In the pharmaceutical industry, maintaining strict adherence to Good Manufacturing Practices (GMP) is essential for ensuring product quality and regulatory compliance. However, a GMP Deviation can occur at various stages of the production process, posing serious risks to both product safety and business operations. These deviations may arise from multiple causes, including human error or equipment failure. Effectively addressing a GMP Deviation is crucial to maintaining compliance, protecting product integrity, and preventing costly recalls.
This article delves into the causes, types, and solutions related to GMP Deviation and offers actionable strategies for managing them efficiently.
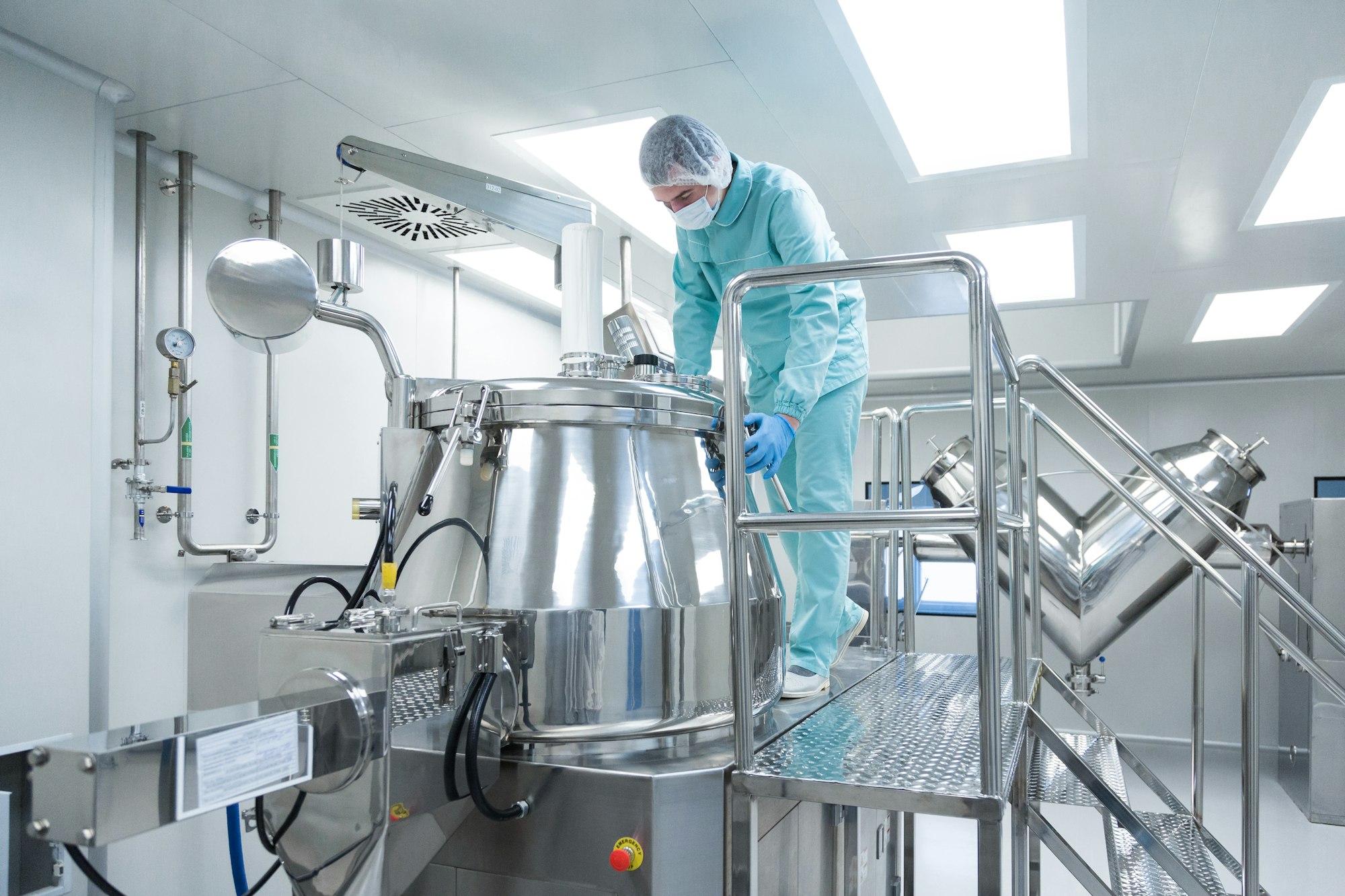
These deviations can happen at any point in the manufacturing or quality control process, and when they do, they compromise product integrity and safety.
