Quality Management Systems (QMS) and Good Manufacturing Practices (GMP) are critical frameworks in ensuring product quality, safety, and compliance in regulated industries like pharmaceuticals and biotechnology. Understanding the connection between QMS and GMP is essential for maintaining operational excellence, adhering to regulatory requirements, and safeguarding public health.
This article explores the relationship between these systems, their shared principles, and actionable steps to integrate them effectively in your organization.
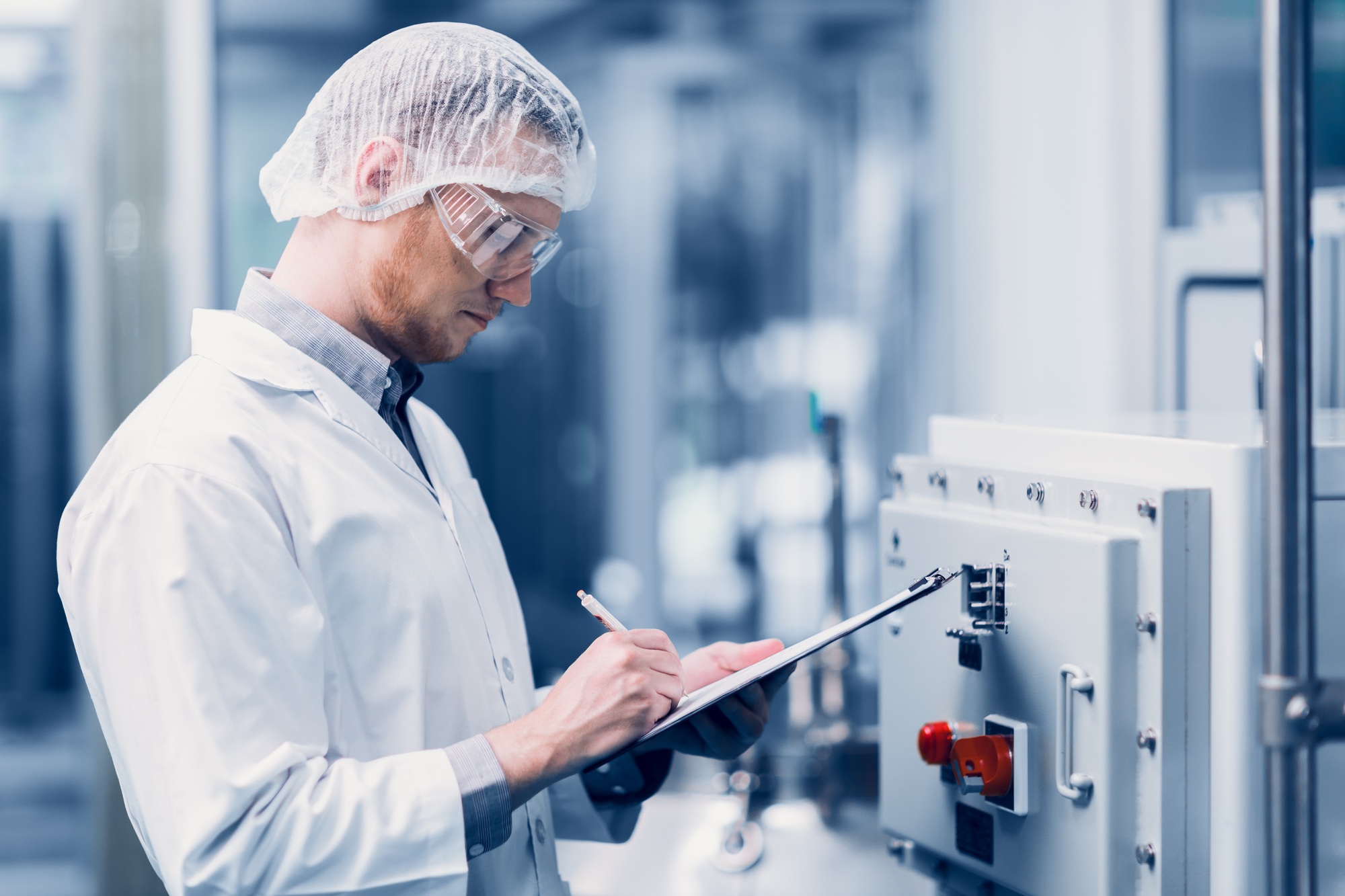
The Foundation of QMS and GMP in Regulatory Frameworks
Both QMS and GMP play essential roles in ensuring quality and safety in regulated industries. QMS provides a structured approach to managing quality across a product’s lifecycle, from concept to customer. It focuses on planning, monitoring, and improving processes to meet quality objectives consistently.
