The Validation Master Plan (VMP) plays a crucial role in ensuring pharmaceutical compliance with strict regulatory guidelines from agencies like the FDA, EMA, WHO, and USP. Designed to outline the strategy, scope, and specific actions for validating equipment, processes, and systems, a VMP creates a cohesive approach to regulatory adherence. By maintaining a structured VMP, pharmaceutical companies can streamline their validation activities, reduce risks, and meet global standards.
In this article, we’ll explore the significance of a VMP, its key components, and how it aligns with the latest regulatory guidelines.
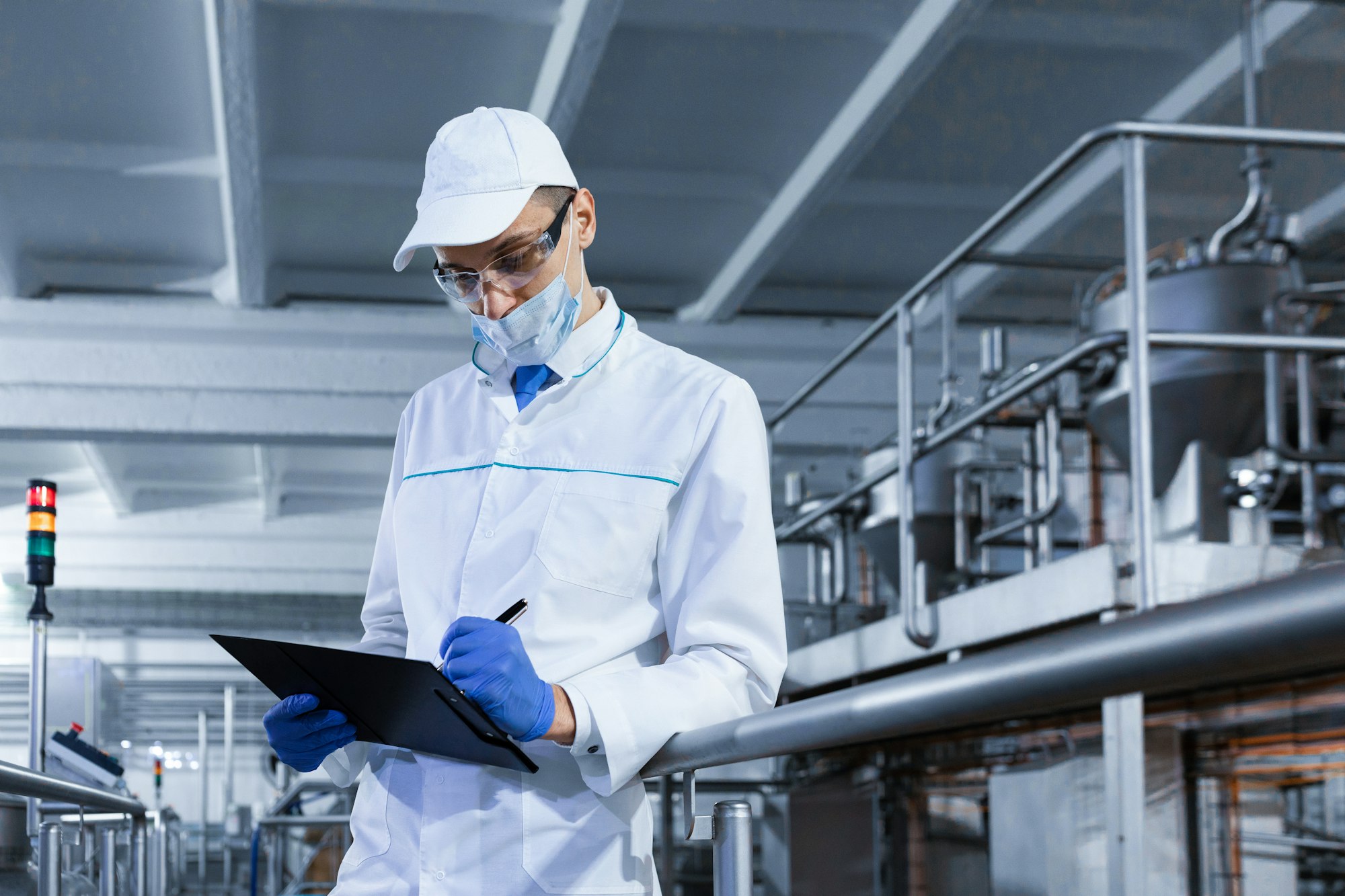
The Importance of a VMP in Pharmaceutical Compliance
A Validation Master Plan holds crucial importance in pharmaceutical compliance. It serves as a comprehensive guide that ensures all validation activities align with regulatory requirements. With strict standards from authorities like the FDA, EMA, WHO, and USP, a VMP helps pharmaceutical companies meet these demands. It outlines the processes, systems, and equipment that require validation to ensure consistent quality and safety. By following a VMP, companies minimize risks, avoid compliance gaps, and maintain high standards in manufacturing. Additionally, a Validation Master Plan brings transparency, offering clear roles and responsibilities for each team member involved in validation.
