In the pharmaceutical industry, Good Manufacturing Practice (GMP) audits play a critical role in maintaining high-quality standards and regulatory compliance. Conducting internal GMP audits is essential for identifying gaps, enhancing processes, and ensuring products meet both quality and safety requirements.
This article provides a comprehensive guide to performing internal GMP audits effectively, with a step-by-step approach to creating robust auditing processes. Whether you’re looking to enhance compliance or improve operational efficiency, these insights will help streamline your auditing practices and support a successful GMP framework.
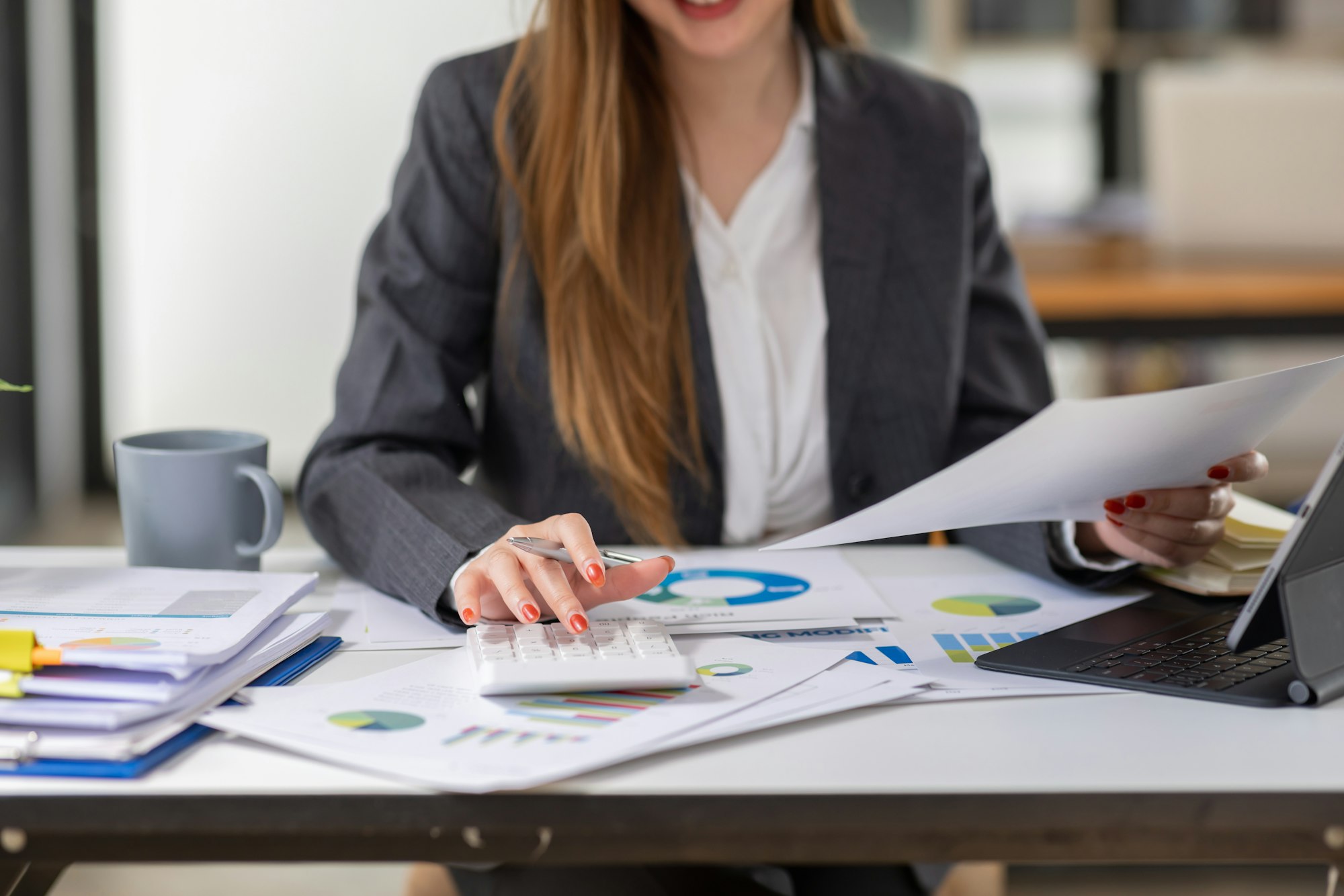
The Role of Internal GMP Audits in Quality Assurance
Conducting regular internal GMP audits forms the backbone of every quality management system in the pharmaceutical industry. These audits allow companies to assess their processes, detect deviations, and maintain regulatory compliance. By proactively evaluating their operations, pharmaceutical organizations can identify and address issues early, which helps prevent costly mistakes, regulatory penalties, and threats to public safety. More importantly, these audits provide ongoing opportunities for improvement, which empowers companies to continuously elevate their quality standards.
