GMP change control plays a critical role in pharmaceutical manufacturing. It ensures that any planned changes to processes, systems, or equipment follow a controlled and documented path. If companies skip these steps or mishandle change control, they risk regulatory violations, product recalls, or even harm to patients. That’s why proper training is no longer optional.
Teams must understand what change control means and how to apply it in real-life scenarios. From line supervisors to quality assurance specialists, every member must know their responsibilities. Yet many companies still leave gaps in training, assuming that SOPs and checklists are enough. Unfortunately, this often leads to confusion during audits or failure in compliance.
Let’s face it—change is inevitable in pharma. But managing it poorly isn’t. With targeted training, teams can spot risks early, follow the correct processes, and maintain data integrity. In this article, we’ll break down the key elements of GMP change control, highlight why training matters, and show how to build a knowledgeable, audit-ready team.
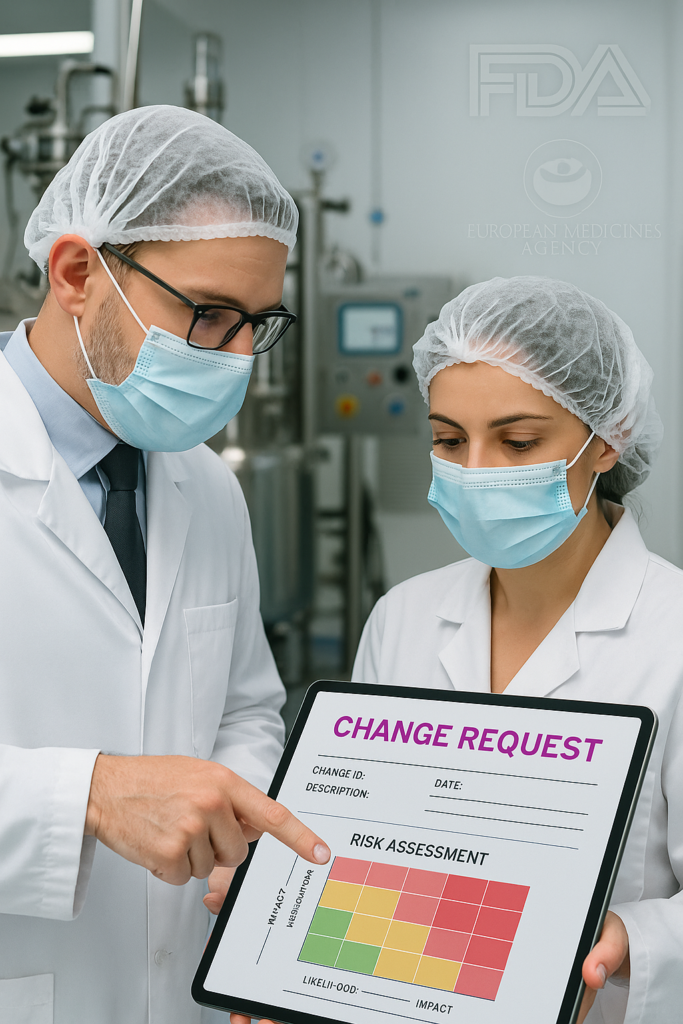
What Is GMP Change Control and Why Does It Matter?
GMP change control is the formal process used to assess, document, and approve changes that could impact product quality or compliance. These changes may involve equipment, raw materials, software systems, facilities, or procedures. Regulatory agencies like the FDA and EMA expect every change to follow a consistent and validated process.
The core goal of change control is to prevent unintended consequences. For example, changing a cleaning procedure might seem simple. However, without a formal evaluation, it could lead to contamination or cross-contamination. The change control process ensures that risk assessments, validation steps, and approvals are completed before implementation.
Furthermore, poorly managed changes often trigger warning letters during inspections. Regulators want to see that each change was documented, justified, and reviewed by qualified personnel. That’s where training becomes vital. Team members must understand when a change qualifies as significant, what documentation is required, and how to collaborate with other departments.