Moreover, a Validation Master Plan supports efficient operations in highly regulated environments. It enables companies to plan, execute, and review validation steps methodically, reducing costly errors. Regulatory bodies expect a Validation Master Plan to address risk management, highlighting areas needing frequent checks and updates. Through regular monitoring and adjustments, a VMP helps companies stay compliant with evolving regulatory guidelines. Importantly, it fosters a culture of accountability, ensuring all team members contribute to product safety and quality. A well-maintained VMP doesn’t just meet compliance; it enhances overall operational integrity and readiness for audits.
Sign up for GMP Device Qualification Course
Core Components of a VMP
An effective Validation Master Plan includes several essential components that work together to ensure thorough validation processes:
Outlines which areas of manufacturing the VMP covers.
Establishes key goals such as compliance, efficiency, and risk mitigation.
Defines roles and responsibilities for team members.
Details the approach for validating equipment, processes, and software.
Provides a timeline for validation activities.
Sets standards for successful validation outcomes.
Ensures proper handling of any changes.
Outlines conditions that trigger revalidation.
Regulatory Expectations for a VMP
FDA Guidance
The FDA expects companies to use the Validation Master Plan as a blueprint for reliable operations. This plan outlines how systems, processes, and equipment should function to ensure consistent quality.
By following a VMP, companies can confidently show that every aspect works as intended. Importantly, the FDA requires companies to focus on risk-based validation. This approach helps identify areas with the highest potential risks and ensures teams prioritize these issues. With this focus, companies can minimize hazards, improve quality, and maintain control over their production processes.
Moreover, the FDA’s guidance highlights a VMP’s role in supporting product safety. The plan directs validation efforts, so companies can address specific risks and prevent issues early. This proactive approach strengthens both product quality and manufacturing integrity. Through consistent adherence to VMP guidelines, companies avoid quality lapses that could impact patient safety.
The VMP also prepares companies for FDA inspections, showing they follow robust, regulated practices. Ultimately, a strong Validation Master Plan aligns with FDA expectations, keeping companies compliant and safeguarding their products.
