Sterile manufacturing is a critical process in the pharmaceutical and healthcare industries. Ensuring product sterility protects patients from harmful contaminants and maintains product integrity. Companies must follow strict guidelines to uphold high standards.
In this article, we will explore the top considerations for sterile manufacturing practices, providing actionable insights and valuable information.
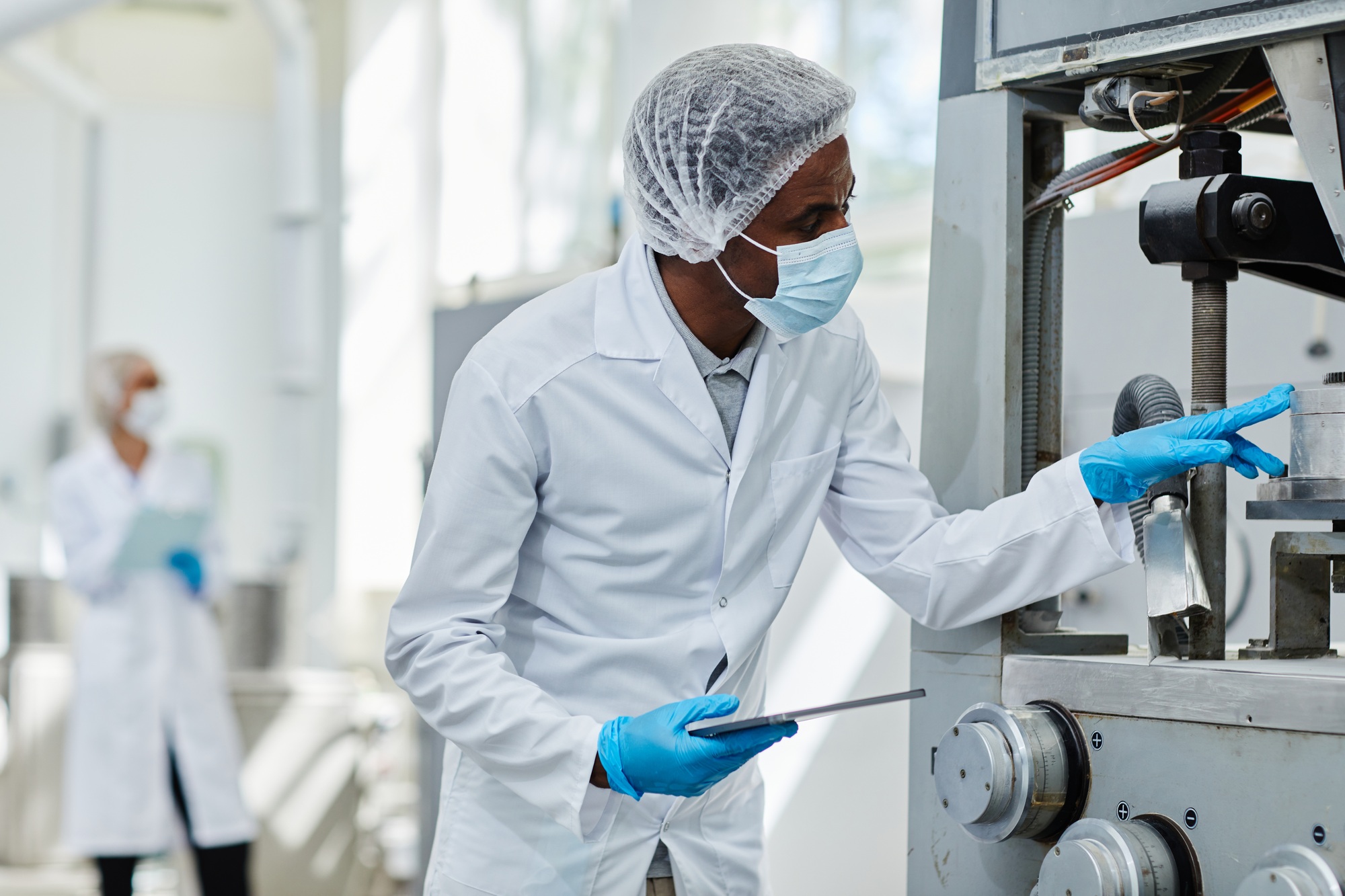
Mastering the Basics of Sterile Manufacturing
Sterile manufacturing is the production of products that are free from microorganisms. This involves controlling environmental factors, materials, and procedures to prevent contamination. Companies engaged in sterile manufacturing must prioritize cleanliness, compliance, and monitoring.
