Change control is a critical component in the pharmaceutical industry, ensuring that processes, equipment, and documentation remain consistent and compliant with regulations. It serves as the backbone of quality assurance, minimizing risks while maintaining product integrity and patient safety. With increasingly stringent global regulations, pharma companies must implement robust change control strategies to navigate complex compliance landscapes.
This article outlines the essential components of change control, its objectives, procedures, and best practices, helping pharma organizations maintain efficiency and compliance.
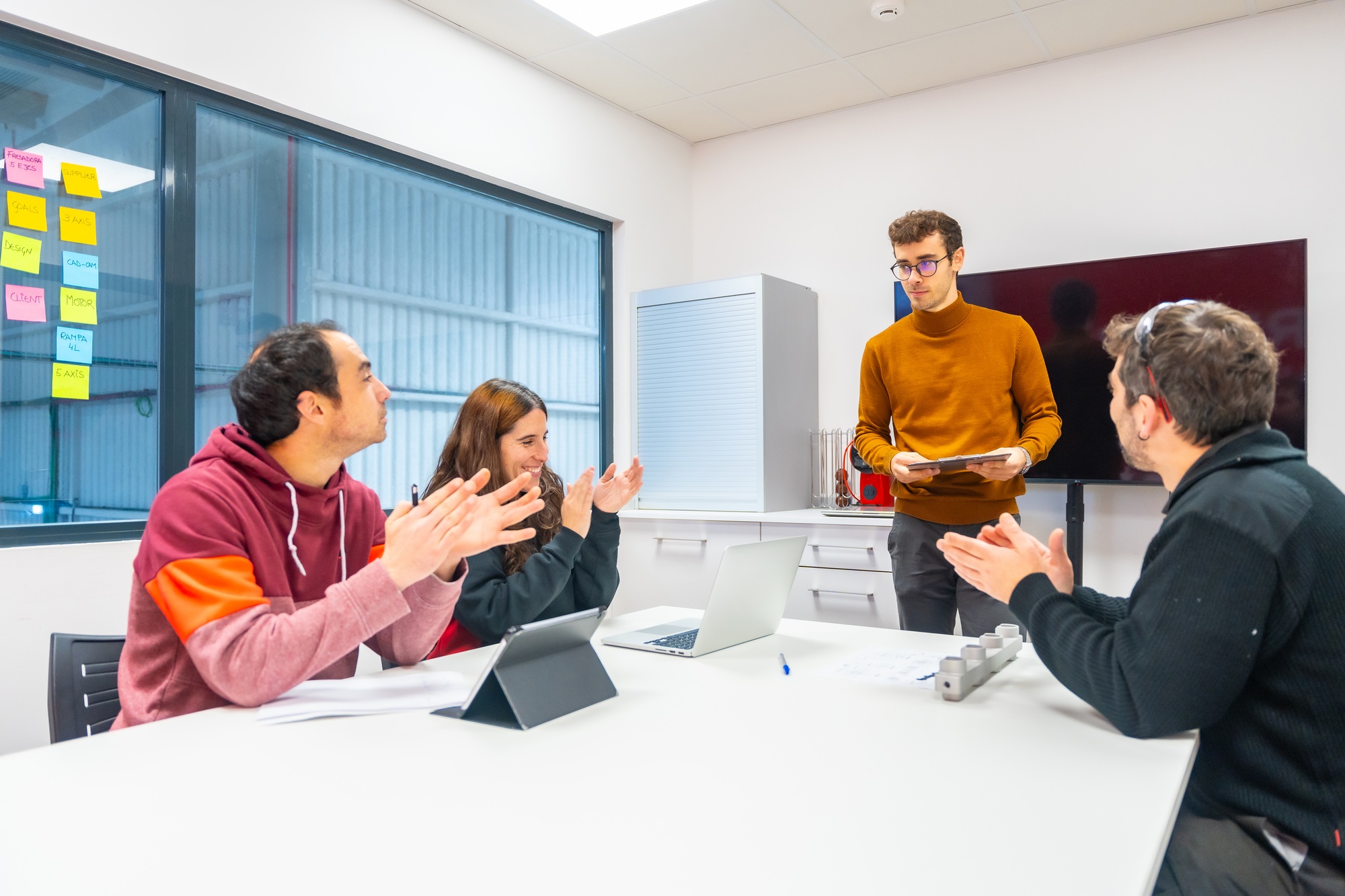
What is Change Control?