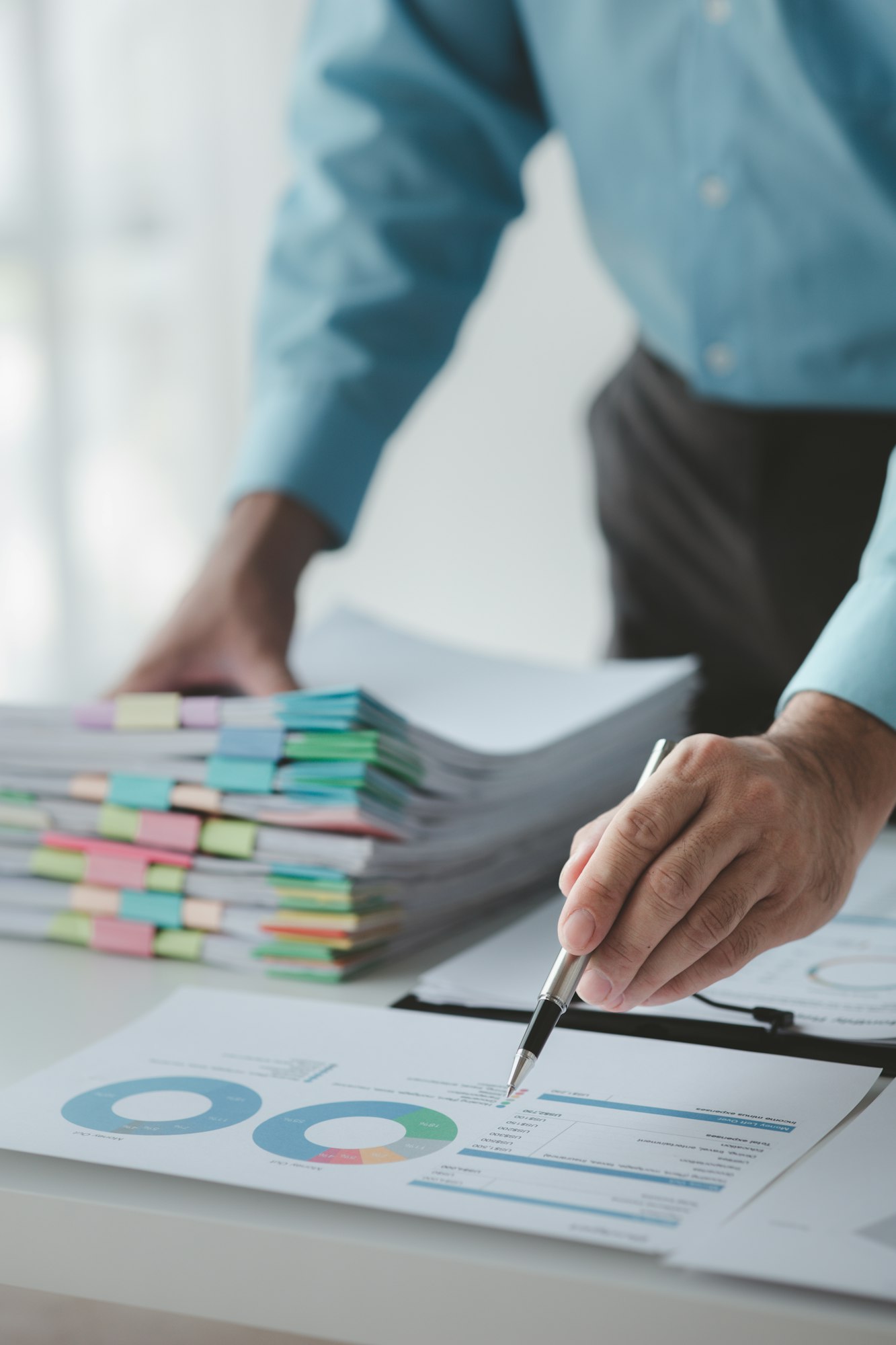
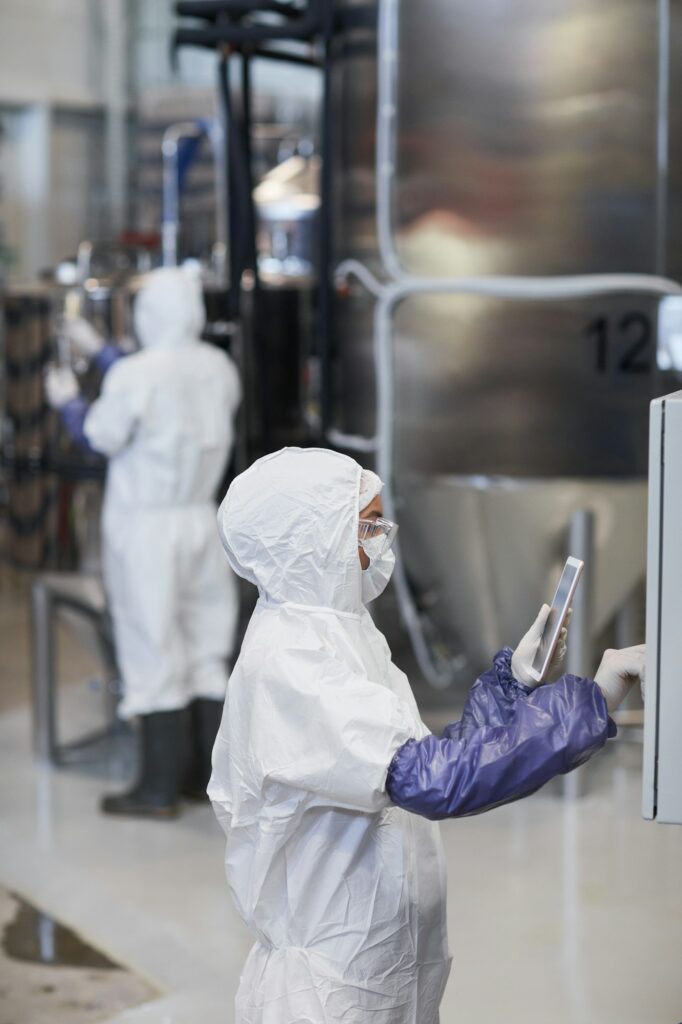
EMA Expectations
The EMA considers a Validation Master Plan essential for maintaining high standards in pharmaceutical manufacturing. It forms a vital part of a company’s Quality Management System (QMS) and ensures ongoing compliance with Good Manufacturing Practices (GMP). By including clear validation parameters, the VMP helps companies consistently meet these strict standards. The EMA also highlights the need for regular updates to the Validation Master Plan. With frequent adjustments, companies can address changes in processes or new regulatory requirements promptly. This dynamic approach keeps the VMP relevant, ensuring that all validated processes continue to work effectively.
Additionally, the EMA’s emphasis on revalidation strengthens a company’s overall quality framework. Through routine revalidation, companies confirm that their processes, systems, and equipment remain reliable and effective over time. This proactive strategy not only supports compliance but also improves operational quality and safety. Following EMA guidelines allows companies to identify potential gaps early and take corrective action quickly.
By prioritizing Validation Master Plan updates, companies also prepare better for inspections and audits. Ultimately, adhering to EMA standards with a well-maintained Validation Master Plan promotes a culture of quality, accountability, and safety.
Developing a Validation Master Plan: Key Steps
To create a robust Validation Master Plan, companies should follow a series of structured steps that ensure all essential elements are included:
Define Scope and Objectives
Begin by specifying which processes and equipment will be validated, along with clear goals.
Assign Responsibilities
