Installation Qualification (IQ) is a critical step in ensuring pharmaceutical equipment is installed and functions according to regulatory requirements. This process guarantees that systems meet the necessary standards before moving on to the next phases of qualification, such as Operational Qualification (OQ) and Performance Qualification (PQ).
In this guide, we will explore the essential steps of IQ, its objectives, procedures, and how it contributes to ensuring that pharmaceutical equipment operates safely and effectively.

Installation Qualification in Pharma Industry
Pharmaceutical companies use Installation Qualification (IQ) to verify that equipment, systems, or instruments are installed correctly. This process ensures that all components function as intended and meet manufacturer specifications. Additionally, IQ confirms that equipment configurations align with regulatory requirements from agencies like the FDA and EMA.
During this phase, key documentation is reviewed, and systems are physically tested to confirm that installation adheres to both safety and operational requirements. Verification procedures include assessing utilities, system integrity, and software configurations. Successful completion of IQ paves the way for the next stages in the qualification process, such as OQ and PQ, ensuring that systems are ready for real-world production conditions.
Sign up for Performing Phase of GMP Equipment Qualification Course
Key Steps in the Installation Qualification Procedure
Performing Installation Qualification correctly is essential for ensuring that equipment performs as expected and complies with all necessary regulations. Below are the main steps involved in IQ:
Preparation of IQ Protocol
The first step involves preparing the Installation Qualification protocol, a detailed document that outlines the specific tests, procedures, and acceptance criteria for the equipment installation. This protocol must be aligned with regulatory standards and should cover all installation-related checks.
Pre-Installation Review
Before equipment installation begins, a thorough review of the installation site is conducted. This includes verifying that utilities (water, electricity, air, etc.) and environmental conditions (temperature, humidity) are suitable for equipment use.
Installation Verification
Once the equipment is installed, it undergoes a thorough inspection. This process ensures the equipment has been physically set up according to the manufacturer’s specifications, including system integration and configuration.
Functionality Testing
After verifying installation, equipment functionality is tested. This includes assessing all components and systems to ensure they operate correctly and meet the functional requirements outlined in the IQ protocol.
Documentation of Results
All results from the installation checks, tests, and inspections must be documented. This documentation ensures traceability and compliance with regulatory standards, and provides evidence for future audits or inspections.
The Role of Installation Qualification in GMP Compliance
Understanding Installation Qualification’s Role in GMP
Installation Qualification (IQ) plays a vital role in ensuring that pharmaceutical equipment meets Good Manufacturing Practice (GMP) standards. GMP ensures that products are consistently produced and controlled according to quality standards. By verifying the correct installation of equipment, IQ ensures that systems function properly and meet these stringent requirements. Without proper IQ, equipment might fail to perform as expected, which could compromise product quality and safety. Therefore, IQ directly impacts product reliability, ensuring that the equipment operates consistently and efficiently.
Additionally, IQ helps identify potential issues early in the process, preventing costly delays or non-compliance. By testing and documenting installation procedures, companies demonstrate adherence to GMP, which is crucial for regulatory inspections. Furthermore, IQ establishes a solid foundation for the next qualification stages, such as Operational Qualification (OQ) and Performance Qualification (PQ). These stages, in turn, confirm that equipment continues to operate according to specifications in real-world conditions. In summary, IQ ensures that equipment functions reliably, maintaining the high standards necessary for pharmaceutical manufacturing.
