Cleanroom design is a critical factor in sterile manufacturing. Ensuring the environment remains free from contaminants directly impacts product quality and patient safety. Cleanrooms must meet strict regulatory standards to support sensitive production processes. A well-designed cleanroom helps control airflow, temperature, and particle levels, enabling consistent compliance with Good Manufacturing Practices (GMP). Manufacturers who prioritize cleanroom design reduce contamination risks, boost operational efficiency, and maintain regulatory compliance.
This article explores the essential aspects of cleanroom design, including its purpose, ISO classifications, and requirements. Learn how proper design can optimize your manufacturing processes and support long-term success.
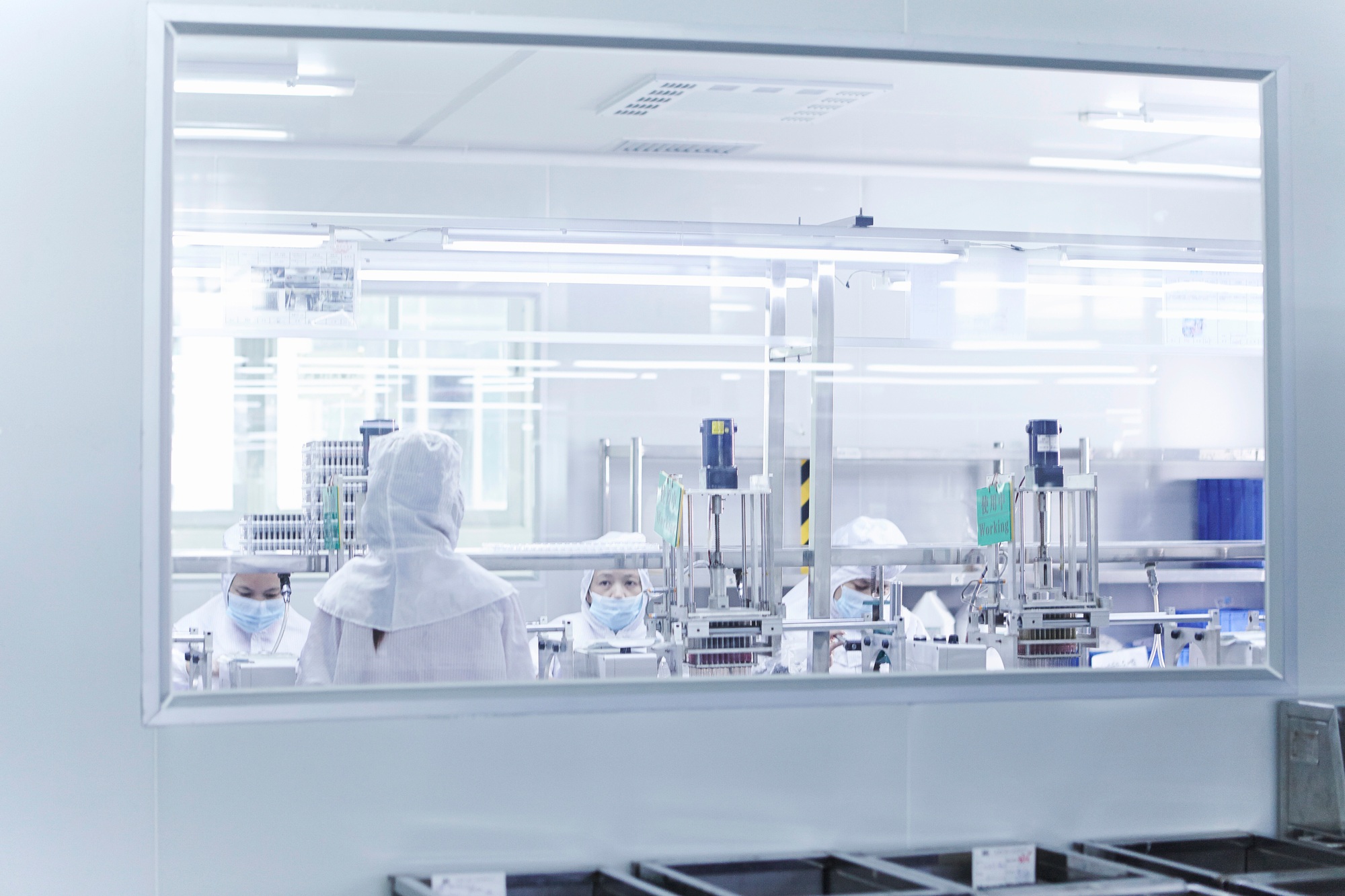
What is Cleanroom Design?