By fostering clear procedures and regular evaluations, QMS enhances efficiency and builds trust with customers. On the other hand, GMP concentrates on maintaining high standards during manufacturing. It establishes strict guidelines for equipment, personnel, and processes to prevent errors and ensure compliance. Together, QMS and GMP create a comprehensive framework for achieving regulatory excellence.
QMS drives consistency by setting clear policies and procedures that guide every quality-related activity. It emphasizes planning and monitoring to identify areas for improvement and reduce variability. With QMS, organizations can align processes with quality goals and adapt to changing requirements. Conversely, GMP ensures products meet established safety, efficacy, and quality standards. It focuses on preventing issues such as contamination and mislabeling through rigorous controls and thorough documentation. By integrating these systems, companies can streamline operations, maintain compliance, and enhance customer satisfaction. Both QMS and GMP support a proactive approach to quality, enabling businesses to meet regulatory demands effectively.
Sign up for Introduction to Good Manufacturing Practices (GMP) Free Course
Benefits of Aligning QMS and GMP
Combining QMS with GMP creates a powerful synergy that enhances operational performance and regulatory compliance. Here are some key advantages:
QMS strategies optimize GMP practices, leading to superior product quality.
Integrated systems reduce redundancy and enhance operational efficiency.
Harmonized QMS and GMP ensure readiness for audits and inspections.
Identifying gaps through both frameworks reduces production and compliance risks.
Alignment improves record accuracy and traceability.
Clear guidelines improve workforce understanding of compliance standards.
Reduced errors and waste lower operational costs.
Meeting international standards boosts market reputation.
Key Principles of QMS and GMP Integration
Aligning Objectives with Regulatory Goals
Aligning quality objectives with regulatory goals creates a strong connection between QMS and GMP. Organizations must prioritize this alignment to ensure consistent production standards and regulatory compliance. By doing so, companies can reduce errors, avoid penalties, and maintain customer trust. To achieve this, businesses should evaluate their quality objectives and compare them with current regulatory requirements. This comparison helps identify gaps and ensures both frameworks work harmoniously. Moreover, aligning objectives supports a unified approach, making it easier to meet industry demands. With clear goals, organizations can focus resources on improving efficiency and delivering quality products.
Effective integration of QMS and GMP requires clear communication, thorough training, and detailed documentation. Companies must establish transparent processes to eliminate confusion and prevent misalignment. Regular training sessions help employees understand the connection between quality objectives and regulatory expectations. Documentation also plays a critical role by providing a reference point for maintaining compliance. Businesses should look for overlapping elements within QMS and GMP to streamline processes and reduce redundancy. For instance, integrating documentation systems or combining quality checks can improve efficiency. These efforts not only simplify operations but also foster a culture of accountability.