When companies train their staff effectively, change control becomes more than just a box-checking exercise. It becomes a tool for continuous improvement, reducing risk and increasing process reliability. In a regulated environment where one error can halt production or endanger patients, change control isn’t just paperwork—it’s your frontline defense.
Key Components of a GMP Change Control Process
- Initiation and Documentation: Clearly define the change, including the reason and potential impact.
- Risk Assessment: Evaluate the risks to product quality, safety, and compliance.
- Impact Analysis: Check how the change affects equipment, procedures, and validation.
- Review and Approval: Get formal reviews from QA and affected departments before proceeding.
- Implementation Plan: Include timelines, responsibilities, and training needs.
- Testing and Validation: Verify the change works as intended without introducing new risks.
- Closure and Documentation: Complete final reports and archive them for audit readiness.
The Hidden Risk of Poorly Trained Teams
Even the best change control system fails when people don’t understand how to use it. Many companies invest in tools and SOPs but forget the foundation—people. When teams lack proper training, they often make small mistakes with big consequences. These mistakes may go unnoticed until an audit or a product issue occurs. Unfortunately, most errors don’t happen because of laziness—they happen because no one showed them the right way.
Teams skip risk assessments, overlook documentation, or misunderstand when to initiate change control. Without clear guidance and practical training, even experienced staff struggle. This creates hidden gaps that slowly erode compliance. However, with continuous, role-specific training, teams gain the confidence and skills to act correctly. Let’s explore how proper training builds awareness and improves collaboration—two key drivers of GMP success.
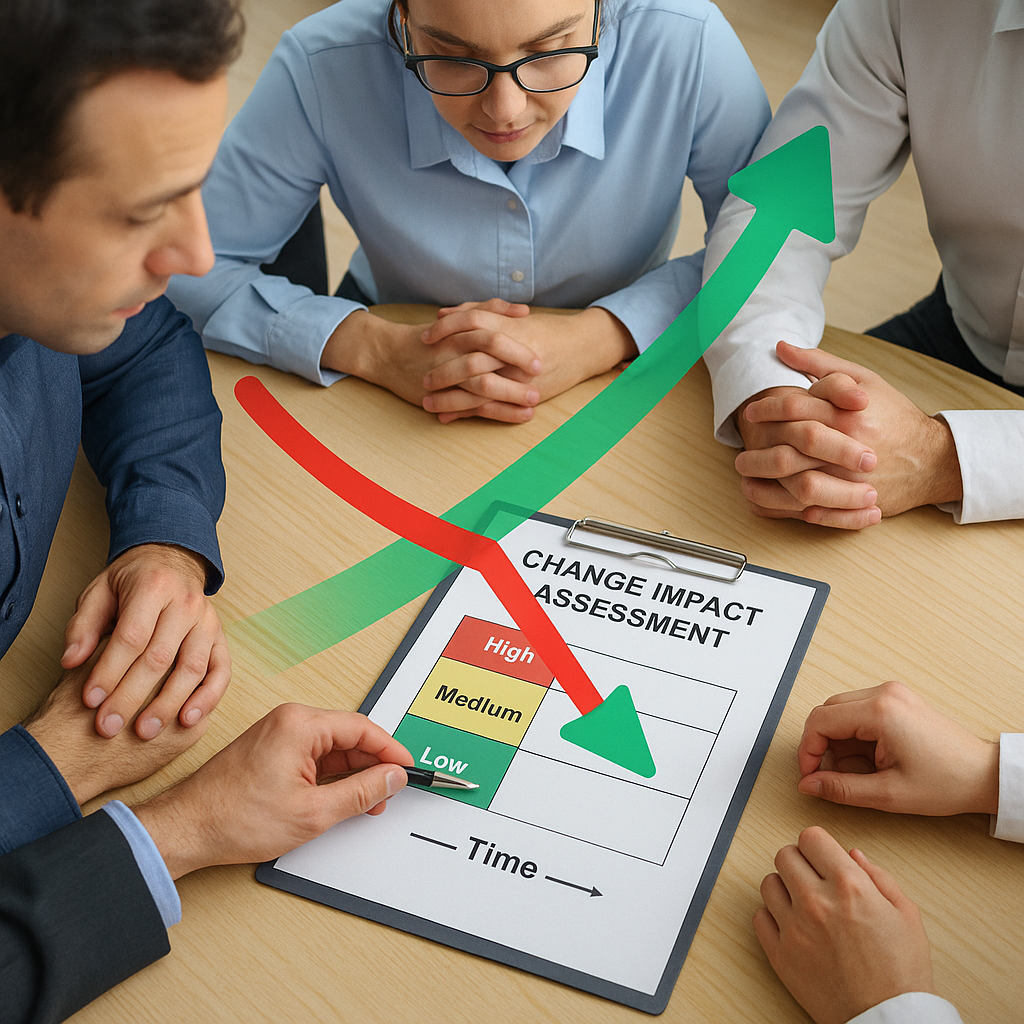