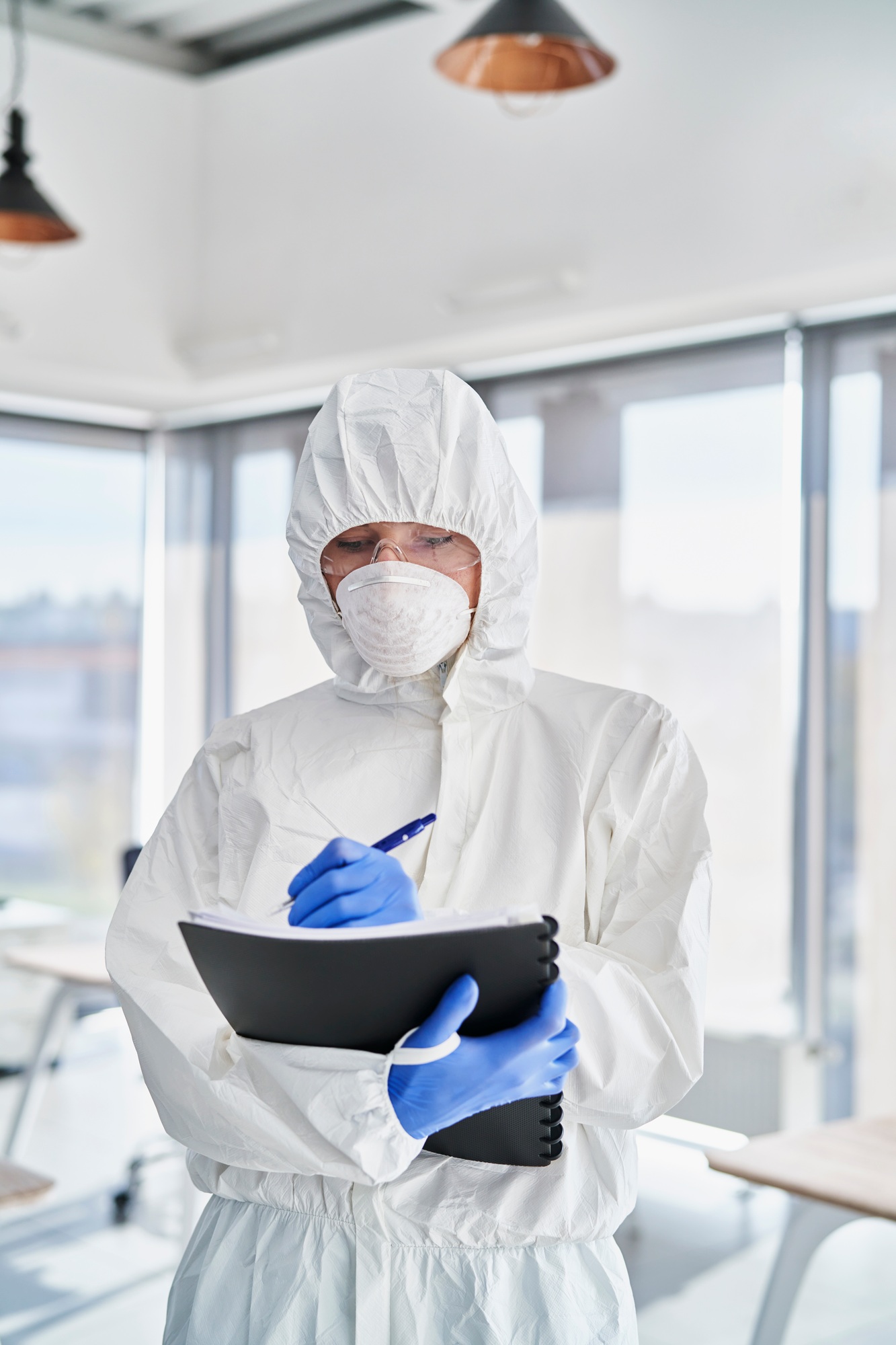
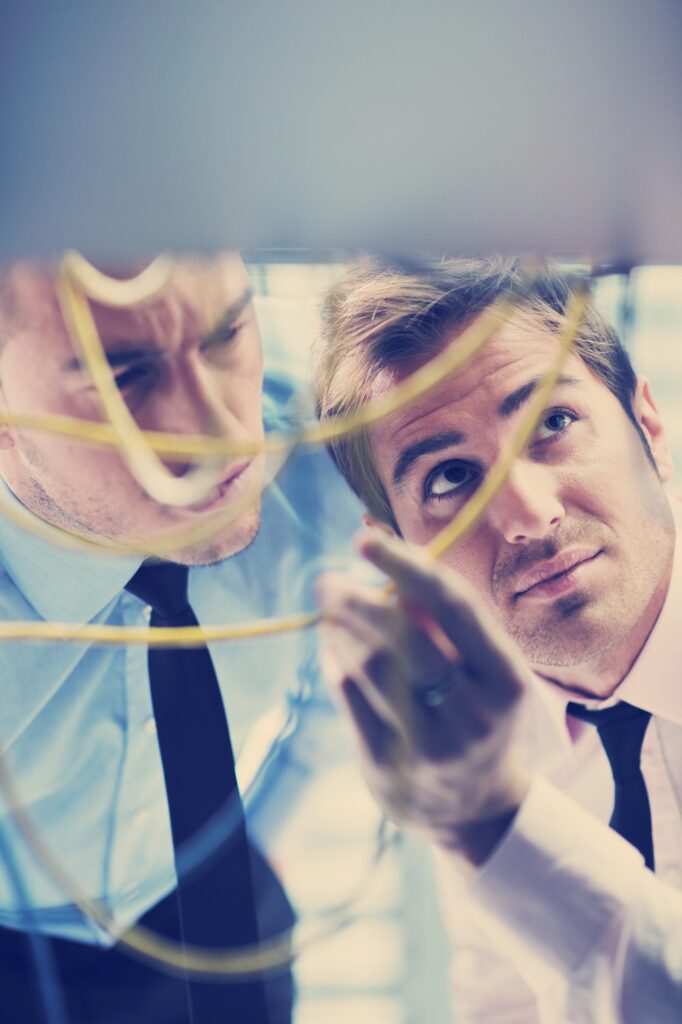
GMP Compliance Through Proper Installation
A properly installed system plays a crucial role in GMP compliance by ensuring that equipment functions correctly. When equipment is correctly installed, it operates as expected, minimizing the chances of production errors.
Moreover, it reduces the risk of contamination and ensures the final product meets the required quality standards. By confirming that all components are set up according to specifications, IQ prevents potential issues that could affect product safety and efficacy. As a result, businesses reduce the likelihood of costly recalls or compliance failures.
IQ is also essential for documenting that the equipment meets all operational requirements set by regulatory authorities. Regulatory bodies, such as the FDA or EMA, require thorough documentation to prove that systems are correctly installed and fully compliant. This documentation verifies that the equipment is safe to use and capable of maintaining product consistency. Additionally, it provides evidence of ongoing compliance during inspections and audits. In summary, proper installation through IQ ensures that systems contribute to safety, efficacy, and product consistency, reinforcing GMP compliance and safeguarding public health.
Key Objectives of Installation Qualification in Pharma
The main goals of Installation Qualification are to confirm that all installed systems meet regulatory and manufacturer standards and to ensure they will function reliably throughout their lifecycle. Here are five core objectives of IQ in the pharmaceutical industry:
Compliance with Regulatory Standards
Ensuring that the installation adheres to FDA, EMA, or other relevant regulatory bodies’ guidelines is essential to avoid non-compliance issues.
Verification of System Integrity
Confirming the integrity of installed systems ensures that they operate as designed, with all components working in harmony.
Functional Readiness
The equipment must be ready to perform at full capacity, meeting both performance and safety standards for production.
Risk Mitigation
Identifying and mitigating risks during installation helps prevent operational failures or safety hazards that could affect product quality.
Documentation and Traceability
All verification activities are documented, ensuring compliance and providing valuable data for audits, inspections, or troubleshooting.
The Role of Installation Qualification in GMP Compliance
Understanding Installation Qualification's Role in GMP
Ensuring pharmaceutical equipment meets Good Manufacturing Practice (GMP) standards requires a strong Installation Qualification (IQ) process. GMP establishes strict regulations to guarantee product quality and safety. IQ verifies proper equipment installation, ensuring systems operate as intended. By detecting issues early, IQ prevents disruptions that could compromise reliability. Without thorough IQ procedures, equipment may fail to meet standards, increasing the risk of errors and quality defects.
