In today’s competitive pharmaceutical landscape, ensuring consistency and quality in production is, therefore, crucial. Consequently, process validation plays a pivotal role in achieving this, where data-backed insights become essential for making informed decisions. Moreover, statistical tools are indispensable in this validation process. They empower quality assurance teams to effectively evaluate, monitor, and maintain product standards. With a wide range of statistical techniques, teams can uncover patterns, continuously monitor deviations, and readily identify areas for improvement.
In this article, we delve into the importance of statistical tools, specifically highlighting their use, benefits, and overall impact on process validation. By integrating these tools into operations, companies can streamline processes, significantly reduce errors, and ultimately build stronger confidence in product quality.
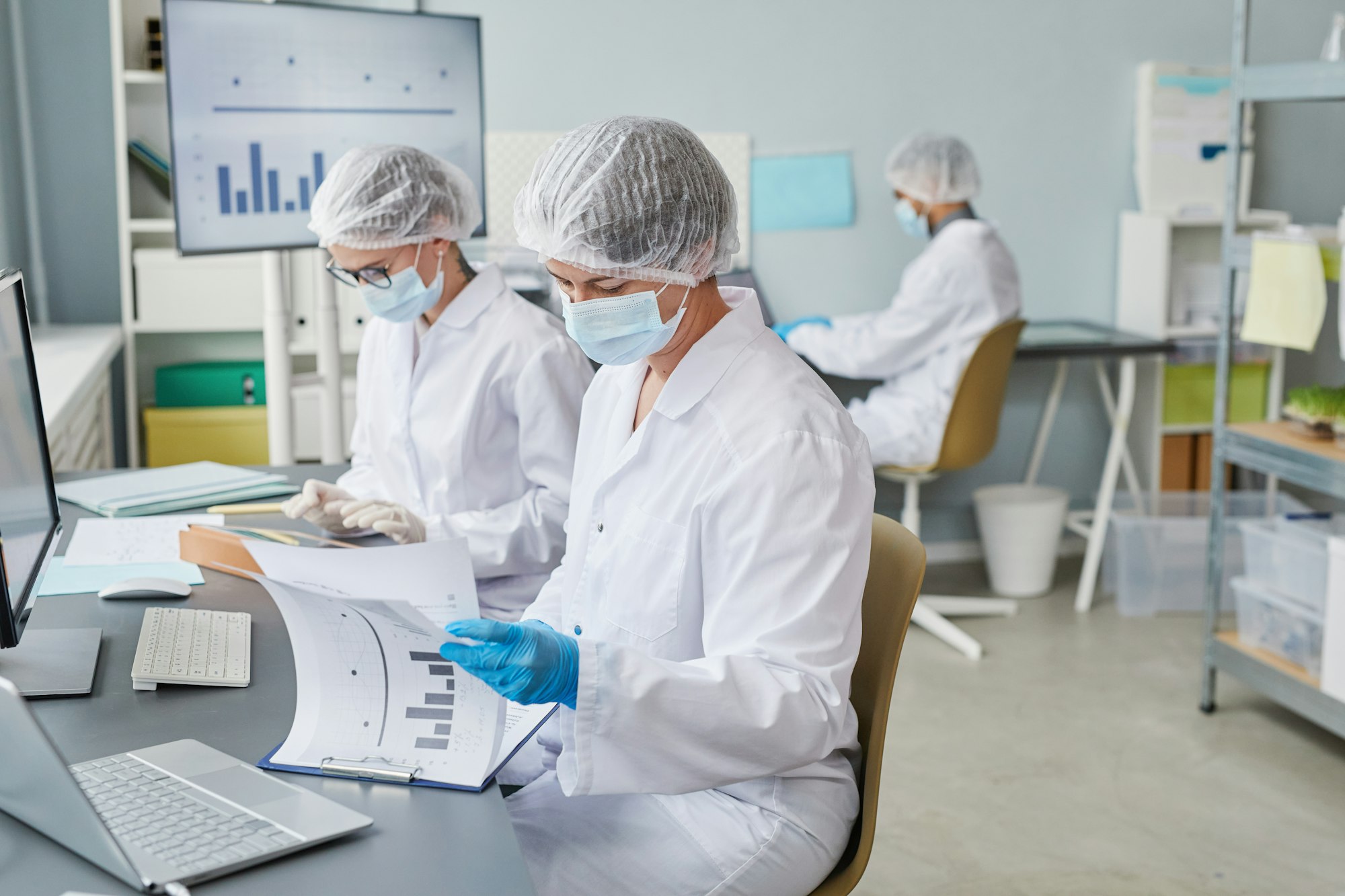
Role of Statistical Tools in Process Validation
Statistical tools play a vital role in process validation, providing insights beyond surface observations. These tools allow teams to monitor variations that may affect product quality and ensure consistency. By analyzing data, teams can detect irregularities early and maintain strict control over production quality. This proactive monitoring helps prevent potential issues before they impact the product. As a result, teams can uphold high standards and meet regulatory requirements, which builds confidence in the production process.
