Corrective and Preventive Actions (CAPA) play a critical role in ensuring operational efficiency and regulatory compliance. Effective CAPA processes are essential for organizations to address non-conformities, reduce risks, and prevent issues from recurring. A well-implemented CAPA strategy improves quality, minimizes operational disruptions, and fosters continuous improvement. Regulatory bodies like the FDA and ISO standards place great emphasis on CAPA processes to safeguard quality and compliance.
This article outlines the key steps required to implement Effective CAPA, providing actionable insights and strategies for businesses to enhance their quality management systems.
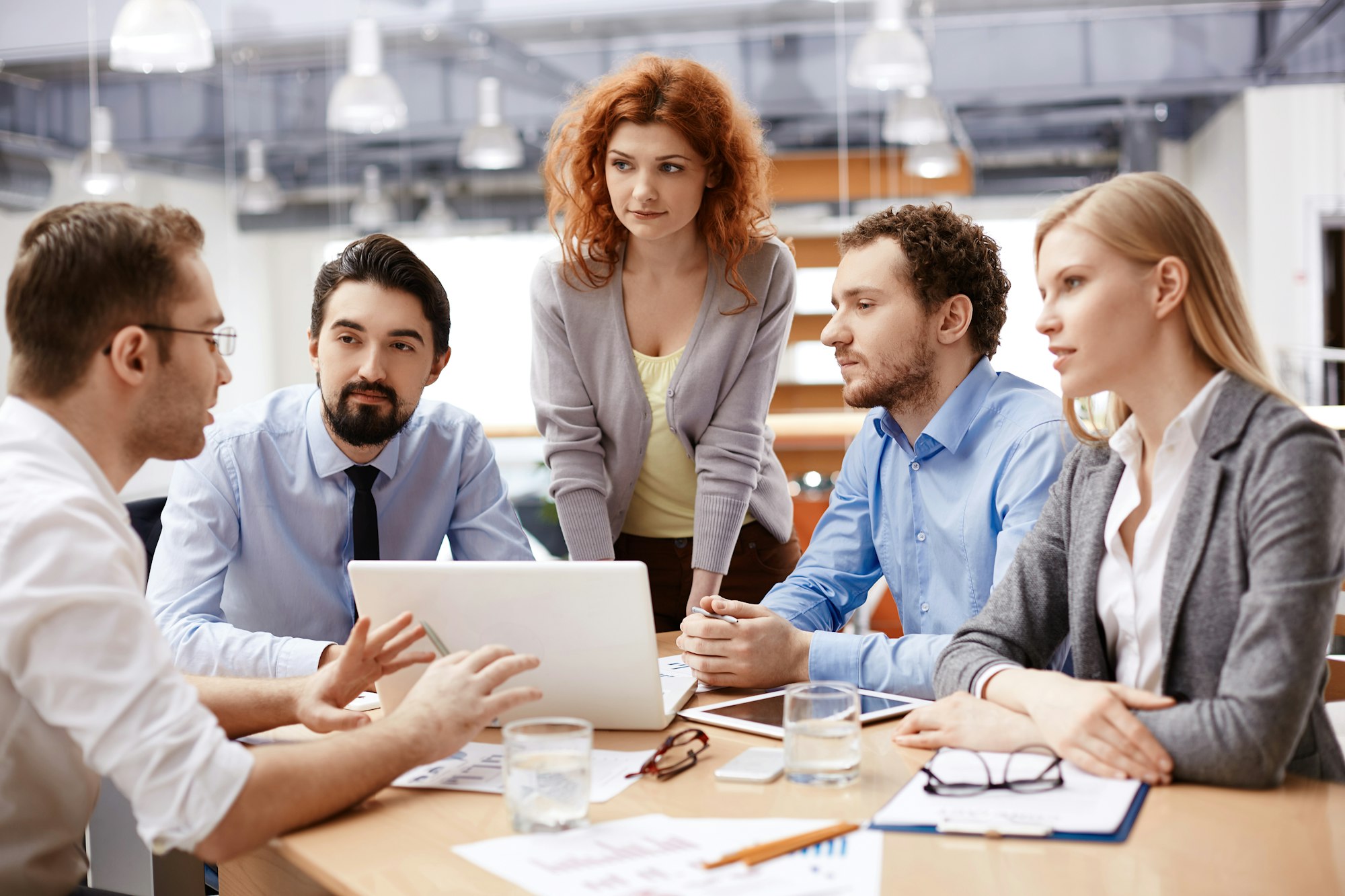
Understanding Effective CAPA Processes
Effective CAPA processes help organizations identify, correct, and prevent recurring issues. To begin, companies must first recognize a problem and document it accurately to ensure clarity. Proper documentation provides a clear understanding of the issue, setting the foundation for the next steps. After identifying the problem, teams proceed by conducting a thorough root cause analysis to uncover the actual reason behind it. This step is critical because it ensures that corrective actions directly target the source of the problem, avoiding incomplete solutions.