If left unchecked, they can lead to regulatory action, product recalls, or even patient harm.
When a deviation is identified, the first step is to assess its impact. This includes evaluating whether the deviation affects product quality, safety, or compliance with regulatory standards. Addressing deviations promptly ensures that the issue does not escalate into a more significant problem. Companies should also document every instance of a deviation, outlining the root cause and the steps taken to resolve it. This documentation is critical during audits and inspections, as it demonstrates a commitment to maintaining GMP standards.
Sign up for GMP Deviation Management Online Course
Types of GMP Deviation
GMP Deviation can be categorized into several types, depending on their severity and potential impact. Understanding these types is crucial for determining the appropriate response and ensuring regulatory compliance:
Critical deviations are the most severe type. They directly impact product quality, patient safety, or regulatory compliance. Immediate corrective action is required to prevent harmful outcomes.
Major deviations have a significant impact on product quality but may not pose an immediate risk to patient safety. Nonetheless, they must be addressed promptly to prevent future problems.
Minor deviations have minimal or no impact on product quality or regulatory compliance. These deviations are often routine and can be resolved through standard operating procedures.
Planned deviations occur intentionally, with prior approval, to address temporary changes in the process or materials used. They must be justified, documented, and aligned with regulatory standards.
Causes of GMP Deviation