In process validation, statistical tools help teams identify the causes of variability. Teams use these tools to measure key process parameters and product attributes, tracking performance over time. This data allows them to make precise adjustments that keep production within acceptable quality ranges. These adjustments are essential to ensure that the final product consistently meets set standards. Statistical tools also support regulatory compliance by documenting quality measures across each stage.
Sign up for GMP Device Qualification Course
Key Statistical Tools in Process Validation
Control charts are valuable for tracking data over time, helping to identify trends and variations that could affect process stability. They enable teams to see if a process remains within control limits, making them essential for routine monitoring.
Capability analysis evaluates if a process can consistently produce within specification limits. By analyzing process capability indices, teams determine if adjustments are needed to meet quality standards.
A Pareto analysis helps prioritize issues by identifying the most common sources of variation. This analysis can guide efforts to correct the most significant factors affecting process quality.
Hypothesis testing determines whether observed variations in process data are statistically significant. This tool helps assess if differences between production batches are due to chance or actual process changes.
Regression analysis helps identify relationships between variables. By understanding these relationships, teams can make adjustments to maintain optimal process conditions and predict outcomes.
Design of Experiments (DoE) is a structured method for exploring the relationships between factors affecting a process and the output results. This tool is particularly useful during process development.
SPC uses statistical methods to monitor and control a process, ensuring that it operates at its maximum potential without compromising quality.
Applying Statistical Tools
The Importance of Control Charts in Process Validation
Control charts serve as a crucial tool for effectively monitoring and managing processes, especially in dynamic production environments. Notably, these charts display data over time, offering teams a clear view of performance consistency. By visually highlighting both normal and abnormal variations, control charts help quality teams quickly detect potential issues. This swift identification allows teams to take prompt, corrective action, which, in turn, protects product quality. Furthermore, control charts simplify the process of tracking trends, making it easier to understand any ongoing changes within the production line and anticipate future issues.
To use control charts effectively, teams must carefully select the right data points and set accurate control limits. Therefore, establishing well-defined upper and lower control limits is essential, as these mark acceptable performance boundaries. When data points fall outside these set limits, it clearly signals a process issue that demands immediate action. Regular use of control charts not only keeps processes stable but also ensures that teams maintain consistently high quality standards. By monitoring these charts routinely, teams can promptly identify and address deviations, ensuring that product quality remains reliably high.
