Equipment Qualification plays a crucial role in pharmaceutical and medical device manufacturing. It ensures that equipment operates according to regulatory standards and meets Good Manufacturing Practice (GMP) requirements. Without proper qualification, companies risk compliance failures, product recalls, and safety issues.
Manufacturers must plan and execute Equipment Qualification carefully. This process includes multiple stages, such as Installation Qualification (IQ), Operational Qualification (OQ), Performance Qualification (PQ), and Requalification. Proper calibration and maintenance also contribute to the effectiveness of this process.
This guide explains how to implement GMP Equipment Qualification successfully and maintain compliance.
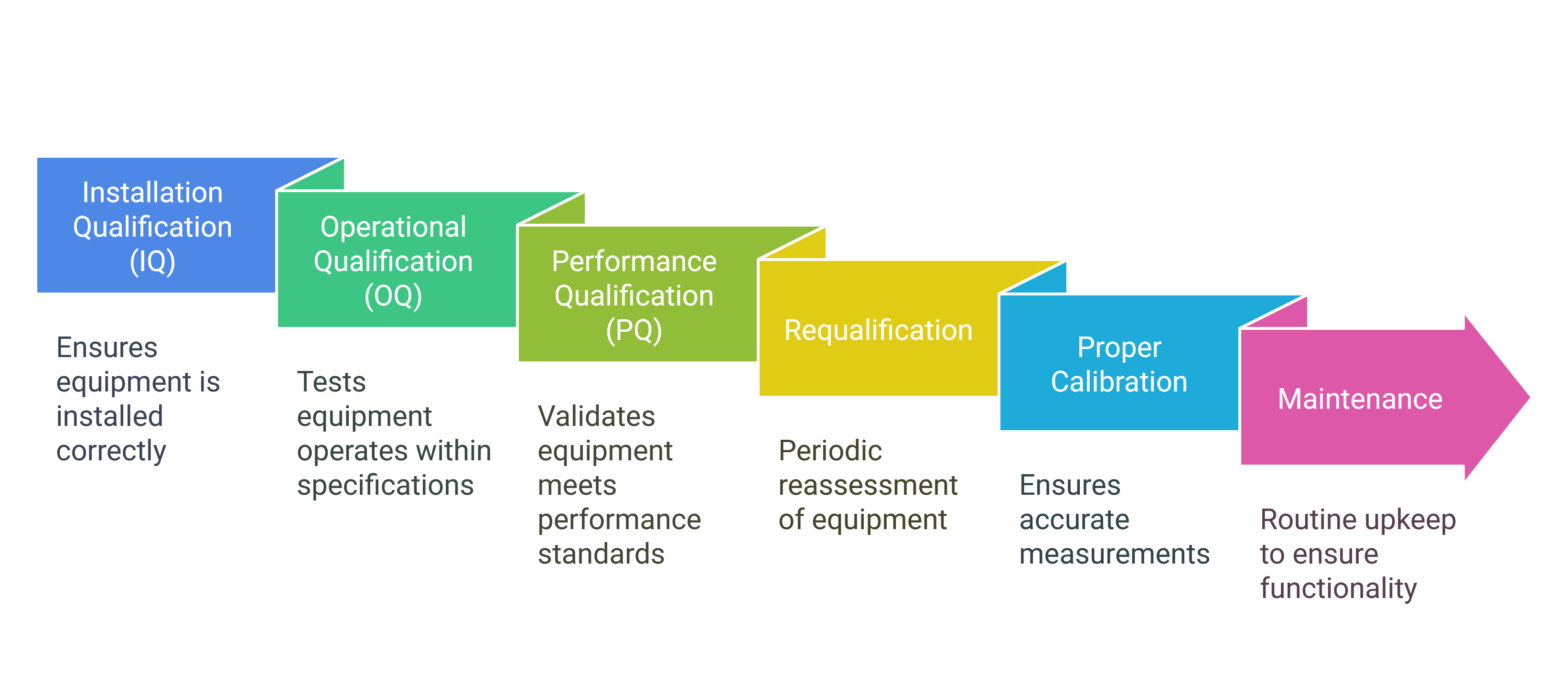
Understanding Equipment Qualification and Its Importance
Equipment Qualification ensures that machines and systems in production meet regulatory requirements. Manufacturers must validate accuracy, consistency, and reliability to comply with GMP standards. Regulatory agencies, such as the FDA and EMA, require documented proof of qualification. Without proper qualification, companies risk compliance failures, safety issues, and costly recalls. Each step in the qualification process helps identify potential equipment failures before they impact production. Companies must follow a structured approach to confirm that machines operate correctly. By implementing qualification protocols, manufacturers improve efficiency and maintain product integrity. A strong qualification process also enhances trust with regulators and customers.
