Good Manufacturing Practice (GMP) standards are crucial for ensuring that pharmaceutical products are produced with the highest levels of quality and safety. Over the years, these standards have evolved to promote consistency and reliability in the pharmaceutical industry worldwide. With increasing globalization, countries have worked towards harmonizing GMP standards to ensure that products meet the same rigorous criteria across borders.
This article delves into the significance of GMP standards, their global harmonization efforts, and how they influence the pharmaceutical industry.
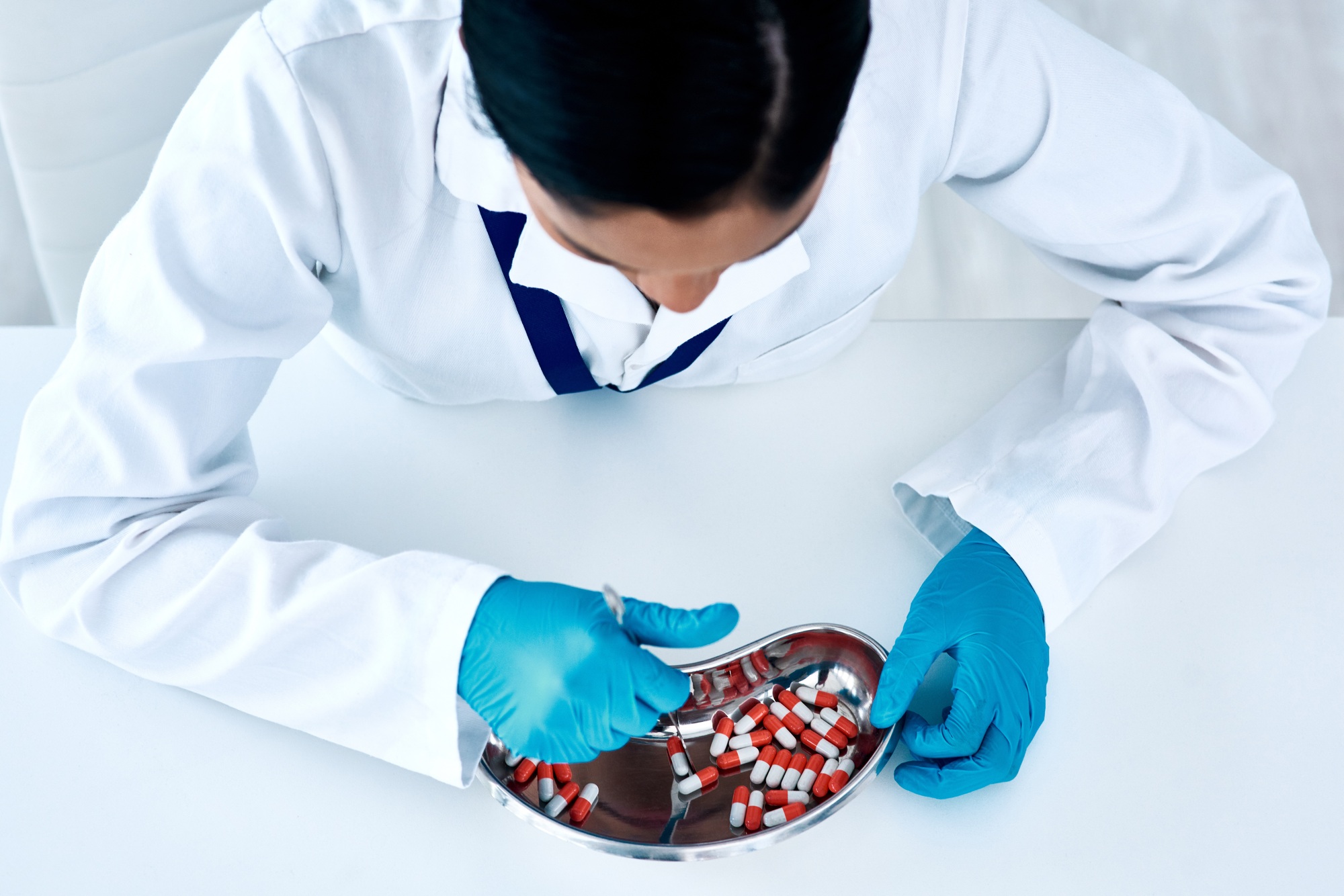
GMP Standards and Their Global Importance
Good Manufacturing Practices (GMP) standards provide a structured approach to ensuring the quality, safety, and efficacy of pharmaceutical products.