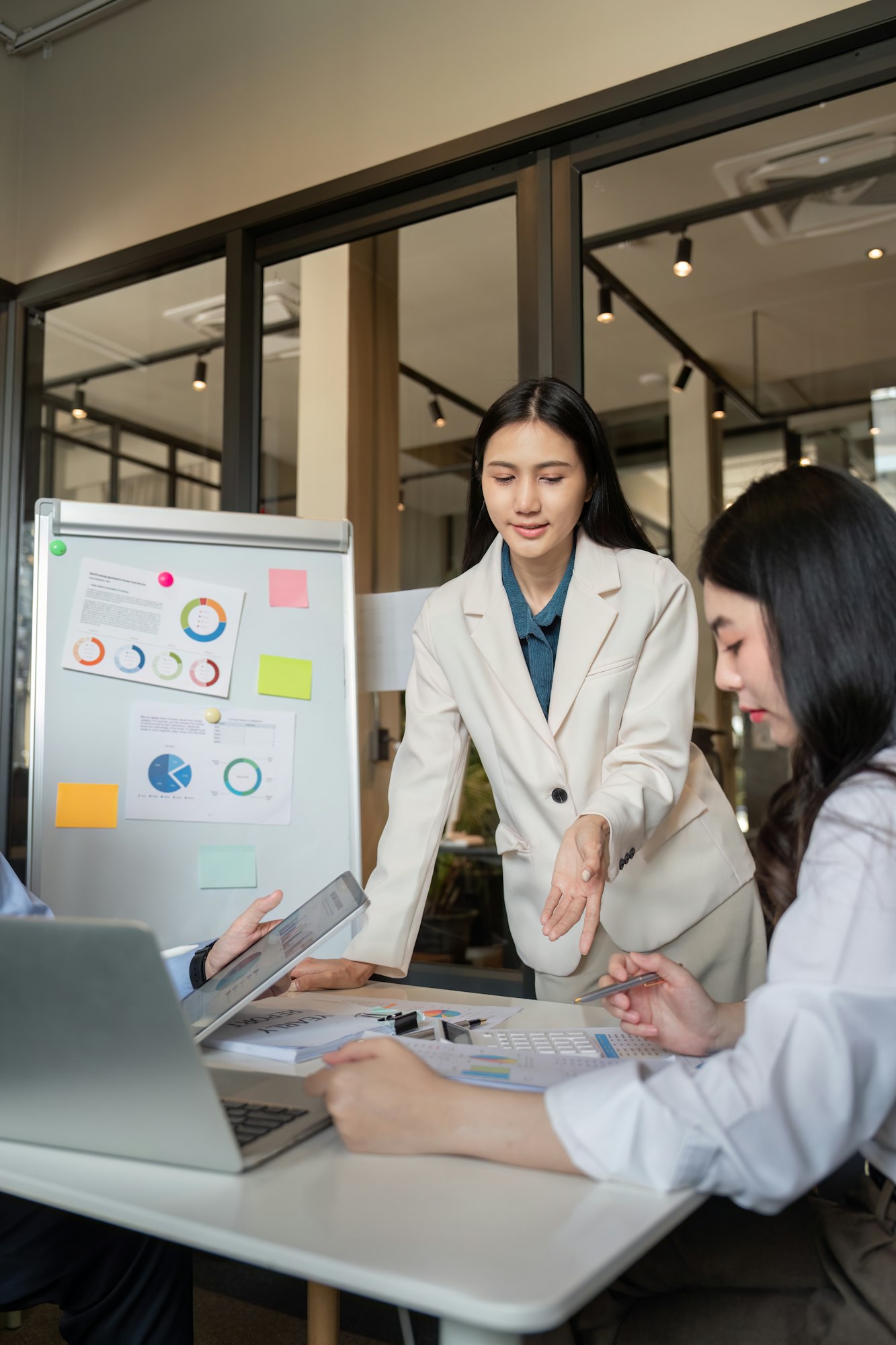
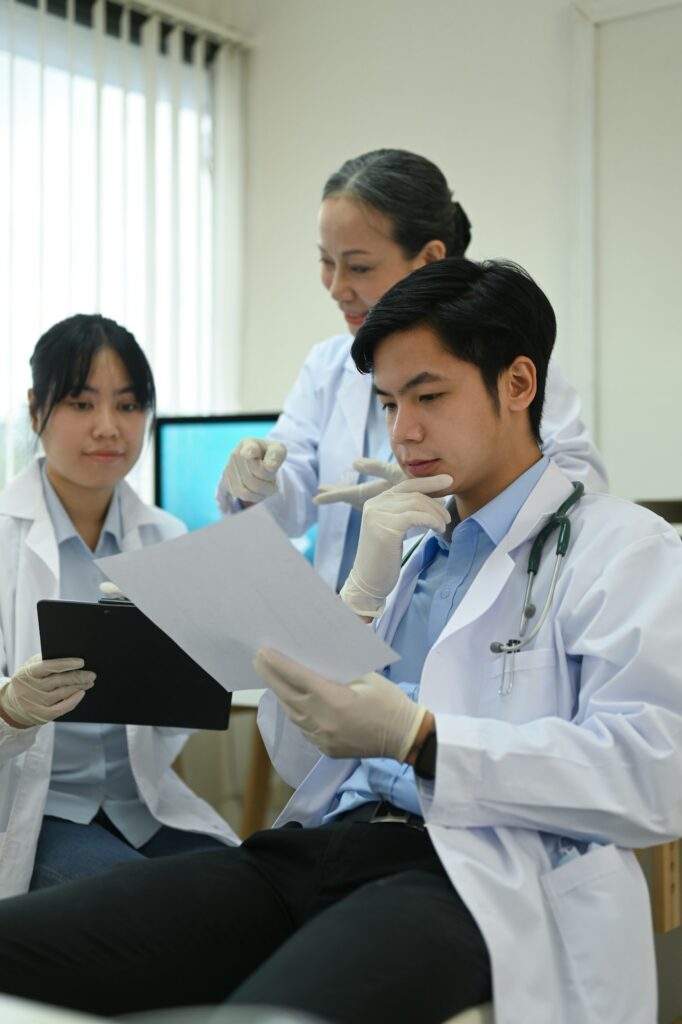
Capability Analysis as a Measure of Process Performance
Capability analysis provides a highly valuable approach for assessing processes during validation. Importantly, this statistical tool helps determine if a process can consistently produce within set specifications. By calculating capability indices, such as Cp and Cpk, quality teams gain crucial insights into how effectively a process performs. Moreover, these indices measure the process’s ability to consistently produce outputs that meet established quality standards. With this information at hand, teams can make well-informed decisions about potential adjustments needed to improve performance. Thus, capability analysis enables teams to identify whether a process requires specific adjustments to maintain the desired quality.
For a capability analysis to be effective, teams must collect data under normal operating conditions. This approach ensures that the data accurately represents the process’s usual performance. Additionally, by analyzing this data, teams can confirm whether the process remains within defined limits. When they detect deviations, they can promptly focus on making targeted improvements. Furthermore, capability analysis serves as a continuous quality control method, helping companies maintain consistency over time. It empowers organizations not only to meet quality benchmarks but also to strive for higher standards.
What are the benefits of statistical tools in process validation?
Improved Decision-Making
Statistical tools enhance decision-making by providing clear, data-driven insights. Teams can rely on facts rather than assumptions, ensuring that their decisions are both informed and effective.
Enhanced Process Efficiency
By identifying sources of variation early, statistical tools help streamline processes. Fewer disruptions mean faster production cycles and lower costs.
Consistency in Quality