A well-executed Equipment Qualification process prevents deviations and reduces operational risks. Manufacturers must define requirements, conduct tests, and maintain thorough records. Each qualification stage verifies equipment performance before, during, and after production. Regular assessments help detect issues early and prevent costly downtime. Companies should integrate qualification into their quality management systems to ensure long-term compliance. Properly documented procedures also streamline audits and regulatory inspections. Without qualification, companies may face penalties, rejected batches, or legal consequences. Consistent monitoring and requalification ensure that equipment remains reliable over time. By prioritizing qualification, manufacturers safeguard their operations and protect public health.
Sign up for Performing Phase of GMP Equipment Qualification Course
Key Phases of Equipment Qualification
Each phase of Equipment Qualification verifies different aspects of equipment performance. Following a structured approach helps manufacturers achieve consistent results and regulatory compliance.
Design Qualification (DQ)
Verify that equipment specifications match process requirements before purchasing.
Installation Qualification (IQ)
Confirm that installation meets design specifications and regulatory guidelines.
Operational Qualification (OQ)
Test equipment functionality under normal and stress conditions.
Performance Qualification (PQ)
Demonstrate that the equipment performs consistently during production.
Requalification
Periodically reassess equipment performance to maintain compliance.
Calibration and Maintenance
Ensure measurement tools remain accurate and within required tolerances.
Change Control and Documentation
Track modifications and maintain qualification records.
Comparing Installation Qualification and Operational Qualification
Ensuring Proper Setup
Manufacturers install equipment correctly by following Installation Qualification (IQ) procedures based on regulatory and manufacturer requirements. This process confirms that power connections, environmental conditions, and component configurations meet safety standards. Companies must inspect each installation to ensure proper setup and performance. Incorrect installation can lead to equipment failures and production disruptions. Teams document every installation detail, including part numbers, materials, and software versions. Maintaining accurate records helps track changes and supports compliance with GMP regulations. A structured IQ process minimizes errors and prevents unexpected operational issues. Completing this step properly builds a reliable foundation for long-term equipment performance.
Reducing malfunctions and ensuring smooth validation processes depends on a well-executed Installation Qualification. Teams must verify that equipment meets all design and regulatory specifications before advancing to operational testing. Early identification of installation issues through IQ helps companies avoid costly downtime and compliance risks. Skipping this step increases the likelihood of failures during later qualification phases. Detailed documentation simplifies troubleshooting and accelerates regulatory approvals. Routine audits and reviews of installation records support long-term equipment reliability and compliance efforts.
