The V Model is an essential methodology in the pharmaceutical industry, designed to ensure quality, safety, and regulatory compliance throughout the development process. This framework is integral in Commissioning, Qualification, and Validation (CQV) activities, enabling pharmaceutical companies to meet stringent standards in product and process development. By aligning development stages with validation steps, the V Model minimizes risks and enhances quality assurance.
In this article, we’ll explore the phases of the V Model in detail, covering each stage from User Requirements Specification (URS) to Factory Acceptance Testing (FAT), Site Acceptance Testing (SAT), and the critical qualification stages.
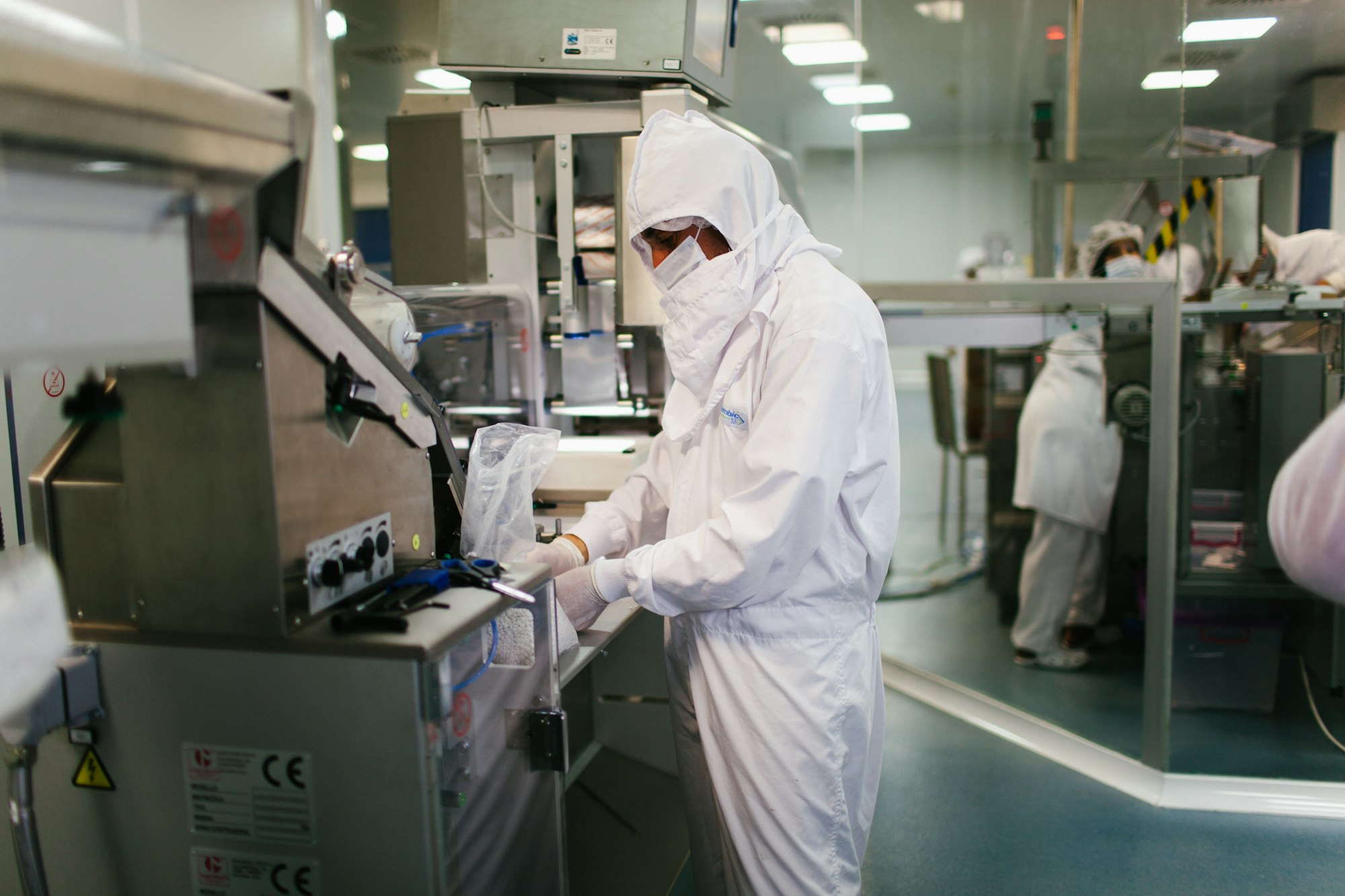
Introduction to the V Model in Pharmaceuticals
The V Model offers a clear and structured pathway for developing and validating pharmaceutical systems. This lifecycle model breaks down the process into distinct phases, aligning each development stage with a corresponding validation step. Such precise alignment ensures thorough testing at every stage, reducing the risk of errors. Moreover, this structured approach supports regulatory compliance, which is essential in pharmaceuticals. By pairing development and validation phases, the V Model strengthens quality assurance and builds confidence in product reliability. This systematic structure also improves traceability, which makes it easier to identify and resolve issues early.