Once the root cause is identified, teams implement corrective actions to eliminate it, followed by preventive actions to stop the same issue from happening again. To ensure smooth execution, teams must act quickly and collaborate effectively throughout the process.
Transitioning from problem identification to solution implementation requires structured planning and coordination. Organizations assign specific tasks to responsible team members, ensuring accountability at each step. Regular follow-ups also play a crucial role in verifying whether the solutions are working as intended. Furthermore, continuous monitoring ensures that preventive measures remain effective over time, reducing the risk of recurrence. Detailed records help companies maintain compliance, making future audits run smoothly and building trust with regulators. With consistent monitoring and ongoing improvements, companies foster a proactive quality culture. Well-executed CAPA processes not only resolve current issues but also mitigate potential risks, promoting long-term operational stability and success.
Sign up for GMP Corrective and Preventive Actions (CAPA) Management Course
Key Steps to Implement Effective CAPA
Accurately document the non-conformity or deviation to begin the CAPA process.
Use tools like fishbone diagrams or the 5 Whys to uncover the root cause.
Create actionable steps to eliminate the identified root cause of the issue.
Plan preventive actions to stop future occurrences of similar problems.
Designate accountable team members to oversee corrective and preventive actions.
Track the results of CAPA to ensure the effectiveness of the implemented solutions.
Maintain clear records for audits and future reference, supporting continuous improvement.
Root Cause Analysis: A Key Component of Effective CAPA
Fishbone Diagram
A fishbone diagram, also called an Ishikawa diagram, visually maps the possible causes of a problem. It helps teams organize contributing factors and focus their investigation on specific areas. Typically, the diagram divides causes into categories such as manpower, materials, equipment, methods, and environment. As teams explore each branch, they uncover potential issues within these categories, ensuring no critical factor is overlooked. This structure promotes thorough problem analysis and prevents any aspect from going unnoticed during the problem-solving process.
Moreover, teams often rely on fishbone diagrams to tackle complex challenges effectively. This tool encourages collaborative brainstorming by involving multiple departments, promoting diverse insights. As teams analyze each category, they quickly identify areas requiring corrective actions. Furthermore, it helps avoid premature conclusions by fostering a structured, step-by-step approach to problem-solving. The fishbone diagram’s clear, visual layout simplifies communication, enabling team members to stay aligned throughout the process. Additionally, it enhances decision-making by organizing information logically. By adopting this method, organizations not only resolve issues more efficiently but also improve their CAPA processes.
