GMP (Good Manufacturing Practice) Compliance is a regulatory requirement essential for ensuring the quality, safety, and efficacy of pharmaceutical products. For pharma professionals, understanding and implementing GMP compliance is vital to meet regulatory standards and avoid significant consequences like recalls, penalties, or reputational damage.
In this article, we will dive into the best practices for GMP compliance in the pharmaceutical industry, providing actionable steps and strategies for ensuring consistent adherence to these critical regulations.
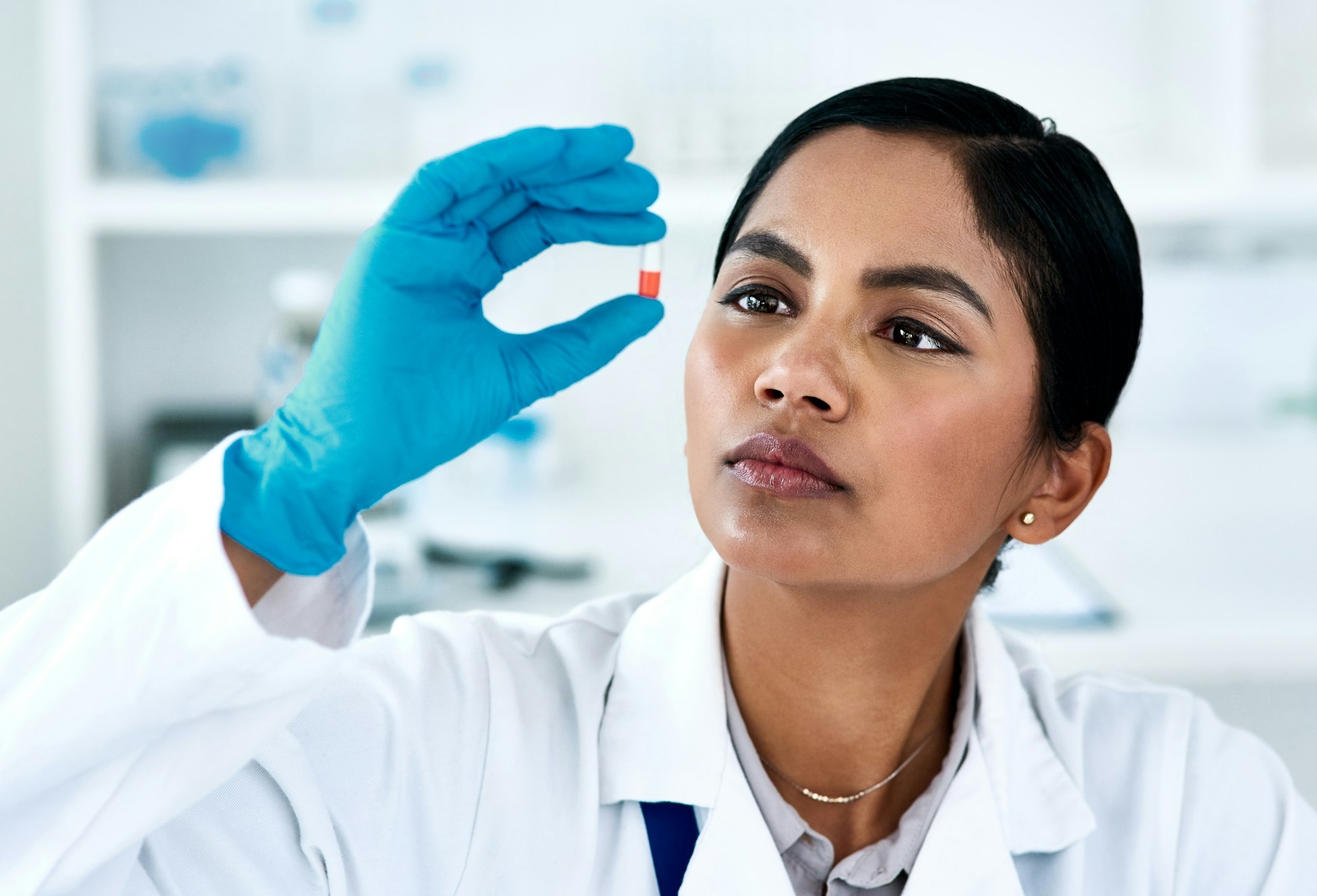
What is GMP Compliance?
