Clear and precise documentation is essential in any regulated industry, particularly in pharmaceuticals, manufacturing, and healthcare. Proper documentation enhances transparency, supports regulatory compliance, and strengthens operational efficiency. However, even minor documentation mistakes can lead to serious setbacks, including compliance challenges, costly errors, and process inefficiencies.
In this article, we’ll delve into the most common documentation mistakes, why they happen, and practical strategies to prevent them. By understanding these pitfalls and their solutions, you can ensure your records consistently uphold the highest quality standards.
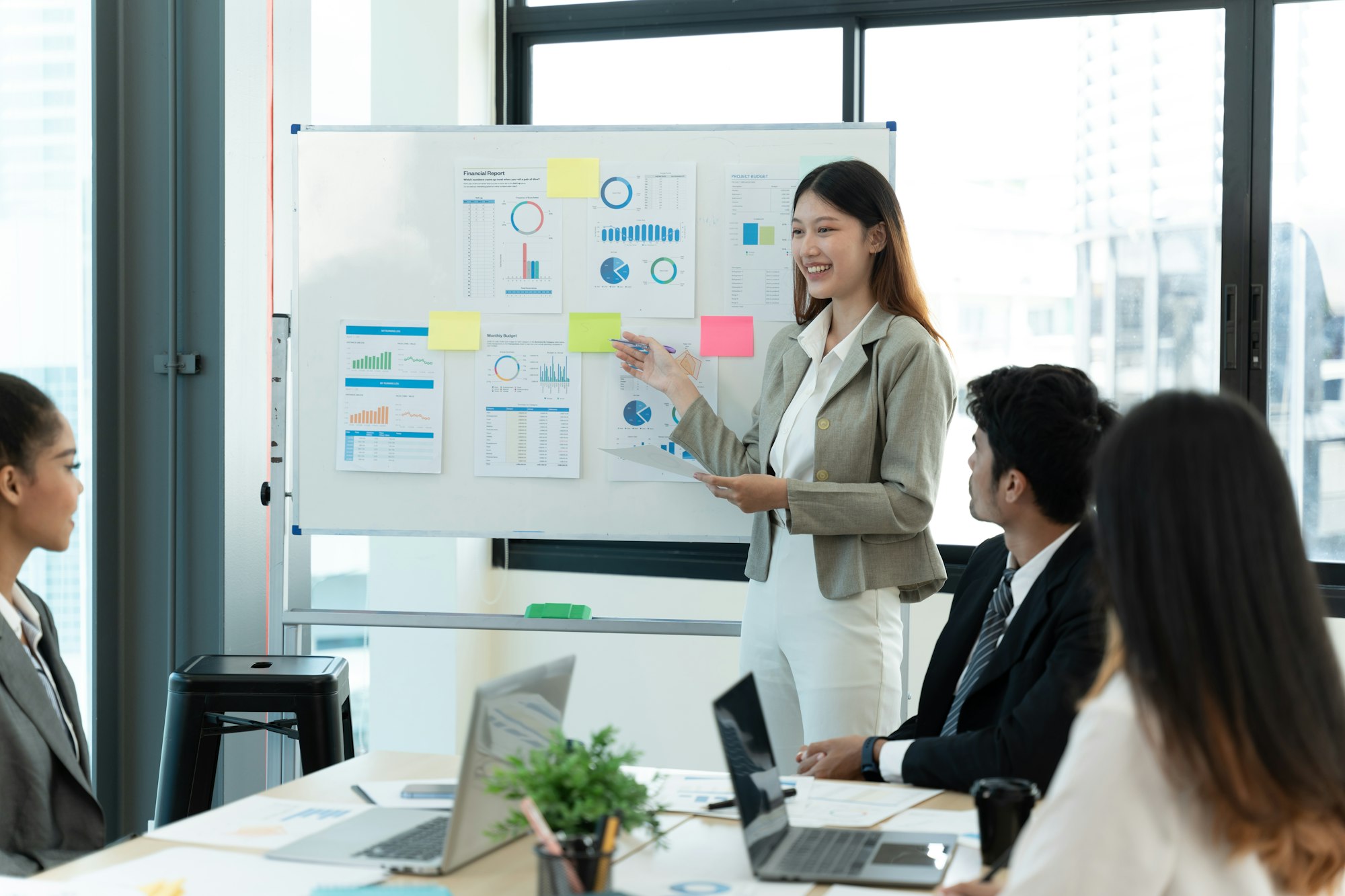
Overlooking Standardization: The Gateway to Inconsistencies
Overlooking standardization in documentation creates inconsistencies across departments. Without a unified format, styles and terminologies vary, leading to confusion and errors. These inconsistencies make it difficult for employees to interpret documents accurately. As a result, teams struggle to communicate effectively, slowing down workflows and risking critical misunderstandings. Standardized documentation serves as a guide, but without it, each department follows its own approach. This lack of standardization makes documents harder to audit and complicates compliance efforts. When teams don’t follow a single format, the documentation loses its reliability, affecting the organization’s credibility.