Training Builds Risk Awareness
Trained teams recognize early signs of change and know when to take action. For instance, they understand that switching a supplier or updating equipment may introduce new risks. Because of training, they follow procedures without delay or hesitation. They also understand how even minor changes affect validation, documentation, or patient safety.
Moreover, regular training teaches them how to assess potential risks using proven tools. It also helps them report risks clearly using standardized formats. This consistency ensures that no step gets overlooked. As a result, companies avoid compliance gaps and reduce the chance of rework or costly recalls. With stronger risk awareness, teams protect both the product and the company’s reputation.
Trained Teams Boost Cross-Functional Collaboration
Change control isn’t a solo task—it requires smooth coordination between multiple teams. Trained employees know when to involve QA, validation, engineering, and regulatory. This avoids delays and keeps everyone aligned. They understand how their work affects others and communicate changes before problems arise.
Because of training, employees feel comfortable asking questions or flagging concerns. They escalate potential issues early and help prevent misunderstandings. In cross-functional projects, trained staff reduce back-and-forth emails and avoid costly handoff mistakes. Everyone works from the same playbook and follows consistent steps.
Furthermore, collaboration improves when teams understand each other’s roles. Instead of finger-pointing, departments share responsibility and work toward shared goals. With the right training, teams build mutual respect, strengthen trust, and increase success during audits. Good change control becomes a team win—not just a quality task.
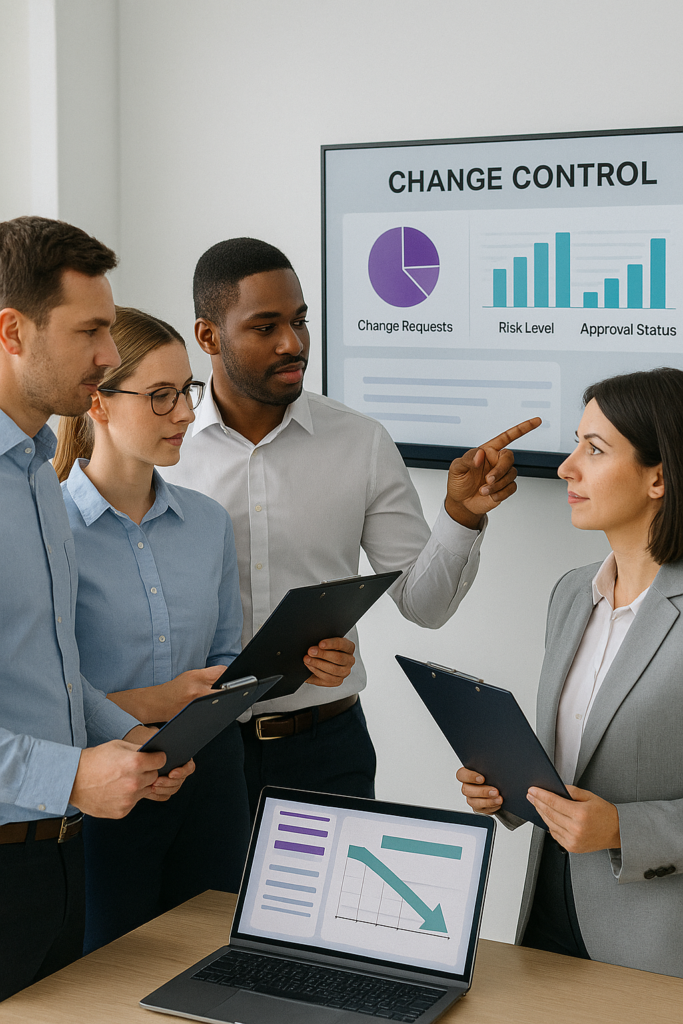
5 Signs Your GMP Change Control Training Is Failing
Repeated Audit Findings
Inspectors highlight the same training-related errors repeatedly.