A well-designed sterile manufacturing process begins with understanding regulatory requirements. The U.S. FDA, EMA, and WHO provide comprehensive guidelines for sterile production. Facilities must ensure all personnel receive proper training. Additionally, the right tools and equipment must be used to maintain sterility throughout production.
Ensuring product sterility also means addressing potential risks proactively. For example, isolators and Restricted Access Barrier Systems (RABS) help reduce contamination. These systems create physical barriers between operators and the product, maintaining an environment free from external contaminants. By implementing stringent protocols, manufacturers can ensure sterility during and after production. Monitoring environmental conditions such as temperature, humidity, and particulate levels plays a vital role. Automated systems offer real-time data, enabling quick responses to deviations. Moreover, risk assessments help identify vulnerabilities before issues arise.
Sign up for Introduction to GMP Annex 1 Free Course
Establishing Robust Sterile Manufacturing Foundations
A cleanroom must meet ISO classification standards to control airborne particles. Proper airflow systems, such as laminar flow hoods, maintain clean environments. Regular maintenance and validation of HVAC systems are crucial to sustain ISO compliance.
Employees should wear sterile gowns, gloves, and masks to avoid contamination. Regular hygiene training and audits help maintain awareness of cleanliness protocols.
Regular checks for particulate matter and microbial presence ensure compliance. Advanced monitoring tools like particle counters and microbial samplers enhance accuracy.
Ensure equipment and processes are validated to maintain consistency. Validation includes tests to confirm that procedures produce the expected outcomes under specified conditions.
Sterilize materials before introducing them to the production area. Use proper storage and transportation protocols to maintain sterility
Each factor plays a pivotal role in ensuring the final product remains sterile. Manufacturers must focus on these to avoid risks and achieve regulatory approval. Regular audits and process evaluations help identify gaps and areas for improvement.
The Role of Cleanroom Standards in Sterile Manufacturing
Cleanroom Design
Cleanroom design is essential for maintaining contamination control in sterile manufacturing. It ensures regulated air quality, temperature, and humidity to create a sterile environment. HEPA filters effectively remove airborne contaminants, providing consistent cleanliness. Positive air pressure pushes unfiltered air out, preventing contamination from entering critical areas. These features work together to safeguard sensitive processes and uphold high sterility standards. Additionally, proper airflow management ensures particles do not accumulate in the cleanroom. By implementing these measures, manufacturers create a controlled environment that supports product safety and compliance.
Regular inspections and maintenance schedules enhance the reliability of cleanrooms and reduce contamination risks. Operators must strictly follow gowning protocols, which include wearing sterile suits, gloves, and masks. Proper material transfer procedures also prevent harmful particles from entering the cleanroom. Routine cleaning schedules with approved disinfectants eliminate microbial threats from surfaces. These actions reinforce the sterility of the manufacturing process. Furthermore, consistent adherence to these practices protects both product integrity and patient safety. Through careful design and diligent management, cleanrooms become a cornerstone of sterile manufacturing success.