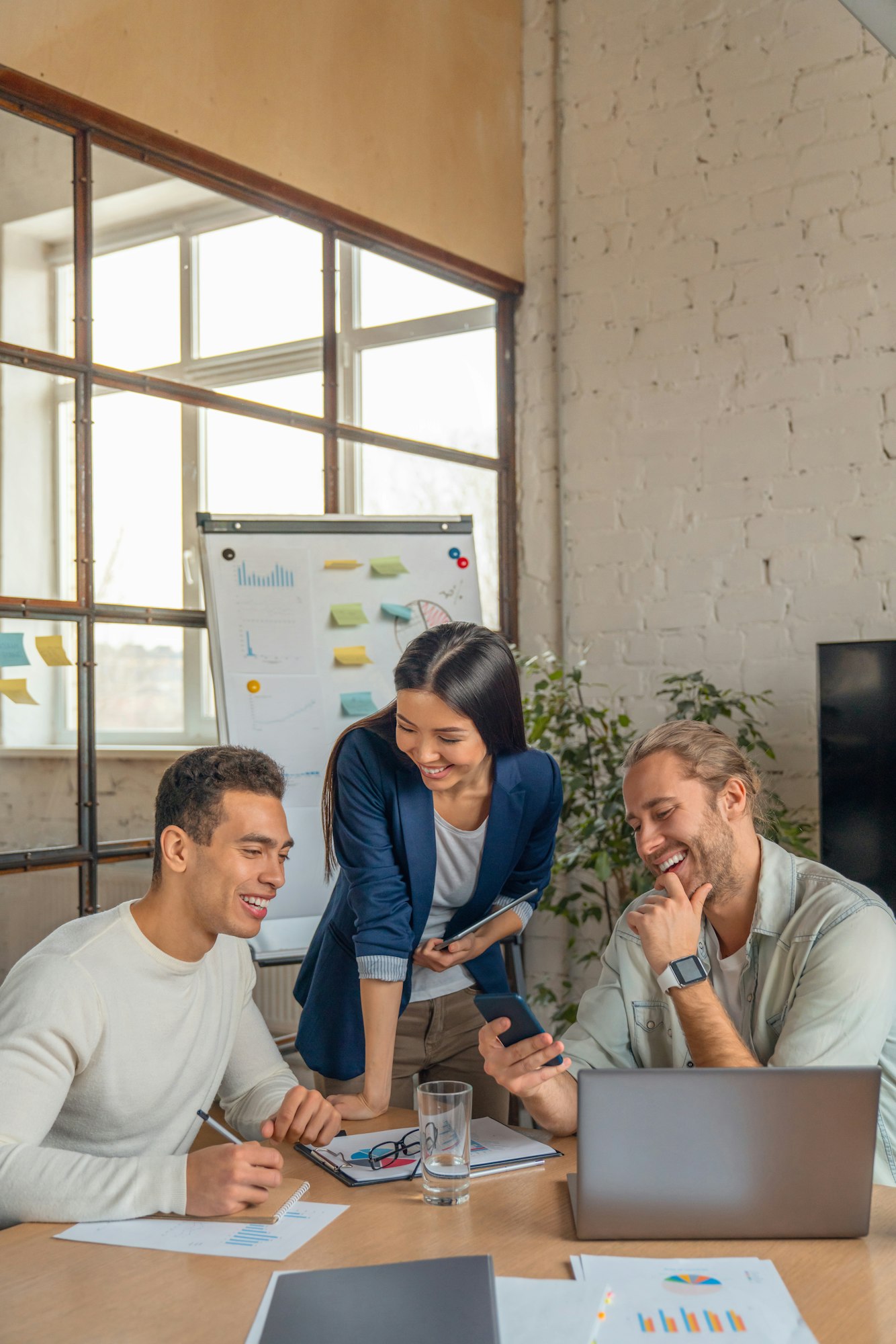
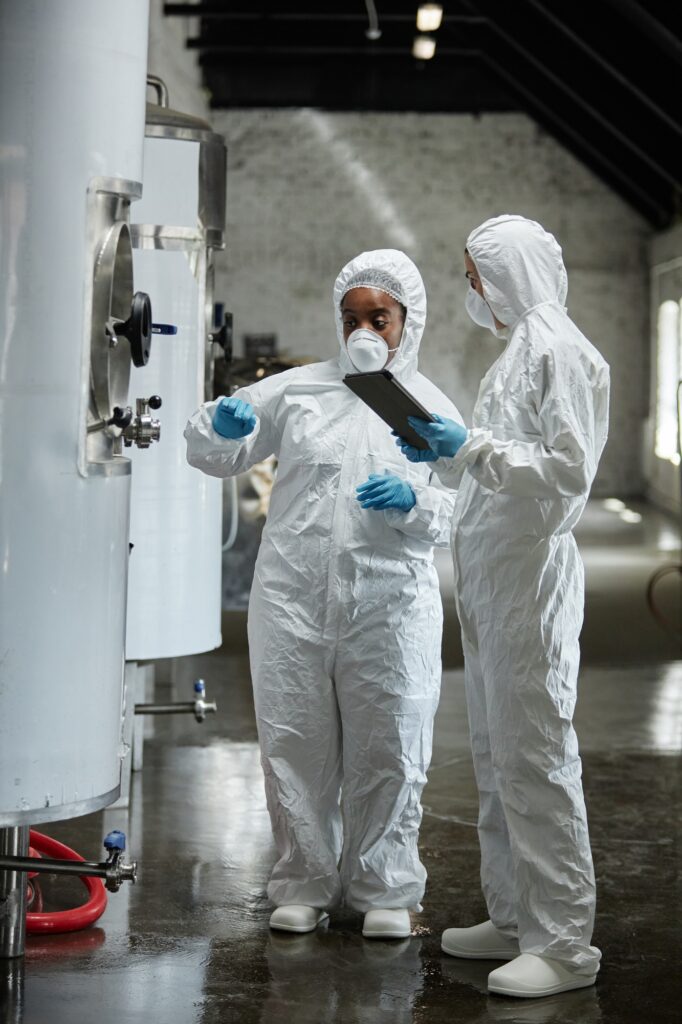
Leveraging Technology for Seamless Integration
Digital tools, like ERP systems and document management platforms, simplify integrating QMS and GMP processes. These tools streamline workflows by centralizing data and improving access to critical information. For example, ERP systems track production activities and ensure compliance with quality standards. Document management platforms help organize records, making it easier to retrieve and update them. Moreover, these systems enhance communication between departments, reducing delays and errors. With digital tools, organizations can improve efficiency and maintain consistent compliance. They also reduce manual efforts, allowing employees to focus on value-added tasks.
Automated systems play a key role in real-time monitoring and issue resolution. These tools quickly identify deviations from quality standards, minimizing potential risks. For instance, automated alerts notify teams of non-compliance issues, prompting immediate corrective actions. Real-time data tracking also helps businesses monitor trends and address recurring problems. Additionally, automation improves accuracy by eliminating human errors in data collection and analysis. This precision ensures compliance with GMP requirements and strengthens QMS processes. By using digital tools, companies can respond proactively to challenges and maintain high-quality operations. Transitioning to automated systems ultimately saves time, reduces costs, and enhances overall productivity.
Challenges in Harmonizing QMS and GMP
Overcoming Resistance to Change
Employees may resist process changes due to unfamiliarity with new requirements. Training and stakeholder involvement are crucial to gain workforce buy-in.
Navigating Complex Regulations
Regulatory landscapes vary by region, requiring organizations to adapt QMS and GMP processes accordingly. A comprehensive understanding of local and international standards helps address these complexities.
The Role of Quality Audits in QMS and GMP
Internal Audits as a Compliance Tool
Internal audits act as a powerful tool to ensure compliance with QMS and GMP standards. These audits provide a structured way to evaluate processes and identify areas needing improvement. By conducting regular audits, organizations can uncover weaknesses before they escalate into serious issues. For example, an internal audit might reveal gaps in documentation or deviations in manufacturing practices. Addressing these findings early helps prevent costly mistakes and ensures readiness for external inspections. Moreover, audits promote consistency across operations, ensuring all processes align with regulatory requirements. This proactive approach builds confidence in a company’s ability to meet quality standards.
Internal audits also foster accountability and encourage staff to take ownership of quality processes. Employees understand their roles better when audits highlight specific responsibilities and expectations. This clarity motivates teams to maintain high standards and avoid repeated errors. Additionally, audits create opportunities for open communication, allowing employees to share concerns and suggest improvements. Over time, this collaborative environment strengthens the organization’s culture of quality and compliance. Regular audits also demonstrate the company’s commitment to continual improvement, which reassures regulators and stakeholders.