Change control refers to a structured approach that manages changes in processes, systems, or documentation in a pharmaceutical environment. This method evaluates, authorizes, and implements changes systematically, ensuring consistency and reducing disruptions. By following a clear process, companies can identify potential risks and address them before they cause problems. Additionally, change control ensures compliance with strict regulatory standards, which are essential in the pharma industry. Organizations that adopt robust change control frameworks gain better oversight, enabling them to respond to changes effectively. Moreover, they can maintain operational stability while adapting to industry advancements.
In the pharmaceutical industry, change control protects product quality and patient safety. It ensures that manufacturing processes and related operations remain consistent and reliable. Without a strong change control process, companies face risks like non-compliance and product recalls. Such issues can harm a company’s reputation and compromise patient health. Therefore, well-defined change control procedures are critical for success in this highly regulated sector. Furthermore, these procedures enable companies to stay compliant while improving efficiency and collaboration. By managing changes effectively, organizations can minimize risks, meet regulatory expectations, and maintain trust in their products.
Sign up for Introduction to GMP Quality Management Systems Course
Key Procedures for Change Control Implementation
Document all proposed changes, including a clear description, rationale, and potential impact on operations and compliance.
Evaluate how the change affects processes, quality, and compliance, considering risks and mitigation strategies.
Secure approvals from relevant stakeholders, including quality assurance, production, and regulatory teams, before proceeding.
Develop a detailed plan outlining steps, timelines, and responsibilities for executing the change.
Oversee the implementation process to ensure adherence to approved protocols and identify any issues early.
Conduct post-implementation reviews to confirm success and document findings for continuous improvement.
Fast-track your career with VIP consultation
Main Objectives of Change Control in Pharma
Ensuring Regulatory Compliance
Change control ensures that all modifications in the pharmaceutical industry comply with regulatory requirements. It helps companies align their processes with standards set by FDA, EMA, and other global authorities. This alignment allows organizations to meet legal obligations and avoid costly penalties. Additionally, change control prevents delays in product approvals by addressing compliance issues early. With a structured process, companies can quickly identify potential risks and take corrective actions. As a result, they maintain a smooth workflow and avoid disruptions in manufacturing or distribution. Furthermore, this approach builds trust with regulators and strengthens market access strategies.
By implementing change control, companies safeguard their products and ensure consistent quality. Regulatory bodies emphasize compliance to protect patient safety and maintain product reliability. Therefore, adhering to these standards minimizes risks and supports the approval of pharmaceutical products. Moreover, change control provides a transparent framework for managing modifications, which improves communication with regulatory agencies. This transparency helps demonstrate compliance during inspections and audits. Companies that prioritize change control also enhance their reputation in the industry. Ultimately, a robust change control system allows organizations to meet regulatory expectations and achieve long-term success.
