A Quality Management System (QMS) plays a critical role in maintaining high standards in any organization. Whether it’s in manufacturing, pharmaceuticals, or another highly regulated industry, a robust QMS ensures compliance with regulatory requirements while simultaneously driving continuous improvement. Companies that adopt a strong QMS benefit from streamlined operations, reduced risks, and better overall product quality.
In this article, we’ll explore the various aspects of how a QMS ensures compliance and quality, offering practical tips and strategies to maximize its benefits.
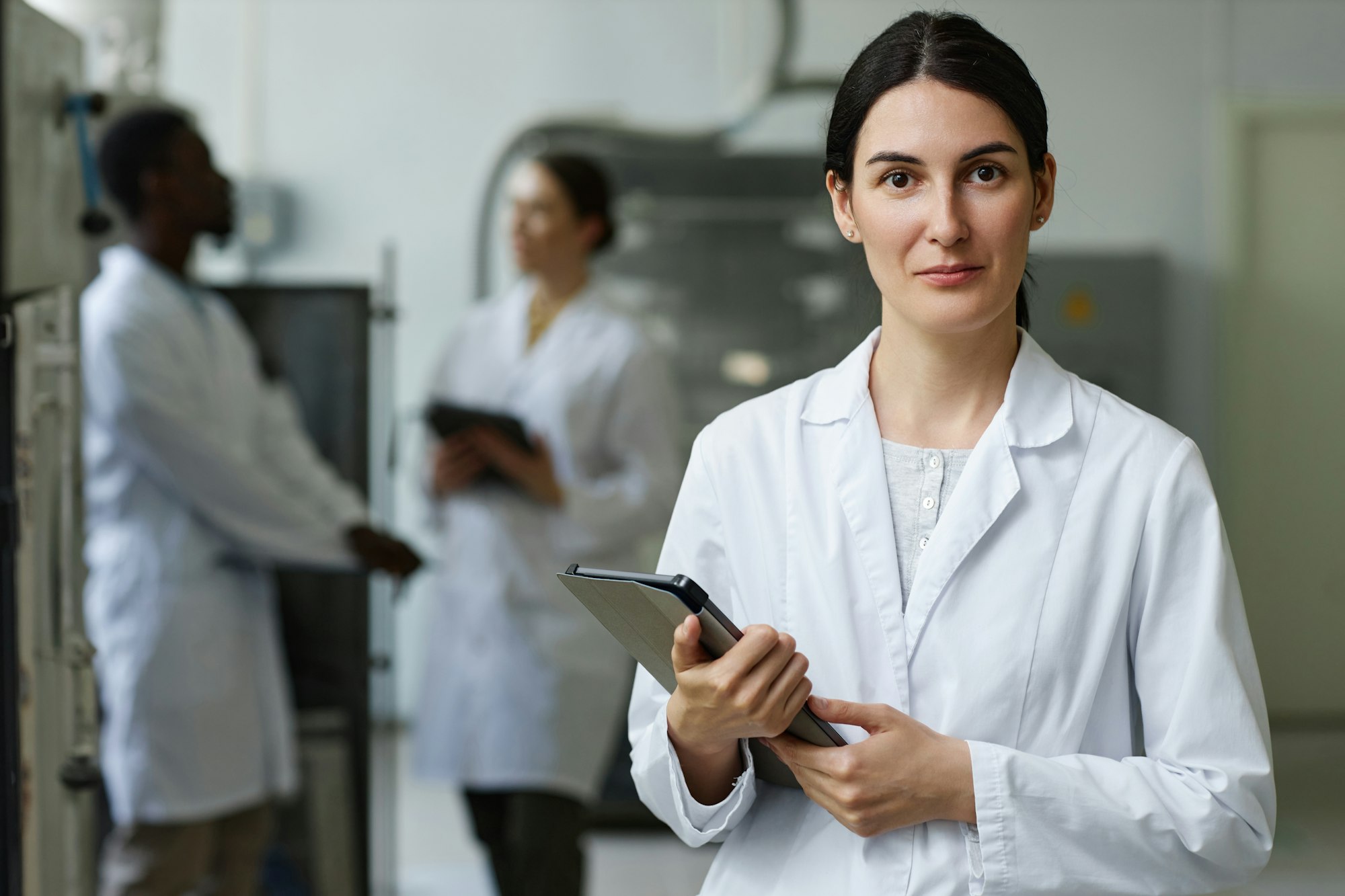
What is the Role of QMS in Driving Compliance?