Human Error
Human error is a leading cause of GMP Deviation in pharmaceutical operations. It can occur at any stage of the production process, from raw material handling to final product packaging. Common human errors include misinterpretation of SOPs, failure to follow established procedures, or miscommunication between departments. For instance, an operator might misread instructions, leading to incorrect measurements or improper handling of equipment.
The root of many human errors lies in inadequate training or insufficient experience. Employees who are not fully trained in GMP protocols are more likely to make mistakes. To reduce human error, companies must invest in regular and comprehensive training programs. These programs should cover all aspects of GMP, including proper documentation, adherence to SOPs, and the importance of accuracy in every step of the production process. Clear communication between teams is also essential to avoid misunderstandings that can lead to deviations. Regular audits and refresher courses ensure that employees stay updated on the latest GMP practices and continue to perform their roles correctly.
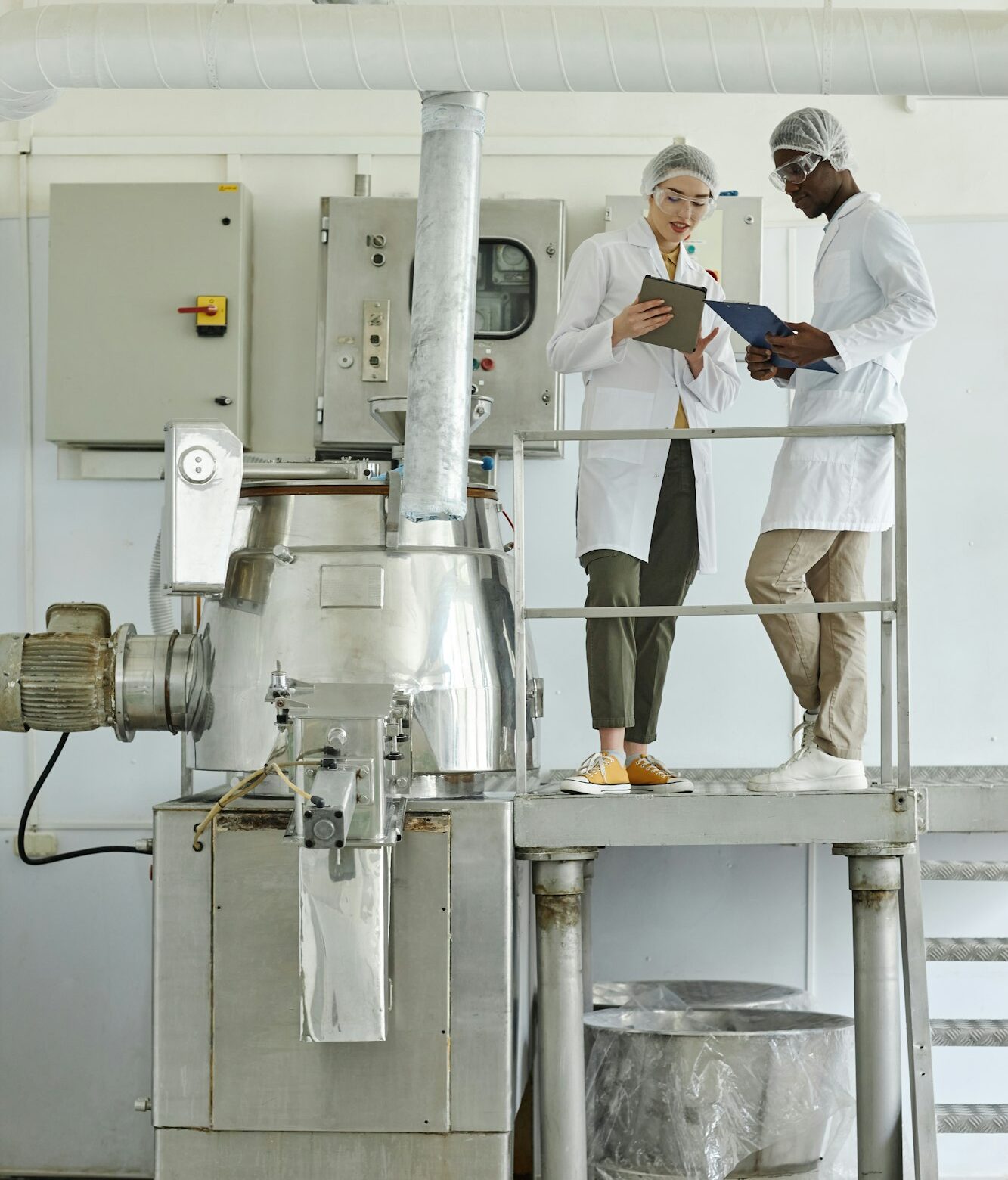
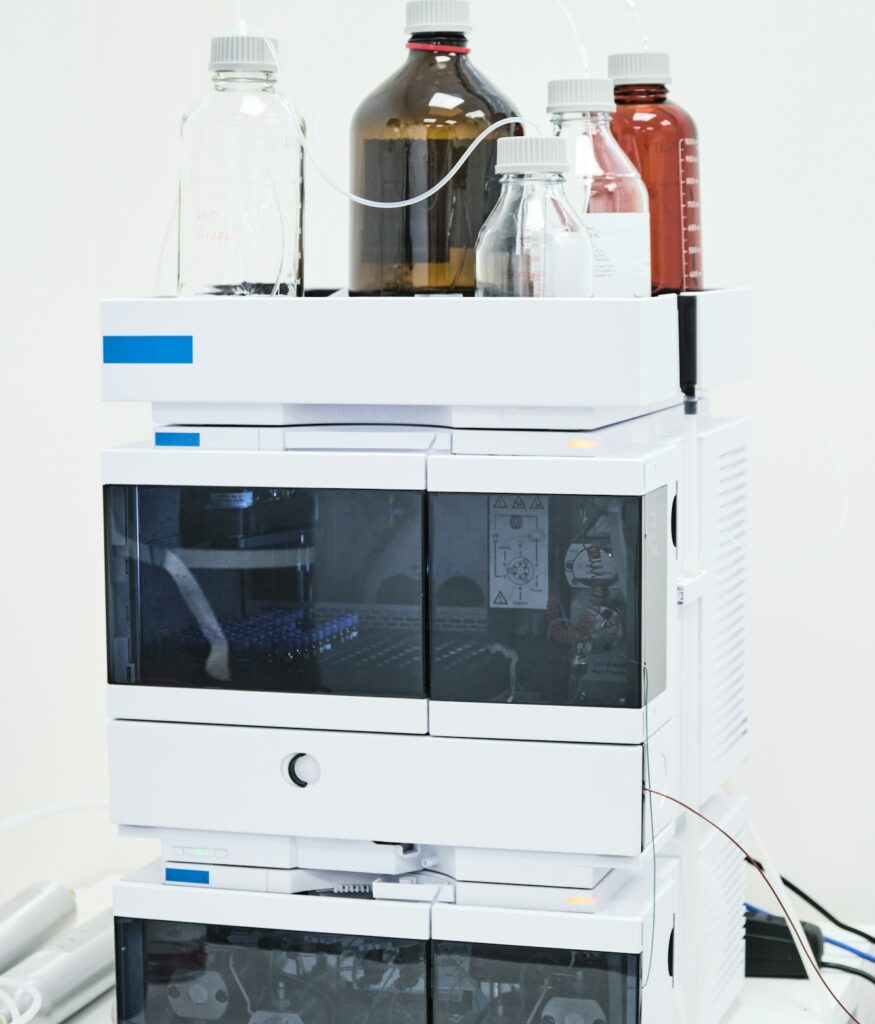
Equipment Failure
Equipment failure is another common cause of GMP Deviation. Pharmaceutical manufacturing relies heavily on machinery, and when equipment malfunctions, it can disrupt production and compromise product quality. For example, a piece of equipment that is not calibrated correctly may produce batches that do not meet required specifications. In other cases, equipment breakdowns can lead to production delays or contamination risks if not addressed quickly.