Cleanroom design involves planning and constructing environments with strict control over contaminants. Industries like pharmaceuticals, biotechnology, and electronics depend on cleanrooms to ensure product safety. These environments regulate airflow, temperature, and humidity to prevent contamination during production. Without effective control, airborne particles and microorganisms could compromise product quality. Designers focus on minimizing risks by creating spaces where environmental conditions stay consistent. Every design element supports sterile processes, helping manufacturers meet stringent industry standards.
The design process ensures cleanrooms meet required cleanliness levels for different applications. Designers install advanced filtration systems, such as HEPA and ULPA filters, to remove particles from the air. Controlled airflow patterns prevent cross-contamination by directing clean air properly. Additionally, seamless surfaces reduce the chances of dust accumulation and microbial growth. Designers also implement strict entry and exit protocols using airlocks and gowning rooms. These measures prevent pollutants from entering and affecting cleanroom performance. Through well-thought-out designs, manufacturers maintain safe, clean, and compliant production environments.
Sign up for Introduction to GMP Annex 1 Free Course
Cleanroom Design and ISO Classifications
Cleanroom design in pharmaceutical manufacturing requires strict adherence to ISO classifications to maintain sterility and prevent contamination. Each ISO class defines the maximum allowable particle concentration, ensuring products meet stringent regulatory standards. Below are the key ISO classifications commonly used in pharmaceutical cleanrooms:
Essential for sterile drug manufacturing and aseptic processing, this class limits particle levels. It ensures clean environments for critical processes such as filling, capping, and packaging sterile products.
Typically used in areas supporting aseptic processes, like rooms adjacent to ISO Class 5 cleanrooms. It helps create a controlled environment for product preparation and reduces contamination risks.
This classification applies to non-sterile operations, such as preparing clean components before sterilization. ISO Class 7 cleanrooms also serve as support areas for ISO Class 5 environments.
Used for less critical operations, including bulk drug production and raw material handling. This class ensures contamination levels remain within acceptable limits during early production stages.
While less common in pharmaceutical production, ISO Class 9 areas handle pre-cleaned materials that undergo further sterilization. They are used when contamination control is still required, but less stringent conditions are acceptable.
Adhering to the correct cleanroom classifications ensures safe and compliant pharmaceutical production. Maintaining proper classification throughout manufacturing helps meet GMP requirements and minimizes contamination risks, safeguarding product integrity.
ISO 14644 Standards and Cleanroom Design
Cleanroom Design and Validation by ISO 14644
Cleanroom validation relies on essential guidelines to maintain strict cleanliness and ensure contamination control. Manufacturers use these guidelines to classify cleanrooms based on particle concentrations in the air. They also validate cleanroom performance to maintain consistent environmental conditions during production. Following proper validation processes helps manufacturers prevent contamination risks and ensure product quality. Regular validation ensures cleanrooms operate within required cleanliness levels, reducing the chances of costly production issues. Without these measures, manufacturers risk compromising product safety and regulatory compliance.
ISO 14644 outlines specific steps for testing and monitoring cleanroom performance. Manufacturers perform particle count measurements to confirm cleanroom classifications and maintain sterility. They also validate airflow patterns to prevent cross-contamination during critical operations. Periodic revalidation helps detect performance changes, ensuring consistent cleanroom reliability. Additionally, ISO 14644 emphasizes the importance of maintaining detailed documentation to track compliance and support audits. By following these guidelines, manufacturers protect product integrity and reduce contamination risks. Ultimately, adhering to ISO 14644 plays a vital role in maintaining cleanroom performance and meeting regulatory standards.