These standards guide manufacturers at every stage, from sourcing raw materials to packaging the final product. By following GMP guidelines, manufacturers can prevent contamination, minimize errors, and guarantee that each batch meets the required specifications. GMP standards also help ensure accurate labeling, reducing the risk of misinformation and potential health hazards. As a result, the public can trust that pharmaceutical products are safe, effective, and consistent.
The global importance of GMP standards continues to grow as pharmaceutical trade expands. International markets demand higher consistency in product quality, making GMP harmonization essential. Harmonizing GMP standards allows for the smooth movement of pharmaceutical products across borders without additional regulatory delays. This alignment reduces manufacturing inconsistencies and regulatory burdens, making it easier for companies to comply with different countries’ requirements. Moreover, harmonization promotes better health outcomes by ensuring that all products meet the same high standards, regardless of where they are manufactured.
Sign up for Introduction to Good Manufacturing Practices (GMP) Free Course
Principles of GMP Standards in the Context of Global Harmonization
The global harmonization of Good Manufacturing Practices (GMP) standards aims to align regulatory requirements across different countries, ensuring consistent quality, safety, and efficacy in pharmaceutical products worldwide. The following key principles are critical to achieving this goal:
Harmonized GMP standards require the implementation of a global quality management system (QMS) that ensures consistency in manufacturing processes. A unified QMS facilitates the integration of best practices across different regions and ensures continuous monitoring, validation, and improvement of production processes to meet international quality standards.
Global GMP harmonization stresses the importance of uniform training and certification for personnel across different jurisdictions. This ensures that all personnel, regardless of location, are adequately trained to uphold GMP principles, reducing variability in knowledge and compliance levels between regions.
The global approach to GMP emphasizes the need for standardized controls on raw materials. Consistent testing and validation procedures for raw materials ensure that they meet international quality standards, thus minimizing the risk of contamination or substandard product batches, no matter where they are sourced from.
Global harmonization requires standardized documentation practices, ensuring that records of production, testing, and quality assurance are consistent and traceable across different regions. This provides transparency and facilitates the auditing process, enabling easier global trade and regulatory compliance.
Harmonized GMP guidelines ensure that facilities and equipment meet internationally recognized standards. This includes standardized requirements for cleanroom design, equipment calibration, and maintenance protocols, ensuring that facilities globally can produce pharmaceutical products of the same high quality.
With global harmonization, manufacturing processes are validated according to uniform international standards. This ensures that all production lines, regardless of location, can consistently produce products that meet predefined safety and quality specifications, contributing to global product reliability.
Harmonized GMP standards require uniform cleaning and sanitation protocols to maintain high levels of hygiene across all manufacturing sites. By adhering to consistent sanitation practices worldwide, manufacturers reduce the risk of contamination, ensuring product safety across different markets.
The Impact of GMP Standards on Global Trade
Increased Efficiency in Product Approvals
Harmonized GMP standards boost the efficiency of product approvals across multiple countries. When regulatory requirements align internationally, pharmaceutical companies no longer struggle with meeting different standards in each market. This unification streamlines the approval process by allowing manufacturers to submit the same documentation, data, and compliance evidence to all regulatory agencies.
As a result, manufacturers eliminate the need for duplicative testing or inspections in each country. They can now focus their resources on meeting one set of requirements, accelerating the process and shortening approval times.
Harmonization also reduces the administrative complexity and cost of managing multiple regulatory frameworks. Pharmaceutical companies can avoid delays caused by discrepancies in local guidelines, improving communication and reducing roadblocks.
With a shared understanding of GMP standards globally, regulators gain confidence in the quality and consistency of products from different countries. This speeds up approvals and enhances the flow of goods across borders, promoting a more efficient global pharmaceutical market.