A Quality Management System (QMS) plays a vital role in ensuring compliance across industries. It provides a structured framework that helps organizations meet regulatory standards consistently. By implementing a QMS, companies can establish clear processes for managing quality, reducing errors, and staying aligned with industry regulations. This system helps businesses track their performance, identify areas for improvement, and ensure that they meet all compliance requirements. Transitioning from manual processes to an organized QMS makes compliance easier, quicker, and more efficient.
Moreover, a QMS supports continuous monitoring of operations, ensuring that compliance is maintained over time. Regular internal audits, reviews, and updates to processes help organizations avoid penalties and maintain their reputation. The system also ensures that employees understand their roles in maintaining compliance, which reduces risks and improves accountability. With clear guidelines and defined responsibilities, everyone in the organization knows how to contribute to meeting regulatory standards. This proactive approach strengthens both compliance efforts and overall business success.
Sign up for Introduction to GMP Quality Management Systems Free Course
Why is a QMS Essential for Quality Assurance?
Quality assurance is another crucial aspect where a QMS proves its worth. At its core, quality assurance ensures that products or services consistently meet customer expectations. By standardizing processes and improving communication, a QMS provides a structured approach to quality. It allows companies to track performance, identify inefficiencies, and implement corrective actions as needed.
Moreover, by focusing on continuous improvement, a QMS enables organizations to move beyond merely meeting minimum standards. It empowers teams to seek excellence by refining processes, reducing waste, and increasing efficiency. For instance, routine audits and inspections under a QMS help in spotting potential issues before they become costly problems, allowing the company to maintain high-quality standards while staying compliant.
Key Components of a Successful QMS
A successful QMS integrates several essential components that work together to ensure compliance and quality:
Document Control
A central feature of any QMS, document control ensures that policies, procedures, and records are consistently up-to-date and easily accessible.
Internal Audits
Regular internal audits are crucial for identifying non-conformances and areas that need improvement, helping maintain compliance.
Corrective Actions
Corrective actions address any non-compliances identified during audits or day-to-day operations, ensuring continuous improvement.
Training and Competence
Ensuring that employees are trained and competent to perform their roles is critical for compliance and maintaining high-quality standards.
Risk Management
Proactive risk management allows companies to foresee potential compliance or quality issues and address them before they become problems.
QMS Improve Process Efficiency and Reduce Risks
What Role Does a QMS Play in Reducing Operational Risks?
A Quality Management System (QMS) plays a key role in reducing operational risks. It provides a structured approach that helps organizations identify potential risks early.
By implementing consistent processes, a QMS minimizes the chances of errors occurring during operations. Regular audits and reviews help detect any non-conformances, allowing the organization to address them before they cause bigger problems. This proactive approach reduces risks and improves overall efficiency, helping businesses avoid costly delays and compliance penalties.
Additionally, a QMS enhances transparency in operations, making it easier to track issues and resolve them quickly. Clear procedures ensure that employees understand how to handle unexpected situations, reducing confusion during critical moments. With better documentation and communication, teams can address potential risks faster and more effectively.
The QMS also ensures that the organization remains flexible, adapting to changes in regulations or market conditions. By constantly refining processes, businesses can mitigate risks and maintain high standards of quality and compliance.