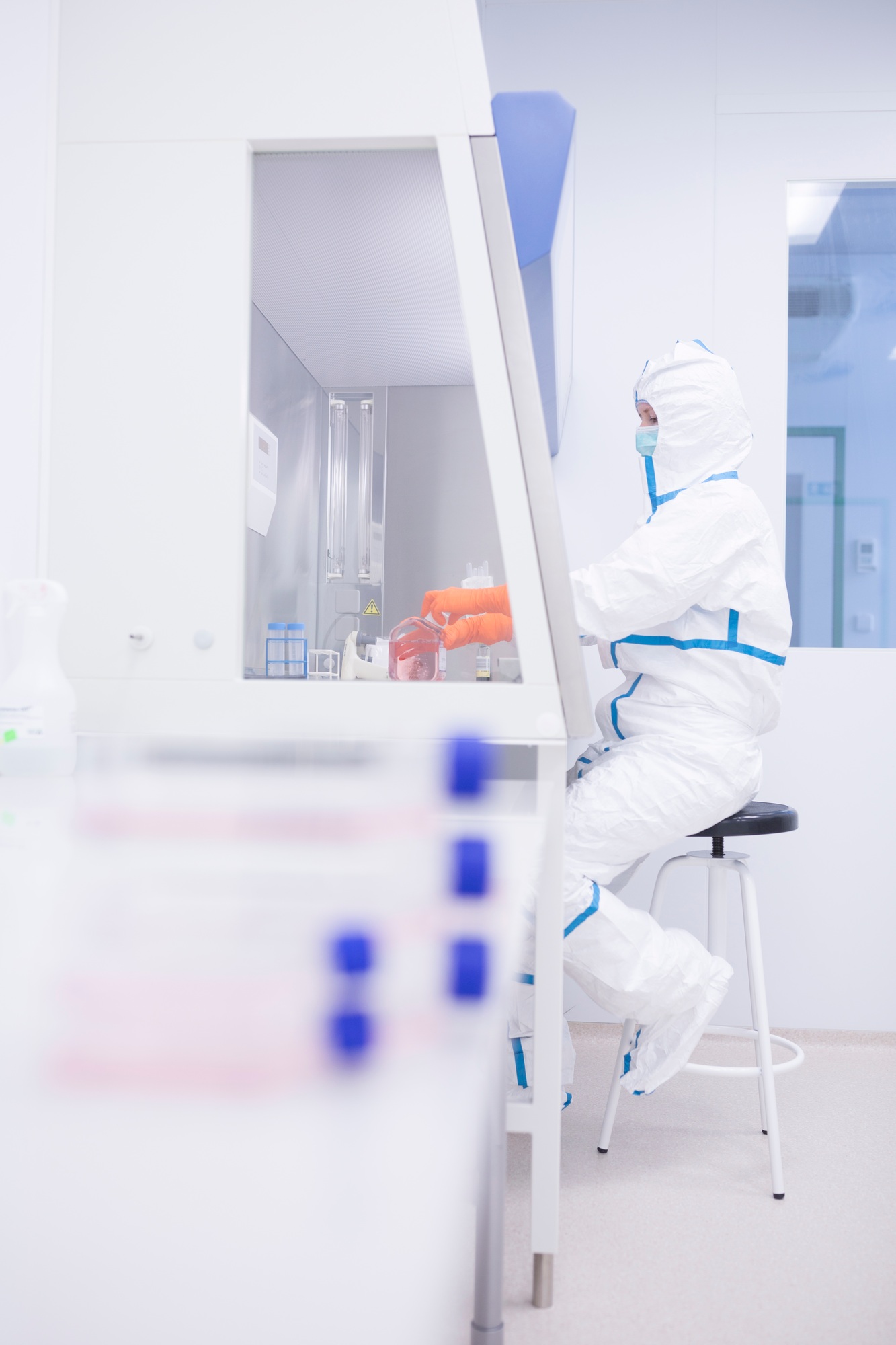
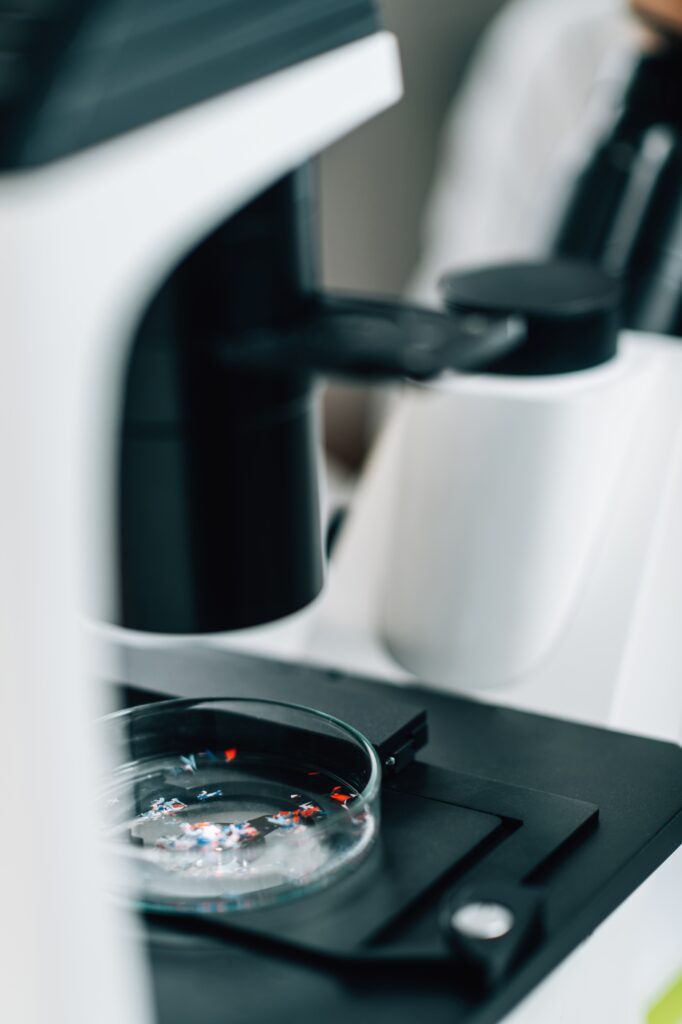
Key Sections of ISO 14644
Key sections guide manufacturers in cleanroom design, classification, and monitoring to maintain sterile environments. These sections help create controlled conditions required for sensitive production processes. The first part, ISO 14644-1, defines cleanroom classifications by specifying allowable airborne particle concentrations. This classification ensures manufacturers can assign cleanrooms correctly based on process requirements. Next, ISO 14644-2 focuses on monitoring and testing cleanroom performance. Regular testing ensures cleanrooms remain within particle count limits, preventing contamination and ensuring product quality.
In addition to classification and monitoring, ISO 14644-3 details the test methods for cleanroom validation. This section outlines procedures for testing airflow, measuring particle counts, and verifying pressure differences. These methods help manufacturers identify risks early and maintain stable production environments. Meanwhile, ISO 14644-4 addresses cleanroom design and construction, ensuring new cleanrooms meet cleanliness standards from the start. Following these sections allows manufacturers to build and maintain cleanrooms effectively. By adhering to the full scope of ISO 14644, companies improve compliance, product safety, and operational consistency.
Key Risk Management Strategies in Cleanroom Design
Implementing comprehensive risk management strategies ensures cleanrooms maintain optimal performance and reduce contamination risks. Below are additional key strategies:
Airflow Validation
Conduct airflow validation regularly to ensure proper air circulation and prevent cross-contamination. Controlled airflow patterns, such as laminar flow, direct clean air in a specific direction, reducing particle spread.
