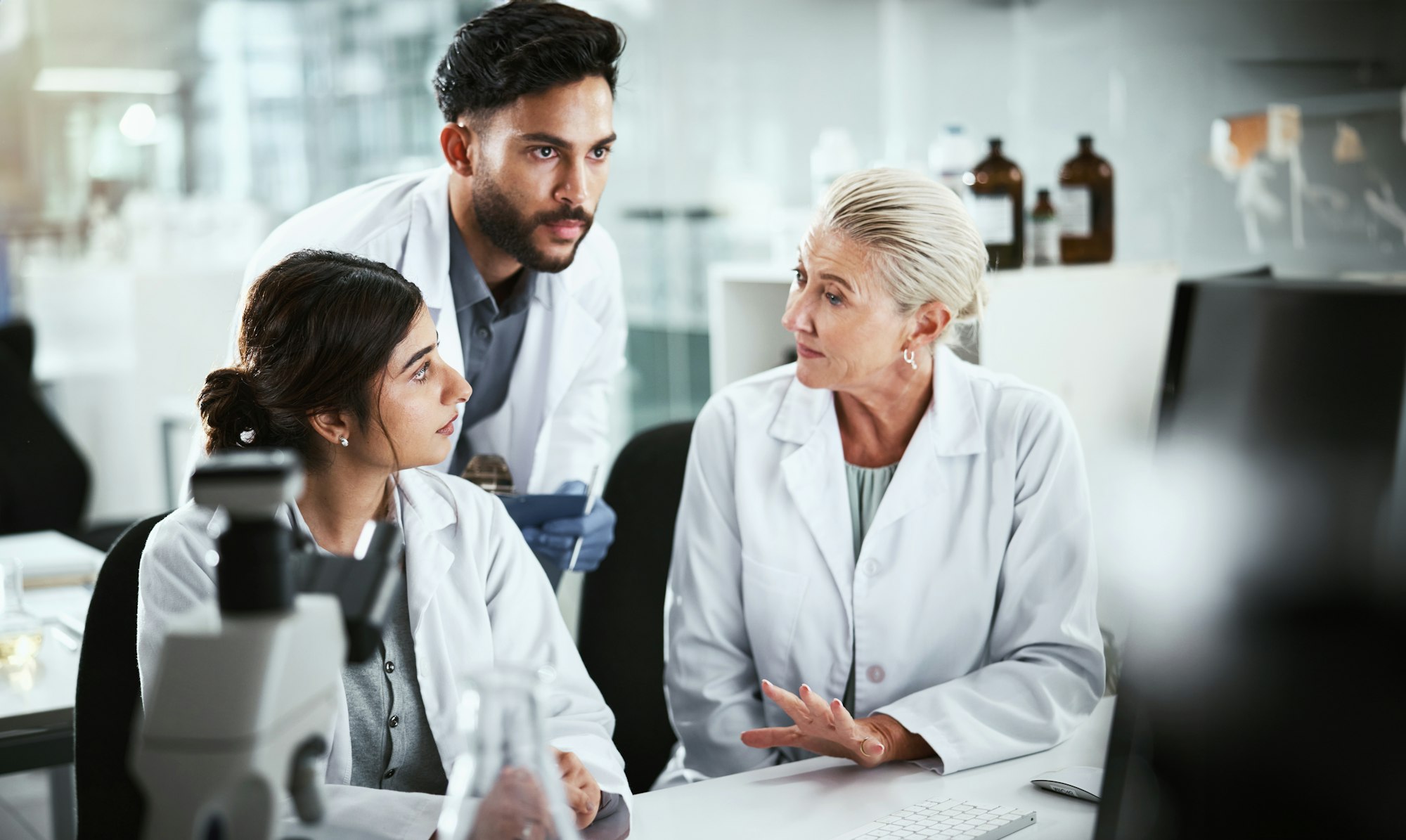
Quality Performance and the Impact of CAPA on Operations
Implementing CAPA significantly influences quality performance by addressing and eliminating root causes of quality issues. CAPA actions improve processes, optimize workflows, and ensure regulatory compliance across departments. Understanding the impact of CAPA on operations helps organizations make informed decisions and continuously refine quality processes. CAPA’s influence on quality performance spans various GMP functions, including production, quality control, and supply chain. By measuring CAPA’s effectiveness, organizations gain insights into areas needing improvement and ensure long-term product consistency and quality.