To avoid this pitfall, organizations should implement a standardized template for documentation. By enforcing this template, they create a consistent style and format that employees can follow easily. Training employees on these guidelines strengthens understanding and promotes uniformity.
In turn, standardization builds a reliable foundation for compliance and smooth audits. Clear, standardized documents become accessible across all teams, enhancing collaboration and efficiency. When everyone follows the same structure, teams can work seamlessly, creating a stronger documentation process that supports the entire organization.
Sign up for Introduction to Good Documentation Practices Course
Documentation Mistakes: A Quick Overview
Inaccurate Information
Failing to provide accurate data leads to misinterpretation.
Incomplete Records
Missing information disrupts workflows and causes compliance issues.
Ambiguous Language
Vague wording can lead to misunderstandings and errors.
Omitting Dates and Signatures
Critical to track document approval and validity.
Overwriting Previous Versions
Losing document history impacts traceability.
Lack of Formatting
Inconsistent format makes it difficult to read and interpret.
Documentation Mistakes by Department
Quality Control (QC)
Quality Control (QC) documentation plays a crucial role in ensuring product quality and regulatory compliance. However, missing or incomplete records in QC documentation often create significant issues. When essential entries are absent, audits face delays, and compliance risks increase. Inaccurate or missing data can result in misinterpretations, leading to errors in quality checks. This not only impacts product quality but can also compromise patient safety. Furthermore, auditors expect complete and accurate documentation to verify each process step. If records don’t meet these standards, organizations may face compliance issues and potential penalties.