Clarify the roles for each team member involved in validation activities.
Develop Validation Strategy
Outline the approach for validating different types of systems and processes.
Establish Documentation Standards
Set expectations for the documentation required at each stage.
Implement Change Control
Include procedures for managing changes in equipment or processes.
Schedule Periodic Reviews
Plan regular reviews to keep the VMP current and compliant.
Determine Revalidation Criteria
Identify when revalidation will be necessary to maintain compliance.
Implementing a VMP in Pharmaceutical Companies
Training and Awareness
Training plays a crucial role in successfully implementing a Validation Master Plan. Employees need a clear understanding of their roles in upholding validation standards. Regular training helps them stay informed about regulatory requirements and specific validation procedures. When companies prioritize training, they empower their teams to follow validation protocols accurately. This focus on training also builds awareness of the VMP’s importance, which promotes stronger compliance across all departments. As a result, companies reduce errors, prevent compliance gaps, and maintain higher quality standards.
Moreover, training creates a culture of responsibility and precision among employees. By regularly updating staff on VMP guidelines, companies help them stay aligned with evolving regulations. This consistency ensures that each team member understands current expectations and can apply them correctly. Through hands-on training sessions and refresher courses, employees gain the skills they need to handle validation tasks with confidence. Ultimately, a well-trained team drives VMP success, improves product quality, and strengthens the company’s compliance framework.