Additionally, the V Model helps pharmaceutical professionals maintain consistent standards throughout the development process. By following each phase closely, teams can ensure every requirement is met without overlooking crucial details. This alignment aids in addressing potential issues quickly, keeping projects on track. Understanding and using the V Model is crucial for professionals focused on safe, effective, and compliant products. This model not only supports regulatory needs but also enhances overall product quality. Ultimately, the V Model plays a critical role in building trust in pharmaceutical development, delivering products that meet both safety and quality standards.
Sign up forGMP Device Qualification Course
Key Elements of the V Model in Pharmaceuticals
The V Model comprises several key components that define its structure and function. Each component contributes to a robust, step-by-step approach to development and validation in the pharmaceutical industry.
User Requirements Specification (URS)
The URS is a document that outlines what the system or equipment should accomplish. It is a high-level requirement list that ensures the equipment will meet regulatory and operational needs.
Functional Design Specification (FDS)
The FDS translates the URS into a detailed functional outline. This specification describes how the system will work and how each component will interact to fulfill the URS requirements.
Detail Design Specification (DDS)
The DDS specifies the technical aspects of each component, ensuring that they meet both functional and compliance standards.
Construction and Assembly
This phase involves building the equipment or system according to the DDS. Construction must adhere to precise specifications to avoid issues during testing and qualification.
Understanding Commissioning, Qualification, and Validation
Commissioning