Regular Maintenance
Perform routine maintenance on cleanroom equipment to ensure optimal performance and minimize failures. Well-maintained systems, such as air filters and HVAC units, help sustain the required cleanliness levels.
Employee Training
Provide thorough training for employees to reduce human errors that could cause contamination. Ensure workers understand proper gowning, hygiene protocols, and cleanroom procedures to maintain a controlled environment.
Proper Gowning Procedures
Enforce strict gowning protocols to prevent particles from entering cleanrooms through clothing. Require personnel to use appropriate cleanroom garments, gloves, masks, and shoe covers to reduce contamination risks.
Strict Material Handling
Use validated materials and cleanroom-compatible tools to prevent the introduction of contaminants. Ensure materials entering the cleanroom undergo proper decontamination and storage procedures.
By implementing these risk management strategies, manufacturers create a controlled, safe environment that supports sterile production and meets regulatory expectations.
Cleanroom Design: Ensuring Compliance
ISO Classifications vs. Regulatory Compliance
Understanding the connection between ISO classifications and regulatory compliance is essential for effective cleanroom design. ISO classifications set particle limits for various cleanroom environments, ensuring manufacturers maintain proper cleanliness levels. These standards help create controlled environments where sensitive pharmaceutical products can be safely manufactured. However, regulatory bodies like the FDA and EMA go beyond just particle control. They establish additional requirements focusing on manufacturing processes, product sterility, and thorough documentation.