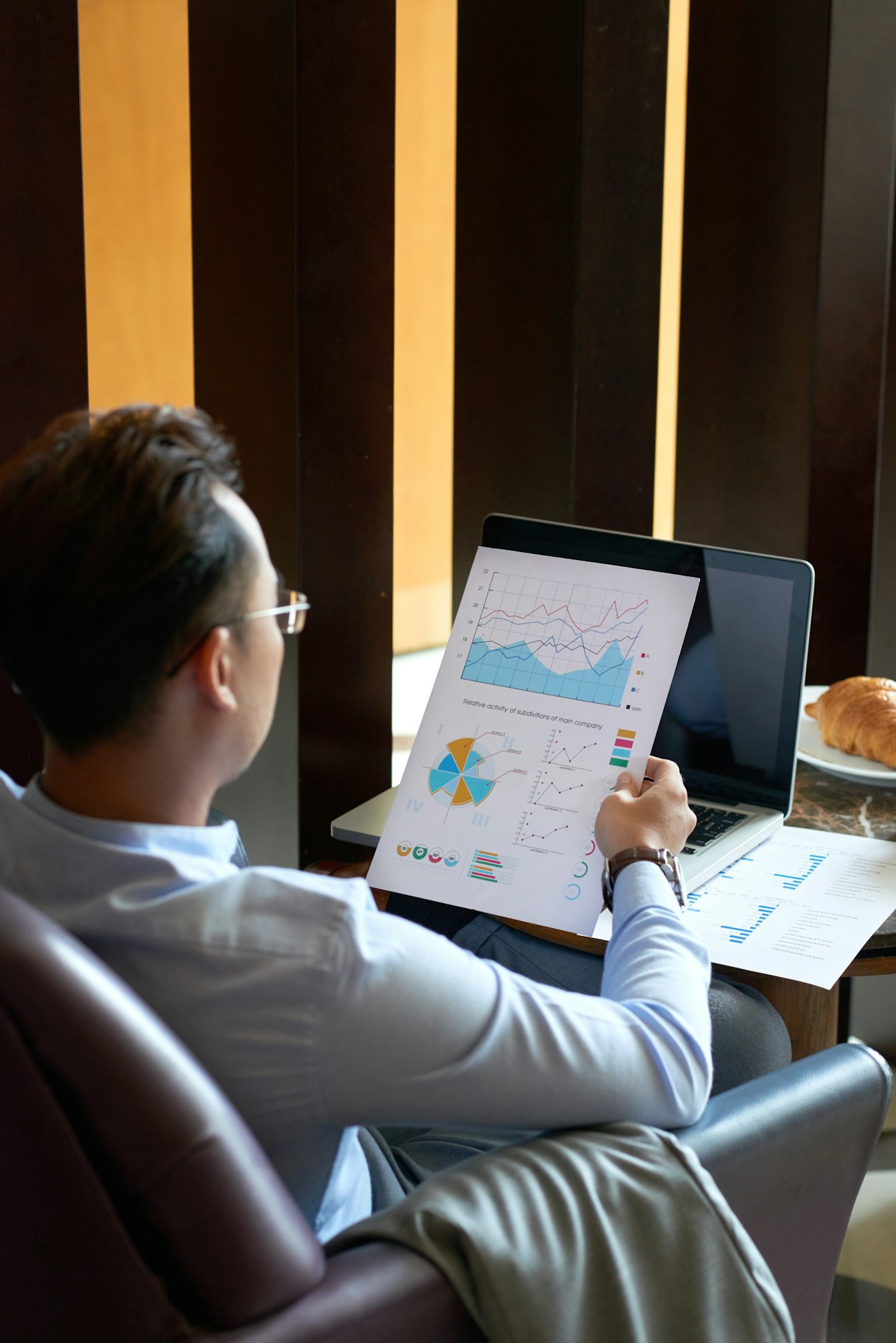
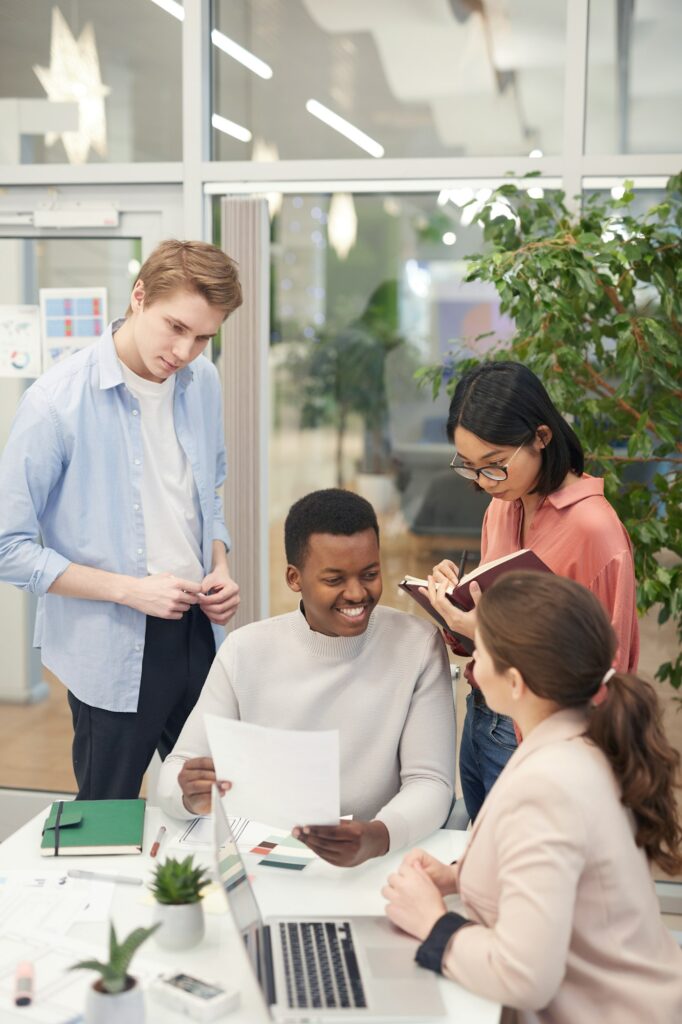
The 5 Whys Method
The 5 Whys method helps teams uncover the root cause of a problem by repeatedly asking “Why?” multiple times. As a result, this technique pushes beyond surface-level issues, promoting deeper thinking and more meaningful analysis. Each answer to “Why?” reveals new insights, gradually narrowing the focus toward the root problem.