GMP audits do more than ensure compliance; they promote efficiency and consistency across operations. When organizations conduct audits routinely, they foster a quality-focused culture that spans the entire company.
Employees become more aware of compliance requirements, which enhances operational transparency and accountability. This proactive approach establishes a strong foundation for quality, driving success and resilience in an industry where product safety and adherence to standards are paramount.
Sign up for Preparing for GMP Audits Course
Steps to Prepare for an Effective GMP Audit
Before conducting any audit, establish clear objectives that align with regulatory and organizational goals. A well-defined objective sets the scope, allowing auditors to focus on specific areas of improvement.
Choose auditors with the expertise and knowledge to assess GMP compliance effectively. They should understand the processes they will evaluate and know how to identify potential non-compliance risks.
Develop an audit plan outlining areas of focus, timelines, and personnel involved. An organized plan ensures that all audit aspects are covered systematically.
Gather all relevant documents, including SOPs, process maps, and previous audit reports. Adequate documentation provides auditors with the context they need for a thorough evaluation.
Schedule the audit to minimize disruptions in daily operations while allowing sufficient time for a detailed review. Plan audits during periods of regular operation to gain an accurate picture of compliance.
Inform departments of the upcoming audit to ensure their cooperation and preparedness. Transparent communication builds trust and enhances the efficiency of the auditing process.
Managing Deviations During GMP Audits