With continuous monitoring, organizations can ensure that products consistently meet quality standards. This consistency builds consumer trust and supports regulatory compliance.
Cost Reduction
Identifying and addressing issues early reduces waste and rework costs. Preventative action based on statistical insights often leads to significant cost savings.
Strengthened Regulatory Compliance
Many industries, particularly pharmaceuticals, require strict documentation of quality processes. Statistical tools provide the necessary evidence, demonstrating that products meet regulatory standards.
Early Detection of Process Deviations
Tools like SPC and control charts help detect potential issues before they affect product quality. This proactive approach minimizes the risk of defects and recalls.
Implementing a Statistical Tools Framework: Steps for Success
Developing a SPC Strategy
Statistical Process Control (SPC) plays a vital role in process validation, as it provides a systematic approach to monitoring and controlling production quality. By using SPC, teams can maintain stability and reduce variability, which are crucial to ensuring consistent quality. To implement SPC effectively, teams must set precise control limits and monitor data regularly to stay ahead of potential issues. This consistent monitoring not only promotes stability but also gives teams the tools they need to catch deviations early.
A solid SPC strategy requires several key steps. First, teams should identify critical parameters that directly impact process performance. Next, they define control limits that set acceptable boundaries for each parameter. Finally, teams use control charts to track data and detect any variations outside these limits. Together, these actions create a structured way to manage quality, making SPC an indispensable tool in process validation. For successful SPC, however, teams need training in data interpretation and analysis, ensuring they can recognize and address deviations promptly. Understanding SPC data empowers teams to take corrective actions as needed, keeping processes on track.