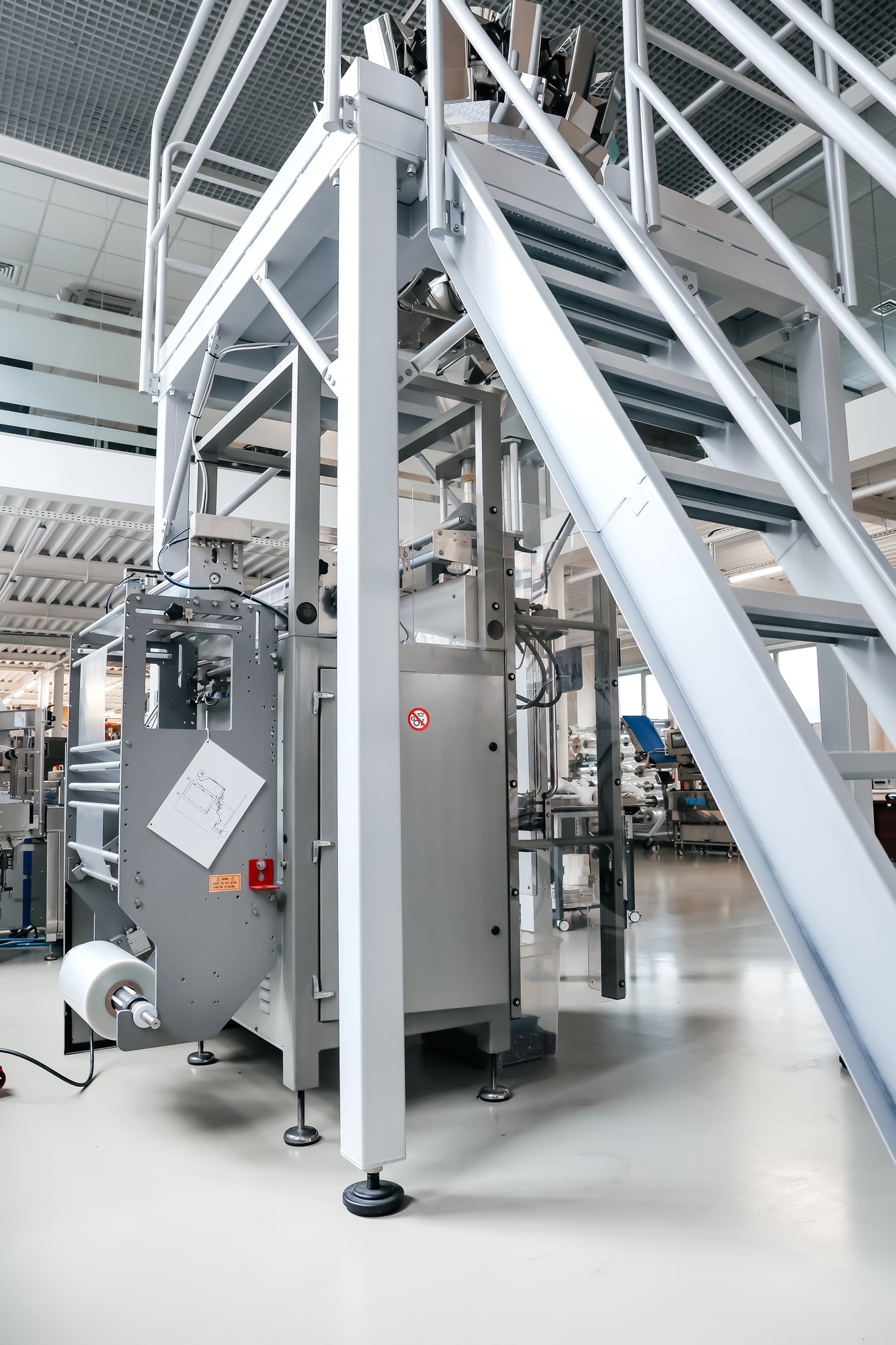
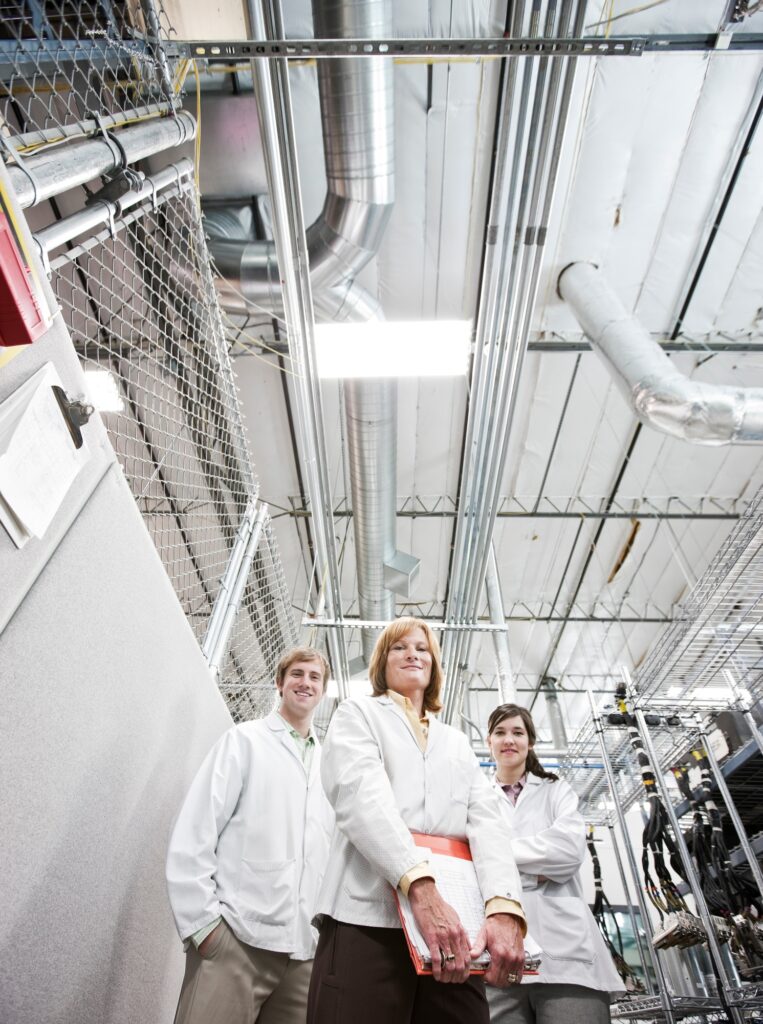
Confirming Functional Performance
Testing equipment performance under various conditions ensures reliability through Operational Qualification (OQ). Engineers conduct predefined tests to verify functionality, control systems, and safety mechanisms. Before full-scale production begins, machines must pass these evaluations. Detecting potential issues early helps companies prevent unexpected malfunctions. Running real-world simulations reduces operational risks and enhances process efficiency. Meeting regulatory and quality standards depends on successful OQ execution. Equipment failures can lead to costly production delays without proper testing. Following a structured OQ process helps manufacturers maintain consistency and optimize overall performance.
Preventing breakdowns and ensuring long-term reliability requires thorough Operational Qualification. Manufacturers record test results to demonstrate compliance with GMP guidelines. These records serve as essential documentation during audits and inspections. Routine OQ assessments help identify signs of wear before they escalate into failures. Addressing issues early allows companies to schedule preventive maintenance efficiently. Reducing downtime through proactive measures extends the lifespan of critical equipment. Workplace safety improves when machines function within established performance limits.
5 Key Differences Between Performance Qualification and Requalification
Timing
Scheduled intervals determine Requalification timing, while PQ occurs prior to production.
Purpose
Long-term compliance is upheld through Requalification, while PQ establishes initial reliability.
Test Conditions