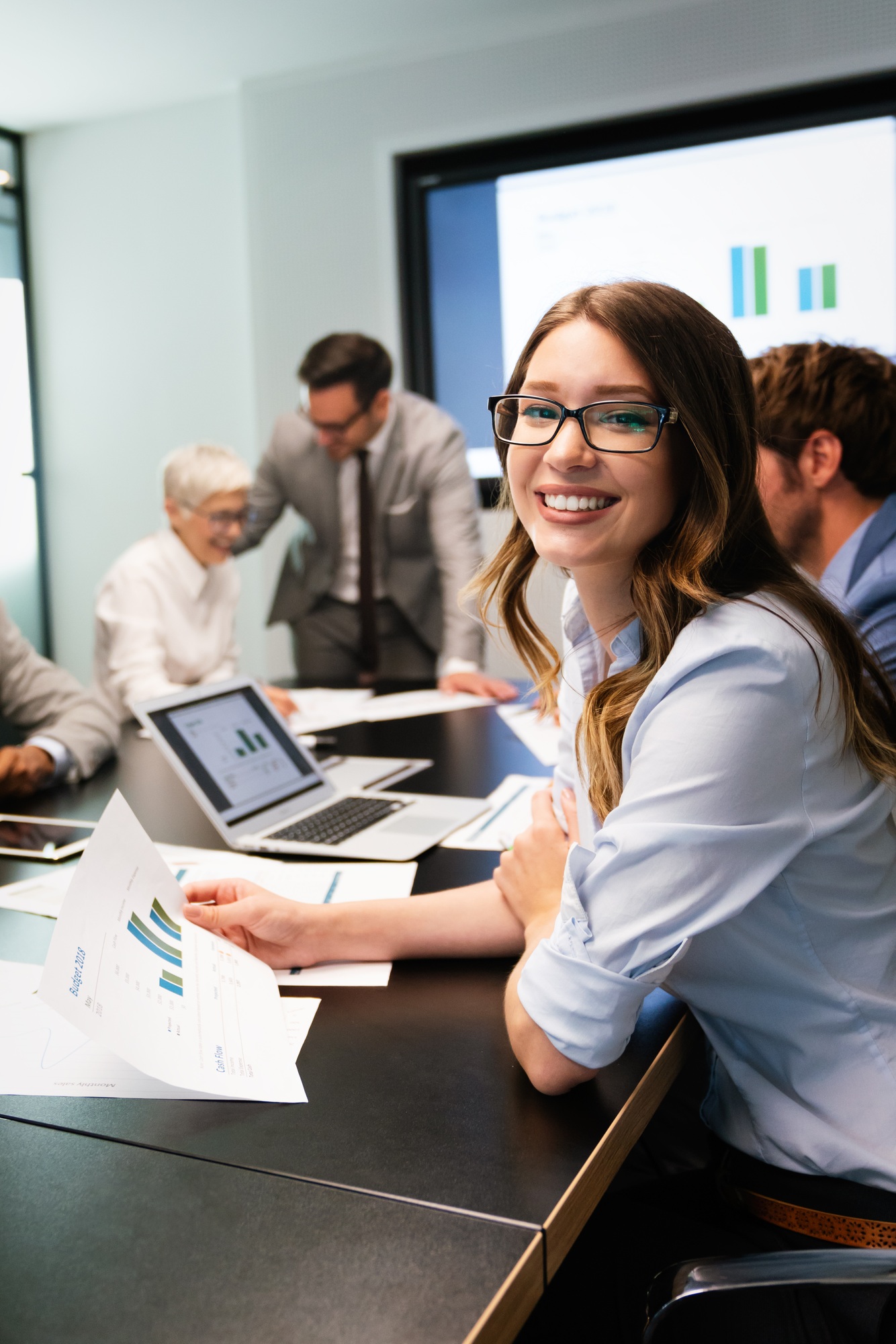
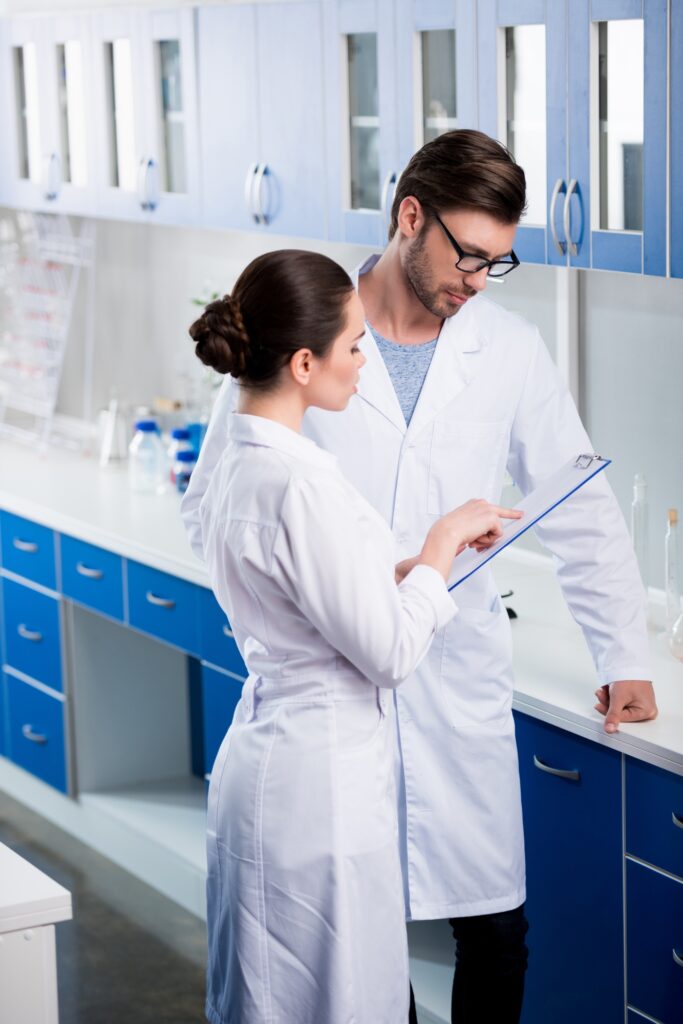
Safeguarding Product Quality
Effective change control protects product quality by minimizing deviations during manufacturing and distribution. It ensures that processes remain consistent and aligned with established standards, reducing risks of errors. When companies implement change control, they proactively address potential issues before they affect operations. This approach helps maintain the integrity of products, ensuring they meet quality specifications. Additionally, consistent quality reassures stakeholders and builds trust with consumers. By minimizing deviations, companies also avoid costly rework or recalls, which can disrupt supply chains. Furthermore, effective change control improves overall efficiency, allowing smoother operations and better resource utilization.
Change control safeguards the end-user by ensuring that pharmaceutical products meet safety requirements. When companies manage changes effectively, they protect patients from harmful deviations or quality lapses. This level of care strengthens the reliability of pharmaceutical products in the market. Furthermore, ensuring consistent quality enhances a company’s reputation and fosters consumer confidence. Trust in pharmaceutical products grows when customers experience reliability and safety. Companies that prioritize change control also comply with regulatory standards, which reinforces public trust. In the long run, effective change control not only protects end-users but also secures business success.
Guidelines for Robust Change Control Processes
Establish Clear Policies