Types of Deviations to Identify
Deviations occur when actions or conditions fail to meet GMP standards. Recognizing these deviations helps companies address issues early, preventing larger problems.
Deviations can appear at any stage of production, making it essential to detect them quickly. When companies catch deviations promptly, they avoid costly errors and improve product safety. Proactively managing these issues strengthens quality control, which ensures better compliance with GMP requirements.
There are three main types of deviations: minor, major, and critical. Minor deviations involve small inconsistencies that don’t impact product quality significantly. However, major deviations indicate serious flaws in processes, which can compromise quality.
Most importantly, critical deviations pose risks to product safety, potentially endangering public health. By categorizing deviations this way, companies can respond appropriately and focus on maintaining high standards. Identifying and resolving these deviations quickly helps ensure that all products meet regulatory and safety requirements.
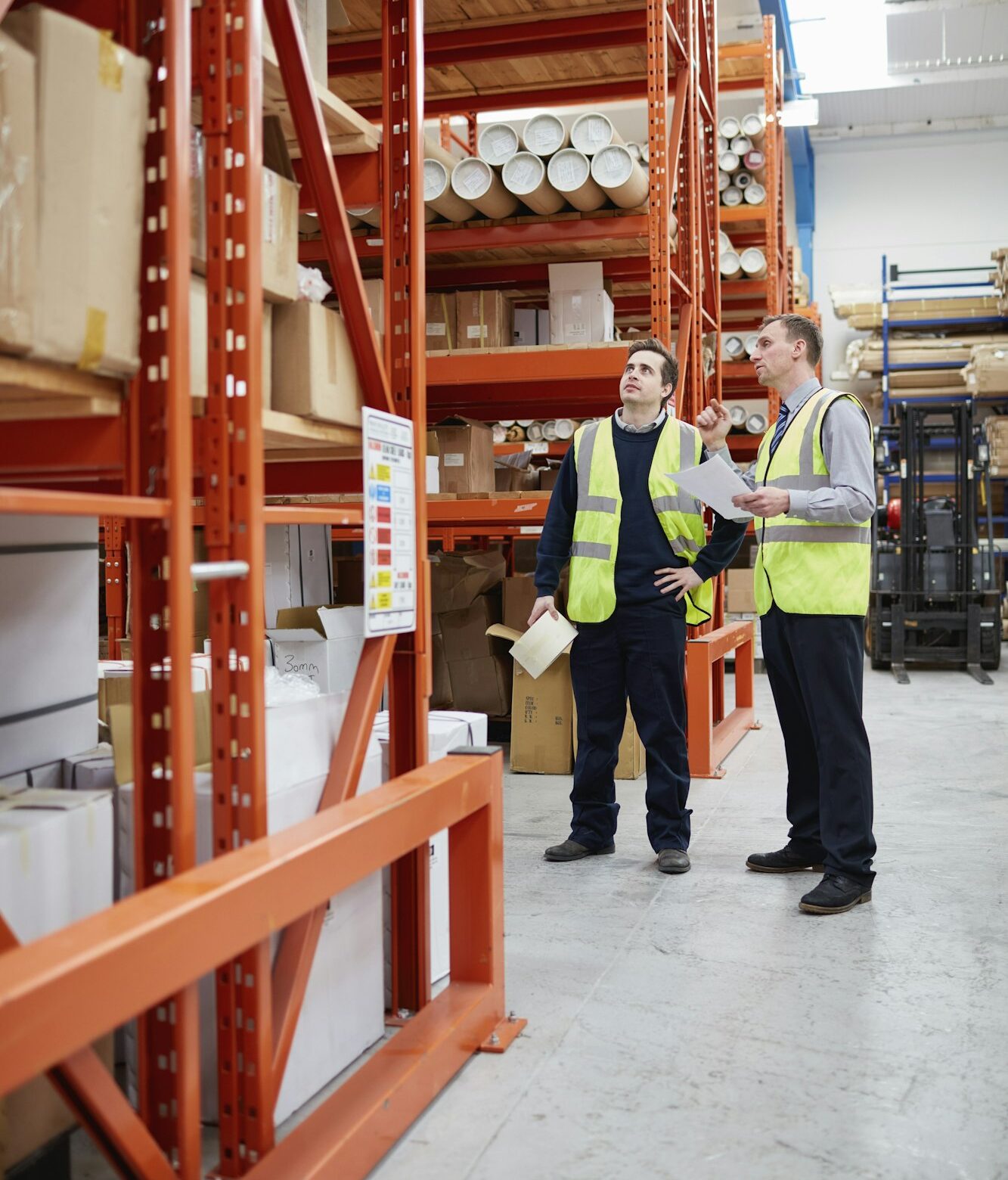
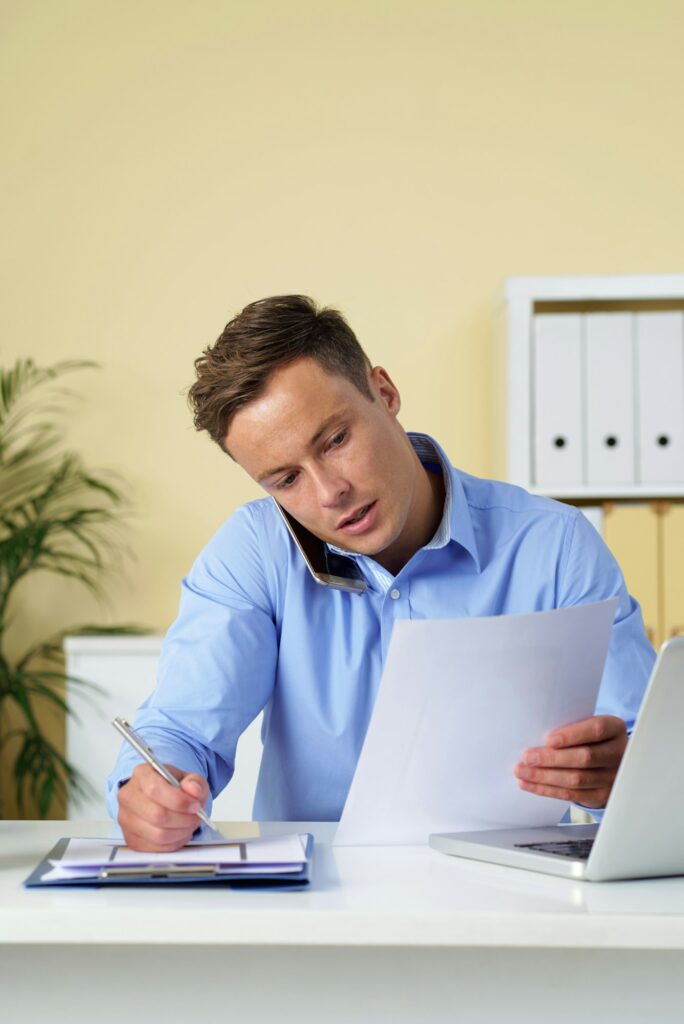
Recording Deviations Accurately
Recording deviations accurately is a foundational step in maintaining GMP compliance and ensuring quality standards. A well-documented deviation report includes a clear description of the issue, the exact processes affected, and a thorough assessment of potential risks. This information guides the team in assessing the full impact of the deviation, both immediately and in the long term. Proper documentation empowers auditors and regulatory bodies to review the company’s corrective measures, ensuring compliance with GMP requirements.