GMP Compliance, or Good Manufacturing Practice, refers to the regulations that govern how pharmaceutical products are made. These rules ensure that every product is safe, high quality, and consistent. GMP Compliance covers every step of production, from sourcing raw materials to packaging and labeling finished products.
By following these regulations, pharmaceutical companies protect consumers from unsafe products and maintain their credibility.
GMP Compliance requires strict control over manufacturing processes, facility conditions, and employee training. It prevents errors, contamination, and product defects. Regular inspections by regulatory authorities help ensure that companies adhere to these standards. Without proper compliance, companies risk penalties, product recalls, and reputational damage. Therefore, staying compliant with GMP is critical for ensuring trust and safety in the pharmaceutical industry.
Sign up for Introduction to Good Manufacturing Practices (GMP) Free Course
Key Principles of GMP Compliance
Understanding the fundamental principles of GMP Compliance is the first step for any pharma professional. These core principles guide everything from the facilities to personnel, ensuring that pharmaceutical products are of the highest quality and free from contamination or defects.
A comprehensive quality management system (QMS) is the foundation of GMP Compliance. It ensures that all processes are documented, deviations are identified, and corrective actions are implemented.
Personnel must be properly trained in GMP regulations to perform their duties correctly. Regular training ensures that all staff members understand their responsibilities and can identify potential compliance issues.
Proper documentation of procedures, processes, and activities is essential. A well-maintained documentation system allows easy tracking of any changes or deviations, ensuring full traceability.
Every stage of production, from raw material acquisition to final product release, must be controlled to avoid contamination or errors. This includes monitoring environmental conditions and ensuring that proper sanitation practices are followed.
GMP Compliance Training: Why It Matters
Continuous Education for Professionals
Continuous education for professionals is essential to keep their skills current and relevant. In fast-changing industries like pharmaceuticals, new regulations and technologies frequently emerge. Professionals need to stay updated to remain competitive and effective. By regularly engaging in training and learning opportunities, they can adapt to these changes with ease. Continuous education also enhances their ability to handle complex tasks and solve problems quickly. It helps them remain confident and capable in their roles, reducing the risk of mistakes and improving overall performance.
Moreover, companies benefit greatly from investing in continuous education for their employees. Well-trained professionals ensure compliance with new industry standards, which reduces the risk of penalties or non-compliance issues. Offering regular training programs also boosts employee morale and motivation, as they feel valued and supported in their career development. This leads to higher job satisfaction and retention rates, saving companies the costs of high turnover. Additionally, continuous education fosters innovation, as employees bring fresh ideas and solutions to the table. By prioritizing ongoing learning, companies not only improve individual performance but also build a more resilient and adaptable workforce. This long-term investment in education creates a solid foundation for future success in any organization.