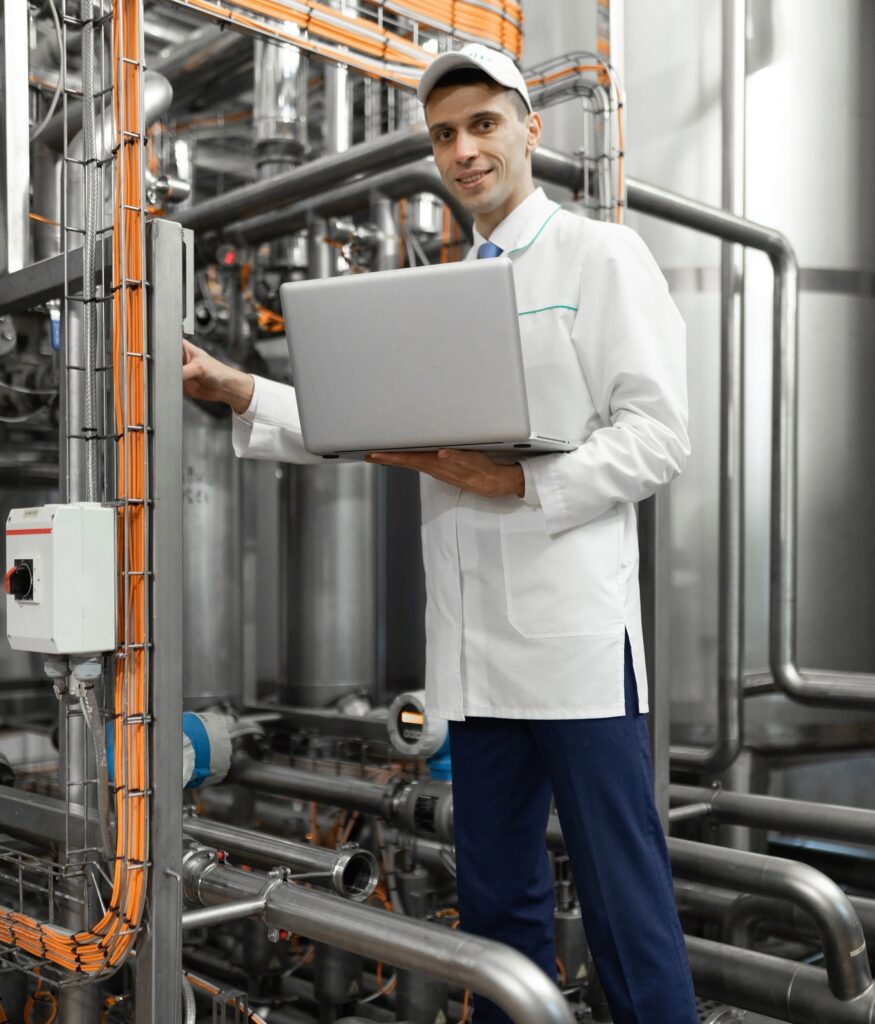
External Audits for Regulatory Readiness
External audits offer an unbiased evaluation of how well QMS and GMP align in an organization. These assessments identify gaps and highlight areas that need improvement to meet regulatory standards. By preparing for external audits, businesses can strengthen their processes and address compliance issues proactively. For instance, companies may review documentation, update procedures, and train staff before audits occur. This preparation ensures smooth evaluations and demonstrates the organization’s commitment to quality. Moreover, external audits validate the effectiveness of internal systems, providing valuable insights for continuous improvement.
Regular third-party audits build trust and enhance the company’s credibility with stakeholders. Customers, regulators, and partners feel confident when external reviews confirm adherence to high-quality standards. These audits also encourage organizations to maintain consistent practices and meet industry expectations. Additionally, third-party evaluations help businesses stay ahead of changing regulations and adapt quickly to new requirements. By acting on audit findings, companies can improve their reputation and secure a competitive advantage.
Steps to Build a Unified QMS and GMP Framework
Building a unified QMS and GMP framework requires a clear strategy and consistent execution. Start by conducting a gap analysis to assess current processes and identify misalignments between QMS and GMP. This step helps pinpoint areas needing improvement and sets the foundation for alignment. Next, develop clear documentation to ensure all quality and manufacturing activities are recorded accurately. Consistent records improve traceability and simplify compliance. Standardize procedures by creating SOPs that address the requirements of both frameworks. Uniform SOPs streamline operations and reduce confusion across teams. These initial steps create a strong base for integration and ensure a smooth transition.