Commissioning involves testing and verifying that facilities, equipment, and systems are ready for qualification. This process focuses on ensuring operational readiness by checking each system thoroughly. Under Good Engineering Practices (GEP), commissioning confirms that systems are installed correctly. It also ensures that every component functions as intended before moving to the qualification stage. Technicians test and calibrate equipment to meet specific standards, which reduces the risk of issues later. Moreover, commissioning identifies any potential adjustments needed, allowing teams to make changes early. This preparation stage saves time and resources in the long run.
Additionally, commissioning strengthens overall quality assurance in pharmaceutical projects. By addressing installation and calibration at the start, it helps maintain high standards throughout development. The commissioning process also builds a solid foundation for qualification, where systems will undergo further testing. When commissioning is thorough, qualification and validation stages proceed more smoothly. This phase, therefore, plays a vital role in preparing for complex qualification activities. Effective commissioning ensures that each system, tool, or piece of equipment meets initial specifications. Ultimately, commissioning supports a streamlined, reliable pathway for delivering safe and compliant pharmaceutical products.
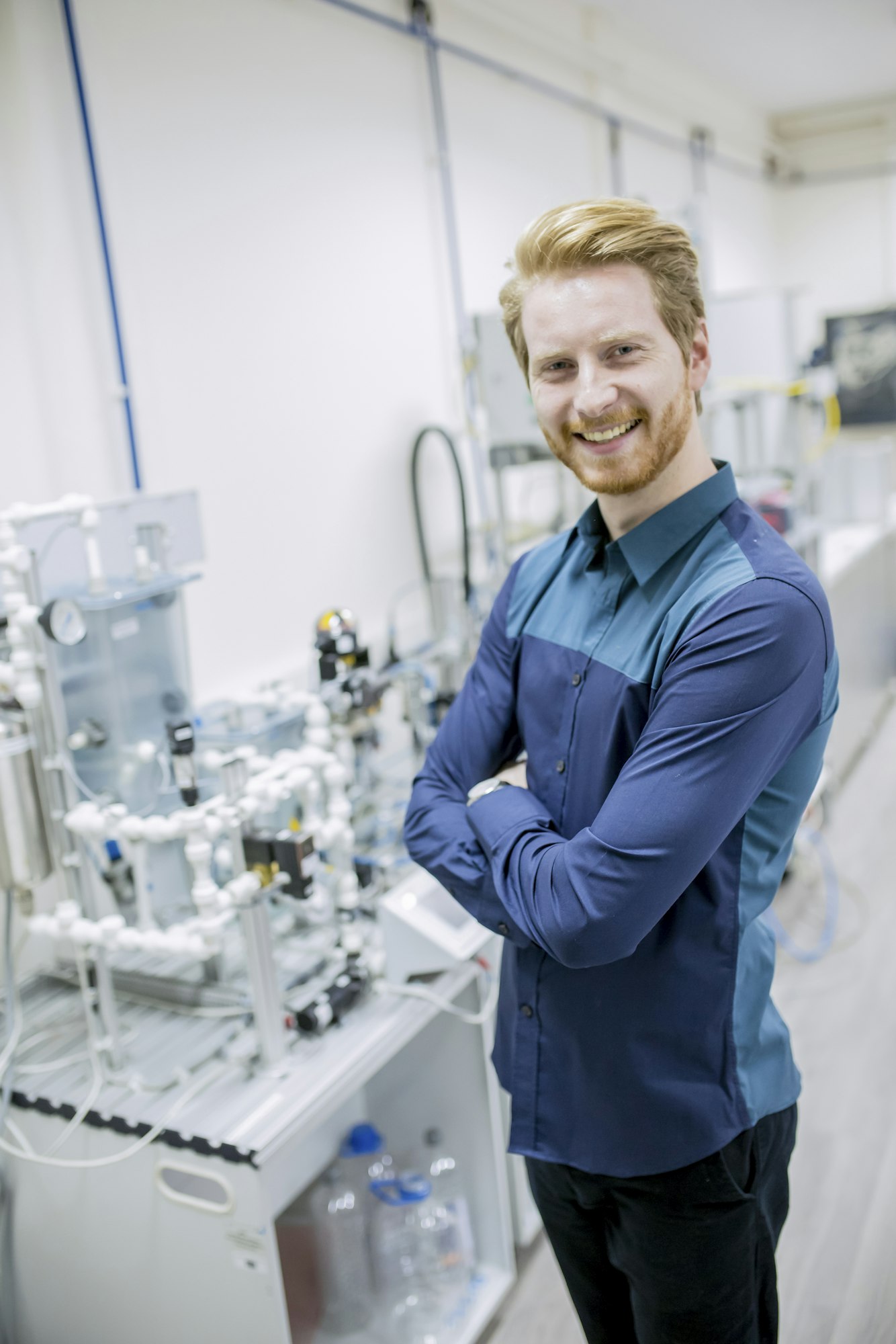
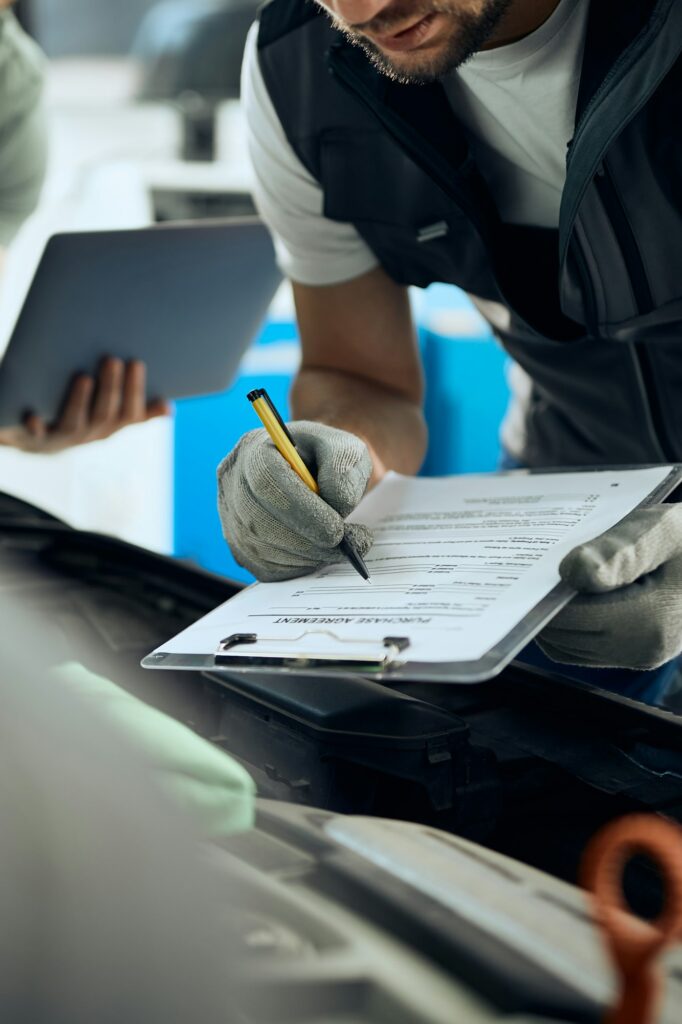
Qualification
Qualification ensures that equipment and systems meet all initial design requirements. This process confirms that each component aligns with specifications from the very beginning. Design Qualification (DQ) starts this journey by verifying that the design matches intended functions. Then, Installation Qualification (IQ) checks if the equipment is installed according to plan. At this stage, teams inspect components and calibrate instruments, ensuring precise setup. Each step reduces potential issues in future phases, establishing a strong foundation for operations.