To avoid these risks, QC teams must prioritize thorough, accurate documentation. Regular checks help detect missing information early, ensuring records stay complete. Training employees on QC documentation standards also reduces errors and boosts consistency. Additionally, implementing standardized templates for QC records promotes accuracy and reduces misinterpretation risks. With clear templates, employees know exactly what details to include.
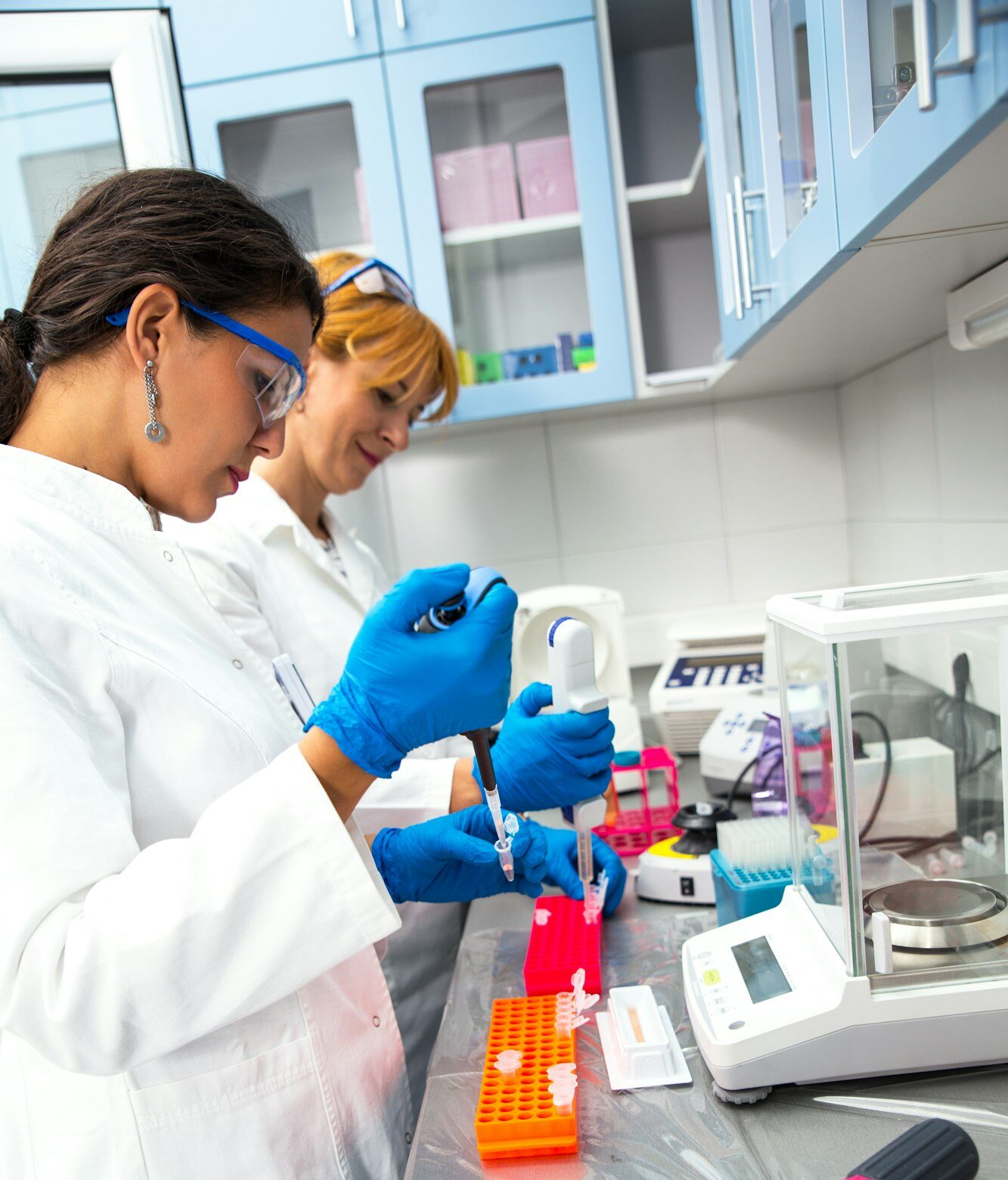
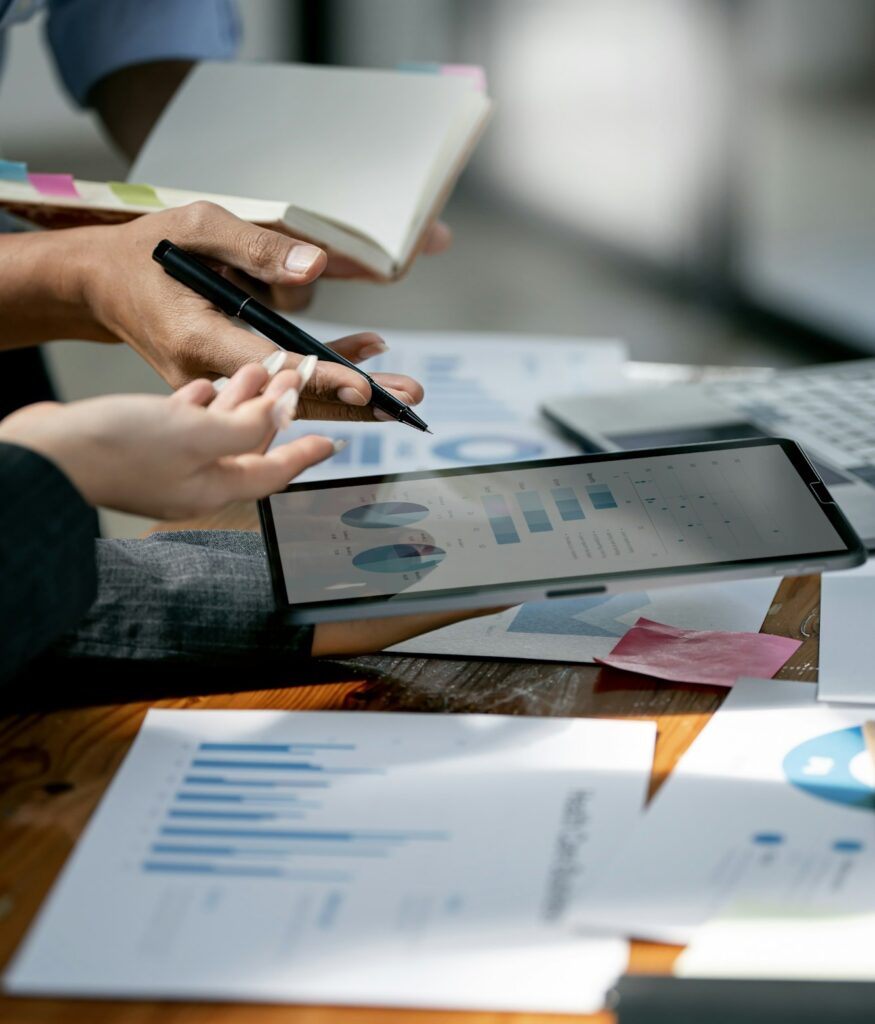
Manufacturing
Manufacturing documentation requires consistency to maintain clear communication and product quality. Yet, inconsistent formats often disrupt this process, especially when production methods shift or team members change. When different teams use varied formats, essential details may become difficult to locate. This inconsistency can lead to miscommunication, delays, and even production errors. Moreover, without a unified documentation style, interpreting instructions or verifying steps becomes challenging, especially during audits. These issues can compromise product quality and regulatory compliance, posing significant risks to manufacturing operations.
To prevent these problems, manufacturers should enforce a standardized documentation format across all teams. By using a uniform template, employees can easily follow and complete records. Training all staff members on documentation standards strengthens this approach, ensuring consistency despite team changes or new processes. Additionally, periodic reviews of manufacturing documents can catch format inconsistencies early, reducing the risk of production errors.
No Backup? A Critical Documentation Mistake
Having a backup and recovery plan is crucial to avoid the irreversible loss of vital information. Here are essential steps:
Here is some tips to Avoid Poor Version Control and Document Management
Implement a Secure Backup System
A secure backup system prevents data loss in emergencies.
Regularly Test the Recovery Process
Testing ensures that the backup works as intended.
Assign a Recovery Manager
Designating a responsible person aids in smooth recovery.
Automate Backups
Automation minimizes the chances of missed backups.
Educate Staff on Backup Protocols
Employees should know the importance of secure backups.
Document Control: Avoiding Critical Documentation Mistakes
Lack of Version Control
Documentation mistakes, such as lacking version control, pose serious risks to accuracy and consistency. Without a clear versioning system, employees may unknowingly follow outdated procedures, leading to inconsistencies in operations. These documentation mistakes can result in errors as teams use conflicting information to complete tasks. Furthermore, without version control, identifying the most recent document becomes challenging, creating confusion and increasing compliance risks. For industries where accuracy is critical, version control is essential to maintain product quality and regulatory compliance.
To avoid these documentation mistakes, implement a version control system that clearly labels each document version. Include dates, version numbers, and author initials to accurately track updates. Training employees on version control practices helps ensure they use the correct documents. Regularly reviewing and archiving older versions prevents accidental use of outdated information. By keeping only the latest versions accessible, you reduce confusion and enhance operational efficiency. When teams follow an organized version control system, they improve accuracy, uphold compliance, and maintain consistency in all documentation.