Confusion About Ownership
Staff don’t know who is responsible for initiating or approving changes.
Incomplete Forms
Teams skip fields, forget signatures, or miss required attachments.
Inconsistent Risk Assessments
Employees use different formats or fail to assess key risks.
Lack of Post-Implementation Review
Changes go live without proper evaluation or documentation updates.
Each of these signals a deeper issue. Without correction, they can trigger 483s or warning letters. Address them early through better training and documentation practices.
How to Improve GMP Change Control Training
- Develop Role-Specific Training - Generic training won’t work. Customize sessions based on job functions to make them relevant and memorable.
- Include Real-Life Scenarios - Use examples from past change requests to simulate decisions. This helps staff apply theory to daily tasks.
- Reinforce SOP Awareness - Link training to actual SOPs your team uses. Help them navigate, interpret, and apply each section.
- Teach Risk Assessment Skills - Give employees tools and examples for evaluating impact. Show them how to document risks clearly and consistently.
- Integrate Cross-Functional Training - Invite different departments to shared sessions. This builds empathy and improves teamwork in high-impact projects.
- Make Training Recurring - Regulations evolve and roles shift. Refresh knowledge regularly to stay ahead of audits and internal gaps.
How Tech and Tools Can Strengthen Change Control
Digital tools can transform change control from a slow, paper-heavy process into a streamlined system. They improve documentation accuracy, enforce SOPs, and give teams real-time visibility. Without the right tools, companies struggle with tracking, consistency, and version control. Even the best-trained teams can fall behind when systems lack structure.
However, technology works best when people know how to use it. So, training must include tools—not just theory. Employees should know how to log changes, assign tasks, and monitor progress. Clear dashboards help everyone stay aligned and reduce guesswork. When your tech supports your workflow, audits run smoother and fewer errors happen. Let’s explore two ways technology enhances change control—starting with automated workflows and data-driven oversight.