Next, Operational Qualification (OQ) verifies that equipment functions within defined operational ranges. Teams test each piece under typical conditions, checking for consistency and reliability. Finally, Performance Qualification (PQ) assesses whether the system delivers expected results in real-world scenarios. During PQ, equipment must perform repeatedly within set limits, ensuring stable output. This thorough qualification process supports quality control, enhancing confidence in each system. By following each qualification stage, teams minimize errors and boost regulatory compliance. Qualification plays a vital role in developing safe, effective, and compliant pharmaceutical products.
Validation
Validation goes a step further than qualification, ensuring that processes consistently deliver quality products. It focuses on verifying that systems and equipment operate reliably within set parameters. During validation, teams check that each process performs as expected under real production conditions. This stage confirms that systems can produce consistent, repeatable results over time. Validation strengthens confidence in the equipment’s long-term performance, which is essential for quality control. By validating each component, teams ensure that the entire process meets industry standards and regulatory requirements.
Moreover, validation maintains quality throughout the lifecycle of the equipment and processes. It involves continuous monitoring to detect any variations that may impact performance. If issues arise, teams can make necessary adjustments early to avoid larger problems. Validation thus supports ongoing compliance, keeping production within approved guidelines. This proactive approach minimizes risks, ensuring that each product batch meets strict quality standards. Ultimately, validation builds a strong foundation for safe, reliable, and effective pharmaceutical products. By completing thorough validation, teams create a robust framework that supports consistent product quality over time.
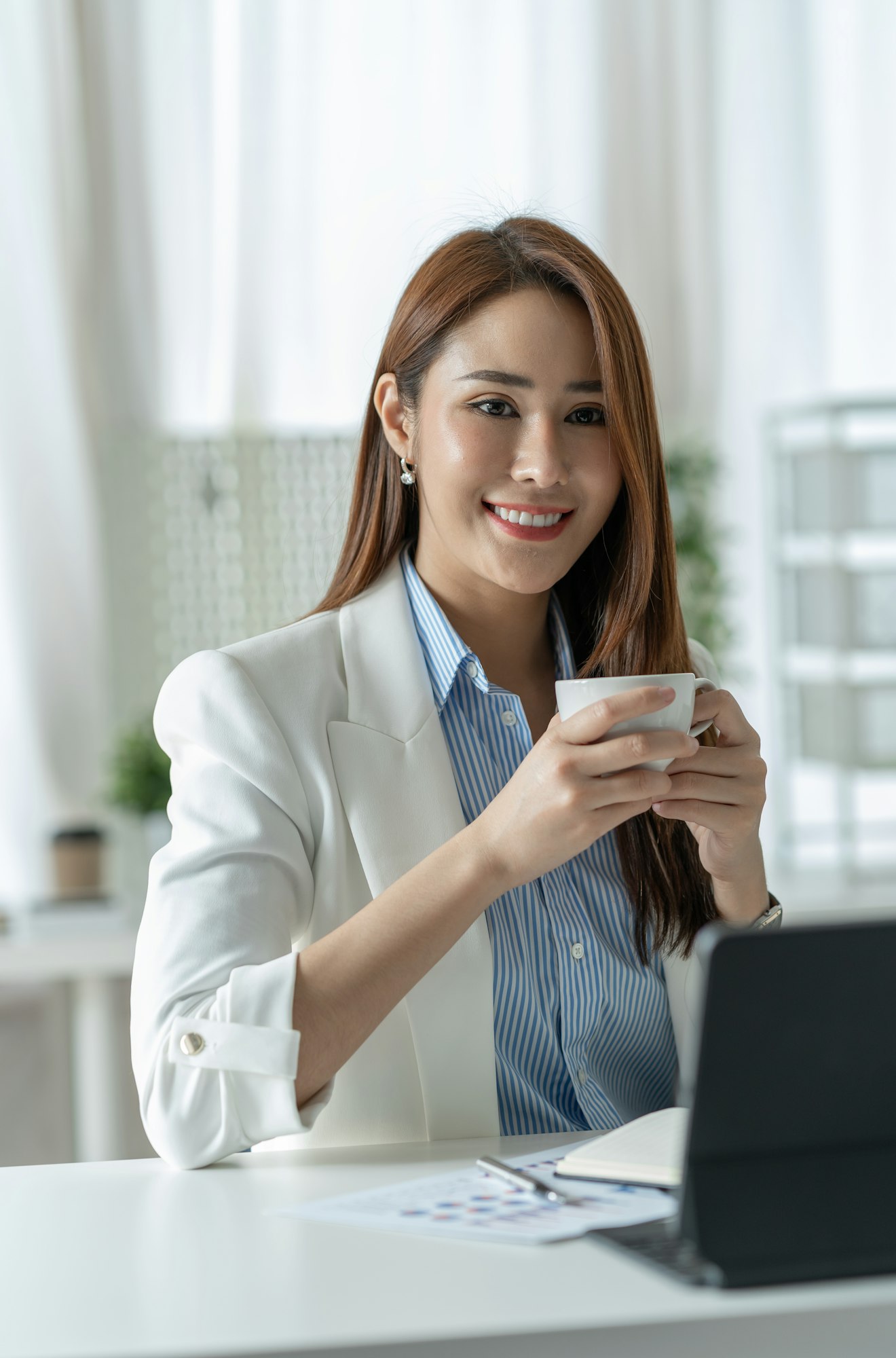
Qualification Phases in the V Model
The V Model includes several distinct qualification phases, each serving a unique purpose in ensuring regulatory compliance and product quality.