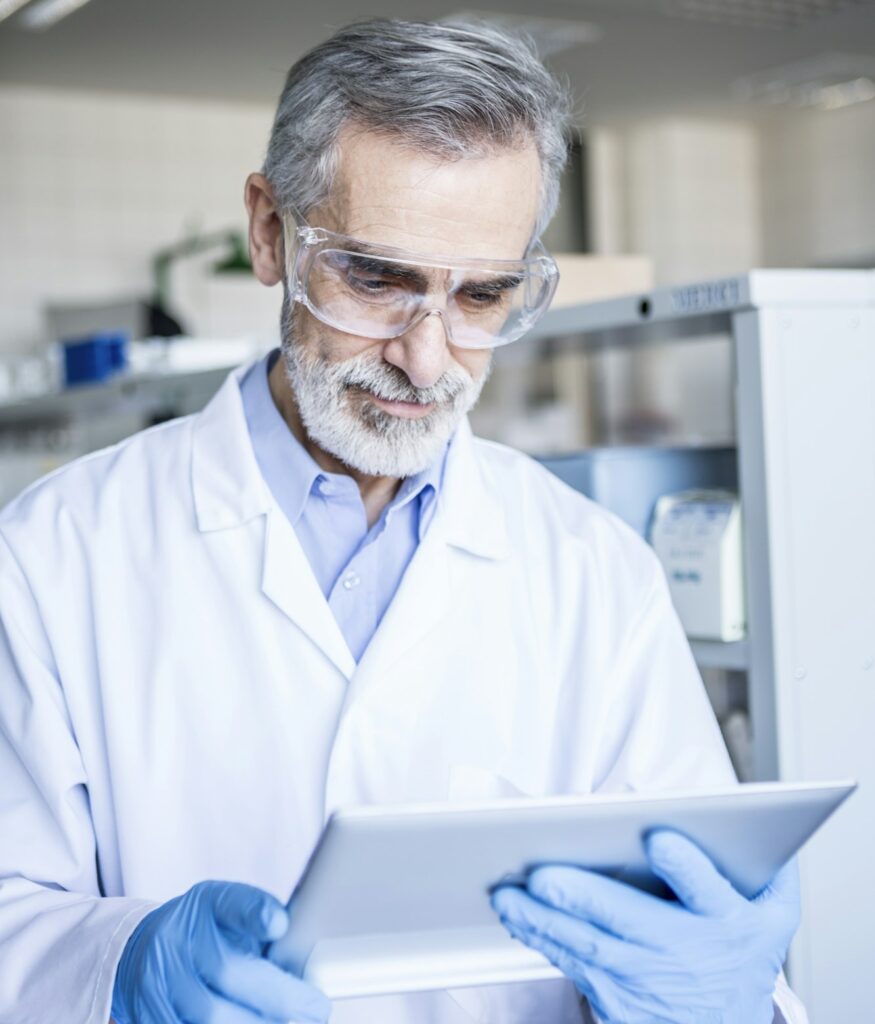
Monitoring and Continuous Improvement
A Validation Master Plan must adapt to regulatory changes and evolving operational needs. Companies should update their VMP regularly to ensure it stays aligned with current standards. Ongoing monitoring plays a vital role in this process, helping teams identify areas for improvement. Regular audits also provide valuable insights, allowing companies to detect gaps and make necessary adjustments. By continuously refining the VMP, organizations strengthen their compliance and maintain consistent quality in all validation activities.
Additionally, a commitment to continuous improvement fosters a culture of quality across the organization. When companies prioritize VMP updates, they empower their teams to meet regulatory standards confidently. This proactive approach ensures readiness for inspections and helps avoid compliance issues. Regular improvements also build a strong foundation for quality, which benefits every aspect of operations. In the long run, an evolving VMP not only supports compliance but also promotes excellence in manufacturing practices, helping the company meet both industry standards and customer expectations effectively.
Strategies for Tackling VMP Implementation Challenges
Implementing a Validation Master Plan presents several challenges that companies must manage effectively. Allocating sufficient resources for validation efforts is often difficult, yet crucial for success. Without adequate resources, companies may struggle to meet all validation requirements, risking compliance issues. Additionally, smooth cross-department coordination can be challenging but essential for effective VMP implementation. When departments work together seamlessly, they reduce miscommunication, which helps maintain validation standards and consistency. These steps strengthen the company’s ability to meet regulatory standards and maintain quality.