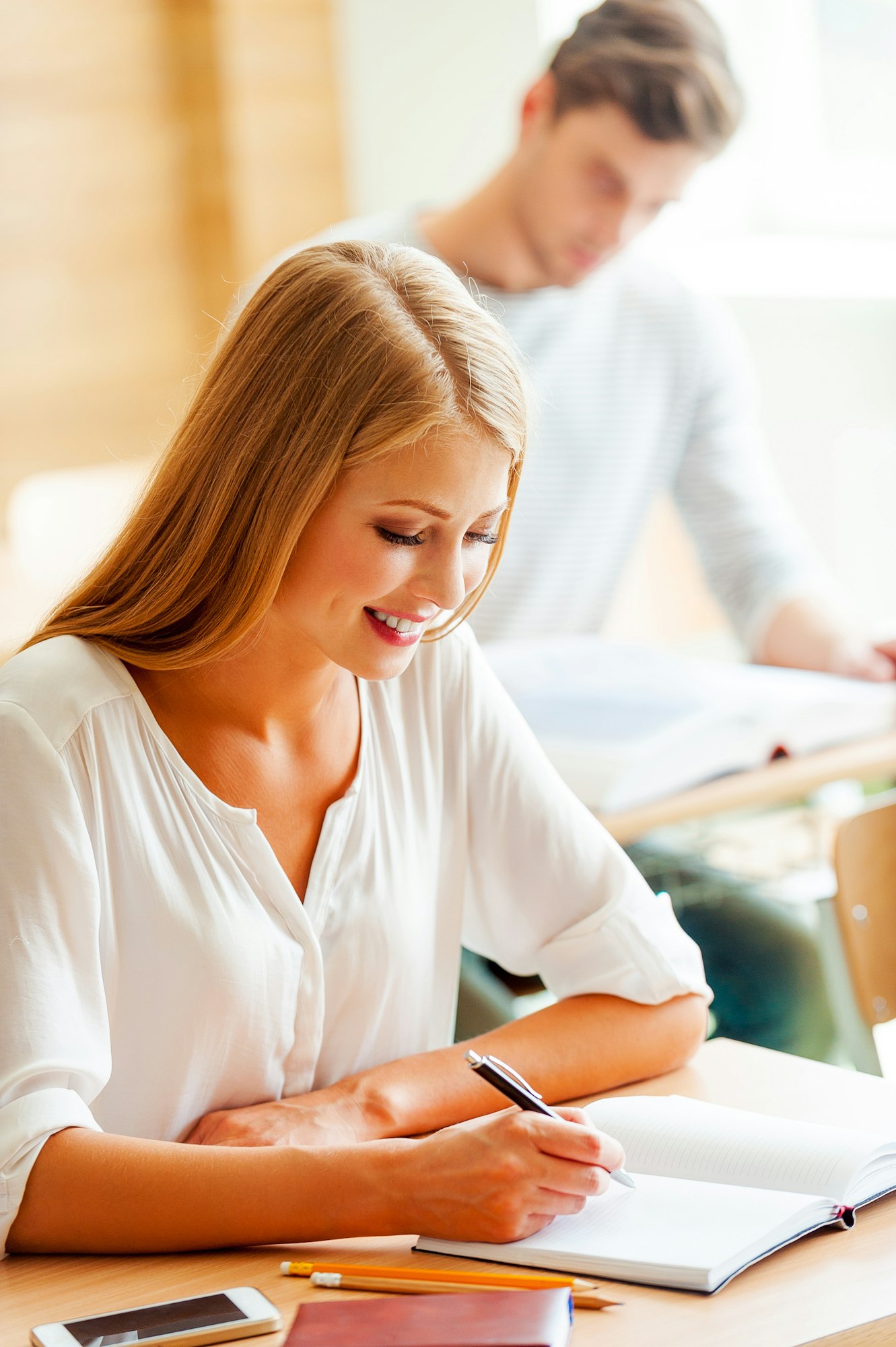
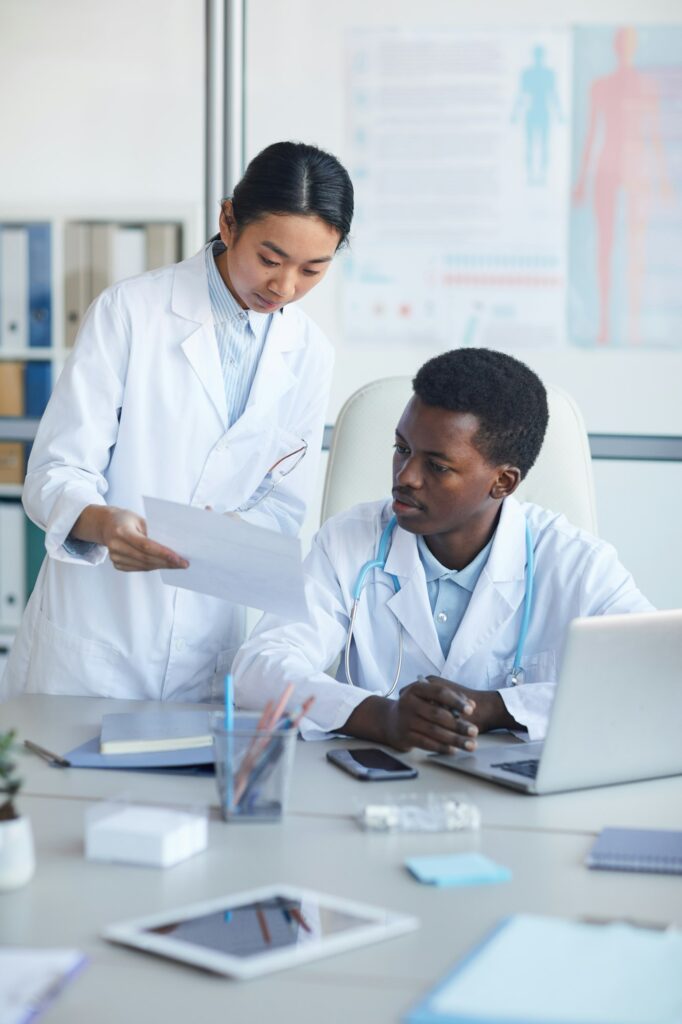
Building a Proactive Compliance Culture
Building a proactive compliance culture ensures that everyone in the organization prioritizes regulatory adherence. Instead of reacting to issues, a proactive approach helps prevent problems before they arise. Employees at all levels must understand the importance of compliance and take responsibility for maintaining it. Regular training and clear communication keep the team informed about changing regulations. This culture fosters an environment where employees feel confident in identifying and addressing potential risks. By catching issues early, the company avoids costly mistakes and ensures smoother operations.
Managers play a key role in cultivating a proactive compliance culture. They must lead by example and emphasize the importance of compliance in everyday actions. Encouraging open dialogue about compliance helps employees share concerns without fear of repercussions. Regular audits and assessments allow the organization to continuously improve its processes. Additionally, recognizing employees for their compliance efforts motivates others to follow suit. By building this culture, companies not only meet regulatory standards but also build trust with clients and regulatory authorities. This proactive mindset strengthens the company’s reputation and sets the foundation for long-term success.
Essential Strategies for Ensuring GMP Compliance
Regular GMP Training
Employees must receive ongoing training on GMP Compliance to stay current with the latest regulations and industry best practices.
Document Everything
Maintain meticulous documentation for every process, including equipment calibration, material inspections, and production methods.
Monitor Environmental Conditions
Use regular environmental monitoring to prevent contamination during the manufacturing process, especially in sterile production environments.