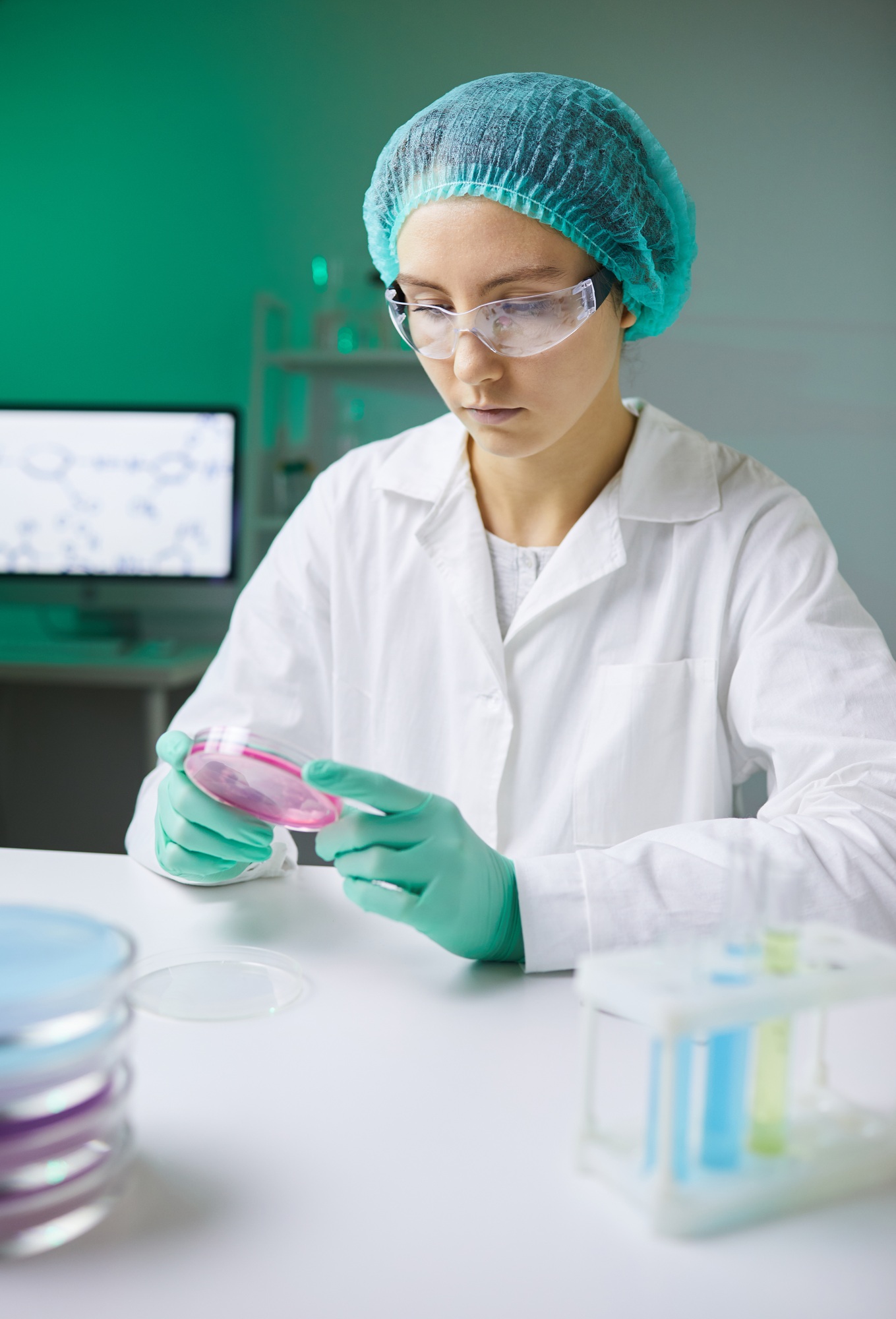
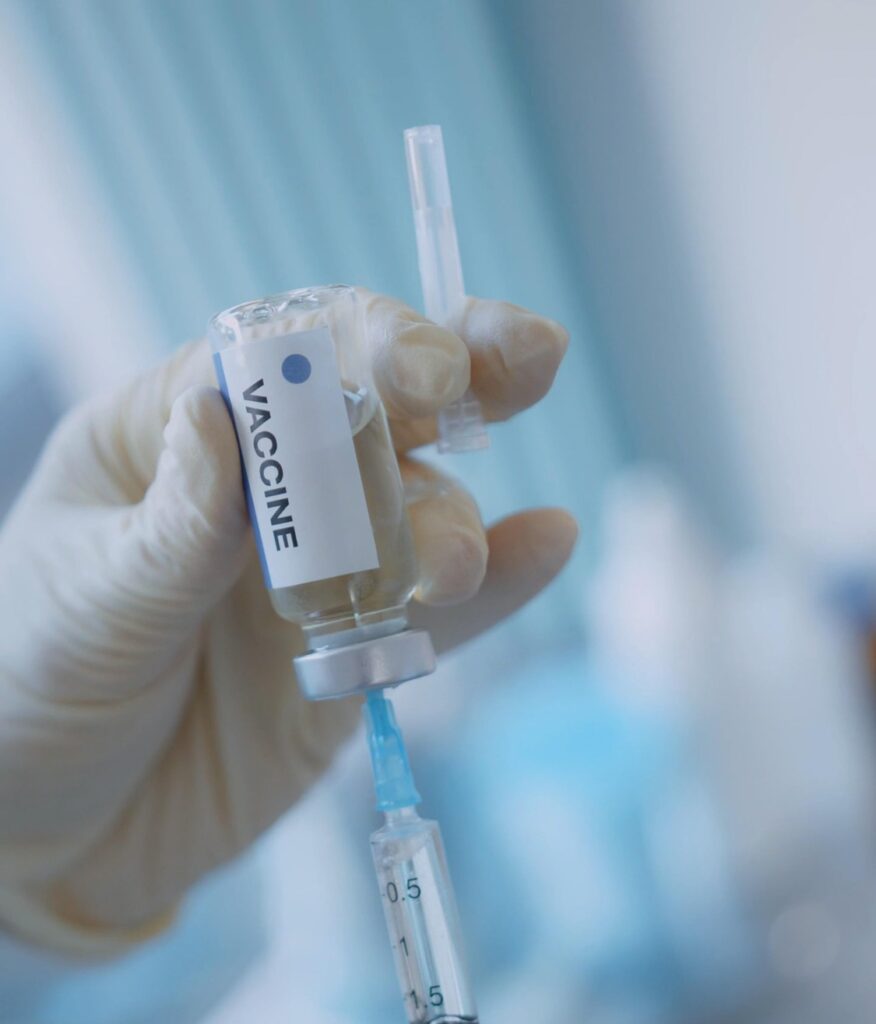
Improved Consumer Confidence
As countries align their GMP standards, the benefits extend beyond improving product safety to fostering consumer trust. Harmonized standards ensure that drugs, regardless of their manufacturing location, adhere to strict quality and safety requirements. This consistency removes uncertainty for consumers about the origin of their medications. It reassures them that every product meets the same rigorous standards, whether produced domestically or imported. When consumers trust the safety and efficacy of their medicine, they feel more confident in the pharmaceutical system. This trust helps strengthen the relationship between the public and the pharmaceutical industry, ultimately boosting industry credibility.
Moreover, harmonized GMP standards enhance transparency and reduce risks in the global pharmaceutical market. Consumers no longer worry about potential variations in product quality due to differences in regulatory requirements. When manufacturers comply with uniform GMP standards, patients know they are receiving reliable, effective treatments.
The Role of Regulatory Authorities in GMP Standards
Regulatory authorities worldwide enforce GMP standards and regulations to ensure pharmaceutical products are safe for consumption. Different countries have their own regulatory bodies, but they often align their guidelines with international organizations to harmonize GMP standards. Two key regulatory authorities include:
The U.S. Food and Drug Administration (FDA)
The FDA is one of the world’s most influential regulatory bodies, enforcing GMP standards through the 21 CFR 210/211 guidelines. It ensures that pharmaceutical manufacturers meet strict quality requirements by conducting regular inspections and audits. The FDA also works on harmonizing its standards with global regulations to facilitate smoother international trade.