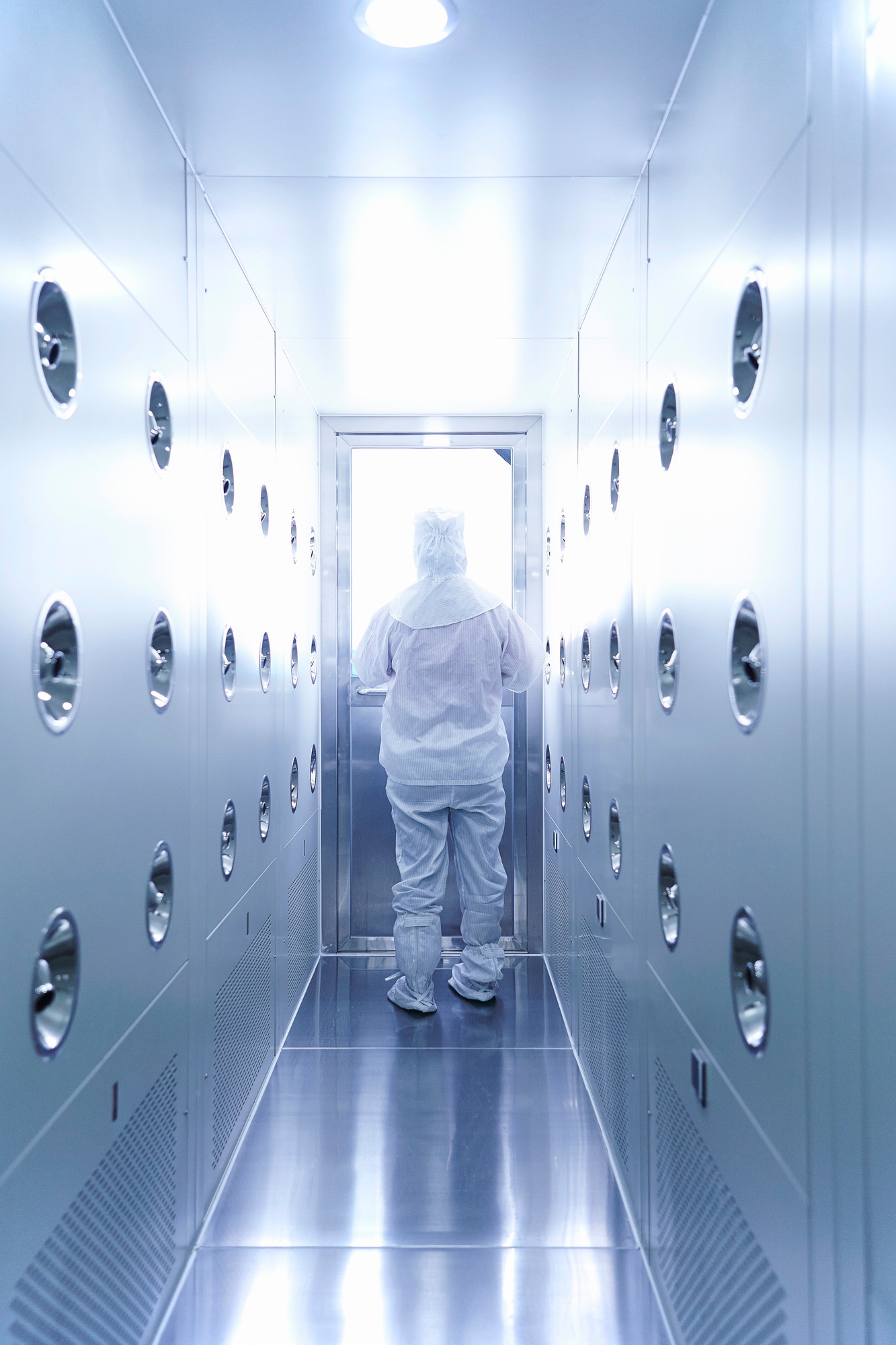
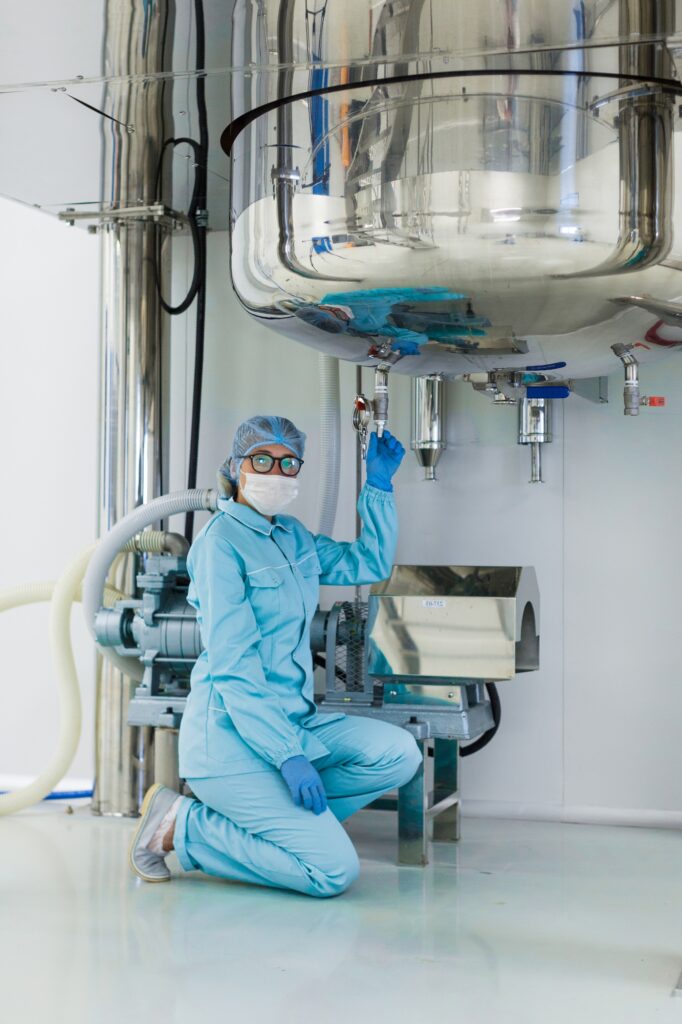
Continuous Monitoring
Continuous monitoring plays a crucial role in maintaining consistent cleanroom conditions in sterile manufacturing. Real-time monitoring systems provide immediate data on key parameters like air quality and humidity. Operators use this data to detect and address deviations before they escalate into major issues. Regular microbial and particulate testing further validates cleanroom integrity and ensures compliance with industry standards. Frequent testing also helps identify potential risks, allowing manufacturers to implement timely corrective actions. By prioritizing these practices, companies create a stable and contamination-free environment for their production processes.
Employee training programs complement monitoring efforts by ensuring staff understand and follow cleanroom protocols. Training sessions teach operators the importance of proper hygiene and sterile procedures. Employees learn how to gown correctly, handle materials safely, and navigate cleanrooms without introducing contaminants. Refresher courses reinforce these concepts and keep staff updated on regulatory changes and best practices. Regular assessments ensure employees apply these skills consistently during operations. Together, monitoring and training foster a culture of accountability and excellence. These measures maintain cleanroom efficiency while supporting high standards in sterile manufacturing.
Essential Tools and Techniques for Sterile Manufacturing
Air Filtration Systems
HEPA filters remove contaminants and maintain sterility.
Temperature Control Systems