Meeting regulatory requirements in pharmaceutical manufacturing depends on effective Installation Qualification (IQ). This process confirms that systems are installed correctly, reducing risks of contamination and malfunctions. As a result, companies minimize non-compliance risks during audits and regulatory inspections. Additionally, IQ helps prevent costly production setbacks by ensuring seamless operations. When systems function reliably from the start, manufacturers maintain efficiency and consistently produce high-quality pharmaceuticals that comply with GMP guidelines.
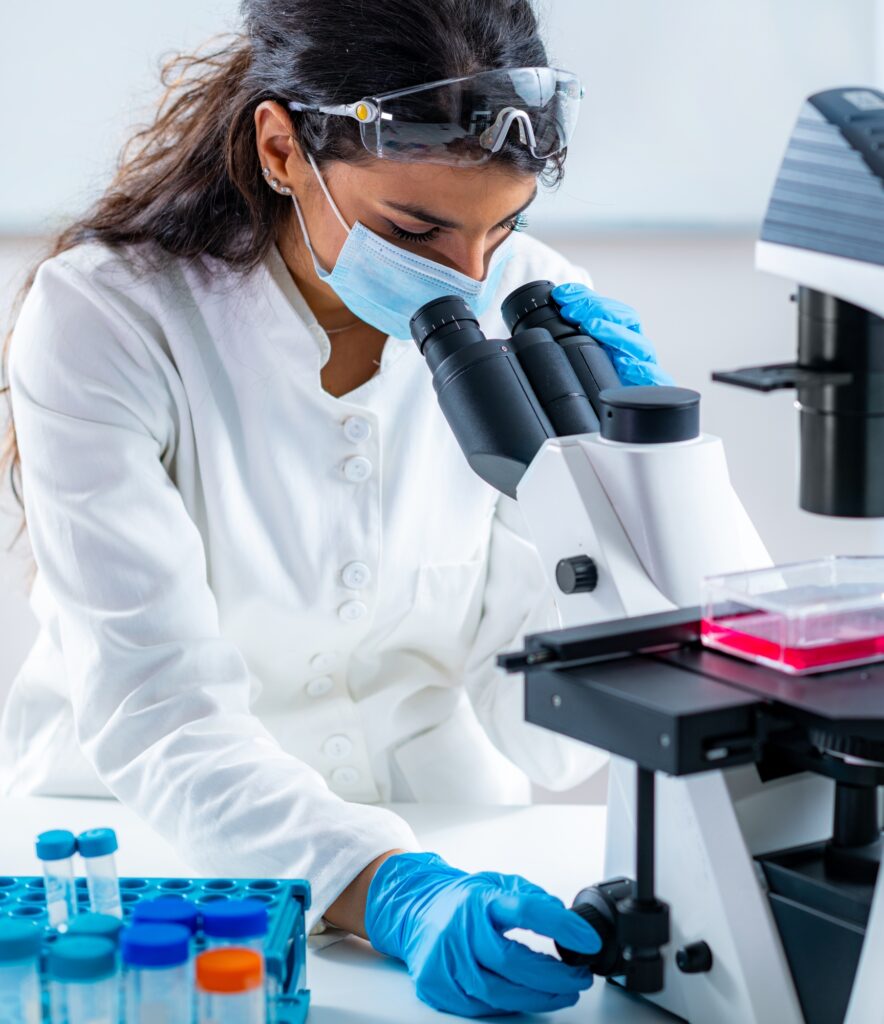
GMP Compliance Through Proper Installation
A properly installed system plays a significant role in ensuring GMP compliance. When equipment functions correctly, it minimizes production errors and prevents contamination. This ensures that the final product maintains the required quality standards. Additionally, a properly installed system helps maintain the equipment’s reliability, preventing any unforeseen issues that could affect production. By meeting the operational requirements set by regulatory authorities, companies demonstrate their commitment to safety, efficacy, and product consistency. Thus, the equipment contributes to a seamless manufacturing process, reducing risks that could compromise product quality.