Root cause analysis is crucial after identifying and documenting a deviation. It involves investigating why the deviation occurred and pinpointing contributing factors. Teams may examine equipment performance, employee procedures, and environmental conditions to determine the root cause. By thoroughly understanding what led to the issue, companies can implement corrective actions that address the problem’s source rather than just its symptoms. Effective corrective actions improve operational resilience and reduce the likelihood of similar deviations in the future.
Moreover, accurate deviation records support continuous improvement and help build a culture of accountability. Over time, these records reveal patterns in processes, helping teams identify areas for improvement.
Key Areas to Evaluate During a GMP Audit
Documentation Compliance
Ensure that all documentation meets regulatory requirements. Consistent and thorough records are essential to demonstrate compliance during an external audit.
Personnel Training
Verify that staff members receive adequate training for their roles. Well-trained personnel are crucial to maintaining GMP standards across operations.
Equipment Maintenance
Check that equipment undergoes regular maintenance and calibration. Properly functioning equipment reduces the risk of non-compliance.
Hygiene and Cleanliness
Confirm that facilities are clean and adhere to hygiene standards. Maintaining a clean environment is a fundamental aspect of GMP compliance.
Process Control
Review all processes to ensure they follow established SOPs and regulatory guidelines. Consistent processes contribute to product safety and quality.
The Role of Checklists in GMP Audits
Using checklists in GMP audits is a practical way to maintain consistency and thoroughness. Checklists ensure that auditors cover all necessary areas without missing any essential steps. A well-structured checklist should cover documentation, personnel, equipment, facilities, and operational processes. Each item in the checklist represents a critical compliance element, guiding the auditor through a systematic review of GMP standards.
Use this checklist to confirm that employees are adequately trained and certified.
Effective QMS implementation requires collaboration across departments, from R&D to production and quality control. Ensuring smooth communication between teams is essential for success.
This checklist verifies that equipment maintenance and calibration meet GMP requirements.
Use this list to ensure that facilities meet cleanliness and safety standards.
Training Auditors for Successful GMP Audits
Developing a Training Program for Auditors
Creating a training program for auditors builds the foundation for successful GMP audits. A strong program starts with regulatory knowledge, equipping auditors with a deep understanding of GMP standards and expectations. This knowledge helps auditors assess compliance effectively, ensuring they know what to look for in each audit. Regulatory updates also play a crucial role, so the training should include regular refreshers. With up-to-date knowledge, auditors can stay aligned with current standards, reducing compliance risks.
In addition to regulatory knowledge, process-specific training sharpens auditors’ focus on internal procedures. When auditors understand the exact processes they will evaluate, they conduct audits with more precision. Process knowledge allows auditors to spot deviations quickly and suggest targeted improvements. Alongside this, communication skills are equally essential. Training auditors to share findings constructively promotes collaboration, reducing friction during audits. Effective communication also helps teams act on feedback faster, streamlining corrective actions and boosting overall compliance.