Regulate temperature and humidity for optimal conditions.
Surface Cleaning Protocols
Use approved cleaning agents to eliminate microbes.
Equipment Placement
Arrange tools strategically to minimize movement and contamination.
Regular Testing
Perform swab and air sampling to ensure compliance.
These tools and techniques help manufacturers maintain cleanroom environments and uphold high standards of sterility.
The Power of Validation in Sterile Manufacturing
Why Validation Is a Game-Changer
Validation plays a critical role in ensuring sterile manufacturing meets strict regulatory standards. It involves rigorous testing to confirm sterility, reliability, and consistency throughout the production process. Without validation, manufacturers cannot guarantee that their processes meet compliance requirements. Validation ensures every step aligns with regulatory guidelines, protecting both product integrity and patient safety. For example, testing equipment performance ensures it functions as intended under specified conditions. By thoroughly validating processes, companies reduce risks and build confidence in their operations.
The validation process includes three essential stages: Installation Qualification (IQ), Operational Qualification (OQ), and Performance Qualification (PQ). IQ confirms that manufacturers have installed equipment correctly and according to specifications. OQ evaluates how well the equipment operates under defined parameters, ensuring optimal performance. PQ tests the equipment under real-world conditions to verify long-term consistency and reliability. Each stage addresses critical aspects of process validation, creating a robust framework for compliance.