European Medicines Agency (EMA)
The EMA sets GMP guidelines for pharmaceutical production across Europe. Its role in global harmonization is vital, as it collaborates with regulatory bodies worldwide, ensuring that pharmaceutical products produced in the EU meet GMP requirements. The EMA also helps influence international standards, contributing to the global harmonization of GMP practices.
World Health Organization (WHO)
The WHO plays a crucial role in global health and GMP standardization, issuing guidelines that are widely adopted by countries across the globe. Their guidelines aim to improve the quality of pharmaceutical products, particularly in developing nations, ensuring that global health challenges are addressed with safe and effective medicines.
International Council for Harmonisation (ICH)
The ICH works on harmonizing regulatory requirements across key pharmaceutical markets including the US, Europe, and Japan. By setting global guidelines on GMP standards, the ICH helps streamline regulatory procedures and improve the quality of medicines worldwide.
Key Areas of GMP Standards Beyond Production
GMP Standards in Packaging and Labeling
GMP standards cover a wide range of activities, and one critical area is packaging and labeling. Packaging materials are subjected to stringent tests to ensure they meet safety standards and do not contaminate the product. For example, packaging must be made from materials that are chemically inert, ensuring that the drug remains stable and uncontaminated during storage and transportation. Furthermore, the packaging process itself must be carefully controlled. Any changes to packaging materials or design must be validated to ensure they do not affect the quality or safety of the drug. This includes testing for potential interactions between the drug and the packaging, such as leaching of harmful chemicals or alteration of the drug’s properties.