Organizations leverage CAPA to strengthen quality processes, reduce deviations, and create a culture focused on continuous improvement. CAPA implementation fosters interdepartmental collaboration, helping to identify problem areas, streamline workflows, and achieve sustainable compliance.
CAPA impact metrics enable quality teams to assess the efficacy of corrective actions, prevent recurrence, and minimize risks. With consistent monitoring, companies can enhance CAPA effectiveness, build resilience, and better respond to evolving regulatory demands, which ultimately strengthens the entire quality management system.
Sign up for GMP Corrective and Preventive Actions (CAPA) Management Course
Metrics to Measure the Impact of CAPA
To understand CAPA’s effectiveness, organizations must track specific metrics that reveal its impact on quality and compliance. Here are key CAPA metrics to consider:
Measures how quickly CAPA actions close, indicating process efficiency.
Assesses the reduction in repeated deviations, showing CAPA’s preventive effect.
Tracks the identification accuracy of root causes, impacting CAPA relevance.
Evaluates how CAPA aligns with GMP guidelines and standards.
Monitors the effectiveness of preventive measures, highlighting CAPA’s proactive impact.
Analyzing the Impact of CAPA on Deviation Reduction
CAPA Effect on Recurring Deviations
Reducing recurring deviations remains a core objective of CAPA. CAPA processes work by identifying the root causes of issues and implementing solutions that prevent them from happening again. Through targeted corrective actions, CAPA stops recurring problems, which ultimately enhances consistency across operations. This process reduces the frequency of repeated issues and strengthens overall stability, keeping workflows on track. As CAPA addresses and resolves these deviations, companies experience fewer disruptions in their processes, resulting in smoother production cycles.
Moreover, CAPA’s impact on reducing deviations supports continuous improvement. Each time CAPA addresses a deviation, it also improves the organization’s understanding of potential problem areas. With this insight, teams can proactively identify and correct similar issues before they escalate. Over time, CAPA creates a ripple effect, lowering deviation rates and fostering a proactive quality culture.
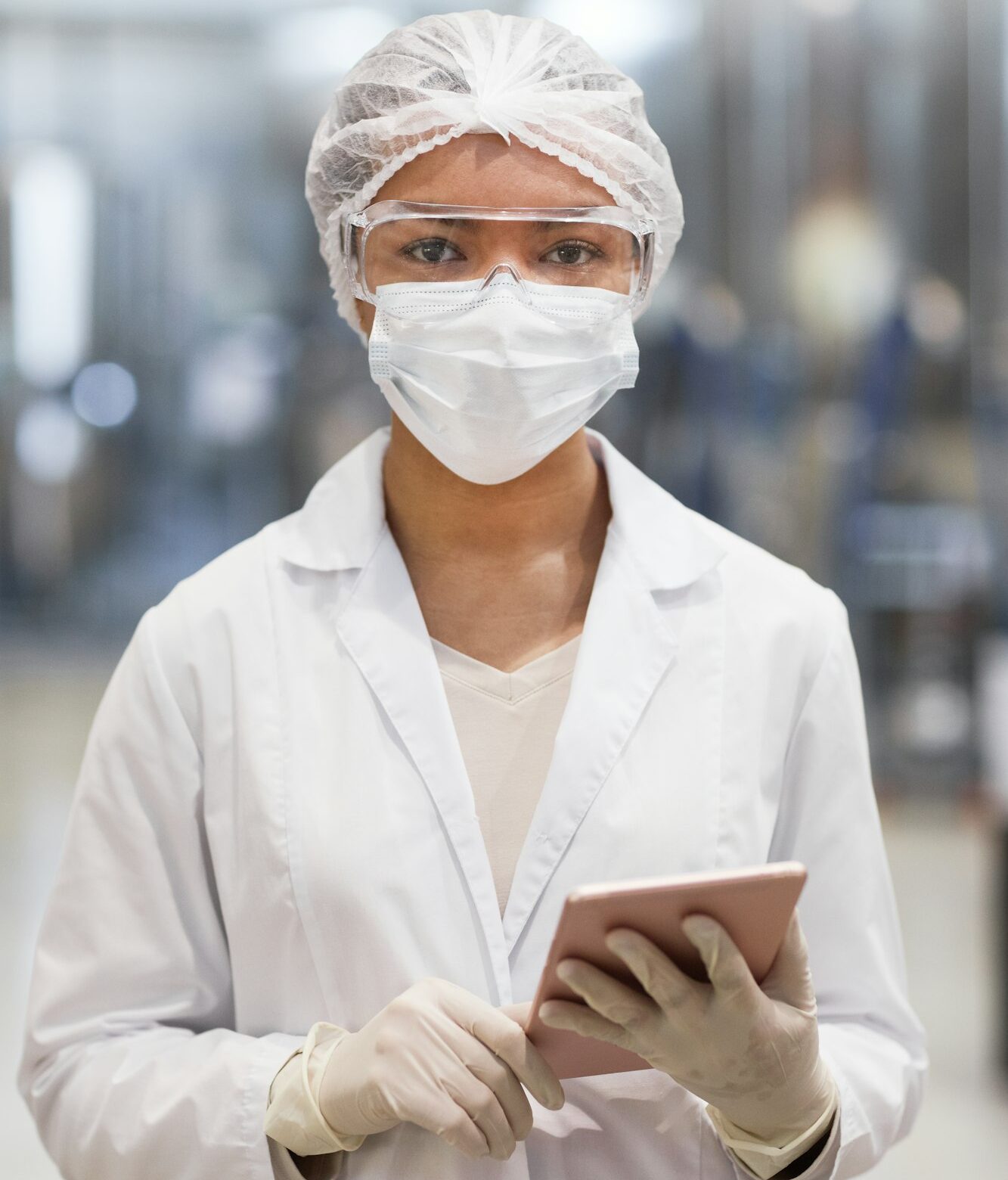
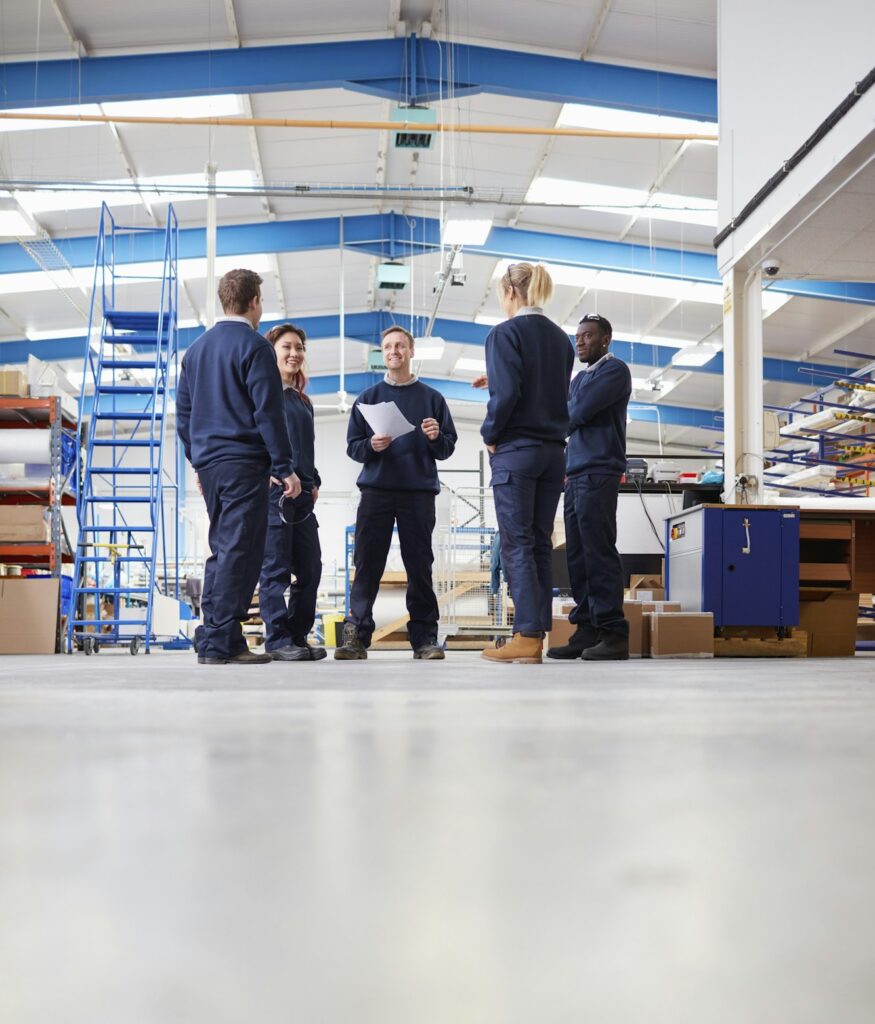
CAPA’s Role in Optimizing Process Efficiency
CAPA’s focus on process efficiency delivers long-term benefits by embedding continuous improvement into daily operations. Each corrective action taken through CAPA doesn’t just address an immediate issue; it also strengthens the overall system by preventing similar problems from arising.