Design Qualification (DQ)
DQ verifies that the design meets all specified requirements and is suitable for its intended purpose in the production environment.
Installation Qualification (IQ)
IQ checks that equipment is installed correctly and in accordance with the manufacturer’s specifications and approved designs.
Operational Qualification (OQ)
OQ ensures that the system performs as expected under specified conditions, verifying its functionality and reliability.
Performance Qualification (PQ)
PQ evaluates the system’s performance under real-world conditions, confirming its capability to produce consistent results.
Testing Phases in V Model
Factory Acceptance Testing (FAT)
Factory Acceptance Testing (FAT) occurs at the manufacturer’s site, verifying that equipment functions according to specifications. This phase ensures that the system meets all requirements before it arrives for installation. FAT is essential because it identifies design or operational issues early. By catching problems at the manufacturer’s location, teams can make adjustments before delivery. This proactive step saves time and resources, reducing the chances of issues later. FAT tests the equipment’s capabilities in a controlled environment, which provides a clear picture of its expected performance. As a result, teams gain confidence in the equipment’s readiness for installation.
The objective of FAT is to confirm that the equipment meets all functional specifications. During this phase, technicians conduct various tests to identify any potential operational issues. If issues arise, the manufacturer can address them immediately to avoid future setbacks. This thorough testing approach helps streamline the installation process and minimizes unexpected challenges on-site. FAT allows teams to verify that the system performs reliably under standard conditions. Ultimately, completing FAT builds a solid foundation for the next stages, including Site Acceptance Testing (SAT) and final installation.
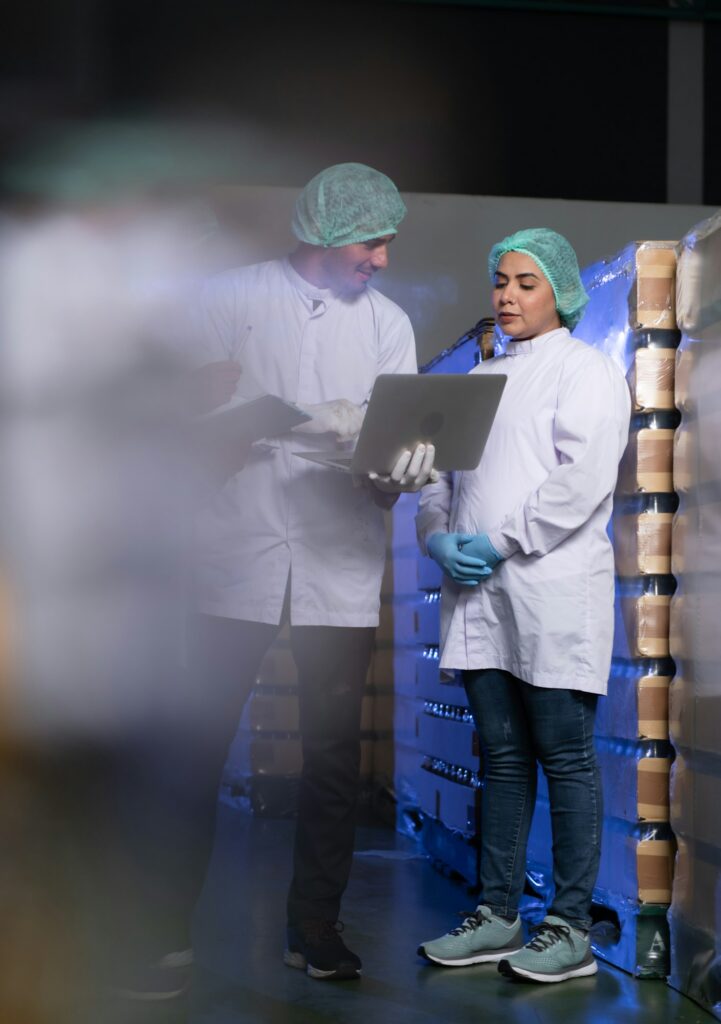
Site Acceptance Testing (SAT)
Site Acceptance Testing (SAT) happens after the equipment is installed on-site. This test confirms that the equipment works correctly in its actual production environment. SAT focuses on ensuring the system functions as intended within the facility’s setup. By testing on-site, teams verify that the equipment integrates smoothly with other processes. This step is crucial because it reveals any adjustments needed to improve performance. Technicians can fine-tune settings, ensuring the equipment operates effectively and reliably. Ultimately, SAT reduces risks by confirming that all components align within the production setup.