Conduct Routine Audits
Internal and external audits should be scheduled regularly to assess whether GMP Compliance protocols are being followed correctly.
Implement QMS
A robust QMS ensures that every step in the production process adheres to GMP Compliance standards.
Risk-Based Approach
Adopt a risk-based approach to focus efforts on the most critical areas that could impact product safety or quality.
Continuous Improvement
Continuously improve processes by incorporating feedback, addressing non-conformities, and keeping up with regulatory changes.
Ensuring Long-Term GMP Compliance in Your Organization
Leadership Commitment to Compliance
Leadership commitment to compliance is vital for maintaining high standards in any organization. When leaders prioritize compliance, it sets the tone for the entire company. They must actively promote adherence to regulations and ensure that all employees understand their role in maintaining compliance. By communicating the importance of compliance regularly, leaders create a culture where following rules becomes second nature. They should also allocate resources, such as training and tools, to support compliance efforts. This proactive approach ensures everyone is equipped to meet regulatory standards consistently.
In addition, leaders must lead by example to reinforce a strong compliance culture. When executives and managers follow the rules, it encourages employees to do the same. Consistency in enforcing policies shows that compliance is not just a box to check but a priority for the company’s long-term success. Leaders can also implement regular audits and reviews to track compliance performance. This practice helps identify areas for improvement and prevents issues from escalating. Ultimately, leadership commitment to compliance builds trust with regulators, clients, and employees. It strengthens the company’s reputation and reduces the risk of costly violations or penalties.