This proactive approach helps teams anticipate potential bottlenecks before they impact production, creating a smoother, more predictable workflow. As CAPA continues to improve processes, teams can concentrate on achieving higher-quality outputs rather than constantly troubleshooting recurring issues.
Additionally, CAPA’s role in optimizing process efficiency extends to improved resource planning and allocation. With a reliable system in place, teams can better manage time, equipment, and personnel, leading to consistent productivity gains.
CAPA helps reduce unexpected downtime, allowing teams to hit production targets and meet delivery timelines without compromise.
Compliance Improvements Driven by the Impact of CAPA
Improved Documentation Consistency
Consistent documentation practices reduce errors and ease audit readiness.
Focused Employee Training
CAPA-driven training builds staff knowledge and helps prevent common mistakes.
Streamlined Audit Processes
Alignment with GMP standards through CAPA simplifies and accelerates the audit process.
Increased Risk Awareness
Risk identification and mitigation efforts safeguard patient health and safety.
Strengthened Quality Mindset
A commitment to quality instilled by CAPA fosters proactive adherence to standards.
CAPA’s Impact Across GMP Functions
CAPA Influence on Production Quality
CAPA significantly enhances production quality by targeting errors and equipment issues that affect consistency. In production, CAPA identifies problem areas and applies corrective actions to resolve them quickly. This proactive approach ensures reliable processes and consistent product quality. By addressing specific production issues, CAPA helps prevent disruptions that could compromise product standards. With these corrective actions in place, production flows more smoothly, maintaining steady output and quality throughout operations.
Additionally, CAPA’s preventive measures further support production quality by reducing downtime and delays. When CAPA identifies potential risks, it implements preventive actions that keep equipment functioning optimally. This minimizes unexpected breakdowns, allowing production teams to maintain continuous workflows. CAPA’s influence on production also includes enhancing overall product integrity, ensuring each product meets high-quality standards. Over time, CAPA creates a stable production environment that fosters long-term compliance with GMP requirements. Through these efforts, CAPA supports efficient production while protecting product quality at every stage.

CAPA’s Role in Quality Assurance (QA)
CAPA plays an essential role in Quality Assurance (QA) by identifying gaps in procedures that impact product quality. In QA processes, CAPA pinpoints issues in testing and validation protocols, enabling teams to address them quickly. By closing these gaps, CAPA ensures that testing procedures remain accurate and reliable. This proactive approach helps QA teams maintain consistency in results, which is crucial for meeting regulatory standards. As CAPA strengthens these testing protocols, it supports a higher level of quality control across all stages of production.
Furthermore, CAPA initiatives in QA reduce testing errors, allowing teams to uphold strict validation standards. CAPA-driven improvements enhance each step of the testing process, ensuring thorough and precise assessments. With fewer errors, QA teams release batches more confidently, knowing they meet quality requirements. CAPA also reinforces adherence to GMP guidelines by improving QA workflows and minimizing risks. Through its structured approach, CAPA helps QA teams maintain high standards, protect product integrity, and support regulatory compliance consistently.
CAPA’s Role in Proactive Risk Prevention
CAPA plays a vital role in proactive risk prevention by tackling quality issues early. By identifying problems before they escalate, CAPA helps teams prevent potential failures and minimize disruptions.
This proactive approach reduces overall risk, creating a safer production environment. Through preventive actions, CAPA protects patient safety, which remains a top priority in regulated industries. CAPA measures also support compliance by addressing risks that could lead to regulatory breaches.