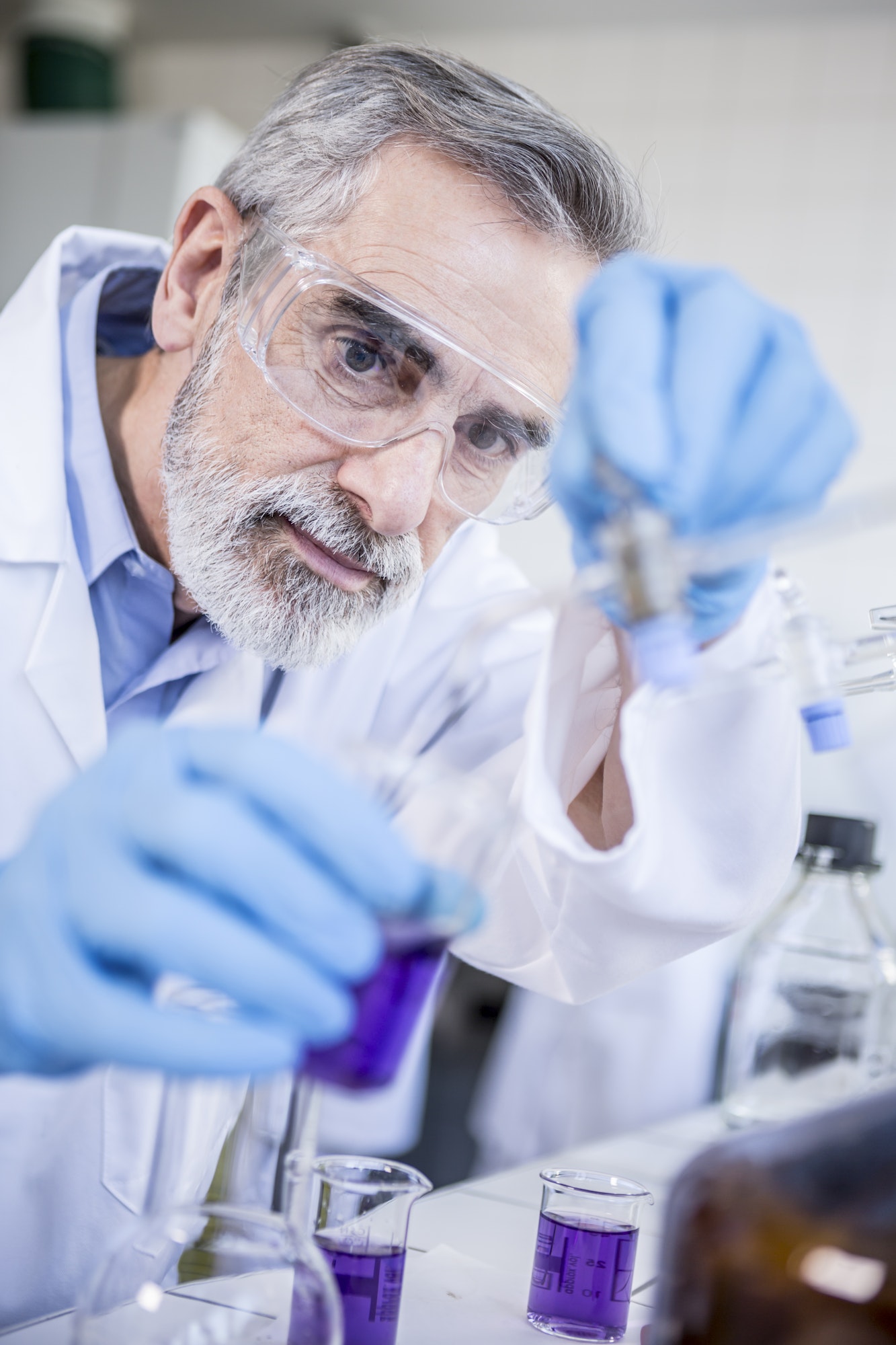
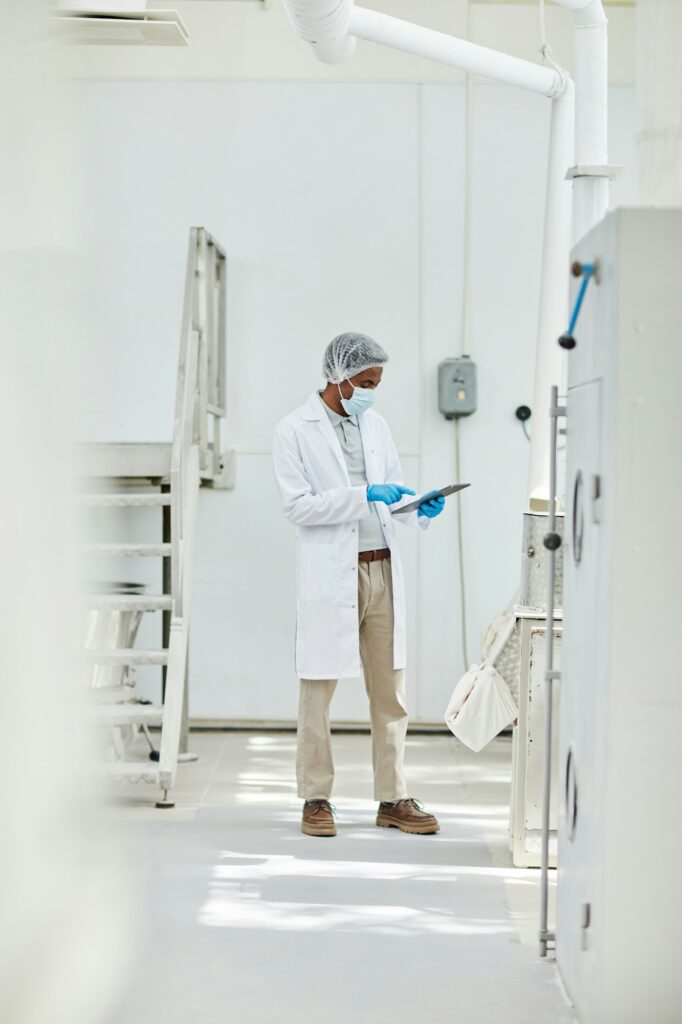
How Does a QMS Help in Continuous Improvement?
A Quality Management System (QMS) drives continuous improvement by encouraging regular evaluations and refinements. It helps organizations set clear goals for quality and performance, which motivates teams to constantly improve.
With a QMS, businesses can track key metrics, identify inefficiencies, and take corrective actions quickly. These improvements create a culture of ongoing development, where employees strive to enhance their processes and results. By continually refining workflows, organizations increase efficiency, reduce waste, and achieve better outcomes.
Additionally, a QMS supports continuous improvement by promoting collaboration and knowledge sharing. It provides a platform for teams to communicate effectively, share insights, and learn from past mistakes. Regular reviews and audits help uncover areas needing improvement, allowing organizations to stay ahead of issues.
This systematic approach helps companies remain competitive, as they adapt quickly to changing market demands. Continuous improvement through a QMS not only enhances quality but also drives innovation, ensuring long-term success and growth.
Top Benefits of Implementing a QMS
Enhanced Regulatory Compliance
A QMS ensures companies consistently meet regulatory standards, including EU GMP and FDA guidelines, reducing the risk of fines or product recalls.
Improved Product Quality
By standardizing processes, a QMS minimizes errors, leading to higher consistency and product quality.
Operational Efficiency
Streamlined workflows and clear procedures reduce inefficiencies, improving overall operational performance and productivity.