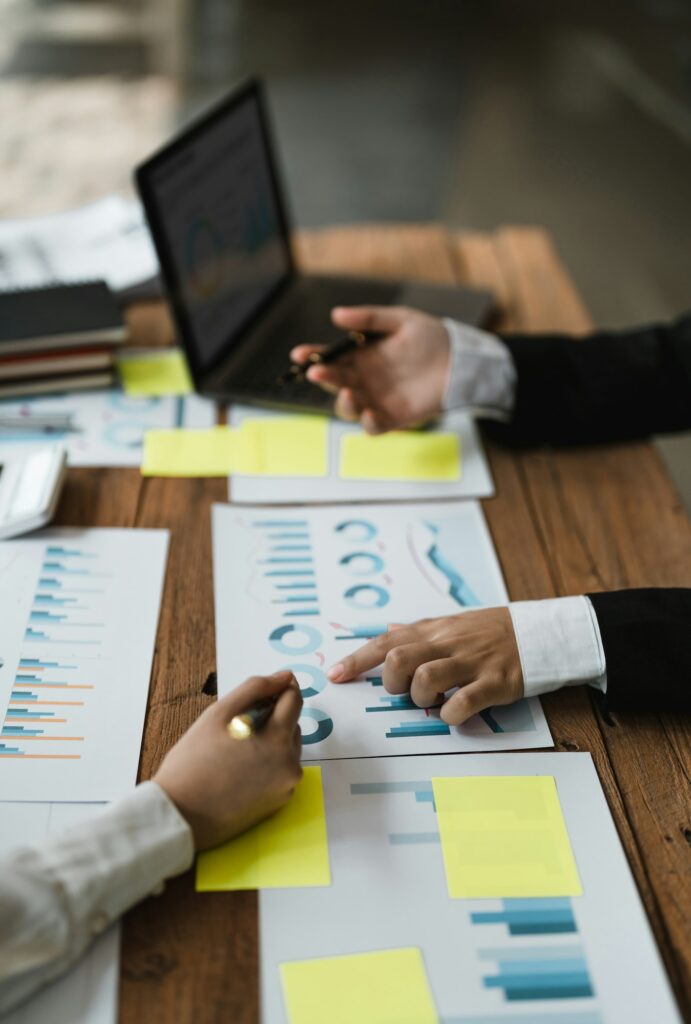
Continuous Improvement Culture
A continuous improvement culture drives organizations to constantly refine processes and achieve better results. It encourages employees to look for ways to enhance efficiency and quality. This mindset creates a proactive environment where problems are quickly identified and resolved. Instead of accepting the status quo, teams focus on ongoing learning and development. Leaders play a crucial role in promoting this culture by encouraging open discussions and feedback. Regularly reviewing operations ensures that the organization remains agile and adapts to industry changes.
Continuous improvement requires everyone’s involvement to be truly effective. Leaders must motivate employees to share ideas for improvements and reward innovative thinking. By fostering collaboration across departments, companies can find solutions that benefit the entire organization. Additionally, setting measurable goals helps track progress and shows where adjustments are needed. Regular training and development opportunities support this culture by keeping employees’ skills sharp. Embracing a continuous improvement culture not only enhances performance but also boosts employee morale. It builds a sense of ownership and accountability, making teams more invested in the company’s success. Over time, this approach strengthens competitiveness and ensures long-term growth.
Top GMP Compliance Pitfalls and Prevention
Incomplete or inaccurate records can lead to non-compliance. To avoid this, always ensure thorough documentation for every procedure and action taken.
Employees who lack up-to-date knowledge on GMP Compliance may inadvertently cause violations. Continuous training helps ensure that all personnel are well-versed in the latest regulations.
Failure to maintain clean and properly functioning equipment can result in contamination. Regular maintenance schedules should be strictly adhered to.
Environmental factors like humidity and temperature can affect product quality. Implementing strict monitoring and control protocols is essential to mitigate this risk.
Skipping internal audits can allow non-compliant processes to persist. Regular internal audits are crucial for identifying issues before they lead to regulatory penalties.
Building a Comprehensive GMP Training Program
Identify Training Needs
Assess the specific roles within your company to identify who needs GMP Compliance training and to what extent. Some employees may require more advanced or specialized training depending on their responsibilities.