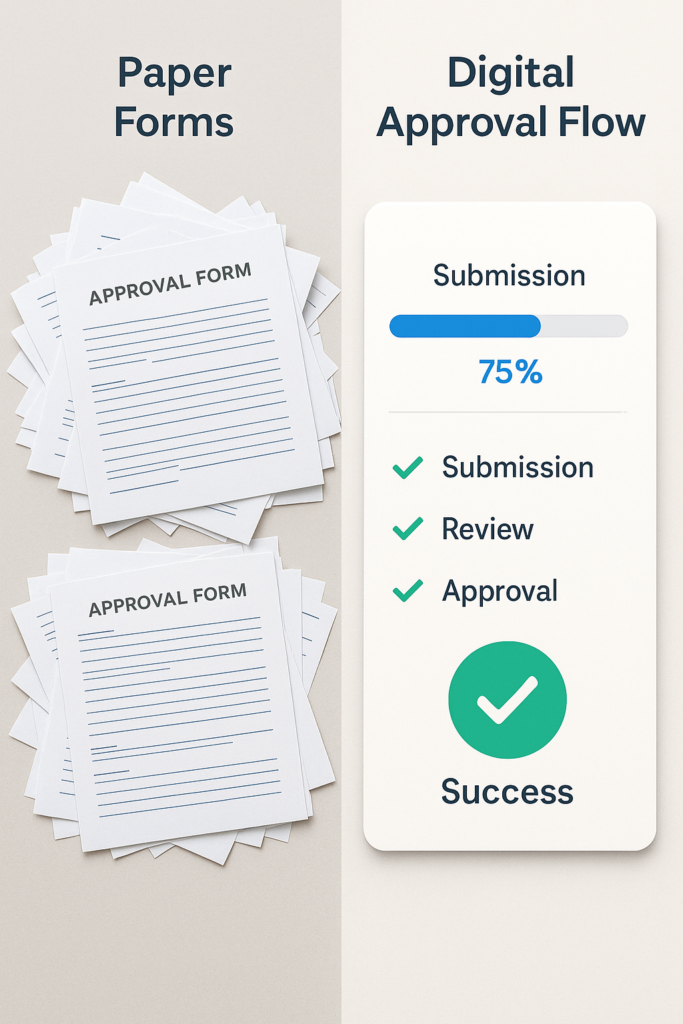
Digital Workflows Ensure Consistency
Manual change control often slows progress and increases risk. Teams lose forms, miss steps, or forget signatures. That’s why digital workflows offer a smarter alternative. They guide employees through every phase, ensuring no task slips through the cracks. Each step becomes mandatory, from risk assessment to QA signoff.
Moreover, digital tools store change records securely and allow version control. Teams access information quickly and reduce redundancy. When inspectors arrive, your documents stay organized and easy to trace. Additionally, built-in alerts remind employees to complete tasks on time.
Training your staff on these tools is essential. With the right skills, teams complete tasks faster and more accurately. They navigate interfaces confidently and know exactly where to upload files or track requests. When workflows stay consistent, audit outcomes improve—and your company reduces costly delays or compliance risks.
Dashboards and Metrics Improve Oversight
Change control isn’t just about completing tasks—it’s also about seeing the bigger picture. Dashboards help teams monitor active changes, overdue steps, and potential risks in real-time. These visual summaries guide decision-making and highlight bottlenecks early.
Moreover, leadership gains clarity through metrics like closure times and SOP adherence rates. They use this data to adjust processes or allocate resources effectively. Metrics also reveal training gaps, allowing managers to target improvements and avoid repeated errors.
But dashboards only help when staff know how to read them. So, train your team to interpret graphs and alerts. Teach them to act on data—not just review it. This builds accountability and strengthens compliance culture.
When everyone understands the metrics, change control becomes proactive—not reactive. Teams solve problems before they escalate. That’s how you move from chaos to clarity—by combining insights with action.