Labeling is equally critical in the GMP framework. Labels provide essential information to consumers and healthcare providers, including dosage instructions, ingredients, expiration dates, and storage conditions. The accuracy of labeling is essential to ensure that patients take the right medication in the right dosage at the right time. Moreover, GMP standards require that labels meet local regulatory requirements, including language, format, and additional warnings.
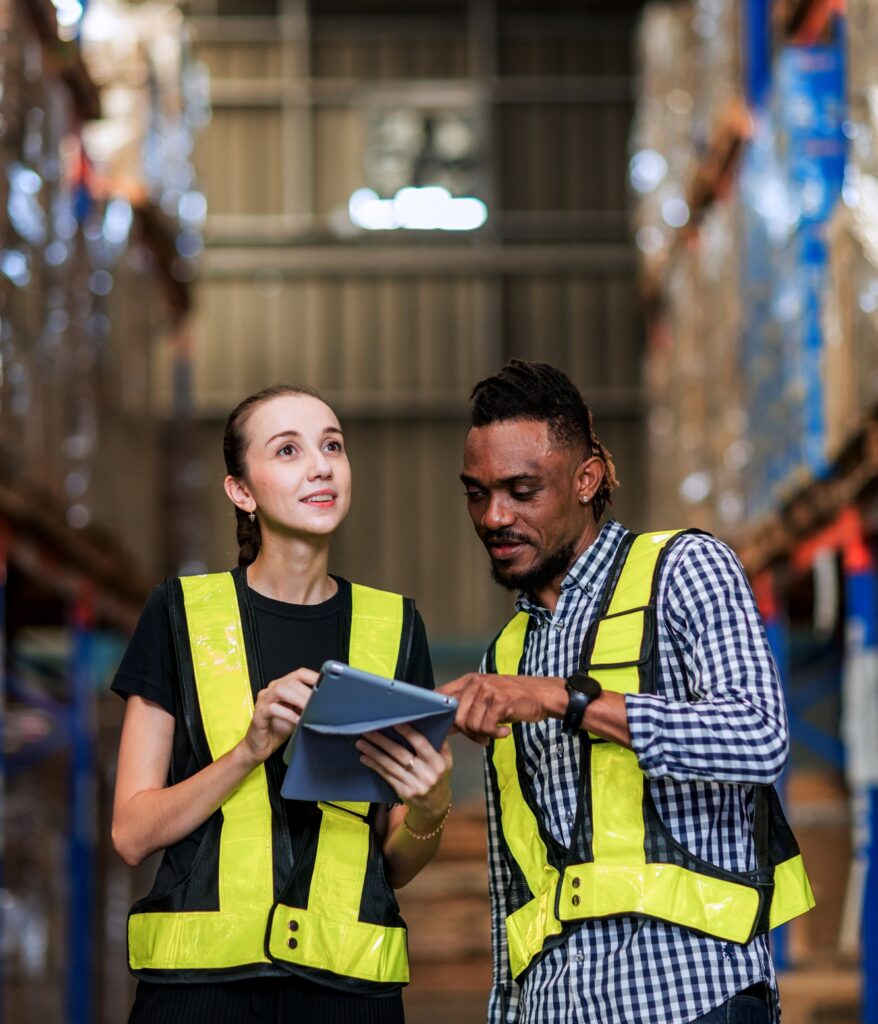
GMP Standards in Supply Chain and Distribution
GMP standards do not just apply to manufacturing, but also to the entire pharmaceutical supply chain and distribution process. The safety, efficacy, and quality of a product can be compromised if it is exposed to suboptimal conditions during storage or transit. For example, many drugs require specific temperature and humidity conditions to remain stable and effective. To comply with GMP, manufacturers must ensure that products are stored in controlled environments and transported using suitable methods that prevent exposure to extremes of temperature or contamination. In some cases, this may require specialized transport containers or refrigerated trucks for sensitive drugs like biologics or vaccines.
Additionally, GMP standards require that pharmaceutical distributors meet the same stringent standards as manufacturers. This ensures that third-party distributors, wholesalers, or retailers maintain the integrity of the product throughout the distribution process. Companies are required to perform regular audits of their distribution networks to verify that storage facilities and transport practices meet GMP requirements. They must also implement a robust traceability system to track products from manufacturer to end user, ensuring transparency in the supply chain.
What are the best practices for GMP implementation?