Continuous Improvement
A QMS identifies areas needing improvement, enabling organizations to implement corrective actions and enhance performance over time.
Transparency and Accountability
A QMS fosters a culture of accountability through clear documentation and well-defined roles, ensuring compliance with international standards.
Competitive Advantage
Companies with a strong QMS maintain higher quality standards, boosting customer confidence and market competitiveness.
Challenges Companies Face in Implementing the Role of QMS
Overcome Resistance to QMS Implementation
Resistance to change is one of the most common challenges when implementing a Quality Management System (QMS). Employees may resist the new processes, fearing that it will complicate their workflows or increase their workload. To address this, leadership should clearly communicate the role of QMS in improving operations, compliance, and overall efficiency. Explaining how the QMS can simplify tasks, improve quality, and make day-to-day work more streamlined will help employees see the benefits. Effective training is essential, as it equips staff with the necessary skills and confidence to use the system efficiently.
Additionally, involving employees early in the QMS implementation process can reduce resistance. Encourage feedback and suggestions, showing employees that their input matters. This collaborative approach fosters a sense of ownership, making them more likely to embrace the new system. Companies should also celebrate early wins and success stories, demonstrating how the role of QMS enhances operations and benefits employees directly. By continuously supporting and communicating the value of the QMS, resistance will gradually diminish, leading to smoother implementation.