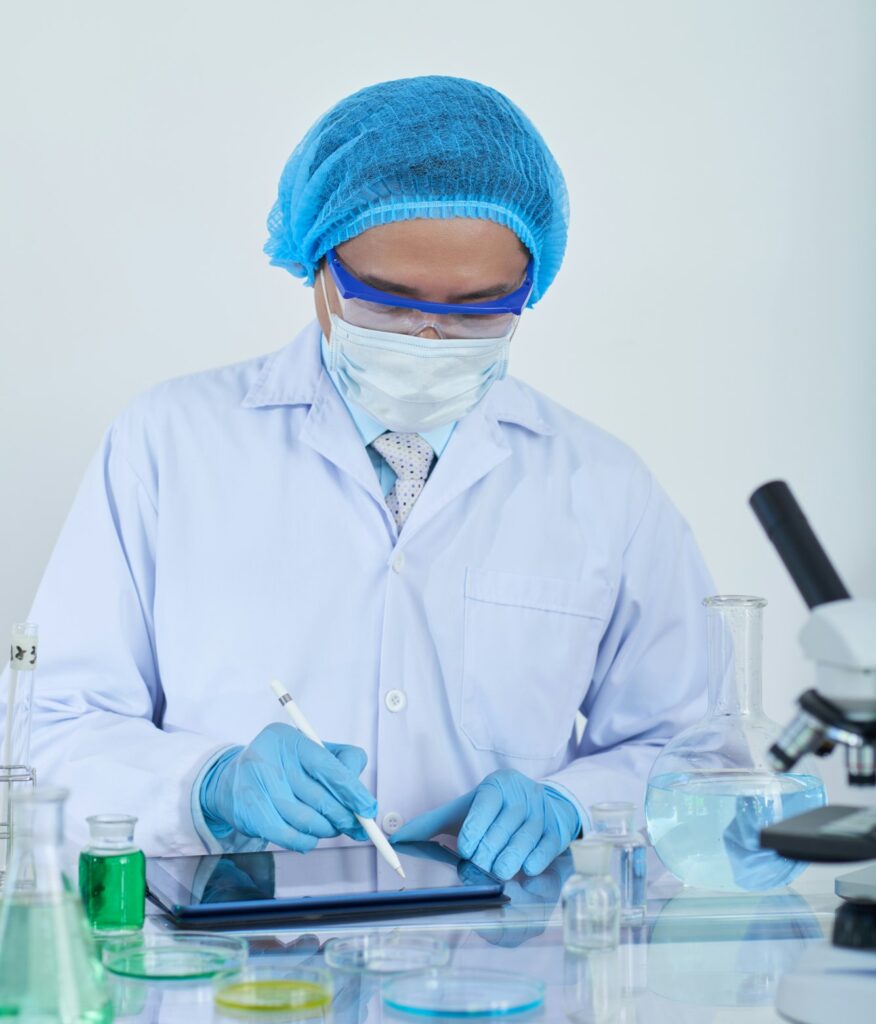
Incorporating Design of Experiments (DoE) into Validation
Design of Experiments (DoE) is an invaluable tool in process development, as it allows teams to explore various factor combinations and better understand their impact on outcomes. By testing different variables, teams can determine which operating conditions deliver the best results. Additionally, this method pinpoints specific factors that significantly influence product quality and overall process efficiency. With DoE, teams gain a deeper understanding of how different elements interact, leading to more informed, strategic decisions that ultimately enhance process performance.
To maximize the benefits of DoE, teams must first establish clear objectives and hypotheses. These goals provide essential direction, ensuring that each experiment produces meaningful and actionable results. Moreover, well-planned DoE studies enable teams to interpret findings accurately, helping them apply insights effectively. This structured approach empowers organizations to build a more resilient and predictable process. With the insights gained from DoE, companies can fine-tune operating conditions, improve process consistency, and uphold quality standards.
Continuous Improvement with Statistical Tools
Statistical tools play a crucial role in continuous quality improvement, far beyond one-time validation. Using tools like control charts and Statistical Process Control (SPC), organizations can encourage a mindset of ongoing enhancement. These tools help teams monitor data consistently, catching trends and variations that impact quality. With regular analysis, teams can make timely adjustments to maintain high standards. This proactive approach ensures that quality remains a focus at every stage of production.