Implementing GMP standards requires a strategic approach, involving detailed planning, attention to every process, and ongoing monitoring. One of the first steps is to establish a clear GMP compliance strategy.
Every pharmaceutical company should have a dedicated team responsible for overseeing GMP adherence. This team should conduct regular audits and evaluations to ensure that all operations align with local and international regulations. Additionally, continuous training is essential to keep employees updated on the latest GMP guidelines and practices. By maintaining a clear compliance strategy, companies can proactively address potential issues and remain compliant with evolving regulations.
Another critical aspect of successful GMP implementation is investing in advanced technologies. Automation can greatly enhance the accuracy and efficiency of the manufacturing process. For instance, automated data collection and tracking systems help reduce errors and ensure consistent reporting. Validation software can also play a key role in maintaining the quality of production by identifying potential issues before they become problems. Furthermore, continuous monitoring and audits are essential to track GMP compliance over time. Regular audits can uncover areas for improvement, ensuring that deviations are caught early and corrected promptly. Finally, building strong relationships with suppliers ensures that raw materials meet GMP standards, supporting the overall consistency of product quality.
Challenges in Harmonizing GMP Standards Across Borders
While the harmonization of GMP standards has led to significant improvements, several challenges still exist in the pharmaceutical industry. Some of these challenges include:
Differences in Local Regulations
Some countries have local regulations that may not fully align with international GMP standards. These differences can cause delays in product approval or create additional compliance burdens for manufacturers.
Varying Interpretation of Standards
Even though regulatory bodies like the WHO and ICH work to create uniform guidelines, there can be differences in how local authorities interpret and enforce these standards. This can lead to confusion and inconsistencies in manufacturing practices.
Language Barriers
The pharmaceutical industry is global, but language differences can pose significant challenges in interpreting GMP guidelines accurately. This can result in miscommunications and errors during manufacturing or inspections.
Resource Constraints in Developing Countries
Many developing nations struggle with limited resources to implement GMP standards effectively. This results in gaps in regulatory enforcement, which can affect the quality of pharmaceutical products coming from those regions.
Conclusion
Global harmonization of GMP standards is essential for ensuring the consistent quality, safety, and efficacy of pharmaceutical products worldwide. Although challenges remain, the ongoing efforts by regulatory authorities, along with the adoption of best practices by manufacturers, are paving the way for smoother international trade and better healthcare outcomes. By aligning GMP standards globally, we can ensure that high-quality medicines reach people around the world, no matter where they are produced.
As we look to the future, continuous improvements in risk management, digital technology, and sustainability will further enhance the global pharmaceutical manufacturing landscape, ensuring that GMP standards continue to safeguard public health.
References
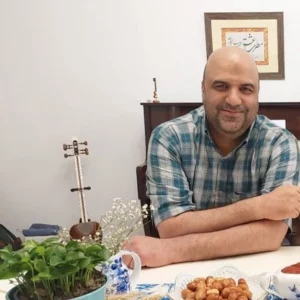
Ershad Moradi
Ershad Moradi, a Content Marketing Specialist at Zamann Pharma Support, brings 6 years of experience in the pharmaceutical industry. Specializing in pharmaceutical and medical technologies, Ershad is currently focused on expanding his knowledge in marketing and improving communication in the field. Outside of work, Ershad enjoys reading and attending industry related networks to stay up-to-date on the latest advancements. With a passion for continuous learning and growth, Ershad is always looking for new opportunities to enhance his skills and contribute to pharmaceutical industry. Connect with Ershad on Facebook for more information.
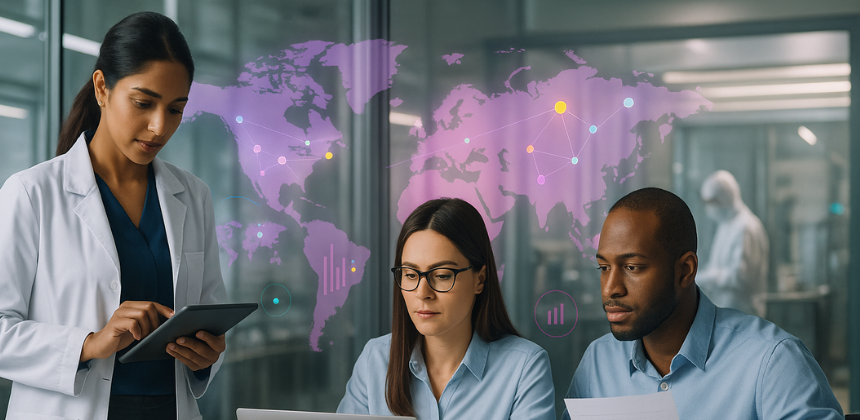
Pharma Job Market Trends: What’s Hot Now
Pharma job market trends show sustained growth across quality, regulatory affairs, pharmacovigilance, and data. New modalities, including cell and gene therapy, expand validation and aseptic roles quickly. Meanwhile, digital tools reshape trials, manufacturing, and safety reporting. Therefore, candidates who blend science, GxP, and analytics win more interviews.