Customize Training Content
Tailor the content of the training to meet the specific needs of different departments. For example, production staff may require different training compared to the quality assurance team.
Regularly Update Training Materials
Keep training materials up to date with the latest regulations and industry practices. Outdated content can lead to misunderstandings and mistakes.
Use Practical Examples
Incorporate real-world examples of GMP Compliance failures and successes to illustrate the importance of adhering to guidelines.
Assess Competency
At the conclusion of the training, assess employees’ understanding to ensure that the key principles of GMP Compliance are fully understood.
Conclusion
GMP compliance goes beyond meeting regulatory requirements; it’s about ensuring quality, safety, and efficiency in pharmaceutical production. By following best practices, such as consistent training, thorough documentation, and utilizing advanced technology, professionals can maintain high standards. These steps not only protect consumers but also help companies avoid costly errors and penalties.
In addition, a proactive approach and continuous improvement culture strengthen compliance efforts. Regularly updating processes, addressing risks early, and encouraging innovation create a more resilient organization. By committing to these practices, pharma companies build trust with regulators and consumers, leading to long-term success in a highly regulated industry.
References
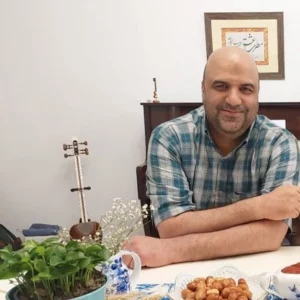
Ershad Moradi
Ershad Moradi, a Content Marketing Specialist at Zamann Pharma Support, brings 6 years of experience in the pharmaceutical industry. Specializing in pharmaceutical and medical technologies, Ershad is currently focused on expanding his knowledge in marketing and improving communication in the field. Outside of work, Ershad enjoys reading and attending industry related networks to stay up-to-date on the latest advancements. With a passion for continuous learning and growth, Ershad is always looking for new opportunities to enhance his skills and contribute to pharmaceutical industry. Connect with Ershad on Facebook for more information.

Pharmaceutical Storage: Everything You Need to Know
Pharmaceutical storage is critical for safety, compliance, and efficiency. This guide explains cold chain solutions, stability testing, and warehouse systems. You’ll also learn about regulatory requirements, ISO standards, and practical strategies to optimize pharmaceutical storage facilities and distribution networks.
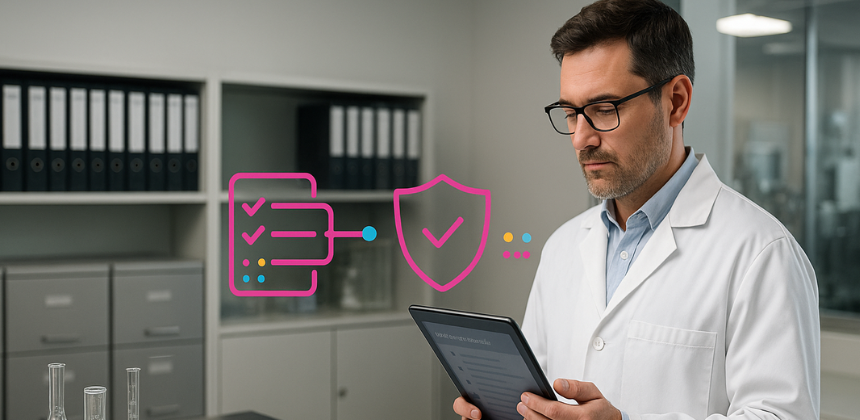
GMP Audit Checklist: Pass Your Next Inspection With Confidence
Use this gmp audit checklist to see if you would pass today. Run a 10-minute self-test, verify evidence, and prioritize fixes. Then follow 30- and 90-day plans to strengthen data integrity, CAPA, Annex 1, training, and documentation. Build proof that convinces auditors, reduces risk, and keeps your site inspection-ready year-round.