IQ is essential for documenting that the system meets all operational and regulatory requirements. It provides detailed records to verify that each component of the system operates correctly. These records help prove compliance during inspections and audits. Furthermore, IQ documents that the equipment will maintain its performance throughout its lifecycle, ensuring consistency in product output. Without thorough IQ documentation, companies may face challenges proving regulatory adherence, risking penalties or delays. In conclusion, IQ ensures the proper installation of systems, safeguarding product quality, and ensuring GMP compliance across the production process.
Equipment Qualification and Regulatory Compliance
How Installation Qualification Supports Regulatory Compliance
Installation Qualification directly supports regulatory compliance by ensuring that all equipment is installed according to predefined specifications, which is a cornerstone of Good Manufacturing Practice (GMP). Following these processes helps pharmaceutical companies meet the regulatory expectations set forth by authorities like the FDA and EMA.
Role in Ongoing Compliance and Audits
IQ also helps pharmaceutical companies prepare for audits and inspections. Regulatory bodies require documented evidence of installation verification, and successful completion of IQ ensures that equipment is ready for subsequent qualification phases. Properly installed equipment reduces the likelihood of production disruptions and quality issues, thus supporting ongoing regulatory compliance.
How to Create an Installation Qualification Protocol
Creating a detailed Installation Qualification protocol is one of the most critical steps in the IQ process. Here’s a step-by-step guide on how to create an effective IQ protocol:
Define Equipment Specifications
Start by defining the exact specifications of the equipment. This includes model numbers, manufacturer details, and the required installation conditions.
Outline Test Procedures
Develop a series of tests that will be performed on the equipment during the installation process. Each test should have clear acceptance criteria to ensure the equipment meets all specifications.
Designate Responsible Personnel
Specify who is responsible for carrying out each step of the installation and validation process. This ensures accountability and helps streamline the process.
Conclusion
In conclusion, Installation Qualification (IQ) is a critical first step in the validation process for pharmaceutical equipment, ensuring that systems are correctly installed, meet regulatory standards, and are ready for further qualification phases. By adhering to best practices, understanding the regulatory requirements, and creating thorough documentation, pharmaceutical companies can avoid common pitfalls and ensure compliance with GMP standards. The success of IQ plays a significant role in mitigating risks, enhancing product quality, and contributing to the overall safety and efficacy of pharmaceutical production processes.
By following a structured and detailed IQ process, you pave the way for smoother operational qualification and performance qualification phases, ultimately ensuring that all equipment meets the highest standards required for the production of safe and effective pharmaceutical products.
References
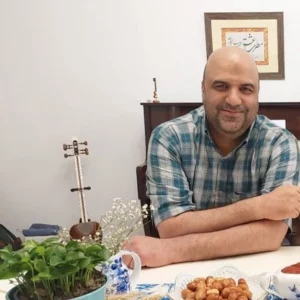
Ershad Moradi
Ershad Moradi, a Content Marketing Specialist at Zamann Pharma Support, brings 6 years of experience in the pharmaceutical industry. Specializing in pharmaceutical and medical technologies, Ershad is currently focused on expanding his knowledge in marketing and improving communication in the field. Outside of work, Ershad enjoys reading and attending industry related networks to stay up-to-date on the latest advancements. With a passion for continuous learning and growth, Ershad is always looking for new opportunities to enhance his skills and contribute to pharmaceutical industry. Connect with Ershad on Facebook for more information.