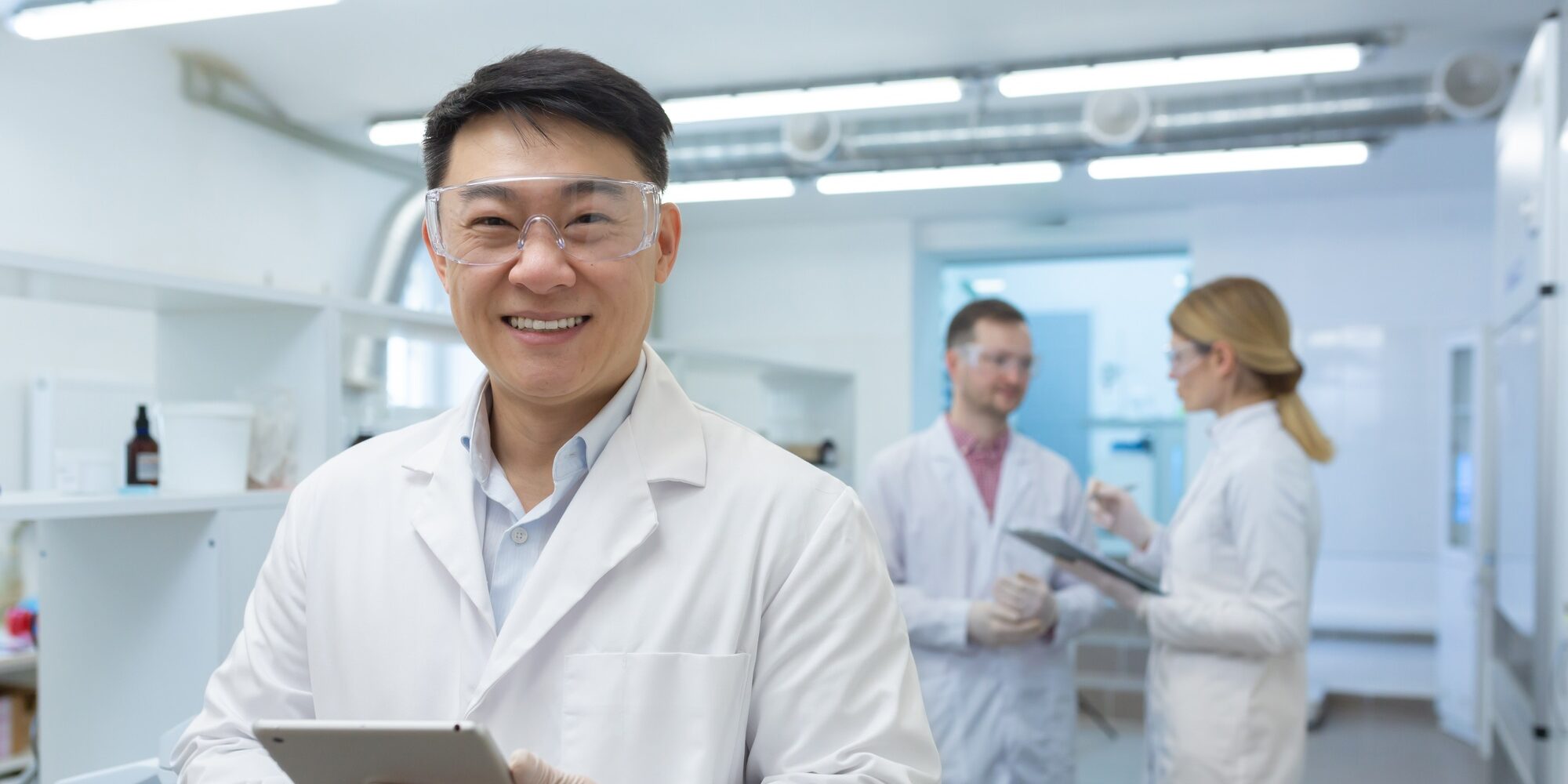
GMP Laboratory – Your Complete Guide to Compliance and Quality
This comprehensive guide explains GMP laboratories, their services, and compliance needs. Learn about cGMP, GLP labs, testing standards, and industry-specific requirements. Get actionable tips, comparisons, and insights to select the right GMP lab for your business or career growth.