Preventing equipment-related deviations requires proactive maintenance and regular calibration. Companies should have a robust preventive maintenance program in place to ensure that all machinery operates smoothly and within specified parameters. Additionally, performing regular checks on equipment and keeping detailed maintenance logs can help identify potential issues before they lead to deviations. Investing in modern, high-quality equipment also reduces the likelihood of unexpected failures and enhances overall operational efficiency. By ensuring that machinery functions correctly, companies can minimize the risk of deviations and maintain compliance with GMP standards.
How to Prevent GMP Deviation in Manufacturing
Comprehensive Risk Assessments
Conduct regular risk assessments to identify potential deviation risks in processes, equipment, and personnel. Early identification allows for proactive measures to prevent deviations.
Standard Operating Procedures (SOPs)
Well-documented and clear SOPs ensure that all processes are followed correctly. Regularly reviewing and updating SOPs ensures they remain compliant with current regulations and industry standards.
Cross-functional Collaboration
Encourage collaboration between departments to ensure that all aspects of the production process are aligned. This reduces miscommunication, which is often a significant cause of GMP deviation.
Quality Audits
Conduct frequent internal quality audits to identify any lapses in GMP compliance. Audits provide an opportunity to catch deviations before they become critical.
Corrective and Preventive Actions (CAPA)
Corrective Actions
In GMP Deviation management, corrective actions play a vital role in resolving issues that have already occurred. These actions aim to eliminate the immediate cause of the deviation and prevent it from affecting product quality or compliance. The first step in implementing corrective actions is conducting a thorough root cause analysis. This analysis helps identify the underlying reason for the deviation, whether it’s human error, equipment failure, or another contributing factor.
Once the root cause is identified, corrective actions are initiated to address the problem. These actions could include revising or updating standard operating procedures (SOPs), retraining employees on specific processes, repairing malfunctioning equipment, or implementing more stringent oversight during critical stages of production. Each corrective action must be documented carefully to demonstrate compliance during audits and inspections.
Corrective actions also require monitoring to ensure they are effective. After implementing a corrective measure, companies must evaluate whether it has fully resolved the issue and prevented further occurrences.
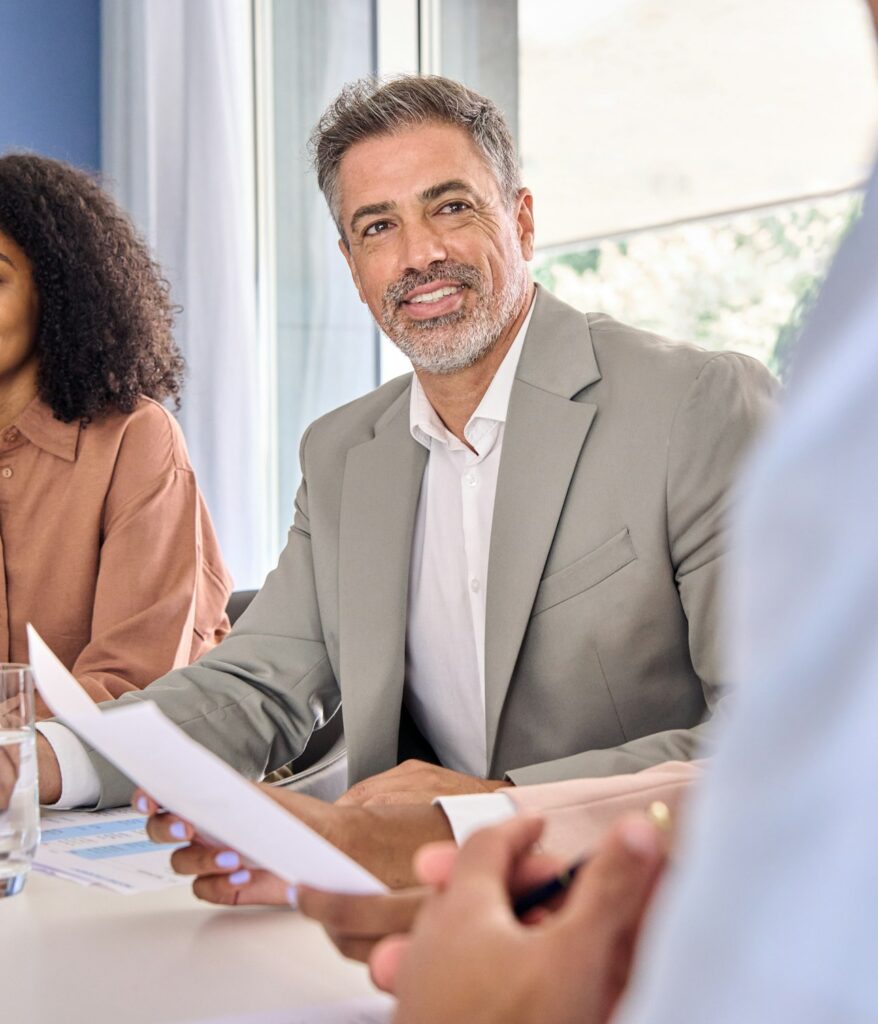
Preventive Actions
Preventive actions are essential in GMP Deviation management as they focus on preventing the recurrence of deviations by addressing underlying risks before they become issues. While corrective actions resolve immediate problems, preventive actions take a more forward-thinking approach, identifying potential causes of future deviations and implementing measures to avoid them altogether.