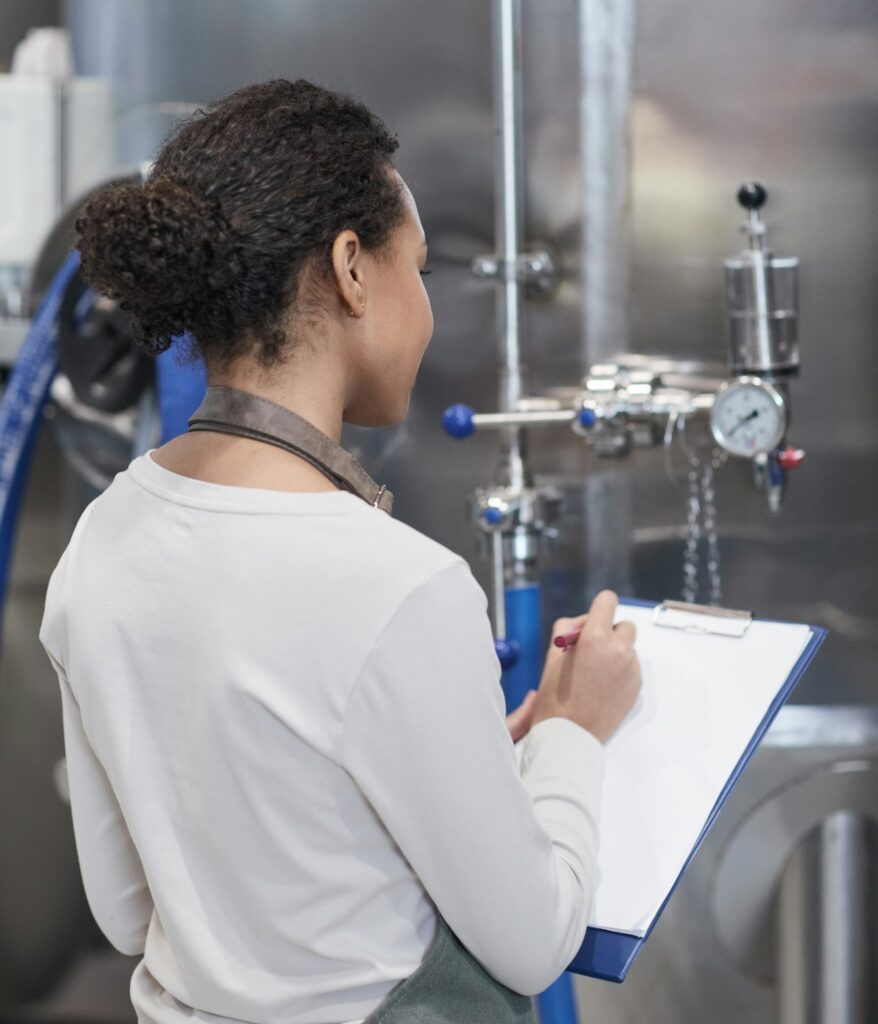
Ensure Proper Resource Allocation for QMS
Allocating the right resources is critical for the success of any QMS implementation. A common challenge is ensuring that enough financial, time, and personnel resources are committed to the project.
The role of QMS in maintaining compliance and improving quality must be recognized at the leadership level, so management should allocate an adequate budget for the system’s setup and ongoing maintenance. Setting clear timelines and milestones ensures the project stays on track without unnecessary delays.
Moreover, companies must assign skilled personnel to manage and oversee the QMS implementation. This includes appointing project managers who understand both the technical aspects of the QMS and the company’s regulatory obligations. Without the proper team, the system may fail to deliver its intended benefits.
Regularly reviewing the resource allocation during the rollout is essential to ensure continued progress. By fully committing to the role of QMS and the necessary resources, organizations can prevent setbacks and ensure a smooth and successful implementation.
Role of QMS Impact Long-Term Business Success
The role of QMS is vital in building and maintaining a strong brand reputation. Customers value companies that consistently deliver high-quality products and services, and a QMS ensures that these standards are met. When businesses implement a reliable QMS, they earn customer trust by offering products that are safe, compliant, and of the highest quality. This, in turn, leads to increased customer loyalty and retention, which are essential for long-term business success.