Although teams typically stop after five iterations, they can ask additional questions if further clarity is needed. Furthermore, the simplicity of this method makes it highly effective for resolving complex problems without requiring specialized tools.
It ensures a systematic approach, helping organizations avoid quick fixes and, instead, focus on sustainable solutions that address the issue at its source.
Incorporating the 5 Whys method into group discussions fosters collaboration by engaging multiple viewpoints. As team members brainstorm together, they share diverse perspectives, often uncovering unexpected causes.
Additionally, this method shifts the focus away from assigning individual blame, encouraging teams to identify flaws within processes, systems, or workflows. It also helps teams logically connect related causes, revealing hidden patterns that may otherwise go unnoticed.
Common Pitfalls to Avoid in Effective CAPA Implementation
Inadequate Root Cause Analysis
Failing to identify the real cause leads to repeated non-conformities. Teams should invest time in comprehensive analysis.
Delayed CAPA Implementation
Delays in executing CAPA plans can worsen problems and affect compliance. Timely action is essential.
Lack of Documentation
Incomplete or missing records complicate audits and hinder continuous improvement. Ensure all CAPA activities are documented.
Insufficient Monitoring
Monitoring is essential to evaluate whether the implemented actions are effective. Regular tracking ensures desired outcomes.
Poor Communication Across Teams
Cross-functional collaboration is crucial for CAPA success. Miscommunication can cause confusion and delays.
Developing and Implementing CAPA Plans
Corrective Actions
Corrective actions aim to address and fix the root cause of non-conformities within processes or systems. These actions ensure that the same problem does not happen again, safeguarding operational stability. To resolve issues effectively, teams may revise procedures, replace faulty equipment, or provide additional training to employees. Each step must focus directly on the identified root cause to prevent future occurrences. Moreover, corrective actions help businesses maintain compliance, which is crucial for avoiding regulatory penalties and costly mistakes. With prompt action, organizations can reduce downtime and improve overall product quality.
Implementing corrective actions requires careful planning and clear communication among all team members involved. Assigning specific responsibilities ensures accountability at every stage and promotes smooth execution. Additionally, teams need to monitor progress closely to confirm that corrective measures are delivering the desired outcomes. Regular reviews further help organizations fine-tune strategies, especially if new problems emerge during the process. Acting swiftly and decisively builds trust with both stakeholders and regulatory bodies, enhancing the organization’s reputation. Furthermore, effective corrective actions strengthen CAPA processes by creating sustainable solutions that align with long-term goals.

Preventive Actions
Preventive actions focus on stopping potential problems before they occur, ensuring smoother operations. Teams take proactive steps such as scheduling regular maintenance, closely monitoring equipment, and training employees to prevent disruptions. These actions address risks early, helping processes run efficiently without unexpected interruptions. Additionally, preventive actions promote consistency by keeping equipment and systems in optimal condition. As teams identify areas vulnerable to failure, they can act swiftly to mitigate risks, preventing minor issues from escalating into major problems.
Implementing preventive actions requires careful planning and continuous monitoring to maintain their effectiveness. Teams must regularly track critical parameters to detect early warning signs and address them promptly. Furthermore, training programs equip employees to handle challenges efficiently and ensure process stability. Clear communication across all levels ensures that everyone understands their responsibilities in preventing future problems. By prioritizing preventive actions, organizations improve operational stability and minimize downtime. Over time, these proactive measures also reduce the likelihood of costly repairs and compliance issues.