Define comprehensive policies and standard operating procedures (SOPs) to manage change requests systematically.
Train Employees Effectively
Conduct regular training sessions to ensure that employees understand the importance of change control and follow protocols.
Utilize Advanced Tools
Implement digital platforms to track, assess, and document changes efficiently, improving accuracy and accessibility.
Incorporate Risk Assessments
Integrate risk assessment methodologies to identify potential impacts and devise mitigation strategies for proposed changes.
Perform Regular Audits
Conduct periodic reviews of change control processes to identify gaps and ensure continuous improvement.
Maintain Cross-Functional Collaboration
Foster collaboration among quality assurance, production, and regulatory teams to streamline decision-making.
Steps to Effective Issue and Change Management
Addressing Issues Through Documentation
To manage issues effectively, always record details comprehensively and consistently. Maintain detailed logs of all issues, including the time they occur and affected areas. This documentation helps identify patterns and root causes quickly, improving response times. By including information about the potential impact on quality or compliance, teams can make informed decisions. Additionally, detailed records provide a solid foundation for audits and regulatory reviews. When you document issues thoroughly, you enhance transparency and accountability across the organization. Moreover, this practice allows seamless communication among teams, ensuring everyone stays informed and aligned. Regularly updating logs also ensures that critical information remains accurate and accessible.