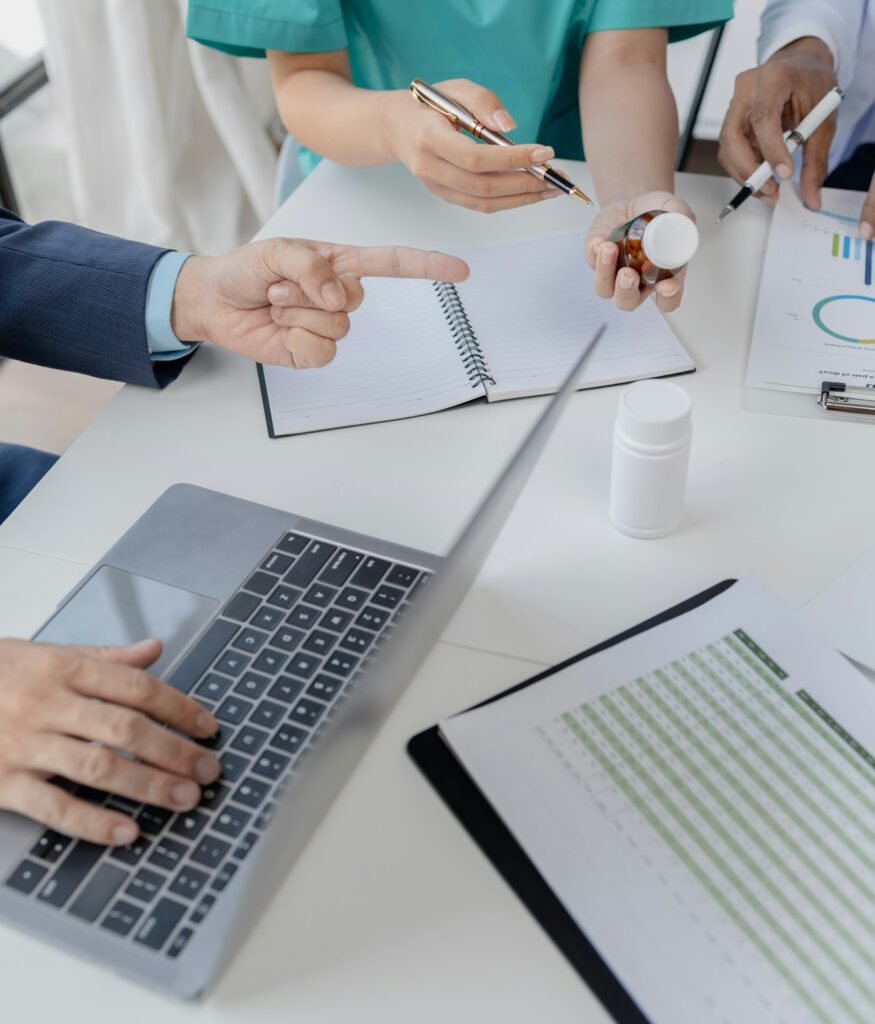
Missing Traceability
Missing traceability in documentation creates serious challenges for tracking changes and identifying authorship. When records lack organization, teams struggle to see who made updates or when changes occurred. This absence of traceability can lead to compliance issues, as regulators often require clear records of document history. Without traceability, inconsistencies arise, making it difficult for teams to validate steps or ensure quality standards. Over time, poorly organized documents create confusion, increasing the risk of mistakes and miscommunication across departments. For industries where accuracy and accountability are crucial, missing traceability poses significant risks.
To resolve traceability issues, establish clear document organization practices that ensure each change is recorded. Use tools or systems that log changes automatically and assign author names to every update. Training teams on proper documentation habits also reinforces the importance of tracking modifications. Regular audits of documentation can help identify traceability gaps before they impact compliance. By prioritizing traceability, teams can track document history more effectively, reduce errors, and uphold compliance.
Importance of Consistent Terminology in Documentation
Inconsistent terminology in documentation confuses readers and increases the chance of misinterpretation. When departments use different terms for the same concept, communication breaks down, and errors multiply. For example, one team may use “quality control” while another says “QC,” assuming everyone understands. Without a standard language, these small differences lead to big misunderstandings. This issue grows more complicated when new team members or external partners try to interpret the documents. Misinterpretations slow down workflows, create compliance risks, and weaken overall document reliability.
To prevent these issues, companies should standardize terminology across all documents. Start by creating a glossary with clear definitions for essential terms, ensuring every team understands each term’s meaning. Train employees on the importance of consistent terminology and encourage them to consult the glossary when needed. Regularly reviewing documents for terminology consistency also strengthens clarity and avoids confusion. By using standardized language, departments align with a common understanding, reducing errors and improving efficiency. When everyone uses the same terms, communication flows smoothly, and documentation maintains accuracy across all levels.