To meet both ISO and regulatory requirements, manufacturers need to carefully align their cleanroom designs. This process involves selecting the appropriate ISO class for the cleanroom and ensuring adherence to GMP guidelines. Proper alignment helps reduce contamination risks, improve product consistency, and avoid regulatory penalties. Additionally, manufacturers must validate their cleanrooms regularly to maintain compliance and avoid unexpected issues during inspections. Balancing ISO classifications with regulatory expectations ensures cleanrooms remain reliable and compliant, protecting both product quality and company reputation.
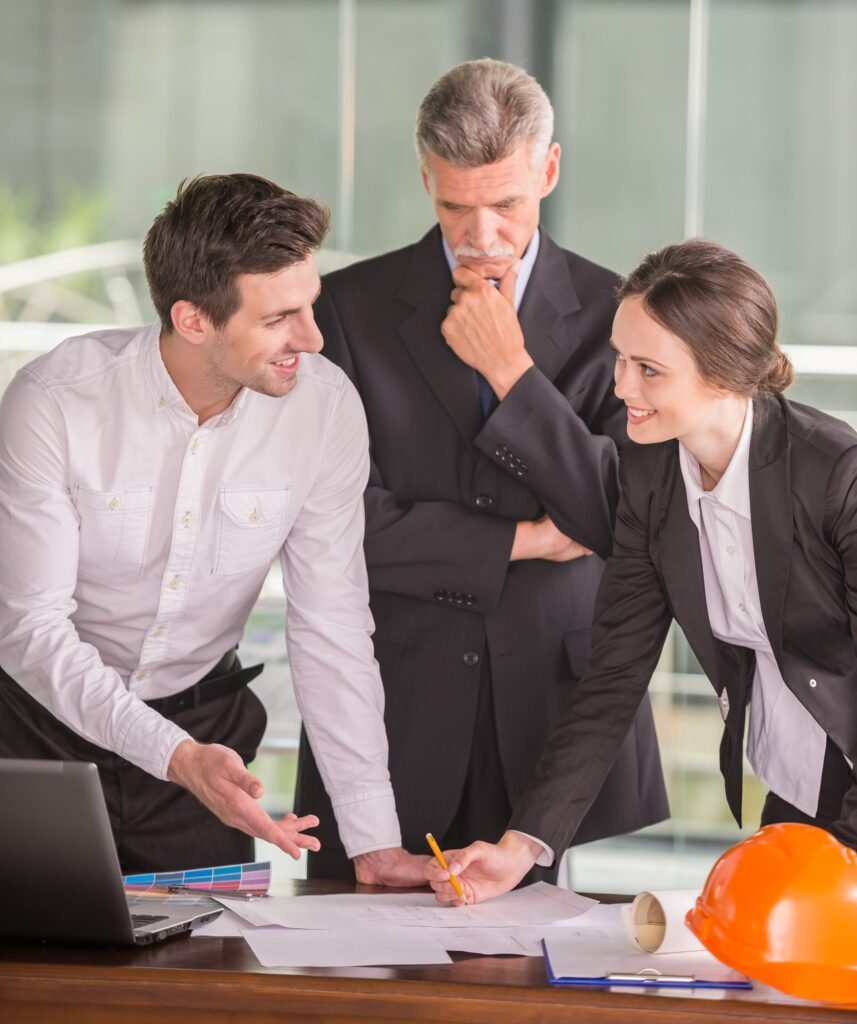
Ensuring Compliance through Design
Manufacturers achieve compliance by integrating ISO standards and regulatory guidelines into every aspect of cleanroom design. They start by selecting the correct ISO class, which determines particle limits and required cleanliness levels. Next, they design cleanrooms with effective airflow control, advanced filtration systems, and strict access protocols. These design elements reduce contamination risks and maintain clean environments during critical production processes.
Additionally, companies must ensure their cleanroom practices align with GMP regulations. This includes proper employee training, consistent monitoring, and maintaining detailed records for inspections. Conducting regular audits helps identify issues early, preventing costly production delays. By following these practices, manufacturers can improve operational efficiency, enhance product safety, and maintain trust with regulatory agencies. Combining ISO standards with regulatory compliance ensures cleanrooms meet stringent quality requirements, supporting long-term business success.