To support continuous improvement, teams should make data analysis a regular practice. Reviewing process data frequently reveals areas for refinement and optimization. Teams can then use these insights to update production methods, leading to higher efficiency and fewer errors. This process builds a culture where quality comes first, empowering teams to take charge of improvement efforts. By prioritizing statistical tools, organizations not only maintain quality but also drive lasting positive change in their processes.
Practical Tips for Using Statistical Tools in Process Validation
Define Clear Objectives
Each statistical tool should be used with a specific goal in mind. Clearly defining objectives enhances the relevance of the data collected.
Use a Centralized Data Collection System
A centralized system allows teams to access all data in one place, facilitating analysis and ensuring data integrity.
Train Quality Teams on Data Interpretation
Statistical tools are only effective if teams understand how to interpret results. Regular training is essential.
Start with Small-Scale Validation Studies
Begin with pilot studies to understand process behavior before full-scale validation. Small studies reduce the risk of errors.
Regularly Review and Adjust Control Limits
As processes evolve, control limits may need adjustments. Regular reviews ensure they remain relevant to current production conditions.
Conclusion
Statistical tools are indispensable in process validation, providing a robust framework for ensuring quality, consistency, and regulatory compliance. By integrating tools like control charts, SPC, and DoE, organizations can monitor process variations, detect deviations early, and make informed adjustments. These tools support a culture of continuous improvement, where quality standards are consistently upheld. Adopting statistical tools empowers organizations to produce high-quality products, minimize costs, and maintain regulatory compliance effectively. The commitment to using these tools reflects a broader dedication to process excellence, setting companies apart in a competitive industry.
References
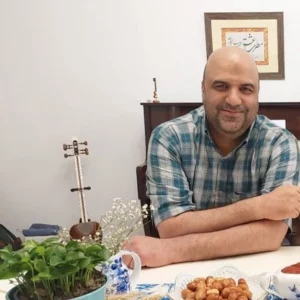
Ershad Moradi
Ershad Moradi, a Content Marketing Specialist at Zamann Pharma Support, brings 6 years of experience in the pharmaceutical industry. Specializing in pharmaceutical and medical technologies, Ershad is currently focused on expanding his knowledge in marketing and improving communication in the field. Outside of work, Ershad enjoys reading and attending industry related networks to stay up-to-date on the latest advancements. With a passion for continuous learning and growth, Ershad is always looking for new opportunities to enhance his skills and contribute to pharmaceutical industry. Connect with Ershad on Facebook for more information.
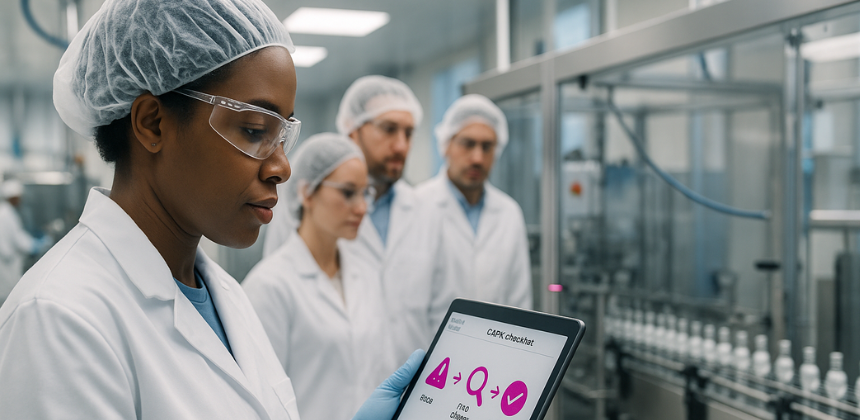
What Is a CAPA Plan? A Beginner’s Guide
This beginner’s guide explains CAPA plans in plain language. You’ll define problems clearly, analyze root causes with proven tools, and turn findings into targeted corrective and preventive actions. Then, you’ll verify effectiveness with metrics and close confidently.

Computerized Maintenance Management: The Complete 2025 Guide
This guide explores computerized maintenance management with practical strategies, CMMS comparisons, and implementation tips. Designed for professionals, entrepreneurs, and job seekers, it helps you choose the right tools, optimize workflows, and boost ROI with preventive and predictive maintenance methods.