Documentation Mistakes: Solutions for Process Gaps
Neglecting Employee Training
Untrained staff are more likely to make documentation errors.
Solution: Regular training and refresher sessions improve documentation skills across departments.
Insufficient Resources for Documentation
Limited resources, such as templates and tools, can lead to subpar documentation.
Solution: Invest in high-quality resources, like digital tools and software for documentation.
Skipping Document Audits
Regular audits are essential to catch and correct mistakes early.
Solution: Schedule routine audits to assess documentation accuracy and relevance.
Conclusion
Avoiding documentation mistakes is crucial for maintaining compliance, efficiency, and reliability in any organization. Recognizing common errors like inconsistent terminology, missing traceability, and lack of version control can prevent costly setbacks. By proactively addressing these issues, your documentation process becomes a valuable asset. Clear, standardized records improve team communication, streamline workflows, and strengthen compliance efforts. When everyone follows consistent documentation practices, your organization can better meet regulatory requirements and avoid potential penalties.
Taking proactive measures ensures that your records stay accurate, consistent, and audit-ready. Training employees on documentation standards and regularly reviewing records are essential steps to achieve this. By creating standardized templates, defining terms, and using version control, you build a reliable documentation system. These efforts not only support compliance but also improve overall operational efficiency. When you prioritize strong documentation practices, you protect your organization’s integrity, enhance productivity, and establish a solid foundation for future growth.
References
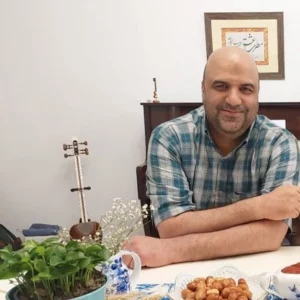
Ershad Moradi
Ershad Moradi, a Content Marketing Specialist at Zamann Pharma Support, brings 6 years of experience in the pharmaceutical industry. Specializing in pharmaceutical and medical technologies, Ershad is currently focused on expanding his knowledge in marketing and improving communication in the field. Outside of work, Ershad enjoys reading and attending industry related networks to stay up-to-date on the latest advancements. With a passion for continuous learning and growth, Ershad is always looking for new opportunities to enhance his skills and contribute to pharmaceutical industry. Connect with Ershad on Facebook for more information.
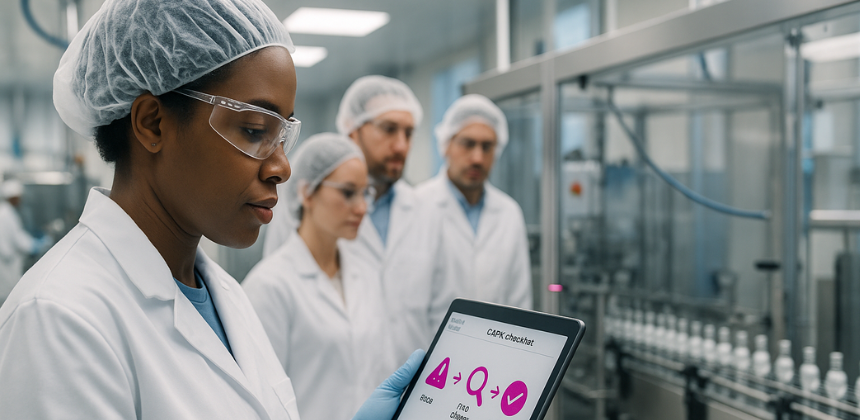
What Is a CAPA Plan? A Beginner’s Guide
This beginner’s guide explains CAPA plans in plain language. You’ll define problems clearly, analyze root causes with proven tools, and turn findings into targeted corrective and preventive actions. Then, you’ll verify effectiveness with metrics and close confidently.

Computerized Maintenance Management: The Complete 2025 Guide
This guide explores computerized maintenance management with practical strategies, CMMS comparisons, and implementation tips. Designed for professionals, entrepreneurs, and job seekers, it helps you choose the right tools, optimize workflows, and boost ROI with preventive and predictive maintenance methods.