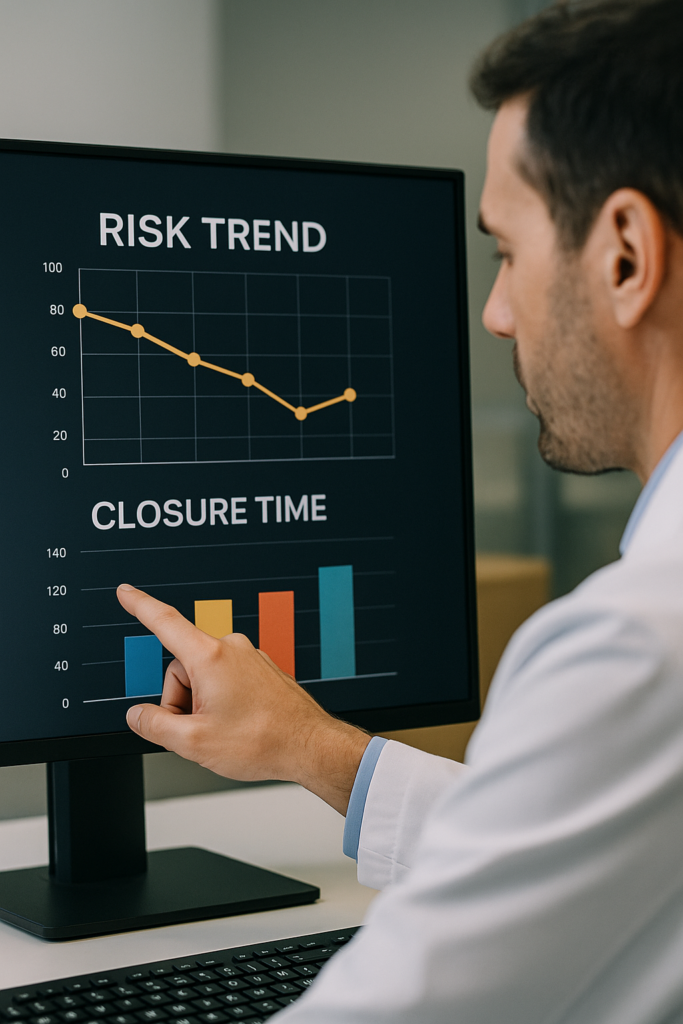
Key Metrics to Monitor in GMP Change Control
Average Time to Closure
Long delays may signal unclear roles or training issues.
Percentage of Changes Needing Rework
High rates often point to poor initial documentation.
Audit Readiness Score
Track how many records are inspection-ready at any given time.
SOP Adherence Rate
Measures how well staff follow documented procedures.
Cross-Department Collaboration Score
Based on how often approvals involve all necessary functions.
Tracking these metrics provides early warnings before problems escalate. Use them to drive training, adjust SOPs, or streamline workflows.
Continuous Learning Is the Key to Long-Term Success
In GMP environments, one-time training doesn’t cut it. New regulations, emerging technologies, and staff turnover make ongoing learning essential. Change control must evolve with your business. That’s why continuous learning programs matter so much.
Create structured plans that include annual refreshers, microlearning modules, and internal audits. Let employees own their development with access to online platforms like Pharmuni. Encourage team members to upskill—not just in change control, but across related GMP areas.
This approach fosters confidence and reduces stress during audits. Employees feel empowered to lead change requests, complete assessments, and collaborate across teams. Most importantly, it helps you build a quality culture—not just a compliance checklist.
Ready to Master GMP Compliance from A to Z?
Conclusion
GMP change control isn’t just a regulatory requirement—it’s a daily practice that protects patients, product quality, and your company’s reputation. Yet many failures happen because of one simple problem: lack of training. Whether it’s missed documentation, unclear responsibilities, or poor communication, these gaps can cost your business dearly.
Training your team isn’t a one-time task. You need an ongoing strategy that includes role-based learning, practical examples, digital tools, and regular evaluations. Empower your team to understand the full lifecycle of change—from initiation to closure. Teach them how to assess risk, collaborate across departments, and follow documented procedures.
The good news? You don’t have to do it alone. Pharmuni offers over 40 Pharma-focused courses, expert guidance, and tools like our Career Path platform to help every team member grow. With the right training, your team becomes not only compliant—but proactive, efficient, and audit-ready.