Drift and deviations are identified in Requalification, while PQ validates operational conditions.
Regulatory Focus
Meeting initial GMP standards relies on PQ, while Requalification maintains compliance.
Data Collection
Baseline performance is documented in PQ, whereas Requalification tracks changes over time.
Calibration and Maintenance Best Practices for Equipment Qualification
Maintaining Accuracy in Equipment Qualification
Calibration ensures that measuring instruments provide accurate and reliable readings in GMP manufacturing. Manufacturers must routinely calibrate sensors, gauges, and other devices to maintain precision. Inaccurate measurements can lead to product defects and regulatory issues. Companies compare device readings against certified reference standards to detect deviations. If readings fall outside acceptable limits, they adjust the equipment immediately. Regular calibration prevents small errors from becoming major problems. By following a structured calibration schedule, manufacturers improve efficiency and maintain quality standards. Without proper calibration, machines may produce inconsistent results and compromise product safety.
Companies must document calibration records as part of their Equipment Qualification process. These records prove compliance with GMP regulations and support audit readiness. Regular calibration reduces the risk of costly mistakes and product recalls. It also helps extend equipment lifespan by preventing performance degradation. Companies that neglect calibration may face regulatory penalties and production failures. Unexpected measurement errors can lead to rejected batches and financial losses. Preventive calibration minimizes downtime and keeps production running smoothly.