The objective of SAT is to validate the equipment’s functionality in a real-world setting. This on-site testing allows teams to assess how well the equipment handles production demands. If any issues appear, they can resolve them immediately for optimal performance. SAT ensures that each piece of equipment performs its role safely and efficiently within the larger process. This phase enhances both reliability and safety, contributing to consistent product quality. SAT not only confirms integration but also strengthens confidence in the system’s overall readiness. By completing SAT, teams help secure smooth, safe, and effective pharmaceutical production.
Lifecycle Phases in the V Model
The V Model’s lifecycle phases guide projects from initial requirements gathering to comprehensive validation. This structured approach ensures consistent quality and compliance in both development and production. By breaking down each phase, the V Model helps teams focus on specific tasks and requirements at each step. This method not only enhances efficiency but also reduces errors, ensuring every component meets regulatory standards. From beginning to end, the V Model supports a clear, traceable path for pharmaceutical development. It aligns each development stage with a corresponding validation step, fostering both precision and reliability.
The Design and User Requirements Specification (URS) phases form the V Model’s foundation. The URS outlines what the system must achieve, setting clear goals and expectations. Next, the design phase translates these goals into technical specifications, detailing how each component will meet the URS criteria. This early planning phase is essential because it establishes quality and regulatory standards to guide development. The Functional and System Design phases then provide a detailed blueprint of the system’s architecture. These phases ensure all components align precisely with the URS and Functional Design Specifications (FDS). This careful planning prepares the system for smooth integration in later stages, reducing issues during installation and qualification.
Benefits of Implementing the V Model in Pharmaceuticals
Ensures Compliance
The V Model helps pharmaceutical companies meet strict regulatory standards by aligning development and validation phases.
Enhances Traceability
Documentation within the V Model promotes traceability, making it easier to identify and resolve issues quickly.
Improves Quality Control
The model’s structured approach reinforces quality control, reducing the risk of errors and rework.
Saves Costs
Detecting issues early in the development cycle reduces costs associated with corrective actions.
Minimizes Risks
With each phase validated, the V Model minimizes operational risks, ensuring reliability in pharmaceutical production.
Conclusion
The V Model is a comprehensive framework that strengthens compliance and quality control in pharmaceutical development. By integrating phases like Commissioning, Qualification, and Validation with thorough documentation and testing, the V Model offers a robust solution for meeting industry standards. Embracing this methodology allows pharmaceutical companies to minimize risks, ensure regulatory compliance, and deliver high-quality, safe products.
Understanding the V Model is crucial for professionals committed to excellence in the pharmaceutical industry. This structured approach not only improves regulatory compliance but also fosters a proactive stance on quality, ensuring that every step in development and production adheres to the highest standards.
References
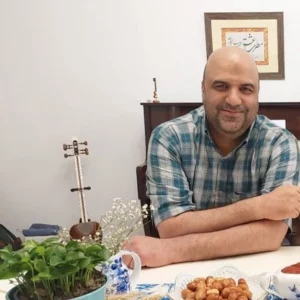
Ershad Moradi
Ershad Moradi, a Content Marketing Specialist at Zamann Pharma Support, brings 6 years of experience in the pharmaceutical industry. Specializing in pharmaceutical and medical technologies, Ershad is currently focused on expanding his knowledge in marketing and improving communication in the field. Outside of work, Ershad enjoys reading and attending industry related networks to stay up-to-date on the latest advancements. With a passion for continuous learning and growth, Ershad is always looking for new opportunities to enhance his skills and contribute to pharmaceutical industry. Connect with Ershad on Facebook for more information.