Types of Cleanroom Contaminants
Particulate Matter
Includes dust, fibers, and skin flakes that can compromise sterile environments during production.
Microbial Contaminants
Bacteria, fungi, and viruses pose significant risks to product safety and efficacy.
Chemical Vapors
Volatile organic compounds (VOCs) from cleaning agents or raw materials can disrupt sensitive processes.
Electrostatic Charges
Electrostatic buildup attracts particles, leading to increased contamination risks in critical areas.
Process-Generated Contaminants
Equipment operations, such as cutting or grinding, can produce particles and aerosols that compromise cleanliness.
Key Cleanroom Design Requirements
Key cleanroom design requirements help manufacturers maintain a controlled environment and prevent contamination. Air filtration systems form the backbone of cleanroom cleanliness by removing airborne particles. HEPA and ULPA filters ensure that only clean, filtered air enters the room.
Additionally, controlled airflow patterns, such as unidirectional or laminar flow, help keep particles from settling on surfaces. Proper airflow design reduces cross-contamination risks during critical operations. Manufacturers who implement these systems improve product quality and meet cleanliness standards consistently.
Seamless surfaces further enhance cleanroom performance by minimizing particle accumulation and making cleaning easier. Using smooth, non-porous materials for walls, floors, and ceilings helps prevent microbial growth. Consistent temperature and humidity control is also essential for sensitive processes. Fluctuations in environmental conditions can compromise product stability and sterility. Installing reliable HVAC systems ensures cleanrooms maintain optimal conditions throughout production. Finally, manufacturers must enforce strict access control systems to limit contamination from personnel. Airlocks and gowning rooms help reduce pollutants entering the cleanroom.
Conclusion
Cleanroom design is essential for sterile manufacturing success. By controlling environmental factors, minimizing contaminants, and adhering to ISO standards, manufacturers create safe and efficient production spaces. Proper cleanroom design ensures product quality, regulatory compliance, and long-term operational efficiency. Investing in cleanroom design is a strategic move that builds trust, supports business growth, and safeguards patient safety.
References
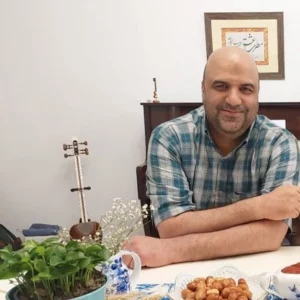
Ershad Moradi
Ershad Moradi, a Content Marketing Specialist at Zamann Pharma Support, brings 6 years of experience in the pharmaceutical industry. Specializing in pharmaceutical and medical technologies, Ershad is currently focused on expanding his knowledge in marketing and improving communication in the field. Outside of work, Ershad enjoys reading and attending industry related networks to stay up-to-date on the latest advancements. With a passion for continuous learning and growth, Ershad is always looking for new opportunities to enhance his skills and contribute to pharmaceutical industry. Connect with Ershad on Facebook for more information.