Training plays a vital role in equipping staff to comply with a unified framework. Implement targeted training programs to enhance employees’ understanding of QMS and GMP processes. Adopt technology solutions, such as ERP systems, to manage processes efficiently and automate repetitive tasks. Use these tools to track progress and ensure seamless integration. Monitoring and evaluation are equally important to maintain system effectiveness. Regularly review the framework to identify improvement opportunities and address emerging challenges. By following these steps, businesses can align their QMS and GMP processes effectively. Strategic planning, clear communication, and ongoing evaluation ensure lasting success and compliance.
Training and Education for QMS and GMP Compliance
Customized Workshops
Tailor training to address specific challenges in QMS and GMP. Employees gain practical knowledge relevant to their roles.
E-Learning Platforms
Use digital tools for interactive training, ensuring flexibility and engagement.
Case Studies
Share real-world examples to illustrate successful integration. These stories motivate staff to embrace change.
Clear Certification Programs
Encourage employees to pursue certifications to deepen their expertise.
Ongoing education reinforces the importance of compliance and equips the workforce with skills to manage evolving industry demands.
Conclusion
Understanding the connection between QMS and GMP is essential for ensuring quality, safety, and compliance. Integrating these frameworks helps organizations streamline operations, reduce risks, and meet regulatory requirements efficiently. This alignment not only improves productivity but also strengthens trust with stakeholders and regulators. By adopting a unified approach, businesses can adapt to industry challenges and maintain a competitive edge. Embracing the synergy between QMS and GMP fosters continuous improvement and ensures long-term success in an ever-evolving market. Commit to this integration to achieve operational excellence and deliver consistent, high-quality outcomes.
References
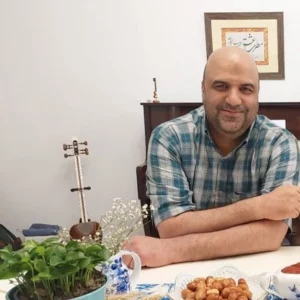
Ershad Moradi
Ershad Moradi, a Content Marketing Specialist at Zamann Pharma Support, brings 6 years of experience in the pharmaceutical industry. Specializing in pharmaceutical and medical technologies, Ershad is currently focused on expanding his knowledge in marketing and improving communication in the field. Outside of work, Ershad enjoys reading and attending industry related networks to stay up-to-date on the latest advancements. With a passion for continuous learning and growth, Ershad is always looking for new opportunities to enhance his skills and contribute to pharmaceutical industry. Connect with Ershad on Facebook for more information.
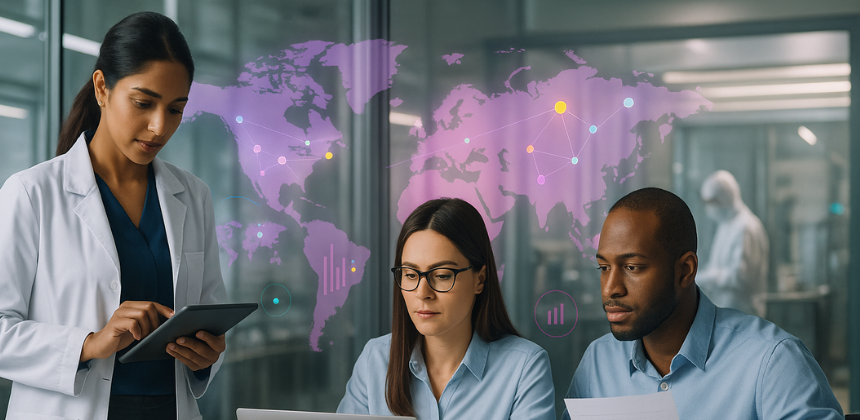
Pharma Job Market Trends: What’s Hot Now
Pharma job market trends show sustained growth across quality, regulatory affairs, pharmacovigilance, and data. New modalities, including cell and gene therapy, expand validation and aseptic roles quickly. Meanwhile, digital tools reshape trials, manufacturing, and safety reporting. Therefore, candidates who blend science, GxP, and analytics win more interviews.