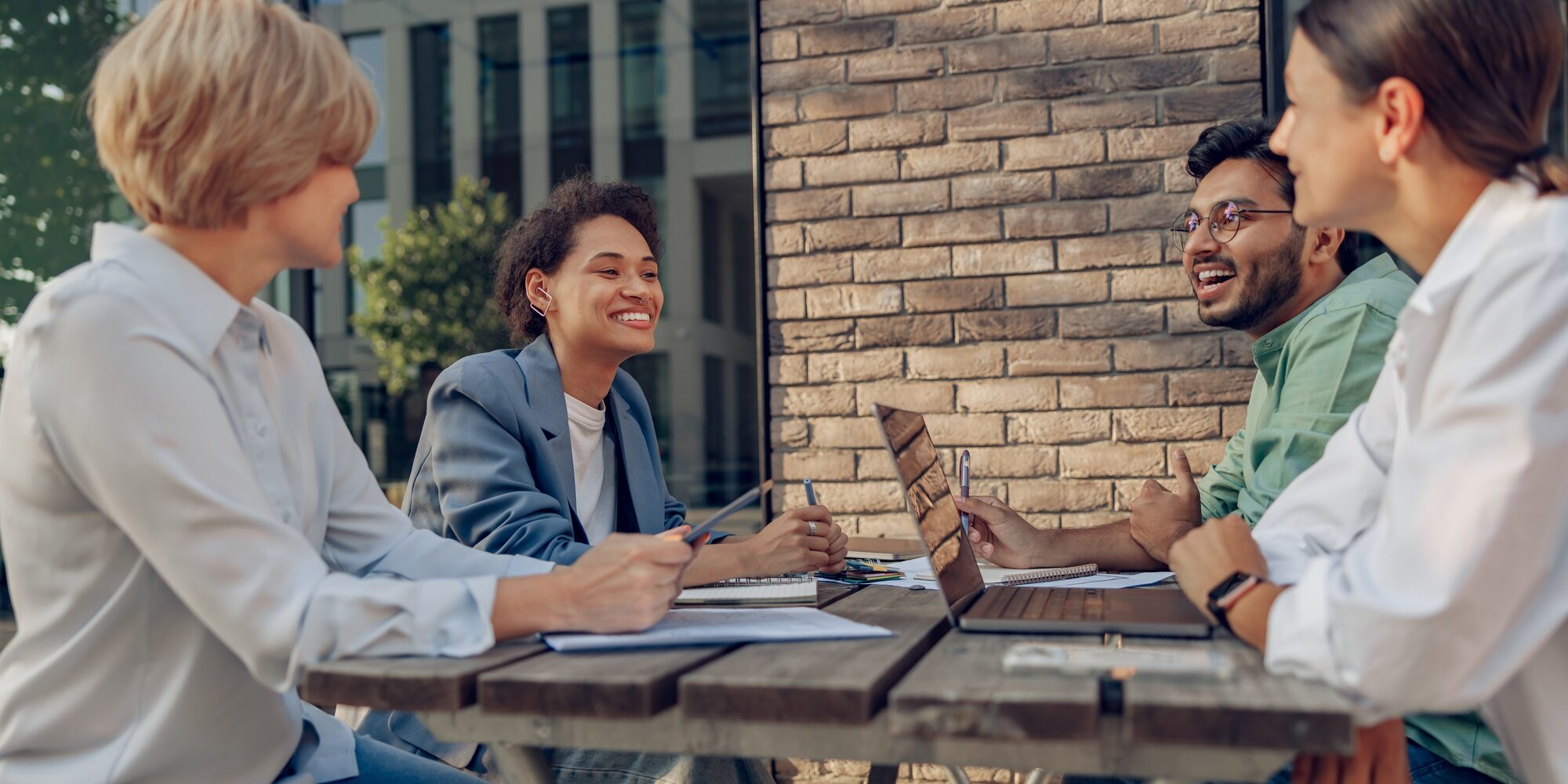
Pharma Sales Secrets to Skyrocket Success
Pharma sales is more than just selling medications. It combines science, strategy, and relationship building. Whether you’re starting out or refining your approach, this guide gives you practical tools, career insights, and tips to succeed in today’s competitive pharmaceutical sales industry.