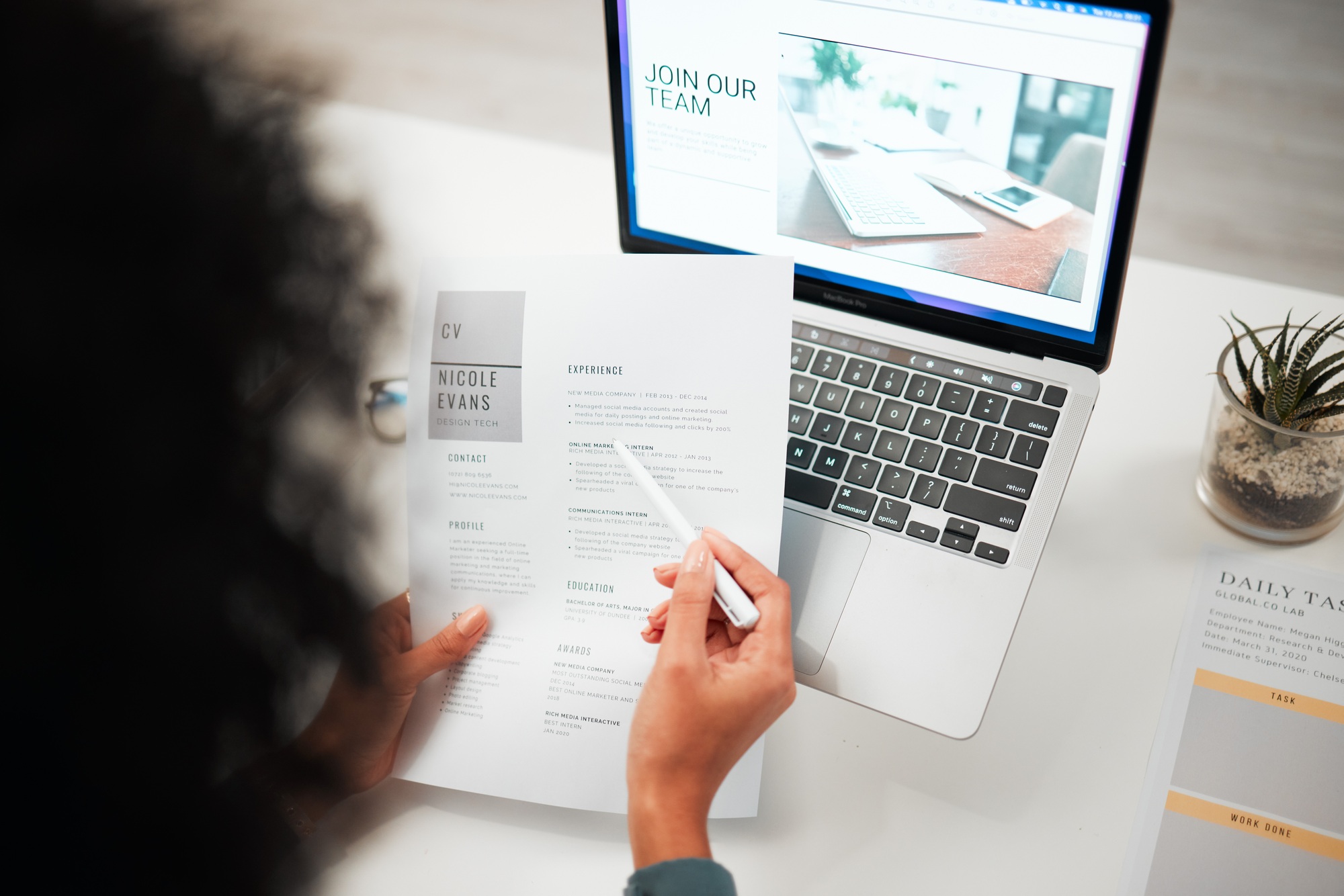
How to Choose the Right Special Skills for Resume Success
Learn how to choose, organize, and present special skills for resume success. This guide includes technical and soft skills, comparison tables, and AI-friendly strategies to pass ATS filters and stand out in competitive job markets.