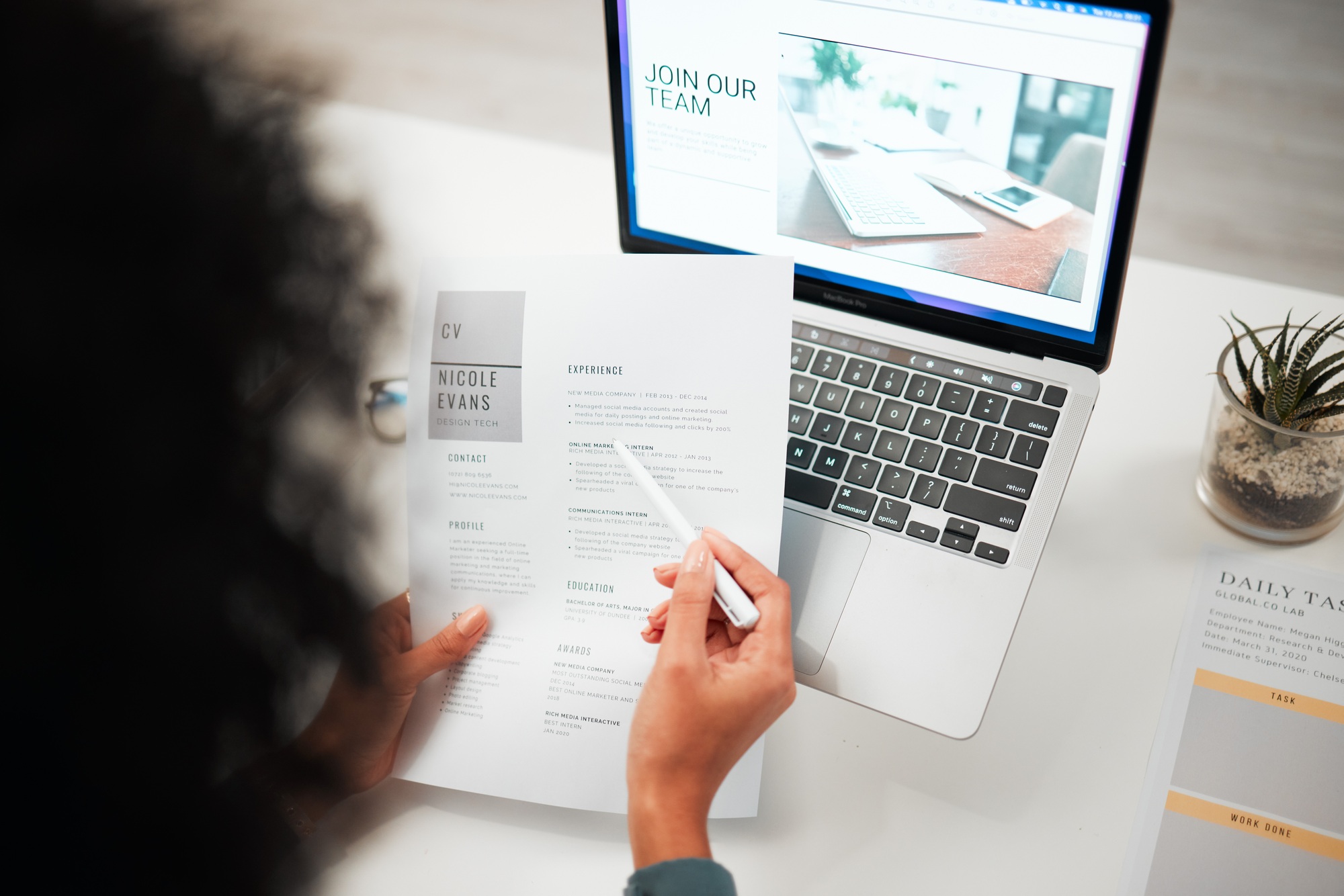
How to Choose the Right Special Skills for Resume Success
Learn how to choose, organize, and present special skills for resume success. This guide includes technical and soft skills, comparison tables, and AI-friendly strategies to pass ATS filters and stand out in competitive job markets.
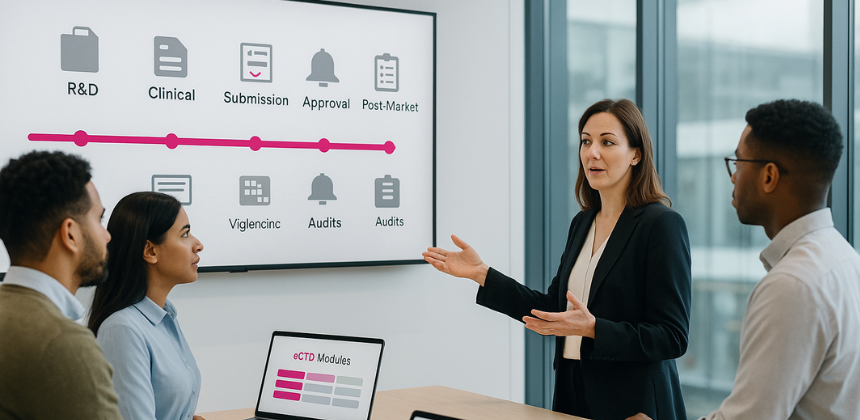
Career Path in Regulatory Affairs: A Step-by-Step Learning Map
Want a clear career path in regulatory affairs? This guide maps each stage—from assistant to director—with practical skills, templates, and quarterly goals. You master eCTD, labeling, change control, risk, and stakeholder leadership. Then you apply the plan to a live project and track real wins.