In addition, CAPA impact assessments help organizations pinpoint high-risk areas, focusing resources where they matter most. By analyzing data from past issues, CAPA provides insights that guide decision-making. This approach allows companies to anticipate and avoid costly errors, optimizing their operations. With CAPA in place, teams can allocate resources strategically, focusing on areas with the highest risk potential. Over time, CAPA builds a robust quality framework that consistently safeguards against risks, supporting both regulatory goals and operational efficiency.
Maximizing the Impact of CAPA on GMP Compliance
Organizations can enhance CAPA’s impact by implementing strategic measures that improve process quality and reduce compliance risks. Here are some key strategies:
Cross-Functional Involvement
Ensures that all departments contribute to CAPA efforts, leading to more holistic solutions.
Comprehensive Root Cause Analysis
Uses tools like the 5 Whys to accurately identify and address root causes.
Frequent CAPA Audits
Conducts regular CAPA reviews to monitor effectiveness and address new issues.
Targeted Employee Training
Keeps staff informed about CAPA procedures, enhancing compliance.
Data-Driven CAPA Decisions
Leverages CAPA data to make continuous improvements and optimize quality processes.
Conclusion
Understanding and measuring the impact of CAPA in GMP environments is essential for sustaining compliance and achieving quality objectives. CAPA’s role spans quality improvement, risk management, and operational efficiency, supporting companies in meeting regulatory expectations and enhancing product safety. By focusing on key metrics, leveraging data, and implementing effective strategies, organizations can maximize CAPA’s impact and drive continuous improvement across GMP functions. CAPA ensures that companies maintain high-quality standards, foster a culture of excellence, and safeguard public health by producing safe and compliant products.
References
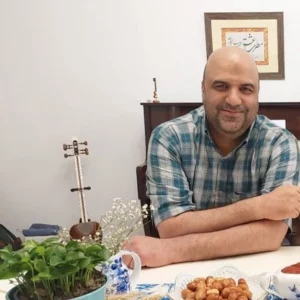
Ershad Moradi
Ershad Moradi, a Content Marketing Specialist at Zamann Pharma Support, brings 6 years of experience in the pharmaceutical industry. Specializing in pharmaceutical and medical technologies, Ershad is currently focused on expanding his knowledge in marketing and improving communication in the field. Outside of work, Ershad enjoys reading and attending industry related networks to stay up-to-date on the latest advancements. With a passion for continuous learning and growth, Ershad is always looking for new opportunities to enhance his skills and contribute to pharmaceutical industry. Connect with Ershad on Facebook for more information.
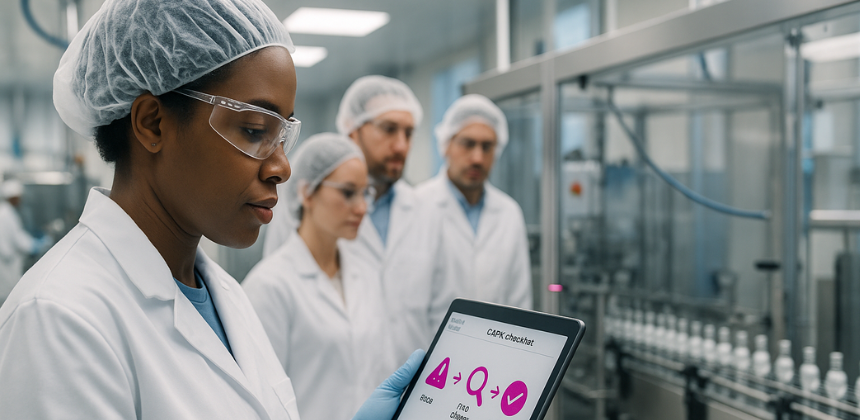
What Is a CAPA Plan? A Beginner’s Guide
This beginner’s guide explains CAPA plans in plain language. You’ll define problems clearly, analyze root causes with proven tools, and turn findings into targeted corrective and preventive actions. Then, you’ll verify effectiveness with metrics and close confidently.

Computerized Maintenance Management: The Complete 2025 Guide
This guide explores computerized maintenance management with practical strategies, CMMS comparisons, and implementation tips. Designed for professionals, entrepreneurs, and job seekers, it helps you choose the right tools, optimize workflows, and boost ROI with preventive and predictive maintenance methods.