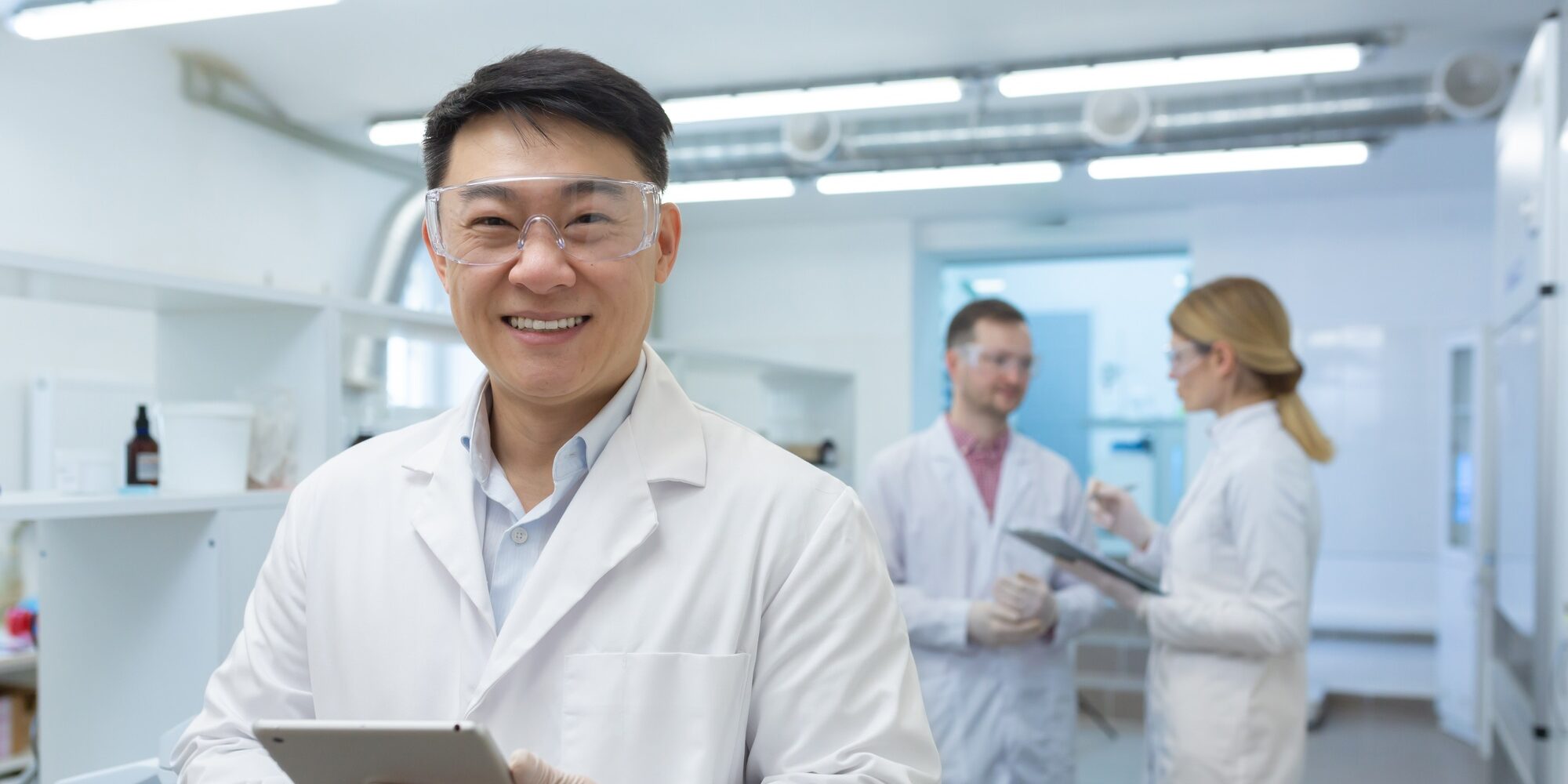
GMP Laboratory – Your Complete Guide to Compliance and Quality
This comprehensive guide explains GMP laboratories, their services, and compliance needs. Learn about cGMP, GLP labs, testing standards, and industry-specific requirements. Get actionable tips, comparisons, and insights to select the right GMP lab for your business or career growth.