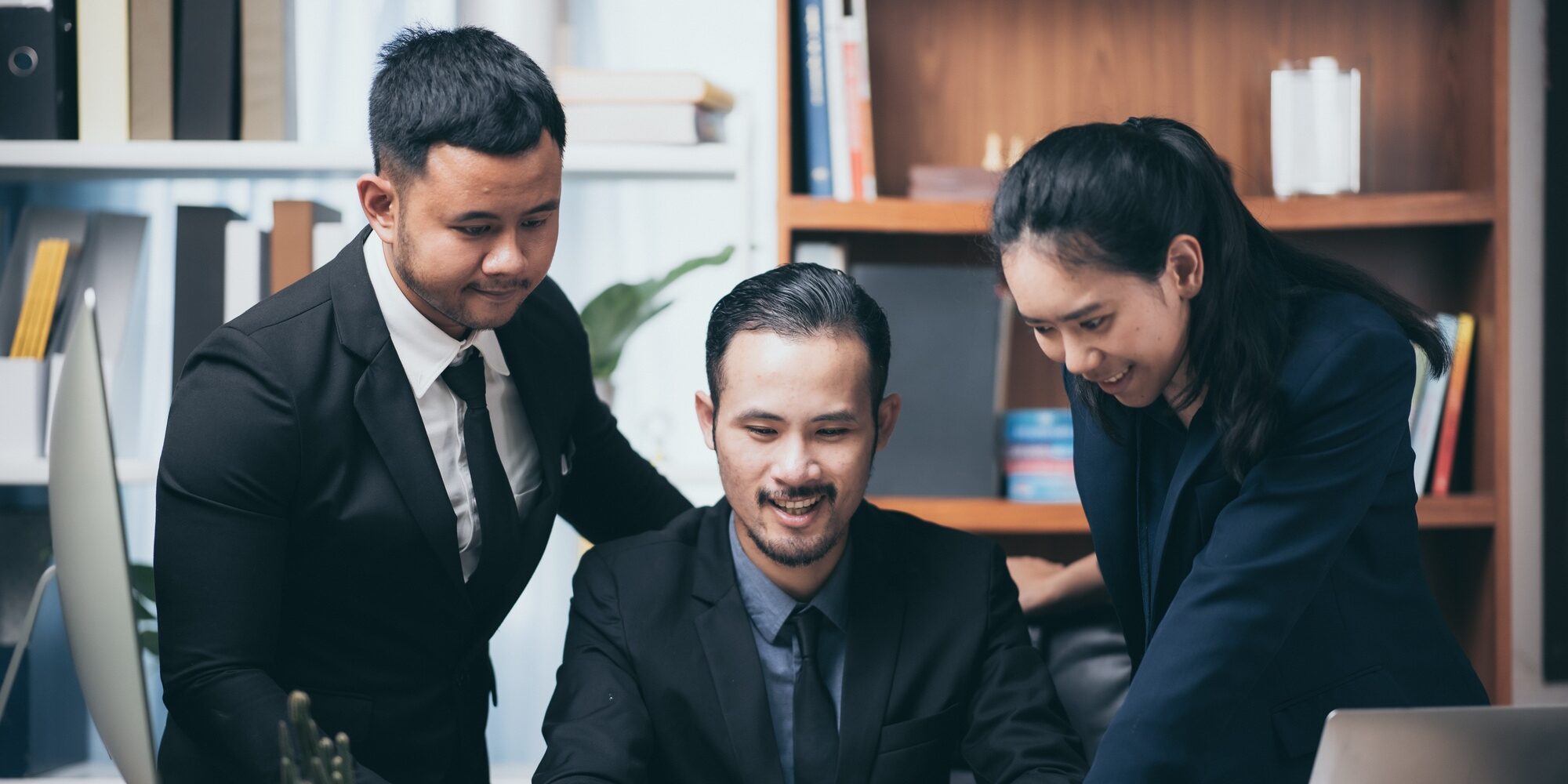
Pharma Regulatory Services: What You Must Know
Pharma regulatory services are essential for product safety, compliance, and success. This guide breaks down everything professionals need to know—from FDA submissions to global frameworks. Get actionable tips, comparison tables, and best practices to thrive in this highly regulated field.