Furthermore, managing documentation within a VMP adds complexity that companies cannot overlook. Each validation step requires detailed records, which demand a structured approach to prevent errors. Change management also poses challenges, as companies must handle updates or adjustments in processes with clear procedures. Proper change control ensures that any modifications align with the VMP and remain compliant with regulations. Keeping up with evolving FDA, EMA, WHO, and USP guidelines is also essential, as these updates directly impact compliance. Addressing these challenges supports a strong VMP, enhances overall validation, and boosts the company’s compliance efforts.
Best Practices for an Effective VMP
Implementing the following best practices can enhance the effectiveness of a VMP:
Continuous Improvement
Regularly review and update the VMP to stay compliant with regulatory changes.
Risk-Based Approach
Focus validation efforts on high-risk areas to ensure thorough coverage.
Cross-Functional Collaboration
Foster collaboration among departments for smoother VMP implementation.
Efficient Documentation
Simplify documentation to make it easy to maintain, review, and update.
Conclusion
The Validation Master Plan is an indispensable component of any pharmaceutical company’s quality management strategy. A well-structured VMP not only facilitates regulatory compliance but also enhances operational efficiency, mitigates risks, and promotes a culture of quality. By understanding regulatory expectations and adhering to best practices, pharmaceutical companies can establish a VMP that meets FDA, EMA, WHO, and USP guidelines, safeguarding their operations and ensuring the highest standards of product quality and patient safety.
References
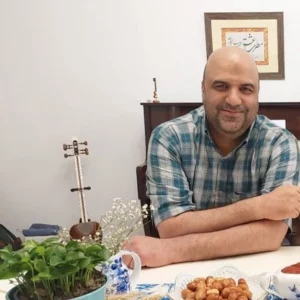
Ershad Moradi
Ershad Moradi, a Content Marketing Specialist at Zamann Pharma Support, brings 6 years of experience in the pharmaceutical industry. Specializing in pharmaceutical and medical technologies, Ershad is currently focused on expanding his knowledge in marketing and improving communication in the field. Outside of work, Ershad enjoys reading and attending industry related networks to stay up-to-date on the latest advancements. With a passion for continuous learning and growth, Ershad is always looking for new opportunities to enhance his skills and contribute to pharmaceutical industry. Connect with Ershad on Facebook for more information.

Pharmaceutical Storage: Everything You Need to Know
Pharmaceutical storage is critical for safety, compliance, and efficiency. This guide explains cold chain solutions, stability testing, and warehouse systems. You’ll also learn about regulatory requirements, ISO standards, and practical strategies to optimize pharmaceutical storage facilities and distribution networks.
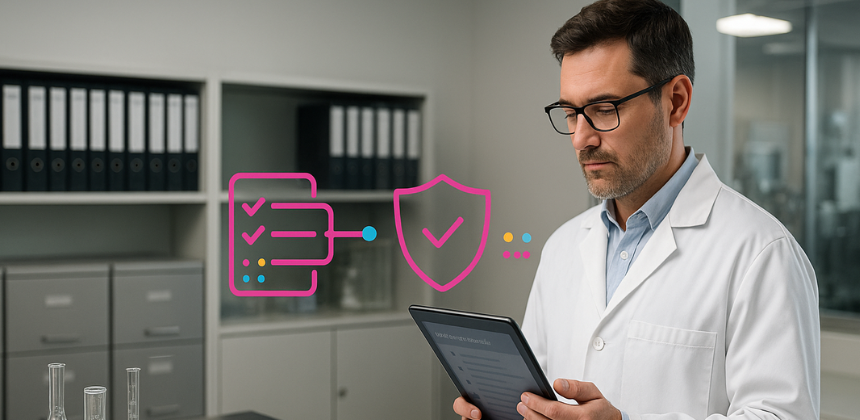
GMP Audit Checklist: Pass Your Next Inspection With Confidence
Use this gmp audit checklist to see if you would pass today. Run a 10-minute self-test, verify evidence, and prioritize fixes. Then follow 30- and 90-day plans to strengthen data integrity, CAPA, Annex 1, training, and documentation. Build proof that convinces auditors, reduces risk, and keeps your site inspection-ready year-round.