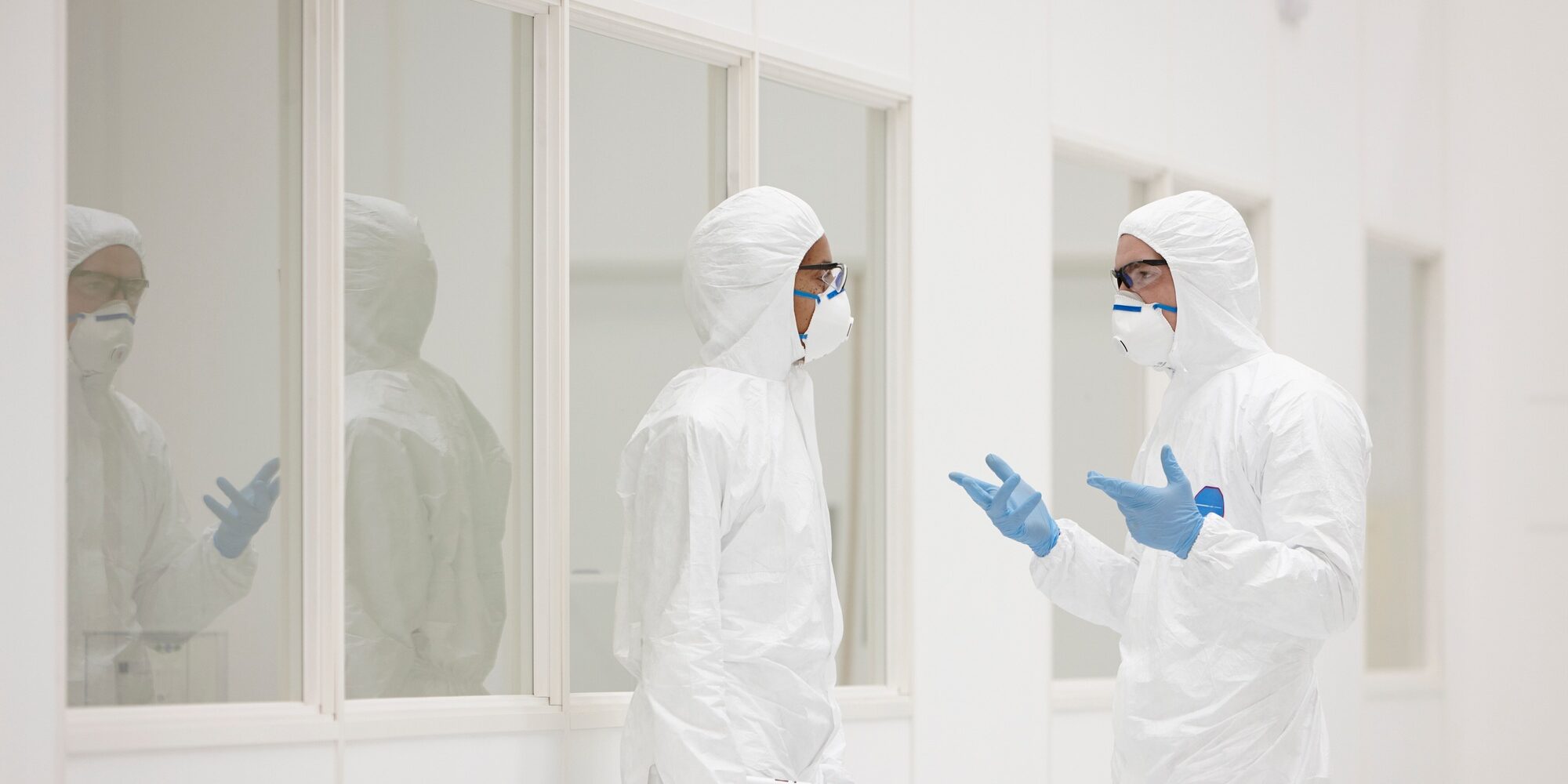
GMP Certification Cost: Reduce It with Free GMP Training
GMP certification cost can be high — but preparation reduces expenses. This guide explains costs, savings, and how Pharmuni’s free GMP course helps you get audit-ready without overspending. Access related GMP learning resources to boost compliance confidence.