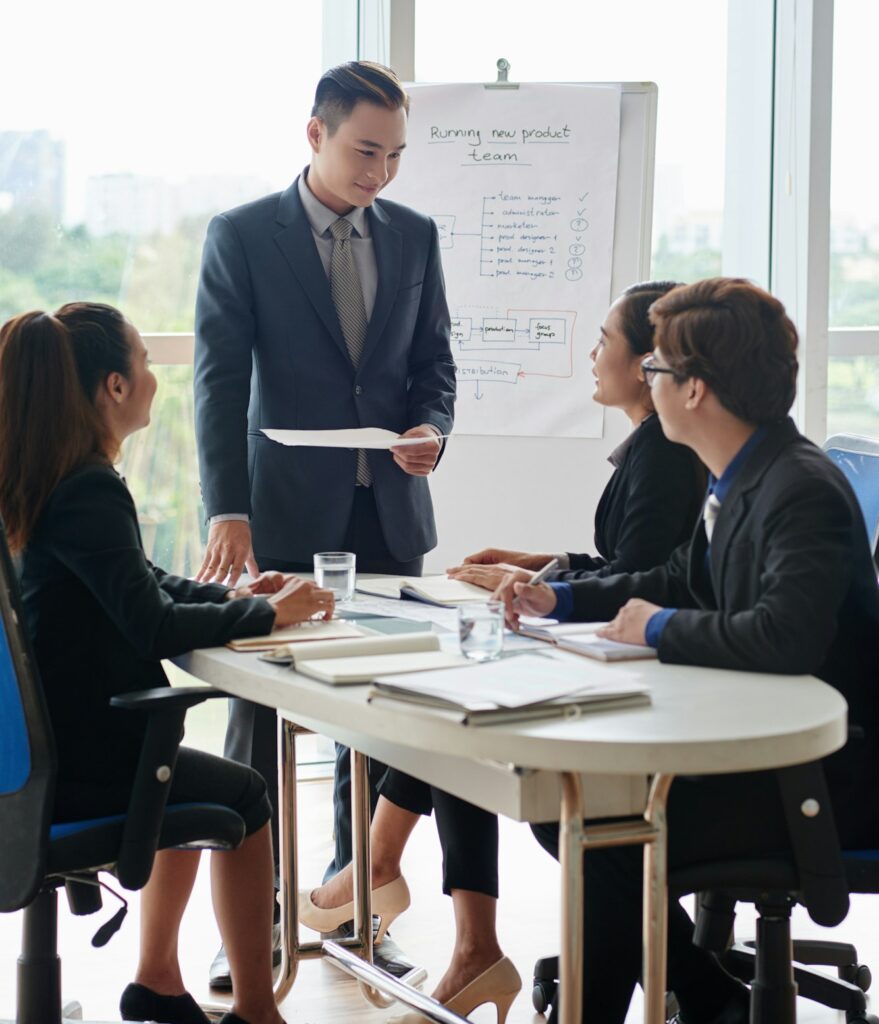
Evaluating Auditor Performance and Effectiveness
Evaluating auditor performance is crucial for maintaining high audit standards. Start by assessing auditors’ ability to spot non-compliance issues accurately. Look at how well they identify risks and determine if they can recommend effective corrective actions. When auditors consistently recognize areas of concern, they help the organization improve compliance proactively. Additionally, evaluations reveal strengths and weaknesses, allowing management to provide targeted support or additional training. This approach ensures that auditors continue to grow in their roles and maintain effectiveness.
Effective performance evaluations also refine the entire auditing process. By analyzing each auditor’s work, you can identify best practices and areas needing improvement. For instance, auditors with strong skills in specific areas can mentor others, creating a culture of shared knowledge. Regular evaluations keep the team aligned with the latest GMP standards, which enhances the overall quality of audits. This continuous improvement benefits the organization by promoting a high standard of compliance, ultimately contributing to safer, more reliable products.
Conducting Post-Audit Reviews and Follow-Ups
Reviewing Audit Findings
After the audit, review all findings with the relevant departments. A collaborative review encourages ownership and timely action.
Creating an Action Plan
Develop a corrective action plan based on audit findings. Assign responsibilities and timelines to ensure that all issues are addressed.
Conducting Follow-Up Audits
Schedule follow-up audits to verify that corrective actions have been implemented. Regular follow-ups reinforce a culture of compliance and continuous improvement.
Conclusion
Conducting internal GMP audits is vital for maintaining compliance, ensuring product quality, and fostering a proactive culture of improvement. By following a structured approach, using comprehensive checklists, and training auditors effectively, companies can enhance the efficiency and accuracy of their GMP audits. Overcoming challenges like resistance, inadequate documentation, and untrained personnel can streamline audit processes, ensuring continuous improvement and long-term success in the pharmaceutical industry. Regular GMP audits not only safeguard regulatory compliance but also build a foundation for quality, safety, and excellence.
References
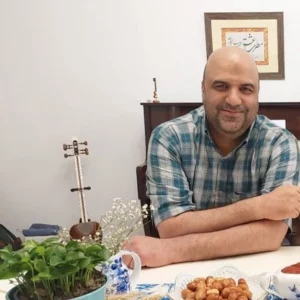
Ershad Moradi
Ershad Moradi, a Content Marketing Specialist at Zamann Pharma Support, brings 6 years of experience in the pharmaceutical industry. Specializing in pharmaceutical and medical technologies, Ershad is currently focused on expanding his knowledge in marketing and improving communication in the field. Outside of work, Ershad enjoys reading and attending industry related networks to stay up-to-date on the latest advancements. With a passion for continuous learning and growth, Ershad is always looking for new opportunities to enhance his skills and contribute to pharmaceutical industry. Connect with Ershad on Facebook for more information.