After documenting issues, evaluate their severity and prioritize actions based on urgency. Assess how each issue impacts processes, quality, or compliance to determine its importance. This prioritization helps allocate resources effectively, focusing attention on high-risk problems first. Addressing critical issues promptly minimizes disruptions and prevents further complications. Moreover, a structured evaluation process ensures that minor issues do not overshadow significant concerns. By ranking issues clearly, teams can create a manageable action plan to resolve them efficiently.
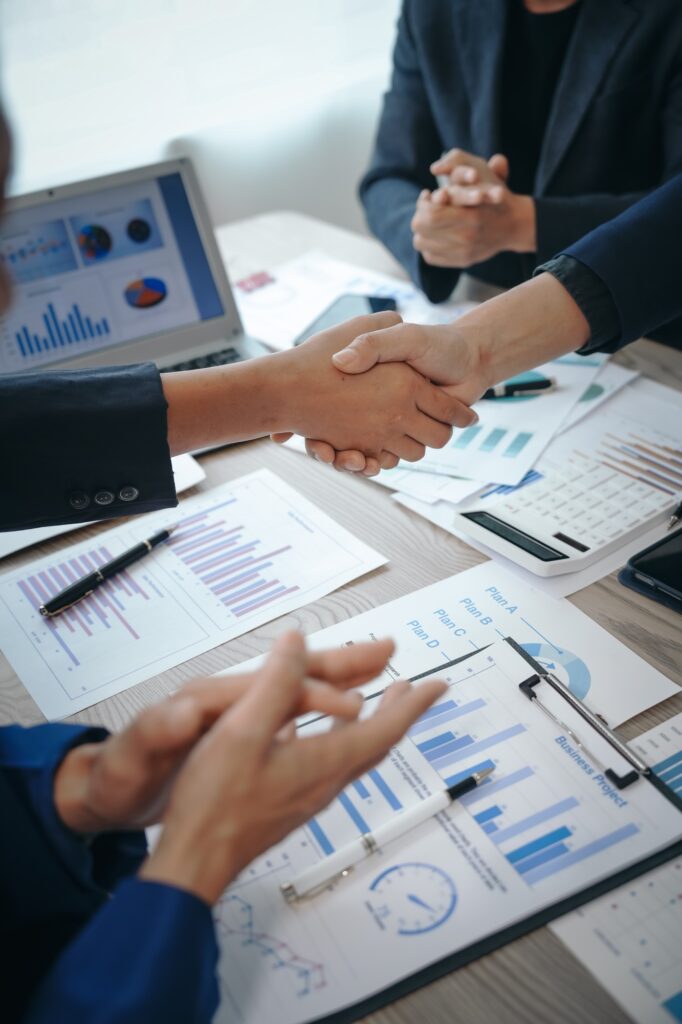
Implementing Change Management Systems
Streamline communication to ensure all stakeholders stay informed throughout the change management process. Clear communication prevents misunderstandings and keeps everyone aligned with the project goals. Use regular updates, team meetings, and concise documentation to share essential information. Additionally, encourage open discussions to address concerns or questions promptly. When teams understand their roles and responsibilities, they can work together more effectively. Streamlined communication also reduces delays caused by confusion or missed updates. Furthermore, using digital tools for collaboration enhances transparency and accessibility. By maintaining clear communication, organizations improve teamwork and ensure smoother implementation of changes.