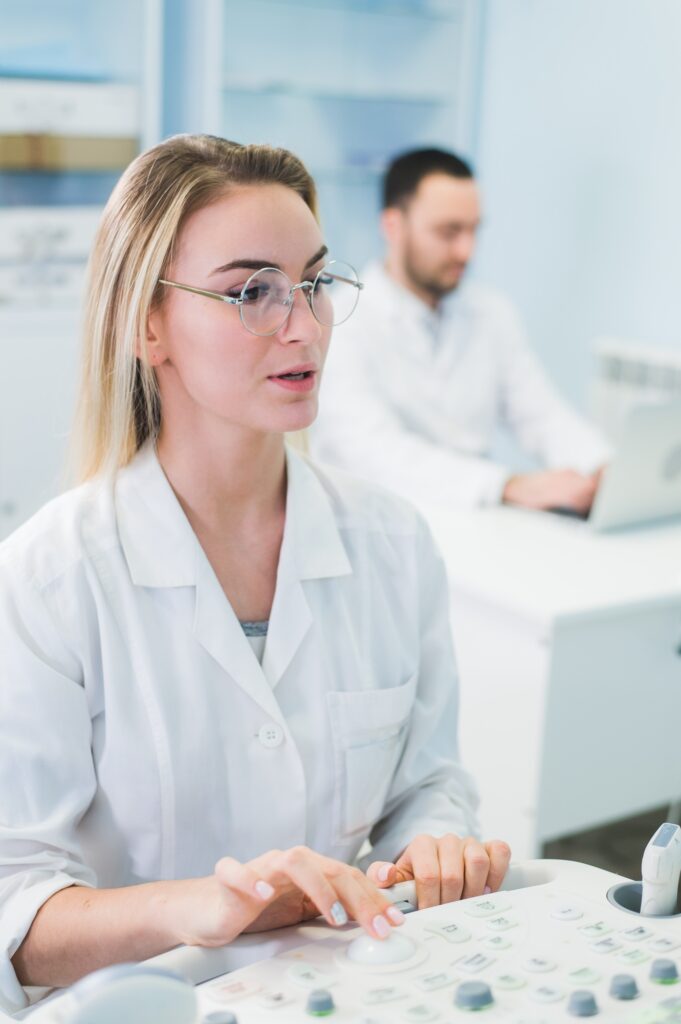
Preventing Failures in Equipment Qualification
Maintenance strategies keep equipment in optimal condition and ensure smooth production processes. Manufacturers must schedule routine inspections, lubrication, and part replacements to prevent unexpected failures. Regular maintenance helps identify potential issues before they cause major breakdowns. By addressing minor problems early, companies avoid costly repairs and production delays. A proactive approach reduces risks and maintains consistent equipment performance. Well-maintained machines support efficient operations and improve overall productivity. Neglecting maintenance can lead to sudden malfunctions, compromising product quality and compliance. Companies must train staff to follow maintenance schedules and report any irregularities immediately.
A structured maintenance plan minimizes downtime and extends the lifespan of GMP equipment. When manufacturers maintain machines properly, they reduce the risk of deviations and requalification failures. Regular servicing ensures that equipment operates within required specifications at all times. Proper documentation of maintenance activities also supports audit readiness and regulatory compliance. Inspectors review these records to verify adherence to GMP guidelines. Without clear documentation, companies may struggle to prove compliance during inspections. A well-documented maintenance strategy prevents regulatory penalties and improves operational reliability.
Main Objectives of Equipment Qualification
Drug Manufacturers must meet FDA, EMA, and GMP regulatory standards to ensure compliance and avoid penalties. Validating equipment helps maintain reliability, supporting consistent production and meeting process demands. By verifying performance, companies reduce the risk of equipment failures. Proper qualification also prevents product contamination by maintaining controlled conditions. Unqualified machines can introduce defects and compromise product safety. Strict validation procedures minimize contamination risks and ensure smooth production. Well-maintained and qualified machines improve overall efficiency. Companies optimize workflows by keeping equipment in peak condition.