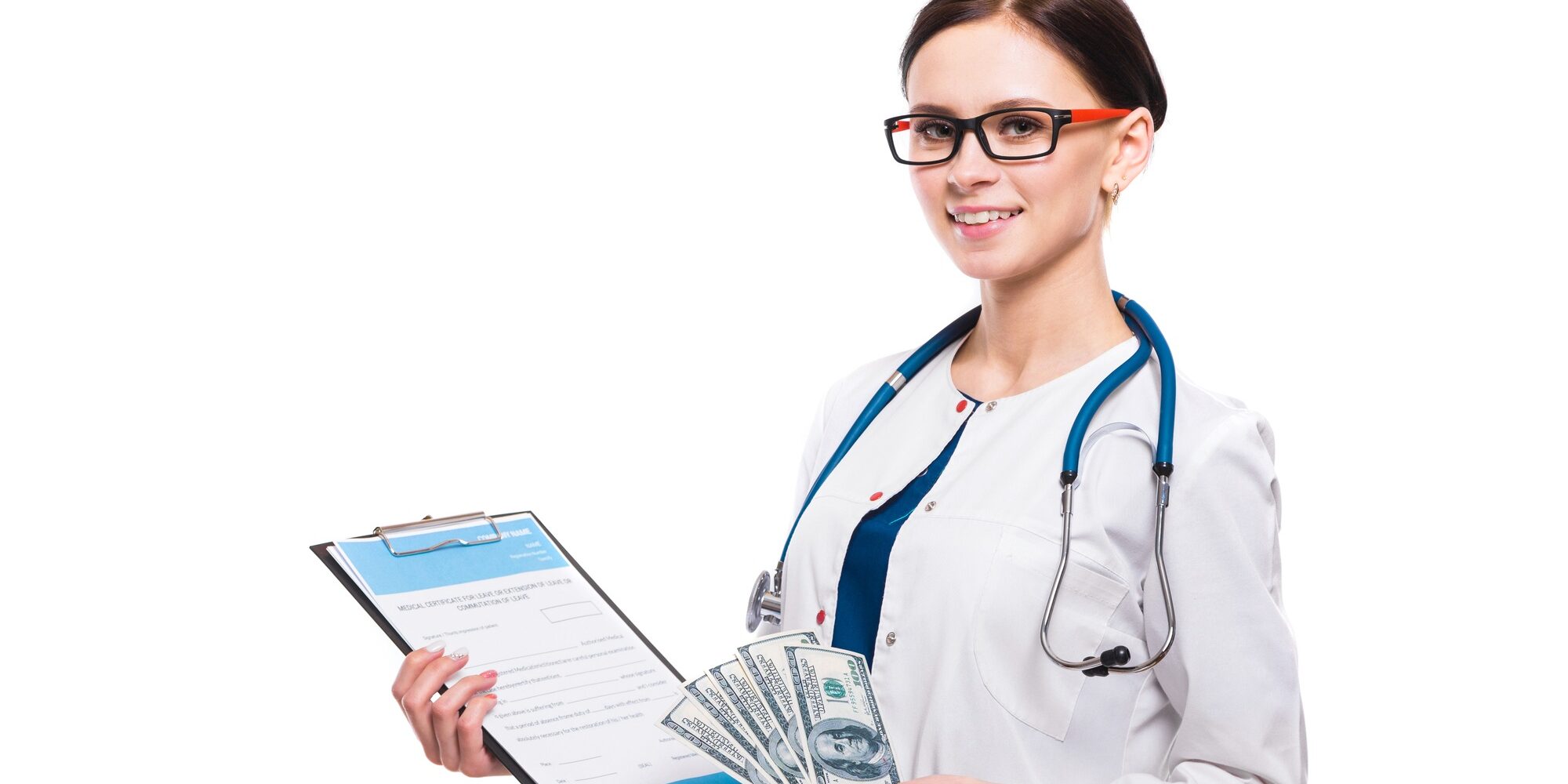
Pharmacist Salary in the US: What You Need to Know
This article explains pharmacist salary ranges—from hourly to annual pay—across practice settings. Learn how experience, location, and role shape wages, and find actionable advice on negotiating compensation, career advancement, and securing the best package through Pharmuni’s courses, resume tools, and GMP training.