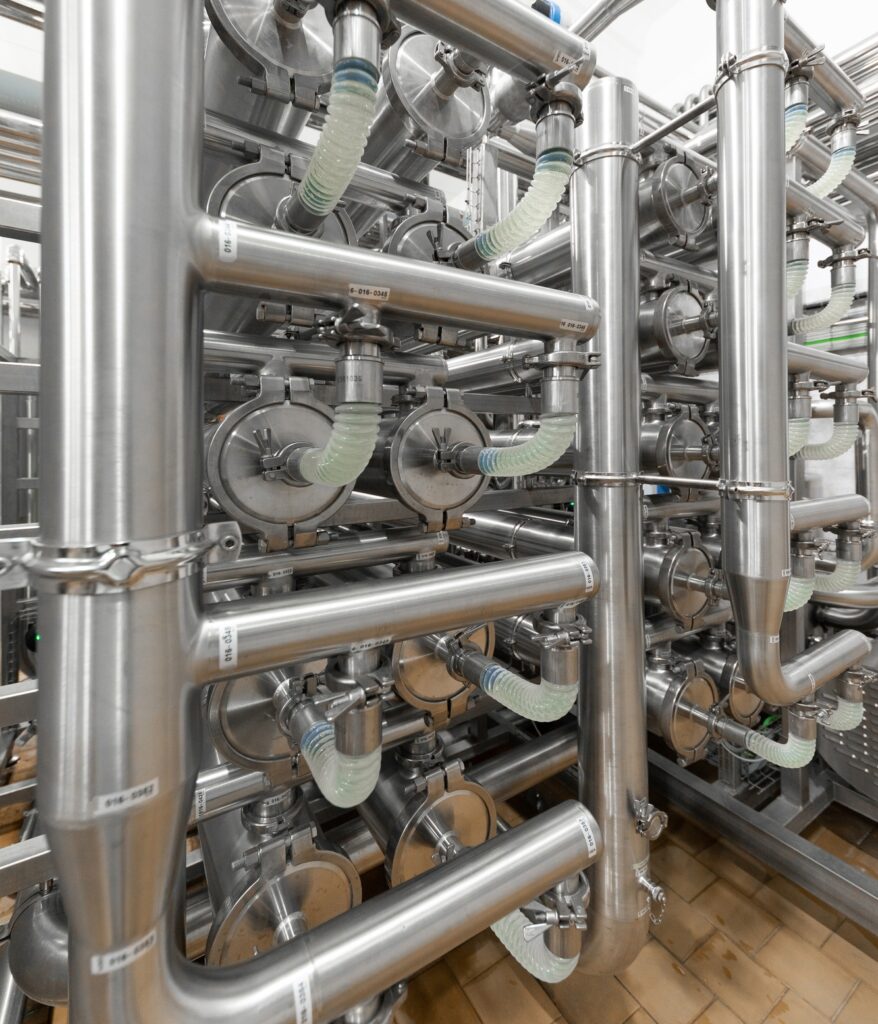
Keeping Validation Alive and Relevant
Keeping validation active and relevant ensures manufacturers maintain consistent product safety and compliance. Continuous monitoring helps track system performance and identify potential issues before they escalate. Periodic revalidation confirms that processes remain effective over time, especially as technologies evolve. Regular audits play a vital role by uncovering risks and providing actionable insights. These audits help manufacturers address gaps quickly, reducing downtime and avoiding costly errors. By staying proactive, manufacturers strengthen their commitment to quality and build trust with regulators.
Validation also requires evaluating cleaning procedures, sterilization methods, and environmental monitoring systems regularly. These assessments ensure that all protocols align with current standards and industry advancements. For example, reviewing sterilization techniques can uncover areas for optimization or necessary upgrades. Additionally, change management processes help manufacturers adapt when they introduce new equipment or alter procedures. These steps ensure changes integrate smoothly without compromising compliance. With ongoing validation efforts, manufacturers maintain high standards, protect product integrity, and support efficient operations.
Innovations Transforming Sterile Manufacturing
Innovations in cleanroom management are transforming sterile manufacturing, enhancing both efficiency and sterility. Automation and robotics have introduced precision and reliability to manufacturing processes. Automated monitoring systems track environmental conditions, such as air quality and humidity, in real time. These systems enable operators to detect deviations quickly, reducing the chance of contamination. Additionally, robotics handle repetitive tasks with consistent accuracy, minimizing human intervention and error. Closed systems, such as isolators, provide an extra layer of protection by creating physical barriers against contaminants. Together, these advanced technologies streamline operations and support higher standards of sterility.