A strong qualification process prevents unexpected failures and reduces downtime. Detecting potential issues early allows manufacturers to fix problems before they disrupt production. Validation also enhances data integrity by ensuring accurate records for audits and inspections. Regulators review these records to confirm compliance with industry standards. Poor documentation can lead to regulatory action and operational risks. Companies must maintain detailed qualification data to support ongoing compliance efforts. A structured validation process also drives continuous improvement in manufacturing. Teams analyze qualification data to refine processes and increase efficiency. By prioritizing proper qualification, manufacturers improve product quality, maintain compliance, and enhance productivity.
How to Implement an Effective Equipment Qualification Plan
Define Qualification Requirements
Outline equipment specifications, regulatory expectations, and testing procedures.
Create Qualification Protocols
Develop IQ, OQ, PQ, and requalification procedures based on industry guidelines.
Perform Qualification Tests
Execute protocols systematically and document results accurately.
Address Deviations and Corrective Actions
Identify non-conformances and implement corrective measures.
Review and Approve Documentation
Ensure qualification reports meet internal and external audit standards.
Conclusion
Equipment Qualification is an essential process in GMP-regulated industries. It ensures that manufacturing equipment operates correctly, meets regulatory standards, and delivers consistent results. Proper execution of IQ, OQ, PQ, and requalification minimizes risks, enhances compliance, and maintains product quality.