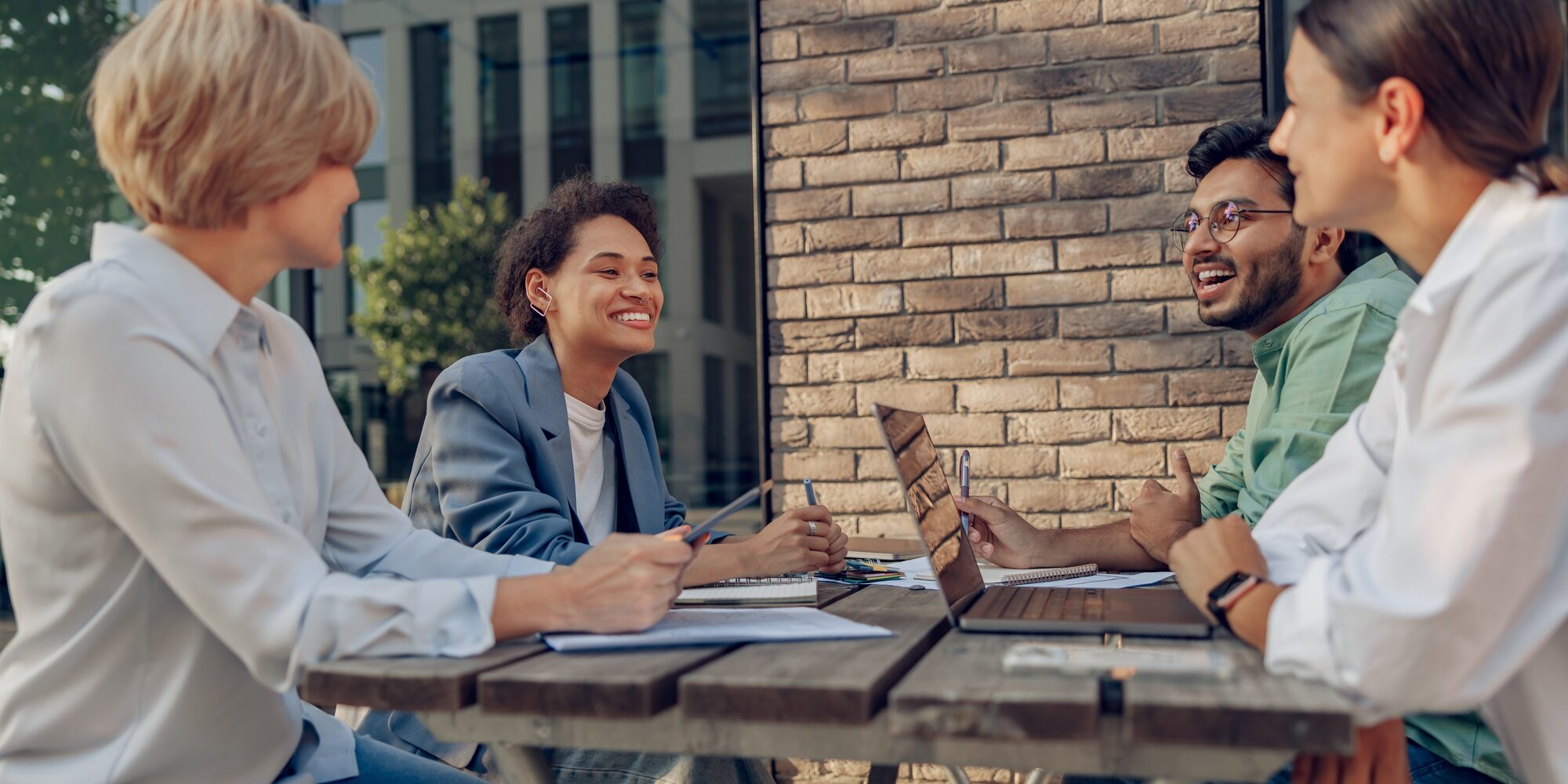
Pharma Sales Secrets to Skyrocket Success
Pharma sales is more than just selling medications. It combines science, strategy, and relationship building. Whether you’re starting out or refining your approach, this guide gives you practical tools, career insights, and tips to succeed in today’s competitive pharmaceutical sales industry.