References:
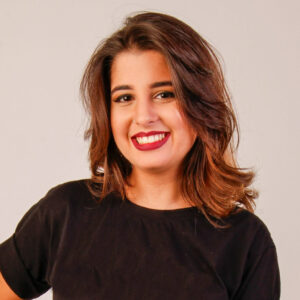
Stephanie Männicke
Digital Marketing Especialist at Zamann Pharma Support, brings 8 years of experience in Corporate and Digital Communication. Specializing in Digital Marketing and Content Creation, Stephanie is currently focused on creating strategic content for Pharmuni's networks, especially content on topics such as recruitment, onboarding and employer branding. Outside of work, Stephanie is a mum, a crocheter and a movie fan. An avid reader and in search of expanding her knowledge, Stephanie is always looking for ways to innovate communication in the digital environment and connect people in a genuine way.
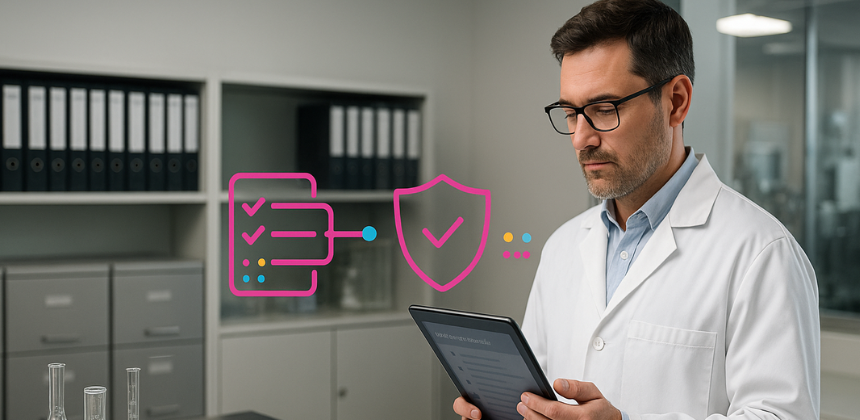
GMP Audit Checklist: Pass Your Next Inspection With Confidence
Use this gmp audit checklist to see if you would pass today. Run a 10-minute self-test, verify evidence, and prioritize fixes. Then follow 30- and 90-day plans to strengthen data integrity, CAPA, Annex 1, training, and documentation. Build proof that convinces auditors, reduces risk, and keeps your site inspection-ready year-round.