A key step in preventive action is conducting a trend analysis to detect patterns in deviations. By reviewing past deviations and identifying recurring issues, companies can target specific areas that require improvement. For instance, if human error is a common cause, preventive measures might include more comprehensive training programs or enhanced supervision in critical areas. These actions help reinforce employee knowledge and reduce the likelihood of mistakes.
In cases of equipment-related deviations, preventive actions often involve implementing regular maintenance schedules, updating calibration procedures, and investing in newer, more reliable technology. By ensuring equipment runs smoothly, companies reduce the risk of malfunctions that could lead to deviations.
Benefits of a Strong Deviation Management System
Improved Product Quality
A robust deviation management system ensures that products meet quality standards, reducing the likelihood of defective or non-compliant products entering the market.
Regulatory Compliance
Proactive deviation management helps companies maintain compliance with regulatory standards, reducing the risk of penalties or enforcement actions.
Operational Efficiency
Effective GMP Deviation management streamlines operations, minimizing disruptions caused by deviations. This results in more efficient processes and reduced downtime.
Enhanced Reputation
Companies that handle deviations effectively build trust with regulators and customers. A reputation for quality and compliance can be a significant competitive advantage in the pharmaceutical industry.
Conclusion
In the pharmaceutical industry, managing GMP Deviation is essential for maintaining quality and compliance. Understanding the causes, types, and solutions for deviations helps companies navigate the complexities of pharmaceutical manufacturing with greater efficiency. By implementing proactive strategies, such as comprehensive risk assessments, robust CAPA systems, and ongoing training, companies can minimize deviations and ensure that products meet the highest quality standards.
A structured approach to GMP Deviation management not only ensures regulatory compliance but also fosters trust with customers and regulatory bodies alike. By prioritizing deviation management, companies can safeguard their operations, enhance product quality, and maintain their reputation for excellence in the industry.
References
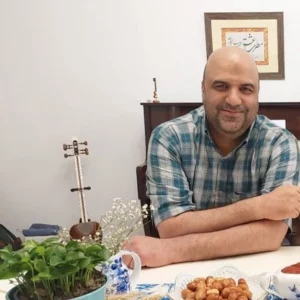
Ershad Moradi
Ershad Moradi, a Content Marketing Specialist at Zamann Pharma Support, brings 6 years of experience in the pharmaceutical industry. Specializing in pharmaceutical and medical technologies, Ershad is currently focused on expanding his knowledge in marketing and improving communication in the field. Outside of work, Ershad enjoys reading and attending industry related networks to stay up-to-date on the latest advancements. With a passion for continuous learning and growth, Ershad is always looking for new opportunities to enhance his skills and contribute to pharmaceutical industry. Connect with Ershad on Facebook for more information.