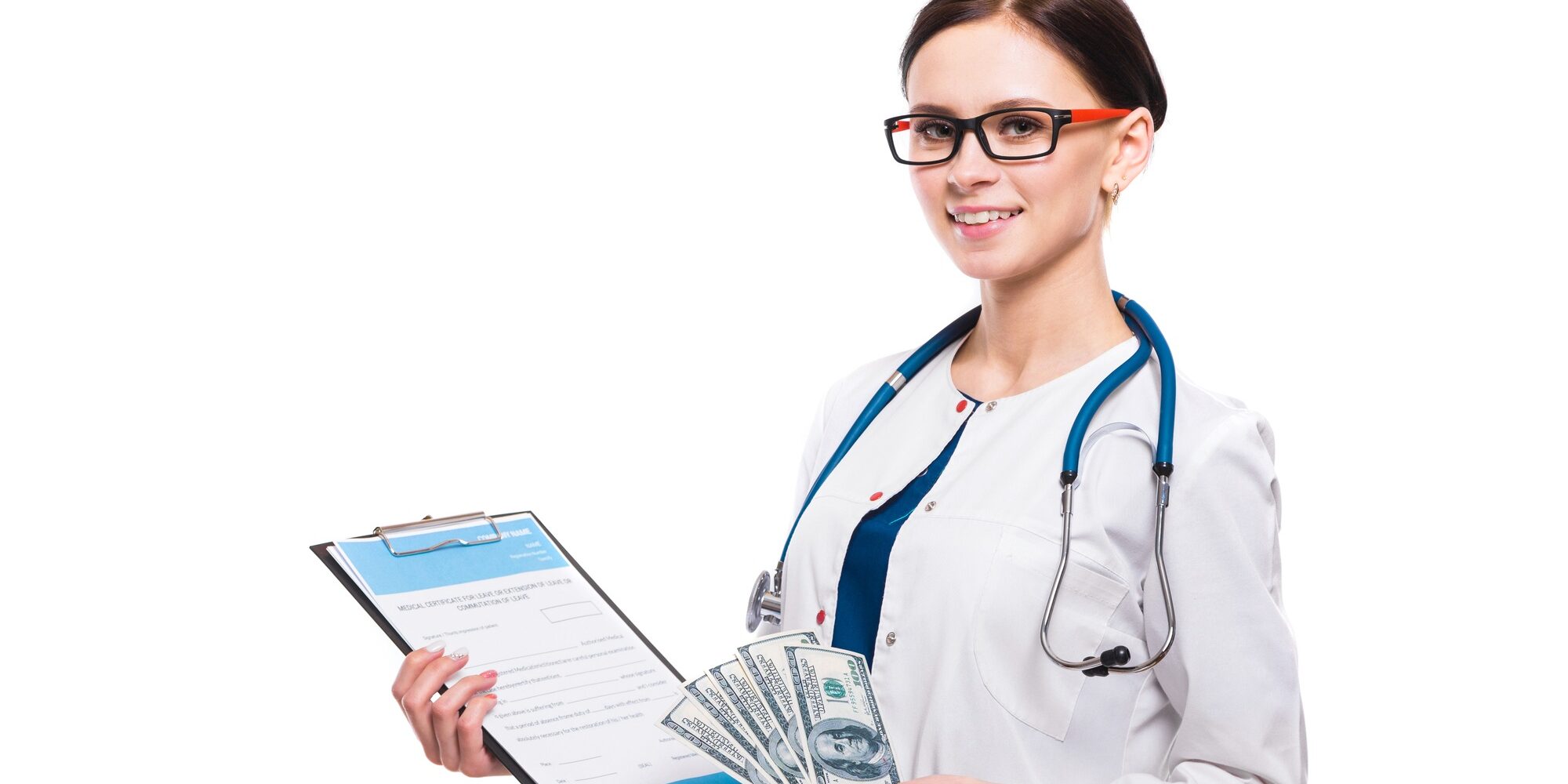
Pharmacist Salary in the US: What You Need to Know
This article explains pharmacist salary ranges—from hourly to annual pay—across practice settings. Learn how experience, location, and role shape wages, and find actionable advice on negotiating compensation, career advancement, and securing the best package through Pharmuni’s courses, resume tools, and GMP training.