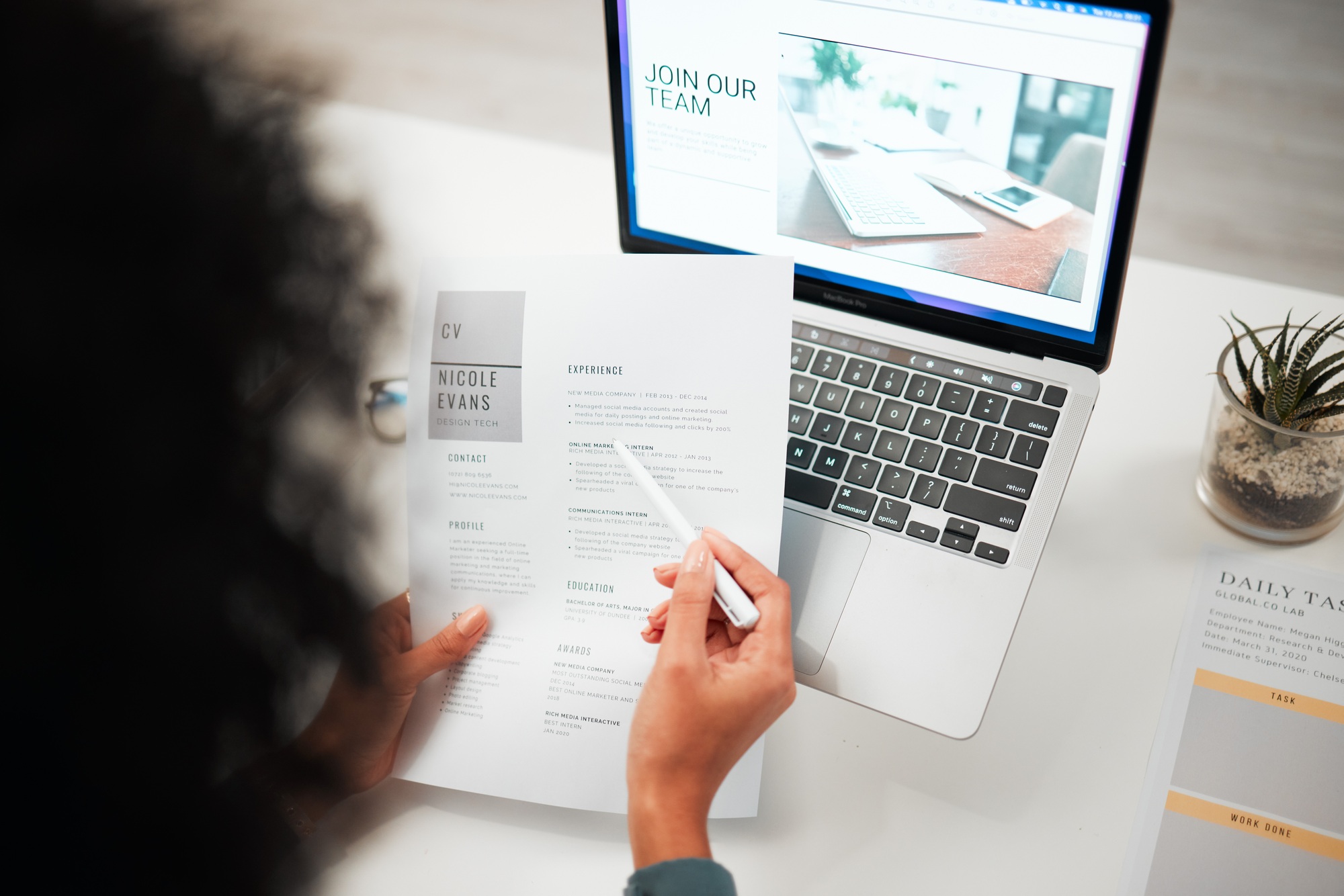
How to Choose the Right Special Skills for Resume Success
Learn how to choose, organize, and present special skills for resume success. This guide includes technical and soft skills, comparison tables, and AI-friendly strategies to pass ATS filters and stand out in competitive job markets.