Manufacturers must prioritize calibration, maintenance, and documentation to sustain long-term GMP compliance. By following a structured Equipment Qualification plan, companies can optimize production efficiency, reduce operational risks, and meet global regulatory expectations.
References
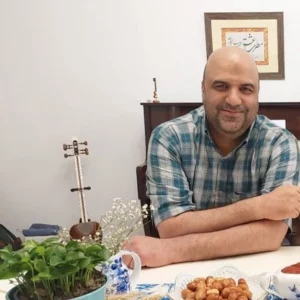
Ershad Moradi
Ershad Moradi, a Content Marketing Specialist at Zamann Pharma Support, brings 6 years of experience in the pharmaceutical industry. Specializing in pharmaceutical and medical technologies, Ershad is currently focused on expanding his knowledge in marketing and improving communication in the field. Outside of work, Ershad enjoys reading and attending industry related networks to stay up-to-date on the latest advancements. With a passion for continuous learning and growth, Ershad is always looking for new opportunities to enhance his skills and contribute to pharmaceutical industry. Connect with Ershad on Facebook for more information.
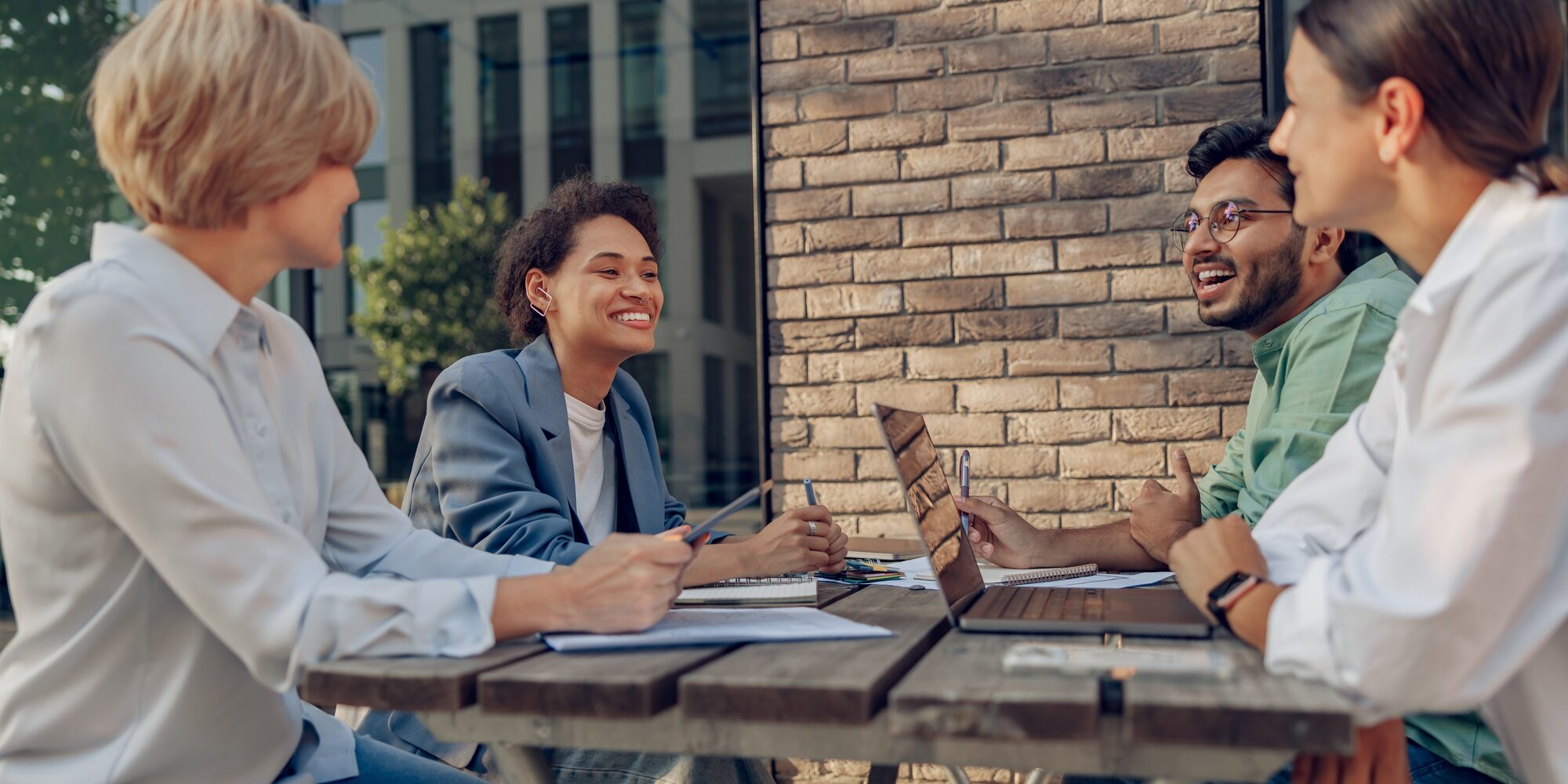
Pharma Sales Secrets to Skyrocket Success
Pharma sales is more than just selling medications. It combines science, strategy, and relationship building. Whether you’re starting out or refining your approach, this guide gives you practical tools, career insights, and tips to succeed in today’s competitive pharmaceutical sales industry.
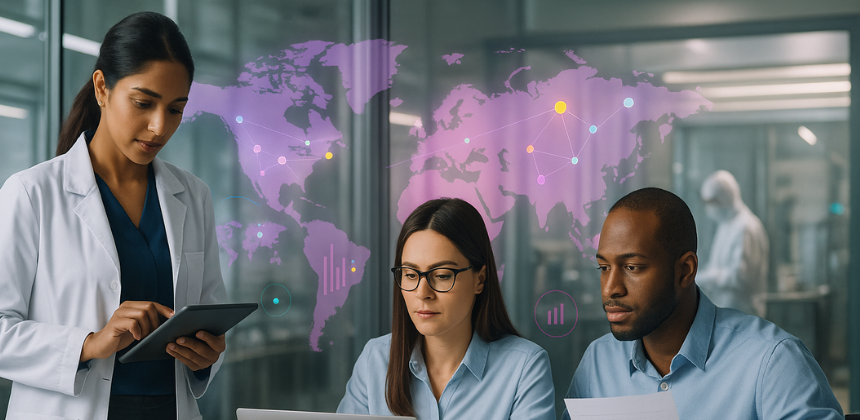
Pharma Job Market Trends: What’s Hot Now
Pharma job market trends show sustained growth across quality, regulatory affairs, pharmacovigilance, and data. New modalities, including cell and gene therapy, expand validation and aseptic roles quickly. Meanwhile, digital tools reshape trials, manufacturing, and safety reporting. Therefore, candidates who blend science, GxP, and analytics win more interviews.