Sustainable practices are also reshaping cleanroom maintenance, making it more eco-friendly and cost-effective. Energy-efficient HVAC systems maintain optimal conditions while reducing energy consumption. Manufacturers now use biodegradable cleaning agents that effectively sanitize without harming the environment. Waste reduction programs promote the reuse of materials and minimize disposal needs. Furthermore, incorporating recyclable materials into production processes aligns with global sustainability goals. By embracing these practices, manufacturers reduce their operational footprint and improve resource management. These innovations not only enhance sterile manufacturing but also demonstrate a commitment to environmental stewardship.
Best Practices for Cleanroom Operations
Gowning Protocol
Use sterile garments to prevent contamination.
Material Handling
Transfer materials through controlled processes.
Cleaning Schedules
Follow strict cleaning routines to maintain hygiene.
Airflow Management
Ensure proper circulation to minimize particle accumulation.
Training Programs
Reinforce cleanroom standards and compliance requirements.
These practices create a cleanroom environment that supports reliable sterile manufacturing processes.
Conclusion
Sterile manufacturing practices are essential for producing safe and effective pharmaceutical products. Cleanroom design, personnel hygiene, process validation, and emerging technologies all contribute to maintaining sterility. By understanding and implementing these considerations, manufacturers can ensure compliance, protect patients, and drive innovation in sterile production. Consistent efforts to improve processes and adapt to new trends will position companies as leaders in sterile manufacturing.
References
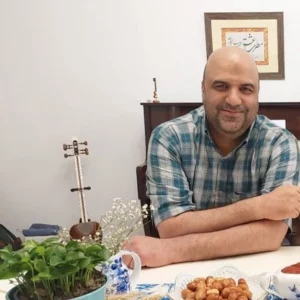
Ershad Moradi
Ershad Moradi, a Content Marketing Specialist at Zamann Pharma Support, brings 6 years of experience in the pharmaceutical industry. Specializing in pharmaceutical and medical technologies, Ershad is currently focused on expanding his knowledge in marketing and improving communication in the field. Outside of work, Ershad enjoys reading and attending industry related networks to stay up-to-date on the latest advancements. With a passion for continuous learning and growth, Ershad is always looking for new opportunities to enhance his skills and contribute to pharmaceutical industry. Connect with Ershad on Facebook for more information.
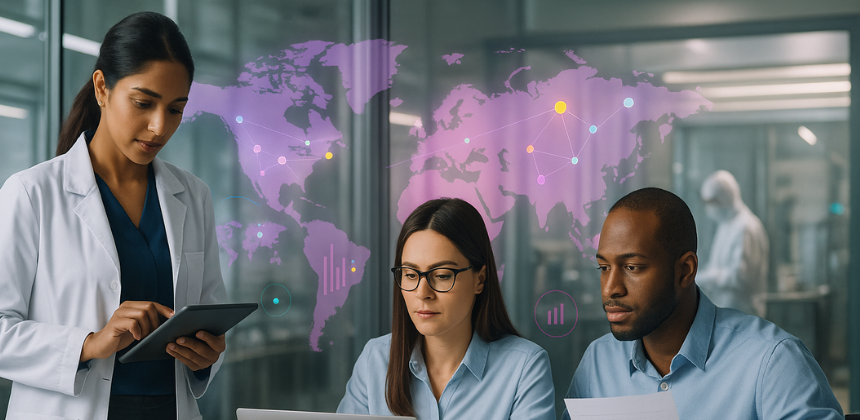
Pharma Job Market Trends: What’s Hot Now
Pharma job market trends show sustained growth across quality, regulatory affairs, pharmacovigilance, and data. New modalities, including cell and gene therapy, expand validation and aseptic roles quickly. Meanwhile, digital tools reshape trials, manufacturing, and safety reporting. Therefore, candidates who blend science, GxP, and analytics win more interviews.