Monitor and review outcomes regularly to confirm the success of implemented changes. Evaluate how changes impact processes, quality, and compliance, using measurable criteria to track results. This evaluation helps identify areas that need improvement or additional support. Document lessons learned during the review process to enhance future change management efforts. Additionally, sharing these insights with the team builds collective knowledge and avoids repeating mistakes. Monitoring outcomes also ensures that implemented changes align with regulatory requirements and business objectives. Regular reviews enable organizations to adapt quickly if unexpected issues arise. By consistently monitoring and reviewing, companies maintain control over changes and drive continuous improvement.
Building a Culture of Change Control Excellence
Building a culture of change control excellence requires organizations to prioritize continuous employee engagement. When employees understand the importance of change control, they become active participants in maintaining compliance. Regular training sessions and open communication help reinforce this understanding across all teams. By creating a collaborative environment, companies ensure that employees contribute valuable insights during the change management process. Additionally, involving staff in decision-making increases their commitment to adhering to protocols. Strong engagement not only boosts compliance but also fosters a sense of ownership among team members, which enhances overall efficiency.
Proactive risk management forms another cornerstone of a strong change control culture. Identifying potential risks early allows teams to develop strategies that mitigate their impact effectively. Leveraging technology further strengthens this approach by streamlining risk assessments and automating routine tasks. Advanced tools also improve documentation and tracking, ensuring transparency in the change process. By embedding these practices into daily operations, companies align compliance with innovation. This alignment supports regulatory adherence while driving operational improvements. Building this culture ultimately ensures that organizations adapt seamlessly to industry demands while maintaining product quality and safety.
Best Practices for Sustained Change Control Success
Approval Timeframes
Track how long change requests take to move through the approval process. Shorter approval times reflect efficient workflows and help maintain project momentum.
Implementation Accuracy
Measure the success of implemented changes by monitoring deviations or execution issues. High accuracy ensures changes meet quality standards and align with regulatory requirements.
Stakeholder Communication
Establish clear and consistent communication among all stakeholders during change control processes. Regular updates prevent misunderstandings and keep everyone aligned with project goals.
Risk Assessment
Evaluate potential risks for each proposed change to prioritize actions and allocate resources effectively. Addressing risks early minimizes disruptions and supports smooth implementation.
Continuous Monitoring
Regularly review and monitor changes after implementation to confirm success and identify issues. Ongoing evaluation helps refine processes and fosters continuous improvement.
Documentation Standards
Maintain detailed and accurate documentation for all changes, including approvals and outcomes. Clear records improve transparency, support audits, and enhance organizational knowledge for future initiatives.
Conclusion
In conclusion, implementing robust change control strategies ensures compliance and operational excellence in the pharmaceutical industry. By adopting a structured approach, organizations can manage changes effectively while maintaining product quality and patient safety. Clear procedures, such as documenting requests and assessing impacts, streamline the process and minimize disruptions. Furthermore, aligning with regulatory standards protects companies from penalties and supports timely product approvals. When teams work collaboratively and communicate openly, they address challenges efficiently and drive continuous improvement. These practices not only safeguard compliance but also enhance organizational resilience in a dynamic industry.
Building a culture of change control excellence requires commitment, proactive risk management, and leveraging advanced tools. Organizations that prioritize employee engagement and training empower their teams to uphold compliance consistently. By tracking metrics like approval timeframes and implementation accuracy, companies can measure success and refine their processes. Regular monitoring and transparent documentation strengthen trust with regulators and stakeholders alike. Ultimately, sustained change control success fosters innovation, operational efficiency, and long-term growth. With these strategies, pharmaceutical companies can adapt to evolving demands while delivering safe and reliable products to the market.