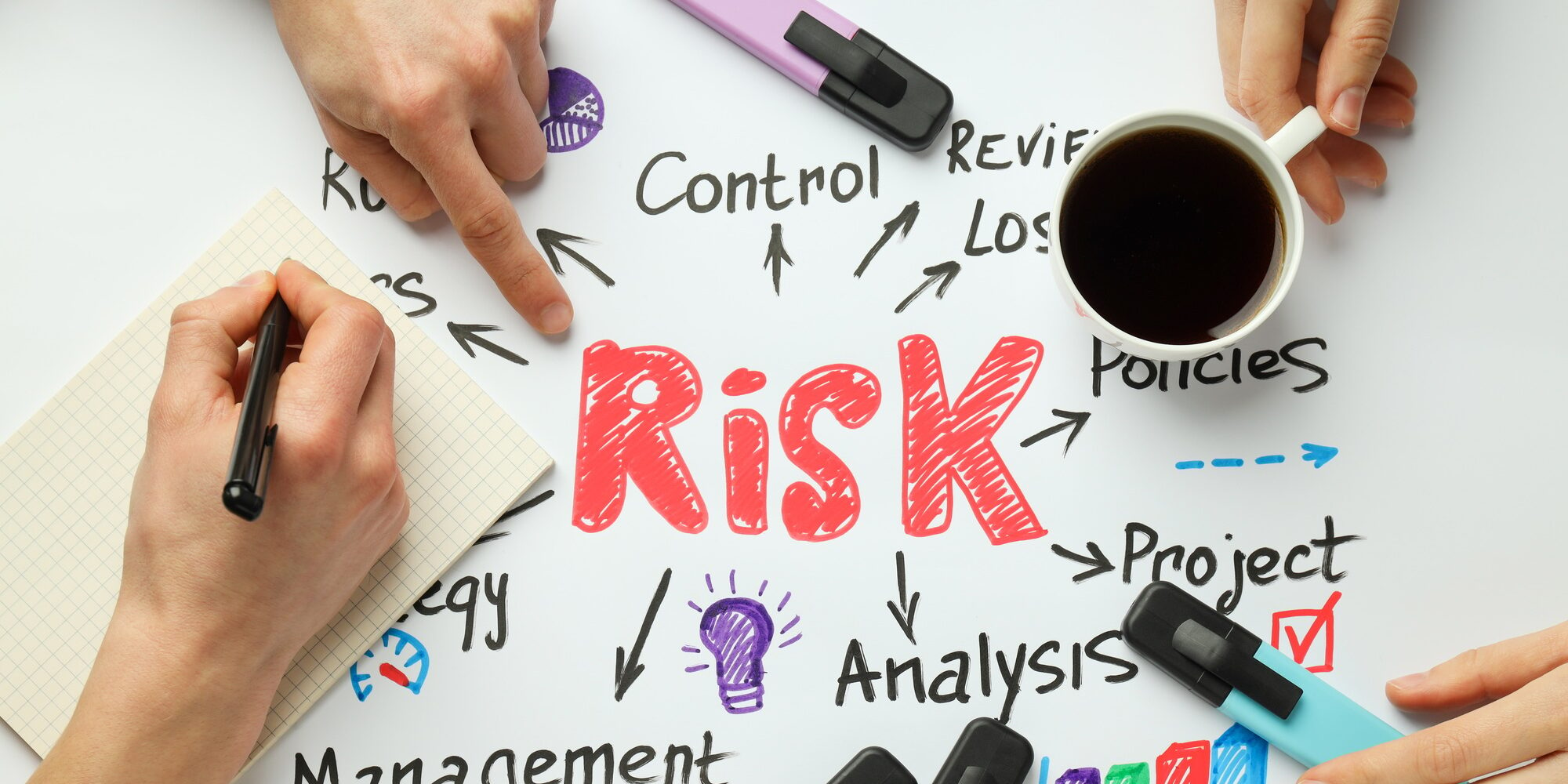
Risk Assessment Tools: Your Complete Guide to Smarter Decisions
Risk assessment tools help businesses identify, analyze, and control risks before they cause problems. From healthcare to pharma, tools like FMEA, HACCP, and Johns Hopkins fall risk assessments empower professionals with reliable strategies. Learn methods, compare approaches, and apply practical insights for better outcomes.