Additionally, a well-functioning QMS allows companies to respond quickly to customer feedback and make necessary adjustments to meet evolving demands. This agility strengthens the company’s ability to attract new customers while retaining existing ones. Over time, the role of QMS in maintaining quality and compliance not only boosts customer satisfaction but also elevates the company’s market position, contributing to greater market share and competitive advantage.
Key Factors in Choosing the Role of QMS
Choosing the right QMS for your organization requires careful consideration. Here are some factors to keep in mind:
Industry-Specific Requirements
Different industries have unique compliance standards. Make sure the QMS is tailored to your industry’s needs.
Scalability
Choose a QMS that can grow with your business, allowing you to scale up operations without sacrificing quality.
User-Friendliness
A complex or difficult-to-use QMS can lead to low adoption rates. Opt for a user-friendly interface.
Integration Capabilities
Ensure the QMS integrates smoothly with other systems, such as ERP or document management tools, for seamless operations.
Conclusion
The Role of QMS in ensuring compliance and quality cannot be overstated. From driving regulatory compliance to improving product quality, a well-implemented QMS provides organizations with the tools they need to succeed in today’s competitive markets. By focusing on key components like document control, risk management, and employee training, companies can use their QMS to not only meet current standards but to continually improve. Leaders play a critical role in QMS success, and with the right strategies, organizations can overcome common challenges to achieve long-term success.
References