Monitoring and Measuring CAPA Effectiveness
Monitoring CAPA implementation ensures that corrective and preventive actions deliver the intended results. Teams need to establish performance indicators that track key metrics, such as time-to-closure and recurrence rates. These metrics help assess if the solutions effectively address the root cause. Regular reviews also allow teams to make necessary adjustments if the corrective actions fail to produce the expected outcome. This ongoing evaluation ensures the CAPA process remains on track and supports continuous improvement.
Effective monitoring involves frequent check-ins and real-time data tracking. Teams must document the progress and outcomes of every CAPA activity, making the data available for audits and future reference.
Continuous monitoring allows companies to detect and resolve issues before they escalate, ensuring long-term operational stability. CAPA systems that emphasize regular evaluation help organizations respond quickly to new challenges, fostering a proactive quality management culture.
Advanced Techniques to Ensure Effective CAPA
Automated CAPA Systems
Utilize software tools to streamline CAPA workflows, ensuring timely completion of tasks. Automation reduces manual errors and speeds up implementation.
Performance Metrics and KPIs
Establish measurable KPIs to track the effectiveness of CAPA. Metrics like time-to-closure and recurrence rates provide valuable insights.
Cross-Functional Audits
Conduct regular internal audits involving cross-functional teams. This approach ensures compliance and uncovers potential issues before they escalate.
Feedback Loops for Continuous Learning
Incorporate feedback from CAPA outcomes into future processes. Learning from past CAPA activities helps improve future actions.
Conclusion
Implementing Effective CAPA ensures that organizations maintain high standards of quality and compliance. A well-designed CAPA system not only addresses current issues but also prevents future occurrences, fostering a proactive approach to problem-solving. Key steps like identifying the issue, conducting thorough root cause analysis, implementing corrective and preventive actions, and ensuring accountability are vital to success. Monitoring outcomes, maintaining documentation, and engaging employees further strengthen CAPA processes. By following these strategies, businesses can enhance their quality management systems and drive continuous improvement, securing long-term operational excellence and regulatory compliance.
References
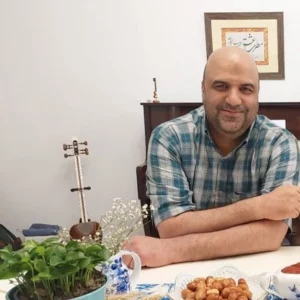
Ershad Moradi
Ershad Moradi, a Content Marketing Specialist at Zamann Pharma Support, brings 6 years of experience in the pharmaceutical industry. Specializing in pharmaceutical and medical technologies, Ershad is currently focused on expanding his knowledge in marketing and improving communication in the field. Outside of work, Ershad enjoys reading and attending industry related networks to stay up-to-date on the latest advancements. With a passion for continuous learning and growth, Ershad is always looking for new opportunities to enhance his skills and contribute to pharmaceutical industry. Connect with Ershad on Facebook for more information.
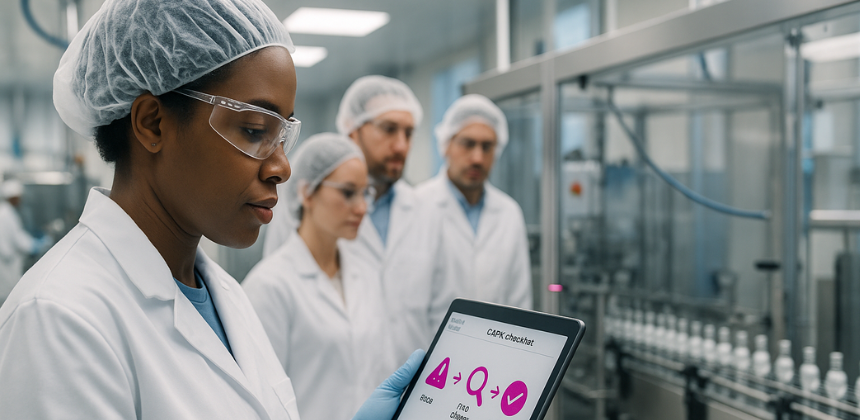
What Is a CAPA Plan? A Beginner’s Guide
This beginner’s guide explains CAPA plans in plain language. You’ll define problems clearly, analyze root causes with proven tools, and turn findings into targeted corrective and preventive actions. Then, you’ll verify effectiveness with metrics and close confidently.