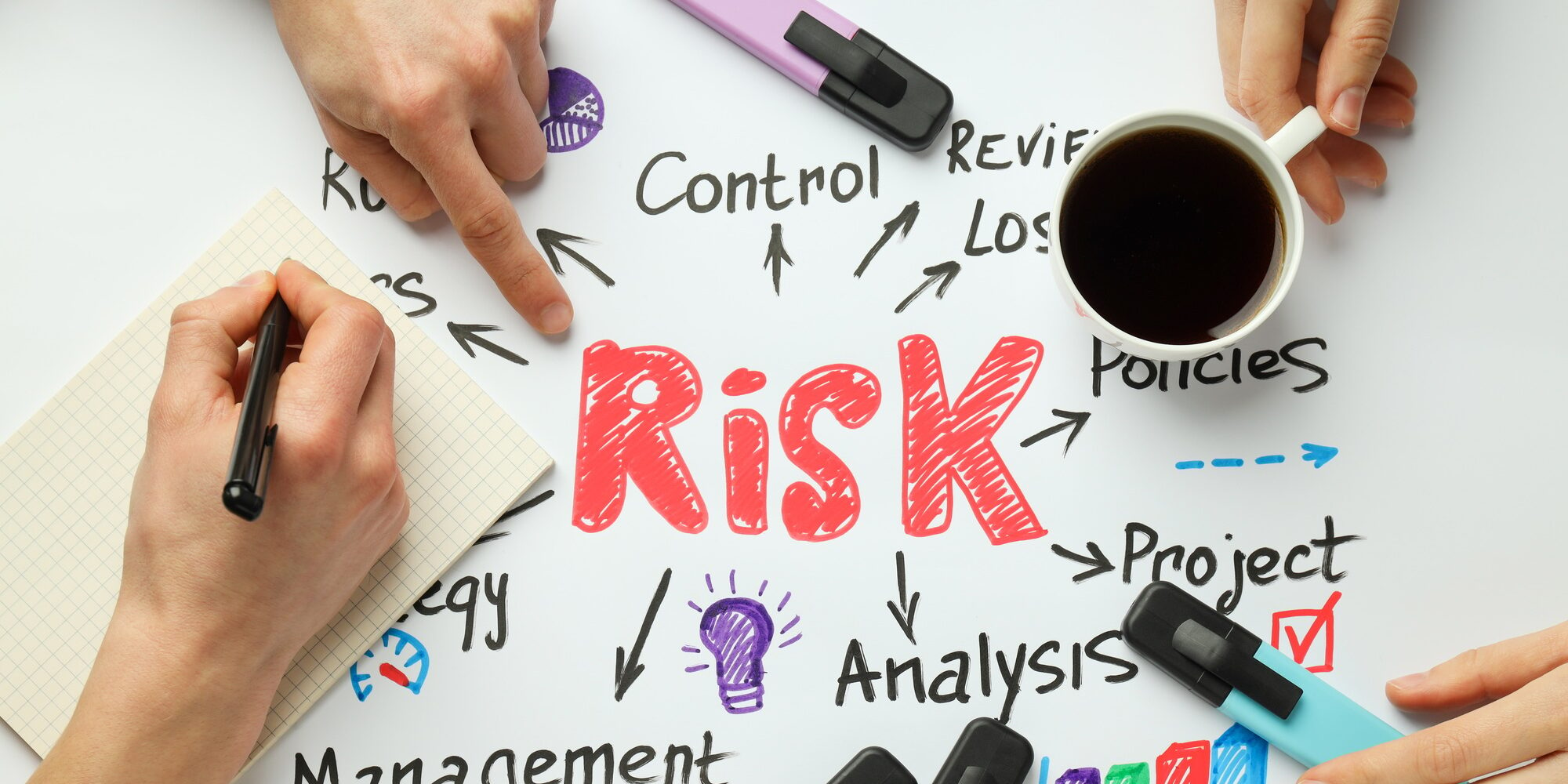
Risk Assessment Tools: Your Complete Guide to Smarter Decisions
Risk assessment tools help businesses identify, analyze, and control risks before they cause problems. From healthcare to pharma, tools like FMEA, HACCP, and Johns Hopkins fall risk assessments empower professionals with reliable strategies. Learn methods, compare approaches, and apply practical insights for better outcomes.