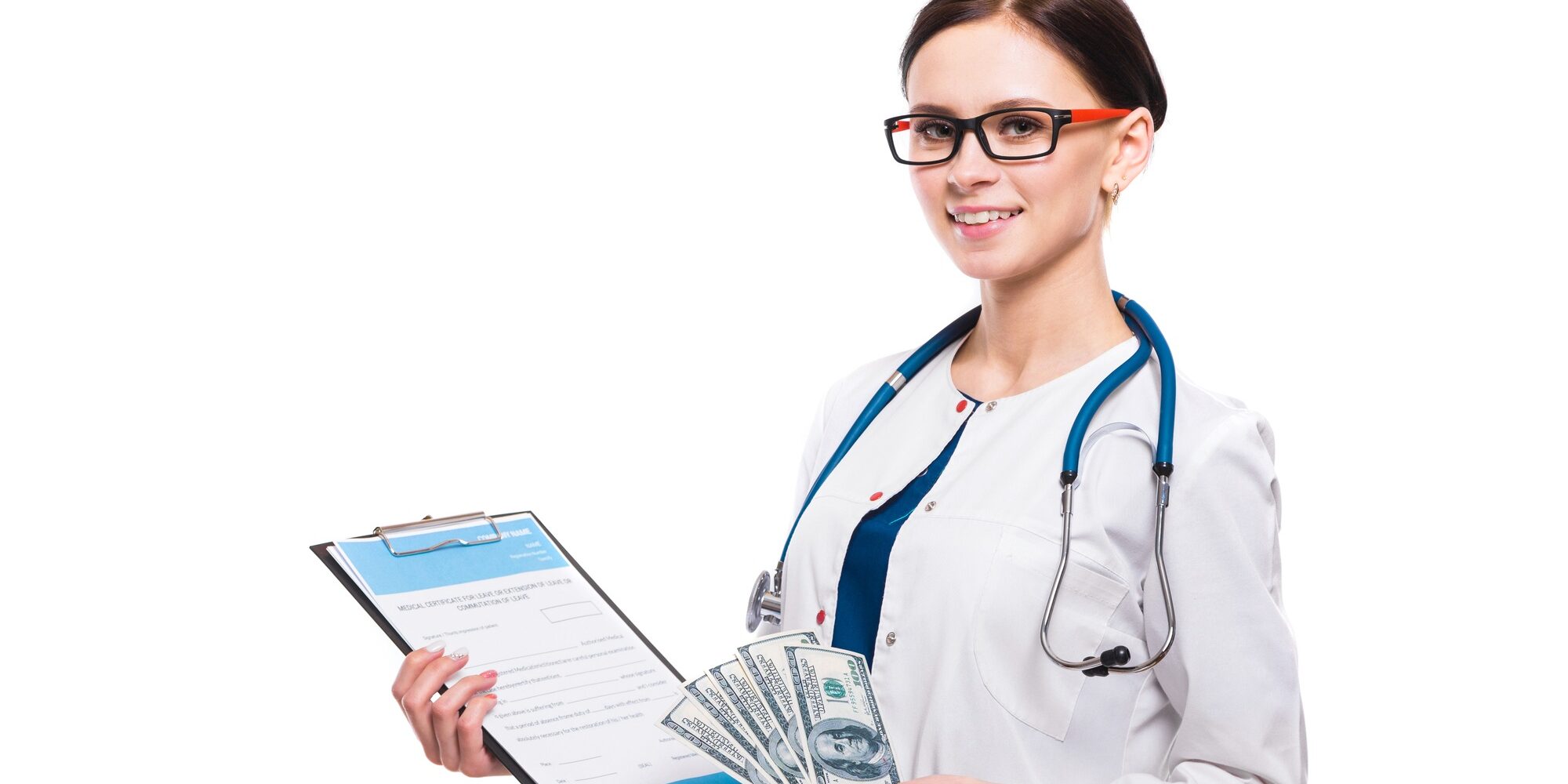
Pharmacist Salary in the US: What You Need to Know
This article explains pharmacist salary ranges—from hourly to annual pay—across practice settings. Learn how experience, location, and role shape wages, and find actionable advice on negotiating compensation, career advancement, and securing the best package through Pharmuni’s courses, resume tools, and GMP training.