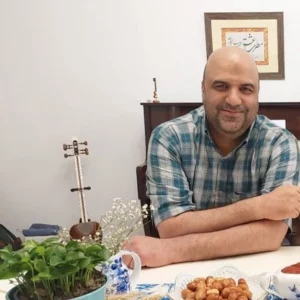
Ershad Moradi
Ershad Moradi, a Content Marketing Specialist at Zamann Pharma Support, brings 6 years of experience in the pharmaceutical industry. Specializing in pharmaceutical and medical technologies, Ershad is currently focused on expanding his knowledge in marketing and improving communication in the field. Outside of work, Ershad enjoys reading and attending industry related networks to stay up-to-date on the latest advancements. With a passion for continuous learning and growth, Ershad is always looking for new opportunities to enhance his skills and contribute to pharmaceutical industry. Connect with Ershad on Facebook for more information.
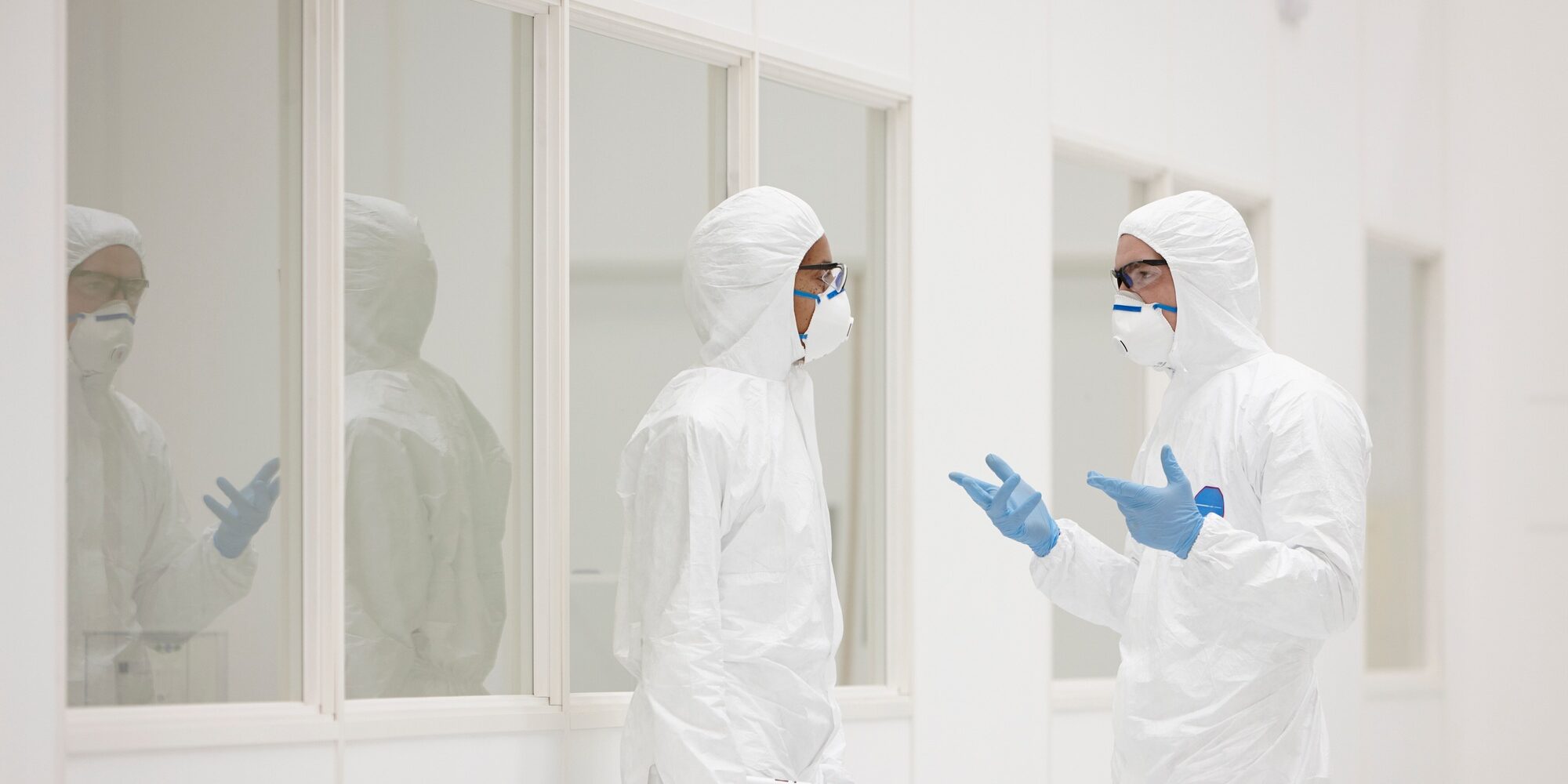
GMP Certification Cost: Reduce It with Free GMP Training
GMP certification cost can be high — but preparation reduces expenses. This guide explains costs, savings, and how Pharmuni’s free GMP course helps you get audit-ready without overspending. Access related GMP learning resources to boost compliance confidence.
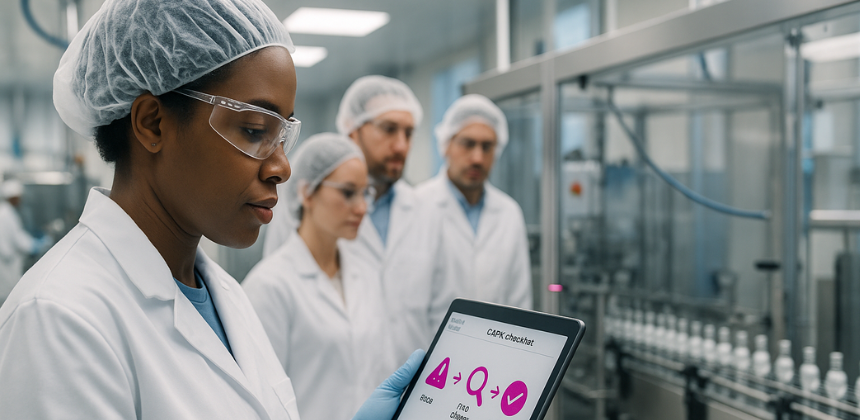
What Is a CAPA Plan? A Beginner’s Guide
This beginner’s guide explains CAPA plans in plain language. You’ll define problems clearly, analyze root causes with proven tools, and turn findings into targeted corrective and preventive actions. Then, you’ll verify effectiveness with metrics and close confidently.

Computerized Maintenance Management: The Complete 2025 Guide
This guide explores computerized maintenance management with practical strategies, CMMS comparisons, and implementation tips. Designed for professionals, entrepreneurs, and job seekers, it helps you choose the right tools, optimize workflows, and boost ROI with preventive and predictive maintenance methods.