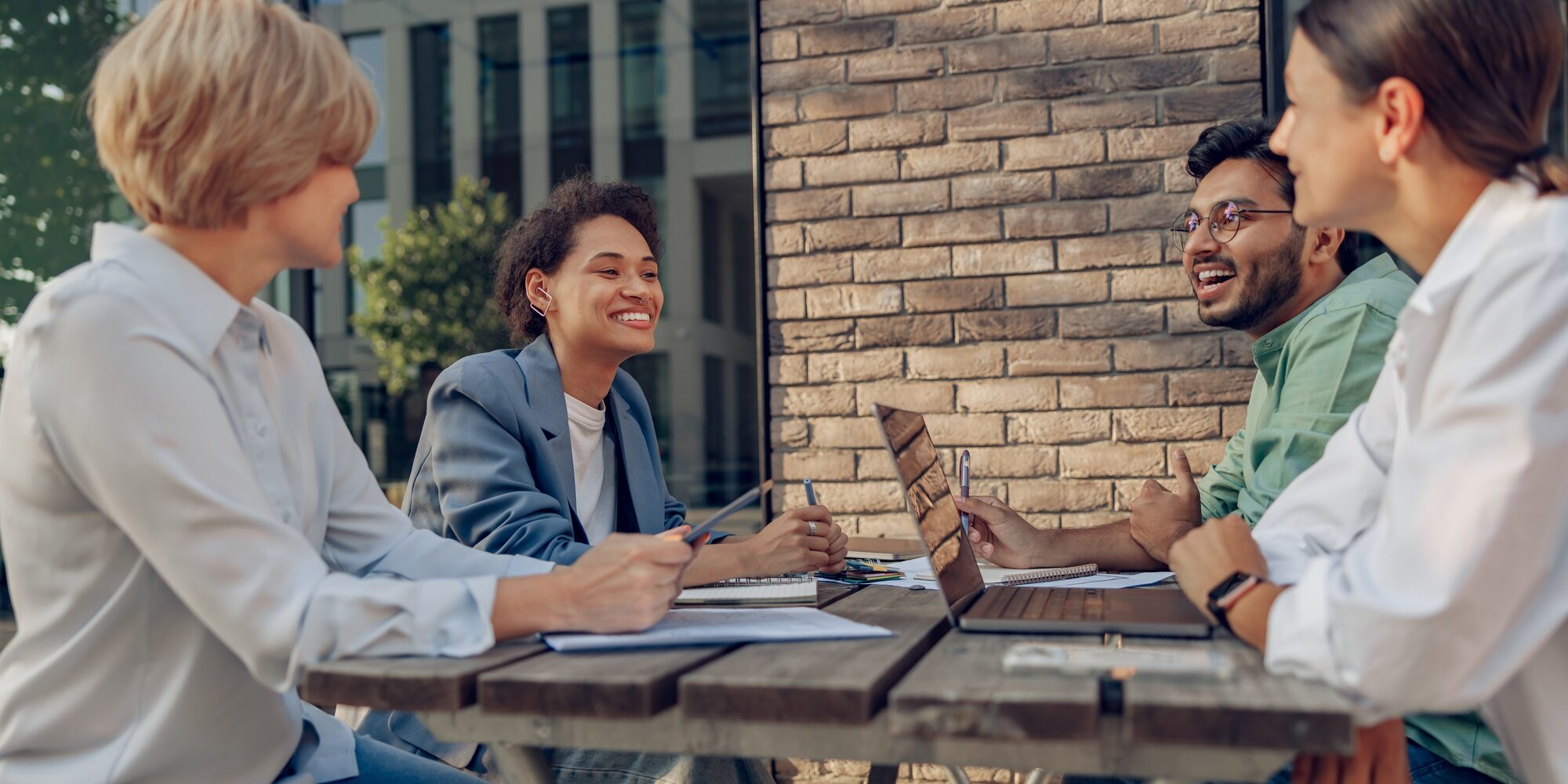
Pharma Sales Secrets to Skyrocket Success
Pharma sales is more than just selling medications. It combines science, strategy, and relationship building. Whether you’re starting out or refining your approach, this guide gives you practical tools, career insights, and tips to succeed in today’s competitive pharmaceutical sales industry.
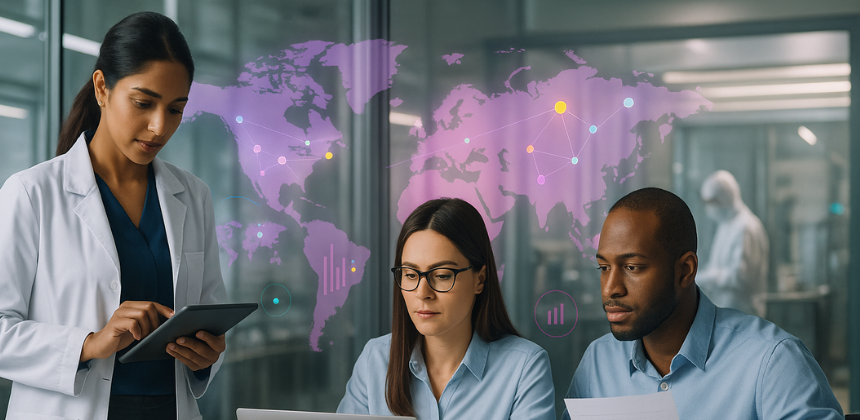
Pharma Job Market Trends: What’s Hot Now
Pharma job market trends show sustained growth across quality, regulatory affairs, pharmacovigilance, and data. New modalities, including cell and gene therapy, expand validation and aseptic roles quickly. Meanwhile, digital tools reshape trials, manufacturing, and safety reporting. Therefore, candidates who blend science, GxP, and analytics win more interviews.