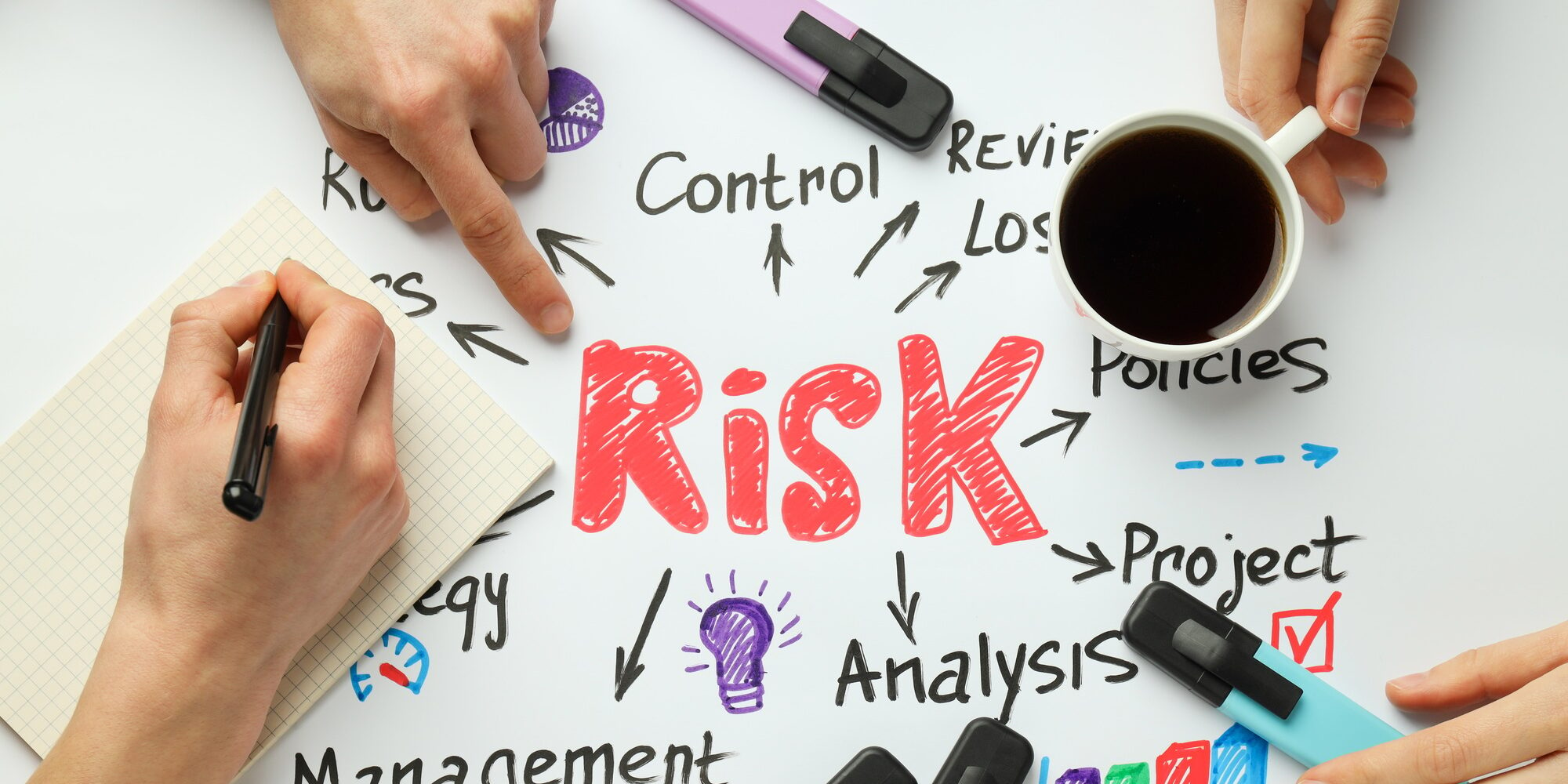
Risk Assessment Tools: Your Complete Guide to Smarter Decisions
Risk assessment tools help businesses identify, analyze, and control risks before they cause problems. From healthcare to pharma, tools like FMEA, HACCP, and Johns Hopkins fall risk assessments empower professionals with reliable strategies. Learn methods, compare approaches, and apply practical insights for better outcomes.