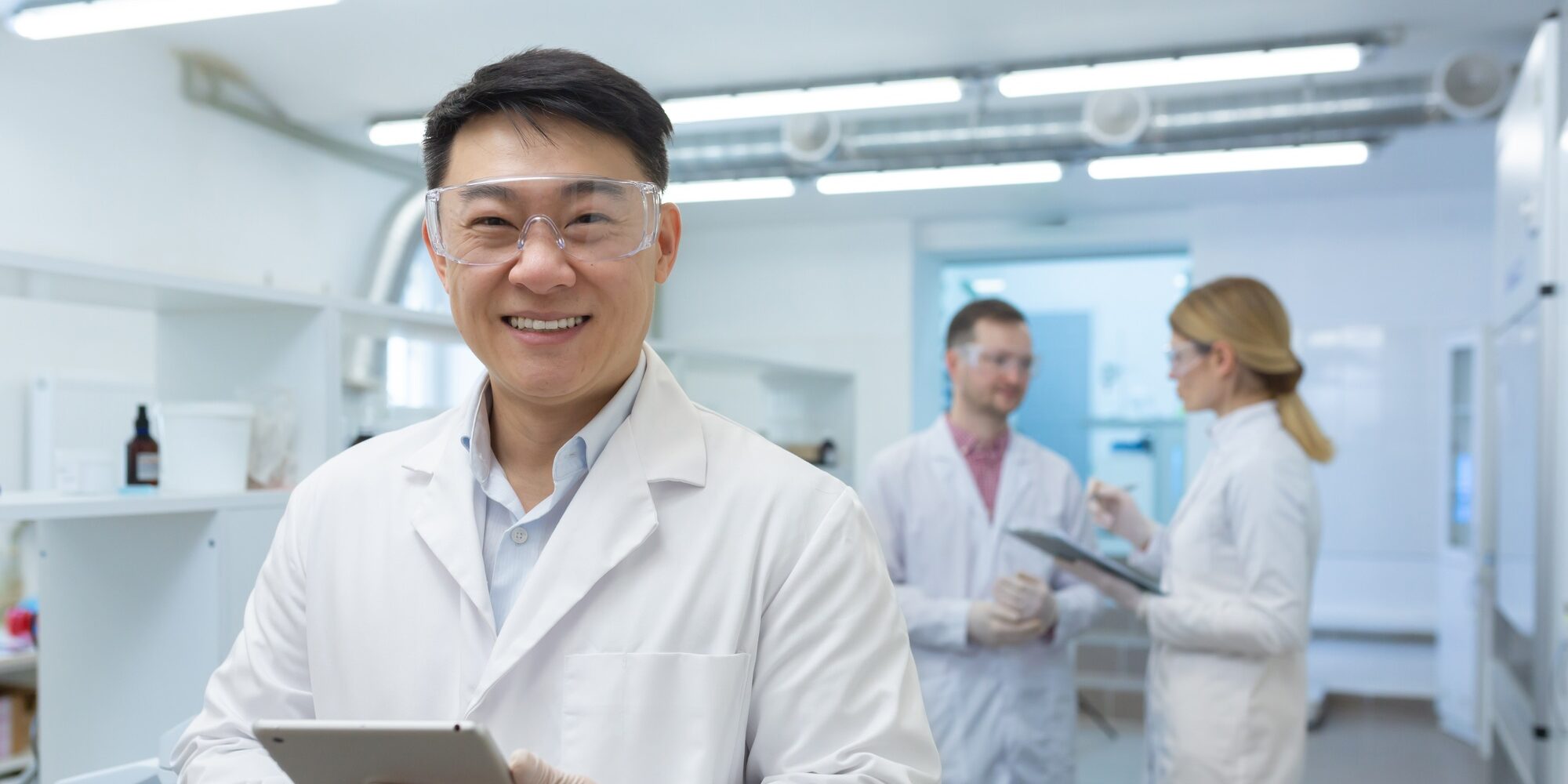
GMP Laboratory – Your Complete Guide to Compliance and Quality
This comprehensive guide explains GMP laboratories, their services, and compliance needs. Learn about cGMP, GLP labs, testing standards, and industry-specific requirements. Get actionable tips, comparisons, and insights to select the right GMP lab for your business or career growth.