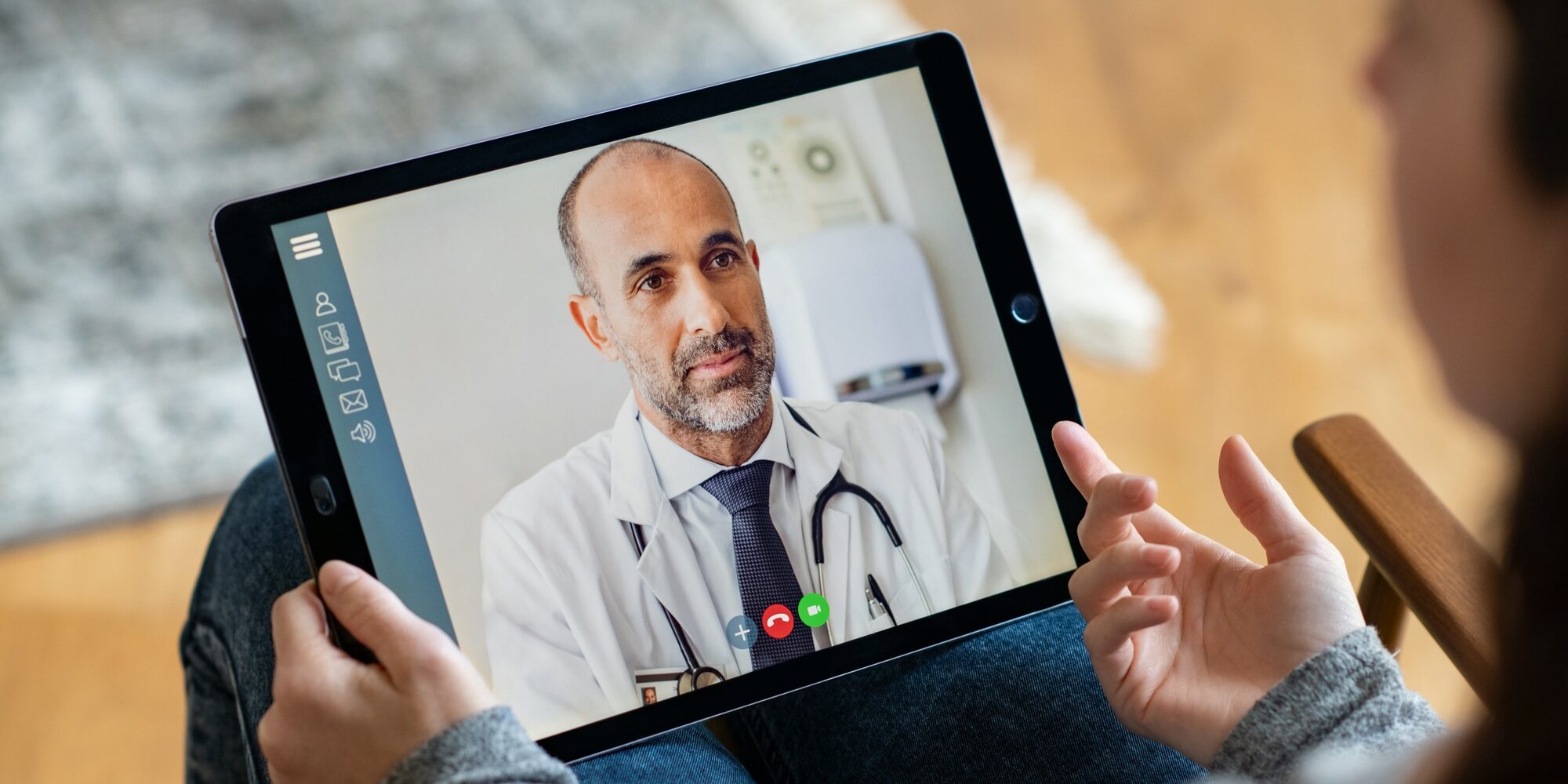
Pharmacovigilance Jobs Remote: The Complete Career Guide
Looking for pharmacovigilance jobs remote? This guide shows you where to find remote drug safety roles, how to qualify, and which global opportunities exist. Learn practical strategies, entry-level tips, and career insights to boost your chances in the competitive pharmacovigilance market.