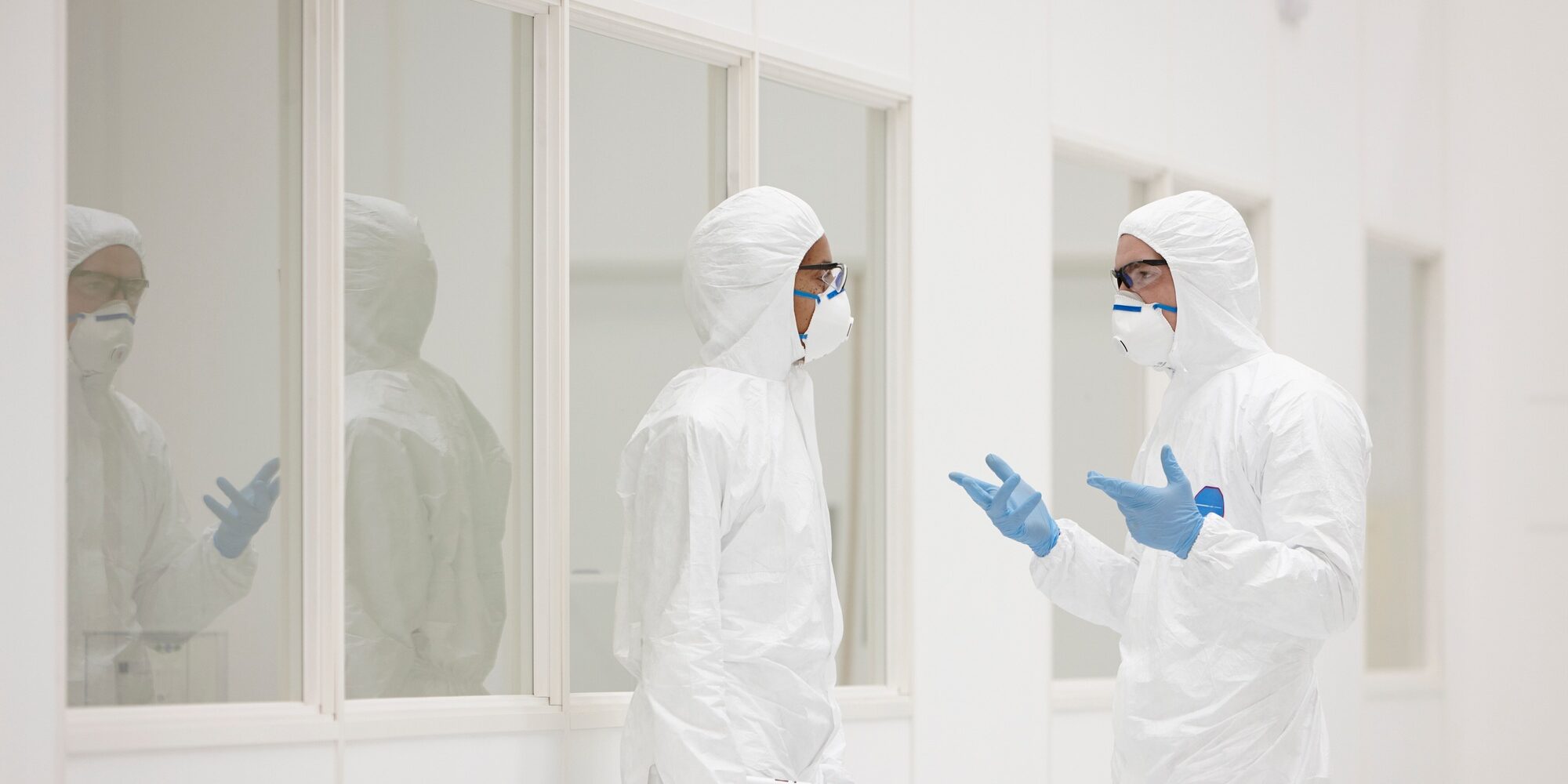
GMP Certification Cost: Reduce It with Free GMP Training
GMP certification cost can be high — but preparation reduces expenses. This guide explains costs, savings, and how Pharmuni’s free GMP course helps you get audit-ready without overspending. Access related GMP learning resources to boost compliance confidence.