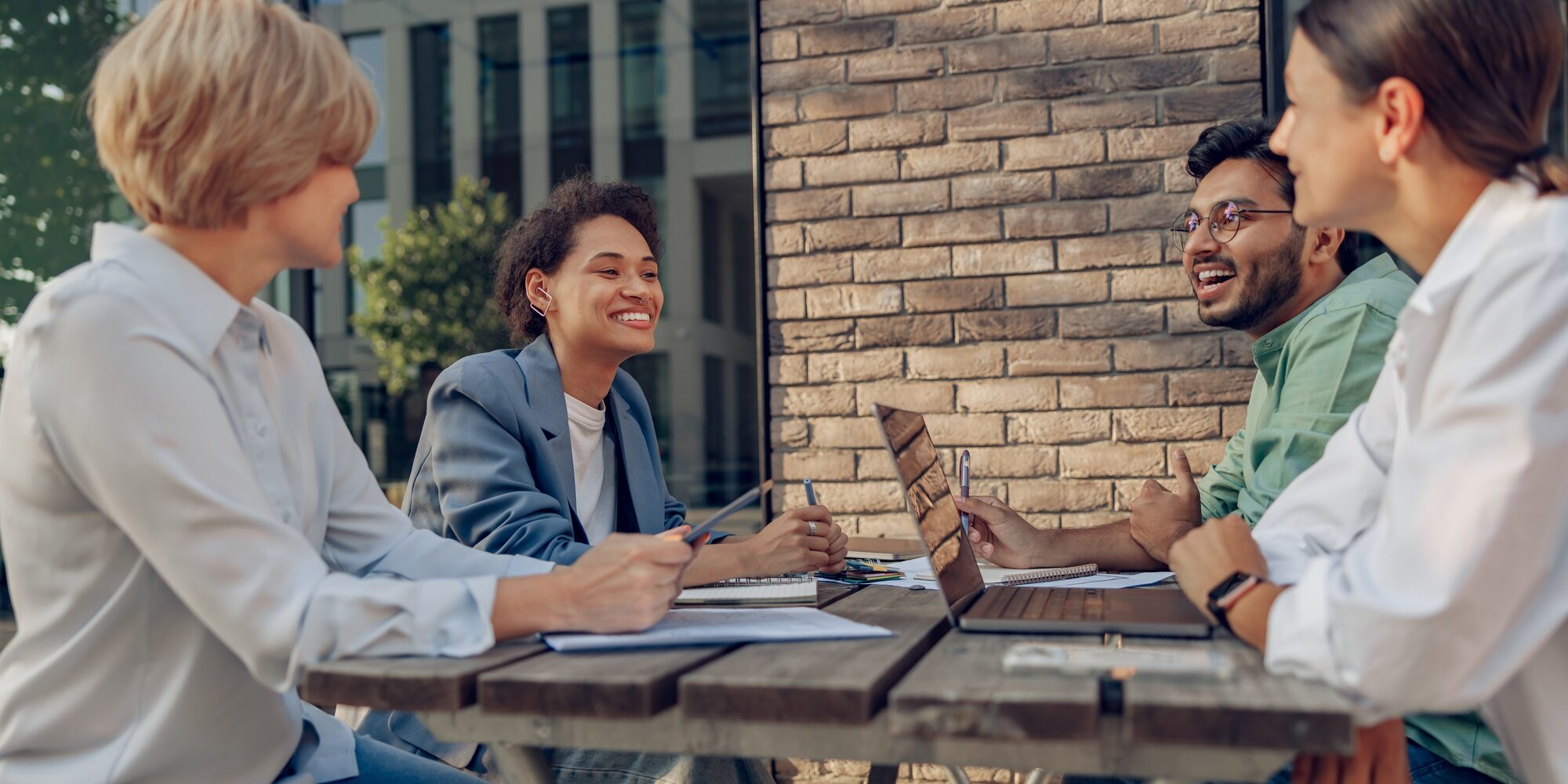
Pharma Sales Secrets to Skyrocket Success
Pharma sales is more than just selling medications. It combines science, strategy, and relationship building. Whether you’re starting out or refining your approach, this guide gives you practical tools, career insights, and tips to succeed in today’s competitive pharmaceutical sales industry.
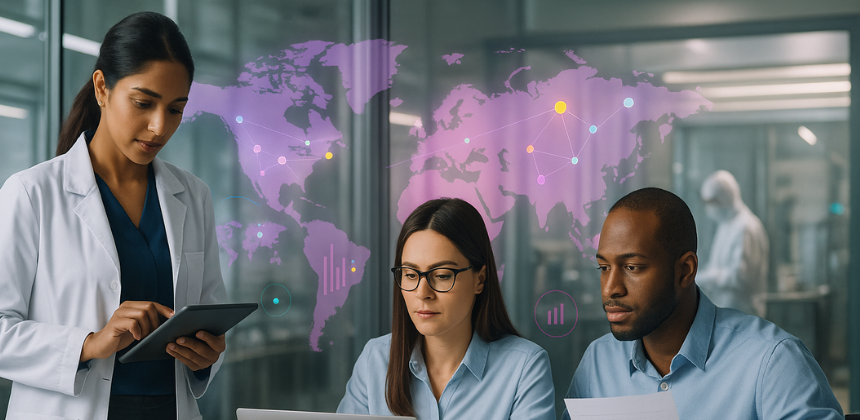
Pharma Job Market Trends: What’s Hot Now
Pharma job market trends show sustained growth across quality, regulatory affairs, pharmacovigilance, and data. New modalities, including cell and gene therapy, expand validation and aseptic roles quickly. Meanwhile, digital tools reshape trials, manufacturing, and safety reporting. Therefore, candidates who blend science, GxP, and analytics win more interviews.