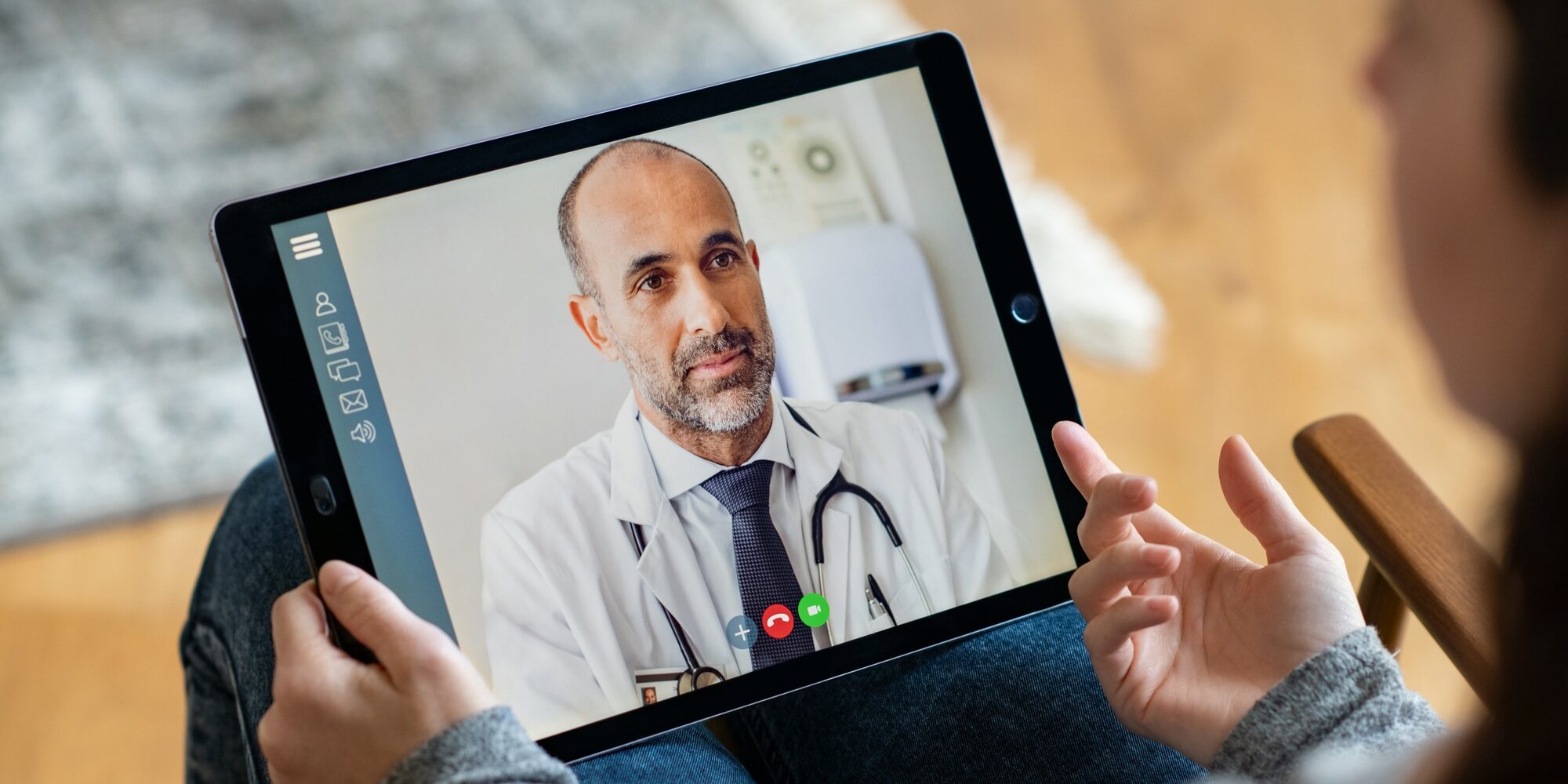
Pharmacovigilance Jobs Remote: The Complete Career Guide
Looking for pharmacovigilance jobs remote? This guide shows you where to find remote drug safety roles, how to qualify, and which global opportunities exist. Learn practical strategies, entry-level tips, and career insights to boost your chances in the competitive pharmacovigilance market.