References
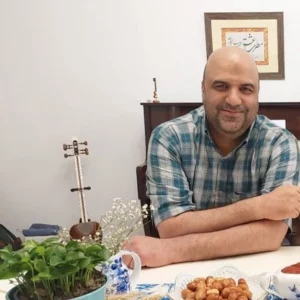
Ershad Moradi
Ershad Moradi, a Content Marketing Specialist at Zamann Pharma Support, brings 6 years of experience in the pharmaceutical industry. Specializing in pharmaceutical and medical technologies, Ershad is currently focused on expanding his knowledge in marketing and improving communication in the field. Outside of work, Ershad enjoys reading and attending industry related networks to stay up-to-date on the latest advancements. With a passion for continuous learning and growth, Ershad is always looking for new opportunities to enhance his skills and contribute to pharmaceutical industry. Connect with Ershad on Facebook for more information.
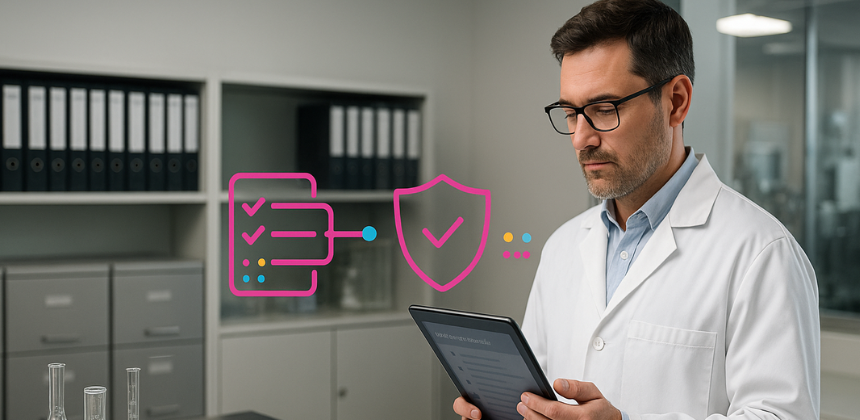
GMP Audit Checklist: Pass Your Next Inspection With Confidence
Use this gmp audit checklist to see if you would pass today. Run a 10-minute self-test, verify evidence, and prioritize fixes. Then follow 30- and 90-day plans to strengthen