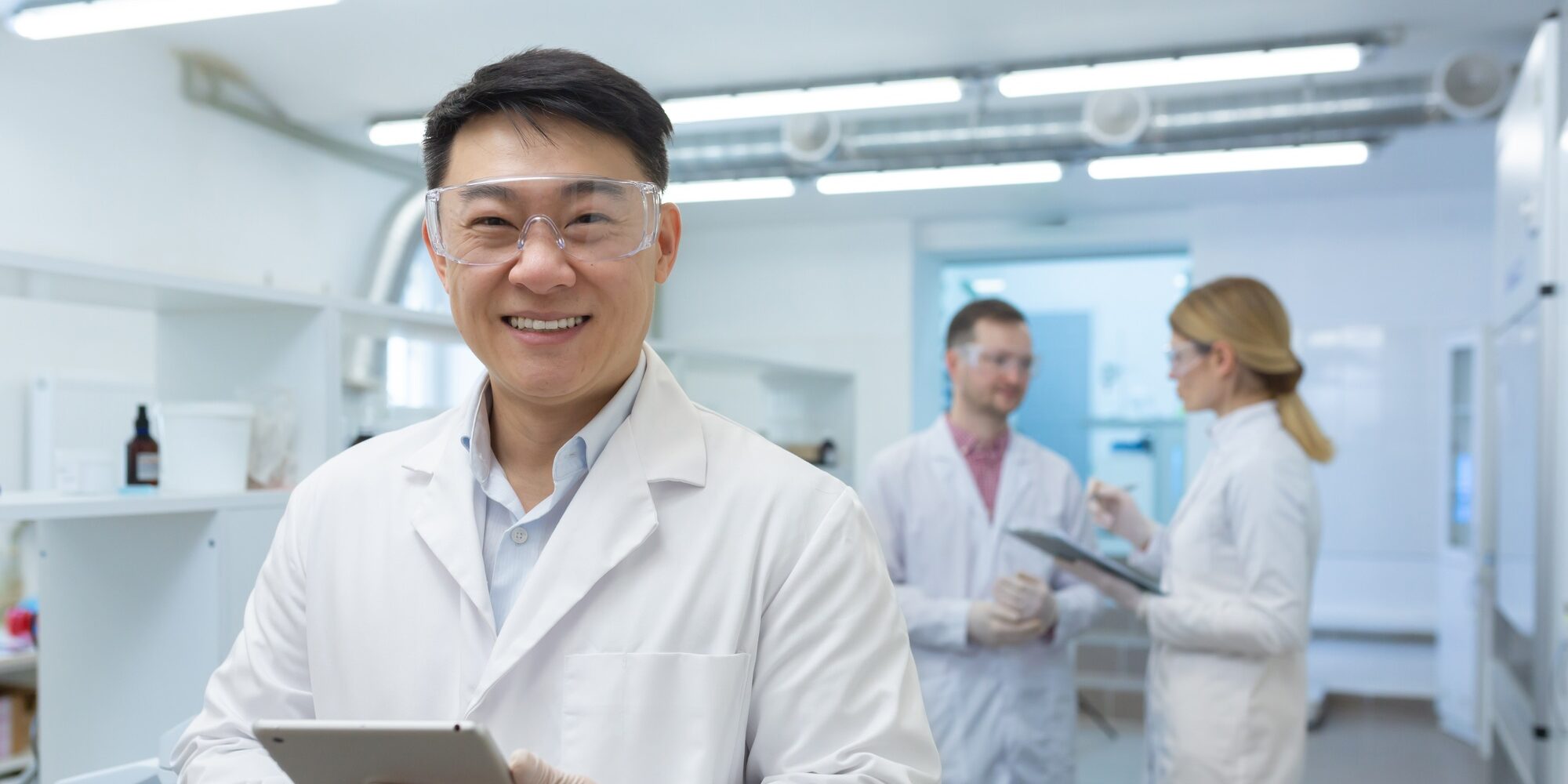
GMP Laboratory – Your Complete Guide to Compliance and Quality
This comprehensive guide explains GMP laboratories, their services, and compliance needs. Learn about cGMP, GLP labs, testing standards, and industry-specific requirements. Get actionable tips, comparisons, and insights to select the right GMP lab for your business or career growth.