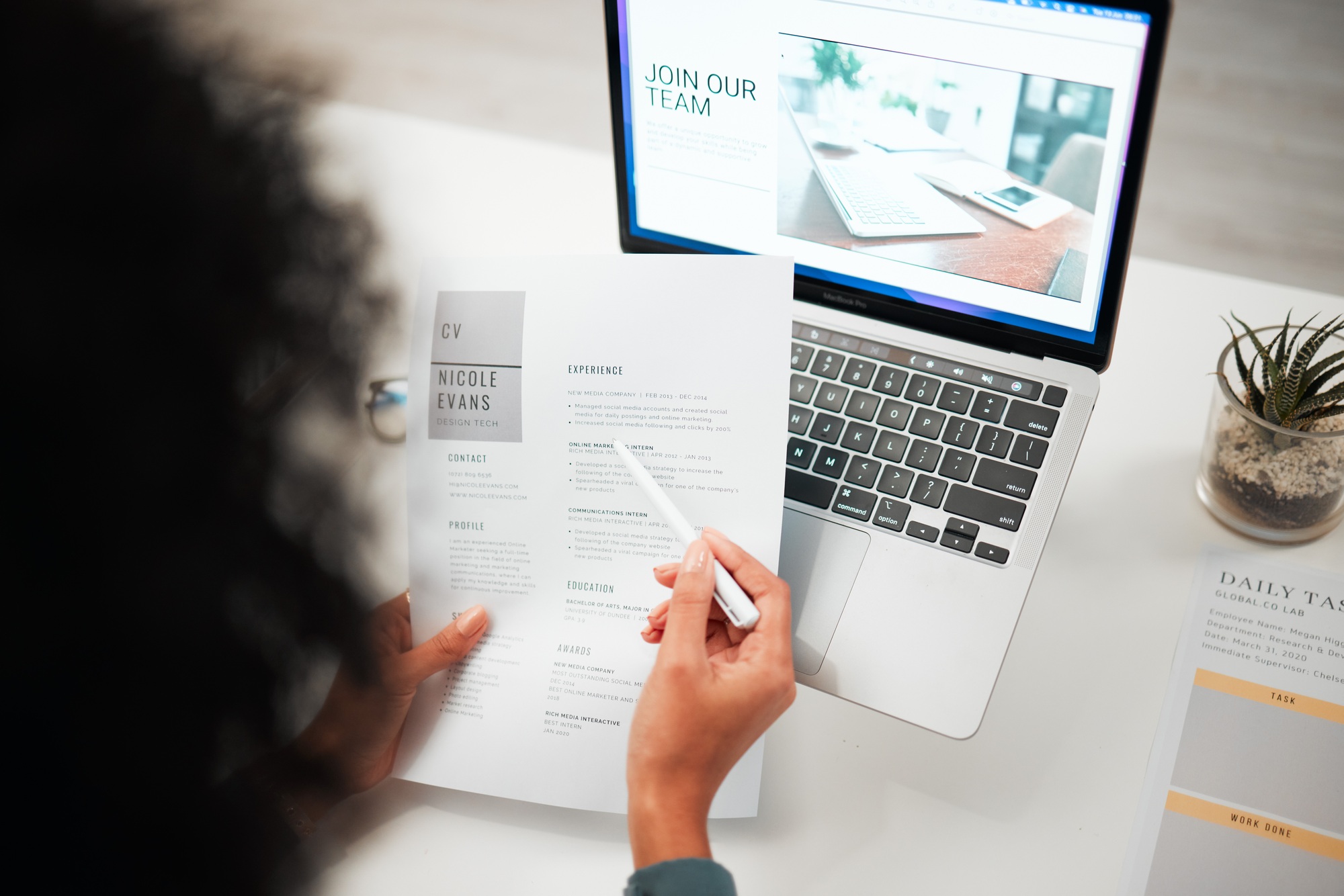
How to Choose the Right Special Skills for Resume Success
Learn how to choose, organize, and present special skills for resume success. This guide includes technical and soft skills, comparison tables, and AI-friendly strategies to pass ATS filters and stand out in competitive job markets.