data integrity, CAPA, Annex 1, training, and documentation. Build proof that convinces auditors, reduces risk, and keeps your site inspection-ready year-round.
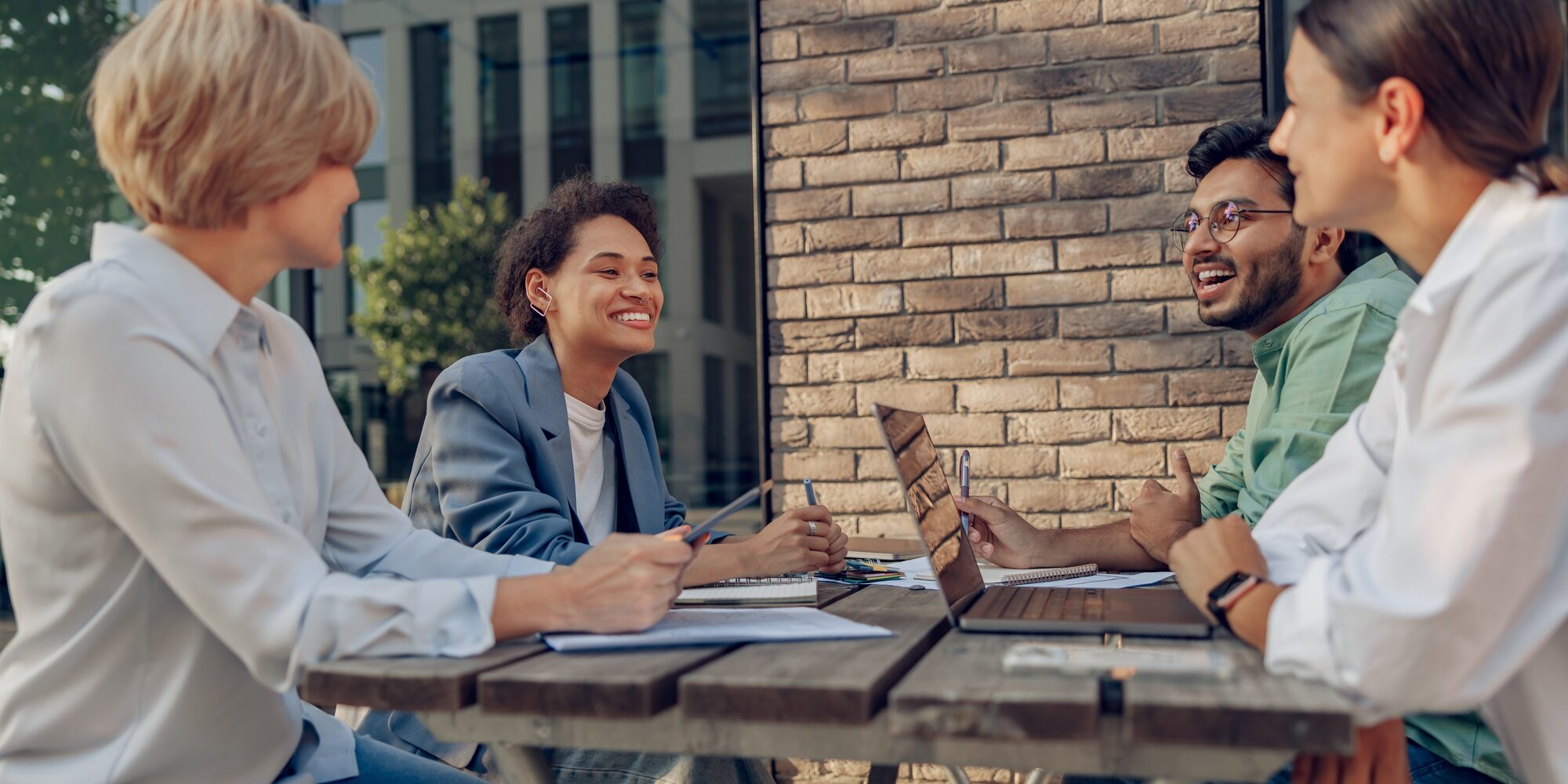
Pharma Sales Secrets to Skyrocket Success
Pharma sales is more than just selling medications. It combines science, strategy, and relationship building. Whether you’re starting out or refining your approach, this guide gives you practical tools, career insights, and tips to succeed in today’s competitive pharmaceutical sales industry.
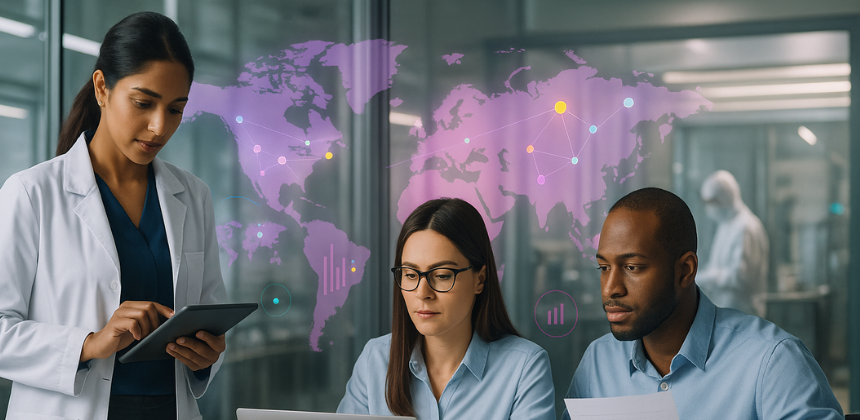
Pharma Job Market Trends: What’s Hot Now
Pharma job market trends show sustained growth across quality, regulatory affairs, pharmacovigilance, and data. New modalities, including cell and gene therapy, expand validation and aseptic roles quickly. Meanwhile, digital tools reshape trials, manufacturing, and safety reporting. Therefore, candidates who blend science, GxP, and analytics win more interviews.