Computerized Maintenance Management: The Complete 2025 Guide
This guide explores computerized maintenance management with practical strategies, CMMS comparisons, and implementation tips. Designed for professionals, entrepreneurs, and job seekers, it helps you choose the right tools, optimize workflows, and boost ROI with preventive and predictive maintenance methods.
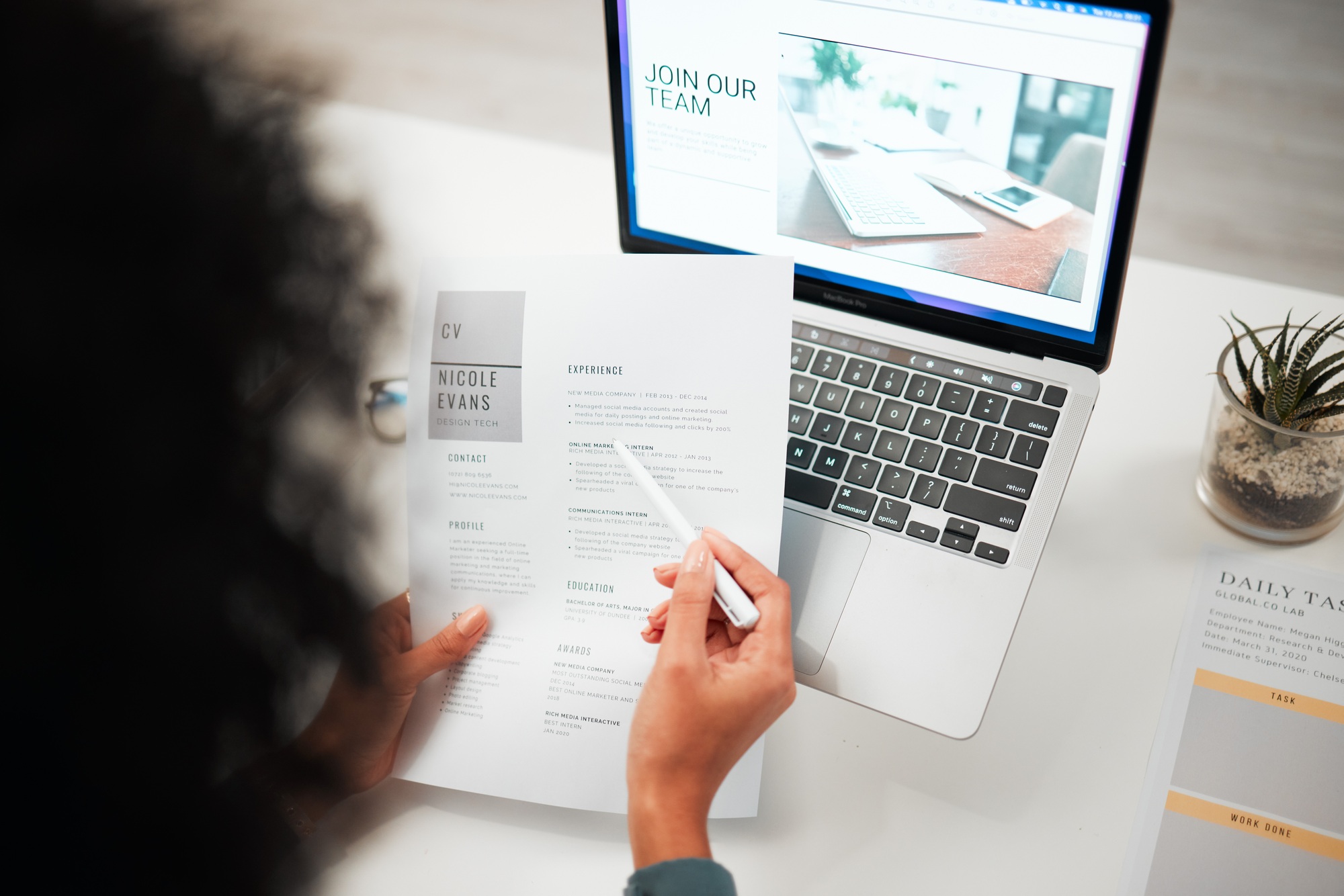
How to Choose the Right Special Skills for Resume Success
Learn how to choose, organize, and present special skills for resume success. This guide includes technical and soft skills, comparison tables, and AI-friendly strategies to pass ATS filters and stand out in competitive job markets.