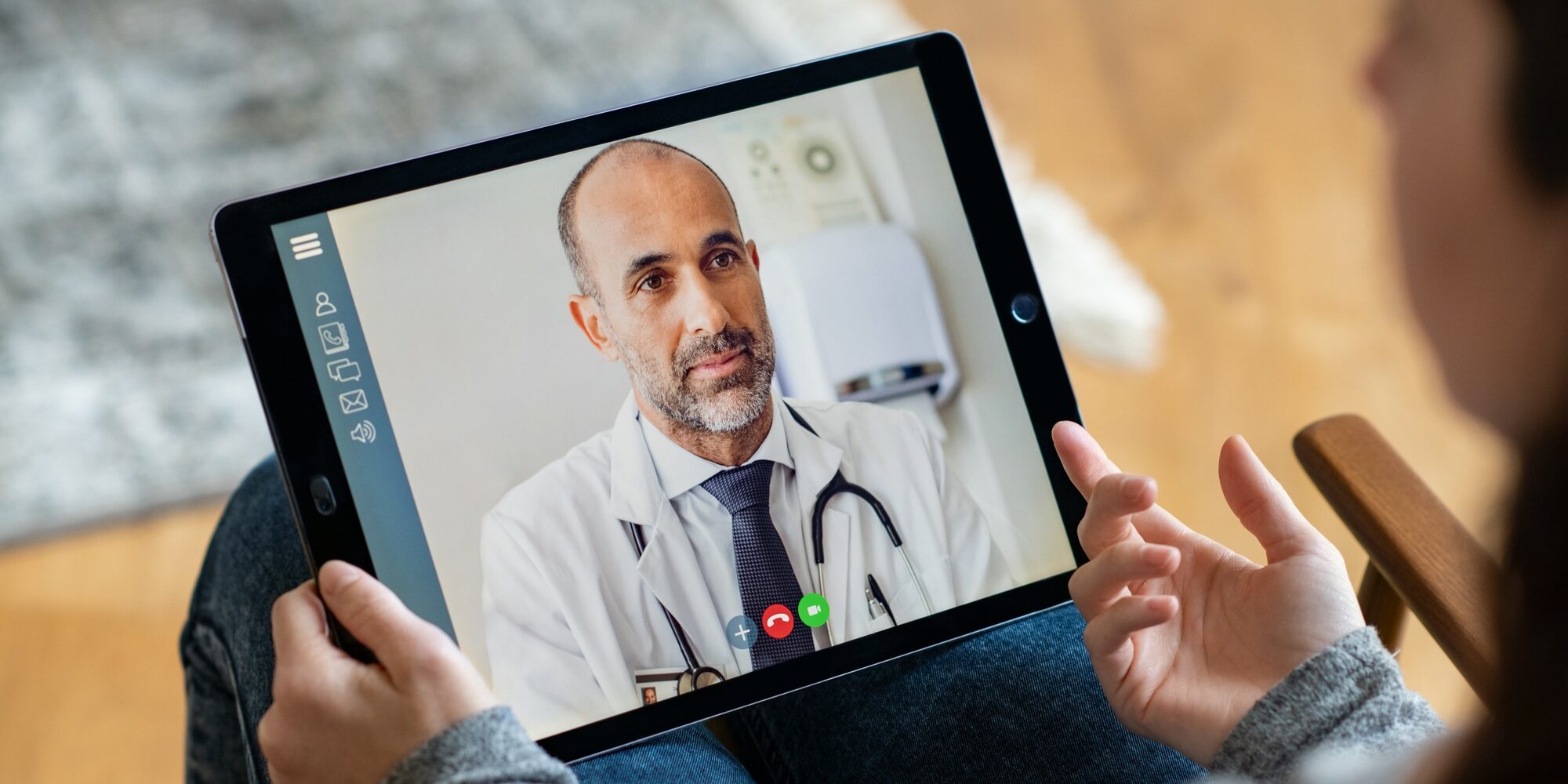
Pharmacovigilance Jobs Remote: The Complete Career Guide
Looking for pharmacovigilance jobs remote? This guide shows you where to find remote drug safety roles, how to qualify, and which global opportunities exist. Learn practical strategies, entry-level tips, and career insights to boost your chances in the competitive pharmacovigilance market.