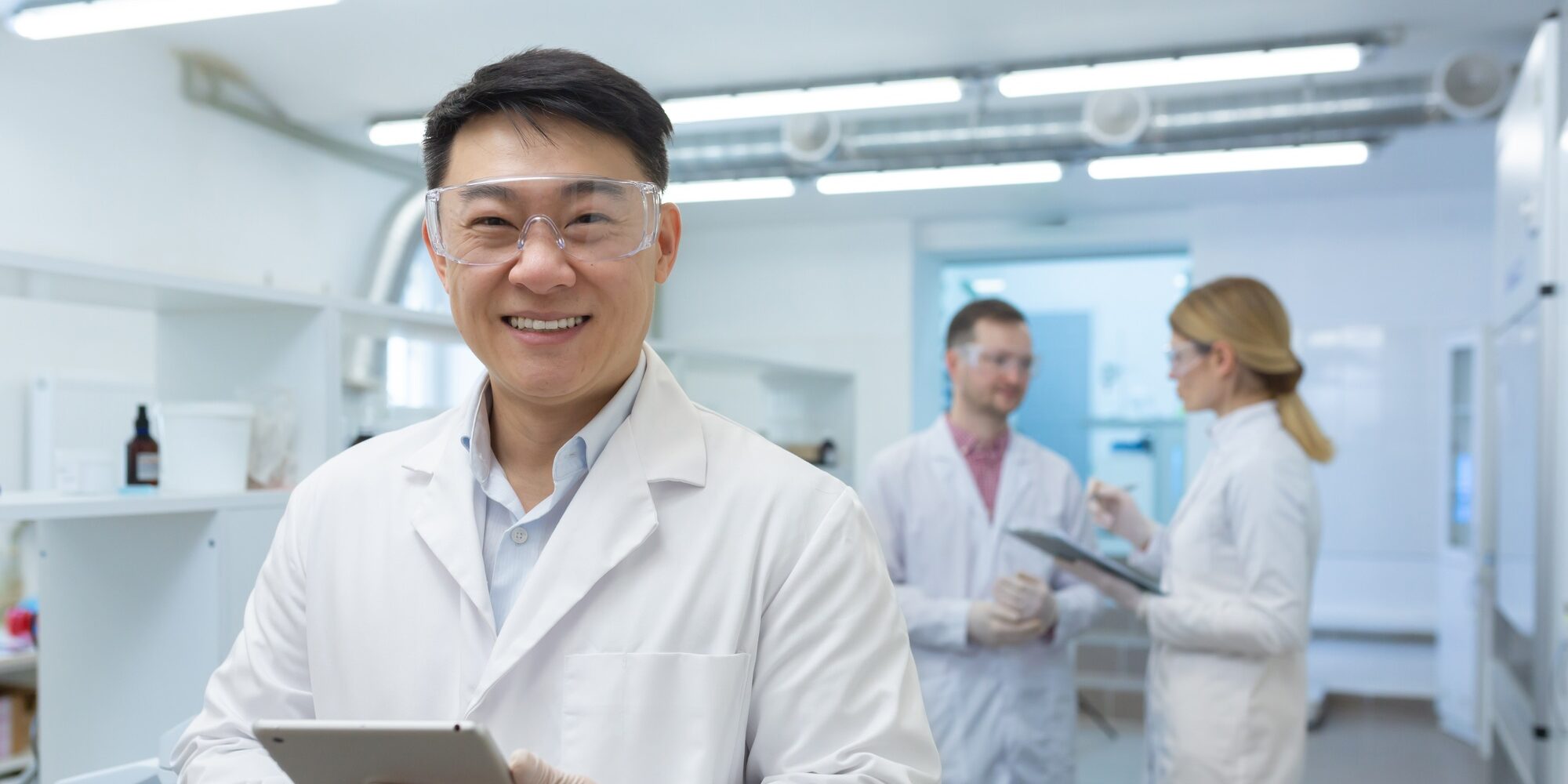
GMP Laboratory – Your Complete Guide to Compliance and Quality
This comprehensive guide explains GMP laboratories, their services, and compliance needs. Learn about cGMP, GLP labs, testing standards, and industry-specific requirements. Get actionable tips, comparisons, and insights to select the right GMP lab for your business or career growth.