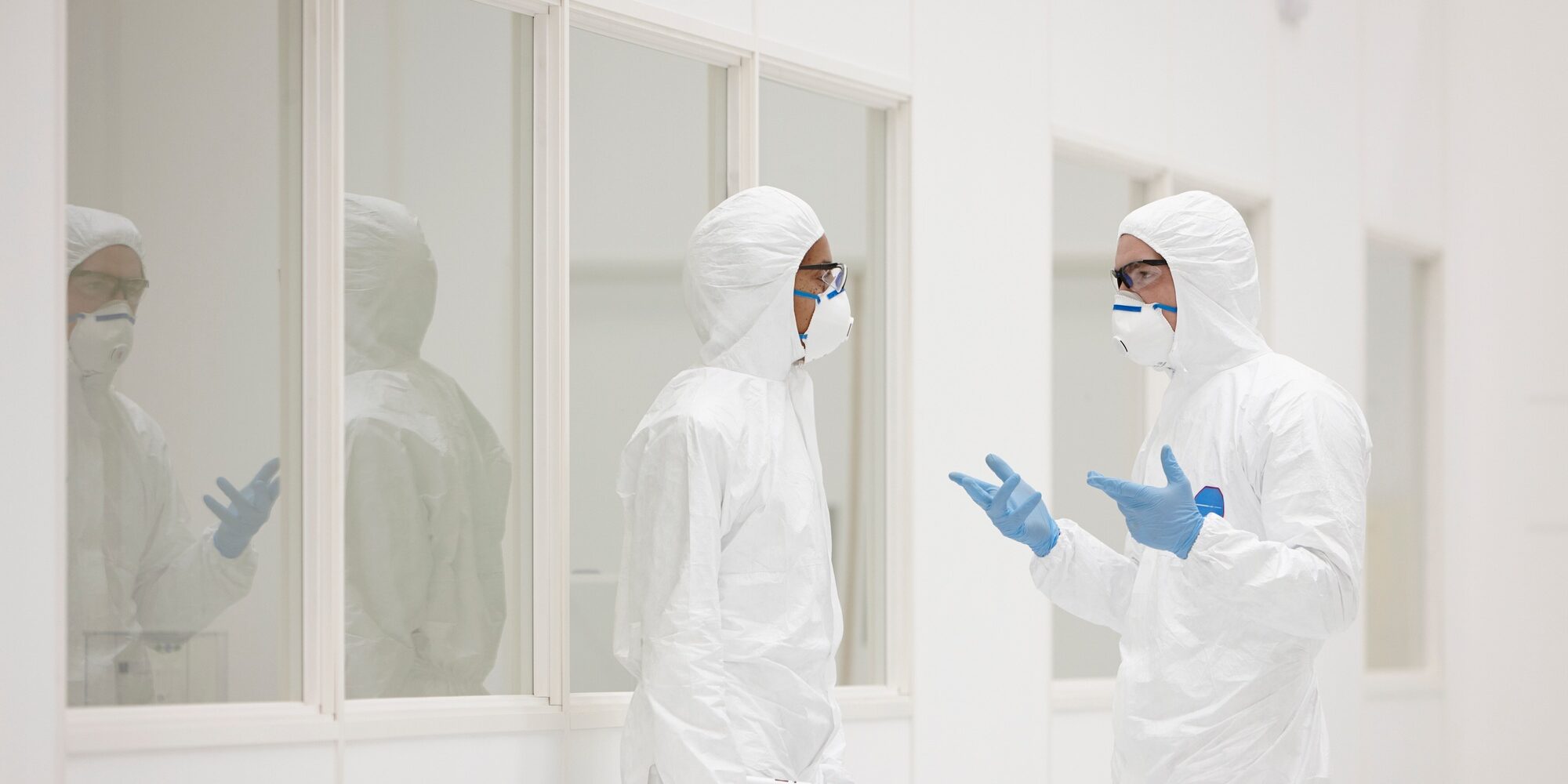
GMP Certification Cost: Reduce It with Free GMP Training
GMP certification cost can be high — but preparation reduces expenses. This guide explains costs, savings, and how Pharmuni’s free GMP course helps you get audit-ready without overspending. Access related GMP learning resources to boost compliance confidence.